塑胶模具设计规范.docx
《塑胶模具设计规范.docx》由会员分享,可在线阅读,更多相关《塑胶模具设计规范.docx(21页珍藏版)》请在冰豆网上搜索。
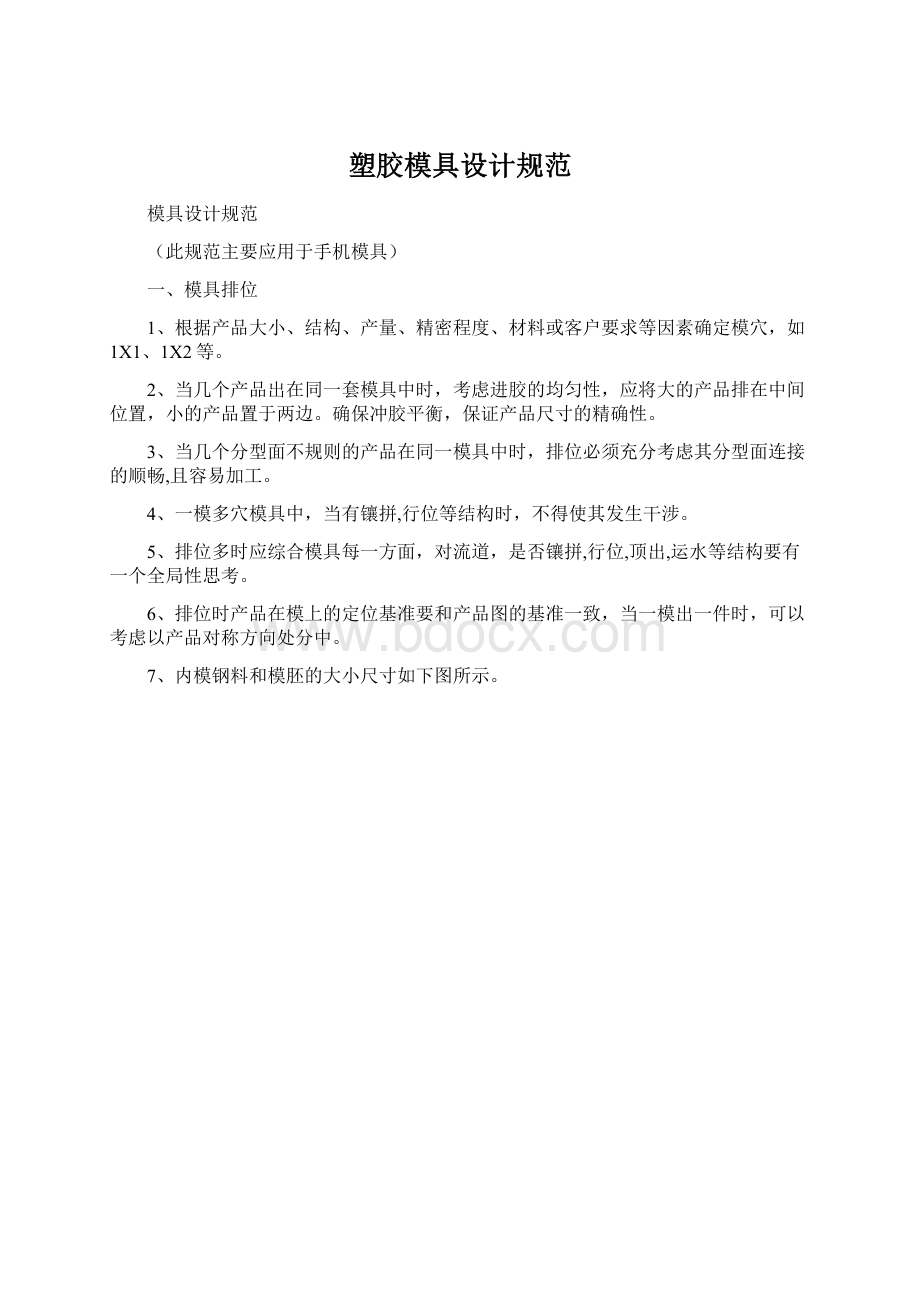
塑胶模具设计规范
模具设计规范
(此规范主要应用于手机模具)
一、模具排位
1、根据产品大小、结构、产量、精密程度、材料或客户要求等因素确定模穴,如1X1、1X2等。
2、当几个产品出在同一套模具中时,考虑进胶的均匀性,应将大的产品排在中间位置,小的产品置于两边。
确保冲胶平衡,保证产品尺寸的精确性。
3、当几个分型面不规则的产品在同一模具中时,排位必须充分考虑其分型面连接的顺畅,且容易加工。
4、一模多穴模具中,当有镶拼,行位等结构时,不得使其发生干涉。
5、排位多时应综合模具每一方面,对流道,是否镶拼,行位,顶出,运水等结构要有一个全局性思考。
6、排位时产品在模上的定位基准要和产品图的基准一致,当一模出一件时,可以考虑以产品对称方向处分中。
7、内模钢料和模胚的大小尺寸如下图所示。
8.产品大小和胶位厚度有较大相差时尽量不要出在同一套模具中。
9.模具方铁高度尽量订做标准高度。
10.模胚型号和中托司使用情况一定要写清楚(细水口需注明SP长度)
11.必要时需注明模胚吊模孔移位情况
12.考虑需不需开精框及内模料材料和规格(确定后模要不要镶大呵,如需要则一起订料,此为粗料.)
二、模具系统设计
一)、行位系统
当塑胶产品确定前后模开模方向后,有下列情况时一般会采用行位或斜顶等结构:
1)、相对出模方向塑胶产品上有倒扣或零度面;
2)、产品的出模斜度不够蚀纹的角度;
3)、保证特殊的外观面不能有夹线。
1、后模行位:
1)、后模行位统一做镶件压块,行位压块用螺丝固定,行位压块材料为油钢淬火至HRC48-52°。
2)、所有与行位相对运动的零部件的滑动面(包括行位底耐磨片,压条,铲基斜面)须锣(磨)油坑,油坑可为平行四边行、V形或圆环形。
3)、行位铲机钢材整体采用738H,在铲机斜面上镶耐磨片,耐磨片可突出斜面0.5mm,耐磨片厚度为6mm(如下图),材料为油钢,淬硬至HRC48-52°。
康铨公司的铲基采用国产S136淬硬至HRC46-50°。
4)、行位沉深B板25mm以上,行位压块沉深B板15mm以上。
5)、行位开模采用斜导柱。
斜导柱的大小及数量视行位大小而定,角度要比行位斜面小2-3°。
6)、行位定位必须准确,行位行程小的尽量采用弹弓加螺丝头的方式定位,行位行程大且不方便加装弹弓时,可采用多个行位波仔的方式定位,所有行位需加装定位螺丝,以防行位掉落,用油缸开合的行位及抽芯结构,要加装合理的行程开关。
7)、行位斜导柱的斜度通常为15°;长度不能与B板相干涉。
模胚上导柱长度要足够长,合模时导柱与导套先合,然后斜导柱才能套入行位。
8)、行位高度与长度理想比例为1:
2,实际视具体情况而定,但尽量不大于1:
1,否则会造成行位不够稳定。
9)、铲机与行位的配合面要求超过行位高度的2/3以上,大面积封胶的行位,铲机必须加反铲,模板上钢料宽度至少有15mm以上,如下图所示。
10)、不论行位的侧面是否封胶,其两侧均要做斜度,一般为单边1-3°。
类似手机底壳行位四面包夹线时,一般尽量在四R角中间以45度方向出行位夹线。
如图所示:
11)、行位行程的计算(以两板合模为例):
为保证制品顺利脱模,行位移动的距离一定要充分,一般以制品可以脱模的最小距离加上3mm为最小行程:
所有手机软胶类产品须做行位时,因为行位开模会将产品扣位略拉长,所以行位行软胶时退开的行程比行硬胶须更长一些。
12)、行位在分型面上行小针需做成隧道含针的形式或做“T”型槽形式。
小针尾部需做到4mm以上:
13)、行位座材料采用718H,行位镶件采用S136淬火加硬至HRC48-52°。
康铨公司的行位座采用国产8407加硬至HRC46-50°。
2、前模行位:
1)、前模行位一般采用GC或FC型模胚,行位做在A板上,铲机做在前模固定板上,A板与水口板用4支自制的标准小拉杆限位,小拉杆直径为16mm。
(附录1)A板和B板之间必须安装机械扣机或拉杆上部加弹簧(也可在水口板上加强力胶)。
结构优先考虑图a,其次考虑图b.
2)、前模行位的铲机采用油钢,行位座采用718H,(康铨公司的行位座采用国产8407加硬至HRC46-50度)。
行位镶件采用S136淬火加硬至HRC48-52°。
3、斜顶:
1)、斜顶结构首选图a,其次图b,再次图c。
斜顶在斜顶座里滑动,斜顶座以螺丝固定在顶针板里面。
斜顶座升入B板内,以青铜片导向(如图d),并将四角倒成C2X45°的C角。
斜顶材料一般用国产8407(康荃公司的斜顶材料为8407淬硬至HRC46-50度),斜顶座用油钢淬硬至HRC48-52度;斜顶能够做到全包胶的一定要做成全包胶形式(但不能影响外观),以防有披锋产生。
2)、当分型面上有斜顶时,需在回程杆下加做弹弓胶。
(如下图)
3)、斜顶有位置做大时尽量做大,以便增加强度。
多个斜顶共用一个斜顶座时,斜顶座可以劈开,方便配模。
二)、浇注系统:
1、流道:
流道应根据成品形状、塑胶特性、啤机调试、型腔的布置、入水位置及形式而进行设计,而且保证塑料能迅速而均匀地充满型腔。
常用流道为圆形或梯形和“U”形。
1)、主流道尽可能短,软胶类的产品的主流道长度应尽量小于50MM。
2)、分流道原则上为圆形,有如下几种情况流道需开成梯形:
a)、后模为推板时,前模分流道为梯形。
b)、采用点胶口入水时,前模A板底部开梯形流道。
c)、电镀产品的辅助流道一般为梯形,都开设在后模。
d)、小产品可在后模一側开梯形流道。
e)、梯形流道的尺寸:
3)、主流道和分流道的末端及拐角处均须做冷料井及排气槽,如图。
4)、需电镀的产品需采用辅助流道,并在流道上做镶针和胶柱,方便胶件叠放。
5)、在同一模具上成型两种尺寸相差太大的成品时,应修正分流道来达到进胶平衡。
6)、当同一模具上有多级分流道时,上一级分流道大约是下一级分流道直径的1.4倍左右。
7)、PC和PMMA等透明材料须采用“S”形分流道。
8)、所有流道必须抛光,以免影响注塑流动性及啤塑外观。
9)、电镀件需考虑做挂位和防呆设计。
10)、叠放孔不宜太深,防止有残余电镀液;流道底尽量倒R角,利于导电。
2、浇口:
浇口的形式及大小需根据成品大小和形状,流道长短,成品塑料特性,客户要求等因素而定,入水位置通常设在成品最大壁厚处。
常用入水形式如下:
1)、直接浇口:
制品在外观和功能均允许的情况下才可使用直接浇口。
2)、侧浇口:
侧浇口设置于制品分型面处,制品允许有浇口痕迹才可以使用,侧浇口包括边缘浇口和搭接浇口,其浇口尺寸与壁厚、大小、材料等许多因素有关,一般规格如图。
3)、点胶口:
4)、潜伏式浇口:
潜伏式浇口有潜顶针、潜薄片、潜产品和潜牛角等几种,手机模的潜水首选潜牛角(注意牛角不易太弯,不利顶出)。
a)、潜顶针:
潜顶针的位置空间上不能太窄,要能方便下剪钳。
b)、潜牛角:
3、唧嘴:
1)、三板模尽量套用自制的标准大唧嘴(附录2)。
2)、两板模使用自制的标准小唧嘴(附录3),软胶模孔径ф2.5,硬胶模孔径ф3.0。
(如下图)
3)、唧嘴R的大小需根据注塑机型号和客户的要求来定,一般R=15.5mm或R=21mm。
(如上图)
4)、唧嘴底距离A板框底做到8—10mm
4、定位圈:
1)、每套模具必须装有定位圈(即定位法兰),以便装模定位。
2)、定位圈直径一般为ф100(公差-0.2~-0.4mm)。
凸出模面板高度10mm,
5、自动脱水口装置:
1)、细水口模(三板模)均采用自制标准小拉杆带动水口板移动使水口自动脱落。
小拉杆直径为16mm(附录1)
2)、一般采用B板(动模板)面上装有4粒尼龙胶塞的结构,当有前模行位时,一定要采用机械扣机的形式。
3)、水口针以ф5mm顶针磨成如下图形式:
三)、冷却系统
1、所有模具冷却水出口必须打“OUT”,入口必须打“IN”,并有数字编号,如“IN1”、
“OUT1”等等
2、运水排布均匀,直径做ф6mm。
大产品做到ф8mm--ф10mm
3、运水孔边至胶位的距离为6mm以上。
4、运水孔边与螺丝、顶针、斜顶、镶件至少相距4mm。
5、所有防水圈均采用耐高温胶圈,胶圈型号为ф12*2.5。
6、为方便安装运水接头,运水每个进、出口之间的距离至少保证有30mm以上。
7、模胚上运水进、出口螺牙采用管螺纹1/8”BSP牙。
8、运水的排布尽量从左右侧进出,并且进出口尽量对准基准一侧。
四)、顶出系统
制品在模具中冷却固化之后,需切实可靠将其从模具中推顶出来,这一机构称之为顶出系统。
同时必须保证,当模具闭合时,它不会与模具其它零部件发生干涉,并回到初始位置,准备进行下一个周期的动作顶出系统要保证除软胶模外所有模具在注塑时都能全自动啤塑。
1、顶出行程:
一般要求制品完全脱离钢料至少10mm,如下图所示,
2、正确的顶出位置,应设在制品脱模困难的地方,如骨位、柱位及有包紧力的地方,同时顶出痕迹不能影响制品外观,并且顶出机构不能和其它零件(如撑头、螺丝等)干涉。
3、常用的顶出方式如下
1)、顶针:
a)许可的情况下,尽量使用3mm以上的顶针,顶针小于或等于2mm时需带托。
3mm以下的顶针都在盘起或在MISUMI订购(视项目而定),托针须注明托位的大小和长度,并使用相应的编号。
b)当顶针位于圆弧面或顶针和司筒受胶位方向限制时,必须要设计定位装置,定位方式如下图,
c)所有顶针必须高出模面0.05mm。
d)所有顶针和镶针为1.5mm及1.5mm以下时,钢料上顶针和镶针孔采用慢走丝线割,1.5mm以上顶针孔采用慢走丝线割,当啤塑材料为PA、POM、软胶系列等一些容易走批峰的塑胶时,所有顶针孔也需要慢走丝线割。
2)、司筒:
a)所有司筒孔采用慢走丝线割。
b)所有司筒都在盘起订购。
在订购时须要注明盘起的编号。
1.尽量采用标准司筒,司筒大小必须小于成形胶柱的尺寸。
2.为了防止司筒偏心,司筒头部切除余量不能超过5mm,模具设计在订购司筒时长度比实际长度长3-5mm。
3.司筒内针不能和顶棍孔干涉。
3)、扁顶针:
a)当产品上有较深骨位时,一般使用扁顶针。
b)所有扁顶针孔采用慢走丝线割。
c)模具设计时,不能选用过薄的扁顶针,厚度优先采用1.0mm以上的扁顶针。
d)所有扁顶针在盘起订购。
在物料订购时,须注明扁顶针托位的长度和大小,并使用盘起的编号。
4)、推方(直顶):
推方一般要做挂台,以螺丝固定在顶针面板上。
5)、推板:
当轮廓封闭,周长较长,并且内外表面均不允许顶针痕迹时,或者当产品过深,又没有足够的位置放置足够的顶针时,常采用推板推出结构.其基本结构见图:
4、顶棍孔
1)、顶棍孔的大小为ф35mm。
2)、特殊顶棍孔孔径及位置根据注塑机型实际尺寸(设计尺寸)来定。
5、方铁(凳子方、模角)
方铁的高度必须保证顶出装置将产品全部顶离钢料10mm以上。
6、顶针板导柱导套(中托司):
1)、所有模具都须加顶针板中托司(视项目而定)。
2)、因明利公司暂无中托司标准,在明利厂订购的模胚时,须由工程部标示中托司的位置和大小,在龙记和富得巴订购模胚时,按标准加中托司。
(现在明利有中托司标准)
3)、康铨公司的模具采用龙记模胚,并且要加滚珠式顶针板中托司。
7、顶针板弹簧:
1)、所有模具必须在顶针板上安装2根或4根复位弹弓,以助顶针板均匀回缩。
2)、除客户有特别要求外,所有模具均采用蓝弹弓,(康铨公司采用盘起黄弹弓)。
3)、复位弹弓压缩比不能大于自由长度的40%,必须在顶针面板上做2个或4个限位钉,防止复位弹弓被过分压缩。
如下图所示: