优秀点检案例文档格式.doc
《优秀点检案例文档格式.doc》由会员分享,可在线阅读,更多相关《优秀点检案例文档格式.doc(51页珍藏版)》请在冰豆网上搜索。
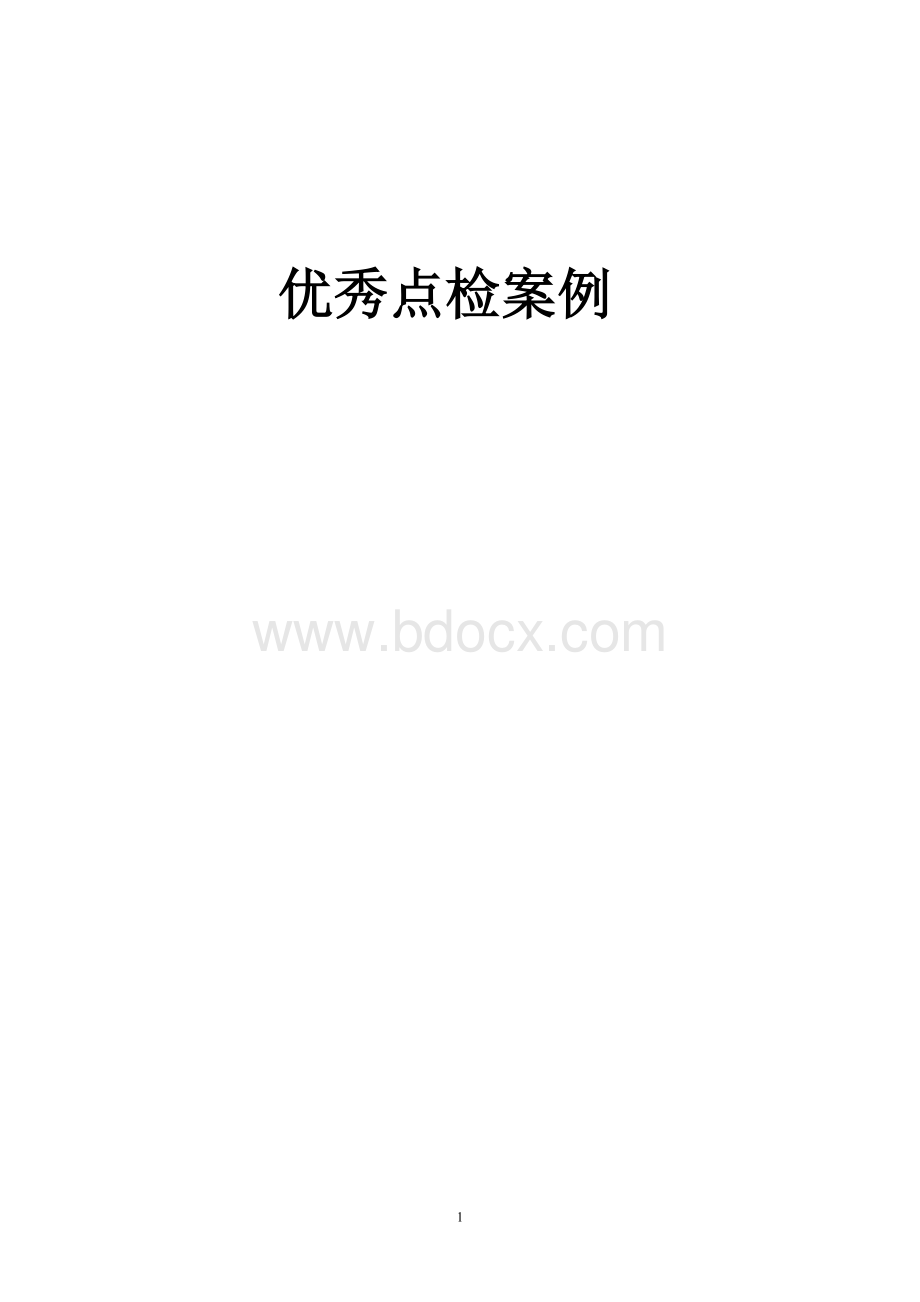
排除“死辊故障”总结创新成果
老设备也能焕发“青春”
2号热处理炉炉压失控故障分析处理
深入浅出打破常规消隐患
方法总比困难多创新理念结硕果
正确判断故障原因避免故障损失扩大
知设备环境快速排除故障
●工作方法
检从“勤”开始
建立培训机制提高设备维护技能
做实做细夯实高炉定修项目管理
关注细节推行作业程序标准化
●降本增效
精心维护延长工作槽使用寿命
备件改制变废为宝
●台帐履历
健全关键备件档案准确把握设备状态
●TPM
团队协同效率高“日清…日毕”隐患除
生产、设备联动消除松卷缺陷
快速拆装及安全便捷的作业平台
●创新
消化、吸收、改进消除煤清液压系统缺陷
创新让RH挡板改造成为现实
锐意进取不断推进技术创新
●看图案例分析
巧动脑筋消除点检盲区
推、拉杆是初轧机重要附属设备推床的传动件,一旦发生断裂,将使初轧
机中断轧钢,主轧线被迫停产,很有可能造成四级以上设备事故。
2005年和2006年,初轧机共发生推、拉杆断裂故障4起,造成停轧时间20多小时。
点检员通过细心观察,发现以下问题:
1、推、拉杆疲劳源一般都出现在底部齿条托板的接口焊缝处;
2、该部位恰好位于齿条箱封闭罩壳内,设备运转时无法点检,推、拉杆换一直作为周期性管理项目在大定修和年修中实施;
3、齿条箱内部空间狭小、光线昏暗、地面粘滑,点检人员在检查过更程中经常容易发生碰伤、滑跤等不安全因素。
找到问题根源,但怎么做才能及时掌握在线备件的使用状况呢?
点检员采取了在两台初轧机八个推床齿条箱两侧,开设点检窥视孔的办法,使点检人员不必钻进齿条箱内部,也不必等到大定修或年修,就可以清楚、方便地检查齿条板螺栓变形、松动、脱落情况和底部齿条托板接口焊缝开裂情况,一举解决了上述3项对掌控设备状态不利的因素;
同时在9672上,将推拉杆易劣化部位点检周期进行了缩短,以达到掌控推拉杆状态的目的。
经过相关的改进仅在2007年中,点检人员就先后发现四根在线推拉杆存在的裂缝缺陷,从而能利用定修或待热更换、处理,使设备隐患消灭在了日常点检过程中。
点评:
点检到位率和点检有效率直接关系到设备的稳定运行,对一些平时不容易点检到或不具备条件点检的设备,不能借侥幸心理对待,否则后患无穷,必须通过改进点检方式凭或点检手段来确保关键部位状态受控。
敏锐洞察消除锡溶解槽锡粒堆积
2007年12月5日,点检员按惯例对锡溶解及锡泥过滤系统的过滤器进行清洗,当清洗至锡溶解槽过滤器时,发现过滤器内锡粒无论是数量还是颗粒大小都骤然猛增。
结合上周清洗该过滤器的情况,及多年的点检维护经验,他初步判定锡溶解槽的多孔网板存在着异常,需立即将锡溶解槽解体进行确认。
通过与生产方紧急协调,生产将锡离子浓度按上限控制、锡离子含量检测送样由每班一次改为每1小时一次、联系计划安排1.1/1.1低镀锡量稳速组织生产,点检员同步迅速将检修人员、工器具、物料安排到位。
在解体之后发现多孔网板存在着严重的变形现象,导致锡粒直接越过网板堆积在下槽,将过滤器堵塞,通过更换多孔网板备件,在发现异常5个小时之后,锡溶解系统恢复了正常。
这个异常如果没有及时发现,将会造成锡溶解槽内锡粒堆积,系统无法进行吹氧,最终将会导致锡溶解系统瘫痪,机组长时间停机的严重后果。
评语:
该案例真实地反映了点检员认认真真、脚踏实地的工作作风,从现场出现的一点小异常看出了大问题,显示了该点检员敏锐的判断力、丰富的现场点检经验,从异常的发生到应急措施的有效制定、落实,反映了该点检员极强的横向协调能力。
点检员在与3RH操作人员了解设备运转情况时,听到操作人员反映真空复压阀有时动作不良,要反复开、关多次,才能动作到位。
通过对电磁阀拆卸检查,未发现异常:
阀体无垃圾、密封元件良好;
上线后,气源压力正常,无泄漏故障。
我们马上联想起,最近已有几个操作人员提起,由1#电磁阀箱控制的多个阀门都曾出现过,不能一次动作到位,需要开、关动作多次才动作的情况。
为查清原因,点检员在现场强制动作了几个电磁阀,发现电磁阀的切换声音良好。
就在面对着电磁阀冥思苦想,找不到原因时,一阵冷风吹过,点检员不由自主打了个冷颤,灵感伴随冷颤而至,对了,1#电磁阀箱的安装位置正好处于风口,穿堂风很急,现在正是冬天,由于低温,电磁阀内部润滑用的油脂存在时而凝固的现象,阻力的增加导致阀芯动作不良,所以才会发生需要反复开、关多次的故障。
在把1#电磁阀箱整体移位后,再也没出现类似现象,为设备的稳定运行提供了可靠的保证,也为电磁阀周期管理打下良好的基础。
以上案例中貌似简单的设备故障原因分析和处理过程,乍看以为故障原因分析过程中运气的成分占很大的比例,其实这是和点检员扎实的设备管理技能、兢兢业业的敬业精神密不可分,该案例提示我们在设备管理中不可“老思维,死脑筋”的思考问题,不断改变思维模式、不断创新就能起到事半功倍的效果。
顺藤摸瓜系列措施消除万向轴隐患
1550轧机3#一5#机架使用的主传动轴为日本中村自工设计制造的万向轴,装机量6根。
机组开工后特别近几年的使用中,先后发生轧辊侧十字销轴承的寿命短、花键磨损等问题,曾多次造成长时间停机。
2006年3月主传万向轴改型,试用德国VOITH万向轴,使用效果总体良好。
点检员没有放松对万向轴的状态跟踪,2007年12月中旬,在观察传动轴运行情况时发现,其中一根轴在窜动过程中出现和轧辊窜动不同步的轻微异常。
他仔细分析了万向轴的结构,认为问题应该出现在轴内部弹簧伸缩部位,可能会有弹簧磨损或连接不善的情况。
点检员果断利用12月下旬定修对此轴进行了更换。
传动轴解体后果然发现,轴内部伸缩弹簧与导向杆已脱焊松动,弹簧和导向杆已有磨损。
(见下图)
此事并非小事,点检员立刻通过有关部门联系厂家,在现的实用加固法,巧妙地避免了轴筒解体破除、焊接的大“手术”,并以轴帽作平衡。
经处理后整轴一次通过动平衡试验,获得成功。
点检员没有歇手,对另外两根在线轴提出了同样的疑问。
德方坚持此问题纯属偶然。
点检员翻阅了德方的设计图纸及加工工艺后,初判在线2根轴应存在同样的隐患,他们利用08年3月3日的定修,对在线2根传动轴下机解体,
果然发现了同样的问题,再次避免了一起重大设备事故的发生。
德方在较真的点检员面前,认真审视了设计及加工工艺问题,并对原图纸进行了修改。
**在后续的万向轴申购中也立即进行了调整。
点检不能因为设备先进而放松工作,在持续的跟踪过程中,及时发现微小的设备异常,这是点检的踏实;
从细微中排摸出重大设备隐忠,采取适合现场、打破常规的有效消缺措施,体现了点检的有效:
而抓住异常不放,深究原因、举一反三,甚至敢于向外方说不,是点检员责任感、“设备一生管理”理念的最好实践。
冷轧薄板厂冷轧机组自2000年设备改造以来,原料多头供应来源及板形不佳造成活套高速充套时经常发生带钢跑偏现象,活套充套量只能达到总套量的40%~50%,严重影响了机组产量的发挥。
经过对活套跑偏现场反复跟踪、分析,点检员注意到了:
带钢在活套中的运行状态与活套辊系的接触面有直接的关系,明确了带钢跑偏问题的改善关键点:
辊子和带钢接触中产生的相对作用力。
点检员将问题点聚焦在辊系相对位置精度、摆动门托带辊与带钢的角度、纠偏辊设计长度和摆动角、转向辊辊形”等几个方面,并采取了针对性的措施:
1、对活套辊系位置精度进行系统测量、调整。
2、调整带钢托辊的角度,将摆动门关闭时两扇门的托带辊角度从3度改为0度,与轧制中心线呈垂直方向
平键改为阶梯键
带钢托辊调整示意图
3、加大纠偏辊长度及摆动角度,减少带钢板形偏差较大高速运行时跑出辊面的几率,进一步改善带钢两边张力。
4、将活套小车活套转向辊由梯形辊面,改成2mm弧形凸度辊面,改善带钢与辊面接触面积。
通过对活套辊系、托带辊、纠偏辊及轨道的调整改造,活套冲套量能保证满套(90%)生产要求,机组的轧制速度不断的提高,满足了连续轧制的设计要求。
保证机组的生产能力达标。
设备运行中出现的问题,需要点检员细心地“层层剥茧”,才能发现影响设备状态的系列问题,刘万灵没有局限于简单的问题呈现,而足从多角度去分析问题的产生点,并分别采取针对性、有效的办法,不难但系统、完整、有效。
冷轧薄板主轧线采用无头轧制的连续生产方式,对设备的维护提出了更高的要求,03年3月引进了设备在线故障检测与诊断系统。
投运以来发现2#机架主传动齿轮箱的振动数据逐渐增大,将会对设备的使用寿命大大降低。
为找出原因,点检员对照2#机架主传动齿轮箱图纸基础参数,进行了齿轮啮合频率计算,转速传感器提供的实时输入转速数据显示,齿轮表面存在磨
损。
从振动频率来看,振动峰值一般集中在180Hz~220Hz之间,而2#机架转速350rpm~410rpm,这正好与2#机架高速齿轮啮合频率吻合,故排除了轴承间隙过大的可能性。
通过着色法检查齿间隙。
发现齿轮啮合面为全齿宽的70%以上、齿轮间隙为0.45~0.55mm,齿轮间隙在技术规范范围内。
对高速齿进
一步检查发现高速齿工作侧有一个啮合齿端部呈块状剥落(长20mm、宽15mm);
且高速齿工作图二侧所有啮合齿端部都有疲劳及点蚀现象。
低速轴啮合齿中部也有呈椭圆状剥落现象。
在线检测采集的振动频率图像,振幅警示值4mm/s,该图显示为9mm/s。
振动值较基础数据大大增加。
根据现场高速齿啮合齿端部疲劳及点蚀现象分析:
1)从齿啮合情况来看由于高速齿啮合面有偏移(即齿轮不对中)使齿面受力不均,产生疲劳损坏。
2)由于轧机在正常运行时2#机架轧制力分配较大,导致高速齿面局部受力增大,使该2#机架主传动齿箱齿轮长期处于疲劳状态从而产生啮合齿面点蚀及齿端部有块状剥落。
现场对啮合齿端部剥落处进行修磨去除残余应力。
在修磨过程中发现该齿端部块状剥落处有裂缝,立即进行着色法探伤,并反复修磨直至着色法探伤结果正常(修磨面积:
长25mm,宽20mm,深5mm)。
修磨其它有点蚀的啮合齿面至消除缺陷。
在修磨过的齿面处用抛光机进行抛光,然后在安装后进行齿面啮合的检查,确定啮合面的良好。
经过现场处理后设备进行回装,测量2#机架主传动齿轮箱振动值,较以前有明显降低,设备状态有所改善。
经过一星期的运行,观察2#机架主传动齿轮箱第一对齿(中间上部水平位置)测点振动值的情况,发现振动的最大值比原来明显减小,经检修后2#机架主传动齿轮箱第一对齿测点振动值明显降低。
现代化的设备具有技术先进、结构复杂两大特点,许多部位靠常规点检手段难以掌控,如机械设备的异常振动:
同时结构复杂的主作业线设备的解体检查相当困难,国内、外经验证明,设备诊断技术是与生产设备的状态共同发展、相辅相成的,点检员必须从“五感”的初级点检方法,逐步向以“诊断技术”为基础的状态点检发展,以实现现代化、复杂设备的有效点检。
2050热轧G辊