组合机床毕业论文正.docx
《组合机床毕业论文正.docx》由会员分享,可在线阅读,更多相关《组合机床毕业论文正.docx(28页珍藏版)》请在冰豆网上搜索。
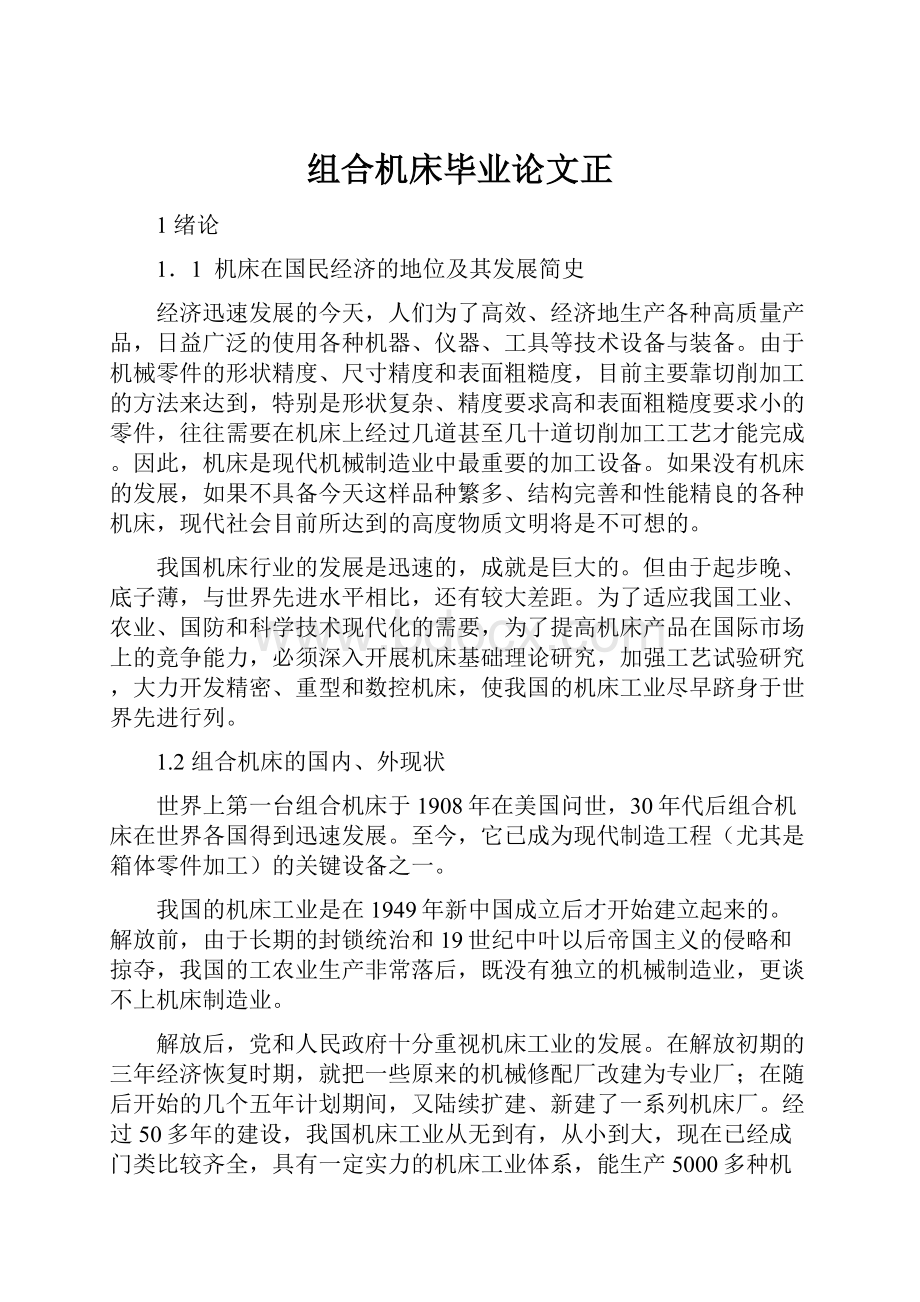
组合机床毕业论文正
1绪论
1.1机床在国民经济的地位及其发展简史
经济迅速发展的今天,人们为了高效、经济地生产各种高质量产品,日益广泛的使用各种机器、仪器、工具等技术设备与装备。
由于机械零件的形状精度、尺寸精度和表面粗糙度,目前主要靠切削加工的方法来达到,特别是形状复杂、精度要求高和表面粗糙度要求小的零件,往往需要在机床上经过几道甚至几十道切削加工工艺才能完成。
因此,机床是现代机械制造业中最重要的加工设备。
如果没有机床的发展,如果不具备今天这样品种繁多、结构完善和性能精良的各种机床,现代社会目前所达到的高度物质文明将是不可想的。
我国机床行业的发展是迅速的,成就是巨大的。
但由于起步晚、底子薄,与世界先进水平相比,还有较大差距。
为了适应我国工业、农业、国防和科学技术现代化的需要,为了提高机床产品在国际市场上的竞争能力,必须深入开展机床基础理论研究,加强工艺试验研究,大力开发精密、重型和数控机床,使我国的机床工业尽早跻身于世界先进行列。
1.2组合机床的国内、外现状
世界上第一台组合机床于1908年在美国问世,30年代后组合机床在世界各国得到迅速发展。
至今,它已成为现代制造工程(尤其是箱体零件加工)的关键设备之一。
我国的机床工业是在1949年新中国成立后才开始建立起来的。
解放前,由于长期的封锁统治和19世纪中叶以后帝国主义的侵略和掠夺,我国的工农业生产非常落后,既没有独立的机械制造业,更谈不上机床制造业。
解放后,党和人民政府十分重视机床工业的发展。
在解放初期的三年经济恢复时期,就把一些原来的机械修配厂改建为专业厂;在随后开始的几个五年计划期间,又陆续扩建、新建了一系列机床厂。
经过50多年的建设,我国机床工业从无到有,从小到大,现在已经成门类比较齐全,具有一定实力的机床工业体系,能生产5000多种机床通用品种,数控机床1500多种,不仅装备了国内的工业,而且每年还有一定数量的机床出口。
1.2.1国内组合机床现状
近年来我国企业的数控机床占有率逐年上升,在大中企业已有较多的使用,在中小企业甚至个体企业中也普遍开始使用。
1.2.2国外组合机床现状
国外汽车工业的大批量生产,每种零件的生产纲领少则几万件,多则几十万件,甚至上百万件,生产节拍为每件几秒钟到几十秒钟,其生产设备采用高效自动化装备。
1.3机床设计的目的、内容、要求
1.3.1设计的目的
机床设计毕业设计,其目的在于通过机床主运动机械变速传动系统的结构设计,使我们在拟定传动和变速的结构方案过程中,得到设计构思、方案的分析、结构工艺性、机械制图、零件计算、编写技术文件和查阅资料等方面的综合训练,树立正确的设计思想,掌握基本的设计方法,培养基本的设计方法,并培养了自己具有初步的结构分析、结构设计和计算能力。
1.3.2设计内容
(1)运动设计根据给定的被加工零件,确定机床的切削用量,通过分析比较拟定传动方案和传动系统图,确定传动副的传动比及齿轮的齿数,并计算主轴的实际转速与标准的相对误差。
(2)动力设计根据给定的工件,初算传动轴的直径、齿轮的模数;确定动力箱;计算多轴箱尺寸及设计传动路线。
完成装配草图后,要验算传动轴的直径,齿轮模数否在允许范围内。
还要验算主轴主件的静刚度。
(3)结构设计进行主运动传动轴系、变速机构、主轴主件、箱体、润滑与密封等的布置和机构设计。
即绘制装配图和零件工作图。
(4)编写设计说明书
1.3.3设计要求
评价机床性能的优劣,主要是根据技术—经济指标来判定的。
技术先进合理,亦即“质优价廉”才会受到用户的欢迎,在国内和国际市场上才有竞争力。
机床设计的技术—经济指标可以从满足性能要求、经济效益和人机关系等方面进行分析。
1.4机床的设计步骤
1.4.1调查研究
研究市场和用户对设计机床的要求,然后检索有关资料。
其中包括情报、预测、实验研究成果、发展趋势、新技术应用以及相应的图纸资料等。
通过对上述资料的分析研究,拟订适当的方案,以保证机床的质量和提高生产率,使用户有较好的经济效益。
1.4.2拟定方案
通常可以拟定出几个方案进行分析比较。
每个方案包括的内容有:
工艺分析、主要技术参数、总布局、传动系统、液压系统、控制操作系统、电系统、主要部件的结构草图、实验结果及技术经济分析等。
1.4.3工作图设计
首先,在选定工艺方案并确定机床配置形式、结构方案基础上,进行方案图纸的设计。
这些图子包括:
被加工零件工序图、加工示意图、机床联系尺寸图和生产率计算卡,统称“三图一卡”设计。
并初定出主轴箱轮廓尺寸,才能确定机床各部件间的相互关系。
2组合机床的总体设计
2.1组合机床方案的制定
2.1.1制定工艺方案
零件加工工艺将决定组合机床的加工质量、生产率、总体布局和夹具结构等。
所以,在制定工艺方案时,必须计算分析被加工零件图,并深入现场了解零件的形状、大小、材料、硬度、刚度,加工部位的结构特点加工精度,表面粗糙度,以及定位,夹紧方法,工艺过程,所采用的刀具及切削用量,生产率要求,现场所采用的环境和条件等等。
根据被加工被零件(减速箱箱盖)的零件图(图2.1),加工八个螺栓孔的工艺过程。
(1)加工孔的主要技术要求。
1)加工4个M8螺纹底孔的孔。
2)孔的位置度公差为Φ0.1mm,与Φ12孔同心。
3)工件材料为HT21-40,HB170~241
4)要求生产纲领为(考虑废品及备品率)年产量6万件,单班制生产
(2)工艺分析
加工该孔时,孔的位置度公差为0.1mm。
根据组合机床用的工艺方法及能达到的经济精度,可采用如下的加工方案。
一次性加工螺纹底孔,孔径为Φ6.5。
(3)定位基准及夹紧点的选择
2.1.2确定组合机床的配置形式和结构方案。
(1)被加工零件的加工精度
被加工零件需要在组合机床上完成的加工工序及应保证的加工精度,是制造机床方案的主要依据。
离合器压盘加工孔的精度要求不高,可采用钻孔组合机床,工件各孔间的位置精度为0.1mm,它的位置精度要求不是很高,安排加工时可以在下一个安装工位上对所有孔进行最终Ra3.2um的孔。
被加工零件图如图2-1所示。
图2.1被加工零件图
(2)被加工零件的特点
这主要指零件的材料、硬度加工部位的结构形状,工件刚度定位基准面的特点,它们对机床工艺方案制度有着重要的影响。
此离合器压盘的材料是HT21-40、硬度HB170-241、孔在整个压盘上呈90度均度分配,孔的直径为Φ6.5mm。
采用多孔同步加工,零件的刚度足够,工件受力不大,振动,及发热变形对工件影响可以不计。
(3)机床使用条件
2.2确定切削用量及选择刀具
2.2.1确定工序间余量
为使加工过程顺利进行并稳定的保证加工精度,必须合理地确定工序余量。
生产中常用查表给出的组合机床对孔加工的工序余量,由于在本钻床上钻孔后重新安装或在其他多工位机床上加工下道工序,应适当加大余量,以消除转、定位误差的影响。
2.2.2选择切削用量
确定了在组合机床上完成的工艺内容了,就可以着手选择切削用量了。
因为所设计的组合机床为多轴同步加工在大多数情况下,所选切削用量,根据经验比一般通用机床单刀加工低30%左右.多轴主轴箱上所有刀具共用一个进给系统,通常为标准动力滑台,工作时,要求所有刀具的每分钟进给量相同,且等于动力滑台的每分钟进给量(mm/min)应是适合有刀具的平均值。
以满足不同直径的加需要,即:
·
=
·
=…=
·
=
式中:
…
——各主轴转速(r/min)
…
——各主轴进给量(mm/r)
——动力滑台每分钟进给量(mm/min)
由于离合器压盘孔的加工精度、工件材料、工作条件、技术要求都是相同的。
按照经济地选择满足加工要求的原则,采用查表的方法查得:
钻头直径D=6.5mm,铸铁HB175~255、进给量f=0.1mm/r、切削速度v=15m/min.
2.2.3确定切削力、切削扭矩、切削功率
根据选定的切削用量(主要指切削速度v及进给量f)确定切削力,作为选择动力部件(滑台)及夹具设计的依据;确定切削扭矩,用以确定主轴及其它传动件(齿轮,传动轴等)的尺寸;确定切削功率,用以选择主传动电动(一般指动力箱)功率,通过查表计算如下:
布氏硬度:
HB=HBmin-
(HBmax-HBmin)
=170-
(241-170)
=146.33
切削力:
=26
=26×6.5×
×
=535.16N
切削扭矩:
=10
=10×
×
×
=2452.26N·mm
切削功率:
=
=2452.26×15/(9740×3.14×10)
=0.123kw
式中:
HB——布氏硬度
F——切削力(N)
D——钻头直径(mm)
f——每转进给量(mm/r)
T——切削扭矩(N·mm)
V——切削速度(m/min)
P——切削功率(kw)
2.2.4选择刀具结构
离合器压盘的布氏硬度在HB170~241,孔径D为6.5mm,刀具的材料选择高速钢钻头(W18Cr4V),为了使工作可靠、结构简单、刃磨简单,选择标准Φ6.5的麻花钻。
孔加工刀具的长度应保证加工终了时刀具螺旋槽尾端与导向套之间有30~50mm的距离,以便排出切屑和刀具磨损后有一定的向前的调整量。
2.3钻孔组合机床总设计“三图一卡”的编制
前面对四轴头多工位同步钻床工艺方案及配置型式、结构方案确定的有关问题,它是钻床总体设计的重要内容。
下面就以钻床加工箱盖总体设计的另一个问题,既总体设计方案的图纸表达形式——“三图一卡”设计,其内容包括:
绘制被加工零件工序图、加工示意图、机床联系尺寸图、编制生产率卡。
2.3.1被加工零件工序图
(1)被加工零件工序图的作用及内容
被加工零件工序图是根据选定的工艺方案,表示一台组合机床完成的工艺内容,加工部位的尺寸、精度、表面粗糙度及技术要求,加工用的定位基准、夹具部位及被加工零件的材料、硬度、重量和在本道工序加工前毛坯或成品状况的图纸,它不能用用户提供的图纸代替,而是在原零件图基础上,突出本机床的加工的内容,加上必要的说明绘制成的。
离合器压盘用钻孔组合机床的被加工零件工序图如2.2所示。
(2)绘制被加工零件工序图的注意事项:
1)为了使被加工零件工序图清晰明了,一定要图出被本机床的加工内容。
绘制时,应按一定的比例,选择足够的视图及剖视图,突出加工部位(用粗实线),并把零件轮廓及与机床、夹具设计有关部位(用细实线)表清楚,凡本道工序保的尺寸、角度等,均应在尺寸数值下方面用粗实线标记。
如图2.2中4-Φ12加工用定位基准,机械夹压位置及方向,辅助支承均须用规定的符号表示出来。
图2.2被加工零件工序图
附注:
1.被加工零件名称及编号:
离合器压盘;
2.材料及硬度:
灰铸铁HT21-40JB307-62HB175~255;
2)加工部位的位置尺寸应由定位基准注起,为便于加工及检查,尺寸应采用直角坐标系标出,而不采用极坐标,但有时因所选定位基准与设计基准不重合,则须对加工部位要求位置尺寸精度进行分析换算。
2.3.2加工示意图
图2.3加工示意图
(1)加工示意图的作用和内容
加工示意图是被加工零件工艺方案在图样上的反映,表示被加工零件在机床上的加工过程,刀具的布置以及工件、夹具、刀具的相对位置关系,机床的工作行程及工作循环等,是刀具、夹具、多轴箱、电气和液压系统设计选择动力部件的主要依据,是整台组合机床布局形式的原始要求,也是调整机床和刀具所必需的重要文件。
图2.3为箱盖上4孔立式钻床。
加工示意图在图上应标注的内容:
1)机床的加工方法,切削用量,工作循环和工作行程。
2)工件、夹具、刀具及多轴箱端面之间的距离等。
3)主轴的结构类型,尺寸及外伸长度;刀具类型,数量和结构尺寸、接杆、导向装置的结构尺寸;刀具与导向置的配合,刀具、接杆、主轴之间的连接方式,刀具应按加工终了位置绘制。
(2)绘制加工示意图之前的有关计算
1)刀具的选择刀具选择考虑加工尺寸精度、表面粗糙度、切削的排除及生产率要求等因素。
刀具的选择前已述及,此处就不在追述了。
2)导向套的选择在组合机床上加工孔,除用刚性主轴的方案外,工件的尺寸、位置精度主要取决于夹具导向。
因此正确选择导向装置的类型,合理确定其尺寸、精度,是设计组合机床的重要内容,也是绘制加工示意图时必须解决的内容。
导向套的参数根据刀具的直径选择固定导向装置,如图2.4所示:
图2.4固定导向装置
固定导向装置的标准尺寸如下表:
表2.1固定导向装置的标准尺
D
D
D1
D2
L
l1
m
R
d1
d2
l0
6.5
12
22
30
28
38
13
18
M8
16
16
固定装置的配合如下表:
表2.2固定装置的配合
导向
类别
工艺
方法
D
D
D1
刀具导向
部分外径
固定
导向
钻孔
G7(或F8)
g6
固定导向装置的布置如图2.5所示
导向装置的布置如表2.3所示:
表2.3导向装置的参数(mm)
尺寸
项目
l1
l2
l3
与直径d的关系
(2~3)d
加工铸铁
d
d/3+(3~8)
计算值
3×d=30
25.4
25.4/3+8=16.5
图2.5固定导向装置的布置
初定主轴类型、尺寸、外伸长度
因为轴的材料为40Cr,剪切弹性模量G=81.0GPa,刚性主轴取ψ=1/4(0)/m,所以B取2.316,
根据刚性条件计算主轴的直径为:
d
B
=2.316×
=17.52mm
式中:
d——轴直径(mm)
T——轴所承受的转矩(N·mm)
B——系数
本设计中所有主轴直径皆取d=20mm,主轴外伸长度为:
L=115mm,D/
为32/20,内孔长度为:
l1=77mm.
选择刀具接杆由以上可知,多轴箱各主轴的外伸长度为一定值,而刀具的长度也是一定值,因此,为保证多轴箱上各刀具能同时到达加工终了位置,就需要在主轴与刀具之间设置可调环节,这个可调节在组合机床上是通过可调整的刀具接杆来解决的,连接杆如图2.6所示,
图2.6可调连接杆
连接杆上的尺寸d与主轴外伸长度的内孔D配合,因此,根据接杆直径d选择刀具接杆参数如表2.4所示:
表2.4可调接杆的尺寸
d(h6)
D1(h6)
d2
d3
L
l1
l2
l3
螺母
厚度
20
Tr20×6
莫氏1号
12.061
17
188
46
40
100
12
确定加工示意图的联系尺寸
从保证加工终了时主轴箱端面到工件端面间距离最小来确定全部联系尺寸,加工示意图联系尺寸的标注如图2.3所示。
其中最重要的联系尺寸即工件端面到多轴箱端面之间的距离(图中的尺寸333mm),它等于刀具悬伸长度、螺母厚度、主轴外伸长度与接杆伸出长度(可调)之和,再减去加工孔深度和切出值。
图2.7工作进给长度
2.3.3机床联系尺寸图
图2.8机床联系尺寸图
(1)、联系尺寸图的作用和内容
一般来说,组合机床是由标准的通用部件——动力箱、动力滑台、立柱、立柱底座加上专用部件——多轴箱、刀、辅具系统、夹具、液、电、冷却、润滑、排屑系统组合而成。
联系尺寸图用来表示机床各组成部件的相互装配和运动关系,以检验机床各部件的相对位置及尺寸联系是否满足要求,通用部件的选择是否合适,并为进一步开展主轴箱、夹具等专用部件、零件的设计提供依据。
如图2.8所示,机床联系尺寸图的内容包括机床的布局形式,通用部件的型号、规格、动力部件的运动尺寸和所用电动机的主要参数、工件与各部件间的主要联系尺寸,专用部件的轮廓尺寸等。
(2)、选用动力部件
选用动力部件主要选择型号、规格合适的动力滑台、动力箱。
1)滑台的选用通常,根据滑台的驱动方式、所需进给力、进给速度、最大行程长度和加工精度等因素来选用合适的滑台。
=
∑
=4×1071.79=4287.16N
式中:
——各主轴加工时所产生的轴向力
2)由下式估动力箱的选用动力箱主要依据多轴所需的电动机功率来选用,在多轴箱没有设计之前,
可算
=
/η
=4×0.123/0.8
=0.615KW
式中:
η——多轴箱传动效率,加工黑色金属时η=0.8~0.9;有色金属时η=0.7~0.8,本系统加工HT21-40JB307-62,取η=0.8.
动力箱的电动机功率应大于计算功率,并结合主轴要求的转速大小选择。
因此,选用电动机型号为Y100L—6B5的1TD25IA型动力箱,动力箱输出轴至箱底面高度为125mm。
主要技术参数如下表:
主电机传动型号
转速范围(r/min)
主电机功率(
)
配套主轴部件型号
电机转速
输出转速
Y100L-6B5
1430
706
1.5
1TA32、1TA32M、1TZ32~1TG32
3)Y轴液压滑台的选用
工件质量计算V=420×240×10+(2×160+2×340)×10×30
=1.308×10-3m3
m=ρv=7.0×103×1.308×10-3
=9.156kg
磨擦系数:
f=0.07~0.12取f=0.1
F=f·N=0.1mg=0.1×9.156×10=9.156N
(2)配套支承部件的选用
立柱1CL25型,立柱底座1CD25
(3)确定装料高度
装料高度指工件安装基面至机床底面的垂直距离,在现阶段设计组合机床时,装料高度可视具体情况在H=580~1060mm之间选取,本系统取装料高度为
976mm。
(4)中间底座轮廓尺寸
中间底座的轮廓尺寸要满足Y轴滑台在其上面联接安装的需要,又考虑到与立柱底座相连接。
因此,中间底座采用侧底座1CC32。
(5)确定多轴箱轮廓尺寸
本机床配置的多轴箱总厚度为301mm,宽度和高度按标准尺寸中选取。
计算时,多轴箱的宽度B和高度H可确定为:
B=500H=500
根据上述计算值,按主轴箱轮廓尺寸系列标准,最后确定主轴箱轮廓尺寸B×H=500X500mm。
2.4多轴箱的设计
2.4.1绘制多轴箱设计原始依据图
多轴箱设计原始依据图是根据“三图一卡”绘制的如图2.9所示:
如图2.9钻孔组合机床多轴箱原始依据图
图中多轴箱的两定位销孔中心连线为横坐标,工件加工孔对称,选择箱体中垂线为纵坐标,在建立的坐标系中标注轮廓尺寸及动力箱驱动轴的相对位置尺寸。
主轴的工序内容,切削用量及主轴尺寸及动力部件的型号和性能参数如表2.6所示:
表2.6主轴外尺寸及切削用量
轴号
主轴外伸尺寸
工序
内容
切削用量
D/d
L
N
(r/min)
V
(m/min)
f
(mm/r)
Vf
(mm/min)
1、2、3、4
20/12
115
钻Φ6.5
478
15
0.1
47.8
注:
1.被加工零件编号及名称:
箱盖;材料:
HT21-40JB297-62;硬度:
HB170-241
2.动力部件型号:
1TD25IA动力箱,电动机型号Y100L-6;功率P=1.5kw。
2.4.2齿轮模数选择
本组合机床主要用于钻孔,因此采用滚珠轴承主轴。
齿轮模数m可按下式估算:
m=(30~32)
=32×
=1.76
式中:
m——估算齿轮模数
P——齿轮所传递率(kw)
Z——对啮合齿中的小齿轮数
N——小齿轮的转速(r/min)
多轴箱输入齿轮模数取m1=3,其余齿轮模数取m2=2。
2.4.3多轴箱的传动设计
(1)根据原始依据图(图2.9),画出驱动轴、主轴坐标位置。
如下表:
表2.7驱动轴、主轴坐标值
坐标
销O1
驱动轴O
主轴1
主轴2
主轴3
主轴4
X
-175
0
-95
95
95
-95
Y
0
94.5
180
180
80
80
(2)确定传动轴位置及齿轮齿数
图2.10齿轮的最小壁厚
1)最小齿数的确定
为保证齿轮齿根强度,应使齿根到孔壁或键槽的厚度a
2m,驱动轴的直径为d=30mm,有《机械零件设计手册》知,如图2.10所示齿轮t=33.3mm,当m1=3时。
驱动轴上最小齿轮齿数为:
2(t/m1+2+1.25)-d0/m1
=2×(33.3/3+2+1.25)-30/3
=18.9
所以驱动轴齿数要大于等于19。
为减小传动轴的种类,所有传动轴的直径取30mm.
当m2=2,d=20时,齿轮t=23.3mm。
主轴上最小齿轮齿数为:
2(t/m2+2+1.25)-d0/m2
=2×(23.3/2+2+1.25)-20/2
=19.8
所以主轴齿数要大于等于20。
2)传动轴11为主轴1,2,3,4都各自在同一同心圆上。
多轴箱的齿轮模数按驱动轴出轮估算
m≥
多轴箱输入出轮模数取m1=3,其余齿轮模数取m2=2。
主轴1,2,3要求的转速一致且较高,所以采用升速传动。
主轴齿数选取Z=45,传动齿轮采用z=45齿的齿轮,变位系数
。
传动轴的转速为:
由于前面选取了主轴直径为30,显然传动轴直径都选取20,这样为了减少传动轴种类和设计题目需要由于传动轴转速是
,则驱动轴至传动轴的传动比为:
所以选择两级传动,且传动比分配为:
一级为1.2×1.2;二级为1.4×1.0。
驱动轴的直径为30mm,由《机械零件设计手册》查得知:
t=33.3mm,当m=3时,驱动轴上的齿数为:
Zmin≥
去驱动齿轮齿数Z=45。
通用的齿轮有三种,即传动齿轮、动力箱齿轮和电机齿轮。
材料均为45钢,热处理为齿部高频淬火G54。
本机床齿轮的选用按照下表选用
齿轮种类
宽度(mm)
齿数
模数(mm)
孔径(mm)
驱动轴齿轮
24
32
16~50连续
16~70
2、2.5、3
2、2.5、3、4
15、20、30、35、40
25、30、35、40、50
传动轴齿轮
44(B型)
45
2
25、30、40、50
输出轴齿轮
32
37
3
18、22、28、32、36
计算各主轴转速
使各主轴转速的相对转速损失在
5%以内。
由公式:
V=
知:
3夹具设计
机床夹具设计在组合机床设计中占有重要的地位。
它的好坏将直接影响工件加工表面的位置精度。
本夹具主要是用来钻沿φ305圆周方向性四等分平均分四个M8螺纹底孔,整个需要加工的孔的位置尺寸用机床和夹具就能直接保证。
因此,在本道工序加工时,主要应考虑如何保证垂直度要求的前题下,提高劳动生产率,降低劳动强度。
为了很好利用工厂实际设备和提高生产率,设计专用夹具进行加工。
3.1机床夹具的概述
3.1.1机床夹具的组成
(1)定位元件和定位装置用于确定工件正确位置的元件或装置,如V形块,定位销,凡是夹具都有定位元件,它是实现夹具基本功能的元件。
(2)夹紧元件和夹紧装置用于固定工件以获得的正确位置的元件或装置。
工件在夹具定位之后引进加工之前必须将工件夹紧,使其在加工时在切削力的作用下不离开已获得的定位,有时同一个元件既能定位,也具有夹紧的双重功效。
(3)导向元件确定刀具的位置并引导刀具的元件,它也可以供钻镗类夹具在机床上安装时做基准找正