完整版模具毕业设计外文翻译353433Word格式.docx
《完整版模具毕业设计外文翻译353433Word格式.docx》由会员分享,可在线阅读,更多相关《完整版模具毕业设计外文翻译353433Word格式.docx(10页珍藏版)》请在冰豆网上搜索。
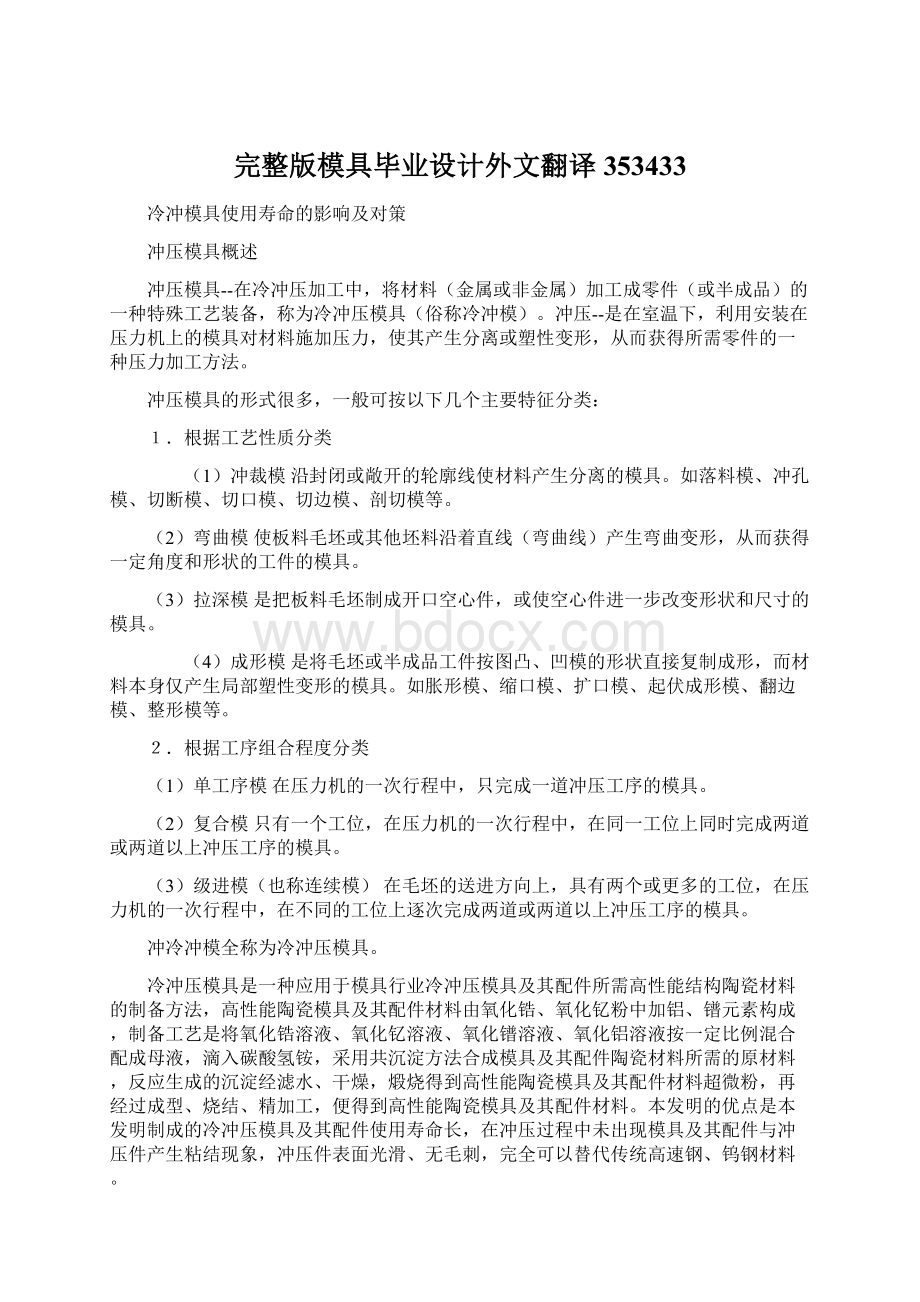
(3)拉深模是把板料毛坯制成开口空心件,或使空心件进一步改变形状和尺寸的模具。
(4)成形模是将毛坯或半成品工件按图凸、凹模的形状直接复制成形,而材料本身仅产生局部塑性变形的模具。
如胀形模、缩口模、扩口模、起伏成形模、翻边模、整形模等。
2.根据工序组合程度分类
(1)单工序模在压力机的一次行程中,只完成一道冲压工序的模具。
(2)复合模只有一个工位,在压力机的一次行程中,在同一工位上同时完成两道或两道以上冲压工序的模具。
(3)级进模(也称连续模)在毛坯的送进方向上,具有两个或更多的工位,在压力机的一次行程中,在不同的工位上逐次完成两道或两道以上冲压工序的模具。
冲冷冲模全称为冷冲压模具。
冷冲压模具是一种应用于模具行业冷冲压模具及其配件所需高性能结构陶瓷材料的制备方法,高性能陶瓷模具及其配件材料由氧化锆、氧化钇粉中加铝、镨元素构成,制备工艺是将氧化锆溶液、氧化钇溶液、氧化镨溶液、氧化铝溶液按一定比例混合配成母液,滴入碳酸氢铵,采用共沉淀方法合成模具及其配件陶瓷材料所需的原材料,反应生成的沉淀经滤水、干燥,煅烧得到高性能陶瓷模具及其配件材料超微粉,再经过成型、烧结、精加工,便得到高性能陶瓷模具及其配件材料。
本发明的优点是本发明制成的冷冲压模具及其配件使用寿命长,在冲压过程中未出现模具及其配件与冲压件产生粘结现象,冲压件表面光滑、无毛刺,完全可以替代传统高速钢、钨钢材料。
冷冲模具主要零件
冷冲模具是冲压加工的主要工艺装备,冲压制件就是靠上、下模具的相对运动来完成的。
加工时由于上、下模具之间不断地分合,如果操作工人的手指不断进入或停留在模具闭合区,便会对其人身安全带来严重威胁。
(一)模具的主要零件、作用及安全要求
1.工作零件凸凹模是直接使坯料成形的工作零件,因此,它是模具上的关键零件。
凸凹模不但精密而且复杂,它应满足如下要求:
(1)应有足够的强度,不能在冲压过程中断裂或破坏.
(2)对其材料及热处理应有适当要求,防止硬度太高而脆裂。
2.定位零件定位零件是确定坯件安装位置的零件,有定位销(板)、挡料销(板)、导正销、导料板、定距侧刀、侧压器等。
设计定位零件时应考虑操作方便,不应有过定位,位置要便于观察,最好采用前推定位、外廓定位和导正销定位等。
3.压料、卸料及出料零件压料零件有压边圈、压料板等。
压边圈可对拉延坯料加压边力,从而防止坯料在切向压力的作用下拱起而形成皱褶。
压料板的作用是防止坯料移动和弹跳。
顶出器、卸料板的作用是便于出件和清理废料。
它们由弹簧、橡胶和设备上的气垫推杆支撑,可上下运动,顶出件设计时应具有足够的顶出力,运动要有限位。
卸料板应尽量缩小闭合区域或在操作位置上铣出空手槽。
暴露的卸料板的四周应设有防护板,防止手指伸入或异物进入,外露表面棱角应倒钝。
4.导向零件导柱和导套是应用最广泛的一种导向零件。
其作用是保证凸凹模在冲压工作时有精确的配合间隙。
因此,导柱、导套的间隙应小于冲裁间隙。
导柱设在下模座,要保证在冲程下死点时,导柱的上端面在上模板顶面以上最少5至10毫米。
导柱应安排在远离模块和压料板的部位,使操作者的手臂不用越过导柱送取料。
5.支承及夹持零件它包括上下模板、模柄、凸凹模固定板、垫板、限位器等。
上下模板是冷冲模具的基础零件,其他各种零件都分别安装固定在上面。
模板的平面尺寸,尤其是前后方向应与制件相适应,过大或过小均不利于操作。
有些模具(落料、冲孔类模具)为了出件方便,需在模架下设垫板。
这时垫板最好与模板之间用螺钉连接在一起,两垫板的厚度应绝对相等。
垫板的间距以能出件为准,不要太大,以免模板断裂。
6.紧固零件它包括螺钉、螺母、弹簧、柱销、垫圈等,一般都采用标准件。
冷冲模具的标准件用量较多,设计选用时应保证紧固和弹性顶出的需要,避免紧固件暴露在表面操作位置上,防止碰伤人手和妨碍操作。
冷冲模具的发展
改革开放以来,随着国民经济的高速发展,市场对冷冲模具的需求量不断增长。
近年来,冷冲模具工业一直以15%左右的增长速度快速发展,冷冲模具工业企业的所有制成分也发生了巨大变化,除了国有专业模具厂外,集体、合资、独资和私营也得到了快速发展。
随着与国际接轨的脚步不断加快,市场竞争的日益加剧,人们已经越来越认识到产品质量、成本和新产品的开发能力的重要性。
而冷冲模具制造是整个链条中最基础的要素之一,冷冲模具制造技术现已成为衡量一个国家制造业水平高低的重要标志,并在很大程度上决定企业的生存空间。
近年许多冷冲模具企业加大了用于技术进步的投资力度,将技术进步视为企业发展的重要动力。
一些国内模具企业已普及了二维CAD,并陆续开始使用UG、ProEngineer、I-DEAS、Euclid-IS等国际通用软件,个别厂家还引进了Moldflow、C-Flow、DYNAFORM、Optris和MAGMASOFT等CAE软件,并成功应用于冲压模的设计中。
以汽车覆盖件模具为代表的大型冲压模具的制造技术已取得很大进步,东风汽车公司模具厂、一汽模具中心等模具厂家已能生产部分轿车覆盖件模具。
此外,许多研究机构和大专院校开展模具技术的研究和开发。
经过多年的努力,在模具CADCAECAM技术方面取得了显著进步;
在提高模具质量和缩短模具设计制造周期等方面做出了贡献。
虽然中国冷冲模具工业在过去十多年中取得了令人瞩目的发展,但许多方面与工业发达国家相比仍有较大的差距。
例如,精密加工设备在冷冲模具加工设备中的比重比较低;
CADCAECAM技术的普及率不高;
许多先进的模具技术应用不够广泛等等,致使相当一部分大型、精密、复杂和长寿命冷冲模具依赖进口。
随着科学技术的不断进步,现代工业产品的生产日益复杂与多样化,产品性能和质量也在不断提高,因而对冷冲压技术提出了更高的要求.为了使冷冲压技术能适应各工业部门的需要,冷冲压技术自身也在不断革新和发展.冷冲压技术的发展思路就是尽可能地完善和扩充冷冲压工艺的优点,克服其缺点.在冷冲压技术的发展过程中,应注意以下几方面:
(1)冷冲压技术的发展过程中应正确地确定工艺参数及冷冲模具工作部分的形状与尺寸,提高冲压件的质量、缩短新产品试制周期,应在加强冲压成形理论研究的基础上,使冲压成形理论达到能对生产实际起指导作用,逐步建立起一套密切结合生产实际的先进的工艺分析计算方法.国外已开始采用弹塑性有限元法对汽车覆盖零件的成形过程进行应力应变分析和计算机模拟,以预测某一工艺方案对零件成形的可能性和可能出现的问题。
(2)加快产品更新换代,克服模具设计周期长的缺点.应大力开展模具计算机辅助设计和制造(CADCAM)技术的研究.在我国,目前要特别注意加强多工位级进模CADCAM技术的研究。
(3)满足大量生产需要以及减轻劳动强度.应加强冷冲压生产的机械化和自动化研究,使一般中、小件能在高速压力机上采用多工位级进模生产,达到生产高度自动化,进一步提高冲压的生产率。
(4)扩大冷冲压生产的运用范围.使冷冲压既适合大量生产,也适合小批量生产;
既能生产一般精度的产品,也能生产精密零件.应注意开发如精密冲裁(特别是厚料精冲)、高能成形、软模成形、施压和超塑性加工等新成形工艺,还要推广简易模(软模和低熔点合金模)、通用组合模、数控冲床等设备的运用。
此外,对冲压板料性能的改进,模具新材料、模具新加工方法的开发也应进一步加强。
冷冲模具的使用寿命是以冲制出的工件数量来计算的。
影响冷冲模寿命的因素很多。
主要有模具结构设计、制造模具所用凸模和凹模的材料、模具的热处理质量与表面强化、冲模零件的制造精度和冷冲压材料的选取。
除此之外,还有冲模的安装、调整、使用以及维修等。
1.模具设计对寿命的影响
(1)排样设计的影响排样方法与搭边值对模具寿命的影响很大,过小的搭边值,往往是造成模具急剧磨损和凸、凹模啃伤的重要原因。
从节约材料出发,搭边值愈小愈好,但搭边值小于一定数值后,对模具寿命和剪切表面质量不利。
在冲裁中有可能被拉人模具问隙中,使零件产生毛刺,甚至损坏模具刃口,降低模具寿命。
因此,在考虑提高材料利用率的同时,必须根据零件产量、质量和寿命,确定排样方法和搭边值。
(2)凹模结构的影响对容易产生应力集中而开裂的凹模结构,可以采用组合结构或镶拼结构,以及预应力结构,从而提高模具使用寿命。
(3)间隙的影响当间隙过小时,压缩挤压利害,摩擦力增大,磨损增大,侧面的磨损加剧,冲裁后卸料和推件时,材料与凸、凹模之间的摩擦还将造成刃口侧面的磨损比端面的磨大大,同时也容易造成凸、凹模温度很高,把金属碎屑吸附在刃口侧面,形成金属瘤,使凸、凹模出现崩刃或胀裂现象。
因此,过小的间隙对模具寿命极为不利。
间隙太大,会增加凸模与凹模端面边缘的集中应力,致使压应力急剧增加,于是刃口边很快屈服变形而失去棱角。
因此又增加了冲裁力,进而使刃口边更快磨损,降低模具寿命。
但为了减小凸、凹模的磨损,延长模具使用寿命,在保证冲裁件质量的前提下,设计时适当采用较大间隙是十分必要的。
(4)模具导向结构对寿命的影响可靠的导向对于减小工作零件的磨损,避免凸、凹模啃伤是非常有效的。
特别对无问隙或小问隙冲裁模、复合模和多工位级进模更为重要。
为提高模具寿命,必须根据工序和零件精度要求,正确选择导向形式和导向精度,所选择导向精度应高于凸、凹模的配合精度。
(5)冷冲压材料选取的影响冷冲压材料应满足制件的设计要求和冲压工艺要求,否则容易损伤模具,降低模具使用寿命。
冷冲压材料表面质量不好,冲压时制件易破裂,也易擦伤模具。
冷冲压材料塑性不好,变形量小,冲压时制件易破裂,也易擦伤模具。
另外,材料的厚度公差应符合国家标准。
因为一副冲模适用于一定材料的厚度,成形、弯曲、翻边、引伸模具的凸、凹模结构间隙是直接根据材料厚度来确定的。
所以材料厚度不均匀,会导致废品产生和模具损坏。
2.模具材料对模具寿命的影响
模具材料对模具寿命的影响是模具材料性质、化学成分、组织结构、硬度和冶金质量等的综合反映。
其中,材料性质和热处理质量影响最为明显。
模具材料性质对模具寿命的影响是很大的。
如将同一种工件,使用不同的模具材料做弯曲试验,试验结果:
用9Mn2V材料,其寿命为5万次;
用Crl2MoV渗氮,其寿命可达40万次。
因此,在选用材料时,应根据制件的批量大小,合理选用模具材料。
模具工作零件的硬度对模具寿命的影响也很大。
但并不是硬度愈高、模具寿命愈长。
这是因为硬度与强度、韧性及耐磨性等有密切的关系。
有的冲模要求硬度高,寿命长。
如采用T10钢制造冲模,硬度为54~58HRC,只冲几千次,制件毛刺就很大。
如果将硬度提高到60~64HRC,则刃磨寿命可达2~3万次。
但如果继续提高硬度,则会出现早期断裂。
有的冲模硬度不宜过高,如采用Crl2MoV制造凹模硬度为58~62HRC时,一般寿命为2—3万件,失效形式是崩刃和开裂以及如果将硬度降到54~58HRC,寿命提高到5~6万件,但硬度降低到50~53HRC会出现凹模刃口易磨钝现象。
由此可见,模具硬度必须根据材料性质和失效形式而定。
应使硬度、强度、韧性及耐磨性、耐疲劳强度等达到特定冲压工序所需要的最佳配合。
3.模具的热处理质量与表面强化对寿命的影响
模具的热处理