冶金安全规程Word格式.docx
《冶金安全规程Word格式.docx》由会员分享,可在线阅读,更多相关《冶金安全规程Word格式.docx(16页珍藏版)》请在冰豆网上搜索。
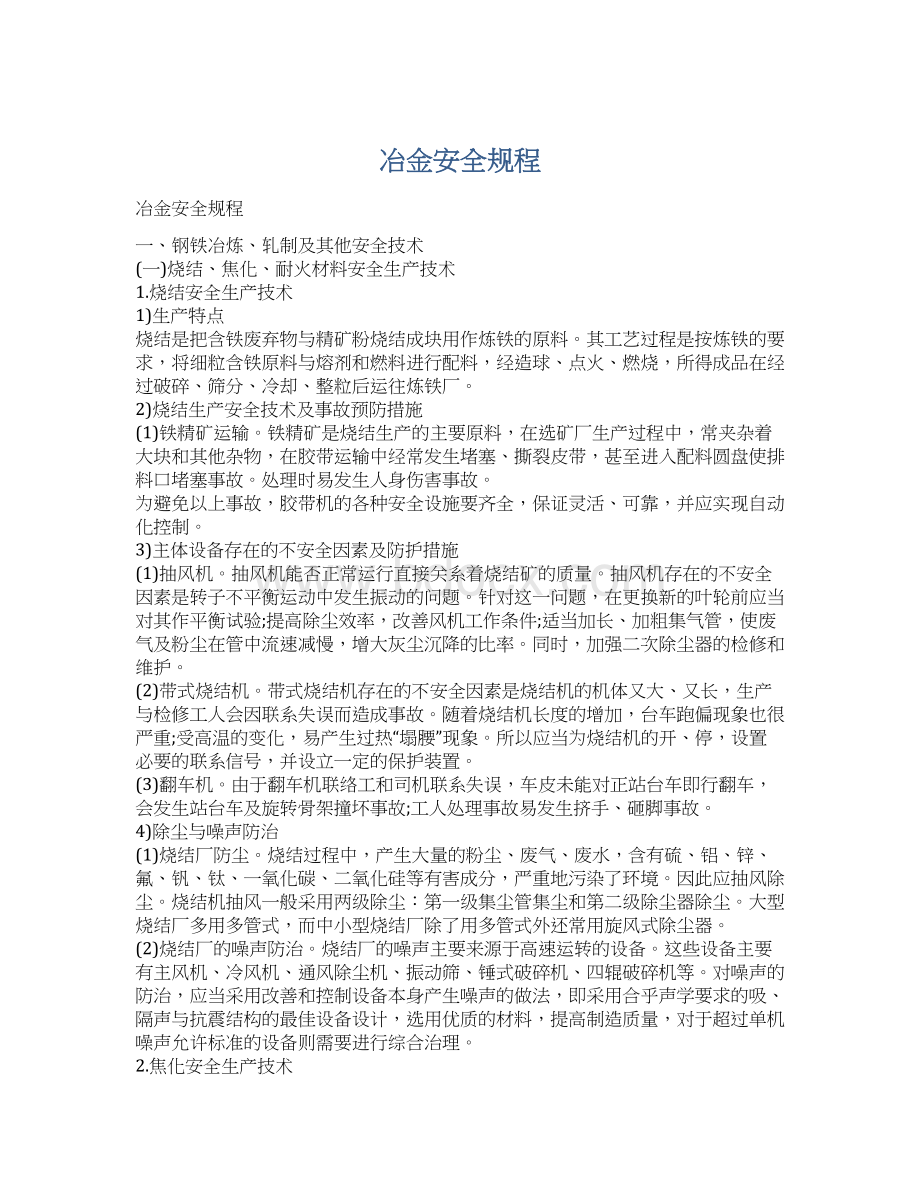
提高除尘效率,改善风机工作条件;
适当加长、加粗集气管,使废气及粉尘在管中流速减慢,增大灰尘沉降的比率。
同时,加强二次除尘器的检修和维护。
(2)带式烧结机。
带式烧结机存在的不安全因素是烧结机的机体又大、又长,生产与检修工人会因联系失误而造成事故。
随着烧结机长度的增加,台车跑偏现象也很严重;
受高温的变化,易产生过热“塌腰”现象。
所以应当为烧结机的开、停,设置必要的联系信号,并设立一定的保护装置。
(3)翻车机。
由于翻车机联络工和司机联系失误,车皮未能对正站台车即行翻车,会发生站台车及旋转骨架撞坏事故;
工人处理事故易发生挤手、砸脚事故。
4)除尘与噪声防治
(1)烧结厂防尘。
烧结过程中,产生大量的粉尘、废气、废水,含有硫、铝、锌、氟、钒、钛、一氧化碳、二氧化硅等有害成分,严重地污染了环境。
因此应抽风除尘。
烧结机抽风一般采用两级除尘:
第一级集尘管集尘和第二级除尘器除尘。
大型烧结厂多用多管式,而中小型烧结厂除了用多管式外还常用旋风式除尘器。
(2)烧结厂的噪声防治。
烧结厂的噪声主要来源于高速运转的设备。
这些设备主要有主风机、冷风机、通风除尘机、振动筛、锤式破碎机、四辊破碎机等。
对噪声的防治,应当采用改善和控制设备本身产生噪声的做法,即采用合乎声学要求的吸、隔声与抗震结构的最佳设备设计,选用优质的材料,提高制造质量,对于超过单机噪声允许标准的设备则需要进行综合治理。
2.焦化安全生产技术
焦化厂一般由备煤、炼焦、回收、精苯、焦油、其他化学精制、化验和修理等车间组成。
其中化验和修理车间为辅助生产车间。
备煤车间的任务是为炼焦车间及时供应合乎质量要求的配合煤。
炼焦车间是焦化厂的主体车间。
炼焦车间的生产流程是:
装煤车从贮煤塔取煤后,运送到已推空的碳化室上部将煤装入碳化室,煤经高温干馏变成焦炭,并放出荒煤气由管道输往回收车间;
用推焦机将焦炭从碳化室推出,经过拦焦车后落入熄焦车内送往熄焦塔熄焦;
之后,从熄焦车卸入凉焦台,蒸发掉多余的水分和进一步降温,再经输送带送往筛焦炉分成各级焦炭。
回收车间负责抽吸、冷却及吸收回收炼焦炉发生的荒煤气中的各种初级产品。
2)焦化安全生产技术及事故预防措施
(1)防火防爆。
一切防火防爆措施都是为了防止生产可燃(爆炸)性混合物或防止产生和隔离足够强度的活化能,以避免激发可燃性混合物发生燃烧、爆炸。
为此,必须弄清可燃(爆炸)性混合物和活化能是如何产生的,以及防止其产生和互相接近的措施。
有些可燃(爆炸)性混合物的形成是难以避免的,如易燃液体贮槽上部空间就存在可燃(爆炸)性混合物。
因此,在充装物料前,往贮槽内先充惰性气体(如氮),排出蒸气后才可避免上述现象发生。
此外,选用浮顶式贮槽也可以避免产生可燃(爆炸)性混合物。
其他非正常形成可燃(爆炸)性混合物的原因和预防措施如下:
(2)泄漏。
泄漏是常见的产生可燃(爆炸)性混合物的原因。
可燃气体、易燃液体和温度超过闪点的液体的泄漏,都会在漏出的区域或漏出的液面上产生可燃(爆炸)性混合物。
造成泄漏的原因主要有两个:
一是设备、容器和管道本身存在漏洞或裂缝。
有的是设备制造质量差,有的是长期失修、腐蚀造成的。
所以,凡是加工、处理、生产或贮存可燃气体、易燃液体或温度超过闪点的可燃液体的设备、贮槽及管道,在投入使用之前必须经过验收合格。
在使用过程中要定期检查其严密性和腐蚀情况。
焦化厂的许多物料因含有腐蚀性介质,应特别注意设备的防腐处理,或采用防腐蚀的材料制造。
二是操作不当。
相对地说,这类原因造成的泄漏事故比设备本身缺陷造成的要多些。
由于疏忽或操作错误造成跑油、跑气事故很多。
要预防这类事故的发生,除要求严格按标准化作业外,还必须采取防溢流措施。
《焦化安全规程》规定,易燃、可燃液体贮槽区应设防火堤,防火堤内的容积不得小于贮槽地上部分总贮量的一半,且不得小于最大贮槽的地上部分的贮量。
防火堤内的下水道通过防火堤处应设闸门。
此闸门只有在放水时才打开,放完水即应关闭。
对可能泄漏或产生含油废水的生产装置周围应设围堰。
化产车间下水道应设水封井、隔油池等。
(3)放散。
焦化厂许多设备都设有放散管,加工处理或贮存易燃、可燃物料的设备或贮槽,放散管放散的气(汽)体有的本身就是可燃(爆炸)性混合物,或放出后与空气混合成为可燃(爆炸)性混合物。
《焦化安全规程》规定,各放散管应按所放散的气体、蒸气种类分别集中净化处理后方可放散。
放散有毒、可燃气体的放散管出口应高出本设备及邻近建筑物4m以上。
可燃气体排出口应设阻火器。
(4)防尘与防毒。
煤尘主要产生在煤的装卸、运输以及破碎粉碎等过程中,主要产尘点为煤场、翻车机、受煤坑、输送带、转运站以及破碎、粉碎机等处。
一般煤场采用喷洒覆盖剂或在装运过程中采取喷水等措施来降低粉尘的浓度。
输送带及转运站主要依靠安设输送带通廓、局部或整体密闭防尘罩等来隔离和捕集煤尘。
破碎及粉碎设备等产尘点应加强密闭吸风,设置布袋除尘、湿式除尘、通风集尘等装置来降低煤尘浓度。
在焦化厂,一氧化碳存在于煤气中,特别是焦炉加热用的高炉煤气中的一氧化碳含量在30%左右。
焦炉的地下室、烟道通廓煤气设备多,阀门启闭频繁,极易泄漏煤气。
所以,必须对煤气设备定期进行检查,及时维护,烟道通廓的贫煤气阀应保证其处于负压状态。
为了防止硫化氢、氰化氢中毒,焦化厂应当设置脱硫、脱氰工艺设施。
过去国内只有城市煤气才进行脱硫,冶金企业一般不脱硫。
至于脱氰,一般只从部分终冷水或氨气中脱氰生产黄血盐。
随着对污染严重性认识的提高,近年来,各焦化厂已开始重视煤气的脱硫脱氰问题。
为了防止硫化氢和氰化氢中毒,蒸氨系统的放散管应设在有人操作的下风侧。
3.耐火材料生产安全技术
不同的耐火制品,使用的原材料及生产时发生的物理化学反应虽不同,但生产工序和加工方法,如原料煅烧、破碎、粉碎、细磨、配料、混料、成型、干燥和烧成等基本一致。
耐火材料生产所用的设备比较笨重,机械化程度低,劳动强度大,环境条件差,生产中易发生事故。
另外,耐火材料生产工艺中的各个环节,都可能产生大量含有较高游离二氧化碳的粉尘,严重地危害着人的身体健康。
2)耐火材料安全生产技术及事故预防措施
(1)主体设备运行的安全。
运行时应注意以下几点:
检查轴承润滑情况,轴承内及衬板的连接处是否有足够而适量的润脂;
检查所有的紧固件是否安全紧固;
检查传动胶带,若有破损应及时更换,胶带轮有油污时,应用干净的抹布将其擦净;
检查防护装置是否良好,发现有不安全的现象时应即行消除;
检查破碎腔内有无矿石及杂物,并清除之,正常运行后方可喂料;
正常启动后若发现有不正常情况,应立即停机检查处理;
在设备运行时,严禁从上面朝机器内窥视、进行任何调整、清理或检查等工作,也严禁用手在进料口上和破碎腔内搬运、移动矿石;
停机前,应首先停止加料,待破碎腔内破碎物料完全排出后,方可断开电源开关。
(2)防尘措施。
耐火厂的各个工艺环节可以说无处不产尘。
经验证明,采取水、密、风、护、革、管、教、查八字方针是有效的、正确的。
(3)安全技术措施。
改进工艺,提高机械化、自动化程度;
安装安全设施和标志,并定期检查;
坚决贯彻执行有关安全生产的政策和法规;
加强劳动保护,定期对职工进行身体检查。
(二)炼铁生产安全技术
1.炼铁安全生产的主要特点
炼铁是将铁矿石或烧结球团矿、锰矿石、石灰石和焦炭按一定比例予以混匀送至料仓,然后再送至高炉,从高炉下部吹入1000℃左右的热风,使焦炭燃烧产生大量的高温还原气体煤气,从而加热炉料并使其发生化学反应。
在1100℃左右铁矿石开始软化,1400℃熔化形成铁水与液体渣,分层存于炉缸。
之后,进行出铁、出渣作业。
炼铁生产所需的原料、燃料,生产的产品与副产品的性质,以及生产的环境条件,给炼铁人员带来了一系列潜在的职业危害。
例如,在矿石与焦炭运输、装卸,破碎与筛分,烧结矿整粒与筛分过程中,都会产生大量的粉尘;
在高炉炉前出铁场,设备、设施、管道布置密集,作业种类多,人员较集中,危险有害因素最为集中,如炉前作业的高温辐射,出铁、出渣会产生大量的烟尘,铁水、熔渣遇水会发生爆炸;
开铁口机、起重机造成的伤害等;
炼铁厂煤气泄漏可致人中毒,高炉煤气与空气混合可发生爆炸,其爆炸威力很大;
喷吹烟煤粉可发生粉尘爆炸;
另外,还有炼铁区的噪声,以及机具、车辆的伤害等。
如此众多的危险因素,威胁着生产人员的生命安全和身体健康。
2.炼铁生产的主要安全技术
1)高炉装料系统安全技术
装料系统是按高炉冶炼要求的料坯,持续不断的给高炉冶炼。
装料系统包括原料燃料的运人、储存、放料、输送以及炉顶装料等环节。
装料系统应尽可能的减少装卸与运输环节,提高机械化、自动化水平,使之安全的运行。
(1)运人、储存与放料系统。
大中型高炉的原料和燃料大多数采用胶带机运输,比火车运输易于自动化和治理粉尘。
储矿槽未铺设隔栅或隔栅不全,周围没有栏杆,人行走时有掉入槽的危险;
料槽形状不当,存有死角,需要人工清理;
内衬磨损,进行维修时的劳动条件差;
料闸门失灵常用人工捅料,如料突然崩落往往造成伤害。
放料时的粉尘浓度很大,尤其是采用胶带机加振动筛筛分料时,作业环境更差。
因此,储矿槽的结构应是永久性的、十分坚固的。
各个槽的形状应该做到自动顺利下料,槽的倾角不应该小于50°
,以消除人工捅料的现象。
金属矿槽应安装振动器。
钢筋混凝土结构,内壁应铺设耐磨衬板;
存放热烧结矿的内衬板应是耐热的。
矿槽上必须设置隔栅,周围设栏杆,并保持完好。
料槽应设料位指示器,卸料口应选用开关灵活的阀门,最好采用液压闸门。
对于放料系统应采用完全封闭的除尘设施。
(2)原料输送系统。
大多数高炉采用料车斜桥上料法,料车必须设有两个相对方向的出入口,并设有防水防尘措施。
一侧应设有符合要求的通往炉顶的人行梯。
卸料口卸料方向必须与胶带机的运转方向一致,机上应设有防跑偏、打滑装置。
胶带机在运转时容易伤人,所以必须在停机后,方可进行检修、加油和清扫工作。
(3)顶炉装料系统。
通常采用钟式向高炉装料。
钟式装料以大钟为中心,有大钟、料斗、大小钟开闭驱动设备、探尺、旋转布料等装置组成。
采用高压操作必须设置均压排压装置。
做好各装置之间的密封,特别是高压操作时,密封不良不仅使装置的部件受到煤气冲刷,缩短使用寿命,甚至会出现大钟掉到炉内的事故。
料钟的开闭必须遵守安全程序。
为此,有关设备之间必须连锁,以防止人为的失误。
2)供水与供电安全技术
高炉是连续生产的高温冶炼炉,不允许发生中途停水、停电事故。
特别是大、中型高炉必须采取可靠的措施,保证安全供电、供水。
(1)供水系统安全技术。
高炉炉体、风口、炉底、外壳、水渣等必须连续给水,一旦中断便会烧坏冷却设备,发生停产的重大事故。
为了安全供水,大中型高炉应采取以下措施:
供水系统设有一定数量的备用泵;
所有泵站均设有两路电源;
设置供水的水塔,以保证柴油泵启动时供水;
设置回水槽,保证在没有外部供水情况下维持循环供水;
在炉体、风口供水管上设连续式过滤器;
供、排水采用钢管以防破裂。
(2)供电安全技术。
不能停电的仪器设备,万一发生停电时