国家节能中心能效评价技术依据.docx
《国家节能中心能效评价技术依据.docx》由会员分享,可在线阅读,更多相关《国家节能中心能效评价技术依据.docx(18页珍藏版)》请在冰豆网上搜索。
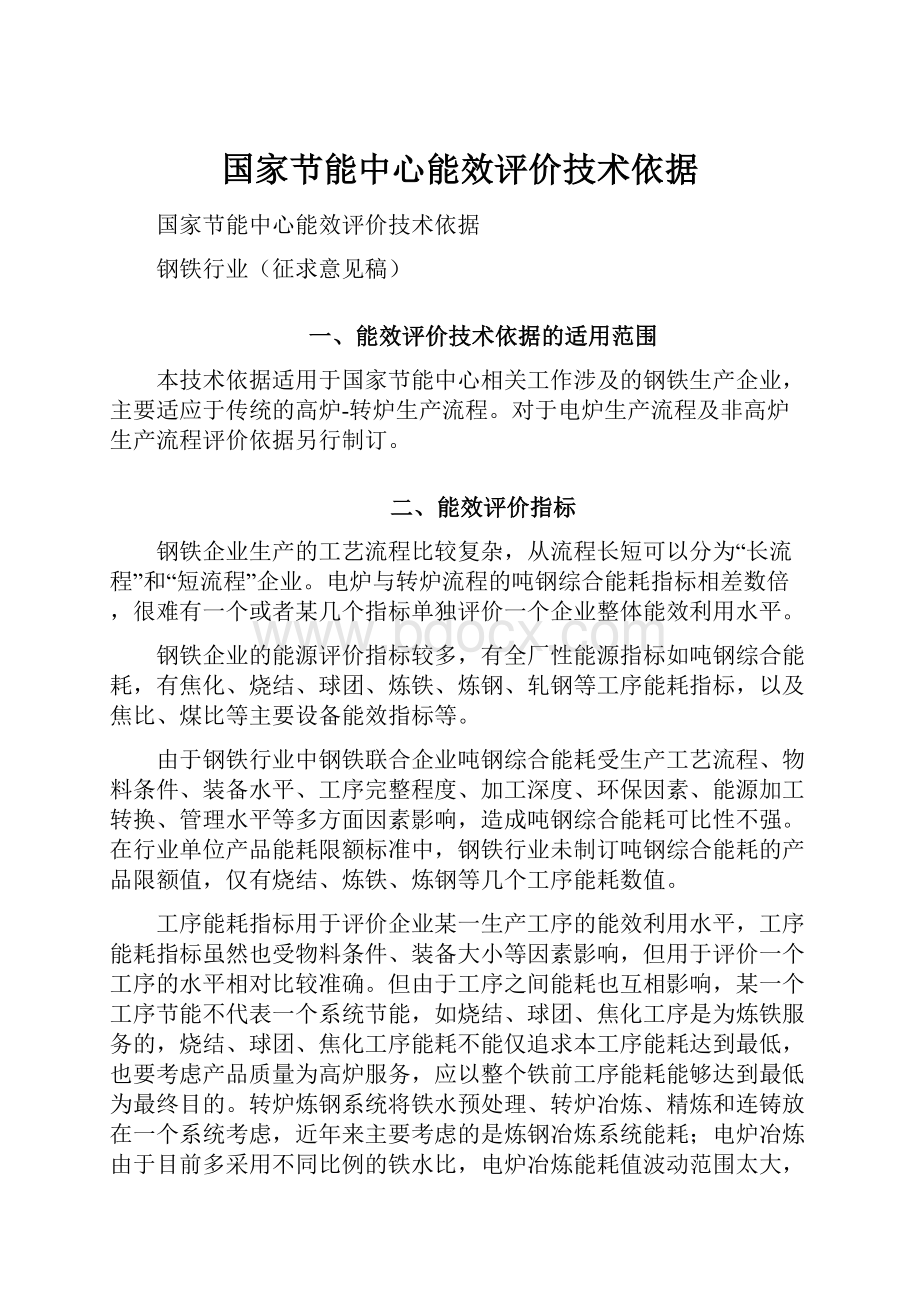
国家节能中心能效评价技术依据
国家节能中心能效评价技术依据
钢铁行业(征求意见稿)
一、能效评价技术依据的适用范围
本技术依据适用于国家节能中心相关工作涉及的钢铁生产企业,主要适应于传统的高炉-转炉生产流程。
对于电炉生产流程及非高炉生产流程评价依据另行制订。
二、能效评价指标
钢铁企业生产的工艺流程比较复杂,从流程长短可以分为“长流程”和“短流程”企业。
电炉与转炉流程的吨钢综合能耗指标相差数倍,很难有一个或者某几个指标单独评价一个企业整体能效利用水平。
钢铁企业的能源评价指标较多,有全厂性能源指标如吨钢综合能耗,有焦化、烧结、球团、炼铁、炼钢、轧钢等工序能耗指标,以及焦比、煤比等主要设备能效指标等。
由于钢铁行业中钢铁联合企业吨钢综合能耗受生产工艺流程、物料条件、装备水平、工序完整程度、加工深度、环保因素、能源加工转换、管理水平等多方面因素影响,造成吨钢综合能耗可比性不强。
在行业单位产品能耗限额标准中,钢铁行业未制订吨钢综合能耗的产品限额值,仅有烧结、炼铁、炼钢等几个工序能耗数值。
工序能耗指标用于评价企业某一生产工序的能效利用水平,工序能耗指标虽然也受物料条件、装备大小等因素影响,但用于评价一个工序的水平相对比较准确。
但由于工序之间能耗也互相影响,某一个工序节能不代表一个系统节能,如烧结、球团、焦化工序是为炼铁服务的,烧结、球团、焦化工序能耗不能仅追求本工序能耗达到最低,也要考虑产品质量为高炉服务,应以整个铁前工序能耗能够达到最低为最终目的。
转炉炼钢系统将铁水预处理、转炉冶炼、精炼和连铸放在一个系统考虑,近年来主要考虑的是炼钢冶炼系统能耗;电炉冶炼由于目前多采用不同比例的铁水比,电炉冶炼能耗值波动范围太大,暂不作研究。
钢铁联合企业加工深度不一,但是加工深度到一次材的吨钢综合能耗指标波动在一个合适范围,可以研究到加工深度只到一次材的钢铁企业吨钢综合能耗合理水平。
为此,从系统节能角度出发,充分考虑现有工作基础和能耗数据的可获得性,重点研究3个主要能耗指标:
(1)铁前系统(含烧结、球团、焦化和炼铁)能耗折吨铁产品能耗;
(2)转炉炼钢系统(含铁水预处理、转炉冶炼、精炼和连铸)折吨坯能耗;
(3)高炉-转炉生产流程到一次材的吨钢综合能耗。
三、指标的定义及计算方法
1、吨钢综合能耗
根据《综合能耗计算通则》(GB-T2589),吨钢综合能耗计算范围和公式如下:
计算范围:
吨钢综合能耗计算时应包括钢铁企业生产直接消耗的各种能源及其辅助生产系统、直接为钢铁企业生产服务的附属生产系统实际消耗的各种能源总量,不包括企业非钢铁部分生产消耗的能源量和外销能源量。
计算公式:
其中:
式中“自耗能源量”的含意是:
企业自耗能源量,还应满足下列公式:
加工深度到一次材的吨钢综合能耗指全厂吨钢综合能耗扣除二次材及以后的深加工能耗所得。
2、工序能耗指标
企业的某一生产环节(生产工序)在统计期内的综合能耗。
它根据该工序的能源消耗及能耗工质实物量消耗的统计计量折算成标准煤进行计算。
钢铁企业生产工艺较长,主生产工序包括焦化、烧结、球团、炼铁、炼钢、轧钢工序。
其中,炼钢工序又包括转炉工序和电炉工序,转炉(电炉)工序包括铁水预处理、转炉(电炉)冶炼、炉外精炼和连铸工序;轧钢工序包括热轧工序和冷轧工序。
各工序能耗的统计范围和计算方法如下:
2.1焦化工序能耗
(1)统计范围
备煤(不包括洗煤)、炼焦和煤气净化工段的能耗扣除自身回收利用和外供的能源量,不包括精制。
备煤工段包括贮煤、粉碎、配煤及系统除尘;炼焦工段包括炼焦、熄焦、筛运焦、装煤除尘、出焦除尘和筛运焦除尘;煤气净化工段内容包括冷凝鼓风、脱硫、脱氰、脱氨、脱苯、脱萘等工序和酚氰污水处理;干熄焦产出只计蒸汽、不含发电。
(2)计算公式
式中:
EJT——焦化工序单位产品综合能耗(kgce/t);
——原料煤量(kgce);
——加工能耗量,指炼焦生产所用焦炉煤气、高炉煤气、水、电、蒸汽、压缩空气等能源(kgce);
——焦化产品外供量,指供外厂(车间)的焦炭、焦炉煤气、煤焦油、粗苯等的数量(kgce);
——余热回收量,如干熄焦工序回收的蒸汽量等(kgce);
——焦炭产量(t);
2.2烧结工序能耗
(1)统计范围
包括生产系统(从熔剂、燃料破碎开始,经配料、原料运输、工艺过程混料、烧结机、烧结矿破碎、筛分等到成品烧结矿皮带机离开烧结工序为止的各生产环节)、辅助生产系统(生产管理及调度指挥系统、机修、化验、计量、水处理、烧结除尘和脱硫等环保设施等)消耗的能源量,扣除工序回收的能源量。
不包括附属生产系统(如食堂、保健站、休息室等)消耗的能源量。
(2)计算公式
式中:
ESJ——烧结工序单位产品能耗(kgce/t);
——烧结工序消耗的各种能源量折标准煤量总和(kgce);
——烧结工序回收的能源量折标准煤量(kgce);
——烧结工序合格烧结矿产量(t),以烧结工序合格烧结矿的生产量计;
2.3球团工序能耗
(1)统计范围
包括生产系统(经配料、原料运输、造球、焙烧、筛分等到成品球团矿皮带机离开球团工序为止的各生产环节)和辅助生产系统(生产管理及调度指挥系统、机修、化验、计量、环保等)消耗的能源量,扣除工序回收的能源量。
不包括附属生产系统(如食堂、保健站、休息室等)消耗的能源量。
(2)计算公式
式中:
EQT——球团工序单位产品能耗(kgce/t);
——球团工序消耗的各种能源量折标准煤量总和(kgce);
——球团工序回收的能源量折标准煤量(kgce);
——球团工序合格球团矿产量(t),以球团工序合格球团矿的生产量计。
2.4高炉炼铁工序能耗
(1)统计范围
包括高炉工艺生产系统(原燃料供给、鼓风、热风炉、煤粉干燥及喷吹、高炉本体、渣铁处理等系统)、辅助生产系统(生产管理及调度指挥系统、机修、化验、计量、水处理及除尘等环保设施)消耗的能源量,扣除工序回收的能源量。
不包括附属生产系统(如食堂、保健站、休息室等)消耗的能源量。
(2)计算公式
式中:
EGL——高炉炼铁工序单位产品能耗(kgce/t);
——高炉炼铁工序消耗的各种能源量折标准煤量总和(kgce);
——高炉炼铁工序回收的能源量折标准煤量(kgce);
——高炉炼铁工序合格生铁产量(t)。
2.5铁前系统折吨铁产品能耗
(1)统计范围
包含烧结、球团、焦化、炼铁四个工序的能耗之和,折算到单位合格生铁的能耗。
(2)计算公式
式中:
ETQ——铁前工序能耗折吨铁单位产品能耗(kgce/t);
——铁前工序消耗的各种能源量折标准煤量总和(kgce);
——铁前工序回收的能源量折标准煤量(kgce);
——炼铁工序合格生铁产量(t);
2.6转炉炼钢工序能耗
(1)统计范围
包括从原料进厂到钢锭、连铸钢坯、铸造用液态钢(铸钢水)出厂的整个炼钢工序过程,包括铁水预处理、转炉冶炼、二次冶金(精炼)、连铸和铸锭精整、产品出厂等全过程的能源消耗量,扣除炼钢工序外供能源量。
(2)计算公式
转炉炼钢综合工序单位能耗(kgce/t)=转炉炼钢综合工序净耗能量(kgce)/转炉钢坯合格产出量(t)
2.7转炉冶炼工序能耗
(1)统计范围
包括从铁水进厂到转炉出合格钢水为止的生产系统(铁水预处理、转炉本体、渣处理、钢包烘烤、煤气回收和处理系统等)和辅助生产系统(生产管理及调度指挥系统和机修、化验、计量、软水、环境除尘等设施)消耗的能源量,扣除工序回收的能源量,不包括精炼、连铸(浇铸)、精整的能耗及附属生产系统(如食堂、保健站、休息室等)消耗的能源量。
(2)计算公式
式中:
EZL——转炉冶炼工序单位产品能耗(kgce/t);
——转炉冶炼工序消耗的各种能源量折标准煤量总和(kgce);
——转炉冶炼工序回收的能源量折标准煤量(kgce);
——转炉工序合格粗钢产量(t);
2.8炉外精炼工序能耗
(1)统计范围
从钢水进入炉外精炼装置,到钢水吊到连铸大包回转台全过程的直接能耗;应包括精炼、电加热及电磁搅拌电耗、辅助及环保等工艺设施的能源消耗量。
(2)计算公式
式中:
—精炼工序单位产品能耗(kgce/t)
—精炼工序消耗的各种能源的折标准煤量总和(kgce);
—精炼工序回收的各种能源的折标准煤量总和(kgce);
—精炼工序处理钢水量(t)。
2.9连铸工序能耗
(1)统计范围
从钢水送入钢包回转台,到合格坯运出连铸车间全过程的直接能耗。
(2)计算公式
式中:
—连铸工序单位产品能耗(kgce/t)
—连铸工序消耗的各种能源的折标准煤量总和(kgce);
—连铸工序回收的各种能源的折标准煤量总和(kgce);
—连铸工序合格铸坯产量(t)。
2.10铁水预处理工序能耗
(1)统计范围
包括预处理剂的运输与输送、喷吹或机械搅拌、铁水扒渣和渣处理(不包括炉渣后加工),辅助设备及除尘环保等设施的能源消耗量。
(2)计算公式
式中:
—铁水预处理单位产品能耗(kgce/t);
—铁水预处理工序消耗的各种能源的折标准煤量总和(kgce);
—铁水预处理工序处理铁水量(t)。
2.11热轧工序能耗
(1)统计范围
包括预处理或加热、轧制、精整及热处理等工艺设施的直接能耗量,并扣除回收的能源量。
有多条轧线的应分别按轧线计算。
(2)计算公式
式中:
ERZ——热轧工序单位能耗(kgce/t);
——热轧工序消耗的各种能源量折标准煤量总和(kgce);
——热轧工序回收的能源量折标准煤量(kgce);
——合格热轧轧材产量(t);
2.12冷轧工序能耗
(1)统计范围
包括酸洗、轧制、退火、涂镀层处理、平整、精整等工艺设施的直接能耗量。
有多条轧线的应分别按轧线计算。
(2)计算公式
式中:
ELZ——冷轧工序单位能耗(kgce/t);
——冷轧工序消耗的各种能源量折标准煤量总和(kgce);
——冷轧工序回收的能源量折标准煤量(kgce);
——合格冷轧轧材产量(t);
四、钢铁行业能效评价指标值
1.吨钢综合能耗(加工深度到一次材)指标值
序号
流程
流程完整度
数值类别
数值大小
1
高炉-转炉
含焦化
A
575
B
585
C
620
D
650
2
高炉-转炉
不含焦化
A
530
B
540
C
570
D
600
其中A值为全国同类钢铁企业能效最高水平,B值为全国同类钢铁企业的前5%水平,C值为全国同类钢铁企业能效前20%水平,D值为全国同类钢铁企业能效平均水平。
2.铁前系统折吨铁工序能耗指标值
序号
工序名称
数值类别
数值大小
1
铁前系统折吨铁工序能耗(含焦化)
A
460
B
480
C
520
D
580
2
铁前系统折吨铁工序能耗(不含焦化)
A
430
B
450
C
480
D
530
注:
烧结和冶炼稀土矿和钒钛磁铁矿的企业,要按照“烧结原料中稀土矿、钒钛磁铁矿用量比例每增加1%,烧结工序能耗增加0.15kgce/t-烧结矿;高炉入炉原料中稀土矿、钒钛磁铁矿用量比例每增加1%,高炉工序能耗增加0.3kgce/t-铁”的原则扣除影响后再进行比较。
其中A值为全国同类钢铁企业能效最高水平,B值为全国同类钢铁企业的前5%水平,C值为全国同类钢铁企业能效前20%水平,D值为全国同类钢铁企业能效平均水平。
3.转炉炼钢系统折吨坯工序能耗指标值
序号
工序名称
数值类别
数值大小
1
转炉炼钢系统折吨坯工序能耗
A
-18
B
-13
C
3
D
13
其中A值为全国同类钢铁企业能效最高水平,B值为全国同类钢铁企业的前5%水平,C值为全国同类钢铁企业能效前20%水平,D值为全国同类钢铁企业能效平均水平。
五、钢铁行业能效评价指标值的应用
1.单项指标能效水平判断方法
根据计算出来的企业(或项目)铁前系统折吨铁工序能耗、转炉炼钢系统折吨坯工序能耗和加工深度到一次材的吨钢综合能耗指标,和上述各表对比判断项目的能效水平。
能耗指标数值>D值,国内落后水平;
D值≥能耗指标数值>C值,国内一般水平;
C值≥能耗指标数值>B值,国内先进水平;
B值≥能耗指标数值>A值,国内领先水平;
能耗指标数值≤A值,国际领先水平。
2.综合能效水平判断方法
企业(或项目)综合能效水平以铁前系统折吨铁工序能耗、转炉炼钢系统折吨坯工序能耗和加工深度到一次材的吨钢综合能耗指标达到的最低能效水平作为企业(或项目)的综合能效水平。
如铁前系统折吨铁工序能耗达到了国际领先水平,转炉炼钢系统折吨坯工序能耗达到了国内领先水平,加工深度到一次材的吨钢综合能耗指标达到了国内先进水平,则最终企业(或项目)的综合能效水平为国内先进水平。
六、钢铁能耗指标的影响因素及改进措施
1、综合能耗影响因素
1)生产工艺流程:
高炉-转炉生产流程、高炉-电炉流程和纯电炉流程对能耗影响因素巨大,差距数倍。
2)物料条件:
高炉入炉矿品位、焦化洗精煤质量、是否特殊矿(稀土矿、钒钛矿)等物料条件对能耗数值影响很大。
3)装备水平:
同等生产条件下,一般来说,大型装备能效水平较小型装备能效水平高,如4000m3高炉和1000m3等。
4)工序完整度:
钢铁企业由于工艺流程长,含焦化、烧结、球团、炼铁、炼钢、轧钢主生产工序,但企业工序并不全部完整,有缺焦化、缺球团等工序的,必然会影响全厂能效水平。
5)加工深度:
钢铁企业产品加工深度不一,有的企业只到一次材,有的企业加工到冷轧,甚至三、四次材深加工,加工深度越深,能源消耗必然越多。
6)环保因素:
钢铁企业环保耗能占全厂能耗比重越来越高,环保工作开展好的企业其环保用能占全厂比重大,相反,环保工作差的企业其环保用能占比就小。
7)能源加工转换:
由于折标系数原因,副产二次能源是输出还是企业自身进行能源转换,对能耗指标的影响是巨大的。
8)能源管理:
同样规模的生产流程,能源管理水平不同,其相应的能耗指标也有差异。
企业能源计量器具配备水平、设备管理水平、能效管理水平的高低在一定程度决定着企业能耗水平的高低。
2、改进措施
1)结构节能措施。
降低铁钢比,特别是在条件许可时,转炉应多“吃”废钢,减少铁前的物料和能源消耗;采用高效连铸工艺技术,进一步提高生产作业率;提高高炉炼铁喷煤比,优化企业用煤结构;采用连铸坯热送热装和直接轧制技术,促进轧钢工序节能;优化高炉炼铁炉料结构,多使用球团矿;淘汰落后工艺装备,充分发挥现代化、大型化装备能效高的优势,提高企业能源利用高效化。
2)技术节能措施。
重点推广焦化干熄焦、煤调湿、上升管余热利用;烧结余热回收与发电、烧结废烟气循环、球团烟气循环;炼铁高炉干式TRT、富氧大喷煤、冲渣水余热利用;炼钢干式除尘及煤气回收、钢渣显热利用、干式精炼、电炉优化供电;轧钢钢材在线热处理;全厂性煤气综合利用、高效热点联产、低温资源综合利用等先进技术。
3)管理节能措施。
加强钢铁企业能源管控中心的建设及实际运营效果,加强能源在线监测能力;完善能源计量、统计等基础工作;加强能效对标;完善企业能源管理结构和管理制度;加强企业能效审计等。
七、附件
1、钢铁能效评价技术相关标准
(1)《综合能耗计算通则》GB/T2589-2008
(2)《粗钢生产主要工序单位产品能源消耗限额》GB21256-2007
(3)《焦炭单位产品能源消耗限额》GB21342-2008
(4)《钢铁企业节能设计规范》GB50632-2010
(5)《企业能量平衡通则》GB/T3484-2009
(6)《钢铁企业能源计量器具配备和管理要求》GB/T21368-2008
(7)《能源管理体系要求》GB/T23331-2009
(8)取水定额第2部分钢铁联合企业GB/T18916.2-2012
(9)中小型三相异步电动机能效限定值及节能评价值GB18613-2006
(10)三相配电变压器能效限定值及节能评价值GB20052-2006
(11)通风机系统电能平衡测试与计算方法GB/T13467-1992
(12)评价企业合理用电技术导则GB/T3485-1998
(13)评价企业合理用热技术导则GB/T3486-1993
(14)清水离心泵能效限定值及节能评价值GB19762-2007
(15)中小型三相异步电动机能效限定值及节能评价值GB18613-2006
(16)容积式空气压缩机能效限定值及节能评价值GB19153-2003
(17)三相配电变压器能效限定值及节能评价值GB20052-2006
(18)通风机能效限定值及节能评价值GB19761-2009
(19)风机、泵类负载变频调速节电GB/T21056-2007
(20)房间空气调节器能效限定值及能源效率等级GB12021.3-2010
2、各种能源折标煤参考系数
各种能源折标准煤参考系数
能源名称
国际单位制下的折算系数
折标准煤系数
原煤
20934kJ/kg
0.7143kgce/kg
干洗精煤
29727kJ/kg
(灰分10%)
1.0143kgce/kg
(灰分10%)
无烟煤
25120kJ/kg
0.8571kgce/kg
动力煤
20934kJ/kg
0.7143kgce/kg
焦炭(干全焦)
28469kJ/kg
(灰分13.5%)
0.9714kgce/kg
(灰分13.5%)
焦粉
28469kJ/kg
0.9714kgce/kg
沥青
39000kJ/kg
1.3307kgce/kg
燃料油
41869kJ/kg
1.4286kgce/kg
汽油
43123kJ/kg
1.4714kgce/kg
煤油
43123kJ/kg
1.4714kgce/kg
柴油
42704kJ/kg
1.4571kgce/kg
液化石油气
50242kJ/kg
1.7143kgce/kg
粗苯
41869kJ/kg
1.4286kgce/kg
焦油
33496kJ/kg
1.1429kgce/kg
重油
41869kJ/kg
1.4286kgce/kg
天然气
35588kJ/m3
1.2143kgce/m3
焦炉煤气
16746kJ/m3
0.5714kgce/m3
高炉煤气
3139kJ/m3
0.1071kgce/m3
转炉煤气
7327kJ/m3
0.2500kgce/m3
重油催化裂解气
3769kJ/m3
0.1286kgce/m3
蒸汽(中压)
3042kJ/kg
0.1038kgce/kg
蒸汽(低压)
2866kJ/kg
0.0978kgce/kg
电力(等价*)
10023kJ/(kW·h)
0.3420kgce/(kW·h)
电力(当量)
3602kJ/(kW·h)
0.1229kgce/(kW·h)
注1:
kgce与kJ的转换系数为29307.6,即1kgce=29307.6kJ
注2:
洗精煤或焦炭灰分每增加1%,热值相应减少334kJ/kg
注3:
电力等价值折算系数为2006年电力联合会发布的火电机组发电煤耗
3、耗能工质折算系数推荐值
主要耗能工质折算系数推荐值
耗能工质名称
电力折算系数取当量值
电力折算系数取等价值
国际单位制下的
折算系数
折标准煤系数
国际单位制下的
折算系数
折标准煤系数
新水
1213kJ/kg
0.0414kgce/kg
3373kJ/kg
0.1151kgce/kg
工业水
1392kJ/kg
0.0475kgce/kg
3874kJ/kg
0.1322kgce/kg
软水
5539kJ/kg
0.1890kgce/kg
15413kJ/kg
0.5259kgce/kg
压缩空气
445kJ/m3
0.0152kgce/m3
1240kJ/m3
0.0423kgce/m3
氧气
2350kJ/m3
0.0802kgce/m3
6539kJ/m3
0.2231kgce/m3
氮气
495kJ/m3
0.0169kgce/m3
1377kJ/m3
0.0470kgce/m3
氩气
495kJ/m3
0.8872kgce/m3
1377kJ/m3
2.4690kgce/m3
氢气
26002kJ/m3
0.3514kgce/m3
72360kJ/m3
0.9778kgce/m3
鼓风
10299kJ/m3
0.0088kgce/m3
28657kJ/m3
0.0246kgce/m3
注:
kgce与kJ的转换系数为29307.6,即1kgce=29307.6kJ