砂型铸造工艺的设计说明文档格式.docx
《砂型铸造工艺的设计说明文档格式.docx》由会员分享,可在线阅读,更多相关《砂型铸造工艺的设计说明文档格式.docx(20页珍藏版)》请在冰豆网上搜索。
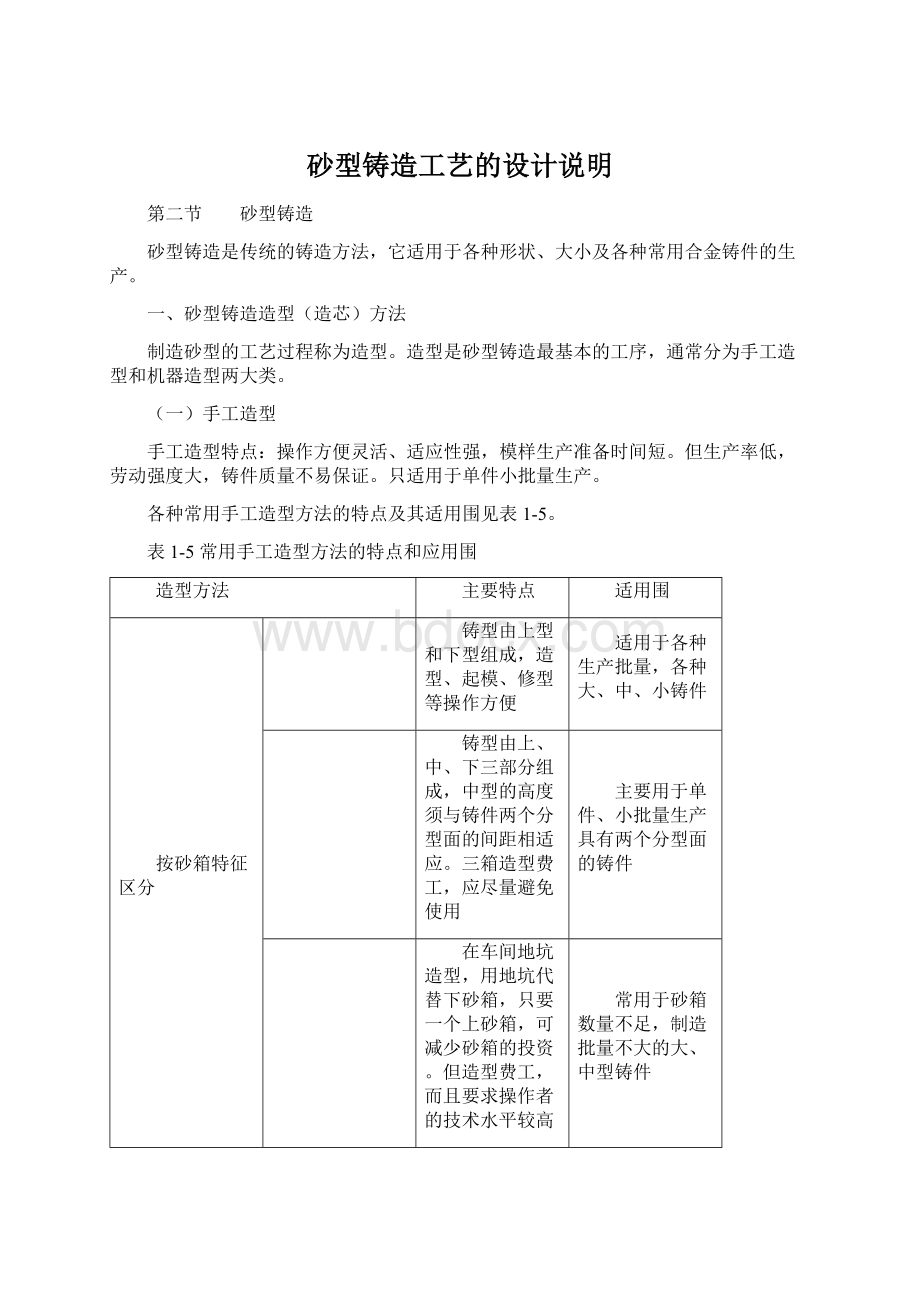
但造型费工,而且要求操作者的技术水平较高
常用于砂箱数量不足,制造批量不大的大、中型铸件
铸型合型后,将砂箱脱出,重新用于造型。
浇注前,须用型砂将脱箱后的砂型周围填紧,也可在砂型上加套箱
主要用在生产小铸件,砂箱尺寸较小
按模样特征区分
模样是整体的,多数情况下,型腔全部在下半型,上半型无型腔。
造型简单,铸件不会产生错型缺陷
适用于一端为最大截面,且为平面的铸件
模样是整体的,但铸件的分型面是曲面。
为了起模方便,造型时用手工挖去阻碍起模的型砂。
每造一件,就挖砂一次,费工、生产率低
用于单件或小批量生产分型面不是平面的铸件
为了克服挖砂造型的缺点,先将模样放在一个预先作好的假箱上,然后放在假箱上造下型,省去挖砂操作。
操作简便,分型面整齐
用于成批生产分型面不是平面的铸件
将模样沿最大截面处分为两半,型腔分别位于上、下两个半型。
造型简单,节省工时
常用于最大截面在中部的铸件
铸件上有妨碍起模的小凸台、肋条等。
制模时将此部分作成活块,在主体模样起出后,从侧面取出活块。
造型费工,要求操作者的技术水平较高
主要用于单件、小批量生产带有突出部分、难以起模的铸件
用刮板代替模样造型。
可大大降低模样成本,节约木材,缩短生产周期。
但生产率低,要求操作者的技术水平较高
主要用于有等截面的或回转体的大、中型铸件的单件或小批量生产
(二)机器造型
机器造型特点:
大批量生产砂型的主要方法,能够显著提高劳动生产率,改善劳动条件,并提高铸件的尺寸精度、表面质量,使加工余量减小。
1.
基本原理图1-18所示为顶杆起模式震压造型机的工作过程。
图1-18震压造型机的工作过程
填砂→震击紧砂→辅助压实→起模
2.
工艺特点机器造型工艺是采用模底板进行两箱造型。
模底板是将模样、浇注系统沿分型面与底板联结成一个整体的专用模具。
造型后,底板形成分型面,模样形成铸型空腔。
(三)造芯
用途:
当制作空心铸件,或铸件的外壁凹,或铸件具有影响起模的外凸时,经常要用到型芯,制作型芯的工艺过程称为造芯。
型芯可用手工制造,也可用机器制造。
形状复杂的型芯可分块制造,然后粘合成形。
注意:
为了提高型芯的刚度和强度,需在型芯中放入芯骨;
为了提高型芯的透气性,需在型芯的部制作通气孔;
为了提高型芯的强度和透气性,一般型芯需烘干使用。
二、砂型铸造工艺设计
目的:
为了获得健全的合格铸件,减小铸型制造的工作量,降低铸件成本,在砂型铸造的生产准备过程中,必须合理地制订出铸造工艺方案,并绘制出铸造工艺图。
铸造工艺图:
在零件图中用各种工艺符号表示出铸造工艺方案的图形,其中包括:
铸件的浇注位置;
铸型分型面;
型芯的数量、形状、固定方法及下芯次序;
加工余量;
起模斜度;
收缩率;
浇注系统;
冒口;
冷铁的尺寸和布置等。
铸造工艺图是指导模样(芯盒)设计、生产准备、铸型制造和铸件检验的基本工艺文件。
依据铸造工艺图,结合所选造型方法,便可绘制出模样图及合箱图。
图1-19为支座的铸造工艺图、模样图及合箱图。
图1-19支座的铸造工艺图、模样图及合型图
a)零件图
b)铸造工艺图(左)和模样图(右)c)合型图
(一)浇注位置的选择
浇注位置:
浇注时铸件在铸型中所处的位置,选择原则如下:
1.铸件的重要加工面应朝下或位于侧面
图1-20所示为车床床身铸件的浇注位置方案。
由于床身导轨面是重要表面,不允许有明显的表面缺陷,而且要求组织致密,因此应将导轨面朝下浇注。
图1-20车床床身的浇注位置
图1-21为起重机卷扬筒的浇注位置方案。
采用立式浇注,由于全部圆周表面均处于侧立位置,其质量均匀一致、较易获得合格铸件。
图1-21卷扬筒的浇注位置
1.
铸件的大平面应朝下
型腔的上表面除了容易产生砂眼、气孔、夹渣等缺陷外,大平面还常容易产生夹砂缺陷。
因此,对平板、圆盘类铸件的大平面应朝下。
2.
面积较大的薄壁部分置于铸型下部或使其处于垂直或倾斜位置
可以有效防止铸件产生浇不足或冷隔等缺陷。
图1-22为油盘铸件的合理浇注位置。
图1-22薄壁件的浇注位置
3.
对于容易产生缩孔的铸件,应将厚大部分放在分型面附近的上部或侧面
以便在铸件厚壁处直接安置冒口,使之实现自下而上的定向凝固。
如前述之铸钢卷扬筒,浇注时厚端放在上部是合理的;
反之,若厚端在下部,则难以补缩。
(二)铸型分型面的选择
铸型分型面的选择恰当与否会影响铸件质量,使制模、造型、造芯、合箱或清理等工序复杂化,甚至还可增大切削加工的工作量。
分型面的选择原则:
1.便于起模,使造型工艺简化尽量使分型面平直、数量少,避免不必要的活块和型芯。
图1-23为一起重臂铸件,按图中所示的分型面为一平面,故可采用较简便的分模造型;
如果选用弯曲分型面,则需采用挖砂或假箱造型,而在大量生产中则使机器造型的模底板的制造费用增加。
图1-23起重臂的分型面
应尽量使铸型只有一个分型面,以便采用工艺简便的两箱造型。
多一个分型面,铸型就增加一些误差,使铸件的精度降低。
图1-24a所示的三通,其腔必须采用一个T字型芯来形成,但不同的分型方案,其分型面数量不同。
当中心线ab呈垂直时(图1-24b),铸型必须有三个分型面才能取出模样,即用四箱造型。
当中心线cd呈垂直时(图1-24c),铸型有两个分型面,必须采用三箱造型。
当中心线ab和cd都呈水平位置时(图1-24d),因铸型只有一个分型面,采用两箱造型即可。
显然,图1-24d是合理的分型方案。
图1-24三通的分型方案
图1-25所示支架分型方案是避免用活块的例子。
按图中方案I,凸台必须采用四个活块制出,而下部两个活块的部位较深,取出困难。
当改用方案II时,可省去活块,仅在A处稍加挖砂即可。
图1-25支架的分型方案
铸件的腔一般是由型芯形成的,有时可用型芯简化模样的外形,制出妨碍起模的凸台、侧凹等。
但制造型芯需要专门的工艺装备,并增加下芯工序,会增加铸件成本。
因此,选择分型面时应尽量避免不必要的型芯。
如图1-26所示的轮形铸件,由于轮的圆周面外侧凹,在批量不大的生产条件下,多采用三箱造型。
但在大批量生产条件下,采用机器造型,需要改用图中所示的环状型芯,使铸型简化成只有一个分型面,这种方法尽管增加了型芯的费用,但可通过机器造型所取得的经济效益得到补偿。
图1-26使用型芯减少分型面
2.尽量使铸件全部或大部置于同一砂箱,以保证铸件精度如图1-27所示。
图1-27车床床身铸件
3.尽量使型腔及主要型芯位于下型这样便于造型、下芯、合箱和检验铸件壁厚。
但下型型腔也不宜过深,并尽量避免使用吊芯和大的吊砂。
如图1-28所示。
图1-28机床支架
选择分型面的上述诸原则,对于某个具体的铸件来说难以全面满足,有时甚至互相矛盾。
因此,必须抓住主要矛盾、全面考虑,至于次要矛盾,则应从工艺措施上设法解决。
(三)工艺参数的确定
在铸造工艺方案初步确定之后,还必须选定铸件的机械加工余量、起模斜度、收缩率、型芯头尺寸等具体参数。
加工余量和最小铸出孔在铸件上为切削加工而加大的尺寸称为机械加工余量。
数值取决于:
铸件生产批量、合金的种类、铸件的大小、加工面与基准面之间的距离及加工面在浇注时的位置等。
采用机器造型,铸件精度高,余量可减小;
手工造型误差大,余量应加大。
铸钢件因表面粗糙,余量应加大;
非铁合金铸件价格昂贵,且表面光洁,余量应比铸铁小。
铸件的尺寸愈大或加工面与基准面之间的距离愈大,尺寸误差也愈大,故余量也应随之加大。
浇注时铸件朝上的表面因产生缺陷的机率较大,其余量应比底面和侧面大。
灰铸铁的机械加工余量见表1-6。
表1-6灰铸铁的机械加工余量(mm)
铸件最大尺寸
浇注时位置
加工面与基准面之间的距离
﹤50
50~120
120~260
260~500
500~800
800~1250
﹤120
顶面
底、侧面
3.5~4.5
2.5~3.5
4.0~4.5
3.0~3.5
4.0~5.0
3.0~4.0
4.5~5.0
3.5~4.0
5.0~5.5
4.5~6.0
5.0~6.0
6.0~7.0
6.5~7.0
5.0~7.0
4.5~5.5
7.0~8.0
7.5~9.0
4.0~5.5
6.5~7.5
7.5~8.0
5.5~6.0
8.0~9.0
5.5~7.0
8.5~10
铸件的孔、槽:
一般来说,较大的孔、槽应当铸出,以减少切削加工工时,节约金属材料,并可减小铸件上的热节;
较小的孔则不必铸出,用机加工较经济。
最小铸出孔的参考数值见表1-7。
对于零件图上不要求加工的孔、槽以及弯曲孔等,一般均应铸出。
表1-7铸件毛坯的最小铸出孔(mm)
生产批量
最小铸出孔的直径d
灰铸铁件
铸钢件
大量生产
12~15
—
成批生产
15~30
30~50
单件、小批量生产
50
起模斜度为了使模样(或型芯)易于从砂型(或芯盒)中取出,凡垂直于分型面的立壁,制造模样时必须留出一定的倾斜度,此倾斜度称为起模斜度,如图1-29所示。
在铸造工艺图上,加工表面上的起模斜度应结合加工余量直接表示出,而不加工表面上的斜度(结构斜度)仅需用文字注明即可。
图1-29起模斜度
3.
收缩率铸件冷却后的尺寸比型腔尺寸略为缩小,为保证铸件的应有尺寸,模样尺寸必须比铸件放大一个该合金的收缩率。
铸造收缩率K表达式为:
式中——模样或芯盒工作面的尺寸,单位为mm;
——铸件的尺寸,单位为mm。
通常,灰铸铁的铸造收缩率为0.7%~1.0%,铸造碳钢为1.3%~2.0%,铸造锡青铜为1.2%~1.4%。
4.
型芯头型芯头可分为垂直芯头和水平芯头两大类,如图1-30所示。
图1-30型芯头的构造
a)垂直芯头b)水平芯头
(四)铸造工艺设计的一般程序
铸造工艺设计:
在生产铸件之前,编制出控制该铸件生产工艺的技术文件。
铸造工艺设计主要是画铸造工艺图、铸件毛坯图、铸型装配图和编