塑料成型模具重点考试范围doc.docx
《塑料成型模具重点考试范围doc.docx》由会员分享,可在线阅读,更多相关《塑料成型模具重点考试范围doc.docx(13页珍藏版)》请在冰豆网上搜索。
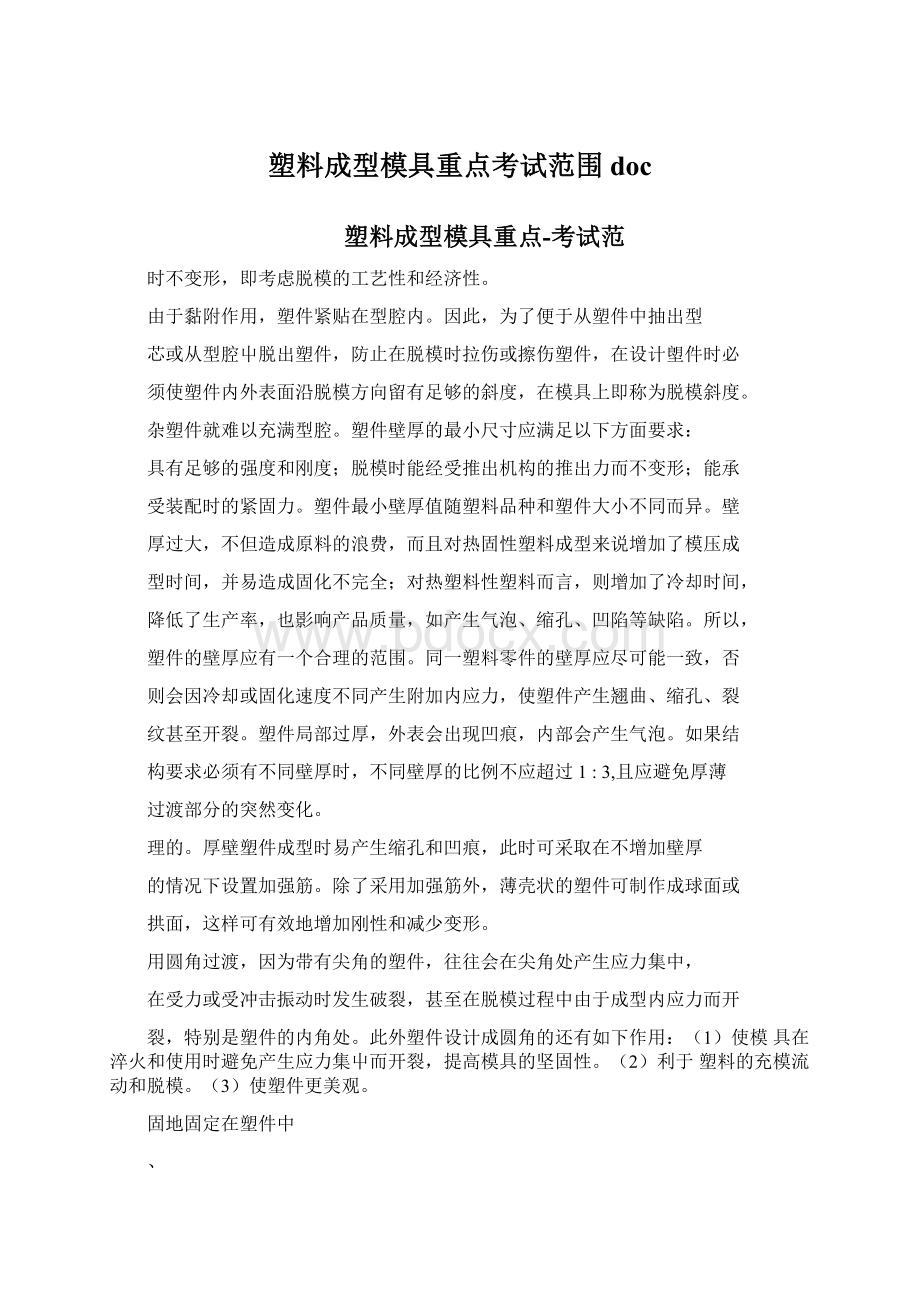
塑料成型模具重点考试范围doc
塑料成型模具重点-考试范
时不变形,即考虑脱模的工艺性和经济性。
由于黏附作用,塑件紧贴在型腔内。
因此,为了便于从塑件中抽出型
芯或从型腔屮脱出塑件,防止在脱模时拉伤或擦伤塑件,在设计塱件时必
须使塑件内外表面沿脱模方向留有足够的斜度,在模具上即称为脱模斜度。
杂塑件就难以充满型腔。
塑件壁厚的最小尺寸应满足以下方面要求:
具有足够的强度和刚度;脱模时能经受推出机构的推出力而不变形;能承
受装配时的紧固力。
塑件最小壁厚值随塑料品种和塑件大小不同而异。
壁
厚过大,不但造成原料的浪费,而且对热固性塑料成型来说增加了模压成
型时间,并易造成固化不完全;对热塑料性塑料而言,则增加了冷却时间,
降低了生产率,也影响产品质量,如产生气泡、缩孔、凹陷等缺陷。
所以,
塑件的壁厚应有一个合理的范围。
同一塑料零件的壁厚应尽可能一致,否
则会因冷却或固化速度不同产生附加内应力,使塑件产生翘曲、缩孔、裂
纹甚至开裂。
塑件局部过厚,外表会出现凹痕,内部会产生气泡。
如果结
构要求必须有不同壁厚时,不同壁厚的比例不应超过1:
3,且应避免厚薄
过渡部分的突然变化。
理的。
厚壁塑件成型时易产生缩孔和凹痕,此时可采取在不增加壁厚
的情况下设置加强筋。
除了采用加强筋外,薄壳状的塑件可制作成球面或
拱面,这样可有效地增加刚性和减少变形。
用圆角过渡,因为带有尖角的塑件,往往会在尖角处产生应力集中,
在受力或受冲击振动时发生破裂,甚至在脱模过程中由于成型内应力而开
裂,特别是塑件的内角处。
此外塑件设计成圆角的还有如下作用:
(1)使模具在淬火和使用时避免产生应力集屮而开裂,提高模具的坚固性。
(2)利于塑料的充模流动和脱模。
(3)使塑件更美观。
固地固定在塑件中
、
注塑模具设计
构成。
其凹模型腔设在定模上,凸模型芯设在动模上,主流道设在定
模上,分流道和浇口设在分型而上,开模后塑料制品连同流道凝料一起留
在动模一侧。
动模一侧设有推出机构,用以推出塑料制品及流道凝料(又
称脱模)。
这类模具的特点是结构简单,对塑料制品成型的适应性很强,
所以应用十分广泛。
充满型腔时,注射压力在型腔内所产生的作用力总是力图使模具沿分
型妞胀开,因此,注射机的锁模力必须大于型腔内熔体压力与塑料制品及
浇注系统在分型面上的投影面积之和的乘积。
成。
(1)侧浇口
(2)点浇口(3)潜伏式浇口(4)直接浇口。
点浇口模
具应设计成双分型面(三板式)模,以便拉断浇口和脱出流道凝料。
潜伏
式浇口模具仍然采用单分型妞结构。
冲击型浇口:
即交口开设方位正对着
型腔或粗大的型芯,塑料流冲击在型腔或型芯上,从而改变流向,降低流
速,均匀地填充型腔。
流动比:
即熔体流程长度与厚度之比,流动比又称
流程比。
型腔注射模具中,要求由各型腔成型的制品表面质量和内部性能差异
不大,这就必须保证各型腔在成型制品时工艺条件相同。
为此分流道的布
置形式应能达到如下要求:
从主流道来的熔体能均衡到达各浇口并同时充
满各型腔。
分流道的布置取决于型腔的布局,有平衡式和非平衡式两种。
所谓平衡式布局,是指分流道的长度、截面形状和尺寸都相同,各个型腔
同时均衡地进料,同时充满型腔。
显然对成型同一种制品的多型腔模,分
流道以平衡式为佳。
在加工时,应保证各对应部位的尺寸误差控制在1%
以内。
非平衡式是指由主流道到各个型腔的分流道的长度可能不是全都对
应相等,为了达到各个型腔均衡进料同时充满的目的,就需要进行浇口平
衡的计算,并将浇门开成不同的尺寸。
采用这类分流道,在多型腔时可缩
短流道的总长度,减少回头料的重量,但对于精度和性能要求较高的塑件
不宜采用,因成型工艺不能很恰当很完善地得到控制。
常见的分流道的横
截lAb1圆形断诎分流道2正六边形分流道3梯形断妞分流道4U形断妞分
流道5半圆形断面分流道6矩形断面分流道
注射机喷嘴起到型腔入U为止这一段流道中的塑料一直保持熔融状
态,从而在开模时只需取产品,
而不必取浇注系统凝料。
(1)分型面应选在塑件外形最大轮廓处(首要原则)。
当己经初步确
定塑件的分型方向后分型面应选在塑件外形最大轮廓处,即通过该方向上
塑件的截面积最大,否则塑件无法从型腔屮脱出。
(2)有利于简化模具结构,避免、减少侧抽机构。
(3)满足塑件的
外观质量要求。
选择分型面时应避免对塑件的外观质量产生不利的影响,
同时需考虑分型面处所产生的飞边是否容易修整清除,在可能的情况下,
应避免分型面处产生飞边。
(4)确定有利的留模方式,便于塑件顺利脱模。
通常分型UJ的选择应尽可能使塑件在开模后留在动模一侧,这样有助于动
模内设置的推出机构动作,否则在定模内设置推出机构往往会增加模具整
体的复杂性。
(5)有利于保证塑件的相关精度。
与分型面垂直方向的高
度尺寸,若精度要求较高,或同轴度要求较高的外圆或内孔,为保证同轴
度,应尽可能设置在同一半模具型腔内。
如果塑件上精度要求较高的成型
表诎被分型面分割,就有可能由于合模精度的影响引起形状和尺寸上不允
许的偏差,塑件因达不到所需的精度要求而造成废品。
(6)有利于减少抽
拔距离。
当塑件需侧向抽芯时,为保证侧向型芯的放置容易及抽芯机构的
动作顺利,选定分型面时,应以浅的侧向凹孔或短的侧向凸台作为抽芯方
向,将较深的凹孔或较高的凸台放在幵合模方向,并尽量把侧向抽芯机构
设置在动模一侧。
(7)有利于排气。
分型面应尽量与型腔充填时塑料熔体
的料流末端所在的型腔内壁表面重合。
(8)便于模具加工制造。
为了便于
模具加工制造,松尽量选择平直分型面或易于加工的分型面。
(9)对成型
面积的影响。
注射机一般都规定其相应模具所充许使用的最大成型面积及
额定锁模力,注射成型过程中,当塑件(包括浇注系统)在合模分型面上
的投影血积超过允许的最大成型lif积时,将会出现涨模溢料现象,这时注
射成型所需的合模力也会超过额定锁模力。
因此,为了可靠地锁模以避免
涨模溢料现象的发生,选择分型面时应尽量减少塑件(型腔)在合模分型
面上的投影面积,
为:
整体式、整体嵌入式凹模、局部镶嵌式、四壁拼合的组合式、底
部大面积镶嵌组合式。
如果凹模镶件是回转体,而型腔是非回转体,则应
考虑只赚定位。
局部镶嵌式凹模的目的:
(1)简化凹模加工,将复杂的凹
模内形部的加工变成镶件的外形加工。
降低了凹模整体的加工难度。
(2)
镶件用高碳钢或高碳合金钢淬火。
淬火后变形较小,可用专用磨床研磨复
杂形状和曲面。
凹模中使用镶件的局部凹模有较高精度,经久的耐磨性并
可置换。
(3)可节约优质塑料模具钢,尤其对于大型模具更是如此。
(4)
有利于排气系统和冷却系统的通道的设计和加工。
计算的方法有两种:
一种是按平均收缩率、平均制造公差和平均磨损
量进行计算,即平均值法;另一种是按极限收缩率、极限制造公差和极限
磨损量进行计算,即极限值法。
前一种计算方法简便,但可能有误差,在
精密塑料制品的模具设计中受到一定限制;后一种计算方法能保证所成型
的塑料制品在规定的公差范围内,但计算比较复杂,主要用于精密成
型
10.
(1)成型零件制造误差。
成型零件制造误差直接影响着塑料制品的
尺寸公差,成型零件的公差等级愈低,塑料制品的公差等级也愈低。
(2)成型收缩率波动。
所谓成型收缩率,是指室温时塑料制品与模
具型腔两者尺寸的相对差。
(3)成型零件磨损量(含修模余量)LM-LS成型零件磨损
量结果使型腔尺eS=?
100%寸变大,型芯尺寸变小,中LM心距基本保持不变。
为了简化计算,凡是垂直于脱模方向的成型零件表面可不考虑磨损;
凡是平行于脱模方向的表面应考虑磨损。
生产大尺寸槊件时,因收缩率波动对制件误差影响较大,若单靠提高
模具制造精度来提高塑件精度是困难的和不经济的,而应着重稳定工艺条
件,选用收缩率波动小得塑件。
生产小尺寸塑件时,影响塑件误差的主要
因素屮模具成型零件的制造误差和成型零件表面的磨损值则占有较大的
例,英语收缩率波动的影响同事给予考虑
11.
应具有足够的强度和刚度。
如果型腔侧壁和底板厚度过小,可能因强
度不够而产生塱性变形甚至破环,也可能因刚度不足而产生挠曲变形,导
致溢料和出现飞边,降低塑件尺寸精度并影响顺利脱模。
因此,应通过强
度和刚度计算来确定型腔壁厚,尤其对于重要的精度要求高的或人型模具
的型腔,更不
能单纯凭经验来确定型腔侧壁和底板厚度,因此要对注塑模进行强度
和刚度计算校核。
12.
作用:
合模时,首先是导向零件接触,引导动定模或上下模准确闭合,
避免型芯先进入型腔造成成型零件损坏。
定位作用:
模具闭合后,保证动
定模或上下模位置正确,保证型腔的形状和尺精确,导向机构在模具装
配过程屮也起定位作用,便子装配和调整。
3
13.
(1)机构简单动作可靠。
推出机构应使推出动作可靠、灵活,制
造方便,机构本身要有足够的强度、刚度和硬度,以承受推出过程中的各
种力的作用,确保塑件顺利地脱模。
(2)保证塑件不因推出而变形损坏。
为了保证塑件在推出过程中不变形、不损坏,设计时应仔细分析塑件对模
具的包紧力和粘附力的大小,合理的选择推出方式及推出位置,从而使塑
件受力均匀、不变形、不损坏。
对脱模机构的要求:
(1)机构简单动作
可靠。
推出机构应使推出动作可靠、灵活,制造方便,机构本身要有足够
的强度、刚度和硬度,以承受推出过程中的各种力的作用,确保塑件顺利
地脱模。
(2)保证塑件不因推出而变形损坏。
为了保证塑件在推出过程中不
变形、不损坏,设计时应仔细分析塑件对模具的包紧力和粘附力的大小,
合理的选择推出方式及推出位置,从而使塑件受力均匀、不变形、不损坏。
塑件在模内冷却定型时,会对型芯有包紧力(即正压力),在脱模过
程中并产生摩擦阻力,
故需对塑件施加脱模力,脱模力须大于摩擦阻力。
对于不带通孔的壳
体类塱件,脱模时还需克服大气压力。
另外,尚需克服塑件与钢材之间的
粘附力及脱模机构本身的运动阻力。
14.
型腔不发生溢料;保证塑件精度;保证塑件顺利脱模。
15.、推杆脱模机构。
用推杆推出制品,尤其是圆推杆推出制品是推
出机构屮最简单、最常用的一种。
因它制造简单,更换方便,滑动阻力小,脱模效果好,设置的位置自由度大,且容易实现标准化,所以在生产中广泛应用。
但因推杆和制品接触面积小,容易引起应力集中,从而可能损坏
制品或使制品变形,因此不宜用于斜度小和脱模力大的管形和箱形制品的
脱模。
2、推管脱模机构。
对于中心带孔的圆筒形制品或局部是圆筒形的制
品,可用推管推出机构进行脱模。
推管推出机构和推杆推出机构的运动方
式基本相同,只是推管屮间有一个固定型芯.用销或键固定型芯,推管屮
部开有槽,槽在销的下方长度I应大于推出的距离。
其特点是型芯较短,
模具结构紧凑,但型芯紧固力小,而且要求推管与型芯和凹模板间的配合
精度较高(IT7),适用于型芯直径较大的模具。
型芯的台肩固定在模具动
模座板上,型芯较长,但结构可靠,多用于推出距离不大的场合;推管在
凹模板内移动,可缩短推管和型芯的长度,但凹模板厚度增加;扇形推管,
这种结构也具有推管在凹模板内移动形式的优点,但推管制造麻烦,强度较低,容易损坏
3
、推件板脱模机构。
推件板又称脱模板。
适用于薄壁容器、筒形制品、
大型罩壳及各种带一个或多个孔的塑件。
这种机构的特点是,在制品的整
个周边进行推出,因而脱模力大而且均匀,运动平稳,无明显推出痕迹。
16.
17.
出机构位于模具的动模一边,所以注射模的推出机构宜设在动模一侧,
幵模后让制品留在动模,以便脱出制品。
但有时因制品的特殊要求或受制
M形状的限制,7T•模后制to将留在定模上(或有可能留在定模上),则应
在定模一侧设置推出机构。
双脱模机构:
在实际生产中往往会遇到一些形
状特殊的塑件,