硝酸生产中氧化炉温度控制系统的设计课程设计.docx
《硝酸生产中氧化炉温度控制系统的设计课程设计.docx》由会员分享,可在线阅读,更多相关《硝酸生产中氧化炉温度控制系统的设计课程设计.docx(25页珍藏版)》请在冰豆网上搜索。
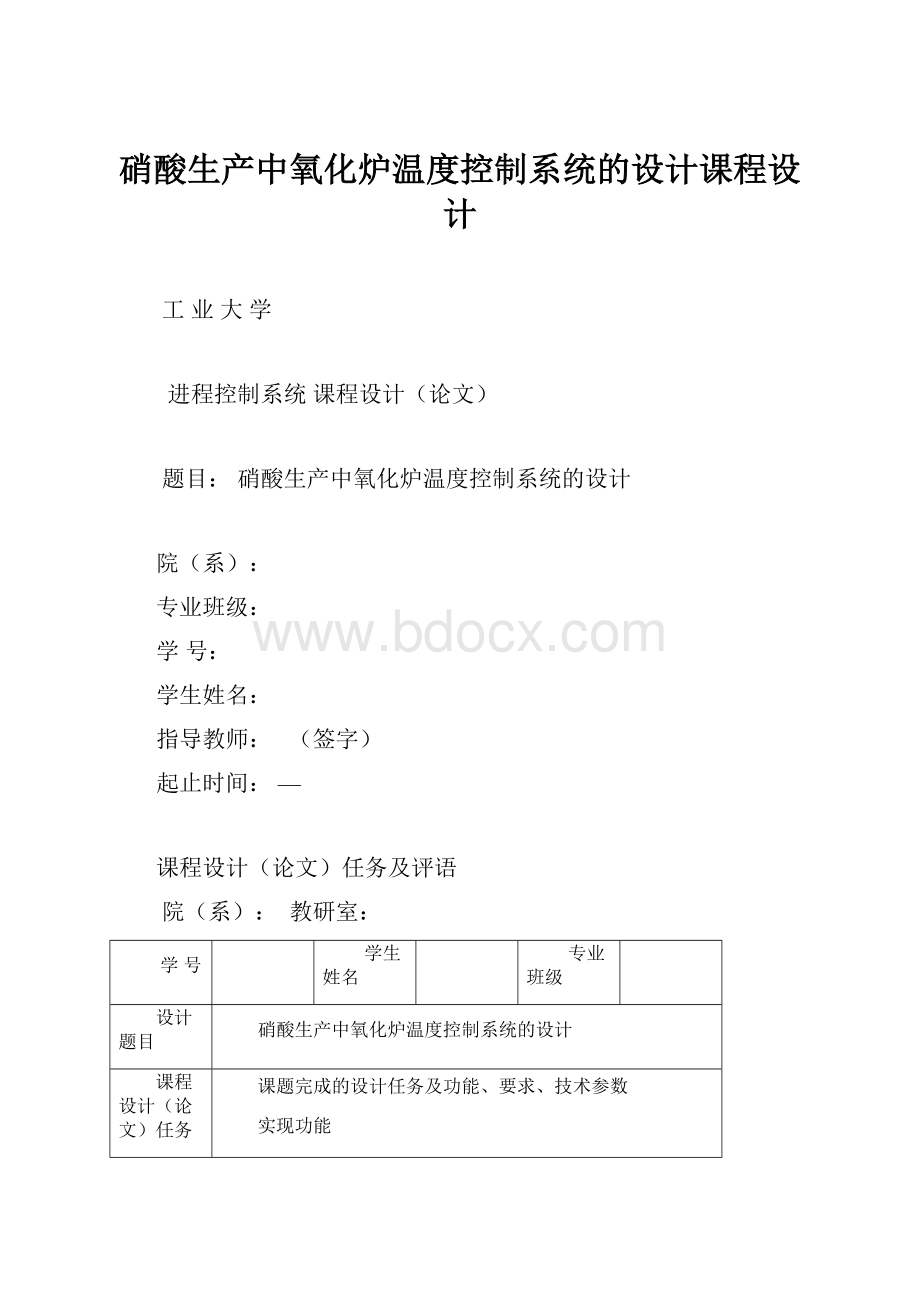
硝酸生产中氧化炉温度控制系统的设计课程设计
工业大学
进程控制系统课程设计(论文)
题目:
硝酸生产中氧化炉温度控制系统的设计
院(系):
专业班级:
学号:
学生姓名:
指导教师:
(签字)
起止时间:
—
课程设计(论文)任务及评语
院(系):
教研室:
学号
学生姓名
专业班级
设计题目
硝酸生产中氧化炉温度控制系统的设计
课程设计(论文)任务
课题完成的设计任务及功能、要求、技术参数
实现功能
氧化炉是硝酸生产中的关键设备,氨气与空气混合后进入炉内,在铂触媒作用下进行氧化反应氨气氧化生成一氧化氮是一种放热反应过程,工艺要求反应温度为850±5℃。
影响温度的主要因素是氨气和空气的比值。
当温度受扰动而变化时,均以改变氨量来补偿。
试设计硝酸生产中氧化炉温度控制系统。
设计任务及要求
1、确定控制方案并绘制工艺节点图、方框图;
2、选择传感器、变送器、控制器、执行器,给出具体型号和参数;
3、确定控制器的控制规律以及控制器正反作用方式;
4、MATLAB仿真分析/实验测试分析;
5、按规定的书写格式,撰写、打印设计说明书一份;设计说明书应在4000字以上。
技术参数
测量范围:
0~1000℃;
控制温度:
850±5℃;
最大偏差:
10℃。
工作计划
1、布置任务,查阅资料,理解掌握系统的控制要求。
(2天,分散完成)
2、确定系统的控制方案,绘制工艺节点图、方框图。
(1天,实验室完成)
3、选择传感器、变送器、控制器、执行器,给出具体型号。
(2天,分散完成)
4、确定控制器的控制规律以及控制器正反作用方式。
(实验室1天)
5、仿真分析或实验测试分析、答辩。
(3天,实验室完成)
6、撰写、打印设计说明书。
(1天,分散完成)
指导教师评语及成绩
平时:
论文质量:
答辩:
指导教师签字:
总成绩:
年月日
注:
成绩:
平时20%论文质量60%答辩20%以百分制计算
摘要
氧化炉是硝酸生产中的关键设备,本文正是针对氧化炉的温度系统进行控制设计的。
在生产硝酸的进程中,氨气与空气混合后进入炉内,在铂触媒作用下进行氧化反映。
氨气氧化生成一氧化氮是一种放热反映进程,工艺要求反映温度为850±5℃。
影响温度的主要因素是氨气和空气的比值,当温度受扰动而转变时,均以改变氨量来补偿。
在硝酸生产进程中,氧化炉炉温控制不稳,致使生产不易稳定运行,利用PMK可编程调节器将原串级控制系统改良成串级比值控制系统,通过压力传感器检测氨气和空气的流量,将比值通过变送器送入控制器,按照温度传感器测得的温度转变,控制器通过执行器调节氨气和空气的比值来实现温度和两种气体之间的关联,优化了控制方案,使氧化炉炉温波动范围控制在±5℃内,解决了生产中碰到的问题。
关键词:
串级控制;比值控制;温度控制;PID调节
第1章绪论
在硝酸生产进程中,氨氧化炉是关键设备。
其工艺流程:
氨气和空气混合气体进入氧化炉,在铂金触煤的作用下进行氧化反映,生成所需要的一氧化氮,这是一个多种参数彼此制约的复杂进程,工艺控制指标的好坏关系到生产可否稳定运行,生产效益和设备安全问题,因此如何实现氧化炉的最优控制,连年来一直是一个被关注,并为之不懈尽力研究的课题。
硝酸是重要的大体化工产品,在国民经济中具有重要的地位。
氨氧化法制硝酸是硝酸生产中比较普遍的方式,具体为将净化后的氨气与空气配成必然比例的混合气,在氧化炉内通过铂网触媒,进行氧化反映,生成氮氧化物气体经吸收塔制取稀硝酸。
硝酸生产中的关键工序是氨氧化生产进程。
氨氧化生产进程中的氨消耗占硝酸生产本钱的80%左右,在保证安全生产的前提下,确保氨氧化生产中高的氨氧化率、低的铂金消耗是提高硝酸生产经济效益的主要手腕。
稀硝装置中最重要的进程是“氨空比值”控制,采用的是氨空比值控制系统,即依据氨、空混合气体中的氨浓度与反映温度成线性正比的关系,通过控制氨-空比值来间接控制反映温度的控制方案,从而实现最终对氧化率的控制。
在氨氧化生产进程的装置中实施计算机控制,实现优化操作,达到高的氧化率、低的铂金消耗与安全生产。
液氨经蒸发、净化后与轴流空气紧缩机送来的空气在氨空混合器内混合后,送入氨氧化炉进行反映,经高温气气换热器、省煤器和低压反映水冷器充分换热,然后经NOx离心紧缩机组去吸收塔、漂白塔制取稀硝酸。
其氨氧化反映方程式如下:
4NH3+5O2→4NO+6H2OΔH=-907280J
一氧化氮再通过初步吸收、二次漂白吸收后生成浓度为60%稀硝酸。
氨氧化炉的一氧化氮生成量直接影响到后续工段最终产品产量,故控制好进入氧化炉的氨气及空气配比,稳定生成一氧化氮的产量是硝酸装置的重点。
氨氧化生产的主要特点是一个高温、快速、易爆的化学放热反映进程。
氨的氧化率是表征反映结果的工艺指标,若排除铂金触媒自身的活性因素,则氨的氧化率与反映温度在必然范围内成正比。
在反映进程中,当其他条件肯定后,反映温度由氨、空混合气中的浓度决定。
按照热量衡算,在混合气中,每1%浓度的氨和空气反映,可使反映温度平均升高70℃。
按如实践经验,氧化炉的反映温度选择在850℃,从而需要控制混合气体中的氨气浓度为%左右。
反映温度太高,虽然氧化效率可以达到更高,但铂金网损耗将大大提高,从而硝酸生产本钱大为增加;而一旦温度超过850℃,氧化炉极易发生爆炸,安全将无法取得保障。
若氨氧化率下降,将使尚未反映完的NH3通过铂金网,NH3在后序的吸收系统中生成硝酸铵和亚硝胺,硝酸铵和亚硝胺有猛烈的爆炸性质,这也是必需避免的。
由生产实践得知,在现有的生产条件下,维持最佳而稳定的中部温度是提高并长期稳定铂金网的活化性能、提高氨氧化率、降低铂金消耗与确保安全生产的主要参数(生产效率与设备安全呈矛盾状态,这就是氧化工艺的特殊性)。
解决这一矛盾的唯一有效方式,就是采用先进的控制方案,提高控制系统的控制性能和控制精度,把被控参数控制在允许的极限值。
表征氧化进程的工艺指标是氨的氧化率。
可是目前的仪表技术对于在线持续、快速检测氧化率,暂时还做不到。
虽然氧化率是重要的工艺指标,但因缺乏有效的检测手腕而不能以氧化率为控制参数。
反映温度与氧化率成单值函数关系,由氧化温度可间接取得氧化率,但如果把温度作为被控参数,因为温度对象的时间常数太大,无法取得满意的调节效果,而被控参数又是控制在临近极限值,被控参数极易超限。
温度一旦越限,就会造成烧坏铂网的庞大损失。
所以,所有稀硝装置中的氧化工艺控制系统,都是依据氨、空混合气体中的氨浓度与反映温度成线性正比的关系,设计以氨气、空气流量比值为被调参数,氨气流量为调节参数的调节系统,采用通过控制氨空比值来间接控制氧化反映温度的控制方案,从而实现最终对氧化率的控制。
为了使进入氧化炉反映的氨空混合气整体适合,确保氧化炉反映充分,炉温稳定在850℃。
氨-空比合理的前提是氨气流量和空气流量测量的准确性,故在测量时要考虑具体工况条件下氨、空流量换算时的压力、温度补偿。
氨空比是一个范围,化学反映中氨氧比为1:
2(氧在空气中约占21%),故氨空比约为1:
11。
实际上氨空比为一个变量,波动范围为7%~15%,小于7%和大于15%都会致使氧化反映不正常而引发装置联锁动作停车。
第2章课程设计的方案
概述
氨气和空气混合气体经静化后,进入氧化炉,在铂金网的作用下,在绝压MPa,温度850℃的条件下,将氨氧化成一氧化氮气体。
影响氧化反映进程的因素有氨的体积分数,压力,氧化率,反映温度,混合气流量,铂网活性等,氧化率是氧化反映的指标,但目前没有有效的检测手腕。
在必然条件下,氧化率正比于反映温度,而氨气是氧化反映的主要成份,反映的温度取决于气体中氨的体积分数,而氨的体积分数又无法测量,只有氧化炉温度能间接反映出氧化率。
为了取得更高的氧化率,氧化炉温度与氨的体积分数均控制在极值,而炉温超到1100℃会烧毁价值昂贵的铂金网,氨的体积分数超过14%会引发恶性爆炸事故损坏生产设备,必需加设联锁保护系统,氧化炉温度及氨空比是最关键的控制参数,对仪表精度要求极高。
方案比较
氧化炉原来的控制方案:
以炉温为主调参数,氨气流量为副调参数,组成串级调节系统,调节品质不好,误差太大,原因是空气控制是开环的,当干扰出现时,由于对象通道太长,检测滞后,而不能克服,串级控制系统如图所示。
图串级控制系统框图
氨气经控制阀控制其流量,与空气在混合器混合,经加压和预热后,进入氧化炉,在铂催化剂和850℃温度下反映,生成一氧化氮和水蒸气。
控制氧化炉温度是控制反映转化率的关键,控制系统工艺节点图如图所示。
图串级控制系统工艺节点图
按照原方案的优缺点,设计了串级比值调节系统,如图所示。
图串级比值控制系统框图
图所示的方案是以炉温为主调节回路,氨空比值为副调节回路,是以一次空气量为主环,氨气流量为副环的双闭环控制系统。
一次空气量是紧缩机出口流路当中去混合器的那一路空气流量;吸收塔的那一路是二次空气流量,其工艺流程图如图所示。
图串级比值控制系统工艺流程图
由于一次空气流量不能随紧缩机量波动而有较大的波动,不然会使紧缩机氧化炉生产系统处于不稳定状态,影响装置的安全生产,因此一次空气量必需加以控制。
其控制阀安装在二次空气管线上,这样会避免安装在一次空气管线上所产生的麻烦。
从工艺安全角度来考虑,二次空气只作记录,不需要控制。
第3章硬件设计
从生产进程和扰动因素来分析,氨气流量的转变是主要矛盾的主要方面。
经研究决定采用QDZ气动单元组合仪表,组合成以氧化炉温度自动校正氨气,空气流量串级比值自动调节系统。
从设计上按照国际仪表生产情况,气体流量选择美国A+K平衡流量计,氨气、空气流量采用QXJ-200型的两针记录仪,比值可以很形象的看出来,氧化炉温度是用QXJ-312型三针记录仪,调节器采用PMK可编程小型调节器。
可编程小型调节器
对氧化炉这个复杂、而特殊的对象,虽然从理论上解决了控制方案问题,但由于常规仪表的局限性,实施起来,系统组成设备太多,存在着极大的事故机率,运算精度难以实现。
主副回路的切换、操作投运十分繁锁,而且无法知足工艺提出的特殊要求,如异样状态的自动处置要全自动等,而进行改造,把常规仪表改成DCS,资金投入量又过大,所以在可编程序调节器利用前氧化炉温度一直是手动状态。
按照系统对控制器的要求,本设计选用FC系列的PMK调节器。
PMK可编程小型调节器,以优越的功能为系统的投运提供了条件:
一、PMK可实现比值计算,串级比值调节系统的投运。
二、PMK在氨空比值达到%,氧化炉温度达到870℃时实现自保。
3、可进行比值、给定、输出上下限设定限幅,确保系统安全。
4、可实现温度、比值参数的预报警。
利用PMK的调节器功能,可化解意外的危险因素,当铂金网活性下降或因意外原因此破裂时,反映温度下降,由于系统对温度是开环的,按照串级比值系统的特性,当这种干扰出现时,系统为保证炉温恒定不变,必将修正比值,增大气氨流量。
当氨空比一旦越限(16%)将会有爆炸危险。
为避免氨空比值超限,利用PMK的靠得住性,当氨空比达到%,将发出报警信号,若氨空比继续增大到
%,将发出脉冲信号,切断气氨流量,保证了设备的安全。
当由于其他原因,如:
停电、停气源等造成控制系统动作,规定当氨空比低于8%,实现设备安全自保。
当温度高于870℃,而氨空比没发生转变,一样实现安全自保。
该方案中主调节器、副调节器、比值器由PMK来实现。
控制阀、快关阀均为气开阀,对象增益大于零,检测变送环节增益大于零,所以调节器均为反作用。
副回路中的一次空气流量自动调节进程,利用PMK调节器来实现,控制阀为气开阀,调节器为正向,一次空气、二次空气、气氨流量、比值、温度由记录仪记录。
温度传感器
温度传感器(temperaturetransducer)是指能感受温度并转换成可用输出信号的传感器。
温度是的核心部份,品种繁多。
按测量方式可分为接触式和非接触式两大类,依照及电子元件特性分为热电阻和两类。
若是要进行靠得住的温度测量,首先就需要选择正确的温度仪表,也就是温度传感器。
其中热电偶、热敏电阻、铂电阻(RTD)和温度IC都是测试中最常常利用的温度传感器。
按照硝酸生产工艺,温度传感器需要测量的温度范围是0~1000℃,所以选用TH-10-44000热敏电阻传感器,此传感器可以直接将温度信号转化为1-5V标准数字信号送入控制器。
TH-10-44000热敏电阻利用半导体材料,大多为负温度系数,即阻值随温度增加而降低。
温度转变会造成大的阻值改变,因此它是最灵敏的温度传感器。
热敏电阻体积超级小,对温度转变的响应也快。
热敏电阻需要利用电流源,小尺寸也使它对自热误差极为敏感。
热敏电阻在两条线上测量的是绝对温度,有较好的精度,比热偶贵,高温器件适用温度高于315℃(目前最高可达到2000℃)。
一种常常利用热敏电阻在25℃时的阻值为5kΩ,每1℃的温度改变造成200Ω的电阻转变。
注意10Ω的引线电阻仅造成可忽略的℃误差。
它超级适合需要进行快速和灵敏温度测量的电流控制应用。
尺寸小对于有空间要求的应用是有利的,但必需注意避免自热误差。
热敏电阻还有其自身的测量技能。
热敏电阻体积小是长处,它能很快稳定,不会造成热负载。
由于热敏电阻是一种电阻性器件,任何电流源都会在其上因功率而造成发烧,功率等于电流平方与电阻的积,因此要利用小的电流源。
流量变送器
变送器(transmitter)是把传感器的输出信号转变成可被控制器识别的信号(或将传感器输入的非电量转换成电信号同时放大以便供远方测量和控制的信号源)的转换器。
传感器和变送器一同组成自动控制的监测信号源。
不同的物理量需要不同的传感器和相应的变送器。
变送器的种类很多,用在工控仪表上面的变送器主要有温度变送器、压力变送器、流量变送器、电流变送器、电压变送器等等。
流量变送器又称为简称为流量计。
目前,已经研发出依照ISO9951标准并结合国内外流量仪表先进技术而研制开发的高精度、高靠得住性的精密计量仪表,它超卓的低压和高压计量性能,多种信号输出方式和对流体扰动的低敏感性,使得流量计成为一种特别优秀的能准确计量气体积累量的工业计量仪表。
采用涡轮进行测量。
它先将流速转换为涡轮的转速,再将转速转换成与流量成正比的电信号。
这种流量计用于检测瞬时流量和总的积算流量,其输出信号为频率,易于数字化。
感应线圈和永久磁铁一路固定在壳体上。
当铁磁性涡轮叶片通过磁铁时,磁路的磁阻发生转变,从而产生感应信号。
信号经放大器放大和整形,送到计数器或频率计,显示总的积算流量。
同时将脉冲频率通过频率-电压转换以指示瞬时流量。
叶轮的转速正比于流量,叶轮的转数正比于流过的总量。
涡轮流量计的输出是频率调制式信号,不仅提高了检测电路的抗干扰性,而且简化了流量检测系统。
它的量程比可达10:
1,精度在±%之内。
惯性小而且尺寸小的涡轮流量计的时间常数可达秒。
气体涡轮流量计普遍应用于石油、有机液体、无机液、液化气、天然气和低温流体等。
按照硝酸生产工艺,测量的气体流量范围在0~40m3/h,所以选用美国A+K平衡流量计。
执行器
(finalcontrollingelement)是自动化技术工具中接收控制信息并对受控对象施加控制作用的装置。
执行器也是控制系统正向通路中直接改变操纵变量的仪表,由和调节机构组成。
在中,执行器由执行机构和调节机构两部份组成。
调节机构通过执行元件直接改变生产进程的参数,使生产进程知足预定的要求。
则接受来自控制器的控制信息把它转换为驱动调节机构的输出(如角位移或直线位移输出)。
它也采用适当的执行元件,但要求与调节机构不同。
执行器直接安装在生产现场,有时工作条件严苛。
可否维持正常工作直接影响的安全性和靠得住性。
执行器是自动化技术工具中接受控制信息并对受控对象施加控制作用的装置,按所用驱动能源分为气动、电动和液压执行器3类。
按照控制系统安全运行准则肯定控制阀的气开、气关形式。
即当控制阀出现故障时,控制阀应处于安全状态,选择控制阀气开、气关形式的一般原则是不使物料进入或流出设备或装置,选用规则:
进入设备或装置原料或热源应切断,因此,选择进料阀为气开阀;设备或装置的出料应切断。
因此,选择出料阀为气开阀;特殊场合,不该使高温高压物流切断或放空,因此,选择保位阀;精馏塔的回流控制阀应在故障时打开,保证全回流,因此选择气关阀;串级控制系统中,当气开和气关形式都可以选用是,为使串级和主控两种模式能方便地切换,选择控制阀的增益与主被控对象增益有相同符号(同时为正或同时为负)。
按照以上原则,本设计的控制阀选用气开阀,型号为TMCU-TMVU-TMVU流量控制阀。
调节阀的流量特性是指介质流过阀门的相对流量与位移(阀门的相对开度)间的关系,理想流量特性主要有直线、等百分比(对数)、抛物线和快开等4种。
常常利用的理想流量特性只有直线、等百分比(对数)、快开三种。
调节阀流量特性的选择可以通过理论计算,但所用的方式和方程都很复杂。
目前多采用经验准则,具体从下几方面考虑:
(1)从调节系统的调节质量分析并选择;
(2)从工艺配管情况考虑;
(3)从负荷转变情况分析。
通过选择调节阀的流量特性来补偿被控进程特性的非线性,从而达到系统总放大倍数不变的目的。
综上所述,系统应采用对数(等百分比)流量特性调节阀。
第4章软件设计
串级比值控制系统又称为变比值控制系统,它是按必然工艺指标自行修正比值系数,克服影响工艺指标的所有干扰。
该串级控制系统按照氧化炉温度的转变自行修正氨空比值系数。
并按新比值系数,实现转变值控制。
系统设计
串级比值调节系统,快速而有效地克服各类干扰,可使温度控制精度达到恒定。
串级比值调节回路中,当出现直接引发氨气,空气流量转变的干扰时,通过比值系统,可以取得及时克服,以维持炉温不变,对于其他干扰如氨气、温度压力转变,触媒活性转变等引发的炉温转变,可通过主调节器对氨空比值进行修正,以保证炉温恒定,系统流程图如图所示。
图系统流程图
当出现影响产品质量的流量干扰时,可通过比值控制回路得以克服,当一次空气流量因某种原因此波动较大时,作为副回路当中的双闭环控制系统,一方面,一次空气的单回路控制能迅速加速克服干扰;另一方面波动部份同时通过比值控制加以克服,当波动量进入氧化炉,并通过氧化炉温度反映出来时,主调节器改变输出以修正比值系数,并按新的比值系数进行控制,这样,副回路相当于进程控制的粗调,主回路则为细调,这正是串级控制的长处。
当物料、温度、压力、成份、铂网活性发生转变时,虽然比值不变,但参加混合反映的有效成份发生转变,即有效比值改变,最后通过反映温度表现出来,主调节器输出改变,修正比值,直到主副流量的有效成份的比例符合要求,这样保证控制质量稳定。
另外,副回路部份采用了双闭环比值控制系统,因此具有如下特点:
一、克服了主流量干扰的影响,使主流量变得比较平稳,通过比值控制,副流量也将比较平稳,从而系统总负荷将是稳定的。
二、起落负荷比较方便,只要缓慢地改变主流量的设定值,就可以够在起落主流量的同时,副流量也将自动跟踪并维持比值不变,因此此方案常常利用在主流量干扰较大,而工艺不允许负荷有较大波动的场合。
除法器的输出即是两流量信号的比值,输出可进行记录和指示,越限报警,实现自保联锁。
对炉温信号,一方面进行常规串级比值调节,温度是主调节器的测量信号;另一方面当炉温越限时,通过报警器进行超温报警,当炉温继续升高超过联锁值,自动切换氨保护装置自保。
比值控制方案有手动和自动两种运行方式。
调节器在手动方式时,操作人员可以通过计算机上的手动增减按钮按设定的步长操纵氨气控制阀的阀门开度。
因为比值控制方案测量值、给定值显示的是氨空比值,所以操作的依据是直接读取仪表上的数据,使按照氨空实际流量算出的氨空比测量值在工艺设定的氨空比值范围内。
调节器在自动方式时,由人工直接设定调节回路的氨空比值设定值,系统自动控制气氨流量控制阀,使氨空比值趋近于比值给定值,在此进程中,气氨流量能实时地自动跟踪空气流量,不需要人工干与。
监控画面组态
该系统稳定状态下,副回路中主副流量恒定,它们别离经测量、开方运算后送入除法器相除,输出表征了它们的比值,同时作为副调节器测量信号,这里表征产品质量指标参数也恒定,则主调节器输出信号恒定且与比值信号相等,副调节器输出不变,控制处于某一开度,产品质量合格,监控画面如图所示。
图监控画面
氨空比值自动控制系统以空气为主动量,氨气为从动量。
氨气流量和空气流量经除法器进行比值运算后的结果,作为PID的测量信号,与氨空比给定值SP进行PID运算后去控制氨气流量控制阀,从而使空气流量随氨气流量的转变而转变,并始终维持实际的氨空比值在允许的范围(7%~15%)之内。
算法下的工艺进程:
①装置开车前,四合一机组先行启动,氧化炉由外供中压蒸汽预热至200℃左右。
②空气经空压机先行进入氧化炉,通过调节轴流空气紧缩机上静叶调节阀开度至50%左右(约40000m3/h)。
③氨球来的液氨经由氨蒸发器蒸发后,进入氨-空混合器与空气进行混合,气流量在未达到氨-空比设定范围前,联锁不投用。
此时的氨空混合气不进氨过滤器及氨-空混合器,通过手动调节阀与氨气快切阀的作用返回至氨回收装置从头回用。
④氨气流量达到预设值,自控系统将切断阀关闭,切断阀打开,使氨气经氨气过滤器净化,在氨空混合器与空气充分混合后进入氨氧化炉,此时启动氧化炉手动点火装置,氨空混合气在铂网的催化作用下,当即被氧化燃烧。
⑤在装置运行正常后,按照装置运行需要,对装置负荷进行调整:
空气紧缩机静叶调节阀开大,空气流量增大,则计算后的氨-空比减小,调节器输出增大,氨气阀门开度增大,使氨-空比值增加,恢复到给定氨-空比范围内;假设因某种原因氨气流量增大或空气流量减小,则计算后的氨空比增大,调节器输出减小,氨气阀门开度减小,使氨-空比值减小,恢复到给定氨-空比范围内。
⑥整个反映进程中,空气始终轻微过量,用氨气流量转变来控制氧化炉炉温,使氨氧化反映温度稳定在850℃。
在气体流量测量系统中,温压补偿是其中一个不可缺少的环节。
若缺少这一环节,就会给测量带来误差,使仪表的示值变得毫无心义。
氨气、空气流量的准确测量关系到氨空比值控制方案的控制品质,因此按照被测气体及仪表类型,选用适合的数学模型,实施温压补偿是十分必要的。
第5章仿真分析
PID控制系统的设计
PID(Proportional,IntegralandDifferemial)控制器是一种基于“过去”,“此刻”和“未来”信息估量的简单算法。
常规PID控制系统原理框图如图所示,系统主要由PID控制器和被控对象组成。
作为一种线性控制器,它按照给定值r(t)与实际输出值y(t)组成控制误差e(t),将误差按比例、积分、和微分通过线性组合组成控制量u(t),对被控对象进行控制。
图PID控制系统原理图
其传递函数可表示为:
PID控制器各校正环节的作用如下:
1.比例环节:
成比例地反映控制系统的误差信号e(t),误差一旦产生,控制器当即产生控制作用,以减少误差。
2.积分环节:
主要用于消除静差,提高系统的无差度。
积分作用的强弱取决于积分时间常数Ti,Ti越大,积分作用越弱,反之越强。
3.微分环节:
反映误差信号的转变趋势(转变速度),并能在误差信号变得太大之前,在系统中引入一个有效的初期修正信号,从而加速系统的动作速度,减少调节时间。
从根本上讲,设计PID控制器也就是肯定其比例系数Kp、积分系数Ti和微分系数Td,这三个系数取值的不同,决定了比例、积分和微分作用的强弱。
控制系统的整定就是在控制系统