油漆通用技术规范.docx
《油漆通用技术规范.docx》由会员分享,可在线阅读,更多相关《油漆通用技术规范.docx(14页珍藏版)》请在冰豆网上搜索。
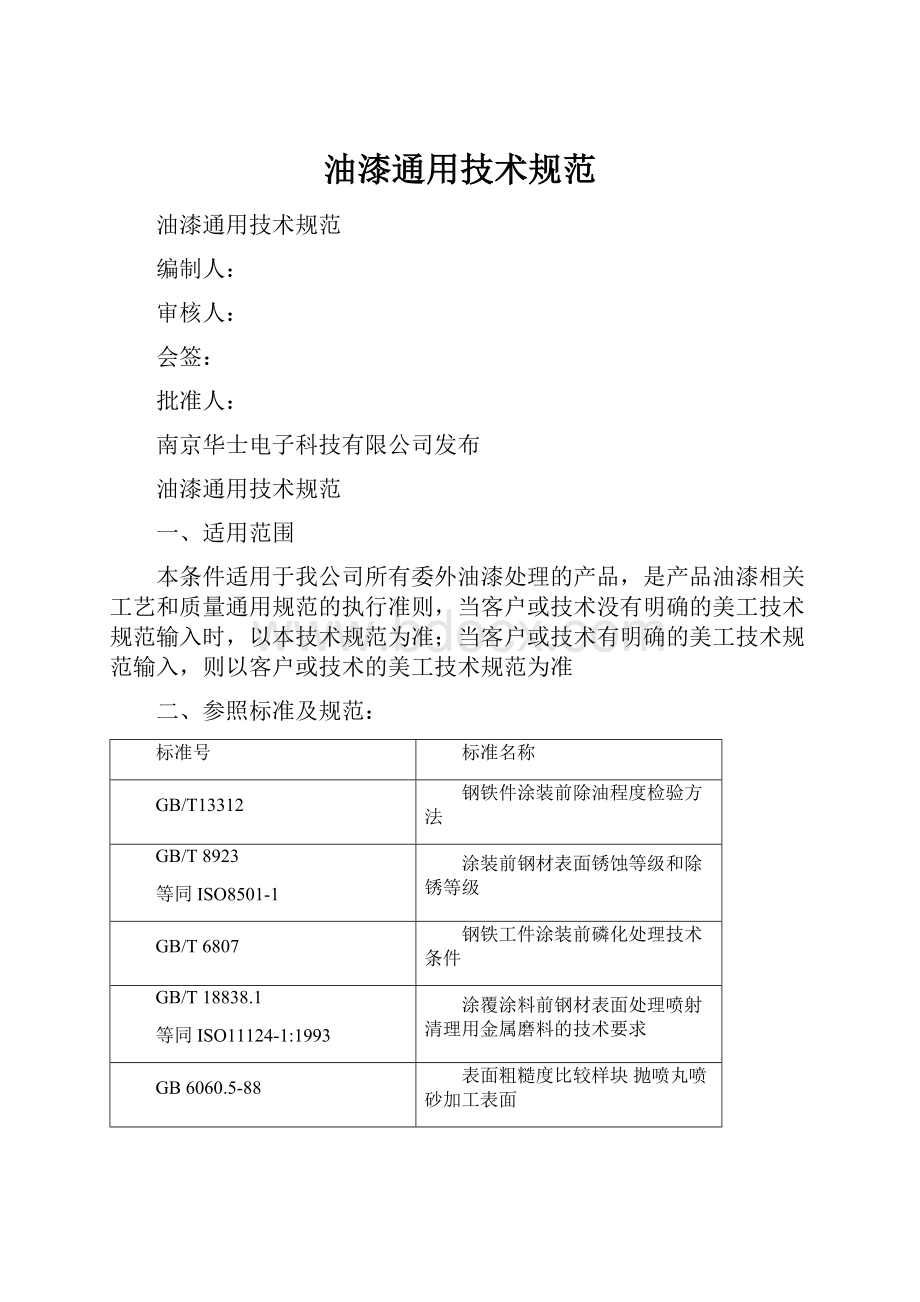
油漆通用技术规范
油漆通用技术规范
编制人:
审核人:
会签:
批准人:
南京华士电子科技有限公司发布
油漆通用技术规范
一、适用范围
本条件适用于我公司所有委外油漆处理的产品,是产品油漆相关工艺和质量通用规范的执行准则,当客户或技术没有明确的美工技术规范输入时,以本技术规范为准;当客户或技术有明确的美工技术规范输入,则以客户或技术的美工技术规范为准
二、参照标准及规范:
标准号
标准名称
GB/T13312
钢铁件涂装前除油程度检验方法
GB/T8923
等同ISO8501-1
涂装前钢材表面锈蚀等级和除锈等级
GB/T6807
钢铁工件涂装前磷化处理技术条件
GB/T18838.1
等同ISO11124-1:
1993
涂覆涂料前钢材表面处理喷射清理用金属磨料的技术要求
GB6060.5-88
表面粗糙度比较样块抛喷丸喷砂加工表面
GB/T13288
等同ISO8503
喷砂清理钢基材表面粗糙度特性
GB/T1743
漆膜光泽度测定法
GB/T9754
等同ISO2813
色漆和清漆.非金属漆膜镜面在20°、60°和85°时光泽的测定
GB/T1720
漆膜附着力测定法
GB/T5210
等同ISO4624
涂层附着力的测定法拉开法
GB/T9286
等同ISO2409
色漆和清漆漆膜的划格试验
GB/T13452.2
等同ISO2808
色漆和清漆漆膜厚度的测定
TB/T2879.1
第1部分:
涂料供货技术条件
TB/T2879.2
第2部分:
涂料检验方法
TB/T2879.3
第3部分:
金属和非金属材料表面处理技术条件
TB/T2879.4
第4部分:
货车防护和涂装技术条件
TB/T2879.5
第5部分:
客车和牵引动力车防护和涂装技术条件
三、技术要求
3.1预处理
3.1.1焊接后的处理
首先需要清除焊接后残余的氧化皮、焊渣、焊接飞溅,此工艺可和除锈工艺合并处理。
3.1.2碳钢表面处理前预处理
3.1.2.1除油
3.1.2.1.1轻微油污可和除锈工艺合并处理;
3.1.2.1.2重度油污
采用低碱液除油脂,利用低碱对植物油的皂化作用,形成溶于水的皂化物以除去油污。
低碱液使用温度为室温~80℃,PH值为9~12,处理试件为5~20分钟。
3.1.2.2除锈
3.1.2.2.1执行标注
根据标准GB8923,锈蚀等级分为A、B、C、D四个等级,除锈等级分为Sa1、Sa2、Sa2.5、Sa3四个等级,若使用手工和动力工具,除锈等级则为St1、St2、St2.5、St3。
3.1.2.2.2手工或动力工具除锈
若喷射处理易造成薄板的变形或零件尺寸较小时,可使用不锈钢丝刷或颗粒度60~80的砂轮打磨除锈。
除锈等级应达到St3。
3.1.2.2.3喷射除锈。
喷射除锈前,应去除厚的锈层,以及油污和污垢。
除锈等级应达到Sa2.5;对特殊性能和特殊加工要求的覆盖层,如喷镀锌、粘贴等应为Sa3。
处理结束后,表面的浮尘和碎屑应予以清除。
喷射除锈后的钢件表面粗糙度Ra12.5~50mm(铸件除外),表面粗糙度按GB6060.5规定的比较样块进行对照检查。
3.1.2.2.4酸洗。
酸洗是利用酸对氧化物溶解以及腐蚀产生氢气的机械剥离作用达到除锈和除氧化皮的目的,当手工或动力工具打磨无法完全除锈,或者客户有特殊要求时,应采用酸洗进行除锈。
酸洗温度在常温~80℃,浓度10%~40%,并加入适量的缓蚀剂。
3.1.2.3磷化。
3.1.2.3.1要求
为增加油漆的附着力,除锈后可进行磷化处理,即把钢件浸入磷酸盐为主的磷化膜厚度一般为1~5μm。
是否需要进行磷化,见各产品的技术条件。
磷化后工件表面颜色应为浅灰色到深灰色或者彩色,磷化膜应结晶致密、连续和均匀。
磷化膜的检验规则与方法按GB6807进行。
3.1.2.3.2以下为允许缺陷
a)轻微的水迹、重酸盐的痕迹,擦白及挂灰现象;
b)由于局部热处理,焊接以及表面加工状态的不同,造成颜色和结晶不均匀;
c)在焊接的气孔和夹渣处无磷化膜;
3.1.2.3.3以下不允许缺陷
a)疏松的磷化膜层;
b)有锈蚀和绿斑;
c)局部无磷化膜(焊接的气孔和夹渣处除外);
d)表面严重挂灰
3.1.3铝合金表面的预处理
a)打磨:
用80~120目的砂纸将工件表面打磨至均匀无光泽,无过深磨痕
b)清洁:
用专用清洁剂去油污、氧化皮、灰尘等杂物
c)除尘:
用高压空气将工件上的尘土吹干净,从一个方向朝另一个方向顺
序过去,特别注意的时要将边角、缝隙处吹净。
d)清洗:
在油漆前进行彻底的清洗。
3.1.4不锈钢表面预处理
3.1.4.1清理打磨、除锈
如由损伤应打磨,尤其与碳钢件接触造成的划伤和飞溅,割渣造成的损伤必须认真地清理打磨干净。
在未采用酸洗钝化或喷砂除锈时,手工或动力工具除锈除锈等级应达到St3。
3.1.4.2除油除尘
用专用清洁剂清除油污、氧化皮、灰尘等杂物。
3.1.4.3酸洗钝化
为增加油漆附着力,必要时可进行酸洗钝化。
酸洗钝化后选用专用的清洗剂进行中和、冲洗、干燥,彻底清除残留的酸液。
3.1.4.4喷砂
除了酸洗钝化,在不会造成产品变形的情况下(如薄板喷砂后易造成变形,则不适用),也可以采用喷砂的方式进行预处理以增加油漆的附着力。
注意砂粒的种类、大小,以及喷砂时压力大小的选择。
3.1.5预处理后检查
处理完毕后表面应无油污、污痕、灰尘、残留的漆膜或焊渣。
3.1.6保护
表面预处理后要做好防护工作,避免人员抚摸和油污、灰尘的二次污染。
3.2涂料的选择
涂覆使用的涂料种类见各产品技术条件,并且应符合TB/T2879.1的要求。
3.3喷涂
3.3.1喷涂车间必要条件
a)涂装区域无尘、土等其他空气污染物
b)涂装区域与其他工作区域隔离,没有直接的污染
c)有足够的通风条件
3.3.2环境条件
每层涂层的涂装和干燥应在室内进行室温工件和涂料温度不低于12℃使用双组份或多组份涂料时温度不低于18℃,相对湿度不超过75%。
漆房具体的环境温、湿度设定可根据各项目作业指导书要求进行调整。
3.3.3表面准备
3.3.3.1保护部位
a)遮蔽图纸中要求不进行喷涂的区域
b)所有螺纹及接地桩(接线面),打钢印号位置不油漆;油漆后,螺纹及接
地桩所有保护膜(纸)需去除
3.3.3.2涂装前表面处理应按3.1的规定进行
3.3.3.3表面处理后的钢材表面应在4h内完成第一层涂装
3.3.3.4在涂下一层涂料前对上一层涂料的表面应清除油脂凝水和焊接溅滴
3.3.3.5腻子湿磨以后边角缝隙搭接处留下的研磨水分须用干燥无油的压缩空气吹干干燥后才能进行下一道工序
3.3.3.6对于平面上的凹坑可以适当采用腻子刮平,腻子每道厚度一般不应超过0.5mm,总的干膜厚度不超过3mm。
3.3.4涂装过程中涂层的修整
4.8.1如果已涂的涂层在施工过程中受到损伤,应按规定的涂装工艺进行修整
4.8.2完全干燥的涂层修整前必须进行打磨。
4.8.3如果损伤较重,特别是伤及底材,表面应按照3.1的规定处理重新进行全部涂装作业。
3.3.5涂层的厚度及干燥
3.3.5.1如果涂层在干燥室中干燥,需要干燥的部件在放入干燥室前应在常温下通风15~30min
3.3.5.2涂层的干燥应达到能够按采用的涂装工艺喷涂下一层涂料的程度,每一油漆层均应均匀、无流淌、起泡等工艺缺陷。
3.3.5.3在涂刷隔热、隔音涂料前,应查清前一道涂层是否确已完全干燥。
3.3.5.4整个涂装工作结束后,整个车辆应置于温度在18℃以上的室内最少48h。
3.4其他要求
3.4.1根据关特防要求,油漆需按特殊过程进行控制,做好特殊过程的确认和过程记录,有效控制好整体系的涂层质量,以确保箱体与车体同等耐腐期。
3.4.2色板要求:
每一涂层喷漆时做样板测试,色板与箱体一共油漆。
3.4.3供应商有义务提供油漆相关信息,如:
如何前处理、涂覆时间,涂层之间的干燥时间等。
3.4.4包装、运输:
表面处理完的结构件应采取必要的包装措施,防止在周转、运输过程中造成磨损、变形、划伤。
3.4.5经检验合格的产品,签发产品合格证,产品合格证应包括下列内容:
制造厂名称、产品名称(或图号)、喷涂日期等。
四、技术参数
4.1外观要求
涂层外观要求分Ⅰ级、Ⅱ级、Ⅲ级、Ⅳ级,Ⅳ级涂层外观不作规定,但不允许有任何影响保护性的缺陷,其余等级要求详见下表要求。
注:
涂层外观质量要求表中杂质及灰尘指标,可在表中给出的数字范围内根据不同产品的要求或生产条件选定;
制品表面允许的杂质及灰尘数量,按面积计算,换算时,小数点后的数值应圆整为整数。
表1Ⅰ级涂层外观
涂层类别
质量要求项目
平态涂层
美术涂层
有光
半光
无光
平态
不平态
光泽
光泽度%
符合涂料产品技术条件的规定。
均匀程度
表面光泽均匀一致。
颜色
与标准色板比较
在色差范围内或无显著差异。
制品之间比较
同台或同批工件间相同涂层颜色一致。
杂质及灰尘
数量
个/m2
0~4
0~6
4~8
4~8
8~12
尺寸
mm
颗粒状(直径)
0~0.5
0.2~0.5
0~0.5
0.2~0.5
0.5~1.0
纤维状(长度)
0~2
0~2
0.5~2.0
0.5~2.0
1~4
间距
100~50
100~50
100~50
100~50
100~50
缺陷修整程度
修整精细,无目视可见修整痕迹。
流痕
不允许。
桔皮痕
允许有极轻微的,均匀的。
磨痕,刷痕,划痕
不允许。
针孔或斑点
不允许。
美术涂层的纹理或斑点
——
美术纹理或斑点清晰,有强烈的美术效果。
表2Ⅱ级涂层外观
涂层类别
质量要求项目
平态涂层
美术涂层
有光
半光
无光
平态
不平态
光泽
光泽度%
符合涂料产品技术条件的规定。
均匀程度
表面光泽均匀一致。
颜色
与标准色板比较
在色差范围内或无显著差异。
制品之间比较
同台或同批工件间相同涂层颜色一致。
杂质及灰尘
数量
个/m2
4~16
4~20
8~24
8~24
12~36
尺寸
mm
颗粒状(直径)
0.5~1.0
0.5~1.0
0.5~1.0
0.5~1.0
0.5~1.0
纤维状(长度)
2~4
2~4
2~4
2~4
2~4
间距
100~50
100~30
100~30
50~22
50~20
缺陷修整程度
修整完好,无显著缺陷。
流痕
不允许有显著的。
桔皮痕
允许有极轻微的,均匀的。
磨痕,刷痕,划痕
允许有局部的,轻微的。
针孔或斑点
允许有个别的,细小的。
美术涂层的纹理或斑点
——
美术纹理或斑点清晰,分布比较均匀。
表3Ⅲ级涂层外观
涂层类别
质量要求项目
平态涂层
美术涂层
有光
半光
无光
平态
不平态
光泽
光泽度%
符合涂料产品技术条件的规定。
均匀程度
表面光泽基本均匀。
颜色
与标准色板比较
在色差范围内或无显著差异。
制品之间比较
同台或同批工件间相同涂层颜色基本一致。
杂质及灰尘
数量
个/m2
1~4
1~4
2~5
2~5
2~5
尺寸
mm
颗粒状(直径)
1~2
1~2
2~3
2~3
2~3
纤维状(长度)
3~6
3~6
1~6
3~6
3~6
间距
不允许有杂质堆积。
缺陷修整程度
允许有少量细小缺陷。
流痕
允许有局部的轻度流痕。
桔皮痕
允许有轻微的。
磨痕,刷痕,划痕
允许有轻微的。
针孔或斑点
允许有少量的,细小的。
美术涂层的纹理或斑点
——
美术纹理或斑点清晰,分布基本均匀。
4.2漆膜厚度
4.2.1干膜厚度符合设计及工艺文件的规定;
4.2.2无明确规定时,至少满足以下要求:
a)车外产品外部零部件底漆的干膜厚度不应小于90um,面漆的干膜厚度应
不小于60um;其它部位底漆的干膜厚度不得小于50um。
b)车内产品零部件底漆的干膜厚度不得小于50um,面漆的干膜厚度应不小
于40mm。
4.3附着力
涂层的附着性若无特殊规定,采用抽样方法进行划格试验以检查防护底漆、腻子、面漆或整个涂装系的附着力应达到GB/T9286中规定的1级标准。
由于划格试验对涂层造成的破坏由制造厂原技术要求进行修复。
五、检验方法
5.1.1光泽度
涂层的光泽度按GB/T9754的规定进行检验。
采用标准样板检验时,应于被检验的涂层在同一映照条件下比较,其结果应符合技术要求。
每个产品上检验点的数量见下表,点的选取均匀分布
产品最大尺寸/m
检验点
<1
5
1至10
20
>10
50
光泽度允许在设计要求的±10%以内,另外可有10%的区域允许超标,允许范围为设计要求范围的±15%。
5.1.2颜色及色差
5.1.2.1环境条件
白天光亮度的漫射日光周围环境为中性灰色,即介于白色(全反射)与黑色(全吸收)中间值的灰色。
检验人员的视力,色觉正常,视距0.5m~1.0m。
5.1.2.2试验方法
用标准色板及色差样板与被检验样板比较,无色差样板时可单独与标准色板比较。
用同台或同批产品互相比较,同台或同批产品颜色应一致。
被检验的样板或产品与标准样板并列放置,为提高鉴别力,在比较时可将样板或产品互换位置。
5.1.3外观
5.1.3.1环境条件
白天光亮度的漫射日光或照度不低于200Lx(40W日光灯,距离0.5m)的人工光源。
检查人员的视力,色觉正常,视距0.4m~0.5m。
5.1.3.2检验方法
方法a:
不断改变光线的入射方向和观察角度,达到最佳鉴别条件,反复检查及评定涂层表面缺陷程度。
方法b:
在入射光和反射光的法线方向检查及评定涂层表面缺陷程度。
涂层外观等级不同,采用不同的方法检验及评定涂层表面缺陷程度。
Ⅰ级用方法a检验评定;Ⅱ级、Ⅲ级、Ⅳ级用方法b检验评定。
5.1.4厚度
涂层的干膜厚度按GB/T13452.2的规定进行测定。
每个产品上检验点的数量见下表,点的选取均匀分布
产品最大尺寸/m
检验点
<1
3
1至10
3~20
>10
20~50
5.1.5附着性
漆膜附着力可以选择下面一种方法进行:
a)按照GB/T9286规定进行;
b)按照GB/T1720规定进行;
c)按照GB/T5210规定进行。
5.1.6涂层涂料的检查
涂层的涂料的检查按涂料产品技术条件规定的检验方法或按照TB/T2879.2的要求检查。
六、检验规则
6.1检验分类
检验项目
检验类别
交收
例行
必须
选择
必须
选择
光泽
△
颜色
△
外观
△
厚度
√
附着性
√
√
涂层涂料
√
√
表中“必须”表示如果无特殊规定,应进行检验的项目
表中“选择”表示根据涂层使用条件,按有关文件的规定进行检验的项目。
表中“△”表示100%检验的项目;表中“√”表示抽检的项目。
6.2交收检验
对于按已经批准的工艺施工的产品,根据交收检验项目进行检验。
6.3例行检验
涂层、电化学及化学处理层处理如有下列情况之一时,应进行例行检验:
a)新材料或新工艺要求确定时;
b)工艺出现重大更改时;
c)施工质量全面检验时;
d)对质量有重大争议需要仲裁时。