汽车左转向节的机械加工工艺规程及工艺夹具设计.docx
《汽车左转向节的机械加工工艺规程及工艺夹具设计.docx》由会员分享,可在线阅读,更多相关《汽车左转向节的机械加工工艺规程及工艺夹具设计.docx(35页珍藏版)》请在冰豆网上搜索。
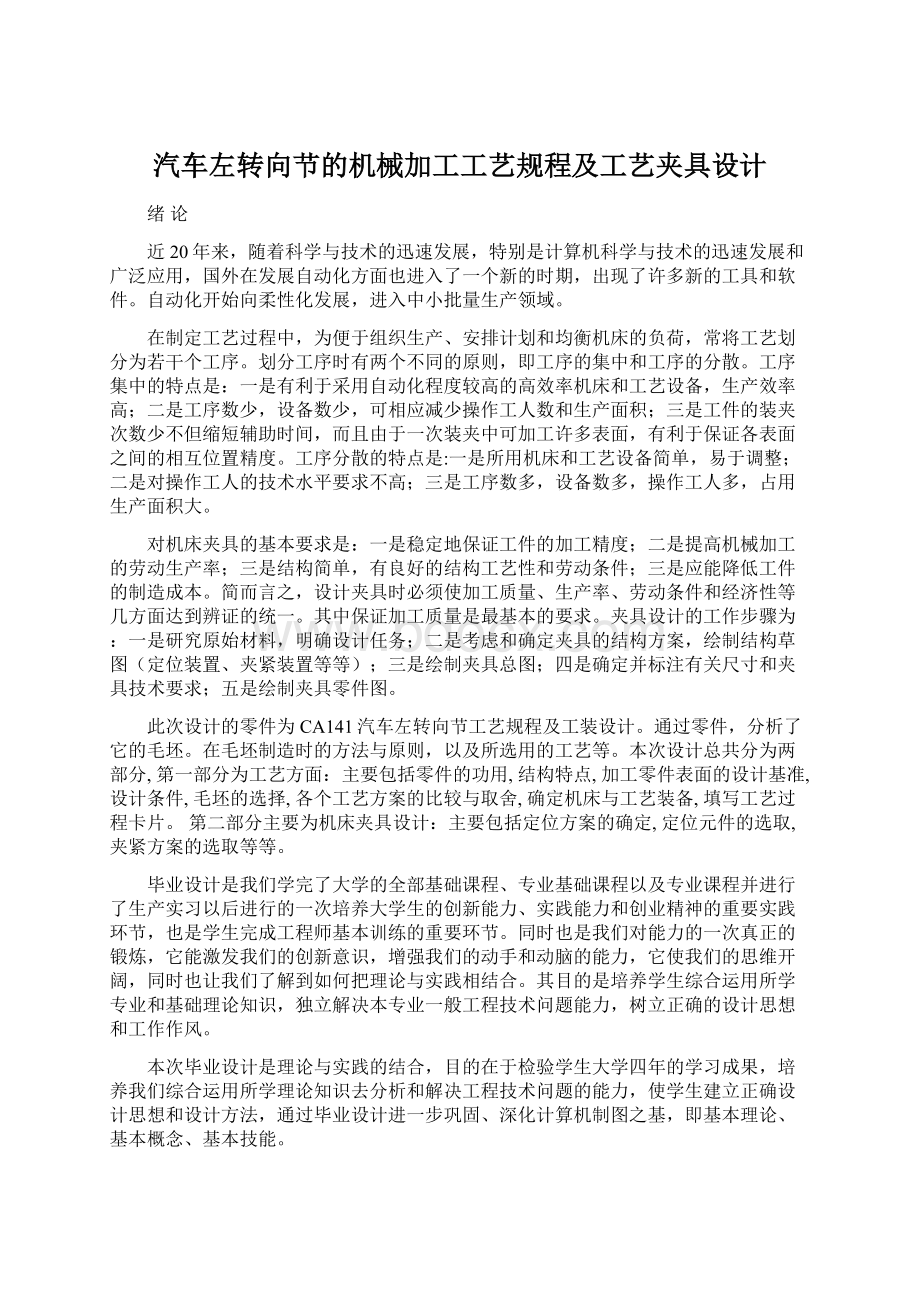
汽车左转向节的机械加工工艺规程及工艺夹具设计
绪论
近20年来,随着科学与技术的迅速发展,特别是计算机科学与技术的迅速发展和广泛应用,国外在发展自动化方面也进入了一个新的时期,出现了许多新的工具和软件。
自动化开始向柔性化发展,进入中小批量生产领域。
在制定工艺过程中,为便于组织生产、安排计划和均衡机床的负荷,常将工艺划分为若干个工序。
划分工序时有两个不同的原则,即工序的集中和工序的分散。
工序集中的特点是:
一是有利于采用自动化程度较高的高效率机床和工艺设备,生产效率高;二是工序数少,设备数少,可相应减少操作工人数和生产面积;三是工件的装夹次数少不但缩短辅助时间,而且由于一次装夹中可加工许多表面,有利于保证各表面之间的相互位置精度。
工序分散的特点是:
一是所用机床和工艺设备简单,易于调整;二是对操作工人的技术水平要求不高;三是工序数多,设备数多,操作工人多,占用生产面积大。
对机床夹具的基本要求是:
一是稳定地保证工件的加工精度;二是提高机械加工的劳动生产率;三是结构简单,有良好的结构工艺性和劳动条件;三是应能降低工件的制造成本。
简而言之,设计夹具时必须使加工质量、生产率、劳动条件和经济性等几方面达到辨证的统一。
其中保证加工质量是最基本的要求。
夹具设计的工作步骤为:
一是研究原始材料,明确设计任务;二是考虑和确定夹具的结构方案,绘制结构草图(定位装置、夹紧装置等等);三是绘制夹具总图;四是确定并标注有关尺寸和夹具技术要求;五是绘制夹具零件图。
此次设计的零件为CA141汽车左转向节工艺规程及工装设计。
通过零件,分析了它的毛坯。
在毛坯制造时的方法与原则,以及所选用的工艺等。
本次设计总共分为两部分,第一部分为工艺方面:
主要包括零件的功用,结构特点,加工零件表面的设计基准,设计条件,毛坯的选择,各个工艺方案的比较与取舍,确定机床与工艺装备,填写工艺过程卡片。
第二部分主要为机床夹具设计:
主要包括定位方案的确定,定位元件的选取,夹紧方案的选取等等。
毕业设计是我们学完了大学的全部基础课程、专业基础课程以及专业课程并进行了生产实习以后进行的一次培养大学生的创新能力、实践能力和创业精神的重要实践环节,也是学生完成工程师基本训练的重要环节。
同时也是我们对能力的一次真正的锻炼,它能激发我们的创新意识,增强我们的动手和动脑的能力,它使我们的思维开阔,同时也让我们了解到如何把理论与实践相结合。
其目的是培养学生综合运用所学专业和基础理论知识,独立解决本专业一般工程技术问题能力,树立正确的设计思想和工作作风。
本次毕业设计是理论与实践的结合,目的在于检验学生大学四年的学习成果,培养我们综合运用所学理论知识去分析和解决工程技术问题的能力,使学生建立正确设计思想和设计方法,通过毕业设计进一步巩固、深化计算机制图之基,即基本理论、基本概念、基本技能。
毕业设计的范围涉及大学四年所学的专业基础课及专业课、选修课内容,知识含量大、跨度仅限于机械制造范围。
设计题目由指导教师提供,其设计内容均由学生自行编排,在巩固专业知识之余意在培养思考、解决问题的能力,同时提倡创新精神。
就个人而言,我通过这次毕业设计一方面能进一步培养我独立思考的能力,另一方面能提高我与同学们互助协作的能力,为以后工作打下良好基础,为伟大祖国建设贡献我的力量。
由于本人能力有限,经验不足,设计过程中有不足之处,希望各位老师给予指教。
我主要的是完成工艺的安排和夹具的设计,夹具是加工过程中最重要的一个组成部分,很多工件由于形状和加工要求等等特殊的原因必须要使工件很好的定位后才能进行加工,所以也就出现了夹具以及专用的夹具。
1零件的分析
1.1零件的作用
转向节(羊角)是汽车转向桥上的主要零件之一,转向节的功用是承受汽车前部载荷,支承并带动前轮绕主销转动而使汽车转向。
在汽车行驶状态下,它承受着多变的冲击载荷,因此,要求其具有很高的强度。
转向节形状比较复杂,集中了轴、套、盘环、叉架等四类零件的结构特点,主要由支承轴颈、法兰盘、叉架三大部分组成。
支承轴颈的结构形状为阶梯轴,其结构特点是由同轴的外圆柱面、圆锥面、螺纹面,以及与轴心线垂直的轴肩、过渡圆角和端面组成的回转体;法兰盘包括法兰面、均布的连接螺栓通孔和转向限位的螺纹孔;叉架是由转向节的上、下耳和法兰面构成叉架形体的。
零件的叉头部位上有两个mm的孔,用以连接转向节主销和滚子轴承,使前轮可以绕主销偏转一定角度进而起到转向的作用。
法兰面上有6的螺钉孔以及2M161.5-6H的螺纹孔,通过螺钉将法兰面与制动器的制动盘连接在一起。
转向节的轴颈通过轮毂轴承与轮毂相连接
内开档部位mm的轴承窝,用以与汽车前桥大梁连接,实现转向动作。
叉架部位带键槽的两个锥形孔用以连接,上孔与转向节臂连接,传递转向时所需的力和扭矩,下孔与梯形臂相连接,通过横向拉杆进而于右侧转向节相连接,左右转向节协调,实现同步转向。
转向节在整个机械转向系统中的位置如下图。
1.2零件的工艺分析
转向节集中了轴、套、盘环、叉架等四类零件的结构特点。
形状较为复杂,如下图:
转向节按三部分进行精度分析,它们之间存在着一定的位置度要求。
现分述如下:
1.2.1轴颈部分
该组加工表面呈阶梯状分布,故称阶梯轴,加工表面包括:
尺寸为mm的轴颈
及其倒角;尺寸为mm的轴颈
及其倒角,同时与轴颈
之间的环形槽;尺寸为39mm的轴颈
;小径为46mm,大径为mm的轴颈
;尺寸为的轴颈
及其圆角;尺寸为95mm的轴颈
;尺寸为的六个螺钉孔以及尺寸为M16的两个限位螺钉孔。
其中主要加工表面分别有:
轴颈
、轴颈
以及轴颈
的左端面(刹车盘止口),三者的表面粗糙度Ra值均不大于0.8,轴颈
的表面粗糙度Ra值不大于12.5。
R7-1mm处是受力集中部位,要求有高的强度,mm油封轴颈端面易磨损,要求表面硬度高,因此,在此区域采用中频淬火,淬深3~6mm,硬度53~55HRC。
因淬火层深,区域大易产生淬火裂纹,对淬火工艺要求极为严格。
在轴颈端头有长29mm、M301.5h6的螺纹,为了装螺母锁环,在螺纹全长上铣平台,保证尺寸mm。
1.2.2法兰面部分
法兰面其上有对称均布的6mm的螺钉孔。
限位螺钉孔2M161.5-6H与轴心线在同一水平面内,距离87.5mm。
1.2.3叉架部分
转向节的上下耳和法兰面构成叉架形体。
(1)主销孔
主销孔尺寸要求mm,是长230.5mm的断续长孔,最大实体状态同轴度不大于0.012mm,与轴心线的位置度不大于0.3mm,到叉架底面距离56mm。
(2)轴承窝座
轴承窝是放置止推轴承的,尺寸为mm,及67mm的沉头孔组成,端面与上耳内端面的距离mm,对主销孔的垂直度不大于0.05mm。
由于空间位置决定轴承窝座的加工只能采用以主销孔定位锪窝座的加工方法,因工艺系统的累计误差大于形位公差的要求,因此垂直度0.05mm不易保证。
(3)锥孔
锥孔小径为29mm,锥度1:
8,孔长50mm,小端面与量规不齐度为0.03mm,锥度与塞规着色面积不小于75%。
上耳外端面距锥孔中心线距离为32mm,两锥孔距离为163.5mm。
至主销孔中心线距离为44mm,在加工中受锥铰刀制造锥角误差和对刀误差的影响,锥孔与塞规着色面积不以达到75%。
叉架部分对表面粗糙度有较高要求的=的加工表面有:
上下耳外端面,两锥孔外端面表面粗糙度Ra均不大于12.5;主销孔内表面及沉头孔、锥孔键槽端面表面粗糙度Ra值不大于6.3;锥孔及锥孔键槽内表面粗糙度Ra值均不大于1.6。
1.2.4位置精度要求
上述加工表面之间有着一定的位置要求,主要是:
(1)mm主销孔与轴颈的轴心线位置度公差为0.3mm。
(2)mm断续孔的同轴度公差为0.012mm。
(3)叉部内开档的端面与mm孔的中心线的垂直度公差为0.05mm。
(4)尺寸为95mm轴颈
的左端面(刹车盘止口)与阶梯轴中心线的垂直度公差为0.01mm.。
(5)mm孔的端面与mm孔的垂直度公差为0.1mm。
(6)6螺钉孔轴心线的位置度公差为0.15mm。
(7)锥孔键槽槽宽的中心线与锥孔的中心线偏转角度为30°,锥孔键槽的对称度公差为0.02mm。
(8)mm的轴颈
与中轴线的同轴度公差为0.01mm。
(9)的轴颈
与中轴线的同轴度公差为0.01mm。
(10)950.03mm的轴颈
与中轴线的同轴度公差为0.03mm。
由以上分析可知,对于这些加工表面而言,可以先加工其中一组表面,然后借助专用夹具加工其他组表面,并且保证它们之间的位置精度要求。
2工艺规程设计
2.1确定毛坯的制造形式
零件材料为40MnB调质。
考虑到汽车在行驶过程中要经常转向,零件在整个工作过程中经常承受交变载荷和冲击性载荷,因此应该选用锻件,以使金属纤维尽量不被切断,保证零件工作可靠。
由于零件的年产量为120000件,已达到大批生产的水平,而且零件的尺寸不大,故可采用模锻成型。
模锻有以下优点:
1.锻件的内部组织结构坚实,可获得较高的强度。
2.锻件的废品少,因为锻件没有疏松、表面杂质、内部裂纹的缺陷。
3.制成的小公差工件可以减少机加工工时。
4.锻件的表面质量高。
5.生产效率高。
考虑到经济性和实用性,采用模锻成型提高了生产率,保证加工精度,符合实际生产的要求。
2.2基面的选择
零件左部位阶梯轴,中部为法兰盘,右部位叉部。
零件存在不加工表面。
2.2.1定位基准的选择
在工艺规程设计中,正确选项定位基准,对保证零件技术要求、合理安排加工顺序有着至关重要的影响。
定位基准有粗基准和精基准之分,用毛培上未经加工的表面做定位基准,这种定位基准称为粗基准。
用加工过的表面作定位基准,这种定位基准称为精基准。
在选择定位基准时应根据零件的加工要求选择精基准,然后再考虑选用哪一组表面作为粗基准才能把精基准加工出来。
2.2.2粗基准的选择
粗基准的选择原则:
1.保证零件加工表面相对于不加工表面具有一定的位置精度的原则。
2.合理分配加工余量的原则。
3.便于装夹的原则。
4.粗基准一般不得重复使用的原则。
当零件有不加工表面应以这些不加工表面作为粗基准;若零件有若干个不加工表面时,则应以与加工表面要求相对位置精度较高的不加工表面作为粗基准。
对于一般的轴类零件而言,以外圆作为粗基准是完全合理的,但对本零件来说,它是个异型件,如果以阶梯轴的的轴颈
外圆表面(或mm的轴颈
外圆)表面作基准(四点定位),则可能造成这一组内外圆柱表面与零件的叉部相对的位置要求及加工精度无法达到。
现选取叉部上、下耳锥孔不加工的外轮廓表面和法兰面作为粗基准,利用一组专用夹具,气动夹紧,达到完全定位。
2.2.3精基准的选择
1.基准重合原则应尽可能选择加工表面的设计基准为精基准,这样可以避免由于基准不重合引起的定位误差。
2.统一基准原则应尽可能选择用同一组精基准加工工件上尽可能多的加工表面,以保证各加工表面的相对位置关系。
3.互为基准原则当工件上两个加工表面之间的位置精度要求比较高时,可采用两个表面互为基准反复加工的方法。
4.自为基准原则一些表面的精加工工序,要求加工余量小而均匀,常以加工表面自身为精基准。
精基准的选择原则:
应有利于保证加工精度,并使工件装夹方便,在选择时主要注意基准重合、基准统一原则,当设计基准与工序基准不重合时,应进行尺寸换算。
转向节轴颈中心线和主销孔中心线以及两中心线交点是零件的设计基准,也是所有加工表面的测量基准,因此在加工过程中均以中心线和精加工后的支承轴颈及主销孔作为定位基准。
2.3工艺规程的设计原则
(1)必须可靠保证零件图纸上所有技术要求的实现,即保证质量,并要提高工作效率。
(2)保证经济上的合理性,即要成本低,消耗小。
(3)保证良好的安全工作条件,尽量减轻工人的劳动强度,保障生产安全,创造良好的工作环境