机械制造工艺学习题集第章参考答案修订Word文件下载.docx
《机械制造工艺学习题集第章参考答案修订Word文件下载.docx》由会员分享,可在线阅读,更多相关《机械制造工艺学习题集第章参考答案修订Word文件下载.docx(17页珍藏版)》请在冰豆网上搜索。
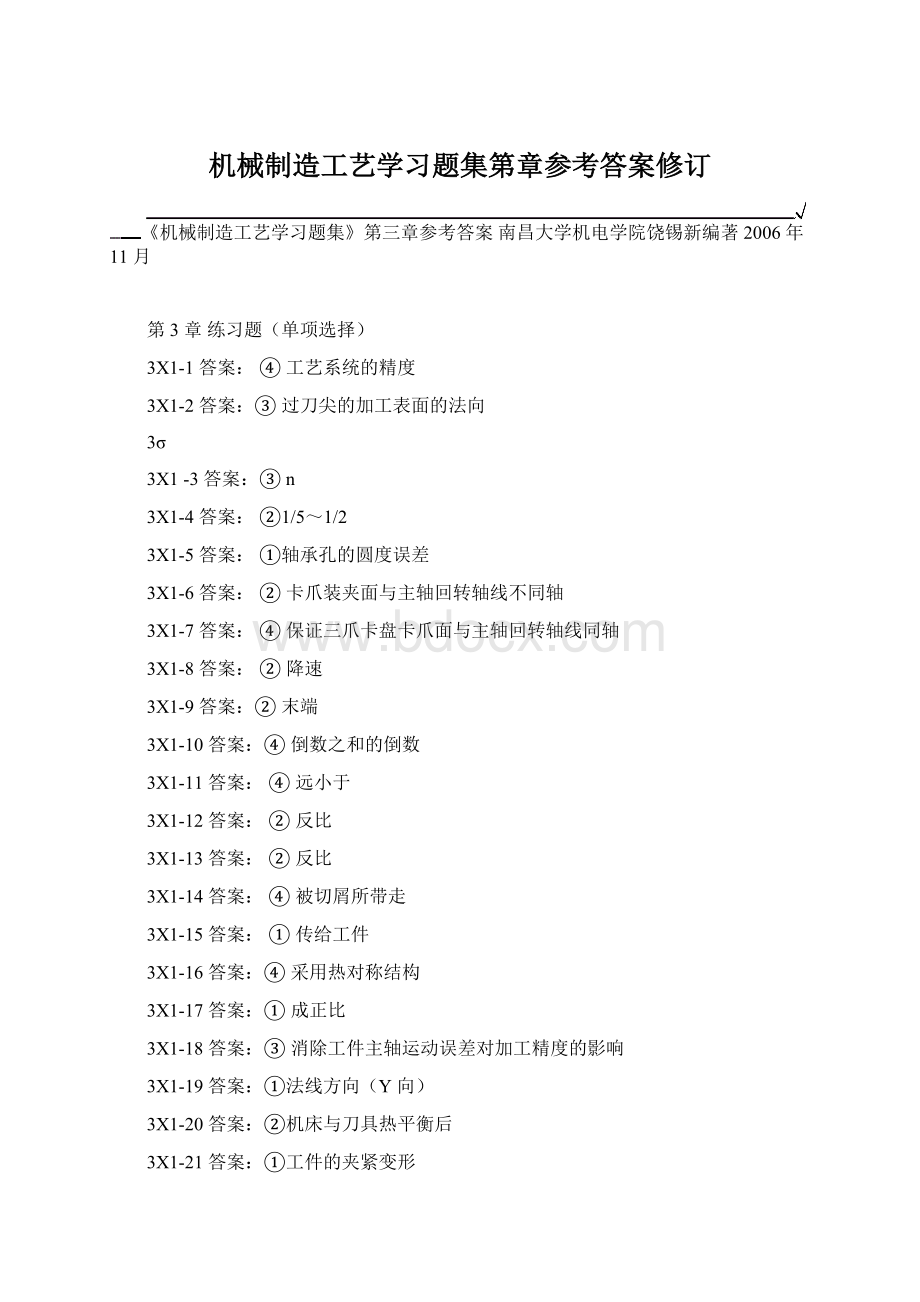
3X1-16答案:
④采用热对称结构
3X1-17答案:
①成正比
3X1-18答案:
③消除工件主轴运动误差对加工精度的影响
3X1-19答案:
①法线方向(Y向)
3X1-20答案:
②机床与刀具热平衡后
3X1-21答案:
①工件的夹紧变形
3X1-22答案:
③刀具磨损
3X1-23答案:
①切削热
3X1-24答案:
④安装误差
3X1-25答案:
②恒温
第四章练习题(多项选择)
3X2-1答案:
①试切法②调整法③定尺寸刀具法④自动控制法
3X2-2答案:
①径向跳动②轴向窜动③倾角摆动
3X2-3答案:
①零件材料②表面粗糙度③名义压强
3X2-4答案:
②三爪装夹面与主轴回转轴线不同轴③车床纵向导轨与主轴回转轴线不
平行
3X2-5答案:
①工件刚度不足③车床纵向导轨直线度误差
3X2-6答案:
②尾顶尖刚度不足③导轨扭曲④车床纵向导轨与主轴回转轴线不平
行
3X2-7答案:
①切削热②摩擦热
3X2-8答案:
②尾座轴线与主轴回转轴线不同轴
③刀具热变形④钻头刃磨不对称
3X2-9答案:
①机床几何误差③调整误差
3X2-10答案:
②工件定位误差③夹紧误差④毛坯余量不均引起的误差复映
3X2-11答案:
①确定工序能力②估算不合格品率③判别常值误差大小
1
3X2-12答案:
②工艺过程是否稳定④是否存在变值系统误差
第3章练习题(判断题)
3X3-1答案:
∨
3X3-2答案:
×
3X3-3答案:
3X3-4答案:
3X3-5答案:
3X3-6答案:
∨提示:
参考图4-31。
3X3-7答案:
提示:
磨削时导轨面温度升高,床身底部温度偏低,床身会上弯。
磨平
后冷却,
3X3-8答案:
导轨面将产生中凹。
3X3-9答案:
3X3-10答案:
3X3-11答案:
3X3-12答案:
3X3-13答案:
3X3-14答案:
3X3-15答案:
3X3-16答案:
3X3-17答案:
3X3-18答案:
第3章练习题(分析题)
3X4-1正确答案:
键槽底面对φ35mm下母线之间的平行度误差由3项组成:
①铣床工作台面与导轨的平行度误差:
0.05/300
②夹具制造与安装误差(表现为交点A的连线与夹具体底面的平行度误差):
0.01/150
③工件轴线与交点A的连线的平行度误差:
为此,首先计算
φ20±
0.05mm外圆中心在垂直方向上的变动量:
Δ0=0.7×
Td=
0.7×
0.1=0.07mm
可得到工件轴线与交点A的连线的平行度误差:
0.07/150
最后得到键槽底面(认为与铣床导轨平行)对工件轴线的平行度误差:
ΔP=0.05/300+0.01/150+0.07/150=0.21/300
3X4-2正确答案:
a)在径向切削力的作用下,尾顶尖处的位移量大于前顶尖处的位移量,加工后工件
外圆表面成锥形,右端止境大于左端直径。
b)在轴向切削力的作用下,工件受到扭矩的作用会产生顺
时针方向的偏转。
若刀具刚度很大,加工后端面会产生中凹。
c)由于切削力作用点位置变化,将使工件产生鞍形误差,
且右端直径大于左端直径,加工后零件最终的形状参见右图。
3X4-3正确答案:
2
A点处的支反力:
FA=300×
100=100N
D点处的支反力:
300
FD=300×
200=200N
在磨削力的作用下,A点处的位移量:
ΔA=100=
0.002mm
50000
在磨削力的作用下,D点处的位移量:
ΔD=200=
0.005mm
40000
由几何关系,可求出B点处的位移量:
ΔB=
0.002+
(0.005−
0.002)150
×
=
0.0035mm
C点处的位移量:
(0.005−
0.002)250
Δc=
0.0045mm
加工后,零件成锥形,锥度误差为0.001mm。
3X4-4正确答案:
1)工艺系统刚度分别为依据误差复映原理。
2)前、中、后3处的误差复映系数分别为:
−h
−
hh
h
ε
h1112
HH
1112
2122
h3132
3132
前、中、后3处的工艺系统刚度分别为:
k=Ck=Ck=C
ε1
ε2
3
ε3
忽略工件的变形,工艺系统刚度主要取决于头架刚度ktj、尾架刚度kwj和刀架刚度kdj。
并且有:
111
k1
=+
k
ktjdj
+
k2
4ktj
4kk
wjdj
k3kk
解上面的方程可得到:
=−
kkk
tj
dj
121⎛
⎞
kdjk2
⎜⎜
2⎝4k
4k
wj
⎟⎟
⎠
kk
3)优点:
可反映工作状态下的系统刚度。
缺点:
工艺系统存在许多影响加工误差的因素,实验中不可能将这些因素全部排除,
会使实验结构存在较大误差。
有时这种误差可能大到使实验结果不可信的程度。
3X4-5正确答案:
工件单面受热会产生翘曲变性,磨平后工件冷却下来,将使导轨产生中凹。
中凹量可
按式(4-24)计算:
Δθ
2×
y
'
˜α·
L·
=1×
10-5×
22405
8H×
8400
0.0784
mm
3X4-6正确答案:
?
分布图
分布曲线
11.99
习图3X4-6ans
12
(公差带)
工艺能力系数CP=0.2/(6×
0.003)=1.1
废品率约为50%
产生废品的主要原因是存在较大的常值系统误差,很可能是砂轮位置调整不当所
致;
改进办法是重新调整砂轮位置。
3X4-7正确答案:
画出分布曲线图,可计算出不合格品率为21.2%(计算过程略)
19.9
19.95
19.98
不合格品率
20
画出分布曲线图,可计算出不合格品率为21.2%
3X4-8正确答案:
1)画出x-R图:
计算各组平均值和极差,见表4-4-8;
计算中心线和上下控制限(参考式(4-32)(4-33),表4-6):
x
UCL=34.825
CL=28.88
LCL=22.935
R
5
10
4
x图
R图
15
样组序号
UCL=21.628
CL=10.25
LCL=0
习图3X4-8ans
x图:
中心线CL=x=?
xiμ
=28.88(m)
上控制线
UCL=x+A2R=
28.88+0.58×
10.25=
μ
34.825(m)
下控制线
R图:
中心线
LCL=x-A2R=28.88-0.58×
10.25=22.935(μm)
CL=R=10.25(μm)
UCL=DR=
2.11×
LCL=0
21.628(m)
根据以上结果作出x-R图,如习图4-4-8ans所示。
2)在x图上,有多个点子越出控制限,可以判定工艺过程不稳定。
3)在x图上,点子没有明显得变化趋势,无法判定有无变值系统误差。
4)在x图上,第4点到第9点之间,点子出现较大波动(R图亦如此),表明工艺系统在
此期间出现异常。
从第12点以后,点子有上升趋势(x图),值得密切注意,应继续采样
观察。
3X4-9正确答案:
1)影响孔径尺寸精度的因素:
刀具调整(调整镗刀刀刃的伸出长度);
刀具磨损;
刀具热变形。
2)影响销孔形状精度的因素:
主轴回转误差;
导轨导向误差;
工作台运动方向
与主轴回转轴线不平行;
机床热变形。
3)影响销孔位置精度的因素:
定位误差(设计基准(顶面)与定位基准(止口端面)
不重合,定位止口与夹具定位凸台、菱形销与销孔的配合间隙等引起);
夹紧误差;
调
整误差(夹具在工作台上的位置调整,菱形销与主轴同轴度的调整等);
夹具制造误差;
机床热变形;
工作台运动方向与主轴回转轴线不平行。
3X4-10正确答案:
答:
产生A圆柱度误差的原因是
51.015
(1)车床导轨在水平面内的直线度误差;
(2)床身导轨和主轴回转轴线在水平面内
不平行;
(3)床身导轨的扭曲;
(4)主轴回转轴线的角度摆动。
产生B对A的垂直度误差的原因是:
51.005