压铸机的工作原理与本体结构Word下载.docx
《压铸机的工作原理与本体结构Word下载.docx》由会员分享,可在线阅读,更多相关《压铸机的工作原理与本体结构Word下载.docx(12页珍藏版)》请在冰豆网上搜索。
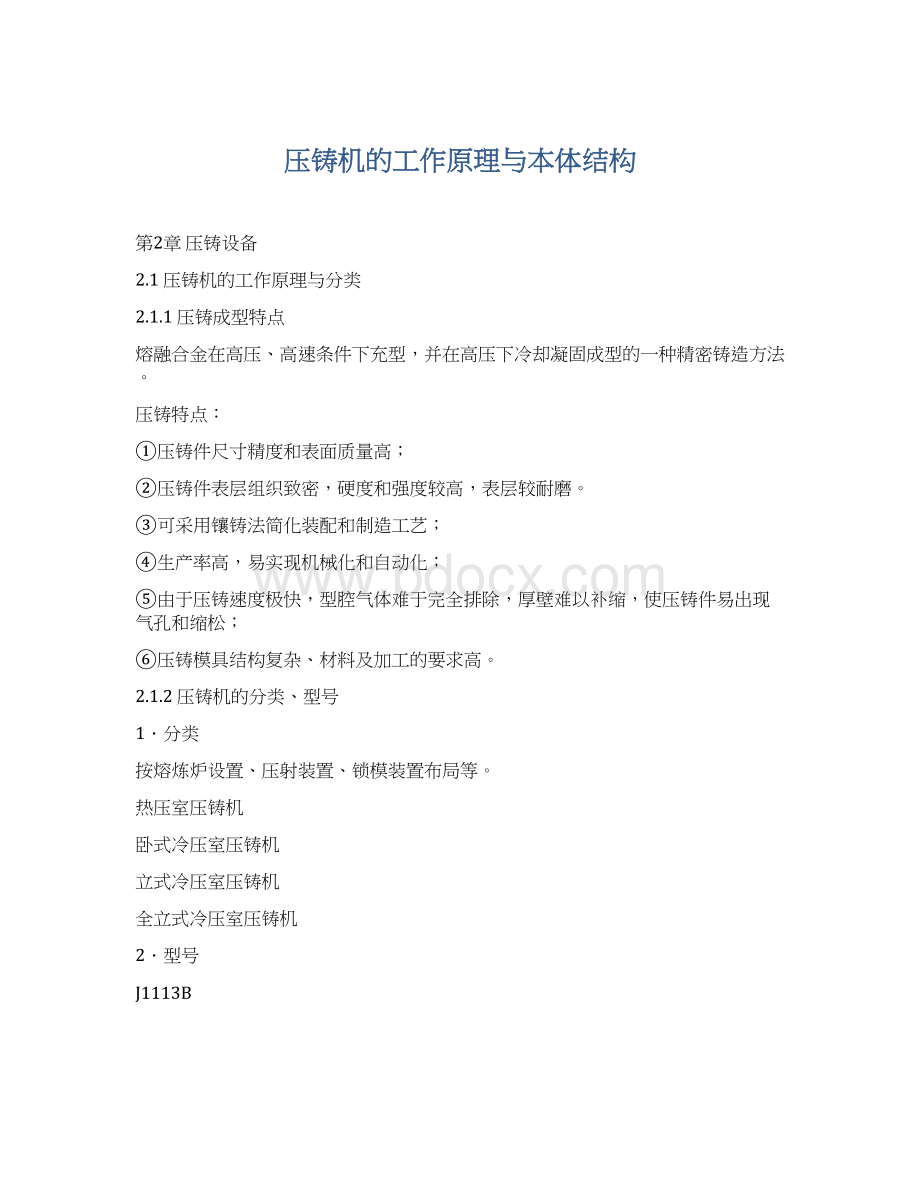
型号后的字母表示第几次改型设计。
2.1.3压铸机的工作原理
2.1.3.1热压室压铸机
热压室压铸机工作原理图
1-动模;
2-定模;
3-喷嘴;
4-压射冲头;
5-压室;
6-坩埚
a-压室通道;
b-鹅颈嘴;
c-鹅颈通道
压射部分与金属熔化部分连为一体,并浸在金属液中。
鹅颈嘴b的高度应比坩埚内金属液最高液面略高,使金属液不致自行流入模腔。
模具闭合。
压射时,冲头向下封住通道a时,压室、鹅颈通道、模腔构成密闭系统。
冲头以一定的推力和速度将金属液压入模腔,充满型腔并保压适当时间后,冲头提升复位。
2.1.3.2立式冷压室压铸机
锁模部分呈水平设置,负责模具的开、合及压铸件的顶出。
压射部分呈垂直设置,压室与金属熔炉分开。
压铸时,模具闭合,舀取一定金属液倒入压室,反料冲头应上升堵住浇道b,以防金属液自行流入模腔。
当压射冲头下降接触金属液时,返料冲头随压射冲头下移,使压射室与模具浇道相通,金属液迅速充满模腔a。
冷却后,压射冲头上升复位,反料冲头往上移动,切断余料e并将其顶出压室,接着开模顶出压铸件。
立式冷压室压铸机工作原理图
a)合模;
b)压射;
c)开模、取件
3-压射冲头;
4-压室;
5-反料冲头
a-模腔;
b-浇道;
c-金属液;
d-压铸件;
e-余料
2.1.3.3卧式冷压室压铸机
压室与熔炉分开设置,压室水平布置,并可从锁模中心向下偏移一定距离。
压铸时,金属液c注入压室→冲头向前压射→金属液经内浇道a压射入模腔b→保压冷却→开模,同时,冲头继续前推,将余料e推出压室,让余料随动模1移动,压射冲头复位。
动模开模结束、顶出压铸件d,再合模。
卧式冷压室压铸机工作原理图
3-压室;
a-内浇道;
b-模腔;
2.1.3.4全立式冷压室压铸机
(1)压射冲头上压式压铸机
金属液2倒入压室3,模具闭合,压射冲头1上压,金属液经浇注系统进入模腔6,冷却后开模,冲头继续上升,推动余料7随铸件移动,通过模具顶出机构顶出压铸件及浇注系统,同时,冲头复位。
全立式冷压室(上压式)压铸机工作原理图
a)浇注金属液;
b)合模、压射;
c)开模、顶出铸件
1-压射冲头;
2-金属液;
4-定模;
5-动模;
6-模腔;
7-余料
(2)压射冲头下压式压铸机
模具闭合后,金属液3浇入压室2,反料冲头在弹簧5作用下上升封住横浇道6,压射冲头1下压时,迫使反料冲头后退,金属液经浇道进入模腔,冷却后开模,冲头复位。
顶出机构顶出铸件及浇注系统凝料。
推出机构复位后,反料冲头在弹簧作用下复位。
全立式冷压室(下压式)压铸机工作过程
a)合模、浇注金属液;
b)压射成型;
2-压室;
3-金属液;
4-反料冲头;
5-弹簧;
6-横浇道
2.2压铸机的本体结构
2.2.1压铸机的结构形式及特点
基本结构:
合模机构、压射机构、机座、动力部分、液压与电气控制系统、其它辅助装置。
合金熔炉、保温炉。
2.2.1.1热压室压铸机
熔炼、保温与压射装置构成机床的铸料系统。
压射装置浸没于金属液中,结构紧凑。
锁模装置类似于塑料注射机。
配有数字式温控和可编程控制系统,可选配自动取件机械手、抽芯装置等附件。
多为中小型机,易实现自动化,生产率高,金属消耗量少。
但压射构件易被浸蚀,也影响合金纯度。
多用于铅、锡、锌等铸件。
PLC控制热压室压铸机
1-电气控制柜;
2-合模部分;
3-取件机械手;
4-压射装置;
5-增压蓄能器;
6-合金熔炉;
7-集中冷却装置;
8-操作面板;
9-床身;
10-手动润滑泵
2.2.1.2卧式冷压室压铸机
压射装置和锁模装置呈水平分布,压射装置由压室和压射冲头组成,并可根据模具浇注系统需要向下偏移一定距离。
锁模装置与卧式塑料注射机相似。
压室工作条件比热压室好,可采用大吨位卧式压射缸,适于中大型压铸机。
可用于铝合金、镁合金、铜合金及黑色金属。
J1116型卧式冷压室压铸机
2-液压系统;
3-锁模装置;
4-操作面板;
5-压射装置;
6-取料机械手;
7-快速压射蓄能器;
8-增压蓄能器;
10-自动润滑系统
2.2.1.3立式冷压室压铸机
压射装置呈垂直分布,由压室、压射冲头、反料冲头组成,进料口在机床模板中心处。
锁模装置水平分布,结构与卧式冷压室压铸机相同。
占地面积小。
杂质上浮、压射时不易进入模腔,有利于提高铸件质量。
模具模腔可沿中心对称布置,使模具压力中心与压铸机锁模中心重合,便于压铸具有中心浇口的铸件。
多了一组余料切除装置,生产率较前二者低,金属液压力损失大。
可用于锌、铝、镁、铜合金压铸件。
2.2.1.4全立式冷压室压铸机
压射装置和锁模装置均呈垂直分布,总体结构类似于四柱液压机。
按压射冲头运动方向的不同可分为上压式和下压式。
特点:
模具水平放置,稳固可靠,安放嵌件方便,广泛用于压铸电动机转子类零件;
金属液进入模腔转折少,流程短,减少了压力和热量损失;
但高度大,铸件顶出后常需人工取出,不易实现自动化。
2.2.2压铸机的主要机构示例
2.2.2.1压射装置
达到工艺要求的压射比压和压射速度,且压射速度、压射力、压力建立时间等方便可调。
(1)增压缸有背压的压射装置
压射增压机构
1-压室;
2-压射冲头;
3-冷却水通道;
4-压射杆;
5-活塞杆;
6-压射缸;
7-压力表;
8-分油器;
9-节流阀杆;
10-弹簧;
11-背压腔;
12-增压活塞;
13-单向阀阀芯;
14-油孔;
15-调节螺杆;
16-压射支架;
17-升降器
由带缓冲器的普通液压缸和增压器组成,联合实现分级压射,具有两种速度和一次增压压射的机构。
第一级压射:
压力油经油孔14进入,由于背压腔11有背压,增压活塞12不能前移,压力油经单向阀进入压射缸后腔,汇集在缓冲杆周围的分油器8中,由于节流阀杆9的作用,只有很小流量的压力油从分油器的中心孔进入,作用在压射活塞的缓冲杆端部截面上,作用力也很小,因而压射活塞慢速前进,进行慢速压射,压射冲头2缓慢地封闭压室1注液口,以免金属液溢出,同时,有利于压室空气排出、减少气体卷入。
第二级压射:
当压射冲头越过注液口,大流量压力油进入压射缸,推动压射活塞快速前进,实现快速压射充模。
第三级压射:
金属液充满模腔,压射活塞停止前进的瞬间,增压活塞及单向阀阀芯13前后压力不平衡,增压活塞因压差作用而前移,单向阀阀芯在弹簧10作用下自行关闭,实现压射增压。
(2)增压缸无背压的压射装置
分罐式压射增压结构
3-随动杆;
4-压射缸;
5-快速压射行程感应开关;
6-增压缸;
7-增压蓄能器入油口;
8-增压缸控制阀;
9-增压速度调节螺栓;
10-增压起始时间调节入油口;
11-压射力调节阀;
12-增压缸起动阀;
13-慢速压射与快速压射蓄能器入油口;
14-压射冲头回程入油口
采用分罐式压射增压器结构。
用两个蓄能器分别对压射缸和增压缸进行快速增压。
增压压力通过调整蓄能器压力来改变,压射速度、压射力和压射力建立时间都能分别单独调节。
工作:
合模结束信号发讯后,压射开始,压力油由油口13进入压射缸4进行慢速压射,当随动杆3离开行程感应开关5时,切换为快速压射,此时,快速压射蓄能器的压力油通过油口13进入压射缸进行快速压射,快速压射工作油同时进入增压缸起动阀12。
当模腔内金属液充满,快速压射因突然停止引起的压力冲击使阀12换向,受阀12控制的增压缸控制阀8打开,增压蓄能器的压力油进入增压缸,推动增压活塞产生压射增压。
优点:
①压射速度高,反应与升压时间短;
②反应与升压时间可单独调节;
③压力稳定不受压射速度影响;
④增压压力可通过增压蓄能器上的减压阀直接进行调整;
⑤由于压射与增压蓄能器分开,互不干扰。
2.2.2.2合模装置
主要完成模具的开、合及铸件顶出等。
要求它动作既平稳又迅速,锁紧可靠,便于压铸模的装卸和模具的清理,压铸件的取出方便可靠。
全液压锁模机构、液压-机械联合锁模机构。
全液压式合模机构
1-差动活塞;
2-充液箱;
3-填充阀;
4-合模缸座;
5-动模板;
6-凸块;
7-增压器
全液压合模机构。
整个机构由合模缸组、活塞组、动模板5、充液箱2、填充阀3和增压器7等组成。
V3为开模腔、V1为内合模腔、V2为外合模腔,活塞组中的差动活塞1和外活塞及动模板相连接。
合模时,V1通入液压油,虽V3也通入液压油,但差动活塞两边受力不同而右移,带着动模快速右移。
随着动模板5移动,V2腔容积不断增大、形成较大的真空度,自动打开填充阀3(此时阀a孔通液压油),使大量油液从充液箱向V2合模缸充液、进行快速合模。
当模具将闭紧时,由于动模板5拖动着拉杆凸块6打开凸轮阀,压力油进入V2腔,V2腔内压力升高,填充阀的阀门关闭,转为慢速合模,直至模具闭合。
此时,V2腔内压力升高到与管路中压力一致(~10MPa),但尚未达到压射时所需的最大合模力,因为增压器未起作用。
增压器通道e与V2腔相通,压射时,压力油从孔c进入增压器,克服弹簧4的弹力,顶开单向阀芯3,进入增压器液压缸左腔,推动活塞右移,使V2腔内压力增高,实现增压,使V2腔压力达23MPa,锁模力达1250kN。
开模时,V1腔和增压器从孔c回油,压力撤消,合模机构的差动活塞在V3腔常压压力油作用下,带着动模回位开模。
此时,V2腔内的油液必须迅速排回充液箱,为此,压力油从填充阀上端b孔通入,让先导推杆6推开填充阀内的先导阀门,从而,打开阀门3,使V2腔中油液先慢后快地排回充液箱,以实现开模过程的动作先慢后快。
全液压合模机构一般用于小型或中型压铸机;
大中型压铸机合模机构,一般采用液压-机械合模机构。
填充阀
1、3-弹簧;
2-阀门;
4-先导阀门;
5-阀座;
6-先导推杆;
7-缸座;
8-活塞缸;
9-活塞
增压器
1-活塞;
2-单向阀体;
3-阀芯;
4-弹簧;
6-活塞;
7-增压缸
2.2.2.3液压系统
2.2.2.4电气控制系统
2.2.2.5辅助装置
(1)气压注料装置
(2)取料机械手
2.3压铸机主要技术参数与选用
2.3.1压铸机的主要技术参数
压射、合模、设备技术经济指标。
2.3.1.1合模力
合模装置对模具所能施加的最大夹紧力,kN
2.3.1.2压射力
压射冲头作用于金属液的最大力,kN
2.3.1.3压射比压
压射冲头作用于单位面积金属液表面上的压力,MPa
是确保制品致密性和金属液充填能力的重要参数。
P为压射比压(Pa);
F为压射力(N);
d为压室直径(m);
A为压射冲头截面积(m2)
2.3.1.4压室容量
压室每次浇注能够容纳金属液的最大质量,kg
2.3.