工艺过程简述.docx
《工艺过程简述.docx》由会员分享,可在线阅读,更多相关《工艺过程简述.docx(16页珍藏版)》请在冰豆网上搜索。
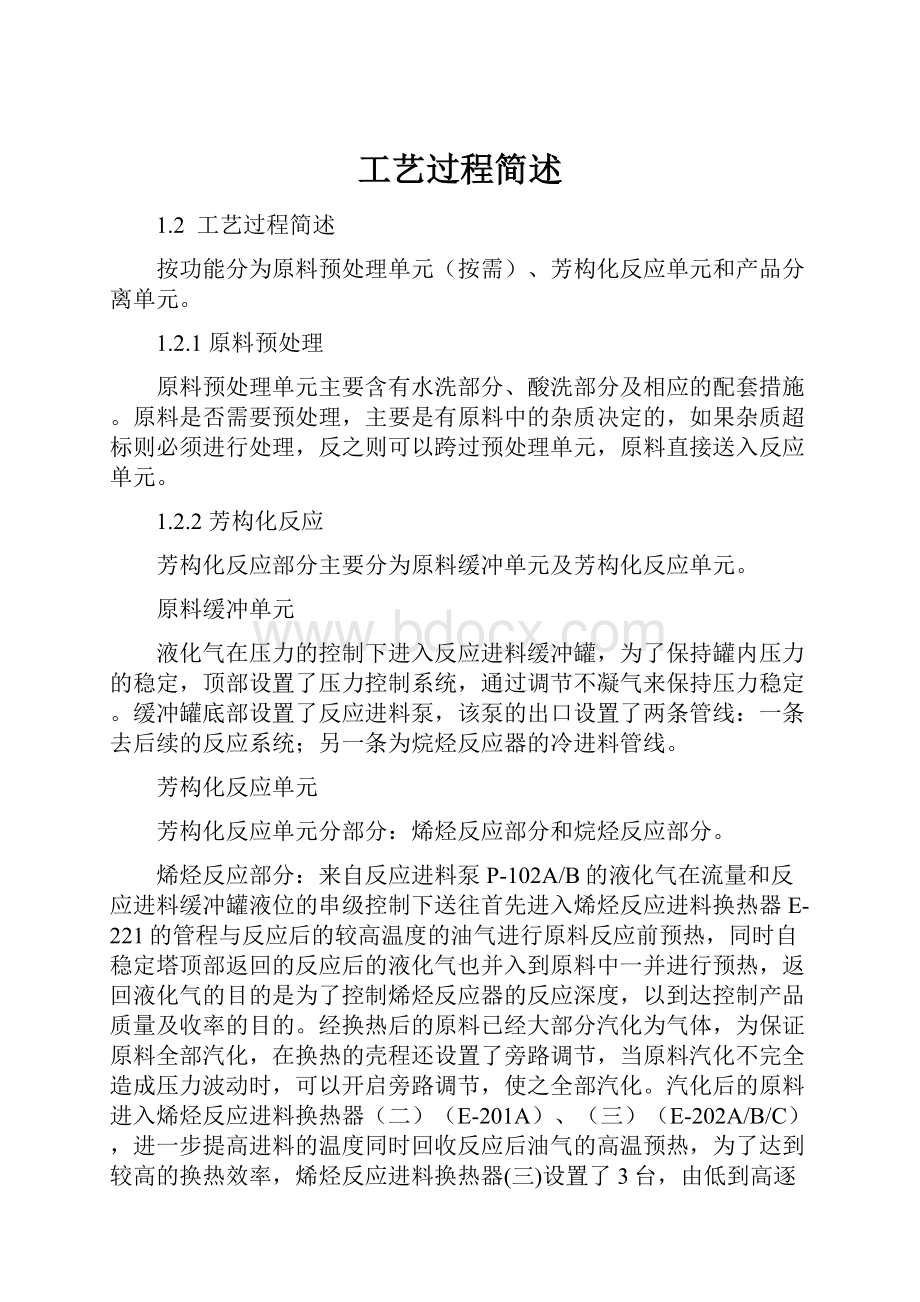
工艺过程简述
1.2工艺过程简述
按功能分为原料预处理单元(按需)、芳构化反应单元和产品分离单元。
1.2.1原料预处理
原料预处理单元主要含有水洗部分、酸洗部分及相应的配套措施。
原料是否需要预处理,主要是有原料中的杂质决定的,如果杂质超标则必须进行处理,反之则可以跨过预处理单元,原料直接送入反应单元。
1.2.2芳构化反应
芳构化反应部分主要分为原料缓冲单元及芳构化反应单元。
原料缓冲单元
液化气在压力的控制下进入反应进料缓冲罐,为了保持罐内压力的稳定,顶部设置了压力控制系统,通过调节不凝气来保持压力稳定。
缓冲罐底部设置了反应进料泵,该泵的出口设置了两条管线:
一条去后续的反应系统;另一条为烷烃反应器的冷进料管线。
芳构化反应单元
芳构化反应单元分部分:
烯烃反应部分和烷烃反应部分。
烯烃反应部分:
来自反应进料泵P-102A/B的液化气在流量和反应进料缓冲罐液位的串级控制下送往首先进入烯烃反应进料换热器E-221的管程与反应后的较高温度的油气进行原料反应前预热,同时自稳定塔顶部返回的反应后的液化气也并入到原料中一并进行预热,返回液化气的目的是为了控制烯烃反应器的反应深度,以到达控制产品质量及收率的目的。
经换热后的原料已经大部分汽化为气体,为保证原料全部汽化,在换热的壳程还设置了旁路调节,当原料汽化不完全造成压力波动时,可以开启旁路调节,使之全部汽化。
汽化后的原料进入烯烃反应进料换热器
(二)(E-201A)、(三)(E-202A/B/C),进一步提高进料的温度同时回收反应后油气的高温预热,为了达到较高的换热效率,烯烃反应进料换热器(三)设置了3台,由低到高逐步进行换热。
经多次有效换热后的原料气温度可以升到250℃左右,再进入烯烃反应加热炉F-201A加热到预定的反应温度。
根据原料烯烃含量的不同,需要的反应温度不同,在原料烯烃含量较高时,由于热效应较大,可能加热炉不需要运行,仅保留长明灯即可。
原料温度与烯烃反应加热炉的燃料气流量设置了串级调节,可以有效保持反应温度的稳定。
原料气经烯烃反应加热炉加热到预定的反应温度后,自烯烃反应器的顶部进入反应器,在这里原料气在催化剂的作用下,发生芳构化反应,生成轻芳烃、丙烷及重芳烃等产品。
为了及时掌握反应情况,调整操作,反应器内部设置了3组温度检测,每一组都有3个测温点,同时在反应器的顶部和底部设置了压差指示,可以随时了解到催化剂的结焦情况。
反应后的油气分成两股,一股和其他反应器的反应油气混合后去脱重塔再沸器E-211同脱重塔底液换热后返回,和另一股反应油气混合进入烯烃反应进料换热器E-202A/B/C、E-201A、烯烃反应进料预热器E-221壳程、反应油气水冷器E-222、E-204冷却到40℃后进入反应液分离罐V-201进行产品的气液分离。
为了保证生产的连续操作,烯烃反应进料换热器、烯烃芳构化反应加热炉、烯烃芳构化反应器采用两条生产线,一条生产线用于连续生产,另外的生产线用于催化剂再生以及再生后备用,以保证反应过程与再生过程可以同时进行,从而保证了产物分离部分的连续操作。
反应器初次开工为保证进料稳定,应先开启一台,一段时间后开启另外一台,间隔的时间以保证反应器的再生时间为原则。
烷烃反应部分:
来自丙烷塔塔底泵P-213A/B的烷烃原料在流量控制器控制下,首先进入烷烃反应进料预热器E-217的壳程与烷烃反应后的反应油气进行换热,为保证汽化完全,在换热的管程还设置了旁路调节,当原料汽化不完全造成压力波动时,可以开启旁路调节,使之全部汽化。
汽化后的原料进入烷烃反应进料换热器E-218A/B,进一步提高进料的温度同时回收反应后油气的高温余热,为了达到较高的换热效率,烷烃反应进料换热器设置了2台,由低到高逐步进行换热。
换热后的原料气温度可以达到200-350℃左右,再进入烷烃反应加热炉加热到预定的反应温度。
加热后的原料温度与烷烃反应加热炉的燃料气流量设置了串级调节,可以有效保持反应温度的稳定。
原料气经烷烃反应加热炉加热到预定的反应温度后,自第一烷烃反应器的顶部进入第一烷烃反应器R-202,在这里原料气在催化剂的作用下,发生芳构化反应,生成轻芳烃、丙烷及重芳烃等产品。
为了及时掌握反应情况,调整操作,反应器内部设置了4组温度检测,每一组都有3个测温点,同时在反应器的顶部和底部设置了压差指示,可以随时了解到催化剂的结焦情况。
第一烷烃反应器底部的物料自第二烷烃反应器顶部进入第二烷烃反应器,为保证轻芳烃产品质量,第二烷烃反应器的进料之前还并入了一股少量的来自反应进料泵P-102A/B的烯烃物料,该物料首先在第二烷烃反应器进料换热器E-223A/B与稳定塔底液进行换热汽化,同时为了便于温度的调节,该换热器还设置了旁路温度调节。
为了及时掌握反应情况,调整操作,第二烷烃反应器内部同样设置了4组温度检测,每一组都有3个测温点,同时在反应器的顶部和底部设置了压差指示,可以随时了解到催化剂的结焦情况。
第二烷烃反应器底部反应后的油气分成两股,一股和其他反应器的反应油气混合后去脱重塔再沸器E-211同脱重塔底液换热后返回,和另一股反应油气混合依次经过烷烃反应进料换热器E-218A/B和烷烃反应原料预热器E-217后,再与烯烃反应产物混合后经烯烃反应预热器E-221进行进一步的换热冷却,最后经反应油气水冷器E-222、E-204冷却到40℃后进入反应液分离罐V-201进行产品的气液分离。
1.2.3产品分离
产品分离部分主要分为气液分离、吸收解吸、稳定及轻芳烃精制等4部分。
气液分离
反应油气经油气水冷器冷却到40℃后,转变为气液两相的物流进入反应液分离罐V-201,在这里反应后的物料进行初步气液分离。
反应液分离罐顶部闪蒸出的气相进入吸收解吸塔的吸收段。
反应液分离罐底部的反应液经泵P-201A/B加压后,在液位的控制下进入吸收解吸塔的解吸段,以解吸其中溶解的轻组分。
吸收解吸
吸收解吸塔的主要目的是将反应气中的氢气、甲烷及C2组分与其他组分分离出来,作为干气送至界区或燃料系统。
该塔塔顶采用压力控制。
反应液分离罐分离出的液体在液位与流量串级控制下,由反应液泵P-201A/B送入吸收解吸塔解吸段的顶部,而反应液分离罐顶部的气相则进入吸收段的底部。
吸收剂为来自稳定塔塔底的C5+馏分。
吸收剂在流量的控制下由塔顶部第1板进入。
因吸收是一个放热过程,因此吸收解吸塔还设有1个或多个中段水冷器,由吸收解吸塔中段循环泵从塔中部抽出部分物料,经冷却后返回塔的下一级塔板。
吸收解吸塔塔底设有再沸器,采用导热油或蒸汽作为热源,加热量由再沸器出口管线温度与导热油或蒸汽流量串级控制。
吸收解吸塔底部物流在塔底液位控制器的控制下稳定塔底物流换热后进入稳定塔中部。
吸收解吸塔顶部干气在压力控制下作为燃料送至燃料气系统。
稳定塔
稳定塔的目的是将C3、C4组分与C5+组分分离开来。
来自吸收解吸塔底部的物料首先在进料换热器E-210中与塔底物料进行换热,然后自稳定塔中部进入塔内。
稳定塔塔顶采用压力分程调节控制,靠回流罐放空和补充塔顶油气实现。
塔底采用导热油或蒸汽作为热源,加热量由塔底再沸器出口管线温度与导热油或蒸汽流量串级控制。
塔顶油汽在稳定塔水冷器中冷凝冷却至40℃后,冷凝液进入稳定塔回流罐。
回流罐中的C3~C4馏分由稳定塔回流泵P-204A/B/C升压后分为三路:
①在塔的灵敏板温度与流量串级控制下作为回流被送入稳定塔。
②在稳定塔回流罐液位及流量的串级控制下送至丙烷进料换热器IE-228的壳程同丙烷塔塔底物料换热后进丙烷塔。
③与烯烃反应进料混合后进烯烃反应进料预热器
(一)(E-222)等预热、换热后送至烯烃反应器,用来进行烯烃反应进料的烯烃含量调节,以保持适宜的反应深度。
稳定塔底部物流C5+馏分(粗轻芳烃)分成2股物流:
一股在流量和液位的控制下靠自压送入脱重塔T-204;另外一股首先进入稳定塔进料换热器E-210管程与稳定塔进料物流进行换热,为保持进料温度的恒定,换热器设置了旁路调节。
换热后的粗芳烃再进入第二烷烃进料换热器E-223A/B中与烷烃进料再次换热,换热后的粗轻芳烃经吸收剂泵P-203A/B加压后再进入吸收剂水冷器E-207A/B冷却到40℃,然后在流量的控制下送入吸收解吸塔顶部作为该塔的吸收剂。
丙烷塔
丙烷塔的目的是将反应后的液化气中的碳三组分分离出来,丙烷可以单独作为产品采出,塔底剩余碳四可以作为产品也可以返回烷烃反应器作为原料,从而提高装置的经济效益,同时可以降低装置能耗。
来自稳定塔顶部含有丙烷的碳四组分经稳定塔回流泵P-204A/B/C加压后,进入丙烷塔进料换热器I(E-228)的管程与丙烷塔底物料换热后、再进丙烷进料换热器II(E-229)和脱重塔顶气相热交换后自丙烷塔中部进入塔内,为稳定丙烷塔进料温度,E-229设有跨线。
丙烷塔塔顶气相经丙烷塔顶水冷器E-226A/B冷却后进入丙烷塔回流罐V-209,罐内液相物料经丙烷塔回流泵P-214A/B加压后一部分在流量的控制下返回塔内作为塔的回流,另一部分在回流罐液位控制器的控制下送出界区。
丙烷塔顶压力采用了热旁路的分程调节系统,当压力低于设定值时,补充塔顶热蒸汽,反之放空阀开启,不凝气排向放空系统。
丙烷塔塔底采用蒸汽作为热源,通过调整蒸汽流量来控制再沸器的出口温度。
塔底的物料经丙烷塔塔底泵P-213A/B加压后分为2路:
①在塔底液位控制器的控制下,依次经过丙烷塔进料换热器E-228及丙烷塔底水冷器E-225,冷却到40℃后作为产品送出界区;②在流量的控制下送往烷烃反应系统;
轻芳烃精制
脱重塔的目的是去除轻芳烃产品中的少量重组分,以保证产品的干点及色泽。
来自稳定塔底部的粗芳烃物料在流量及液位控制器的控制下自脱重塔中部进入塔内。
塔顶压力采用了压差控制的方案,目的是保持本塔的微正压,防止火炬放空气串回塔内,压差靠回流罐放空和补氮实现。
塔底采用来自R-201A/B和R-203的反应油气作为热源,加热量由塔底再沸器出口温度与反应油气流量串级控制。
塔顶油气分别经丙烷进料换热器E-229和轻芳烃水冷器E-230A/B冷凝冷却至40℃,冷凝液进入脱重塔回流罐。
回流罐的轻芳烃由脱重塔回流泵P-206A/B升压后,一部分在流量控制下作为回流被送入脱重塔,另一部分经水冷器II(E-212)冷却至40℃后,在回流罐液位及流量的控制下作为轻芳烃产品送出装置。
该塔底部重组分物流由脱重塔底泵P-205A/B加压后,经重组分冷却器E-213冷却到40℃后,在塔釜液位控制下作为重组分副产品送出装置。
1.2.4催化剂再生及烧焦
反应进行一段时间后,随着反应器中催化剂结焦量的增加,当产品质量或产物分布不能满足要求时,需将反应停止,进行反应器内部烧焦再生处理。
再生时按程序将待再生反应器切换至再生流程。
烧焦开始前,特别注意需加装所需盲板并确认安装位置正确无误,确保与反应系统完全隔离。
启动再生气压缩机,自压缩机入口处引入氮气,增压的氮气经再生气压缩机出口分液罐V-205→烟气换热器E-214A/B/C→进出料换热器→芳构化加热炉→芳构化反应器→进出料换热器→烟气换热器→烟气水冷器E-215→烟气缓冲罐V-204,最后返回到再生气压缩机C-201,进行氮气的循环置换。
分析循环氮气可燃气含量,小于0.5%(v/v)时,系统置换合格,可以进行升温工作。
置换及升温过程中所产生的液相物料通过烟气缓冲罐V-204底部间歇排油至地下污油罐V-207进行回收。
当反应器中的油气达到安全要求,并且反应器入口温度达到烧焦需要的温度时,从压缩机C-201入口处引入空气,开始烧焦作业,要求控制循环气初始氧浓度不高于0.5v%,反应器的温升不高于50℃,如果温度升高过快应立即切断空气注入,必要时加热炉灭火。
根据反应器烧焦状况逐步提高循环再生气中的氧含量和反应器入口温度,当反应器入口温度到450℃,氧含量达到空气中氧的浓度,且反应器中没有温升后,继续缓慢升温至500℃恒温4小时后,停止空气注入,烧焦结束,系统降温。
此时将系统用氮气吹扫置换,系统中的氧含量合格后,泄压至0.01MPag保压备用。
1.2.5支撑设施
支撑设施除了原料球罐之外,还包括地下污油罐、放空罐等,其中地下污油罐、放空罐需要氮封,以减少烃类及苯类芳烃对环境的影响。
公用工程包括工业水、饮用水、消防水、循环水、含油污水和雨水收集管网、工艺废水收集管网、蒸汽管网、蒸汽凝液收集管网、工业风和仪表风管网、氮气管网等。
1.1操作变量分析
本装置的主要操作变量是原料进料的烯烃含量、反应温度、反应压力、空速及各塔的常规操作变量等。
●空速
本手册所指的空速是指重量空速,即单位时间通过催化剂的原料重量与反应器内催化剂重量的比值。
空速是衡量催化剂活性及处理能力的重要指标,操作时应严格按照催化剂专利商所提供的最高空速以下的工况下操作。
空速过大,反应不完全,转化率下降,同时催化剂容易吸附过多的有害杂质,缩短催化剂的运行周期;空速过小,转化率上升,但反应副反应增加,催化剂选择性可能下降,能耗增加,甚至造成催化剂床层结焦过快,影响催化剂的活性及运行周期。
空速越高,催化剂吸附的杂质会越多,对杂质含量多的原料来讲,单程运行周期越短,反之越高。
●反应温度
每一种化学反应都会有一个适合工业生产的合适的反应温度,在此温度下,反应可以达到我们要求的目标,并且能耗最低。
需要说明的是这里所指的反应温度不是反应器的入口温度,而是反应器催化剂床层内部温度,这两个温度通常是不一致的,这取决于进料的烯烃含量。
较高的反应温度可以使反应速度加快,总体上减少杂质的吸附速度,但也加剧了结焦的速度并使副反应增加,造成干气生成量增多;较低的反应温度虽能延长催化剂的运行周期,但在很多情况下,不能达到预想的反应结果,而且有可能由于杂质占据的活性中心不能及时地脱附,使催化剂的活性下降。
反应温度的控制一般要求催化剂床层的最高温度(热点)不能超过所要求的反应温度的最高值。
对DLP系列催化剂而言,选择什么温度与原料及反应器的结构有很大的关系。
●反应压力
低碳烃芳构化过程中,一般伴随着脱氢的反应,脱氢反应对烷烃而言是起始反应,这是一个体积增大的过程,过高的反应压力将抑制脱氢反应的进行,进而降低整个反应过程的转化率。
在一定的压力范围内,压力对芳构化影响不大,但如果压力过高,将会对芳构化反应造成明显的影响并加速催化剂结焦的进程。
在较缓和的轻芳烃生产条件下,由于脱氢反应不是主导反应,齐聚、环化及芳构化是主导反应,因而是一个体积缩小的反应,理论上增加反应压力对反应有利,但压力过高,会造成烯烃缩合程度加剧,使重组分含量增加,也可能会加快催化剂的结焦速度,影响催化剂的单程运行周期。
总体来讲,压力升高不利于芳构化反应,过高的压力还会缩短催化剂的运行周期,对于选用了高压法的客户来讲,要在干气产量合适的情况下,首先降低反应压力,这样可以提高催化剂的运行周期。
●循环量
返回的饱和液化气可以认为是一种惰性组分,它的存在在一定程度上降低了反应物的分压,稀释了烯烃在反应进料的浓度,可以抑制烯烃的聚合结焦。
但返回量不能无限量增大,这样会大幅度增加装置的能耗,同时会降低液体产品收率。
循环量对每一种原料都是不同的,在实际操作中需要不断地进行优化,以达到系统最优。
在轻芳烃(汽油)生产方案中,为了控制温升,同样需要返回部分低烯烃液化气及干气,以降低进料中的烯烃含量,控制适宜的反应温度,返回量的大小同样需要根据原料中的烯烃含量来进行确定。
需要说明的是,如果原料中杂质含量多,运行中须停止干气或饱和液化气返回,否则过多的杂质反而会影响装置的运行周期。
●反应器压差
反应器压差是衡量反应器内部催化剂状态的重要指标之一。
压差过高,增加了物料流经反应器的阻力,造成反应压力上升及物料分布不均匀,影响反应效果催化剂运行周期。
反应压差过高一般有两个原因:
一是催化剂已运行到末期,结焦严重,这种情况下需切换反应器;二是催化剂在装填或运行过程中,出现了粉碎现象,操作中要密切关注运行情况,如果压差上升明显,对装置操作造成了严重影响,则需要停车再生催化剂或更换新的催化剂。
●烯烃
在生产三苯的工艺中,进料中烯烃所产生的热效应较小,对装置的操作影响不大。
在轻芳烃生产方案中,原料中的烯烃含量的高低对装置操作及产品质量影响是很大的,因为高烯烃含量的原料能产生巨大的热效应,使反应器床层出现明显温升,有时可以达到200℃以上。
如果采用这样的原料进行生产,必须在工艺上进行认真的调整,采取各种手段降低床层温度至所要求的温度。
进料中烯烃含量过高,将加快催化剂的结焦过程,缩短催化剂的单程运转周期。
●杂质
原料中的杂质会对催化剂的各项性能及设备产生深远的影响,特别是对催化剂而言,有些杂质是致命的。
随着炼油装置催化裂化装置原料越来越差,液化气中的杂质会越来越多,特别是部分厂家甚至兑入了部分焦化液化气,使原料杂质问题更加严重,客户在选购原料方面更要特别注意。
目前技术方提供的杂质脱出技术有甲醇、硫及砷、碱性氮脱出技术,用户可以根据原料情况进行选择,其它不能脱出的杂质,在原料的采购过程中应严加控制。
典型的杂质包括如下几种:
Ø氮化物:
碱性氮化物会对催化剂产生重大影响,这些影响包括:
运行周期明显缩短、催化剂活性急剧下降、产品芳烃收率下降、汽油的辛烷值明显下降等。
中型或酸性的氮化物对催化剂影响较小,但在较高的温度下,会发生缩合反应生成胶质或沥青质,吸附在催化剂表面,同样会缩短催化剂的运行周期。
Ø甲醇:
甲醇为强极性的物质。
甲醇会优先吸附到催化剂的空穴中,占据活性中心,并可能生产甲烷和水,造成催化剂活性下降,反应副反应增加,干气生成量增加。
甲醇的存在还有可能产生醚化反应,对催化剂造成更大的影响。
Ø二甲醚:
二甲醚是催化剂的毒物,可使催化剂快速的失活。
试验表明,当原料中二甲醚含量超过0.3%时,催化剂的活性就会出现快速的下降,大大缩短催化剂的运行周期。
Ø无机盐:
无机盐的金属离子会占据或置换催化剂的活性中心,造成催化剂永久失活且通过烧焦的方法无法恢复。
Ø硫:
硫的的存在对催化剂没有显著的影响,但过高的硫会影响产品质量,使产品中硫含量超标,并有可能对设备造成腐蚀。
Ø二烯烃:
二烯烃在催化剂及管道低温下就能发生结焦,导致催化剂结焦过快,从而影响催化剂的运行周期。
试验表明,进入反应器的原料中二烯烃含量超过0.3%就会对催化剂的运行周期产生严重影响,这对于MTBE装置加工乙烯裂解的抽余碳四原料来说,是非常不利的,这种原料对芳构化催化剂的运行周期将产生较大影响。
Ø砷及其化合物:
是催化剂的严重毒物,将造成催化剂永久失活。
如果原料中含有砷及其化合物应首先进行脱砷处理。
●其它操作变量
✧吸收解吸塔
该塔分为吸收段及解吸段。
吸收段:
吸收段的主要目的是将反应气中的C3以上的组分吸收下来,氢气、甲烷及碳二组分从塔顶作为干气分离出去,以保证液化气的蒸汽压合格,液化气储罐不超压。
决定吸收段的操作变量主要是吸收比、吸收压力及吸收温度。
吸收比即吸收液的量与进入塔内的气相量之比。
吸收比越大,吸收越完全,也就是说干气中C3以上组分越少,但吸收比不能太大,如果吸收比太大,干气中可能夹带吸收剂的平衡组分,造成干气带液,同时会增加后续装置的负荷,进而增加装置能耗,降低收率。
相反,吸收比过小,吸收不完全,干气中C3以上的组分会增多,造成损失。
操作中要根据干气的质量情况进行优化调整,以达到最佳的吸收效果及较低的能耗。
吸收压力的选择是根据要被吸收的组分所决定的,吸收压力越高吸收越完全,但压力过高会将不需要的轻组分吸收下来,造成解吸塔负荷过高,而且增加设备投资。
吸收温度的高低对吸收效果有着较大的影响。
吸收是一个放热的过程,吸收塔自上而下温度会逐渐升高。
温度越高,被吸收的组分解吸越多,即吸收效果越差,C3以上重组分在干气中就会超标,反之,温度越低,吸收效果越好,干气质量越好。
该塔设计了中段冷却,用以调节吸收温度,以达到较好的吸收效果,减少干气中的C3含量。
解吸段:
解吸塔的主要变量是塔的操作温度。
温度越高解吸越完全,但过高的温度可能造成气体循环量过大,进而造成吸收、解吸塔的超负荷运行;温度过低,C2以下组分可能带入稳定塔,造成稳定塔压力不稳定,而且损失物料。
所以,该塔的操作温度的优化应以稳定塔的操作稳定、物料损失最小为调整方向。
✧稳定塔
该塔的主要操作变量为塔底温度、塔顶压力、回流比及各灵敏塔盘的温度。
塔底温度及灵敏板温度的调整方向是一致的,温度过高,C5组分可能升至塔顶,造成C3/C4产品中碳五含量过高,达不到液化气的要求;反之,温度过低,易造成塔底产品含有轻组分,这些轻组分的存在可能造成脱重塔超压,最终易使汽油的饱和蒸汽压超标,甚至储罐出现超压现象,形成安全隐患。
塔的操作压力是影响精馏塔操作的重要变量,操作压力过高,塔底物料将含有C3/C4轻组分,影响后续系统操作及物料损失,同时还会造成装置能耗增加;操作压力过低,塔底重组分升至塔顶,影响塔顶乙烯原料质量。
操作压力的不稳定,也会造成塔操作不稳定。
回流比也是精馏塔重要操作变量,回流比越大,产品质量越高,塔的能耗越高,但过大的回流比有可能降低塔的操作负荷,能耗急剧上升;回流比越小,塔的操作能耗越小,但回流比过小,将造成塔的上下产品不合格,甚至出现雾沫夹带现象,影响正常操作。
✧脱重塔
该塔的主要操作变量为塔底温度、塔顶压力、回流比及各灵敏塔盘的温度。
塔底温度及灵敏板温度的调整方向是一致的,温度过高,重芳烃组分可能升至塔顶,造成轻芳烃产品中重芳烃含量过高,干点不合格;反之,温度过低,易造成塔底产品含有轻组分,造成轻芳烃收率下降,降低了装置的经济效益。
塔的操作压力是影响精馏塔操作的重要变量,操作压力过高,塔底重芳烃将含有轻组分,降低轻芳烃收率;操作压力过低,塔底重组分升至塔顶,影响塔顶产品质量,使轻芳烃干点超标。
操作压力的不稳定,同样会造成塔操作不稳定,进而产品质量不稳定。
回流比也是精馏塔重要操作变量,回流比越大,产品质量越高,塔的能耗越高,但过大的回流比有可能降低塔的操作负荷,能耗急剧上升;回流比越小,塔的操作能耗越小,但回流比过小,将造成塔的上下产品不合格,甚至出现雾沫夹带现象,影响正常操作。
✧丙烷塔
该塔的主要操作变量为塔底温度、塔顶压力、回流比及各灵敏塔盘的温度。
塔底温度及灵敏板温度的调整方向是一致的,温度过高,过多的碳四组分可能升至塔顶,造成丙烷产品中碳四含量过高,造成丙烷产品不合格;反之,温度过低,易造成塔底产品含有过多丙烷组分,造成烷烃反应器负荷过高,增加装置能耗。
塔的操作压力是影响精馏塔操作的重要变量,操作压力过高,易造成塔底产品含有过多丙烷组分,造成烷烃反应器负荷过高,增加装置能耗;操作压力过低,过多的碳四组分可能升至塔顶,造成丙烷产品中碳四含量过高,造成丙烷产品不合格,同时还会造成塔的处理能力下降。
操作压力的不稳定,同样会造成塔操作不稳定,进而产品质量不稳定。
回流比也是精馏塔重要操作变量,回流比越大,产品质量越高,塔的能耗越高,但过大的回流比有可能降低塔的操作负荷,能耗急剧上升;回流比越小,塔的操作能耗越小,但回流比过小,将造成塔的上下产品不合格,甚至出现雾沫夹带现象,影响正常操作。
2.2催化剂末期操作
2.2.1催化剂再生点的判断
✧催化剂已连续运行了30天以上;
✧烯烃反应器反应温度提高到450℃以上,烷烃反应器温度提至500℃以上,反应效果仍然没有明显改善;
✧反应器温升(或温降)较初期明显变小;
✧转化率下降明显,烯烃反应小于70%,烷烃反应小于30%;
✧装置的轻芳烃产率快速下降;
✧轻芳烃中的芳烃含量明显减少,由正常的20-45%下降到10%以下;
✧气相中的氢气、乙烷、丙烷含量明显下降,丙烯含量增加到5%以上,丙烷含量降至5%以下;
✧反应器的上下压差较开工初期明显偏高。
2.2.2催化剂末期操作注意事项
✓反应温度应逐步提高,随着温度的提高,结焦速度加快,催化剂活性下降速度加快;
✓要密切注意