数控车削加工调节盘.docx
《数控车削加工调节盘.docx》由会员分享,可在线阅读,更多相关《数控车削加工调节盘.docx(14页珍藏版)》请在冰豆网上搜索。
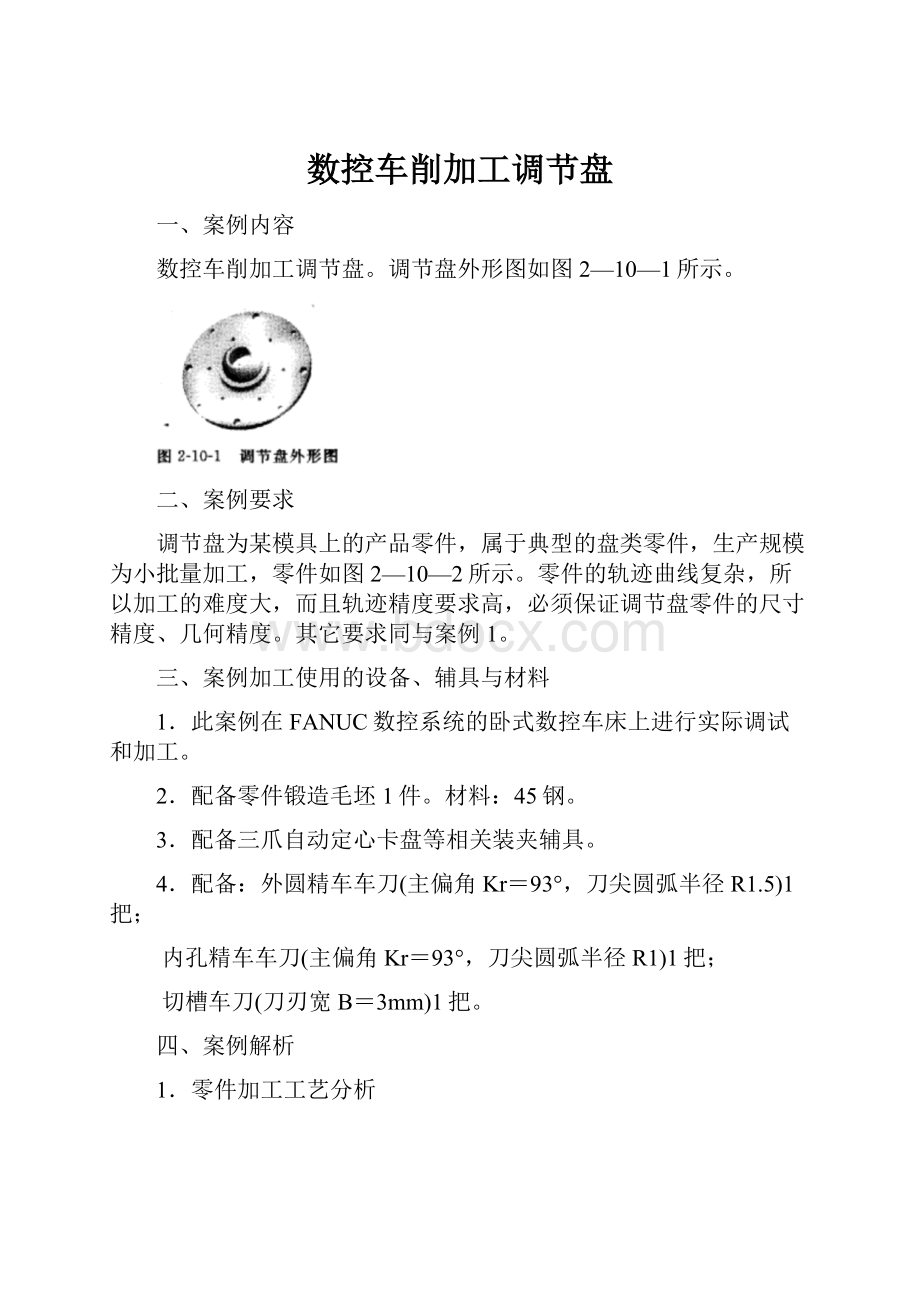
数控车削加工调节盘
一、案例内容
数控车削加工调节盘。
调节盘外形图如图2—10—1所示。
二、案例要求
调节盘为某模具上的产品零件,属于典型的盘类零件,生产规模为小批量加工,零件如图2—10—2所示。
零件的轨迹曲线复杂,所以加工的难度大,而且轨迹精度要求高,必须保证调节盘零件的尺寸精度、几何精度。
其它要求同与案例1。
三、案例加工使用的设备、辅具与材料
1.此案例在FANUC数控系统的卧式数控车床上进行实际调试和加工。
2.配备零件锻造毛坯1件。
材料:
45钢。
3.配备三爪自动定心卡盘等相关装夹辅具。
4.配备:
外圆精车车刀(主偏角Kr=93°,刀尖圆弧半径R1.5)1把;
内孔精车车刀(主偏角Kr=93°,刀尖圆弧半径R1)1把;
切槽车刀(刀刃宽B=3mm)1把。
四、案例解析
1.零件加工工艺分析
(1)结构分析。
零件成型轮廓的形状结构复杂,所以不仅加工的难度大,而且轨迹精度要求高,该零件既要求准确的加工精度,而且要求保证正确的几何精度。
(2)精度分析。
在数控车削加工中,零件重要的径向加工部位有:
φ187-0.015-0.044圆柱段,二零件φ600-0.019球体部,上述各部径向尺寸均有几何形位公差要求。
零件重要的轴向加工部位有:
φ187圆柱段左端面,距球体中心的轴向长度为14±0.135mm。
零件两端的中心孔倒是实现加工上述部位的基准,必须予以保证。
具体要求参见图2—10—2。
图2—10—2调节盘零件图
(3)加工刀具分析。
由图2—10—2可知,零件空刀槽加工使用刃宽B=3内孔切槽车刀,其它刀具选择同案例6。
零件的右端面使用主偏角Kr=93°的内孔精车车刀进行切削加工,既可以保证加工基准的重合,又可以避免零件重新装夹造成不应有的误差,还节省加工中的辅助时间。
(4)毛坯余量分析。
毛坯零件为锻造成形,所以工件轮廓外的切削余量不均匀,在切削过程中会产生变形。
考虑到锻造毛坯余量的不均匀性,因此应该在数控车削前先进行常规的粗车加工,然后再进行数控车削加工。
(5)零件装夹与定位基准分析。
同案例7加工内孔、加工外圆以及加工零件左右端时零件轴向的定位基准均选择在φ187外圆柱段的右端面。
2.工艺处理
在生产实际中,大部分零件的加工,往往是以混合工艺的形式来进行的。
(1)数控加工前的零件预加工。
其目的是为数控车削加工工序提供可靠的装夹工艺基准。
其工艺内容如下。
①毛坯锻造;
②毛坯正火处理。
(2)数控车削加工。
工艺内容见下述数控工艺文件。
(3)数控加工后的零件加工。
其工艺内容如下。
①划线:
孔的位置;
②钻孔加工:
6×φ6孔,4×φ7孔,沉孔4×φ12,4×φ11孔;
③零件边缘去毛刺,球体表面抛光处理;
④工件左端球头部镀铬。
具体要求详见图2—10—2技术要求。
3.数控车削加工工艺与工艺文件
(1)数控车削加工安装方式。
零件粗加工时采用三爪自动定心卡盘装夹方式;工件安装示意图和工件坐标系原点设定卡见表2—10—1。
零件内孔精加工时采用三爪自动定心卡盘装夹方式,与零件外形粗加工时采用的装夹方式相同,零件外形精加工时采用双顶尖一鸡心夹的装夹方式进行零件的装夹定位,工件安装(示意图)和工件坐标系原点设定卡见表2-10-l。
(2)数控车削加工工序。
数控粗车加工、精车加工均分两次切削进行,其工序如下。
①粗车加工I:
利用三爪自动定心卡盘重新装夹零件定位后,使用外圆车刀,粗车加工零件外形与所在端面及其倒角。
留出精车余量0.8mm(双边)。
②粗车加工Ⅱ:
零件掉头利用三爪自动定心卡盘装夹零件,使用内孔车刀,粗车加工零件右端各内孔与所在端面及其倒角。
留出精车余量o.8mm(双边)。
③精车加工I:
利用三爪定心卡盘装夹零件,使用内孔精车车刀,粗车加工零件右端各内孔与所在端面及其零件右端Ø187端面达要求。
④精车、研磨零件左、右端B型中心孔或倒角。
此工序为常规加工工序。
⑤精车加工Ⅱ:
零件掉头利用双顶尖一鸡心夹重新装夹后,使用外圆精车车刀,精车加工零件外形、球面与所在端面及其倒角成形达要求。
数控加工工序卡及切削用量选择见表2-10-2。
(3)数控车削加工刀具。
T1:
主偏角Kr=93°,刀尖圆弧半径R1.5外圆精车车刀(可转位车刀);
T2:
刀刃宽B=3mm切槽车刀(可转位车刀);
T3:
主偏角Kr=93°、Kr′=3°,刀尖圆弧半径RI内孔精车车刀(可转位车刀)。
(4)加I用量的选择与确定。
在数控精车加工中,零件轮廓的精车余量为0.8/g=0.4mm。
(5)编程参数的计算。
零件车削加工的形状较简单,因此由图2-10-2就可直接得到编程所需尺寸。
需要特别注意的是,由于使用的车刀刀尖圆弧为R1.5mm,当应用刀尖圆弧中为I件坐标系始点进行编程时,编程尺寸与零件给定尺寸在圆柱段和端平面处相差1.5mm,但是在倒角处和圆锥处,其编程尺寸与零件给定尺寸均有不同的变化,并且使得零件的轴向编程尺寸和径向编程尺寸均产生变化,如图2-10-3所示。
AB为所需倒角,
C01为车刀刀尖圆弧半径。
实际加工端面时的切削点是刀尖A点,加工倒角时的切削点是刀尖D点。
D、J点均在AB的延长线上。
车削加工中,车刀圆弧中心运行轨迹不是运行到F01就转入倒角,而是延长运行F02线段后再进行倒角。
同理,倒角后的圆柱段运行轨迹不是AB,而是A1线段,此时,转入刀尖C点进行切削加工圆柱面。
因此,在端面转入倒角加工中,车刀圆弧中心的连续运行轨迹为F02→0203→03L。
具体计算略。
粗车编程参数计算方法同此。
粗车加工采用精车运行轨迹留出精车余量的作法进行加工。
(6)机床刀具轨迹节点坐标与零件加工的轨迹运行图见表2-10-4(精车加工零件左端外形)、表2-10-5(精车、粗车加工零件右端与内形)。
零件左端外形粗车加工的轨迹运行图同于表2-10-4、表2-10-5,仅数据尺寸不同,此处略。
(7)程序编制。
零件精车加工程序清单见表2-10-6(零件左端外形加工)、表2-10-7(零件右端与内形加工)。
零件粗车加工程序清单见表2-10-8(零件左端加工)。
案例思考:
请你绘制出使用简单循环指令G80零件加工段的刀具运行轨迹图与轨迹节点坐标。
请你使用闭环车削复合循环G73指令编制此程序,并绘制出刀具运行轨迹图及坐标。
(8)数控加工操作说明。
精车加工时必须按照数控加工工件安装和零点设定卡如表2—10—1安装工件。
安装后工件径向跳动不得大于0.045mm。
(9)数控编程辅助参数的确定(刀号、刀补、间隙补偿等)。
①刀具1号刀位——一T1:
外圆精车车刀(可转位车刀);
2号刀位——一T3:
切槽车刀宽=3mm(可转位车刀);
3号刀位——一T2:
内孔精车车刀(可转位车刀)。
②刀补值未设置(加工中未使用刀具补偿)。
③刀偏值未设置(加工中运用程序在起始点处换刀)。
④间隙补偿值设置为使用机床的间隙测量值。
⑤快速运行值采用数控系统默认值。
(10)数控加工的刀具安装。
外圆精车车刀、内孔精车车刀、切槽车刀的装刀及要求同于案例1。
具体参见图2-1-3、图2-1-4
(11)工件装夹。
工件装夹三爪自动定心卡盘一顶尖方式装夹工件同于案例1。
具体参见图2-1-5、图2-1-6、图2-1-7
(12)工件校正。
三爪自动定心卡盘一顶尖方式装夹后的工件校正同于案例1。
具体参见图2-1-8、图2-1-9。
(13)数控加工的对刀。
①在数控车床是夹装零件,毛坯尺寸φ200×φ26×52mm,如2-10-4所示。
②外圆车刀的X向对刀。
同案例1。
不同处在于:
设定测量零件直径为φ200mm,沿X轴正方向移动车刀152-100-1.5=50.5mm,参见图2-10-4。
图210-4对刀示意图
③外圆车刀的Z向对刀。
同案例1。
不同处在于:
设定测量距离为46+3=49mm(3mm为零件轴向长度余量),沿Z轴正方向移动车刀?
6—49—1.5=25.5mm,参见图2-10-4。
④内孔对刀参阅案例4的内孔精车车刀的对刀。
⑤最终确定工件加工起点同案例1。
(14)数控加工首件试切同案例1。
五、案例思考
1.应该如何进行实际的数控车削加工?
2.如果你认为案例中描述的内容不尽合理或存在不符合实际操作过程的情况,请将你认为或理解的合理操作描述出来。
3.完成程序编制中给定的案例思考。
4.请你在数控铣削加工中完成钻孔加工。