哈工大材料学院材料表界面复习资料.docx
《哈工大材料学院材料表界面复习资料.docx》由会员分享,可在线阅读,更多相关《哈工大材料学院材料表界面复习资料.docx(17页珍藏版)》请在冰豆网上搜索。
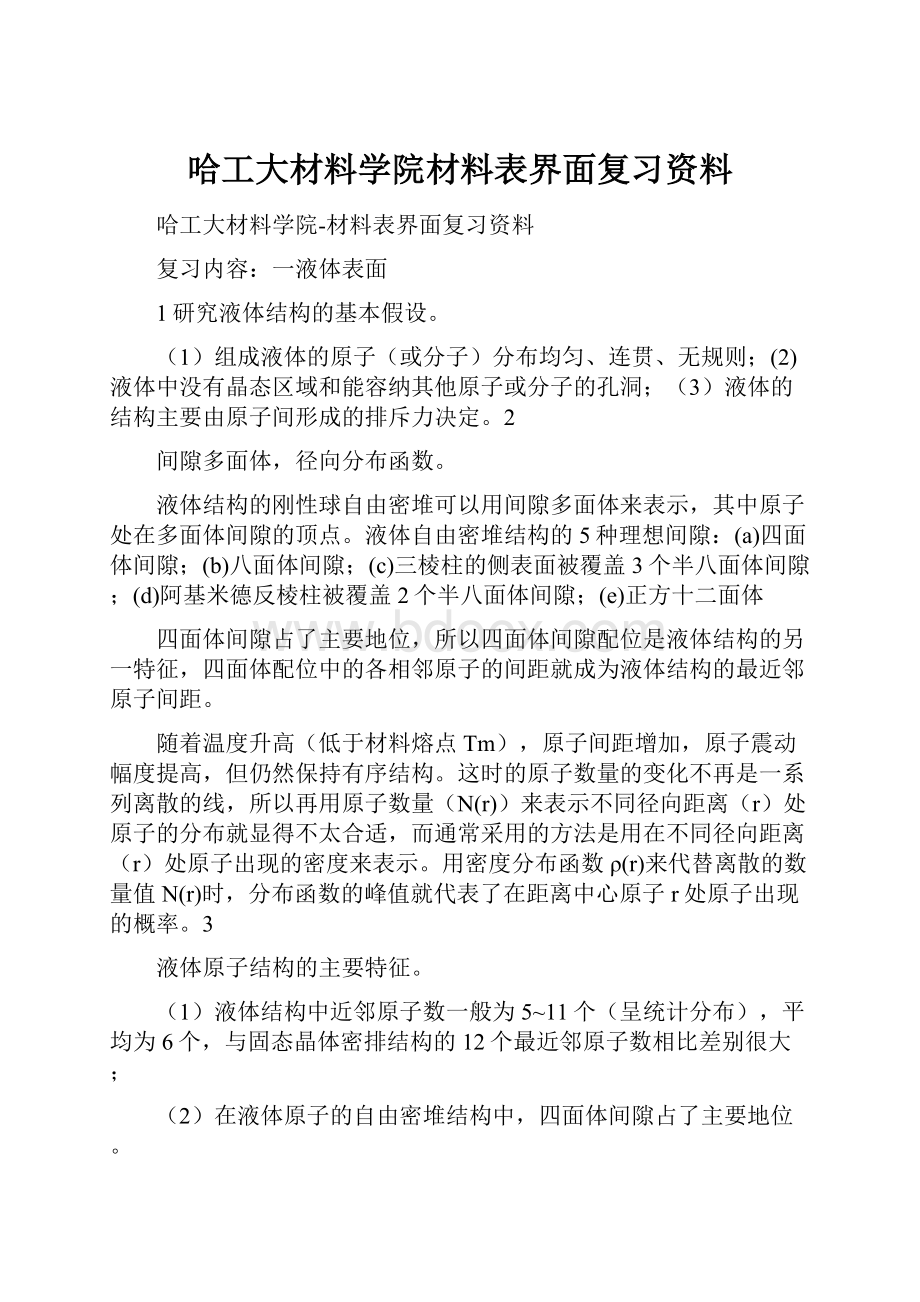
哈工大材料学院材料表界面复习资料
哈工大材料学院-材料表界面复习资料
复习内容:
一液体表面
1研究液体结构的基本假设。
(1)组成液体的原子(或分子)分布均匀、连贯、无规则;
(2)液体中没有晶态区域和能容纳其他原子或分子的孔洞;(3)液体的结构主要由原子间形成的排斥力决定。
2
间隙多面体,径向分布函数。
液体结构的刚性球自由密堆可以用间隙多面体来表示,其中原子处在多面体间隙的顶点。
液体自由密堆结构的5种理想间隙:
(a)四面体间隙;(b)八面体间隙;(c)三棱柱的侧表面被覆盖3个半八面体间隙;(d)阿基米德反棱柱被覆盖2个半八面体间隙;(e)正方十二面体
四面体间隙占了主要地位,所以四面体间隙配位是液体结构的另一特征,四面体配位中的各相邻原子的间距就成为液体结构的最近邻原子间距。
随着温度升高(低于材料熔点Tm),原子间距增加,原子震动幅度提高,但仍然保持有序结构。
这时的原子数量的变化不再是一系列离散的线,所以再用原子数量(N(r))来表示不同径向距离(r)处原子的分布就显得不太合适,而通常采用的方法是用在不同径向距离(r)处原子出现的密度来表示。
用密度分布函数ρ(r)来代替离散的数量值N(r)时,分布函数的峰值就代表了在距离中心原子r处原子出现的概率。
3
液体原子结构的主要特征。
(1)液体结构中近邻原子数一般为5~11个(呈统计分布),平均为6个,与固态晶体密排结构的12个最近邻原子数相比差别很大;
(2)在液体原子的自由密堆结构中,四面体间隙占了主要地位。
(3)液体原子结构在几个原子直径范围内是短程有序的,而长程是无序的。
4液体表面张力的概念及影响因素。
液体表面分子或原子受到内部分子或原子的吸引,趋向于挤入液体内部,使液体表面积缩小,因而在液体表面切向方向始终存在一种使液体表面积缩小的力,液体表面这种沿着切向方向,合力指向液体内部的作用力,就称为液体表面张力。
液体表面张力影响因素很多,如果不考虑液体内部分子或原子向液体表面的偏聚和外部原子或分子对液体表面的吸引,影响液体表面张力的因素主要有:
(2)表面所接触的介质:
液体的表面张力的产生是由于处于表面层的原子或分子一方面受到液体内部原子或分子的吸引,另一方面受到液体外部原子或分子的吸引。
当液体处在不同介质环境时,液体表面的原子或分子与不同物质接触所受的作用力不同,因此导致液体表面张力的不同。
一般来说,介质物质的原子或分子与液体表面原子或分子结合能越大,液体表面能越小,反之越大
(3)温度:
随着温度的升高,液体密度下降,液体内部原子或分子间的作用力降低,液体内部原子或分子对表面原子或分子的吸引力减弱,液体表面张力下降。
最早给出的预测液体表面张力与温度关系的半经验表达式为:
γ=γ0(1-T/Tc)n
式中Tc为液体的气化温度,γ0为0K时液体的表面张力。
5
液体表面偏聚。
液体中溶质原子向液体表面偏聚可以降低液体的表面能,因此是自发进行的过程。
表面能随组成液体的比例变化越大,产生表面偏聚倾向性越大。
式中C为溶质的浓度。
也就是说,在液体中,如果溶质的等温压缩率高于溶剂,则该溶质将具有向液体表面偏聚的倾向性。
另外,溶质原子是否发生表面偏聚,还受到溶质原子和溶剂原子的尺寸差影响。
6
弯曲液面的附加压力。
由液体表面张力和表面能的定义可知,液体表面的原子或分子始终受到一个沿液体表面切线方向使液体表面积缩小的力的作用。
当液体表面为平面时,表面张力的合力与液面垂直,合力为零;当液体表面为曲面时,表面张力合力不为零,合力将指向液体的内部或外部,即对液体产生一个附加压力。
三种液体的表面张力和附加压力示意图
当液面为凸液面时,液面曲率半径为正值,则产生的附加压力亦为正值,附加压力的方向指向液体的内部;当液面为凹液面时,液面曲率半径为负值,则产生的附加压力亦为负值,附加压力的方向指向液体的外部;如果液面为平面时,液面曲率半径为无穷大值,则产生的附加压力为零。
P附=2γ/r(γ为表面张力,r为曲率半径)
二固体表面
1固体表面能的影响因素。
影响固体表面能的主要因素有:
固体原子间的结合能、固体表面原子的晶面取向和温度。
由于表面能的大小主要取决于形成固体新表面所消耗的断键功,因此原子间的结合能越高,断开相同结合键需要消耗的能量越高,所形成的固体表面能越高。
由于固体晶体结构是各向异性的,不同晶面的原子面密度不同,所以形成单位面积的新表面需要断开原子键的数量不同,导致所形成的表面能不同。
一般来说,固体表面原子面密度越高,形成单位面积的新表面需要断开原子键的数量越小,表面能越低。
与液体一样,固体的表面能随温度的升高而下降,并且固体表面能随温度升高而下降的速度大于液体。
2固体不同晶面表面能的计算。
采用“近邻断键模型”(Nearet-neighborbroken-bondmodel)来计算固体晶体的表面能,两点假设:
第一,每个原子只与其最近邻的原子成键(最近邻原子数即为该晶体结构的配位数),并且只考虑最近邻原子间的结合能;
第二,原子间的结合能(-Ua)不随温度变化。
对于具有任意晶体结构的固态晶体,某一晶面{hkl}的表面能(γS{hkl})可以用下式计算:
γS{hkl}=N{hkl}Z(Ua/2)
式中,N{hkl}为{hkl}晶面单位面积的原子数,Z为晶体沿{hkl}晶面断开形成新表面时{hkl}晶面上每个原子需要断裂的键数。
简单立方晶体
晶面{hkl}{001}N{hkl}Z12γS{hkl}1a22Ua2a22a2{011}2Ua2a2{111}333Ua3a2面心立方晶体
晶面{hkl}{001}2a2Z4N{hkl}γS{hkl}2a2251(次表面)34Uaa2{011}a2{111}32Ua2a433a223Uaa2体心立方晶体
晶面{hkl}{001}N{hkl}Z451(次表面)3γS{hkl}2a224Uaa2{011}a2{111}32Ua2a23Uaa2433a2
3固体晶体平衡形状的确定方法。
固体表面的平衡形状为多面体,原因为不同晶面表面能不同,形成的原则是固体总表面自由能最低,确定方法:
在一个单晶体平衡多面体中,由多面体中心引出一组矢量,方向与多面体各表面垂直,矢量的长度与各晶面的表面能成正比。
在各矢量的端点做垂直于该矢量的平面,各平面相交则得到晶体的平衡形状。
二维晶体平衡形状确定示意图(a)和确定结果(b)4
固体晶体表面的小面化。
固体晶体断裂面是晶体的密排面时,表面能最低。
如果固体晶体受外力作用所形成的宏观断裂面不与晶体的密排面平行时,断裂表面的晶面组成可以由小面化理论给与说明。
断裂的宏观表面可以被分解为平行于晶体密排面的若干个小平面与连接这些小平面的连接面组成,使形成的总表面自由能最低。
这就是固体晶体的小面化。
5
固体晶体的表面缺陷。
位错露头:
螺位错形成表面台阶刃位错形成表面空隙三固体和液体的界面1润湿现象与润湿角
液体在固体表面上铺展的现象,称为润湿。
润湿与不润湿不是截然分开的,可用润湿角进行定量描述。
润湿角定义:
当固液气三相接触达到平衡时,从三相接触的公共点沿液—气界面作切线,切线与固-液界
面的夹角为润湿角。
润湿角大小与润湿程度的关系:
<90o:
润湿>90o:
不润湿=0o:
完全润湿=180o:
完全不润湿润湿角公式:
-g=-l+l-gco
所以co=(-g--l)/l-g
当-g>-l时,co>0,<90o,-g与-l差越大,润湿性越好。
当-g90o,-g与-l差越大,不润湿程度越大。
以上方程的使用条件:
-g--l≤l-g,-g为固体的表面能2临界表面张力。
表面能高的固体比表面能低的固体更容易被液体所润湿。
表面能低于0.1Nm的物质为低能表面,如:
有机物,高聚物。
表面能为1~10Nm的物质为高能表面,如:
金属,金属氧化物,无机盐。
低能表面不易被液体润湿,但表面张力很低的液体也可能润湿,甚至完全润湿低能表面。
对于某一低能表面的固体,当液体的表面张力达到c时,可完全润湿该固体,则c称为该固体被完全润湿的临界表面张力。
c是固体材料的一个特征值,其物理意义是:
只有表面张力小于c的液体,才能对该固体完全润湿。
大于c的液体,有一定的值。
由此又提出一个计算的经验公式:
co=1-(1-g-c)其中的单位是:
Nm;-=30~403铺展系数。
一种液体滴在另一种与其不相溶的液体或固体表面上,可能发生两种情况:
第一,液滴在另一液体或固体表面不铺展而成为凸镜或液滴,这时表明液滴本身内聚功大于该液体对另一液体或固体的粘附功。
第二,液滴在另一液体或固体表面铺展开而形成一层薄膜,这时表明液滴的本身内聚功小于该液体对另一液体或固体的粘附功。
一种液体能否在另一种与其不相溶的液体或固体表明上铺展,可用粘附功和内聚功之差来表示:
S=Wa-Wc
=[A+B-AB]-2B=A-B-ABS-铺展系数
S>0时,B在A表面上会自动铺展开,S值越大,铺展越容易。
S<0时,B在A表面上不铺展,负值越大,铺展越难。
S>0是铺展的基本条件,这时A-B-AB>0
对液相在固相表面的铺展:
A=-g,B=l-g,AB=l-,所以-g-l-->0,所以-g-l->l-gl-g。
这时润湿角方法已经不能再适用。
铺展是润湿的最高标准。
四固体和固体的界面1晶界自由度。
二维晶界有两个自由度:
两晶粒间夹角(位向角)和晶界与一个晶粒间夹角(方向角)。
三维晶界有五个自由度:
位向角:
3个,方向角:
2个。
2小角晶界结构特点。
相邻两晶粒间位向差小于15℃——小角晶界。
小角晶界分为倾斜晶界和扭转晶界。
-1
-1
-1
倾斜晶界:
对称倾斜晶界:
由一系列相同符号的刃型位错排列而成:
D=b/式中:
:
位向角,b:
布氏
矢量D:
位错间距
非对称倾斜晶界:
由两组相互垂直的刃型位错组成。
扭转晶界:
旋转轴与晶界面垂直,螺位错网络与中间良好区组成3大角晶界结构模型。
目前对大角晶界提出的晶界结构模型有:
晶界是由非晶体粘合物构成岛状模型:
小岛内原子排列整齐
晶界点缺陷模型:
晶界有大量空位间隙原子晶界结构位错模型
重合位置点阵4重合位置点阵。
多晶体晶界一般为大角晶界。
大角晶界的结构模型很多,其中重合位置点阵晶界(Coincident-iteLattice,CSL)模型比较成熟。
相邻两晶粒旋转时,到某一角度,两晶体中的某些原子位置对称(重合),这种点阵为重合位置点阵。
此时,晶界上的某些原子为两晶粒共有,类似于孪晶,晶界上由排列紊乱部分和无规则部分组成。
为了定量表示重合位置点阵的数值,用“∑”号表重合点阵占晶体点阵多少——重合数。
∑=(CSL单胞体积)/(晶体点阵单胞体积)重合位置点阵表示:
晶面指数、旋转角度、重合数。
5
晶界能与晶界位向角的关系。
晶界能与晶界位向角关系示意图
Eatb0θ晶界的能量为单位面积自由能,包含表面张力和成分偏聚的影响。
式中:
i——i元素化学,Γi——i元素界面与内部浓度差dF从图可以看出,在小角晶界范围内,晶界能(E)随晶界位向角(θ)的增加而迅速增大。
大角晶界界面能与位向角基本无关,但在共格孪晶(t)和重合位置点阵(a和b)出现时,晶界能有一个明显的下降。
6
晶界原子偏聚。
(a)偏聚现象:
晶界上溶质元素浓度高于晶内(10-1000倍)
(b)偏聚动力:
晶界处结构复杂、能量高,溶质元素在晶内产生畸变能。
溶质从晶内向晶界附近偏聚,使系统能量降低。
(c)正吸附与反吸附:
正吸附:
使晶界表面张力降低的溶质原子向晶界偏聚,如钢中C,P。
反吸附:
使晶界表面张力增加的溶质原子远离晶界,如钢中Al。
(d)偏聚与偏析:
偏聚:
固态扩散造成为平衡态——平衡偏聚
dAiidA
偏析:
液态凝固时形成,为非平衡态(e)影响因素:
晶界能;杂质原子与基体原子尺寸差;浓度;第三种元素——共同偏聚;晶界结构。
7
相界结构。
8相界能量9新相形状。
五金属表面热渗镀1概念、特点、分类。
定义:
用加热扩散的方法把一种或几种元素渗入基体金属的表面,可得到一扩散合金层,但有时表面上还
会残留一层很薄的覆层—热渗镀。
特点:
(1)靠热扩散形成表面强化层,结合力很强
(2)热渗镀材料的选择范围很宽
作用:
渗入不同元素,可得到不同的表面组织和表面性能,包括耐磨性、耐热性、耐腐蚀性、耐高温氧化
性。
分类:
(1)固溶法:
粉末包渗法、流化床法。
粉末包渗法:
把工件埋入装有渗层金属粉末的容器里,进行加热扩散。
为防止粉末烧结使工件表面难于清理,在粉末中要加入防粘结粉末(如Al2O3)。
为加速渗入过程,在粉末中加入活化剂(助渗剂),通过化学反应使渗层金属变成活性金属原子。
(2)液渗法:
热浸法,融溶法,盐溶法
热渗法:
将工件直接浸入某一液态金属中,形成合金镀层,继续加热使镀层扩散形成合金层。
例如:
钢热浸铝。
(3)气渗法:
加热工件到渗剂原子在基体中能显著扩散的温度,通入含有渗剂金属卤化物(MCl2)的氢气,在工件表面发生如下反应:
MCl2+A→ACl2+[M](A为基体金属)MCl2+H2→2HCl+[M]
反应生成的活性金属原子[M]渗入工件表面。
(4)离子轰击渗镀法:
通过在低真空下气体辉光放电使渗剂金属变成等离子态。
离子活性比原子高,再加上电场的作用,所以此方法渗速高,质量好。
(5)复合渗:
利用各种方法,将工件表面形一固相涂层,然后加热扩散。
镀层工艺和加热工艺多种多样。
2渗层形成条件。
渗层是基体金属和溶入元素原子混合或化合组成的薄层合金,渗层的形成需要如下条件:
(1)渗入元素必须能与基体金属形成固溶体或金属间化合物。
影响固溶体或金属间化合物形成的重要因素有:
原子相对大小,原子间的化学亲合力,点阵类型。
(2)渗入元素与基体之间必须保持紧密接触,或者说渗入元素可以在界面处被吸附。
(3)必须保持一定的温度,使原子获得足够的扩散动力。
(4)生成活性原子的化学反应必须满足一定的热力学条件,渗剂活性原子一般是依靠化学反应来提供的。
以气固渗剂为例,假定采用金属氯化物为渗剂气体可有以下三种化学反应:
置换反应:
A+MCl2(气)→ACl2+[M]还原反应:
MCl2(气)+H2→2HCl+[M]
分解反应:
MCl2(气)→Cl2+[M]3渗层组织特点。
(1)渗层的形成
渗层形成的过程为:
吸附→界面反应→内扩散→渗层
(2)渗层的组织特点
(a)有无限固溶体相图的渗层组织
渗层组织为单向二元固溶体组织,由表到里浓度逐渐变化。
(b)有限固溶体并有中间化合物形成的渗层组织
有限固溶并有中间化合物形成的渗层组织开始阶段如图中曲线①所示,表面B元素浓度继续增加,达到C1,表面形成AnBm并向内扩散,即形成曲线②,表面B元素浓度继续增加至Cβ,表面形成β相并向内扩散,达到曲线③。
六金属表面热喷涂1分类与特点。
金属表面热喷涂是利用专用设备将固体材料熔化并加速喷射到工件表面形成一种特制薄层,提高工件表面性能的表面处理方法。
分类
液态法:
用坩埚熔化金属,再用高压气体把金属喷射出去。
燃气法:
火焰溅射喷涂法,火焰粉末喷涂法。
气体放电法:
等离子喷涂法。
其技术特点主要有以下几点:
1取材广泛○
2可用于各种基体○
3基体保持较低温度○
4工效高,比电镀快○
5工件大小不受限制,可进行局部喷涂,工件或整体均可○
6涂层厚度易控制○
7满足各种性能需要:
耐磨、耐蚀、高温氧化、隔热、高温强度、密封、减磨(润滑)○、耐辐射、导电、绝缘等。
2涂层形成过程。
涂层的形成
粒子与基体碰撞产生变形,粒子热量被冷基体带走,粒子在变形中凝固,形成盘状组织。
由于冲击,圆盘往往破碎,如软化基体(如预热)、破碎可减弱。
脉冲压力P与以下因素有关:
质点速度、液体密度、质点刚性系数。
3涂层结合强度。
粒子与基体结合强度机械结合:
与基体毛化程度有关——毛化处理,与粒子与基体润湿性关系很大。
化学结合:
动力:
基体预热
喷涂粉末高的熔化潜热粉末自身发生放热反应(Al/Ni)条件:
基体表面充分活化,不能有氧化膜。
作用:
对溶解度极低的涂层可实现牢固结合。
基体预热最低温度与体系有关。
氧化物陶瓷粒子比较稳定,预热稳定较高。
陶瓷涂层残余应力较高,结合强度低于金属涂层
粒子速度很高时,粒子与基体距离达到晶格常数范围,发生键合—冶金结合,结合力提高七激光表面改性1特点
激光束和电子束发生器有足够的能量促使短时间内加热和活化工件大面积的表面区域。
是材料表面改性的重要方法,主要有如下特点:
①由于加热速度极快,基体温度不受影响
②加热层深几个μm,这样薄层熔化需要能量几个J/cm2,三束能量很高,可以在表面产生106~
108K/cm的稳定梯度,表明迅速熔化,此温度梯度又使熔化部分以109~1011K/速度冷却,S-L界面推移速度为每秒几米。
③激光表面改性可提高表面抗蚀性和耐磨性,还可用于半导体技术和催化剂技术。
④激光表面改性包括:
改变表面成分:
合金化、熔覆;改变表面结构:
表面相变硬化。
⑤表面形成亚稳组织,产生特种性能。
2表面相变硬化原理及硬化层组织与性能特点。
激光相变硬化及其组织
利用高能束照射在可相变硬化的材料表面(以钢为例)使表面迅速加入到相变温度以上,形成奥氏体,当光斑扫过后,表层奥氏体被内层金属快速冷却,得到马氏体。
硬化层的组织特点为:
组织超细化;化学成分不均匀——微区成分不均匀的马氏体或残余奥氏体;晶体缺陷密度提高;未熔碳化物数量减少;残余奥氏体增加。
(3)激光硬化层的特征与性能
能量密度为:
式中:
P为激光功率;D为光斑直径;V为扫描速度。
在不熔化的前提下,选择最大的E,得到最大的表面硬度和硬化层深度。
硬化层的性能特点为:
1硬度:
各种金属材料,硬度比极值提高20%,原因主要是细化晶粒;2耐磨性:
可以使GCr15钢的使用寿命提高一倍;3残余应力:
表面为残余压应力,次表面为残余拉应力;4疲劳性能:
由于产生表面压应力,提高疲劳性能(疲劳裂纹多产生于表面)。
3表面合金化方法及组要参数。
(1)工艺介绍
目的:
提高表面耐磨和防腐性能。
方法:
将合金化元素和陶瓷粉末以一定方式添加到基体金属表面,通过激光加热使其与基体表面共熔而混
合,形成表面特种合金层。
表面涂合金方法:
共沉积法和预沉积法。
共沉积法:
激光照射同时送入粉末,要求有高精度送粉设备。
预沉积法:
粉末涂刷、热喷涂、真空镀、电镀、化学镀、预制薄板或金属箔。
影响合金化的主要参数:
激光束参数:
I:
入射能量密度;tp:
脉冲持续时间;Ro:
材料对激光反射率d:
光斑尺寸;de:
有效光斑尺寸材料热力学参数:
D:
热扩散系数;T:
熔点;Po:
蒸气压
过程:
通过熔化表面膜A和部分基体B,把薄膜元素可控地结合入基体B中。
液态混合之后,快速凝固,使合金化元素结合到基体表面。
机制:
形成理想的表面合金;利用快速加热和快速凝固形成特殊的亚稳合金,实现特殊的性能。
4表面熔覆定义与方式及组织特点。
将具有某种特殊性能的粉末材料以最小的稀释度用激光火焰涂在基体表面,从而获得特殊的表面性能的表面改性方法称为激光表面涂覆。
与激光熔凝相似,只是熔化对象不同。
激光涂覆的组织特点为:
1晶粒细小(快冷所致)○。
2稀释度很低时,界面出元素不扩散。
稀释度较大时,涂层一侧发生液态扩散,扩散距离较大;基○
体一侧,固态扩散,扩散距离很小。
3由于涂层凝固收缩受到基体阻碍,冷却后得到的涂层内有残余应力。
另外,涂层与基体热膨胀系○
数不同。
产生裂纹。
解决办法:
预热基体,涂覆后热处理。
4气孔:
高温液相吸收空气中气体,凝固冷却后过饱和析出,凝固收缩形成气孔。
这种气孔细小,○
可用保护气氛进行防止。
基体与涂层界面大气孔和搭接涂层过程产生的大气孔,可以通过控制涂覆参数和搭接度解决。
八纳米材料
1纳米材料制备方法及其特点。
2纳米材料组织特点。
九金属基复合材料界面1界面分类。
金属基复合材料界面主要分为三类:
第一类界面的特征为金属基体和增强体之间既不反应也不互相溶解,界面相对比较平整。
第二类界面的特征为金属基体和增强体之间彼此不发生界面化学反应,但浸润性好,能发生界面相互溶解扩散,基体中的合金元素和杂质可能在界面上富集或贫化,形成犬牙交错的溶解扩散界面。
第三类界面的特征为金属基体和增强体之间彼此发生界面化学反应,生成新的化合物,形成界面层。
取决于复合工艺条件、加工和使用条件,实际复合材料中的界面可能不是单一的类型,而是以上三种类型的组合。
金属基复合材料的界面类型
类型一金属基体和增强体既不反应也不互相溶解Cu-WCu-Al2O3Ag-Al2O3Al-B(表面涂BN)Al-不锈钢Al-BAl-SiCMg-SiC2结合机制。
金属基复合材料中的界面结合基本可分为四类,即:
机械结合;共格和半共格原子结合;扩散结合;化学结合。
机械结合
类型二金属基体和增强体不反应但互相溶解Cu-Cr合金-WNb-WNi-CNi-W类型三金属基体和增强体之间发生反应生成界面反应物Cu-Ti合金-WTi-Al2O3Ti-BTi-SiCAl-SiO2Al-C(在一定温度下)Mg-Al18B4O33w基体与增强体之间纯粹靠机械结合力连接的结合形式称为机械结合。
它主要依靠增强材料粗糙表面的机械“锚固”力和基体的收缩应力来包紧增强材料产生摩擦力而结合。
结合强度的大小与纤维表面的粗糙程度有很大关系,界面越粗糙,机械结合越强。
只有当载荷应力平行于界面时才能显示较强的作用。
机械结合存在于所有复合材料中。
既无溶解又不互相反应的第一类界面属这种结合。
共格和半共格原子结合
共格和半共格原子结合是指增强体与基体以共格和半共格方式直接原子结合,界面平直,无界面反应产物和析出物存在。
金属基复合材料中以这种方式结合的界面较少。
扩散结合
扩散结合是基体与增强体之间发生润湿,并伴随一定程度的相互溶解而产生的一种结合。
这种结合与第二类界面对应,是靠原子范围内电子的相互作用产生的。
化学结合
是基体与增强体之间发生化学反应,在界面上形成化合物而产生的一种结合形式,由反应产生的化学键合提供结合力,它在金属基复合材料中占有重要地位,第三类界面属这种结合形式。
3残余应力的产生、计算及影响因素。
产生:
复合材料中,热残余应力的产生需具备如下三个方面的条件:
1、增强相与基体之间的界面结合良好;2、温度变化;3、增强相与基体间热膨胀系数的差异。
金属基复合材料中,一般基体合金的热膨胀系数相对较大,增强相的热膨胀系数相对较小,较大的热膨胀系数差异是复合材料中热残余应力产生的先决条件。
通常热膨胀系数差异越大,则热残余应力的数值越大。
可以用下面的模型来描述颗粒增强复合材料中热残余应力的产生:
假设无限大基体中镶嵌一弹性球型粒子,模型如图4-4所示。
R表示整个体积球的半径,r2为埋入粒子的半径,r0为没有约束时粒子的半径,rl为未受约束时基体中孔洞的半径。
在某一高温下有:
r2=r1=r0。
在冷却过程中,基体孔洞将向rl位移收缩;由于颗粒的热膨胀系数小,其只能收缩到r2位置,室温下有R≥r0>r2>rl,r0≈r1≈r2。
此时,在粒子与基体的界面处将有热残余应力存在。
普遍认为基体中存在的是平均残余拉应力,增强相承受的是平均残余压应力
图4-4球形夹杂产生残余应力模型
计算:
假设复合材料中界面结合强度足够高,以至在界面热错配应力作用下不发生滑动和开裂。
图(a)为在T1温度下复合材料处于原始状态(热错配应力为零)的示意图。
当该复合材料被加热到T2温度时,如果纤维与基体间无相互约束,则纤维与基体将发生自由膨胀,结果如图(b)所示。
但实际上复合材料中纤维与基体之间是相互约束的,并且我们前面已经假设界面不发生滑动和开裂,所以界面约束的作用结果是纤维受基体的拉伸作用而比自由膨胀时的膨胀量有所增加;而基体受纤维的压缩应力作用而比自由膨胀时的膨胀量有所减小,结果如图(c)所示。
由图1可以很显然得到以下计算公式:
dm=(T2-T1)αml(5.7)df=(T2-T1)αfl(5.8)dc=(T2-T1)αcl(5.9)
其中:
αm、αf和αc分别为基体、纤维和复合材料的热膨胀系数。
从上