零件失效分析讲义.docx
《零件失效分析讲义.docx》由会员分享,可在线阅读,更多相关《零件失效分析讲义.docx(102页珍藏版)》请在冰豆网上搜索。
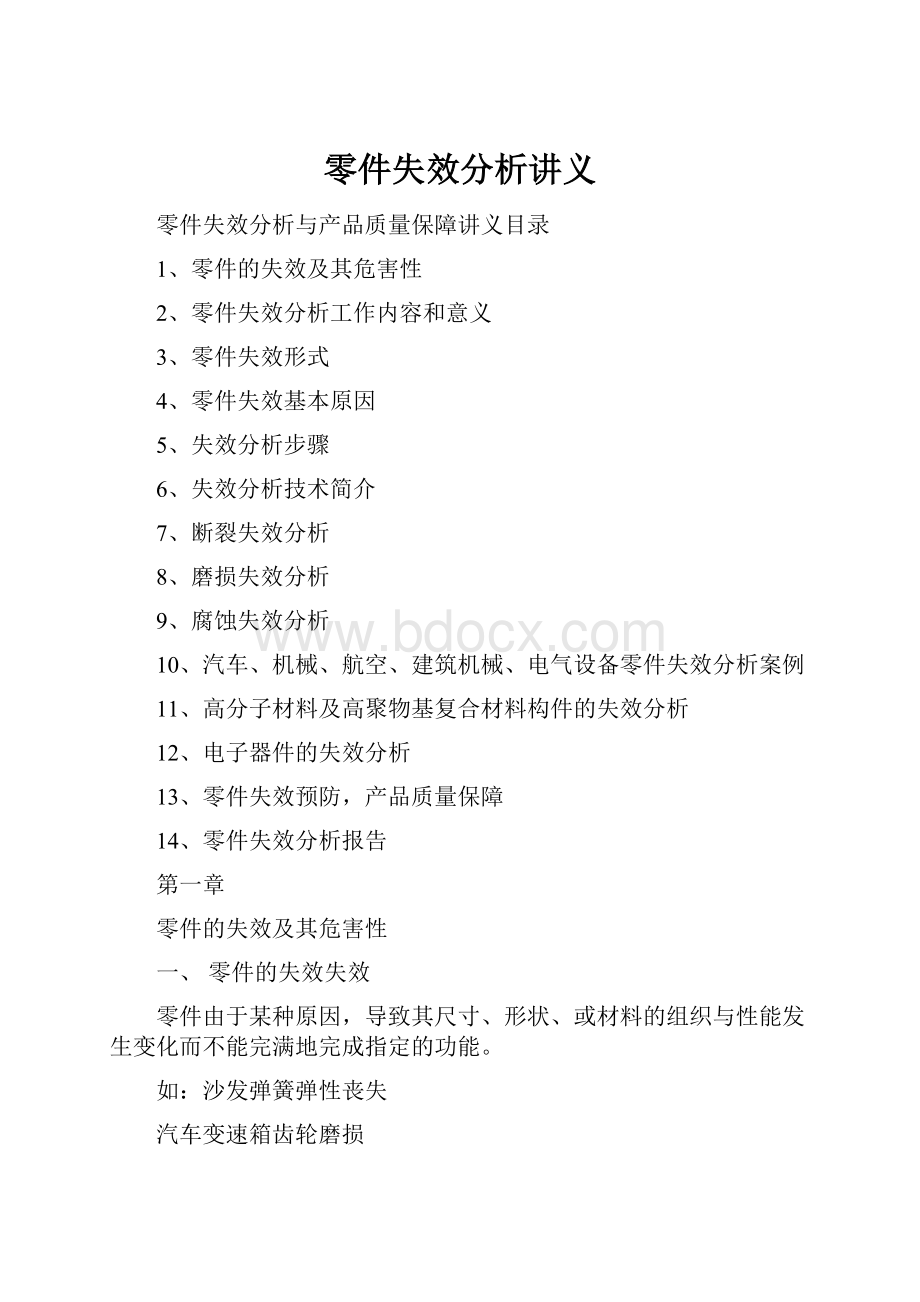
零件失效分析讲义
零件失效分析与产品质量保障讲义目录
1、零件的失效及其危害性
2、零件失效分析工作内容和意义
3、零件失效形式
4、零件失效基本原因
5、失效分析步骤
6、失效分析技术简介
7、断裂失效分析
8、磨损失效分析
9、腐蚀失效分析
10、汽车、机械、航空、建筑机械、电气设备零件失效分析案例
11、高分子材料及高聚物基复合材料构件的失效分析
12、电子器件的失效分析
13、零件失效预防,产品质量保障
14、零件失效分析报告
第一章
零件的失效及其危害性
一、零件的失效失效
零件由于某种原因,导致其尺寸、形状、或材料的组织与性能发生变化而不能完满地完成指定的功能。
如:
沙发弹簧弹性丧失
汽车变速箱齿轮磨损
电动机轴断裂
二、零件失效的危害性
1、零件失效,导致机械不能正常工作,降低生产效率,降低产品质量。
例:
冷冲模具磨损失效
2、零件失效,导致机械不能工作,停工停产,造成重大经济损失。
例:
一汽车运行3天后连杆断裂,汽缸体捣坏、报废。
损失约20万元。
黄河刘家峡水电站水轮发电机风叶掉脱,刮坏全部定子线圈,直接损失257万元。
3、零件失效,导致机毁人亡
一大货车,超载运行,因制动失灵,撞一客车翻入山沟,造成
24人死亡。
第二章
零件失效分析工作内容和意义
一、零件失效分析
零件失效分析:
判断零件失效性质、分析零件失效原因、研究零件失效的预防措施的技术工作。
二、零件失效分析工作内容
1、判断零件失效性质
畸变失效、断裂失效、磨损失效、腐蚀失效。
2、分析零件失效原因
设计、材料、加工、装配、使用、维护。
3、研究零件失效的预防措施,保障产品质量
修改设计?
更换材料?
改进加工?
合理装配?
正确使用?
及时维护?
三、零件失效分析意义
产品质量是企业的生命线。
提高产品质量、延长零部件的使用寿命,是企业的立足之本。
1、减少和预防同类机械零件的失效现象重复发生,保障产品质量,提高产品竞争力。
2、分析机械零件失效原因,为事故责任认定、侦破刑事犯罪案件、裁定赔偿责任、保险业务、修改产品质量标准等提供科学依据。
3、为企业技术开发、技术改造提供信息,增加企业产品技术含量,从而获得更大的经济效益。
第三章
零件失效形式
一、畸变失效
1、弹性畸变失效
不恰当的弹性变形量导致失效。
2、塑性畸变失效
外加应力超过零件材料的屈服极限时发生明显的塑性变形(永久变形)。
3、翘曲畸变失效
尺寸与方向上产生复杂变形,形成翘曲,导致失效。
翘曲畸变往往是由温度、外加载荷、受力截面、材料组成等不均匀性引起。
特别是高温所导致的形状翘曲最为严重。
二、断裂失效
断裂失效机械零件因断裂而产生的失效。
1、断裂失效的分类
塑性断裂、脆性断裂、疲劳断裂、蠕变失效断裂
例1:
客车空气压缩机皮带轮断裂失效
例2:
汽车板簧断裂失效
三、磨损失效
磨损:
相互接触的一对金属表面,相对运动时金属表面不断发生损耗或产生塑性变形,使金属表面状态和尺寸改变的现象。
四、腐蚀失效
腐蚀是金属暴露于活性介质环境中而发生的一种表面损耗。
它是金属与环境介质之间发生的化学和电化学作用的结果(化学腐蚀、电化学腐蚀)。
某客车储气罐放水阀弹簧破断,刹车失灵,造成严重事故。
第四章
零件失效基本原因
一、设计原因
为了保证产品质量,必须精心设计。
根据零件工作条件、可能发生的失效形式,提出技术指标,确定合适的结构、尺寸、材料。
如结构设计不合理,或尺寸设计有误,或材料设计错误,则机械设备或零件将不能使用或过早失效。
二、材质原因
1、用材不当:
所用材料机械性能达不到设计要求而导致失效。
2、材质缺陷化学成分超差、晶粒粗大、夹杂物多、存在裂纹、气孔。
三、制造(工艺)原因
工艺过程中产生的缺陷是零件失效的重要原因。
1、零件在铸造过程中产生的气孔、疏松、夹渣。
2、锻造过程中产生的夹层、冷热裂纹。
3、焊接过程中未焊透、偏析、冷热裂纹。
焊接裂纹热处理淬裂磨削裂纹
4、机加工过程的尺寸公差和表面粗糙度不合适。
5、热处理产生的缺陷,如淬裂、硬度不足、回火脆性。
6、精加工磨削中的磨削裂纹等。
四、安装调试原因
安装过程达不到要求的质量指标,导致零件失效。
1、啮合传动件(齿轮、杆、螺旋等)的间隙不合适(过松或过紧)。
2、连接零件必要的"防松"不可靠。
3、铆焊结构的必要探伤检验不细致。
4、润滑与密封装置不良。
5、安装后,未按规定进行跑合。
五、运转、维修原因
1、不正确的运转工况超载、超速导致零件失效。
2、润滑条件未保证润滑剂和润滑方法不合适。
3、忽视维修未进行定期大、中、小检修和必要的保养
六、人的原因
1、人的素质工作马虎、责任性不强,违反操作规程。
2、人的知识水平安全知识缺乏、使用和操作基本知识不够。
3、人的道德只为赚钱,不负责任,机械产品有安全隐患。
4、人为破坏
第五章
失效分析步骤
一、事故调查
1、现场调查
2、失效件的收集
3、走访当事人和目击者
二、资料搜集
1、设计资料
2、材料资料
3、工艺资料
4、使用资料
三、失效分析工作流程
原则:
先简单后复杂,先宏观后微观。
1、失效机械的结构分析
2、失效件的粗视分析
3、失效件的微观分析
4、失效件材料的成分分析
5、失效件材料的力学性能检测
6、应力分析、测定:
用x光应力测定仪测定应力
7、失效件材料的组成相分析
8、模拟试验(必要时)
四、分析结果提交
1、提出失效性质、失效原因
2、提出预防措施(建议)
3、提交失效分析报告
第六章
失效分析技术简介
一、金相分析技术
取样、镶样、磨制、抛光、浸蚀
钢和铸铁:
硝酸酒精溶液
不锈钢:
氯化铁盐酸水溶液
铜合金:
过硫酸铵水溶液
铝合金:
氢氟酸盐酸水溶液
6、观察,分析
在金相显微镜下观察,分析金属内部的显微组织。
放大倍数:
50~1000倍。
45号钢的显微组织:
T12钢的显微组织:
二、断口分析技术
用电子显微镜观察断口形貌,分析断口特征,确定断裂性质的技术。
(1)扫描电子显微镜。
电子束在试样表面扫描,试样表面产生二次电子。
二次电子的强度、分布与试样表面形貌、成分有关。
获取二次电子信息,在显象管屏幕上显示,形成电镜图象。
得到断口电镜照片。
(2)透射电子显微镜
以电子束作照明光源,用电磁透镜聚焦,透过试样,投射到荧光屏或照相底片上,获得图象。
透射电镜观察试样制备:
(1)复型法
(2)薄膜法
三、力学性能测试技术
1、强度:
金属材料抵抗塑性变形或断裂的能力,材料的强度用拉伸试验测定。
(1)弹性极限σe材料保持弹性变形,不产生永久变形的最大应力。
(2)屈服极限(屈服强度)σs
金属开始发生明显塑性变形的抗力。
铸铁等材料没有明显的屈服现象,用条件屈服极限σ0.2表示(产生0.2%残余应变时的应力值)。
(3)强度极限(抗拉强度σb)表示金属受拉时所能承受的最大应力。
2、塑性:
断裂前材料产生永久变形的能力称为塑性。
(1)伸长率(δ):
试样拉断后,标距的伸长与原始标距的百分比称为伸长率。
(2)断面收缩率(ψ):
试样拉断后,缩颈处截面积的最大缩减量与原横断面积的百分比称为断面收缩率。
3、硬度:
材料抵抗另一硬物体压入其内的能力叫硬度,即受压时抵抗局部塑性变形的能力。
(1)布氏硬度(HB)一定直径的钢球或硬质合金球在一定载荷作用下压入试样表面。
测量压痕直径,计算硬度值。
布氏硬度计洛氏硬度计
(2)洛氏硬度(HRA、HRB、HRC)
采用金刚石压头(或钢球压头),硬度直接从硬度计表盘上读得。
根据压头的种类和总载荷的大小洛氏硬度常用表示方式有:
HRA、HRB、HRC
4、冲击韧度(ak)
许多机械零件和工具受到冲击载荷的作用。
如活塞销、锤杆、冲模和锻模等。
材料抵抗冲击载荷作用的能力称为冲击韧性。
用摆锤冲击弯曲试验来测定。
测得试样冲击吸收功,用符号Ak表示。
用冲击吸收功除以试样缺口处截面积S0,即得到材料的冲击韧度ak。
5、疲劳强度
轴、齿轮、轴承、叶片、弹簧等零件,在工作过程中各点的应力随时间作周期性的变化,这种应力称为交变应力(也称循环应力)。
在交变应力作用下,虽然零件所承受的应力低于材料的屈服点,但经过较长时间的工作而产生裂纹或突然发生完全断裂。
这种过程称为金属的疲劳。
交变应力越大,材料断裂时应力循环次数N越少。
当应力低于一定值时,试样可以经受无限周期循环而不破坏,此应力值称为材料的疲劳极限(亦叫疲劳强度),用σ-1表示。
6、断裂韧性
桥梁、船舶、大型轧辊、转子等有时会发生低应力脆断,名义断裂应力低于材料的屈服强度。
构件或零件存在裂纹。
裂纹在应力作用下失稳扩展,导致机件破断。
材料抵抗裂纹失稳扩展断裂的能力叫断裂韧性。
裂纹尖端应力场大小用应力场强度因子k1c表示。
四、理化分析测试技术
1、密度
单位体积物质的质量称为该物质的密度。
轻金属铝、镁、钛及它们的合金,用于航天航空器上。
重金属,如铁、铅、钨等。
用精密天平测定质量,用量具测定试样体积。
2、导热性
导热性通常用热导率来衡量。
热导率越大,导热性越好。
合金的导热性比纯金属差。
在热加工和热处理时,必须考虑导热性,防止材料在加热或冷却过程中形成过大的内应力,以免零件变形或开裂。
用导热仪测定热导率。
3、热膨胀性
材料随温度变化而膨胀、收缩的特性。
轴和轴瓦之间要根据其膨胀系数来控制间隙尺寸;在热加工和热处理时要考虑材料的热膨胀影响,减少工件变形和开裂。
用膨胀仪测定膨胀系数。
4、化学成分测定
组成金属材料的元素的质量分数。
光谱分析法、能谱分析法
5、耐腐蚀性
金属材料在常温下抵抗氧、水蒸气及其它化学介质腐蚀破坏作用的能力称耐腐蚀性。
碳钢、铸铁的耐腐蚀性较差;钛及其合金、不锈钢的耐腐蚀性好。
铝合金和铜合金有较好的耐腐蚀性。
耐腐蚀性能用腐蚀试验测定:
浸泡法、盐雾腐蚀法
五、微区成分分析
微区成分分析是检验热处理成分偏析及材料组成相成分的重要手段。
(1)电子探针X射线能谱仪
电子束激发样品表面(直径1微米),样品表面产生特征X射线,测量X射线能量,获得元素种类。
测量X射线波的强度,得到该元素的含量。
可测9F(氟)以上的各种元素的含量。
(2)电子探针X射线波谱仪
电子束激发样品表面,样品表面产生特征X射线。
用分光晶体把不同波长的X射线分开,检测某一X射线,测量其波长,可确定产生该X射线的元素。
测量该X射线波的强度,得到该元素的含量。
可测4Be(铍)到92U(铀)的各种元素的含量。
(3)俄歇电子能谱仪
电子束轰击样品表面,样品表面激发出表征元素和化学态的二次电子。
二次电子将能量转移给另一个能级的电子,另一个能级的电子逸出表面,这种电子称为俄歇电子。
测定俄歇电子的能量,可以确定元素种类及含量。
可以测定氢、氦以外的所有元素的种类和含量。
应用举例1:
波纹管套表面的化学组成
应用举例2:
40Cr钢调质处理后产生高温回火脆性。
用扫描电镜分析断口为沿晶断裂。
用俄歇电子能量仪分析断口,断口富集磷、锡。
用离子枪轰击断口,剥离约300-500nm,基体磷、锡含量低。
磷、锡富集于晶界,导致晶界强度降低,产生回火脆性。
六、晶体结构分析技术
晶体结构:
金属材料内部原子排列情况,微观结构。
1.体心立方晶格钼(Mo)、钨(W)、钒(V)、α-铁(α-Fe,<912℃)等。
2.面心立方晶格铝(Al)、铜(Cu)、镍(Ni)、金(Au)、银(Ag)、γ-铁(γ-Fe,912℃~1394℃)等。
3.密排六方晶格镁(Mg)、镉(Cd)、锌(Zn)、铍(Be)
化合物结构:
七、无损检测技术
利用声、光、电、射线等,在不破坏被检测零件的前提下,了解零件内部的缺陷的技术。
可检测零件内部的裂纹、夹杂物。
超声检测、磁粉检测、射线检测
1、超声检测
2、
磁粉检测:
3、射线检测:
。
八、应力分析技术
材料内部存在残余应力。
残余拉应力对材料的抗疲劳性、抗腐蚀性、尺寸稳定性有不良影响。
可用X射线应力仪测定残余应力的大小。
第七章
断裂失效分析
一、断裂失效的分类
塑性断裂、脆性断裂、疲劳断裂、蠕变失效断裂
二、断口分析方法
断口分析是断裂失效分析的关键。
金属材料的室温拉伸试样的塑性断口宏观观察,
断口分为:
F-纤维状区,R-放射状区,S-剪切唇区
三、断裂形式
(1)韧(塑)性断裂:
断裂前有明显的塑性变形。
①宏观特征宏观变形方式为颈缩,典型断口为杯锥状断口,底部成纤维状剪切断口,其平面和拉伸轴大致成45°角。
②微观特征韧窝是金属韧性断裂的微观主要特征,是塑性变形产生的显微空洞生成、长大、聚集、相互连结导致断裂留下的痕迹。
(2)脆性断裂
断裂前无塑性变形。
脆断时承受的工作应力较低,通常不超过材料的屈服强度,甚至不超过常规的许用应力,所以又称为低应力脆断。
1宏观特征:
断口一般与正应力垂直,断口表面平齐,断口边缘没有剪切"唇口"(或很小)。
②微观特征:
解理花样、沿晶断口形态。
解理断裂:
因原子间结合键的破坏而造成的穿晶断裂。
在不同高度的平行解理面之间产生解理台阶。
裂纹扩展过程中,台阶相互汇合,形成河流花样,河流的流向与裂纹扩展方向一致。
(3)疲劳断裂
在交变应力作用下,虽然零件所承受的应力低于材料的屈服点,但经过较长时间的工作而产生裂纹导致发生断裂,称金属的疲劳断裂。
1)疲劳断裂起源的位置确定:
纤微区的中心;放射花样的收敛处;人字纹的最尖顶处;断口的平坦区内;
无明显塑性变形区,或无剪切唇形貌特征区;疲劳弧形的最小半径处;
腐蚀氧化最严重的部位;台阶高差最大处。
疲劳源:
应力集中处:
工件截面尺寸突变、孔槽边缘、尖角等。
表面缺陷:
如夹砂、划痕、折迭。
内部缺陷:
如缩孔、气泡、疏松、夹杂物。
2)疲劳裂纹扩展的宏观方向的确定:
裂纹源区指向最后断裂区的方向;放射线发散的方向;纤维区指向剪切唇区的方向;与疲劳弧线相垂直的放射状条纹分散方向;人字纹的人字张开的方向; 断口的平坦区指向斜断口的方向;无塑性变形或塑性变形小的区域指向变形大的区域的方向;台阶高差减小的方向;氧化、腐蚀减轻的方向。
(4)蠕变断裂
在高温下钢的强度较低,当受一定应力作用时,变形量随时间而逐渐增大的过程,这种过程叫蠕变,产生的断裂叫做蠕变断裂。
引起零件断裂的因素多而复杂,对材料的性能需要综合考虑。
如屈服强度、塑性、断裂韧性、疲劳强度等。
四、裂纹分析方法
1、裂纹种类
1)沿晶扩展裂纹:
制造过程产生的裂纹:
铸造热裂纹、过烧引起的锻造裂纹、回火脆性裂纹、磨削裂纹、焊接裂纹。
使用中出现的裂纹:
冷热疲劳裂纹、蠕变裂纹、热脆裂纹,环境因素引起的应力腐蚀裂纹、氢脆裂纹等。
2)穿晶扩展裂纹:
因冷却速度过大、零件几何尺寸突变等引起的淬火裂纹、焊接裂纹等制造裂纹。
疲劳裂纹、解理裂纹、延性断裂裂纹等使用中形成的裂纹。
3)沿晶与穿晶混合扩展裂纹。
2、裂纹先后顺序判断方法
(1)塑性变形量大小确定法
(2)T型法
(3)裂纹分叉法
(4)断面氧化颜色法
(5)疲劳裂纹长度法
3、裂纹起始位置
裂纹的产生是应力作用的结果,其起始位置取决于应力集中和材料强度两方面综合作用的结果。
应力集中引起裂纹:
零件结构形状上易引起应力集中的部位,如工件截面尺寸突变、厚薄不均、孔槽边缘和尖锐棱角处等;材料缺陷和内应力部位,往往是裂纹出现的部位。
材质原因引起裂纹:
表面缺陷:
如夹砂、划痕、折迭、氧化、脱碳等。
内部缺陷:
如缩孔、气泡、疏松、偏析、夹杂物、白点、过热、过烧、发纹等。
4、典型裂纹特征
铸造热裂纹呈龟裂纹状,沿原始晶界延伸,裂纹内侧一般有氧化和脱碳,末端圆秃。
过热、过烧引起的锻造或热处理裂纹,往往晶粒粗大,并常在晶界处伴有析出物。
磨削裂纹一般细、浅,呈龟裂状或规则直线排列。
局部应力超过材料的强度极限所引起的裂纹,裂纹处具有明显的塑性变形痕迹。
水淬时产生的裂纹,会出现红锈。
碳钢裂纹两侧脱碳,则说明裂纹为热裂纹或裂纹后经过了热过程;
氢脆裂纹扩展过程中一般无分叉现象。
应力腐蚀裂纹往往有分叉现象。
一般沿晶扩展的裂纹与腐蚀介质的作用有关,裂纹中夹有腐蚀产物。
一般张开较大区域为裂纹的起始区。
第八章
磨损失效分析
1、粘着磨损
两个金属表面的微凸部分在高压下产生局部粘结,使材料从一个表面转移到另一表面或撕下作为磨料留在两个表面之间,这一现象称为粘着磨损。
2、磨料磨损
配合表面之间在相对运动过程中,因外来硬颗粒或表面微突体的作用造成表面损伤(被犁削形成沟漕)的磨损称为磨粒(料)磨损。
3、犁削磨损
硬材料表面的微凸点切削较软材料的表面,在较软材料的表面形成"犁沟"。
活塞环与缸套存在粘着磨损、犁削磨损(拉缸现象)、磨料磨损。
4、冲刷磨损
5、表面疲劳磨损
6、腐蚀磨损
第九章
腐蚀失效分析
腐蚀是金属暴露于活性介质环境中而发生的一种表面损耗。
它是金属与环境介质之间发生的化学和电化学作用的结果(化学腐蚀、电化学腐蚀)。
1、均匀腐蚀
2、点腐蚀
3、晶间腐蚀
第十章汽车、机械、航空、
建筑机械、电气设备零件失效分析案例
一、齿轮失效分析
齿轮的失效形式
(1)疲劳断裂
(2)齿面磨损
(3)齿面接触疲劳破坏
(4)过载断裂
案例1汽车主轴齿轮断裂失效分析
1、事故调查
汽车主轴齿轮运行约5公里时发生断裂。
材料:
20CrMnTi
工艺:
锻造-正火-机加工-渗碳(930℃2.5h)-随炉降温到840℃-油淬-回火(180℃,2h)-喷丸-研孔-冷矫正-螺纹中频退火-精加工-表面磷化。
要求:
零件表面硬度58-64HRC,心部硬度35-45HRC,
螺纹部分硬度小于等于48HRC。
渗碳层深度0.8-1.2mm。
2、粗视分析
断口平整,无剪切唇。
断口为疲劳断口。
A区为疲劳源。
C区为最后断裂区。
3、硬度测定硬度符合设计要求
4、化学成分分析化学成分符合国家标准。
5、金相分析渗碳层深度0.83mm。
符合要求。
表面组织:
高碳回火M+碳化物+残余A。
心部组织:
低碳回火M+少量B+少量F。
未见网状碳化物和脱碳现象。
组织正常。
6、断口分析
裂纹起源于花键齿顶部,呈多源特性。
花键齿表面存在大量细小的周向裂纹。
电镜高倍观察,近外表面的断裂面处存在腐蚀产物。
能谱分析含较高的磷。
7、结论
(1)近外表面的断裂面处存在较高的磷。
表明零件磷化前表面已存在裂纹。
裂纹是在冷矫正时产生。
螺纹退火时氧化变色。
(2)汽车运行时产生弯矩与冲击,裂纹扩展而断裂。
8、质量保障措施
(1)控制最终热处理时的弯曲变形。
淬火时采用垂直吊装。
(2)渗碳后进行冷矫正,此时硬度低,塑性好。
(3)改进工艺:
锻造-正火-机加工-渗碳(930℃,2.5h)-随炉降温到500℃出炉空冷-冷矫正-600℃预热-810℃油淬-回火-(200℃,3-5h)-喷丸-研孔--螺纹中频退火-精加工-表面磷化。
案例2重型载货汽车后桥主动锥齿轮断裂失效分析
1、事故调研
汽车后桥主动锥齿轮在小端断裂。
材料:
22CrMoH钢
热处理:
920-930℃渗碳—预冷,840-850℃淬火—180℃低温回火,6h
要求:
渗碳淬火硬化层深度1.7-2.1mm
金相组织:
碳化物1-5级,残余A1-5级。
齿轮表面硬度:
60-64HRC。
齿轮心部硬度:
30-40HRC。
2、宏观观察
主动锥齿轮与被动锥齿轮啮合偏向于主动锥齿轮的小端,距大端20-25mm没有啮合痕迹。
主动锥齿轮受力偏向于小端,导致主动锥齿轮小端受力过高。
3、成分分析与淬透性测定
22CrMoH钢淬透性:
J15=36-42HRC。
成分与淬透性符合标准。
4、硬度测定
表面硬度:
60-62HRC,心部硬度:
36-37HRC。
硬度符合要求。
5、金相分析
渗碳淬火硬化层深度1.75mm,碳化物3级,残余A3级。
符合技术要求
6、断口分析
断口为疲劳断口。
疲劳源在主动齿轮工作面的齿根部。
此处弯曲应力最大。
发生弯曲疲劳。
7、结论
主动锥齿轮与被动锥齿轮安装、配合时不精确,啮合区域偏向于主动锥齿轮的小端,主动锥齿轮小端受力过高。
导致轮齿根部产生疲劳裂纹,使齿破断。
8、预防措施
(1)正确安装、调试主动锥齿轮与被动锥齿轮的啮合位置(调整垫A、B)。
保证齿轮工作状态良好。
防止主动锥齿轮受力偏移,避免齿轮局部地方过载。
(2)齿轮加工铣齿时保证齿根圆滑过渡,避免刀痕引起疲劳源。
(3)汽车运行防止严重超载。
避免齿轮受力过大,防止断裂。
案例3主减速器从动斜齿轮断裂失效分析
1、粗视分析
4吨载重卡车运行3000多公里其主减速器从动斜齿轮突然断裂。
检修发现从动齿轮紧靠油孔的2个轮齿崩断。
其余齿顶部不同程度崩块和挤伤。
断齿断口为疲劳断口。
疲劳源位于油孔边缘的齿根部。
此处弯曲应力最大。
2、材料及热处理
材料:
20CrMn钢
热处理要求:
渗碳淬火硬化层深度1.3-1.5mm。
渗碳层表面不允许有网状碳化物。
齿轮表面硬度:
56-58HRC,齿轮心部硬度:
30-45HRC
3、金相分析断齿表面层存在夹杂和裂纹。
齿表面层组织为回火M+条块状F。
表明渗碳层碳含量不足。
齿心部组织为粗大回火M+少量S。
轮齿根部有较深的刀痕和微裂纹。
4、结论
(1)齿表面渗碳层碳含量不足。
淬火后出现铁素体。
导致表面抗弯强度、弯曲疲劳强度低。
(2)材料含夹杂物较多、尺寸较大。
(3)齿根部有较深的刀痕和微裂纹。
疲劳源在齿轮工作面的齿根部。
此处弯曲应力最大。
发生弯曲疲劳。
5、质量保障措施
(1)选用夹杂物含量少的优质渗碳钢。
(2)提高齿轮加工精度。
铣齿时保证齿根圆滑过渡,避免刀痕引起疲劳源。
(3)进行正确的渗碳、淬火和回火。
保证轮齿获得合格的表面组织和心部组织。
保障轮齿的抗弯强度、弯曲疲劳强度。
二、轴类失效分析
(1)长期交变载荷下的疲劳断裂。
(包括扭转疲劳和弯曲疲劳断裂)。
(3)大载荷或冲击载荷引起的过量变形、断裂;
(4)表面过度磨损。
案例4柴油机曲轴断裂失效分析
1、粗视分析
进口万吨级远洋货轮柴油机曲轴材料为35CrMo钢,曲轴整体锻造。
曲轴在第2曲臂处断裂。
断裂部位在曲臂与主轴的直角处。
断口宏观形貌具有疲劳断口特征。
疲劳源在曲臂与主轴的过渡圆弧处。
2、显微分析
曲臂与