外文翻译混合压电致动式微型阀Word格式.docx
《外文翻译混合压电致动式微型阀Word格式.docx》由会员分享,可在线阅读,更多相关《外文翻译混合压电致动式微型阀Word格式.docx(18页珍藏版)》请在冰豆网上搜索。
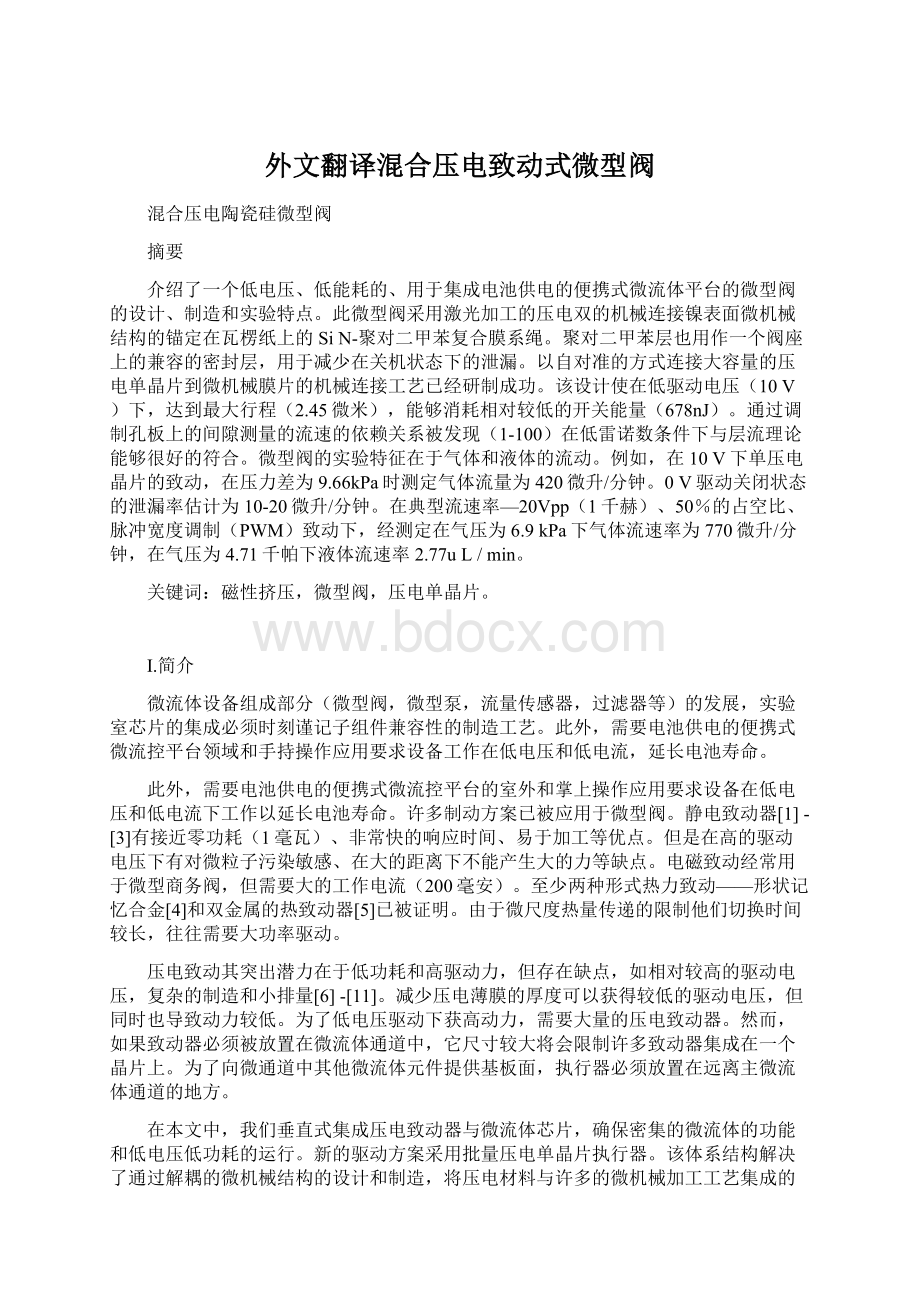
关键词:
磁性挤压,微型阀,压电单晶片。
I.简介
微流体设备组成部分(微型阀,微型泵,流量传感器,过滤器等)的发展,实验室芯片的集成必须时刻谨记子组件兼容性的制造工艺。
此外,需要电池供电的便携式微流控平台领域和手持操作应用要求设备工作在低电压和低电流,延长电池寿命。
此外,需要电池供电的便携式微流控平台的室外和掌上操作应用要求设备在低电压和低电流下工作以延长电池寿命。
许多制动方案已被应用于微型阀。
静电致动器[1]-[3]有接近零功耗(1毫瓦)、非常快的响应时间、易于加工等优点。
但是在高的驱动电压下有对微粒子污染敏感、在大的距离下不能产生大的力等缺点。
电磁致动经常用于微型商务阀,但需要大的工作电流(200毫安)。
至少两种形式热力致动——形状记忆合金[4]和双金属的热致动器[5]已被证明。
由于微尺度热量传递的限制他们切换时间较长,往往需要大功率驱动。
压电致动其突出潜力在于低功耗和高驱动力,但存在缺点,如相对较高的驱动电压,复杂的制造和小排量[6]-[11]。
减少压电薄膜的厚度可以获得较低的驱动电压,但同时也导致动力较低。
为了低电压驱动下获高动力,需要大量的压电致动器。
然而,如果致动器必须被放置在微流体通道中,它尺寸较大将会限制许多致动器集成在一个晶片上。
为了向微通道中其他微流体元件提供基板面,执行器必须放置在远离主微流体通道的地方。
在本文中,我们垂直式集成压电致动器与微流体芯片,确保密集的微流体的功能和低电压低功耗的运行。
新的驱动方案采用批量压电单晶片执行器。
该体系结构解决了通过解耦的微机械结构的设计和制造,将压电材料与许多的微机械加工工艺集成的挑战,在这种情况下,该压电双是激光机械加工的,并连接到微型设备上。
铁-环氧支柱从压电单晶片延伸到复合膜上,而Si-N聚对二甲苯复合膜又是与阀帽相连接的。
Si-N复合膜上的聚对二甲苯层能达到增加氮化物层机械强度、通过增加机械顺从性(力顺)减少流体泄漏的双重目的。
该压电单晶片致动器的位移取决于与驱动器上的电压呈线性关系,也与单压电晶片刚度成反比,呈现为致动器尺寸与工作电压折衷考虑的一种设计。
在这项工作中,制作矩形压电双以保持低的工作电压(0-10V)。
比较大的致动器被粘结在硅晶片的背面,因此,所有的硅表面区域仍然可用于其他微流体组件的制造(例如,流量传感器,反应室等)。
例如,一个过程和力量兼容的流量传感器[12]可以被集成为闭合环路流量控制。
此工艺流程(设备自动化系统)也是一个低温工艺过程(温度小于等于150°
C),使后-CMOS工艺的晶片上微细加工成为可能,可以方便地与电子产品集成。
本文的结构安排如下。
第II节叙述微型阀的操作原理,第三节分析单层压电致动器。
阀板、压电致动器和自对准装配工艺的制造工艺在第IV节讨论。
第五部分为试验结果与讨论。
II、操作原理
图1(a)表示的是微型阀原理图的3D视图。
微型阀的主要组成部分包括压电致动器和微加工的硅晶片,首尾相连的磁挤压铁环氧支柱。
微型阀通过驱动音叉形的压电单压电晶片致动器以提供纵向位移来实现。
此位移通过机械联动装置被转移到镍阀帽,从而调节批量蚀刻的阀孔上的间隙。
这将导致在调制中的流体流动,雷诺数流较低时(1-100)流速与孔口间隙的立方成正比,如[13]、[14]。
音叉形状的设计保证了致动力均匀地施加在镍帽的两端。
压花的SU-8模具被用来定义在聚二甲基硅氧烷(PDMS)帽中的通道,然后将其在硅的上表面上缩放,以形成微流体通道。
就加工步骤而言,不增加成本的情况下过滤器的额外功能可以被纳入微型阀。
可以在孔口中的硅氮层蚀刻出孔眼,起到过滤器筛的作用。
电镀镍阀门帽的尺寸已经选择了,所以盖既不能太薄要允许弯曲,也不能太厚以至于存在残余应力。
厚度大于75微米时,可以观察到相当大的应力诱发的弯曲,薄层厚度小于25微米时则很容易弯曲。
选择一个最佳的厚度--50微米,因为它可以获得我们可接受的刚度和残余弯曲。
选择该锚定区域(直径350微米),是为了适应的后面将要描述的支柱生长过程的对准公差。
选择致动器的尺寸为(2毫米X20毫米,250微米厚的PZT,40微米厚的镍)是为了使位移和阻滞力达到最大值的同时保持操作电压小于10V。
聚对二甲苯膜,既作为阀门的系链又作为镍帽锚,如图1(b)所示呈波纹状(5微米深,20微米的间距)是为了降低它的刚度。
结果发现,如图2(b)系链只有释放过程容易断裂。
因此,如图2(a)所示加入一层聚对二甲苯,可以使屈服率增加至90%。
聚对二甲苯层的厚度被选择为3微米,为了使复合系链机械强度抵抗硅氮薄膜断裂用复合膜,释放过程中往往会导致聚对二甲苯层的剥离,并攻击的聚对二甲苯-硅界面的释放剂(丙酮)。
如图1(b)所示,这个问题已经通过使用保护环锚使聚对二甲苯定位来解决了。
III.单晶片促动分析
在下文中,将介绍对压电单晶片致动的分析。
对致动器尺寸和驱动电压之间的权衡进行了讨论。
如图3所示,为一个矩形压电单晶片致动器的驱动。
它包括一个单一的压电材料层[铅钛酸锆氧化物陶瓷(PZT)],且压电材料层的一侧电镀了一层弹性层(镍)。
沿压电体层厚度方向施加的电压导致了纵向和横向的应变。
弹性层相对的横向应变,导致了复合梁的弯曲变形。
我们分别考虑了一个空载悬臂单压晶片致动器的长度L和宽度W、弹性层和压电层的厚度Hni和Hp、弹性柔度s1和s2、密度1和2。
对于压电材料的横向压电耦合系数d31:
尖端位移、梁的刚度k、阻滞力F、基波谐振频率f、致动电压V式[15]中已给出。
对于我们的设计,PZT[16]和镍层的密度和杨氏模量(E=1/S11)分别是7450Kg/m,63GPaand8900Kg/m,150GPa。
PZT的横向压电耦合系数和介电常数分别采取-262×
10-12coulomb/N,3450。
对于上面所示的PZT的几何参数,镍层的最佳厚度的计算为40微米。
优化是通过最大限度的提高尖端位移实现的,这取决于如图4所示的弹性层厚度。
同时最大限度地减少电镀处理产生的残余应力(及因此导致的单压电晶片致动器的变形),该残余应力随着镍层的厚度增加而增加。
这种设计预计在致动电压10V的条件下将产生9.17微米的位移。
利用式(4),悬臂结构的基本谐振频率计算结果是432赫兹。
由膜的系绳和镍阀帽加载的致动器的谐振频率,可以通过将膜看作一个弹簧同时忽略膜和镍阀帽群的质量来进行建模计算。
开关能量可以通过考虑切换后存储在压电致动器的内部能量来计算。
该压电致动器以机械和介电能源的形式存储能量,这中能量可以通过存储在静态夹持电容Cp中的能量封装起来,按照如下公式
此公式中,其中Cb是阻断电容其中,定义为压电材料应变为零时的电容,及压电材料横向方向上的机电耦合系数。
对于所选的PZT致动器设计,Cb预计是11.6nF的。
鉴于生产商列出的系数k31的值为0.38,静态夹持电容的预期值计算为13.56nF。
致动电压为10V时预期的开关能量计算为678毫焦。
对于给定激励频率的功耗,倘若2лfCR<
<
1,可以通过开关能量和损耗角正切tanδ计算出,如
鉴于列出的损耗角正切值为0.02,在1千赫条件下,10V电压致动时,功率消耗预期值计算为85.15微瓦。
IV.制造和装配
制造工艺采用模块化是因为硅结构和压电致动器是分开制造的。
在最后步骤中,使用铁-环氧树脂支柱将他们组装在一起。
各个模块及其装配过程的制造工艺介绍如下。
A.PZT单层压电致动器
一个250微米厚的极化的1英寸方形的PZT晶片,只在一面电镀40微米厚的镍层,并使用低应力的电镀配方(Technic股份有限公司的镍溶液方案)。
晶片使用1.5-W355nm的二极管激光(Coherent公司的AVIA355-1500),通过消融切割,激光加工成双悬臂形状。
每个致动器的切割过程需要41分钟,由于是非热能的烧蚀切割并没有对压电陶瓷去极化。
如后面所述,铁-环氧树脂支柱是磁力挤压成型的,在悬臂的前端也用激光切割一个直径200-400um的小孔。
B.阀板的制作
阀板焊接在的硅晶片(100)上。
图5显示了主要的制造步骤。
制造开始以硅的反应离子蚀刻(RIE),形成5微米深,宽20微米的槽(如图6(a)),作为随后要沉积的层的模具。
保护环的宽7微米、深30微米的沟槽(图1(b))使用深度反应离子蚀刻技术(DRIE)进行蚀刻,以防止兼容的聚对二甲苯的层在最后释放过程剥离,而是随后沉积下来。
一个700nm厚的LPCVD(低压化学气相沉积)SixNy层被沉积下来[见图5(a)]。
一个反应离子刻蚀(RIE)的步骤常常是,在所沉积的氮化物前侧进行蚀刻来界定进气孔。
如图6(d)所示,进气口可设计为一个有过滤器的筛。
接着,在前侧沉积1.5微米厚的PECVD(低温沉积技术、等离子体增强化学汽相沉积)氧化物,KOH蚀刻即终止。
然后使用反应离子刻蚀工序,在背面上模式化,以定义窗口体型微机械加工[参照图5(b)]。
一个3微米厚的聚对二甲苯层,使用氧等离子体的反应离子刻蚀RIE界定阀座和镍质量的锚定,然后沉积和模式化,[参照图5(C)]。
接着,一个5微米厚的光阻材料层进行纺丝,作为镍阀帽下的待除层。
一个50nm厚的钛膜沉积,随后200nm的铜作为电镀镍的籽晶层。
然后通过一个70微米厚的AZ4903光致抗蚀剂层旋转形成一个电镀模具,并模式化来定义阀帽(如图5(d))。
使用低应力配方电镀一个50微米厚的镍层。
使用一个同步的KOH蚀刻步骤,通过蚀刻硅体释放该膜系链,并且由一个单面蚀刻夹具保护前侧不被KOH腐蚀。
前侧上的PECVD氧化物作为刻蚀阻挡,防止KOH进入腔室壳体的前侧。
此氧化物层通过湿法蚀刻(6:
1BOE)得到,且电镀模具被剥离得到最终的阀板[参照图。
5(e)]。
对于界定微流体通道的PDMS盖的制造,一个模具形成首先通过在基底的硅晶片上模块化一个75微米厚的SU-8层。
注入PDMS(SYLGARD184有机硅弹性体)混合物,并在85℃下固化10分钟。
硬化的帽从模具上被剥离,并安放到阀板上形成微流体通道。
对于氮化物,只要避免表面有尘埃颗粒,(聚二甲基硅氧烷)PDMS盖的粘附性可认为是良好的。
C.经铁环氧支柱,执行器与阀板组合件
图7(a)和(b)所示为微型阀的组装顺序。
硅晶片首先切成成10毫米乘30毫米的小方块。
如图7(a)所示,黄铜垫圈连接在进口和出口端,对齐单压电晶片悬臂梁中心的孔和膜的中心后,(使用超强力胶水层)将压电单晶片悬臂梁接合到硅芯片的背面上。
对准方式并不需要精确,因为支柱可以补偿的任何错位。
如下文所述的铁-环氧树脂支柱,然后生长。
磁性铁-环氧树脂(301环氧树脂和古德费洛EpoTek直径为6微米的铁粒子的4:
1的