外壳塑料零件模具设计说明书Word文档格式.docx
《外壳塑料零件模具设计说明书Word文档格式.docx》由会员分享,可在线阅读,更多相关《外壳塑料零件模具设计说明书Word文档格式.docx(22页珍藏版)》请在冰豆网上搜索。
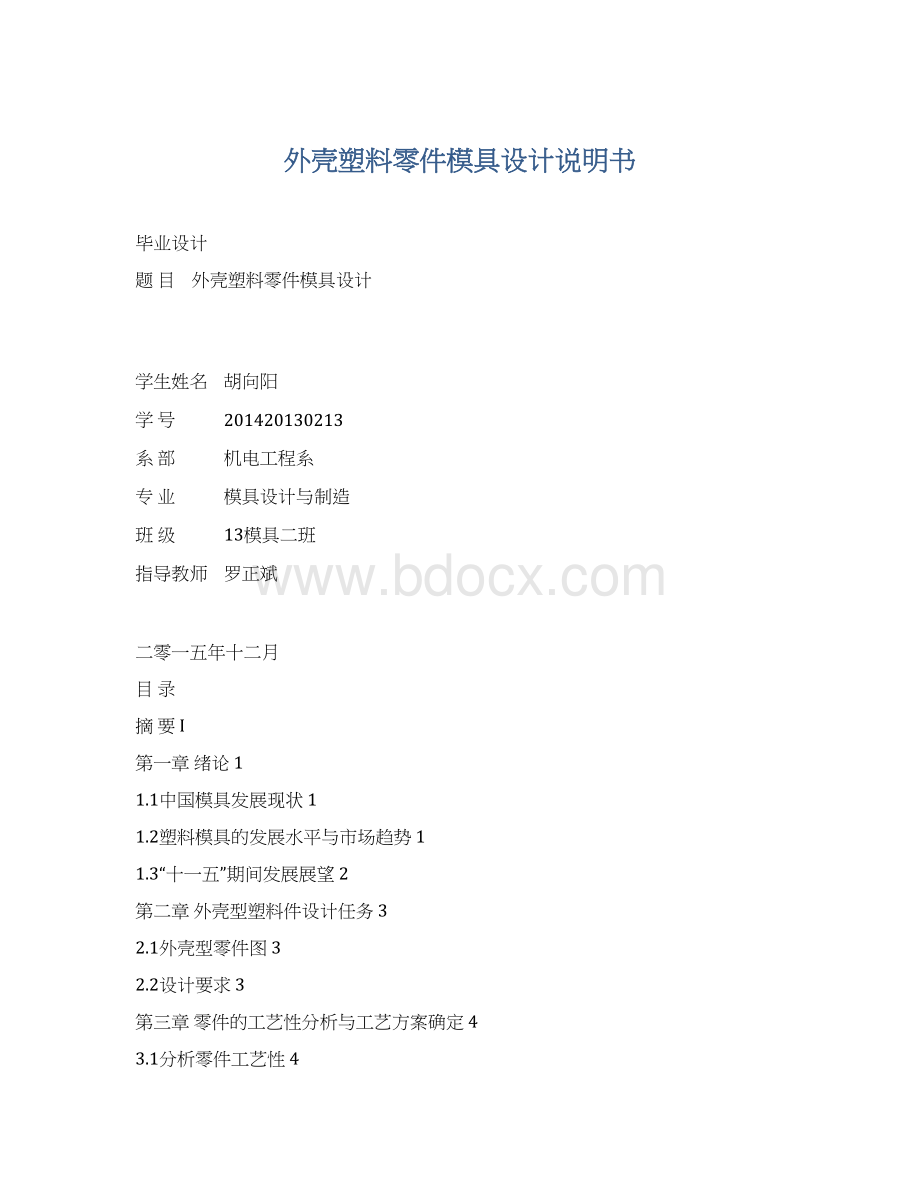
摘要I
第一章绪论1
1.1中国模具发展现状1
1.2塑料模具的发展水平与市场趋势1
1.3“十一五”期间发展展望2
第二章外壳型塑料件设计任务3
2.1外壳型零件图3
2.2设计要求3
第三章零件的工艺性分析与工艺方案确定4
3.1分析零件工艺性4
3.1.1塑件选用材料分析及工艺特性4
3.1.2分析塑件的结构工艺性5
3.2确定工艺方案5
3.2.1拟定模具结构形式5
3.2.2分型面的确定6
第四章塑料模具的设计7
4.1确定注射机的型号7
4.1.1塑件体积计算7
4.1.2注射机型号的确定8
4.1.3注射量的校核8
4.1.4锁模力的校核8
4.1.5开模行程校核9
4.2模架设计9
4.2.1型腔数目的确定模架尺寸9
4.2.2型腔尺寸的分析9
4.3模具结构与设计10
4.3.1、主流道、分流道设计:
10
4.3.2、分流道的布置11
4.3.3、冷料穴和拉料杆的设计11
4.4支撑零部件的设计12
4.4.1支承板设计12
4.4.2垫块设计12
4.4.3定模座板、动模座板的设计12
4.5成型零部件设计12
4.5.1成型零件工作尺寸的计算12
4.5.2成型零部件的强度与刚度计算15
4.6推出机构设计16
4.6.1采用推杆推出16
4.6.2推杆位置的选择16
4.7合模导向机构设计16
4.7.1导柱的设计16
4.7.2推杆的设计17
4.7.3复位杆的设计17
4.8温度调节系统18
第五章总结与展望19
致谢20
摘要
随着现代工业发展的需要,塑料制品在工业、农业和日常生活等各个领域的应用越来越广泛,质量要求也越来越高。
在塑料制品的生产中,高质量的模具设计、先进的模具制造设备、合理的加工工艺、优质的模具材料和现代化的成型设备等都是成形优质塑件的重要条件。
本设计通过对壳型塑料件工艺的正确分析,完成一副一模两腔的塑料模具设计。
详细地完成模具成型零件包括垫块、复位杆、浇口套、拉料杆、上模座、推板等的设计,重要零件的工艺参数的选择与计算,推出机构与浇注系统以及其它结构的设计过程,并对产品的制作过程作了介绍。
第一章绪论
1.1中国模具发展现状
中国的塑料模具虽然在数量、质量、技术等方面都有了很大进步,但与国民经济发展需求、世界先进水平相比,差距仍很大。
一些大型、精密、复杂、长寿命的中高档塑料模具每年仍需大量进口。
目前国内一些中、低档塑料模具供过于求,市场竞争激烈。
近几年,国产塑料模具国内市场满足率一直不足74%,其中大型、精密、长寿命模具满足率更低,估计不足60%。
同时,工业发达国家的模具正在加速向中国转移,国际采购越来越多,国际市场前景看好。
市场需求旺盛,生产发展一时还难以跟上,供不应求的局面还将持续一段时间。
1.2塑料模具的发展水平与市场趋势
近年来,中国塑料模具制造水平已有较大提高。
大型塑料模具已能生产单套重量达到50t以上的注塑模,精密塑料模具的精度已达到2μm,制件精度很高的小模数齿轮模具及达到高光学要求的车灯模具等也已能生产,多腔塑料模具已能生产一模7800腔的塑封模,高速模具方面已能生产挤出速度达6m/min以上的高速塑料异型材挤出模具及主型材双腔共挤、双色共挤、软硬共挤、后共挤、再生料共挤出和低发泡钢塑共挤等各种模具。
在生产手段上,模具企业设备数控化率已有较大提高,CAD/CAE/CAM技术的应用面已大为扩展,高速加工及RP/RT等先进技术的采用已越来越多,模具标准件使用覆盖率及模具商品化率都有较大幅度的提高,热流道模具的比例也有较大提高。
另外,三资企业的蓬勃发展进一步促进了塑料模具设计制造水平及企业管理水平的提高,有些企业已实现信息化管理和全数字化无图制造。
模具的制造正在从过去主要依靠钳工的技艺转变为主要依靠技术。
这不仅是生产手段的转变,也是生产方式的转变和观念的上升。
这一趋势使得模具的标准化程度不断提高,模具精度越来越高,生产周期越来越短,钳工比例越来越低,最终促进了模具工业整体水平不断提高。
中国模具行业目前已有10多个国家级高新技术企业,约200个省市级高新技术企业。
与此趋势相适应,生产模具的主要骨干力量从技艺型人才逐渐转变为技术型人才是必然要求。
当然,目前及相当长一段时间内,技艺型人才仍十分重要,因为模具毕竟难以完全摆脱对技艺的依靠。
发达工业国家的模具正加速向中国转移,其表现方式为:
一是迁厂,二是投资,三是采购。
中国的模具企业应抓住机遇,借用并学习国外先进技术,加快自己的发展步伐。
1.3“十一五”期间发展展望
展望未来,下列几方面发展趋势预计会在行业中得到较快应用和推广。
(1)超大型、超精密、长寿命、高效模具将得到发展。
(2)多种材质、多种颜色、多层多腔、多种成型方法一体化的模具将得到发展。
(3)为各种快速经济模具,特别是与快速成型技术相结合的RP/RT技术将得到快速发展。
(4)模具设计、加工及各种管理将向数字化、信息化方向发展CAD/CAE/CAM/CAPP及PDM/PLM/ERP等将向智慧化、集成化和网络化方向发展。
(5)更高速、更高精度、更加智慧化的各种模具加工设备将进一步得到发展和推广应用。
(6)更高性能及满足特殊用途的模具新材料将会不断发展,随之将产生一些特殊的和更为先进的加工方法。
(7)各种模具型腔表面处理技术,如涂覆、修补、研磨和抛光等新工艺也会不断得到发展。
(8)逆向工程、并行工程、复合加工乃至虚拟技术将进一步得到发展。
(9)热流道技术将会迅速发展,气辅和其它注射成型工艺及模具也将会有所发展。
(10)模具标准化程度将不断提高。
(11)在可持续发展和绿色产品被日益重视的今天,“绿色模具”的概念已逐渐被提到议事日程上来。
第二章毕业设计任务——外壳塑件的模具设计
2.1外壳塑件的模具设计
外壳型零件如图2-1所示
图2-1外壳型零件
1.塑件材料为ABS,平均收缩率为0.75%。
2.5万件。
3.未注公差取MT5级精度。
第三章零件的工艺性分析与工艺方案确定
3.1分析零件工艺性
图3-外壳型零件
图3-1所示零件为壳型零件,对外观面的要求较高,且在装配时所需要的尺寸要求也较高,对内部面的要求一般,尺寸也一般。
对照客户给出的塑件产品图,分析产品要求后选取材料,通过了解产品的用途,可以知道,它对耐老化,抗纵向弯曲强度和耐磨性等要求较高,而且还必须具有良好的回弹性,抗切割性。
所制成的成品外观光洁度,平滑度也具有很高的要求。
3.1.1塑件选用材料分析及工艺特性
该材料为丙烯腈-丁二烯-苯乙烯共聚物(ABS)
基本特征:
ABS是由丙烯腈、丁二烯、苯乙烯共聚而成的。
这三种组分各自的特性,使ABS具有良好的综合力学性能。
丙烯腈使ABS有良好的耐化学腐蚀及表面硬度,丁二烯使ABS坚韧,苯乙烯使它有良好的加工性和染色性能。
ABS无毒、无味、呈微黄色,成型的塑料有较的光泽。
密度为0.9~0.23g/cm。
ABS有极好的抗冲击强度,且在低温下也在不迅速下降。
ABS有良好的机械强度和一定的耐磨性、耐寒性、耐油性、耐水性、化学稳定性和电气性能。
水、无机盐类对ABS几乎无影响,但在酮、醛、酯、中会溶解或形成乳浊液。
ABS不溶于大部分醇类,ABS塑料表面受冰醋酸、植物油等化学药品引起开裂。
ABS有一定的硬度和尺寸稳定性,易于成型加工,经过调色可配成任何颜色。
ABS的缺点就是耐热性不高,连续工作温度为70℃左右,热变形温度93℃左右,且耐气候性差,在紫外线作用先易变硬发脆。
塑料件性能:
(1)力学性能:
屈服强度为50Mpa、拉伸强度38Mpa、断裂伸长率35%、拉伸弹性模量1.8、弯曲弹性模量1.4、弯曲强度80Mpa、布氏硬度9.7HBS、密度1.02—1.16g/cm3、比体积1.02—1.16、吸水性0.2—0.4、熔点130—160℃。
3.1.2分析塑件的结构工艺性
塑件相对一般塑料件较大,其整体结构简单,尺寸测量方便,符合一般塑件的设计要求,主要设计特征是内外抽芯机构。
3.2确定工艺方案
3.2.1拟定模具结构形式
1.一模两腔
由于该产品为大批量生产,所以产用多型腔模具更为适合,可以提高生产效率,降低塑件的整体成本。
型腔数量的确定:
一种方法是首先确定注射机的型号,根据注射机的技术参数和塑件的技术经济要求,另一种方法是根据生产效率的要求和制件的精度要求确定型腔的数目。
按注射机的最大注射量确定型腔的数目。
n<
(kmp—m1)/m
k~注射机的最大注射量的利用系数,一般取0.8
mp~注射机最大注射量,g
m1~浇注系统凝料量,g
m~单个塑件的质量,g
经过计算和壳型零件的分析而确认
型腔的分布:
由于型腔的排布与浇注系统密切相关的,所以在模具设计时应该综合加以考虑,型腔的排布应使每个型腔都能通过浇注系统从总压力中均等地分得所需要的足够压力,以保证塑料熔体能同时均匀的充填每个型腔。
所以用平衡式布置。
2.模具结构形式的确定
根据产品的要求和模具成本的计算等,决定用阴影曲面做分型面,采用合理的模具结构进行设计
3.2.2分型面的确定
选择分型面时,应有几项基本原则:
1.分型面应选在塑件外形最大轮廓处
2.分型面的选择应有利于塑件的顺利脱模
3.分型面的选择应满足塑件的外观面的要求
4.分型面的选择应要便于模具的加工制造
5.分型面的选择应有利于排气
最终采用阴影曲面做分形面,复合以上五点要求。
第四章塑料模具的设计
4.1确定注射机的型号
根据塑料件的体积及主流道、分流道的容量来确定注射机的型号。
图4-1壳型零件
4.1.1塑件体积计算
根据ProEWildfire4.0自带的测量工具测得该塑件的体积是:
47.123cm3
塑件重量为:
GS=V﹒r
=47.123x1.2g=57g
式中r为塑料容重(ABS的容种r=1.2g/cm3)
根据塑件的计算重量或体积,选择设备型号规格,确定型腔数当未限定设备时,须考虑以下因素:
机额定注射量GB,每次注射量不超过最大注射量的80%
即n=(0.8GB-Gj)/GS式中n—型腔数
Gj—浇注系统重量(g)
GS—塑件重量(g)
GB—注射机额定射量(g)
浇注系统估算结果:
Vj=6.2x(0.5/2)2π+12x(0.2/2)2π+2x9x(0.2/2)2π
=1.85cm3
设n=2则得
GB=(nGS+Gj)/0.8
=(2x57+1.85x1.2)/0.8g
=145.28g
从计算结果,并根据塑料注射机技术规格表查表,还根据塑件精度,因为该塑件精度一般,故采用一模两腔,即n=2
所以生产批量该塑件属大批量生产,故选了一模两腔。
4.1.2注射机型号的确定
根据塑件注射量大小故选择注射机额定注射量125㎝3;
型号为XS-ZY-125。
注射机的规格和性能:
额定注射量125cm3、注塞直径42mm、注射压力120Mpa、注射方式:
螺杆式、锁模力900KN、最大开合模行程300mm、模具最大厚度300mm、喷嘴孔圆弧半径12mm、喷嘴孔的直径4mm
4.1.3注射量的校核
根据塑件注射量大小来选择额定注