CNC培训专题计划.docx
《CNC培训专题计划.docx》由会员分享,可在线阅读,更多相关《CNC培训专题计划.docx(9页珍藏版)》请在冰豆网上搜索。
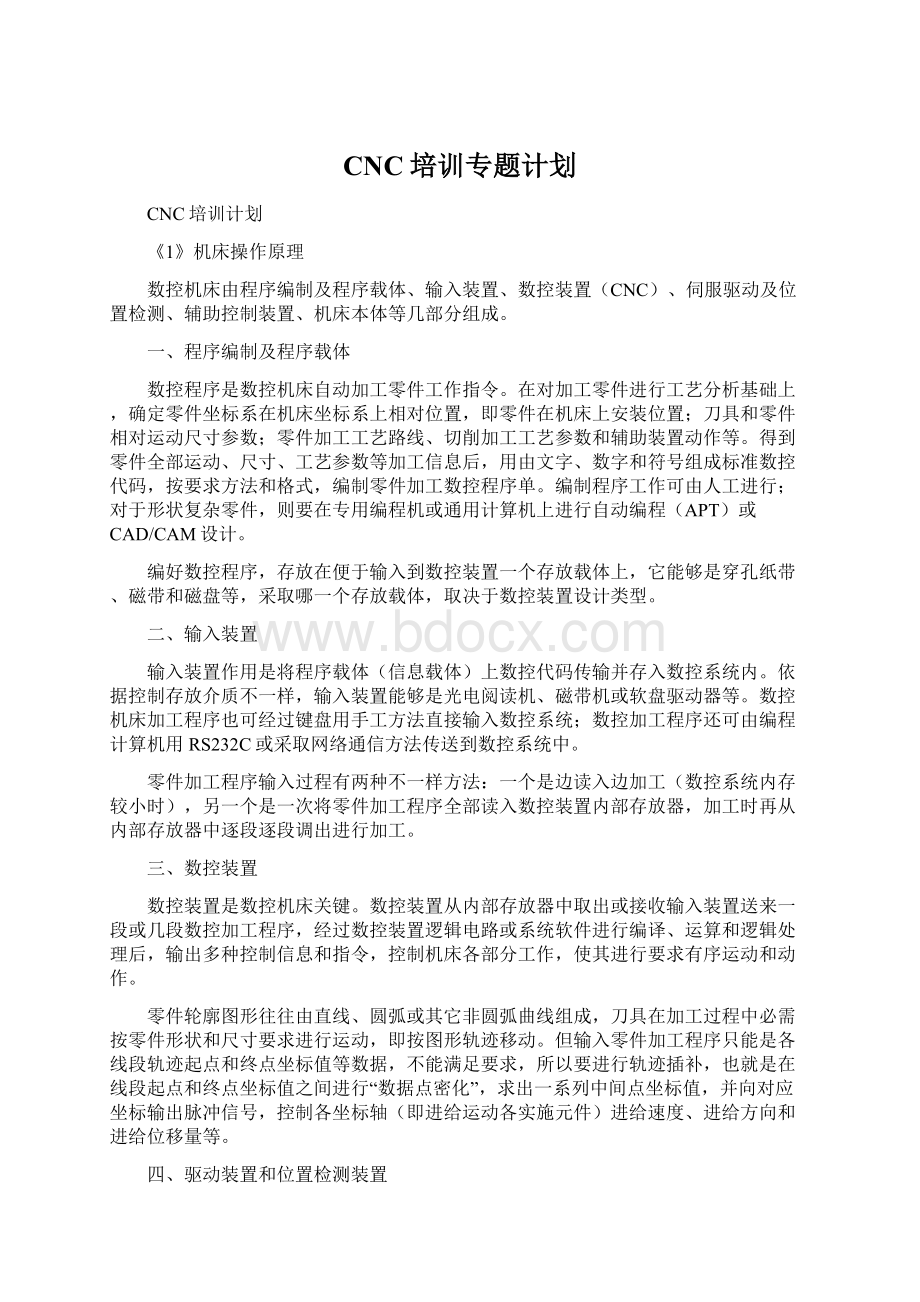
CNC培训专题计划
CNC培训计划
《1》机床操作原理
数控机床由程序编制及程序载体、输入装置、数控装置(CNC)、伺服驱动及位置检测、辅助控制装置、机床本体等几部分组成。
一、程序编制及程序载体
数控程序是数控机床自动加工零件工作指令。
在对加工零件进行工艺分析基础上,确定零件坐标系在机床坐标系上相对位置,即零件在机床上安装位置;刀具和零件相对运动尺寸参数;零件加工工艺路线、切削加工工艺参数和辅助装置动作等。
得到零件全部运动、尺寸、工艺参数等加工信息后,用由文字、数字和符号组成标准数控代码,按要求方法和格式,编制零件加工数控程序单。
编制程序工作可由人工进行;对于形状复杂零件,则要在专用编程机或通用计算机上进行自动编程(APT)或CAD/CAM设计。
编好数控程序,存放在便于输入到数控装置一个存放载体上,它能够是穿孔纸带、磁带和磁盘等,采取哪一个存放载体,取决于数控装置设计类型。
二、输入装置
输入装置作用是将程序载体(信息载体)上数控代码传输并存入数控系统内。
依据控制存放介质不一样,输入装置能够是光电阅读机、磁带机或软盘驱动器等。
数控机床加工程序也可经过键盘用手工方法直接输入数控系统;数控加工程序还可由编程计算机用RS232C或采取网络通信方法传送到数控系统中。
零件加工程序输入过程有两种不一样方法:
一个是边读入边加工(数控系统内存较小时),另一个是一次将零件加工程序全部读入数控装置内部存放器,加工时再从内部存放器中逐段逐段调出进行加工。
三、数控装置
数控装置是数控机床关键。
数控装置从内部存放器中取出或接收输入装置送来一段或几段数控加工程序,经过数控装置逻辑电路或系统软件进行编译、运算和逻辑处理后,输出多种控制信息和指令,控制机床各部分工作,使其进行要求有序运动和动作。
零件轮廓图形往往由直线、圆弧或其它非圆弧曲线组成,刀具在加工过程中必需按零件形状和尺寸要求进行运动,即按图形轨迹移动。
但输入零件加工程序只能是各线段轨迹起点和终点坐标值等数据,不能满足要求,所以要进行轨迹插补,也就是在线段起点和终点坐标值之间进行“数据点密化”,求出一系列中间点坐标值,并向对应坐标输出脉冲信号,控制各坐标轴(即进给运动各实施元件)进给速度、进给方向和进给位移量等。
四、驱动装置和位置检测装置
驱动装置接收来自数控装置指令信息,经功率放大后,严格根据指令信息要求驱动机床移动部件,以加工出符合图样要求零件。
所以,它伺服精度和动态响应性能是影响数控机床加工精度、表面质量和生产率关键原因之一。
驱动装置包含控制器(含功率放大器)和实施机构两大部分。
现在大全部采取直流或交流伺服电动机作为实施机构。
位置检测装置将数控机床各坐标轴实际位移量检测出来,经反馈系统输入到机床数控装置以后,数控装置将反馈回来实际位移量值和设定值进行比较,控制驱动装置根据指令设定值运动。
五、辅助控制装置
辅助控制装置关键作用是接收数控装置输出开关量指令信号,经过编译、逻辑判别和运动,再经功率放大后驱动对应电器,带动机床机械、液压、气动等辅助装置完成指令要求开关量动作。
这些控制包含主轴运动部件变速、换向和启停指令,刀具选择和交换指令,冷却、润滑装置开启停止,工件和机床部件松开、夹紧,分度工作台转位分度等开关辅助动作。
因为可编程逻辑控制器(PLC)含有响应快,性能可靠,易于使用、编程和修改程序并可直接开启机床开关等特点,现已广泛用作数控机床辅助控制装置。
六、机床本体
数控机床机床本体和传统机床相同,由主轴传动装置、进给传动装置、床身、工作台和辅助运动装置、液压气动系统、润滑系统、冷却装置等组成。
但数控机床在整体布局、外观造型、传动系统、刀具系统结构和操作机构等方面全部已发生了很大改变。
这种改变目标是为了满足数控机床要求和充足发挥数控机床特点。
《2》机床日常保养,详见CNC日常保养表
《3》机床操作方法
一看图,二装夹,三校表,四寻边,五装刀,六发程序、摸似程序,七走程序
一.看图纸。
1,看图纸是否是你现在要加工图纸。
是否是最新版本。
2,看清楚基准在那里。
3,看清楚图纸上写注意事项。
加工时要尤其注意。
4,看程式单上刀外面和仓库是否有。
没有程式改过。
二.装夹校表。
1,必需按图纸上放方法一样装工件。
2,装夹前工作台或夹具必需洁净平整。
以方便校表和工件不被夹伤。
3,装夹前还要注意毛料外行尺寸是否够。
有没变形。
4,装夹时要避免工件变型,或是表面被夹伤。
5,移动主轴时要注意不能碰到工件。
尤其是做架子检具。
6,校表要找到正确方法。
要边校边压。
敲不动就松一下不能用太大
力敲击工件,这么工件有可能会变形。
7.打表时首先要确保相对两边平行,相邻两个边垂直,比如:
从左往右打表指针刚开始从0为一直上升到1MM,把表停止在右边,把右边螺母松开一点右边往后敲打指针三分之二,在把表重新打一下,用相同方法边敲打,边锁紧螺母就OK了
8.校表是确保工件尺寸正确性关键步骤。
所以一定要有耐心校好。
9.压紧过后要对三个基准面进行检验。
三,对刀。
1.优异行X,Y方向对刀。
对刀时要注意以下几点。
(1)要清楚你用多大直径寻边器在碰基准边。
(2)每个边最少要有两次全部在同一点为零。
(3)碰好后一定不能忘了偏寻边器半径,如过用刀具直接碰要偏刀具半径。
(4)存入相正确G54坐标值里。
(5)检验坐标值有没输入。
当输入时工件值,目前值还有刚刚输G54坐标值三个数字是一样。
即是前面三个数字必需一样才说明输进去了。
(6)检验刀具赔偿值是否为零。
即G60那栏。
2.Z方向对刀
(1)要熟练机器手轮操作。
将对刀棒在刀具下面时要尤其小心不能摇错方向。
(2)移动主轴时要注意不能碰到工件。
尤其是做架子检具(3)钻头铰刀能够正确到10丝,铣刀必需正确到1丝。
(3)对了刀后要习惯性把Z清零。
(4)存入G54坐标值。
检验方法和X,Y对刀检验方法一样。
要注意是G60刀补是否正确。
3需要借点一定不能忘了借点。
关键要是Z方向借点时候多。
借点要注意
(1)不要忘了减掉对刀棒尺寸。
(2)借了点要把工件Z零点到所借点间距离输入G60赔偿值中。
(3)借了点后目前刀具和后面刀具全部要在所借点位置进行对刀。
四.寻边
1.选择好寻边器稍微带点力装在刀柄上,在把刀柄装在机床上,机床S转速应在500~600转/分钟
五.安装刀具
1.装刀前要清楚刀具大小,所需长度,加工材料。
2.洗铝用白刚刀。
洗钢和铁要用钨钢刀具。
树脂有专门16刀,如用到其它刀号尽可能用钨钢。
3.装之前要确保刀套和主轴里面洁净。
刀具刃口是否能够切削。
4.刀具长度应按加工工件实体和程式单上长度结合而定。
通常要比程式单上写多装2到5毫米。
精刀尤其要注意不可装过长。
刀具不好必需换掉。
六.发程序走程式
1发程式一定要按加工程式单上程序名字和目前你所装刀具三者一至。
然后再摸似一下
2.程序打开第一要看名字是否一至。
第二要看日期是否是最新程序。
第三看程序中刀具和程式单和你所装夹刀具大小型号是否一至。
第四铣刀程序全部要模拟看刀路有没异常地方。
刀路走路线是否是你目前要加工面。
前面任何一点不对程序全部不能用。
3程序发对了,就该跑程序了。
跑程序不可急。
走之前应先看基准是否正确,三个面对刀有没对好。
然后将GOO和GO1速度打慢将单键实施打开。
准备好了在打到联线按程式开启。
走时候要不段看机器屏幕上显示残余余量和下一指令是多少。
尤其是刀具下降时候。
4确定对刀和程序全部没问题了然后把单键取消GOO和GOI打到合理速度。
该快就要快。
该慢就要慢。
5程序在走时候要观察它是否回扎刀,会不会和压铁和其它位置相撞。
当费料快掉下来时要减慢速度要注意掉下来费料卡刀。
6要合理利用走程序中空下时间为下一步工作做好准备。
《4》对本企业产品,检具,零部件熟知情况由车间主任讲解
《5》切削刀具正确使用方法及切削刀具使用注意事项,怎样磨刀,怎样磨钻头
5.1刀具几何参数
刀具几何参数包含刀具切削角度(前角、后角),刀面形式和切削刃形状(直线形、折线形),下面以双刃直槽刀具为例来介绍刀具几何参数。
5.1.1双刃直槽(2B)刀具(图1):
图1
5.1.2刀具前角:
前角----前刀面(切屑沿其流出表面)和中心线(两对称刃尖连线)夹角。
前角大小决定刀刃锋利程度和强固程度,它对切削过程有着关键影响。
前角越大,刀刃则越锋利,切削越轻快,刀刃强度较弱;反之则恰好相反。
通常切削非金属选择较大前角,切削金属选择较小前角。
5.1.3刀具后角:
后角----后刀面(和已加工表面相正确面)和切削平面间(刃尖外圆切平面)夹角。
后角关键功用是降低切削过程中后刀面和加工表面之间摩擦,后角大小还影响作用在后刀面上力、后刀面和工件接触长和后刀面磨损强度,所以对刀具耐用度和加工表面质量有很大影响。
5.2.刀具加工方法
加工方法因刀具旋转切入工件方向和刀具进给方向不一样而分为顺铣和逆铣。
图:
逆铣加工时,刀齿切削厚度从0到最大,刀齿在工件表面上挤压和摩擦,刀齿较易磨损;顺铣则恰好相反,刀齿切削厚度从最大到0,轻易切下切削层,刀齿磨损较少,资料表明,顺铣可提升刀具耐用度2~3倍。
提议去大料时使用顺铣方法。
顺铣加工时,要求工件侧边没有硬皮(通常铸造、磨削加工后钢件表面会产生加工硬化),不然刀具很易磨损。
5.3怎样降低刀具磨损
a刀具安装应确保刀夹清洁无异物,确保刀具安装精度;
b选择刀具时,尽可能选择刚性好(大直径或柄径)刀具;
c刀具安装时,悬出长度应尽可能短;
d刀具在开始使用时,首先应进行低速磨合,速度通常掌握在正常速度50%;
e粗加工时,应尽可能采取顺铣;
f加工过程中,遇振动加剧,应立即暂停,降低转速、走刀速度;
g使用切削液,充足冷却、润滑,不可中途加注或关闭;
h立即清理切削区域切屑。
5.4刀具磨制过程中常见错误
从磨刀步骤上应注意以下常见错误:
1刀具开半平面和刀杆轴线不平行
刀具开半平面和刀杆轴线不平行会造成刀具测量困难,前大后小或前小后大,测量位置不一样,尺寸就不一样。
开半不正确,从而造成刀具质量不稳定。
2刀具开半速度、磨削锥度速度过快
刀具开半速度、磨削锥度速度过快对刀具材质、硬度不会造成大影响,不过当速度过快时,磨削位置温度升高很快,刀具前后温差较大,尤其轻易形成微观裂纹(即温度裂),刀具使用过程中很很轻易产生崩刃,造成损坏。
3刀具偏心
磨刀机收管不正,会使磨出刀具直径出现偏大或偏小。
偏小时,刀具排屑不好;偏大时,刀具强度减弱,易折断。
4点尖问题
刀具点尖出现问题关键是角度点反。
刃偏角点反会使刀具不排屑,底面不光滑,碎屑粘在槽内;刃偏角点过大,底面残料过多,不平整。
副后角点反有两种情况,过大时会使刀具和工件猛烈摩擦,切削阻力加大,刀具很轻易折断;点反较小时,加工底面金属劈花效果,非金属底面不平,会有熔屑粘在材料上。
副后角过大,刀具锋利,易磨损,寿命低。
以上这些问题全部是在磨刀过程种常常出现,尤其是点尖过程,新手掌握起来有一定难度,为了确保点尖角度、尺寸正确性,能够使用磨刀机磨削方法,从而能够确保刀具精度。
5.5切削刀具使用注意事项
刀具种类
事故原因
清除方法
全部切削刀具
因为刀刃很锋利,所以直接用手触及有碰伤可能。
※尤其是从套壳中取出时或将其安装在机床上时,请使用手套等保护用具。
使用错误方法或使用条件不合适,可造成刀具破损飞出,造成碰伤危险。
※请使用安全罩,保护眼睛。
※请使用推荐切削条件,并请仔细阅读使用说明书及样本资料。
因为冲击负荷,刀具过分磨损,使切削力剧增,造成刀具破损飞溅,而有伤害操作人员危险。
※请使用安全罩,保护眼睛。
※请立即更换磨损刀具。
高温切屑飞溅及过长切屑排出,可造成伤害及烫伤操作人员。
※