PE250×400颚式破碎机毕业实习报告.doc
《PE250×400颚式破碎机毕业实习报告.doc》由会员分享,可在线阅读,更多相关《PE250×400颚式破碎机毕业实习报告.doc(17页珍藏版)》请在冰豆网上搜索。
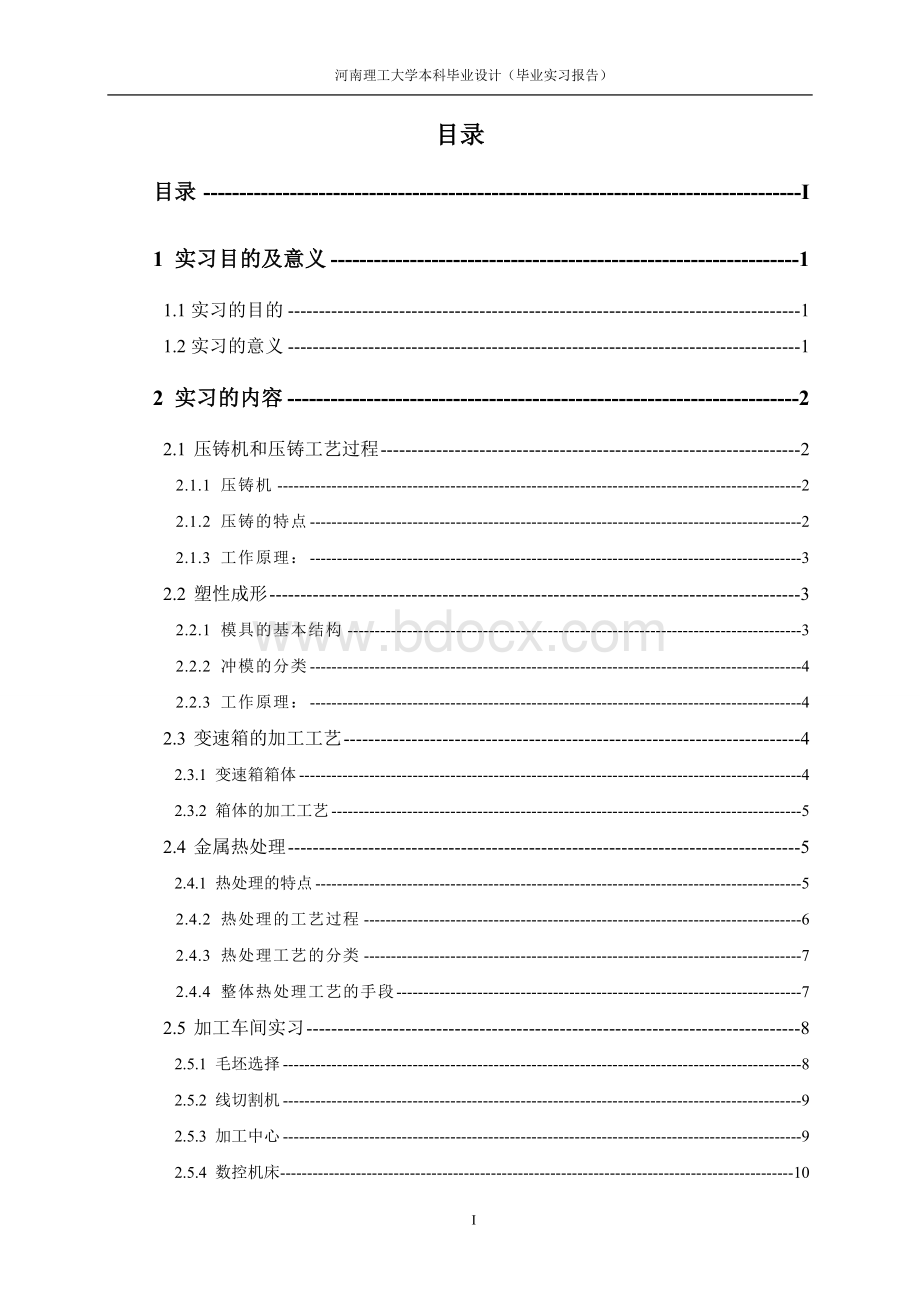
河南理工大学本科毕业设计(毕业实习报告)
目录
目录 I
1实习目的及意义 1
1.1实习的目的 1
1.2实习的意义 1
2实习的内容 2
2.1压铸机和压铸工艺过程 2
2.1.1压铸机 2
2.1.2压铸的特点 2
2.1.3工作原理:
3
2.2塑性成形 3
2.2.1模具的基本结构 3
2.2.2冲模的分类 4
2.2.3工作原理:
4
2.3变速箱的加工工艺 4
2.3.1变速箱箱体 4
2.3.2箱体的加工工艺 5
2.4金属热处理 5
2.4.1热处理的特点 5
2.4.2热处理的工艺过程 6
2.4.3热处理工艺的分类 7
2.4.4整体热处理工艺的手段 7
2.5加工车间实习 8
2.5.1毛坯选择 8
2.5.2线切割机 9
2.5.3加工中心 9
2.5.4数控机床 10
2.6汽车变速箱主壳体压铸 10
2.6.1汽车变速箱主壳体的压铸工艺 10
2.6.2汽车变速箱主壳体压铸模的模具结构设计 11
3实习总结 14
4参考文献 15
15
1实习目的及意义
1.1实习的目的
毕业实习是本专业学生的一门主要实践性课程。
是学生将理论知识同生产实践相结合的有效途径,是增强学生的群众性观点、劳动观点、工程观点和建设有中国特色社会主义事业的责任心和使命感的过程。
通过毕业实习,使学生学习和了解压铸工艺、数控技术、零件深加工等方面的一系列知识,培养学生树立理论联系实际的工作作风,以及生产现场中将科学的理论知识加以验证、深化、巩固和充实。
并培养学生进行调查、研究、分析和解决工程实际问题的能力,为后继专业课的学习、课程设计和毕业设计打下坚实的基础。
通过毕业实习,拓宽学生的知识面,增加感性认识,把所学知识条理化系统化,学到从书本学不到的专业知识,并获得本专业国内、外科技发展现状的最新信息,激发学生向实践学习和探索的积极性,为今后的学习和将从事的技术工作打下坚实的基础。
1.2实习的意义
毕业实习是与课堂教学完全不同的教学方法,在教学计划中,毕业实习是课堂教学的补充。
课堂教学中,教师讲授,学生领会,而毕业实习则是在教师指导下由学生自己向生产向实际学习。
通过现场的讲授、参观、座谈、讨论、分析、作业、考核等多种形式,一方面来巩固在书本上学到的理论知识,另一方面,可获得在书本上不易了解和不易学到的生产现场的实际知识,使学生在实践中得到提高和锻炼。
毕业实习是教育教学体系中的一个不可缺少的重要组成部分和不可替代的重要环节。
它是与今后的职业生活最直接联系的,学生在毕业实习过程中将完成学习到就业的过渡,因此毕业实习是培养技能型人才,实现培养目标的主要途径。
它不仅是校内教学的延续,而且是校内教学的总结。
可以说,没有毕业实习,就没有完整的教育。
学校要提高教育教学质量,在注重理论知识学习的前提下,首先要提高毕业实习管理的质量。
毕业实习教育教学的成功与否,关系到学校的兴衰及学生的就业前途,也间接地影响到现代化建设。
2实习的内容
2.1压铸机和压铸工艺过程
2.1.1压铸机
压力铸造(简称压铸)的实质是在高压作用下,使液态或半液态金属以较高的速度充填压铸型型腔,并在压力下成型和凝固而获得铸件的方法。
1)压铸机分类:
根据压室工作条件不同,分为冷压室压铸机和热压室压铸机两类。
热压室压铸机的压室与坩埚连成一体,而冷压室压铸机的压室是与坩埚分开的。
冷压室压铸机又可分为立式和卧式两种,目前以卧式冷压室压铸机应用较多。
(一)压铸模结构组成
定模:
固定在压铸机定模安装板上,有直浇道与喷嘴或压室联接
动模:
固定在压铸机动模安装板上,并随动模安装板作开合模移动合模时,闭合构成型腔与浇铸系统,液体金属在高压下充满型腔;开模时,动模与定模分开,借助于设在动模上的推出机构将铸件推出.
(二)压铸模结构根据作用分类:
型腔:
外表面直浇道(浇口套)
成型零件:
浇注系统模浇道(镶块)
型芯:
内表面内浇口(涂料)
(三)导准零件:
导柱;导套
(四)推出机构:
推杆(顶针),复位杆,推杆固定板,推板,推板导柱,推板导套.
(五)侧向抽芯机构:
凸台;孔穴(侧面),锲紧块,限位弹簧,螺杆.
(六)排溢系统:
溢浇槽,排气槽.
(七)冷却系统
(八)支承零件:
定模;动模座板,垫块(装配,定位,安装作用)
2.1.2压铸的特点
1)压铸件尺寸精度高,表面质量好,尺寸公差等级为IT11~IT13,表面粗糙度Ra值为6.3~1.6μm,可不经机械加工直接使用,而且互换性好。
可以压铸壁薄、形状复杂以及具有很小孔和螺纹的铸件,如锌合金的压铸件最小壁厚可达0.8mm,最小铸出孔径可达0.8mm、最小可铸螺距达0.75mm。
还能压铸镶嵌件。
2)压铸件的强度和表面硬度较高。
压力下结晶,加上冷却速度快,铸件表层晶粒细密,其抗拉强度比砂型铸件高25%~40%。
3)生产率高,可实现半自动化及自动化生产。
4)不足:
气体难以排出,压铸件易产生皮下气孔,压铸件不能进行热处理,也不宜在高温下工作;金属液凝固快,厚壁处来不及补缩,易产生缩孔和缩松;设备投资大,铸型制造周期长、造价高,不宜小批量生产。
2.1.3工作原理:
成型前,模具在注射机合模装置的作用下闭合并被锁紧。
成型时,金属液从注浇口套及分型面上的流道进入型腔并经过保压、补缩和泠却定型后,注射机的合模装置便带动动模左退,从而使动模与定模从分型面分开。
当动模开启到一定位置时,由推杆、拉料杆、推杆固定板和推板组成的推出机构将在注射机合模装置的顶杆作用下与动模其他部分产生相对运动,于是制件和流道凝料便会被推杆和拉料杆从型芯和分型面流道中推出脱落,从而完成一个成型过程。
2.2塑性成形
2.2.1模具的基本结构
模具的类型虽然很多,但任何一副冲模都是由上模和下模两部分组成。
上模通过模柄或上模座安装在压机的滑块上,可随滑块上下运动,是冲模的活动部分;下模通过下模座固定在压机工作台或垫板上,是冲模的固定部分。
1)上模的组成:
上模由模柄、上模座、垫板、凸模固定板、冲孔凸模、落料凹模、推件装置(由打杆、推板1、连接推杆和推块构成)、导套及联接用螺钉和销钉等零部件组成。
2)下模的组成:
下模由凸凹模、卸料装置(由卸料板、卸料螺钉、弹簧构成)、导料销与、挡料销、凸凹模固定板、垫板、下模座、导柱及联接用螺钉和销钉等零部件组成。
3)工作原理:
工作时,条料沿导料销、送至挡料销定位,开动压力机,上模随滑块向下运动,具有锋利刃口的冲孔凸模落料凹模与凸凹模一起穿过条料使制件和冲孔废料与条料分离而完成冲裁工作。
滑决带动上模回升时,卸料装置将箍在凸凹模上的条料卸下,推件装置将卡在落料凹模与冲孔凸模之间(即箍在冲孔凸模上)的制件推落在下模面上,而卡在凸凹模内的冲孔废料是在一次次冲裁过程中由冲孔凸模逐次从凸凹模内向下推出的。
将推落在下模上面的制件取走后又可进行下一次冲压循环。
2.2.2冲模的分类
根据各零部件在模具中所起的作用不同,一般又可将冲模主要分成以下几个部分:
1)工作零件:
直接使坯料产生分离或塑性成形的零件,
2)定位零件:
确定坯料或工序件在冲模中正确位置的零件,
3)压料、卸料零件:
这类零件起压住坯料的作用,并保证把箍在凸模上或卡在凹模内的废料或制件卸下,以保证冲压工作能继续进行,如上图所示中的卸料板、卸料螺钉、弹簧、打杆、推板、连接推杆、推件块。
4)导向零件:
确定上、下模的相对位置并保证运动导向精度的零件。
5)固定零件:
将上述各类零件固定在上、下模上以及将上、下模固定在压机上的零件,
6)其他零件除上述零件以外的零件,如紧固件(主要有螺钉、销钉)。
2.2.3工作原理:
成型前,模具在注射机合模装置的作用下闭合并被锁紧。
成型时,金属液从注浇口套及分型面上的流道进入型腔并经过保压、补缩和泠却定型后,注射机的合模装置便带动动模左退,从而使动模与定模从分型面分开。
当动模开启到一定位置时,由推杆、拉料杆、推杆固定板和推板组成的推出机构将在注射机合模装置的顶杆作用下与动模其他部分产生相对运动,于是制件和流道凝料便会被推杆和拉料杆从型芯和分型面流道中推出脱落,从而完成一个成型过程。
2.3变速箱的加工工艺
2.3.1变速箱箱体
箱体是机器或部件的基础零件,由它将机器或部件中的有关零件连接成一个整体,以保持正确的相互位置,彼此能协调地运动。
汽车变速箱箱体在整个变速箱总成中的功用,是保证其它零部件占据合理的正确位置,使之有一个协调运动的基础零件,其质量的优劣将直接影响到轴和齿轮等零件互相位置的准确性及变速箱总成使用的灵活性和寿命。
变速箱箱体是典型的箱体类零件,结构特点是形状复杂、薄壁(10~20mm),需加工多个平面孔系和螺孔等,且刚度低,受力、热等因素影响易产生变形。
变速箱箱体零件的工作条件比较恶劣,受载货量和行驶路面的影响,主要承受着振动和冲击力。
2.3.2箱体的加工工艺
变速箱箱体机械加工生产线的安排是先面后孔的原则,最后加工螺纹孔。
这样安排,可首先把铸件毛坯的气孔、砂眼、裂纹等缺陷在加工平面时暴露出来,以减少不必要的工时消耗。
此外,以平面为定位基准加工内孔可以保证孔与平面、孔与孔之间的相对位置精度。
螺纹预孔攻丝安排在生产线后段工序加工,能缩短工件输送距离,防止主要输送表面拉伤,变速箱箱体的机械加工工艺过程基本上分三个阶段,即粗加工、半精加工和精加工阶段。
其主要加工工序见下表:
变速箱箱体主要加工工序
序号
工艺名称
设备
(1)
铣削变速箱上盖结合面
卧式双铣头组合机床
(3)
铣削输送棘爪平面
卧式双面组合铣床
(5)
半精铣前后端面
卧式双面组合铣床
(6)
精镗轴承孔
卧式双面组合镗床
(22)
精铣倒车轴孔
卧式单面组合铣床
2.4金属热处理
2.4.1热处理的特点
金属热处理是机械制造中的重要工艺之一,与其他加工工艺相比,热处理一般不改变工件的形状和整体的化学成分,而是通过改变工件内部的显微组织,或改变工件表面的化学成分,赋予或改善工件的使用性能。
其特点是改善工件的内在质量,而这一般不是肉眼所能看到的。
为使金属工件具有所需要的力学性能、物理性能和化学性能,除合理选用材料和各种成形工艺外,热处理工艺往往是必不可少的。
钢铁是机械工业中应用最广的材料,钢铁显微组织复杂,可以通过热处理予以控制,所以钢铁的热处理是金属热处理的主要内容。
另外,铝、铜、镁、钛等及其合金也都可以通过热处理改变其力学、物理和化学性能,以获得不同的使用性能。
2.4.2热处理的工艺过程
热处理工艺一般包括加热、保温、冷却三个过程,有时只有加热和冷却两个过程。
这些过程互相衔接,不可间断。
这个过程可以借助陶瓷换热器来实现,陶瓷换热器的生产工艺与窑具的生产工艺基本相同,导热性与抗氧化性能是材料的主要应用性能。
它的原理是把陶瓷散热器放置在烟道出口较近,温度较高的地方,不需要掺冷风及高温保护,当窑炉温度1250-1450℃时,烟道出口的温度应是1000-1300℃,陶瓷换热器回收余热可达到450-750℃,将回收到的的热空气送进窑炉与燃气形成混合气进行燃烧,这样直接降低生产成本,增加经济效益。
陶瓷换热器在金属换热器的使用局限下得到了很好的发展,因为它较好地解决了耐腐蚀,耐高温等课题,成为了回收高温余热的最佳换热器。
经过多年生产实践,表明陶瓷换热器效果很好。
它的主要优点是:
导热性能好,高温强度高,抗氧化、抗热震性能好。
寿命长,维修量小,性能可靠稳定,操作简便。
是目前回收高温烟气余热的最佳装置。
加热是热处理的重要工序之一。
金属热处理的加热方法很多,最早是采用木炭和煤作为热源,进而应用液体和气体燃料。
电的应用使加热易于控制,且无环境污染。
利用这些热源可以直接加热,也可以通过熔融的盐或金