双层环氧粉末外涂层通用检验规程.docx
《双层环氧粉末外涂层通用检验规程.docx》由会员分享,可在线阅读,更多相关《双层环氧粉末外涂层通用检验规程.docx(29页珍藏版)》请在冰豆网上搜索。
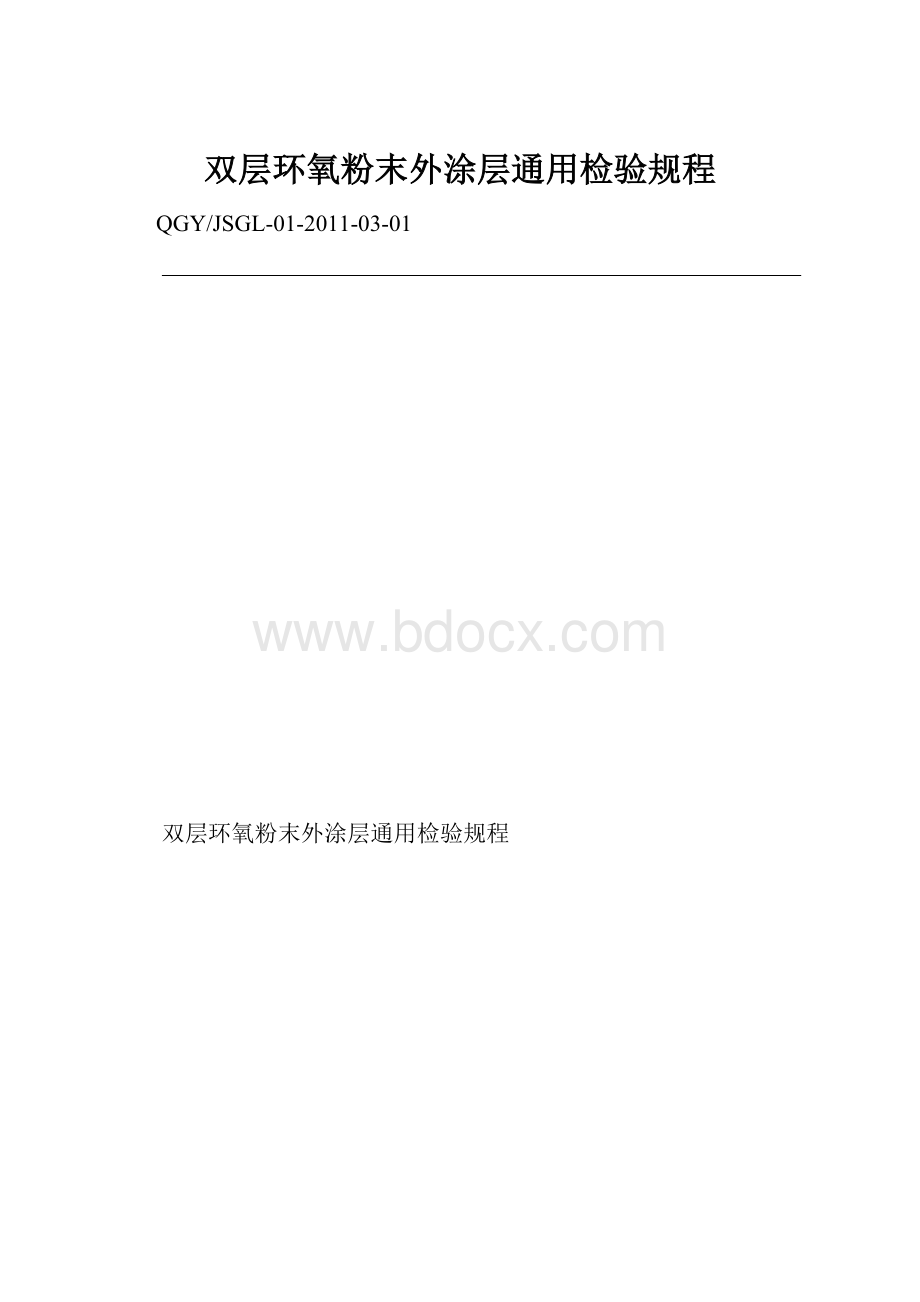
双层环氧粉末外涂层通用检验规程
QGY/JSGL-01-2011-03-01
双层环氧粉末外涂层通用检验规程
江苏给力保温管业有限公司
月11年2011
QGY/JSGL-01-2011-03-01
录目
前言1.
依据规程标准2.
防腐层结构3.
材料检验4.
防腐层材料适用性试验5
防腐层涂敷6.
质量检验7.
检验工艺流程:
8.附件13PE
QGY/JSGL-01-2011-03-01
前言1.
熔结环氧粉末分为单层和双层两种,因单层熔结环氧粉末防腐层存在着耐机械撞击
能力较弱,防水性较差等问题。
为此美国防腐公司针对防腐层的材料
依据规程标准2.
级钢管》1AGB/T9711.1-1997《石油、天然气工业输送钢管交货技术条件
《低中压锅炉用无缝钢管》GB/T3087-2008
《输送流体用无缝钢管》GB/T8163-2008
《埋地钢制管道聚乙烯防腐层技术标准》SY/T0413-2002
《熔融结合环氧粉末涂料的防腐蚀涂装》GB/T18593-2010
《压力管道安全技术监察规程——工业管道》TSGD0001-2009
《压力管道元件制造许可规则》TSGD2001-2006
《钢制管道单层熔结环氧粉末外涂层技术规范》SY/T0315-2005
《埋地钢制管道双层熔结环氧粉末外涂层技术规范》Q/CNPC38-2002
《压力管道元件型式试验规则》TSGD2002-2006
《压力管道规范——工业管道》6-2006GB/T20801.1~
》《NB/T47014-2011承压设备焊接工艺评定
QGY/JSGL-01-2011-03-01
《现场设备工业管道焊接工程施工及验收规范》GB50236-98
《涂装前钢材锈蚀等级和除锈等级》GB8923-1988
《管道防腐层检漏试验方法》SY/T0063-1999
《城市供热用螺旋埋弧焊钢管》JB/T3022-1993
《钢制对焊无缝管件》GB/T12459-2005
《钢板制对焊管件》GB/T13401-2005
《逐步检查计数抽样程序集抽样表》GB2828.1-2003
防腐层结构3
挤压聚乙烯防腐层分二层结构和三层结构两种。
二层结构的底层为胶粘剂层,外层3.1
为聚乙烯层;三层结构的底层通常为环氧粉末涂层,中间层为胶粘剂层,外层为聚乙烯层。
规定值1的规定。
焊接部位的防腐层厚度不应小于表3.2防腐层的最小厚度应符合表1
。
要求防腐层机械强度高的地区,应使用加强级。
70%的
防腐层的厚度1表
钢管公称直径DN
a环氧涂层/μm
胶粘剂层/μm
防腐层最小厚度/mm
普通级(G)
加强级(S)
DN≤100
≥120
≥170
1.8
2.5
<DN≤250100
2.0
2.7
250<<DN500
2.2
2.9
800500≤DN<
2.5
3.2
DN≥800.
3.0
3.7
QGY/JSGL-01-2011-03-01
a不适用于二层结构聚乙烯防腐层。
4.材料检验
4.1钢管
4.1.13PE埋地管所用材料必须符合相应材料标准的规定及使用安全的规范规定,并具
有生产单位合格的材料质量证明书和合格证,按规定验收合格后办理入库手续。
钢管生产单
位应具有相应级别的特种设备制造许可证。
。
,且焊缝应平滑过渡2.5mm注:
为保证挤压聚乙烯防腐层的质量,钢管焊缝的余高不应超过
4.1.2质保书的内容应齐全正确清晰并加盖单位质量检验章。
原质保书复印件必须加盖
供材单位检验章和经办人章方可有效。
4.2对钢管材料的检验
4.2.1材质检验
①无缝钢管应符合GB/T3087-2008《低中压锅炉用无缝钢管》、GB/T8163-2008《输送流
体用无缝钢管》等相关标准要求;螺旋焊钢管应符合GB/T9711.1-1997、SY/T5037-2000及
CJ/T3022-93等相关标准;并依据SY/T0413-2002和GB/T23257-2009标准要求选材。
②外购的无缝管等受压力管件必须有完整合格的质保书;其材质应符合GB/T3087-2008
及GB/T8163-2008标准相关规定要求,并与实物相符合。
③防腐层材料应符合SY/T0413-2002《埋地钢制管道聚乙烯防腐层技术标准》的相关要
求。
4.2.2外观质量检验
钢管质量证明书与实物进行核对后,还必须抽查实物,防止实物存在超标缺陷,保证管
材质量在投用前得到有效控制。
①钢管表面不得存在气泡裂纹、重皮、夹杂锈蚀等缺陷。
检查方法:
现场用卷尺、游标
卡尺等量具抽查实物。
②检验规则如表1
附表1检验规则表
检验项目
工(量)具
检验方法
外观
质量
标记
目测
根据质保书核对实物、炉批号、材质、规格及技术标准
长度
卷尺
做二点测量、每批不少于三支
QGY/JSGL-01-2011-03-01
外径
游标卡尺
做二点测量、每批不少于三支
壁厚
游标卡尺
每批不少于三支,每支不少于三点
弯曲度
米钢板尺1
钢管方向测量,每支不少于二处每批不少于三支
表面质量
目测
钢管方向测量,每支不少于二处,每批不少于三支
核对质保书中化学成分及机械性能
目测
核对质量保证书及有关标准
备注
依据标准:
GB8163-2008、GB3087-2008、CJ/T3022-93
几何尺寸检验4.2.3
①管材厚度不得小于材料要求的负偏差(用游标卡尺测量)。
②3PE埋地管的工作钢管性能和尺寸公差应符合CJ/T3022-93、GB/T3087-
2008、GB/T8163-2008或GB/T9711.1-1997的规定。
工作管的最小壁厚应符合表2的规定。
附表2mm
工作管外径
S最小壁厚
4832~
3.0
7651~
3.5
13389~
4.0
159140~
4.5
273219~
6.0
529~325
7.0
820~559
8.0
防腐层材料检验4.3
4.3.1一般规定;
1防腐层各种原材料均应有出厂质量证明书及检验报告、使用说明书、出厂合格证、生
产日期及有效期。
2防腐层各种原材料均应包装完好,按厂家说明书的要求存放。
3对每种牌(型)号的环氧粉末涂料和胶粘剂以及每种牌(型)号的聚乙烯专用料,在
使用前均应有通过国家计量认证的检验机构对其性能进行检测,性能达不到规定要求的,不
能使用。
4.3.2环氧粉末涂料的质量应符合附表3的规定,熔结环氧涂层的性能应符合附表4的
QGY/JSGL-01-2011-03-01
的规定进行质43和附表规定。
对每一生产批(不超过20t)环氧粉末涂料,均应按照附表
量复检。
)胶粘剂,应按30t的规定。
对每一生产批(不超过胶粘剂的性能应符合附表54.3.3
的规定进行质量复检。
5附表
的规定。
对每一生产批76和附表4.3.4聚乙烯专用料及其压制片材的性能应符合附表
项31、2、项和附表7的第、(不超过500t)聚乙烯专用料,应按附表6规定的第1、23
进行性能复检;对其它性能指标,有怀疑时亦可进行复检。
环氧粉末涂料的性能指标3附表
序号
项目
标性能指
法方试验
1
)粒径分布(%
筛上粉末≤3.0150μm筛上粉末≤0.2250μm
GB/T6554
2
挥发份(%)
≤0.6
GB/T6554
3
)(胶化时间(200℃)S
≥12
GB/T6554
4
)固化时间(200℃)(min
≤3
SY/T0413-2002
熔结环氧涂料的性能指标附表4
序号
项目
标指性能
法方试验
1
附着力(级)
≤2
SY/T0413-2002
2
)阴极剥熟(65℃,48h)(mm
剥离距离≤8
SY/T0413-2002
胶粘剂性能指标附表5
序号
项目
性能指标
试验方法
1
密度(g/cm3)
0.910-0.950
GB/T4474
2
熔体流动速率(190℃,
≥0.5
GB/T3682
QGY/JSGL-01-2011-03-01
)2.16kg
(g/10min)
GB/T1633≥90维卡软化点(℃)3
GB/T54704≤50脆化温度(℃)
附表6聚乙烯专用料的性能指标
序号
项目
性能指标
试验方法
1
密度(g/cm3)
≥0.940
GB/T4474
2
熔体流动速率(190℃,)2.16kg)(g/10min
≥0.12
GB/T3682
3
炭黑含量(%)
2.02.4
GB/T13021
4
)耐热老化(100℃,2400h(100℃,4800h(%)
≤35
GB/T3682
注:
1)耐热老化指标为试验前后的熔体流动速率偏差。
常温型:
试验条件为100℃,2400h;高温型:
试
验条件为100℃,4800h。
附表7聚乙烯专用料压制片的性能指标
序号
项目
性能指标
试验方法
1
拉伸强度(Mpa)
≥20
GB/T1040
2
断裂伸长率(%)
≥600
GB/T1040
3
维卡软化点(℃)
≥110
GB/T1633
4
脆化温度(℃)
≤-65
GB/T5470
5
电气强度(MV/m)
≤25
GB/T1480.1
6
)体积电阻率(Ω.m
≥1×1013
GB/T1410
7
h())耐环境应力开裂(F50
≥1000
GB/T1842
8
耐化学介质腐蚀(浸泡7d)(%)
10%HCL
≥851
SY/T0413-2002
10%NaOH
≥851
10%NaCl
≥851
9
耐紫外光老化(336h)(%)
≥801
SY/T0413-2002
QGY/JSGL-01-2011-03-01
)耐化学介质腐蚀及耐紫外光老化性能指标为试验后拉伸强度和断裂伸长率的保持率。
注:
1
防腐层材料适用性试验5
应对所选定的防腐层材料在涂敷生产线上进行防腐层材料适用性试验,并对防腐5.1.1
层性能惊醒检测。
当防腐层材料生产厂家或牌(型)号或钢管规格改变时,应重新进行适用
性试验。
适用性试验合格后,应按照适用性试验确定的工艺参数进行防腐层涂敷生产。
的规定。
98和附表5.1.2聚乙烯及防腐层性能应符合附表
按确定的工艺参数涂敷聚乙烯层(不含胶和环氧粉末涂层)进行性能检测,结果5.1.3
的规定。
8应符合附表
从防腐管或同一工艺条件下涂敷的试验管段上截取试件对防腐层整体性能进行检5.1.4
的规定9测,结果应符合附表
聚乙烯层的性能指标附表8
项目
性能指标
试验方法
拉伸强度
轴向/MPa
≥20
GB/T1040.2
/MPa周向
≥20
GB/T1040.2
偏差a/%
≤15
断裂伸长率/%
≥600
GB/T1040.2
/mm压痕硬度
(23℃)70℃)(50℃或Ь
≤0.2≤0.3
GB/T23257-2009
/h)耐环境应力开裂(F50
≥1000
GB/T1842
偏差为轴向的周向拉伸强度的差值与两者中较低者之比。
70℃。
50℃;高温型,试验条件为常温型,试验条件为
附表9防腐层的性能指标
QGY/JSGL-01-2011-03-01
项目
性能指标
试验方法
二层
三层
剥离强度/(N/cm)(20℃±10℃)(50℃±5℃)
≥70≥35
≥100(内聚破坏)≥70(内聚破坏)
GB/T23257-2009
阴极剥离(65℃,48h)
≤15
≤15
GB/T23257-2009
)30d阴极剥离(最高使用温度,
/mm
≤25
≤95
GB/T23257-2009
/%环氧粉末固化度:
固化百分率环氧粉末固化度:
玻璃化温度变化g|/℃|ΔΤ值
——
≥95≤5
GB/T23257-2009
冲击强度/(J/mm)
≥8
GB/T23257-2009
抗弯曲(-30℃,2.5°)
聚乙烯无开裂
GB/T23257-2009
6.防腐层涂敷
6.1钢管表面预处理
6.1.1在防腐层涂敷前,先清除钢管表面的油脂和污垢等附着物,并对钢管预热后进行
抛(喷)射除锈。
在进行抛(喷)射除锈前,钢管表面温度应不低于露点温度以上3℃。
除
锈质量应达到GB/T8923中规定的Sa2.5级要求,锚纹深度达到50um~90um。
钢管表面的焊
渣、毛刺等应清楚干净。
6.1.2应将钢管表面附着的灰尘及磨料清扫干净。
钢管表面的灰尘度应不低于
GB/T18570.3规定的2级。
6.1.3抛(喷)射除锈后的钢管应按GB/T18570.9规定的方法或其他适宜的方法检测钢
管表面的盐分含量,钢管表面的盐分不应超过20mg/㎡。
6.1.4钢管表面处理后应防止钢管表面受潮、生锈或二次污染。
表面处理后的钢管应在
4h内进行涂敷,超过4h或当出现返锈或表面污染时,应重新进行表面处理。
6.2在开始生产时,先用试验管段在生产线上分别依次调节预热温度及防腐层各层厚度,
QGY/JSGL-01-2011-03-01
各项参数达到要求后方可开始生产。
应用无污染的热源对钢管加热至合适的涂敷温度,最高加热温度应不明显影响钢管6.3
的力学性能。
环氧粉末的涂敷6.4
预热后的钢管先用第一组静电喷枪喷涂底层,然后用第二组静电喷枪直接喷涂面层粉末。
面层应在粉末厂家要求的延迟时间内用第二组静电喷枪喷涂在底层上。
固化时间应符合环氧粉末涂料的要求;
;外层厚度应大于或等300μm双层熔结环氧粉末外防腐层厚度:
内层厚度应大于或等于
。
800μm于500μm;总厚度应大于或等于
要1涂敷作业不应使用回收的粉末。
粉末材料回掺要求:
首先检测落地粉质量应符合表
%。
5求,其次回掺量不大于
胶粘剂涂敷应在环氧粉末胶化过程中进行。
6.5
采用侧向缠绕工艺时,应确保搭接部分的聚乙烯及焊缝两侧的聚乙烯完全轴压密实,6.6
并防止压伤聚乙烯层表面。
60℃,并确保熔结环氧涂层固化完全。
聚乙烯层包覆后应用水冷却至钢管温度不高于6.7
防腐层涂敷完成后,应出去管端部位的防腐层。
管端预留长度宜为6.8
°的倒角;聚乙烯层端部外可保留不超30~100mm150mm,且聚乙烯层端面应形成不大于
的环氧粉末涂层。
应防止防腐管端部防腐层剥离或翘起。
20mm过
质量检验7
供货商应建立一套常规的、有文件记载的完整的质量检查制度,以保证所有影响产品的
安全性、可靠性、安装操作性能以及长期使用性能的各种因素,都已经过考虑、试验、鉴定
和检验。
对本产品检验项目和试验内容应符合下列条款规定:
生产过程质量检验7.1
表面预处理之后,应对每根钢管是否有表面损伤和可能引起防腐层针孔的表面缺陷进7.1.1
行目测检查。
对可能导致防腐层漏点的表面缺陷,应打磨掉,且打磨后的壁厚应符合钢管订
货技术条件及标准的要求。
表面除锈质量和锚纹深度检验应符合下列要求:
7.1.2
规定的方法检验钢管表面预处理后的除锈质量,除锈等级应达到8923GB/T)应采用a
级。
连续生产时,应逐根检验钢管表面除锈质量;Sa2.5中规定的8923GB/T
)应采用锚纹深度测试仪或锚纹拓印膜检验钢管外表面锚纹深度。
连续生产时,弯管b
QGY/JSGL-01-2011-03-01
检测两根的表面锚纹深度。
根检验外表面锚纹深度一次;直管应至少每4h应至少每10
涂敷前应逐根监测钢管表面的加热温度,且温度应控制在环氧粉末生产商推荐的温度7.1.3
范围内,从生产开始起至少应每小时记录一次温度值。
应逐根对防腐层外观进行目测检查,外观要求平整、色泽均匀、无气泡、无开裂及缩7.1.4
孔,允许有轻度桔皮状花纹。
漏点检验应符合下列要求:
7.1.5
℃的状态下,对每根钢管的全部100)应用电火花检漏仪在防腐层完全固化且温度低于a
计。
检漏仪应至少每班校准一次;5V/μm防腐层做漏点检验,检验电压以
时,平的规定进行修补:
当钢管外径<325mmb)漏点数量在下述范围内时,可按5.3.1
时,平均每平方米外表面漏点数不超过均每米管长漏点数不超过一个;当钢管外径≥325mm
个。
经过修补的防腐层应对修补处进行漏点检验。
当漏点超过上述规定时,或个别漏点0.7
24的规定进行重涂。
5.3.2时,应按的面积≥2.5×10mm
)成品防腐钢管防腐层应确认无漏点。
c
的方法进行防腐层固化度检验。
B附录7.1.6每班至少应抽取一根钢管,按SY/T0315-2005
℃。
当抽检钢管≤5,玻璃化转变温度的变化值(ΔTg)应其涂层固化百分率应大于等于95%
的防腐层固化度不合格时,应加倍抽查,重新进行检验。
若任一检验结果不合格,应对当班
涂敷的钢管进行逐根检验,防腐层固化度不合格的钢管应予以重涂。
防腐层厚度检验应符合下列要求:
7.1.7
)防腐层总厚度检验:
应使用磁性涂层测厚仪,在涂敷管表面温度降到测厚仪允许的a
温度时,沿每根钢管轴向随机取三个位置,测量每个位置圆周方向均匀分布的任意四点的防
的要求。
当测得的某一点的厚度值低于最小厚度要求4.4.2腐层厚度并记录,其厚度应符合
的间隔逐段检验,若测得的平均值不符合要求或某一1m时,应对受此影响的钢管沿轴向以
的规定重涂。
测厚仪应至少每5.3.250μm以上时,应按点的厚度值小于规定的最小厚度值
班校正一次;
)内、外层厚度检验:
正常生产后,每班至少应抽取一根钢管使用多层测厚仪在管端b
的要求。
当总厚防腐层边缘随机测量内、外层厚度一次并记录。
内、外层厚度应符合4.4.2
的规定重涂。
5.3.2度符合要求,内层或外层厚度小于规定的最小厚度值50μm以上时,应按
测量后应对防腐层的损坏处按要求及时进行修补。
多层测厚仪每班校准一次。
钢管外防腐层质量检验7.2
个内抽取一个弯管或同一生产工500个、连续生产后,每批连续涂敷的弯管应在7.2.1100
个时,艺条件下的弯管试验段作为试件。
以后每500个抽取一个。
每批连续涂敷钢管不足500
可抽取一个弯管或同一生产工艺条件下的弯管试验段作为试件。
每批连续生产的直管每种管.
QGY/JSGL-01-2011-03-01
左右的管段或同等生产工艺500mm径、壁厚每工作班(最多间隔12h)应截取一个长度为
中的各项指标进行测试。
3条件下的试验管段作为试件。
试件均应按表
的要求,应立即调整涂敷工艺参数。
同时,在该不合格试验段37.2.2若测试结果不符合表
与前一合格试验段之间,应追加两个试件,重新检验。
当两个重做的试件均合格时,则该区
间内涂敷过的成品管可以通过验收。
若重做的两个试件中有一个不合格,则应将前一个试验
的5.2.1合格的成品管到该不合格试验管件之间的所有产品均视为不合格。
以后的生产仍按
要求抽取管段试件进行测试。
的规定进行重新涂敷。
5.3.27.2.3不合格产品应按
防腐层的修补和重涂7.3
修补7.3.1
采用局部修补的方法修补防腐层缺陷时,应符合下列要求:
缺陷部位的所有锈斑、鳞屑、裂纹、污垢和其他杂质及松脱的防腐层应清除掉;a)
将缺陷部位根据修补材料生产商的要求打磨成粗糙面;b)
用干燥的布或刷子将灰尘清除干净;c)
的缺陷部位,应用环氧粉末生产商推荐的热熔修补棒或双组分液d)25mm直径小于或等于
体环氧树脂涂料进行局部修补;
24的