过程控制系统与仪表全套教案Word格式.doc
《过程控制系统与仪表全套教案Word格式.doc》由会员分享,可在线阅读,更多相关《过程控制系统与仪表全套教案Word格式.doc(170页珍藏版)》请在冰豆网上搜索。
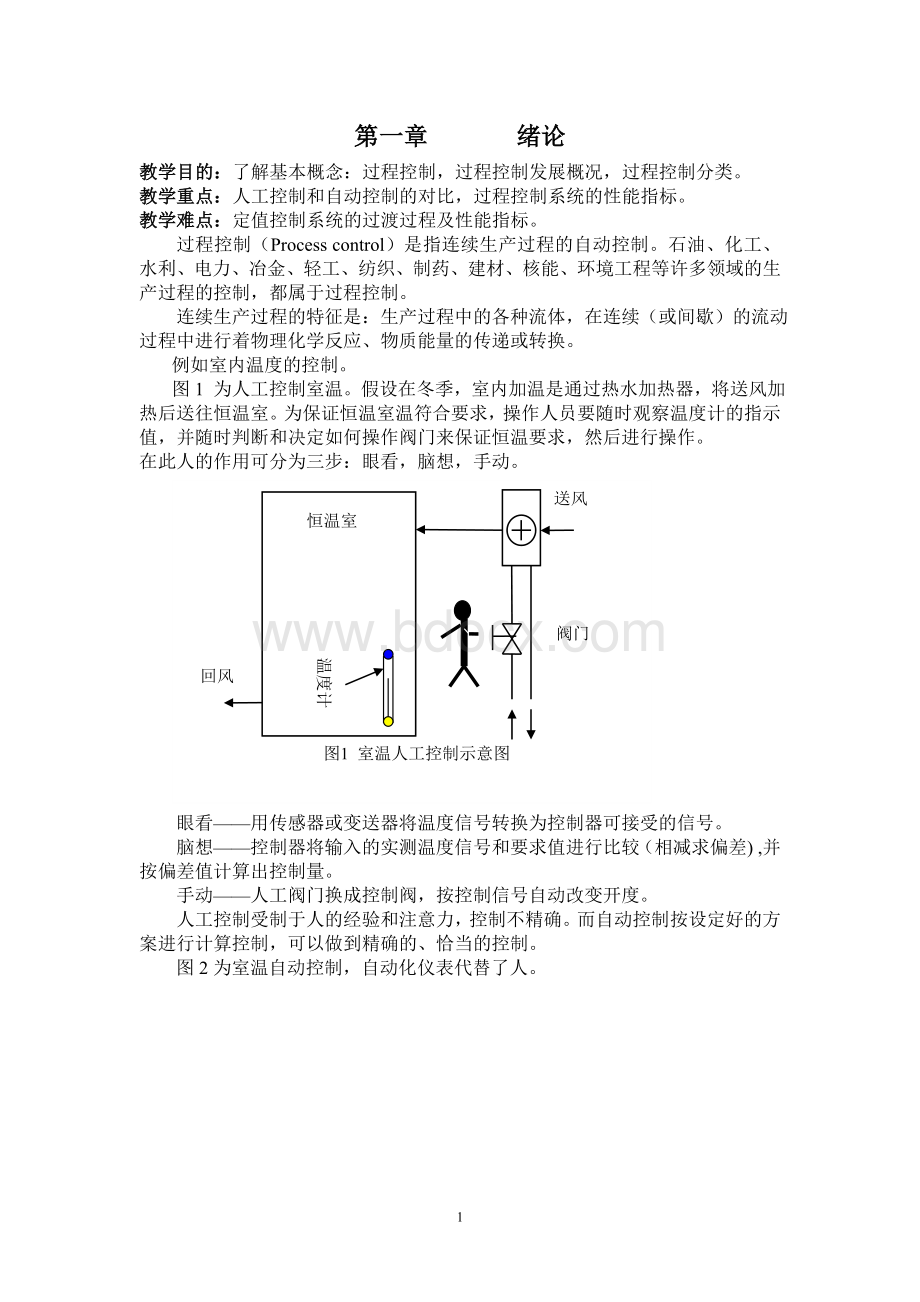
阀门
图1室温人工控制示意图
恒温室
温度计
眼看——用传感器或变送器将温度信号转换为控制器可接受的信号。
脑想——控制器将输入的实测温度信号和要求值进行比较(相减求偏差),并按偏差值计算出控制量。
手动——人工阀门换成控制阀,按控制信号自动改变开度。
人工控制受制于人的经验和注意力,控制不精确。
而自动控制按设定好的方案进行计算控制,可以做到精确的、恰当的控制。
图2为室温自动控制,自动化仪表代替了人。
送风送风风
1
3
4
M
TC
TT
回水水
热水
2
图2室温自动控制示意图
1—热水加热器;
3—控制器;
2—传感变送器;
4—执行器
过程控制系统的定义:
为实现对某个工艺参数的自动控制,由相互联系的自动化仪表、装置及被控对象、工艺设备构成的一个整体。
又称自动控制系统。
在讨论控制系统工作原理时,为清楚地表示自动控制系统各组成部分的作用及相互关系,一般用原理框图来表示控制系统。
如图2的室温控制系统是由温度变送器、控制器、电动调节阀和加热器及房间组成,如图3所示:
给定值
被控变量
干扰f
控制器
变送器
调节阀
加热器及房间
及房间
+
e
实测值
实测实测值值
-
图3室温控制系统组成图
过程控制系统方框图通常用标准名称表示。
如图4所示:
给定值
被控对象及房间
图4过程控制系统方框图
过程控制系统的主要任务是:
对生产过程中的重要参数(温度、压力、流量、物位、成分、湿度等)进行控制,使其保持恒定或按一定规律变化。
1.1过程控制的特点
1).控制对象复杂、控制要求多样
2).控制方案丰富
3).控制对象大多属于慢过程
4).大多数工艺要求定值控制
5).通常使用标准自动化仪表及装置
1.2过程控制的发展概况
过程控制的发展历程,就是过程控制装置(自动化仪表)与系统的发展历程。
1.2.1过程控制装置与系统的发展过程
1.局部自动化阶段(20世纪50~60年代)
1)自动化仪表安装在现场生产设备上,只具备简单的测控功能。
2)适用于小规模、局部过程控制。
2.模拟单元仪表控制阶段(20世纪60~70年代)
特点:
1)自动化仪表划分成各种标准功能单元,按需要可以组合成各种控制系统。
2)控制仪表集中在控制室,生产现场各处的参数通过统一的模拟信号,送往控制室。
操作人员可以在控制室监控生产流程各处的状况。
3)适用于生产规模较大的多回路控制系统。
3.集散控制阶段(20世纪70年代中期至今)
计算机的出现,大大简化了控制功能的实现。
用一台计算机可取代所有回路的控制仪表,实现直接数字控制(DDC,DirectDigitalControl)。
但DDC系统的故障危险高度集中,一旦计算机出现故障,就会造成所有控制回路瘫痪,使生产过程风险加大。
因此,DDC系统并未得到广泛应用。
80年代初,随着计算机性能提高、体积缩小,出现了内装CPU的数字控制仪表。
基于“集中管理,分散控制”的理念,在数字控制仪表和计算机与网络技术基础上,开发了集中、分散相结合的集散型控制系统(DCS,DistributedControlSystem)。
DCS系统实行分层结构,将控制故障风险分散、管理功能集中。
得到广泛应用。
随着CPU进入检测仪表和执行器,自动化仪表彻底实现了数字化、智能化。
控制系统也出现了由智能仪表构成的现场总线控制系统(FCS,FieldbusControlSystem)。
FCS系统把控制功能彻底下放到现场,依靠现场智能仪表便可实现生产过程的检测、控制。
而用开放的、标准化的通信网络——现场总线,将分散在现场的控制系统的通信连接起来,实现信息集中管理。
1.2.2过程控制策略与算法发展
伴随着自动化仪表的发展,过程控制策略与算法也经历了由简单到复杂的发展历程。
以经典控制理论为基础的PID(ProportionalIntegralDerivative)控制算法,由单回路控制发展了串级控制、比值控制、前馈控制、均匀控制、Smith预估控制及选择性控制等控制策略。
随着现代控制理论和人工智能技术的发展,解耦控制、推断控制、预测控制、模糊控制、自适应控制等控制策略与算法,也日趋完善。
现代自动控制技术的主要特点:
1)、功能综合化,控制与管理一体化已成为趋势,其应用领域和规模越来越大。
2)、技术密集化、系统集成化,是控制技术、通讯技术、计算机技术相结合的产物。
3)、系统的智能化程度日益提高,控制精度越来越高,控制手段日益丰富。
常见的自动化仪表生产企业:
西安仪表厂、四川仪表厂、上海仪表公司、Siemens、Yokogawa、Rosemount、Honeywell、Foxboro等公司。
1.3过程控制系统分类及其性能指标
1.3.1过程控制系统的分类
过程控制系统有多种分类方法。
按所控制的参数来分,有温度控制系统、压力控制系统、流量控制系统等;
按控制系统所处理的信号方式来分,有模拟控制系统与数字控制系统;
按照控制器类型来分,有常规仪表控制系统与计算机控制系统等。
但在讨论控制原理时,常用的分类方法是按设定值的形式或系统的结构特点分类。
1.按设定值的形式分类
1)定值控制系统——设定值恒定不变。
2)随动控制系统——设定值随时可能变化。
3)程序控制系统——设定值按预定的时间程序变化。
2.按系统的结构特点分类
1)反馈控制系统(闭环控制系统)
将被控变量输入到控制器,形成闭环,具有被控变量负反馈的控制系统。
如图5所示:
图5反馈控制系统方框图
反馈控制系统是过程控制最基本的结构形式
2)前馈控制系统(开环控制系统)
控制系统没有被控变量负反馈,不将被控变量引入到控制器输入端。
如图6所示:
执行器
被控对象
变送器
干扰f
测量值
图6开环控制系统原理框图
3)复合控制系统
前馈与反馈相结合,优势互补。
如图7所示
加法器
变送器1
控制器2
变送器2
——
控制器1
图7前馈-反馈复合控制系统原理框图
1.3.2过程控制系统的性能指标
当被控对象受到干扰、被控变量发生变化时,控制系统抵制干扰、纠正被控变量的过程,反映了控制系统的优劣。
为此,要有评价控制系统的性能指标。
控制系统的性能指标是根据工艺对控制的要求来制定的,概括为稳定性、准确性和快速性。
t
y
1.3.2.1稳态与动态
1、稳态
被控变量不随时间变化的平衡状态称为系统的稳态(静态)。
当自动控制系统的输入和输出均恒定不变时,就处于一种相对稳定的平衡状态,系统的各个环节也都处于稳定状态。
但生产还在进行,物料和能量仍然有进有出,只是平稳进行没有改变就是了
静态特性—静态时系统各环节的输入输出关系。
静态
动态
2、动态
被控变量随时间变化的不平衡状态称为系统的动态。
当干扰破坏了系统的平衡时,被控变量就会发生变化,而控制器、控制阀等自动化装置就要产生控制作用来使系统恢复平衡。
动态特性—在动态过程中系统各环节的输入输出变化关系。
1.3.2.2控制系统的过渡过程
控制系统的输入变化后,系统从原来的平衡状态,经过动态过程到达新的平衡状态的动态历程称为系统的过渡过程。
系统的过渡响应受内部和外部两种因素的影响。
1、内部因素:
系统特性
系统的特性是由系统中各环节的特性和系统的结构所决定的。
2、外部因素:
输入信号
在系统特性一定的情况下,被控变量随时间的变化规律取决于系统的输入信号。
生产中,出现的干扰信号是随机的。
但在分析和设计控制系统时,为了充分体现系统的特性和分析方便,常选择一些特定的输入信号,其中常用的是阶跃信号和正弦信号。
A
f(t)
时域分析时经常使用阶跃信号。
v阶跃信号变化突然,对被控变量的影响最大。
如果一个控制系统能够有效地克服这种干扰,那么对其它比较缓和的干扰也能很好地克服。
v阶跃信号的形式简单,容易实现,便于分析、实验和计算。
如图,输入信号在t=0时,阶跃上升幅度为A,其后保持。
表达为f(t)=Ae(t)
在阶跃输入的扰动作用下,定值控制系统过渡过程有四种形式:
①单调衰减过程
被控变量在给定值的一侧作单调变化,最后稳定在某一数值上。
②振荡衰减过程
被控变量上下波动,但幅度逐渐减少,最后稳定在某一数值上。
①
θa
③等幅振荡过程
被控变量在给定值附近来回波动,且波动幅度保持不变。
④振荡发散过程
被控变量来回波动,且波动幅度逐渐变大,离给定值越来越远。
③
④
aaa
过渡过程的分类
1)稳定的过渡过程
单调过程和衰减振荡过程是稳定的过渡过程。
被控变量经过一段时间后,逐渐趋向原来的或新的平衡状态。
衰减振荡过程的过渡过程较短,经常采用。
单调过程的过渡过程较长,被控变量长时间地偏离给定值,一般不采用,只是在生产上不允许被控变量有波动的情况下才采用。
2)不稳定的过渡过程
发散振荡过程中,被控变量不但不能达到平衡状态,而且逐渐远离给定值,它将导致被控变量超越工艺允许范围,这是生产上所不允许的。
3)临界过渡过程
处于稳定与不稳定之间,一般也认为是不稳定过程,生产上一般不采用。
只是某些简易的控制系统(如位式控制),只能达到