年产7万吨锌锭的湿法炼锌浸出车间的设计.docx
《年产7万吨锌锭的湿法炼锌浸出车间的设计.docx》由会员分享,可在线阅读,更多相关《年产7万吨锌锭的湿法炼锌浸出车间的设计.docx(42页珍藏版)》请在冰豆网上搜索。
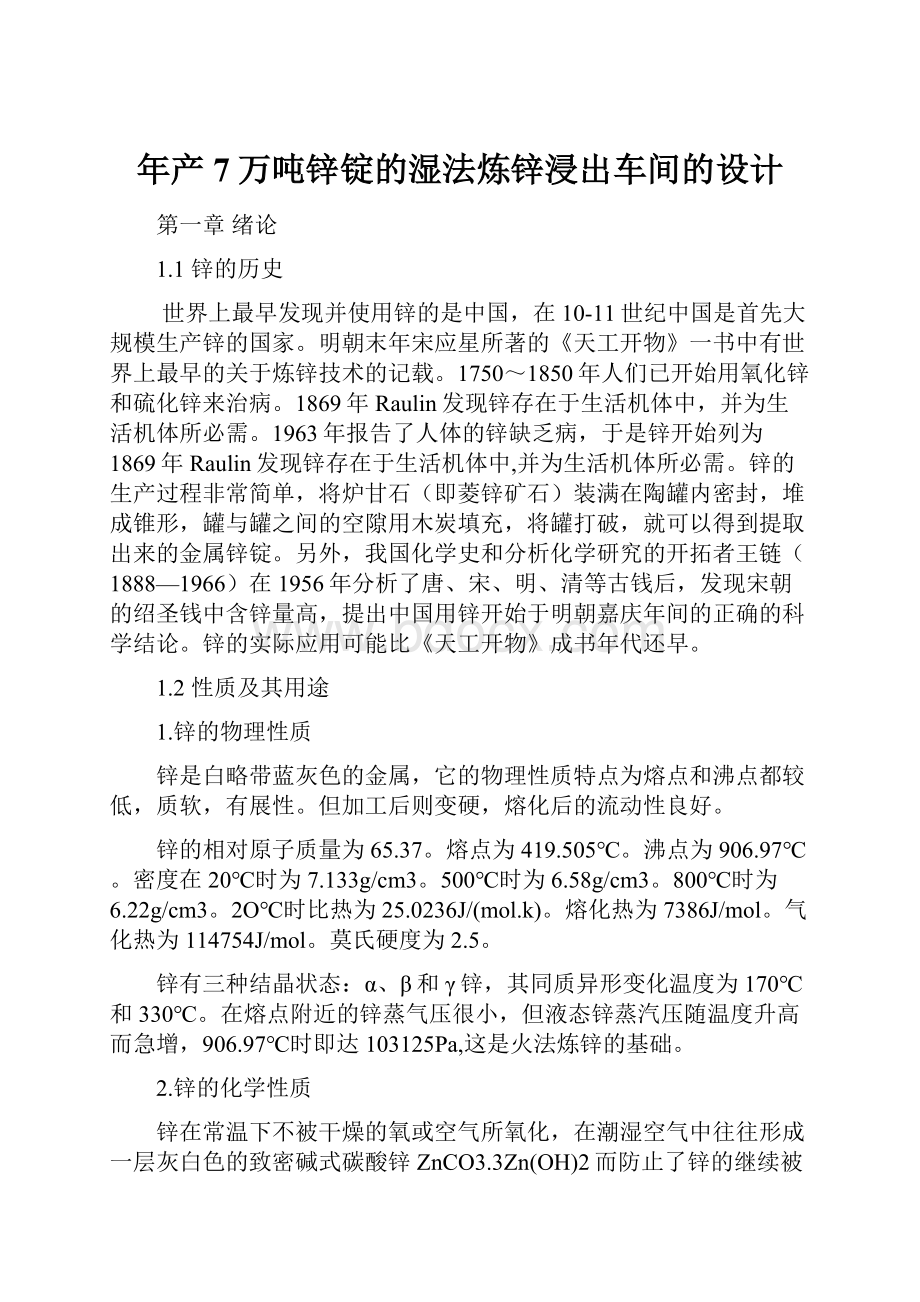
年产7万吨锌锭的湿法炼锌浸出车间的设计
第一章绪论
1.1锌的历史
世界上最早发现并使用锌的是中国,在10-11世纪中国是首先大规模生产锌的国家。
明朝末年宋应星所著的《天工开物》一书中有世界上最早的关于炼锌技术的记载。
1750~1850年人们已开始用氧化锌和硫化锌来治病。
1869年Raulin发现锌存在于生活机体中,并为生活机体所必需。
1963年报告了人体的锌缺乏病,于是锌开始列为1869年Raulin发现锌存在于生活机体中,并为生活机体所必需。
锌的生产过程非常简单,将炉甘石(即菱锌矿石)装满在陶罐内密封,堆成锥形,罐与罐之间的空隙用木炭填充,将罐打破,就可以得到提取出来的金属锌锭。
另外,我国化学史和分析化学研究的开拓者王链(1888—1966)在1956年分析了唐、宋、明、清等古钱后,发现宋朝的绍圣钱中含锌量高,提出中国用锌开始于明朝嘉庆年间的正确的科学结论。
锌的实际应用可能比《天工开物》成书年代还早。
1.2性质及其用途
1.锌的物理性质
锌是白略带蓝灰色的金属,它的物理性质特点为熔点和沸点都较低,质软,有展性。
但加工后则变硬,熔化后的流动性良好。
锌的相对原子质量为65.37。
熔点为419.505℃。
沸点为906.97℃。
密度在20℃时为7.133g/cm3。
500℃时为6.58g/cm3。
800℃时为6.22g/cm3。
2O℃时比热为25.0236J/(mol.k)。
熔化热为7386J/mol。
气化热为114754J/mol。
莫氏硬度为2.5。
锌有三种结晶状态:
α、β和γ锌,其同质异形变化温度为170℃和330℃。
在熔点附近的锌蒸气压很小,但液态锌蒸汽压随温度升高而急增,906.97℃时即达103125Pa,这是火法炼锌的基础。
2.锌的化学性质
锌在常温下不被干燥的氧或空气所氧化,在潮湿空气中往往形成一层灰白色的致密碱式碳酸锌ZnCO3.3Zn(OH)2而防止了锌的继续被侵蚀。
熔融的锌能与铁形成化合物并保护了钢铁,此一特点被用在镀锌上。
常温下无空气的水对锌没有作用,但在红热温度时,锌易分解水蒸气,生成氧化锌。
在空气中加热金属锌至505摄氏度即可燃烧生成非晶形氧化锌。
商品锌易为硫酸或盐酸所溶解并放出氢气,也可溶于碱中,但溶解速度不及在酸中快。
锌可与水银生成汞齐。
二氧化碳与水蒸气混合的气体可使锌迅速氧化成氧化锌,这是火法炼锌的极其重要反应。
锌的电化极电位较负,这一特点被应用于从含金溶液中加锌粉提金和湿法炼锌中加锌置换净液上。
3.锌的用途
锌的消耗量与铜、铅的差不多。
主要消耗在镀锌方面,作为覆盖层以保护钢材和钢铁制品。
锌能与许多金属形成金属形成性质优良的合金。
如铜锌形成的黄铜,铜锡形成的青铜,铜锡铅形成的抗磨合金等,在机械工业、国防工业和交通运输业中得到广泛的应用。
高纯锌制造的Ag-Zn电池,体积小而能量大,多用于飞机和航天仪表上。
由于锌的熔点低和流动性良好,适于压铸制造各种精密铸件。
锌的抗腐性良好,可用于制造火药箱、家具和无线电装置零件。
在化学工业中,锌可供制造颜料。
氧化锌还用于橡胶制造业。
在冶金工业中,锌可用来从含金溶液中置换金;在湿法炼锌中,用锌粉净液除铜、镉等。
1.3锌冶炼技术发展状况
由于锌的快速发展,现代锌冶金工艺分为两大类,火法炼锌和湿法炼锌。
火法炼锌的方法有平罐炼锌、竖罐炼锌、ISP炼锌、电炉法、密闭鼓风炉等。
目前世界主要炼锌的方法是湿法,世界上85%以上的锌由湿法炼锌生产出来的,现代湿法炼锌工艺主要由焙烧、浸出、净化、电积、熔铸等五个工序构成。
湿法炼锌将锌焙砂或其他氧化锌物料和硫化锌精矿中的锌溶解在水溶液中,从中提取金属锌或锌化合的过程,为现代炼锌的主要方法。
由锌浸出、硫酸锌溶液净化、锌电解沉积三大环节组成。
工艺流程湿法炼锌流程大体可分为传统的湿法炼锌流程、热酸浸出炼锌流程和硫化锌精矿直接浸出炼锌流程等三类。
上世纪90年代以来,我国湿法炼锌技术水平有了比较明显的提高。
白银公司建设的109平米焙烧炉、黄钾铁矾法处理、锑盐除钴等技术日趋成熟,国内很多企业都纷纷效仿,目前这种冶炼工艺已经在全国推广。
株洲冶炼集团的湿法工艺经过几十年的完善,在国内湿法冶炼技术上也独树一帜。
需要特别提到的是云南氧化锌矿资源非常丰富,目前黄木冶炼厂和祥云飞龙公司在处理低品位氧化矿方面取得突破,并形成新的生产能力,祥云飞龙实业公司已经申请多项技术专利,并正在扩建产能。
锌电积车间一括电解沉积、电解液冷却、极板制造和电解槽清理等设施。
从20世纪初采用湿法炼锌以来,电积在工艺上无多大变化,只在电解槽材质、电解液冷却方式、冷却设备、熔铸设备和操作制度上有不同程度的改进,并向大型化、机械化和自动化方向发展。
世界上锌的全部消费中大约有一半用于镀锌,约10%用于黄铜和青铜,不到10%用于锌基合金,约7.5%用于化学制品。
通过在熔融金属槽中热浸镀需要保护的材料和制品,锌可用于防蚀。
对金属制品,可分批镀锌;对轧制钢带卷,可连续镀锌。
近年来,钢带热浸镀锌量有显著增长。
电镀锌也有使用,但该法一般用于较薄的镀层和不同的表面光洁度。
使用含锌粉的涂料是涂层的另一种方法;对于与水连续接触的物体,如用于船舶、桥梁和近海油气井架的大的钢构件,只须和大的锌块连接,便可得到保护,不过锌块要定期更换。
压铸是锌的另一个重要应用领域,它用于汽车、建筑、部分电气设备、家用电器、玩具等的零部件生产。
锌也常和铝制成合金,以获得强度高、延展性好的铸件。
在制成薄板时(一般是用连铸连轧法生产薄板),锌还常和少量铜和钛制成合金,以获得必需的抗蠕变性能。
国际铅锌研究组预测,2004年全球锌消费量会比2003年的985万t增长4.8%,2005年将再增长4.3%,预计2005年中国将占世界锌消费总量的四分之一,它的消费增长的部分原因是镀锌钢用量的增长。
相比之下,美国可能只占全球锌需求的十分之一。
根据金融危机前CRU等机构做的预测,到2020年,世界锌需求将增加。
铜铝铅CNMN.COM.CN锌锡镍,中国有色网,小金属,废旧金属。
日本金属经济研究协会预测,到2014年,世界锌的需求将达到1300万吨,之后需求将停滞。
铜铝铅CNMN.COM.CN锌锡镍,中国有色网,小金属,废旧金属。
这个预测是根据‘中国在2014年锌需求将达到顶峰,而亚洲其他的发展中国家和新兴工业国的锌需求也将增加’的预测做出的。
铜铝铅CNMN.COM.CN锌锡镍,中国有色网,小金属,废旧金属。
总之,所有预测都认为2014年后亚洲锌的需求不会出现大幅度的下降或增加。
铜铝铅CNMN.COM.CN锌锡镍,中国有色网,小金属,废旧金属。
但是许多分析家认为,2009年~2010年世界锌矿山产量和金属产量将减产10%~15%,锌矿山关闭的数量也将增加,2011年锌价格将超过2000美元/吨。
铜铝铅CNMN.COM.CN锌锡镍,中国有色网,小金属,废旧金属。
因此可以认为,到2016年世界锌矿山产量和金属产量将恢复到2007年的水平。
铜铝铅CNMN.COM.CN锌锡镍,中国有色网,小金属,废旧金属。
但是,由于印度和中国基础设施投资和汽车产量将持续增加,因此预计到2020年前,亚洲的锌矿石产量和锌金属产量将会保持持续增长势头。
铜铝铅CNMN.COM.CN锌锡镍,中国有色网,小金属,废旧金属。
尽管今后几年中国锌业的发展趋势将与世界锌业的发展趋势大致相同,但中国锌业的发展将决定着世界锌业的未来。
铜铝铅CNMN.COM.CN锌锡镍,中国有色网,小金属,废旧金属。
尽管根据预测的需求,亚洲有必要新建一个锌金属冶炼厂,但对冶炼厂的投产时间和生产能力需要进行认真的研究。
铜铝铅CNMN.COM.CN锌锡镍,中国有色网,小金属,废旧金属。
如果亚洲新兴工业国中现有冶炼厂增加产量,加上一、两个10万吨~20万吨级的新冶炼厂投产,那么基本可以满足亚洲2020年前不断增长的锌需求。
铜铝铅CNMN.COM.CN锌锡镍,中国有色网,小金属,废旧金属。
但是,受世界金融危机影响,无法看清未来亚洲经济恢复和发展的前景,因此很难对需求的增长做出准确的预测。
铜铝铅CNMN.COM.CN锌锡镍,中国有色网,小金属,废旧金属。
对于亚洲的矿山生产来说,现有冶炼厂的生产能力已经完全能够满足新投产矿山矿石的加工需求。
铜铝铅CNMN.COM.CN锌锡镍,中国有色网,小金属,废旧金属。
1.4研究的意义及其主要内容
1.研究的意义
本课题研究使得学生充分了解锌电解车间的工艺流程和生产方法,学习锌电解车间的设计。
2.主要内容
1)工艺流程的选择及主要技术经济指标、条件、厂址的选择与论证;
2)经济核算及“三废”治理的论证;
3)冶金计算及主要设备选型的计算。
第二章工艺流程的选择和论证
2.1电解精炼的基本工艺流程图
2.2电解精炼的基本原理
1.原料:
经净化得到的硫酸锌溶液,其中Zn的含量为120~130克每升,虽经净化处理,但其中仍含有铜、钴、镍、砷、锗、钴、铅等杂质。
其含量大都在危害程度以上,进一步进行电解精炼,以脱除杂质和将Zn的含量提高到99.95%以上。
2.电解精炼的目的
1)把有害杂质进一步除去,得到既宜加工,又具有良好使用性能的电锌。
2)同时回收铅、硫酸等。
3.电解精炼的原理
锌电解精炼是利用锌和杂质的电位不同,采用的电解液为硫酸锌和硫酸的混合溶液。
以铝板为阴极,以铅银合金为阳极。
通过不断供给直流电,则溶液中的Zn离子不断在阴极上被还原,得到金属锌。
而阳极放出氧气。
1)电极过程的电极反应:
阳极:
Zn2++2e=Zn
阴极:
H2O-2e=1/2O2+2H+
总反应:
ZnSO4+H2O=Zn+H2SO4+1/2O2
2)H+的影响
由于电解液是硫酸锌和硫酸的混合液,从而氢离子多,造成氢离子的实际电位比锌的电位高,从而氢在阴极析出,导致阴极层的氢离子浓度减少,严重时发生锌的水解,形成Zn(OH)2被包在析出锌中,形成色暗疏松的析出锌。
此外由于杂质存在使析出锌呈现球苞状、条纹状和孔洞状。
为了避免这些影响,主要方法有:
(1)电解液的温度不宜过高
(2)电流密度不宜过低
(3)电解液中应有足够的硫酸锌和硫酸
(4)阴极表面要光滑、平整、致密
(5)采用超高电位材料
2.3电解对各种杂质的行为
根据杂质对电流效率影响程度的大小可分为以下几类:
(1)铜、钴、镍电解液中存在铜时,析出的锌呈疏松黑色状。
严重时出现孔洞。
这是因为铜较锌电位正,易于锌一起析出,形成Cu-Zn原电池而腐蚀锌,降低电流效率。
另外铜在阴极析出后,在该点氢的超电位下降而析出氢,
也降低电流效率。
铜的来源是净液跑滤和铜导头或其他铜物料溶解所致。
钴腐蚀锌的原因与铜相似,在工业上称为烧板,它使紧贴阴极一面的析出锌产生小黑点和孔眼。
当电解液含酸高和有铋存在时,钴的危害更剧。
但胶的存在可以减轻其危害性。
镍和钴的行为相似。
唯独对电流效率影响更大。
一般电解液中含铜、钴、镍的量分别要小于0.5、3~5、1mg/L。
(2)砷、锗、硒、碲是对电积危害更大的杂质。
电解液中砷、锗的含量要求低于0.1mg/L,硒、碲要低于0.02~0.03mg/L。
其来源是锌精矿和氧化锌烟尘。
电解液中砷、锗的存在,使析出锌呈球苞状、条纹状和疏松状态。
因为它们析出后构成短路原电池,使锌腐蚀,并产生挥发性的As3H和Sb3H,使锌成条纹或求苞状。
与铜、钴、镍一样,当电解液温度和酸度增高时,更剧烈地降低电流效率。
(3)铁、镉、铅对电流效率影响不大。
电解液中铁在阳极能氧化为三价,又在阴极还原为二价,消耗电能。
电解液中的含量可达2~5mg/L。
镉和铅不使锌发生溶解腐蚀,故不影响电流效率。
但它们的电位比锌正,因而会在阴极析出,影响电锌质量。
电解液中可容纳镉量高达5mg/L。
2.4电解液
1.电解液的选择
作为锌电解精炼的电解液,应符合以下条件:
导电性好;稳定、不易挥发;对设备腐蚀性小;对某些杂质溶解度小;无毒。
基于以上条件,锌电解作业中一般采用有游离酸的硫酸锌水溶液,这种电解液较稳定,不易挥发;既可以在高温下使用,导电性较好,一般的耐火材料既可抵抗其腐蚀。
2.电解液的组成
主要成分是硫酸、硫酸锌和水,其次是阳极与可溶杂质的硫酸盐和~作为电解工艺需要加入的添加剂。
其中含酸量根据电流密度而定。
在300~400A/m2电流密度下,电解液含酸约在100~110g/L。
为了强化生产,当电流密度提高到500~600A/m2时,含酸量要达到140~160g/LH2SO4。
只有这样才能保证获得高的电流效率和低得电流效率。
1)上清液及净化后液的质量要求
元素
Zn
Cu
Cd
As
Ge
Ni
Co
Mn
上清液
120~130
0.4~0.38
0.68~0.08
0.00036~0.00018
0.0005~0.0002
0.007~0.002
0.01~0.005
净化液
120~130
<0.0005
<0.005
<0.0005
<0.00005
<0.002
<0.01
2)下表为添加剂的作用
添加剂
作用
动物胶
它能诱发结晶,改善阴极物理状态
硫脲
一般与动物胶混合使用,供阴极表面致密、光滑、平整,从而调整其硬度
干酪素
一般混合使用,能抑制阳极表面粒
子的长大和改变粒子的形态
盐酸
维持电解液中氯离子的含量,电解液中氯离子可以使Pb、Ag生成沉淀,同时还防止阳极钝化,防止阴极树枝状结晶,但过多时,阴极会产生针状结晶
3.电流效率
以实际析出锌量比理论析出锌量的百分数称为电流效率。
电积过程中,析出锌量总是小于依法拉第定律算出的锌量。
因阴极上除锌析出外,还有附属电化反应,如2H++2e=H2以及二次反应如Zn+1/2O2=ZnO,ZnO+H2SO=ZnSO4+H2O等发生。
2.5电解液温度
电解液温度高低影响到氢的超电压大小。
温度高则氢的超电压下降,因而也降低了电流效率,特别是酸度高和杂质多的情况下更甚。
为此要求电积过程在较低的温度(30~40。
C)下进行。
电积过程是放热过程,其产热量为Q=I2Rt(J),因此工业上必须对电解液进行冷却。
如在电解槽内设铅制冷凝管,在中性硫酸锌溶液地下槽或高位槽内设冷凝箱。
真空蒸发冷却或强制鼓风蒸发冷却效果较好,还可蒸发一部分液体以利于湿法过程的溶液体积平衡。
经冷却后的废电解液返回到电解槽内循环。
2.6析出锌的状态和周期
析出锌表面粗糙意味着其表面积增大和电流密度减小,这就降低了氢的超电压,使电流效率下降。
电积时间愈长,阴极表面状态愈不好,由粗糙不平到长疙瘩。
甚至阴极相互接触,造成短路,电流效率下降。
但析出周期过短又增加装槽和剥锌的工作量。
因此,工业上的析出周期一般为24h。
当前,湿法炼锌厂的电流效率为88%~93%。
2.7槽电压
槽电压也是电积过程的重要技术指标,生产上力求降低槽电压。
槽电压由硫酸锌的分解电压、阴阳极间电解液的电压降以及克服阴阳极、导电杆、导电板、接触点等的电压降所组成。
其中,槽电压主要消耗在克服分解电压上,而降低槽电压的途径则应从降低电解液电压降、导体和连接头电压降及阳极泥电压降入手。
阴阳极间电解液电压降由下式求出:
V=IR=DkpL
即电流密度Dk、电解液比电阻p、极间距离愈大,则电解液电压降V也愈大,槽电压也愈高。
降低电解液比电阻可提高温度和酸度的方法,但此时的电流效率会降低,必须综合考虑。
现代电锌厂采用的同极间距离为50~100mm,我国常用58~60mm。
阳极板上形成阳极泥也会使电阻增大。
为此生产上采用定期清洗阳极泥的措施。
应该指出,刷阳极泥后的短时间内,析出锌含铅会略有升高。
2.8添加剂的作用和析出锌的质量
析出锌的质量包括化学质量和物理质量两个方面。
化学质量是指锌中杂质含量多少及锌的等级而言。
湿法电积提取锌一般产出二号锌,也可产出一号锌,其中铁、铜、镉都达到要求,唯有铅的要求不易达到。
所以铅含量是电锌化学质量的关键。
铅来源于阳极,而析出锌中含铅则是由于化学电积和机械夹杂所致。
化学电积就是电解液中的Pb2+在阴极放电析出。
Pb2+增多是由于阳极腐蚀溶解所致。
促使阳极溶解是由于电解液含氯和液温过高。
因为PbSO4在电解液中的溶解度随温度升高而增大。
此外,酸过高对铅阳极的腐蚀也过大。
机械夹杂即阳极泥悬浮被夹杂析出,它与电流密度及电解液搅拌程度有关,更与阳极氧化膜的坚固性有关。
减少电锌的含铅量还可以采用添加碳酸锶的方法。
此添加剂在电解液中形成硫酸锶,它与硫酸铅的结晶晶格几乎一样,因而形成极不易溶的混晶沉于槽底。
碳酸锶的用量为0.4g/L,电锌含铅可降至0.0038%~0.0045%。
因混晶颗粒很细,不易很快沉淀,而有悬浮。
碳酸锶较贵,有用与其性质相似的碳酸钡代替,唯效果较差且用量较多。
物理性质不好的电锌表现为疏松色暗有孔的海绵状锌。
这种锌表面积大,容易返溶和造成短路。
致使电流效率显著下降,电能消耗显著提高。
这种锌还会增加熔化时锌的氧化造成的锌损失。
形成这种锌是由于电解液含杂质多和氢析出多所致。
杂质在阴极析出时,该处得氢超电位下降,遂使析出的锌不紧密,同时会有更多的氢析出,导致阴极层的氢离子浓度减少,严重时发生锌的水解,形成Zn(OH)2被包在析出锌中,成为色暗疏松的析出锌。
此外,由前面所述的由于杂质存在使析出锌呈现球苞状、条纹状、孔洞状,都是其物理质量不好的现象。
锌电积时还添加吐酒石,其目的是使剥锌容易。
剥锌困难是由于阴极铝板上的氧化铝薄膜受破坏和阴极有凹陷。
氟的存在和杂质量多(特别是钴多)是氧化铝薄膜受破坏的主因,甚至发生烧板。
如前所述,阳极反应形成大量氧气逸出会造成酸雾。
加入皂根可改善此情况。
因皂根溶解后在电解液表面形成一层较为坚固的泡沫层,对废液微粒起着过滤的作用。
第三章锌电积工艺过程及设备计算
3.1概述
工业上从硫酸锌水溶液中电解沉积锌有三种工艺:
即低酸低电流密度法(标准法);中酸中电流密度法(中间法)和高酸高电流密度法。
目前我国多采用中酸中电流密度法的下限,低酸低电流密度法上限的电解法。
表3-1为三种方法的比较。
表3-1锌电积三种工艺的比较
工艺方法
电解液含
H2SO4(克/升)
电流密度
(安/米2)
优缺点
酸低电流密度法(标准法)
110--130
300--500
耗电少,生产能力小,基建投资大
中酸中电流密度法(中间法)
130--160
500--300
生产操作比前者简单,生产能力比前者大但比后者小基建投资小
高酸高电流密度法
220--300
800~1000甚至大于1000
生产能力大;耗电多;电解槽结构复杂。
3.2设计任务
设计生产能力为7万吨锌锭的电解设备
3.3原始资料
3.3.1设进入电解槽的电解液成份如表3-2所示:
表3-2进入电解槽的电解液成份(克/升)
组成
Zn
Fe
Cd
Cu
CO
Mn
(克/升)
120
0.045
0.005
0.0004
0.005
4.720
3.3.2电解后电解废液成份如表3-3所示
表3-3电解废液成份(克/升)
组成
Zn
Fe
Cd
Cu
CO
Mn
(克/升)
46
0.028
0.003
0.0002
0.005
3.217
3.3.3一些技术条件及技术经济指标
用于制造锌粉之锌锭占年产锌锭量的百分比,β=0.028;年工作日为330日。
阴极锌熔铸直收率η1=97%
阴极电流密度D阴=520安培
槽电压V槽=3.20伏
电流效率ηi=98%
阴极规格长×宽×厚=1000×666×4(毫米)
3.4工艺过程及设备计算
3.4.1物料平衡及电解槽计算
阴极锌成份的计算
在电积过程中,一部分铜、铁、镉与锌一齐在阴极上沉积,一升电解液得到的阴极锌含金属量如表3-4所示。
表3-4一升电解液沉积的金属量(克)
组成
Zn
Fe
Cd
Cu
共计
(克)
64.00
0.005
0.002
0.0002
64.0072
铅-银阳极在电解过程中被腐蚀,使一部分铅进入到阴极锌中。
设阴极锌含铅0.006%则进入到阴极锌中铅的量为:
克
那么阴极锌的成份如表3-5所示。
表3-5阴极锌成份
组成
Zn
Pb
Fe
Cd
Cu
共计
重量(克)
64.00
0.0038
0.0050
0.0020
0.00020
64.0110
%
99.983
0.006
0.0078
0.003
0.0003
100
3.4.2所需电解槽数量的计算
(1)每日应产出的阴极锌量的计算。
Q1=
吨
式中:
Q1----每日应产出阴极锌的数量,吨;
Q----设计生产能力,吨锌锭/年;
β----用于制造锌粉之锌锭占年产锌锭量的百分比,%;
m----年工作日,日;
η----阴极锌熔铸直收率,%。
Q1=
吨/日
(2)阴极有效总面积及片数的计算
阴极有效总面积的计算。
×106米2
式中:
F-----阴极有效总面积,米2
Q-----每日产出的阴极锌量,吨;
D-----阴极电流密度,安培/米2;
η-----电流效率,%;
1.2195----锌的电化当量,克/安培;
24-----电解析出时间,小时。
F=
×106=15086米2
阴极边上装有塑料绝缘条,没边各占区阴极板宽7毫米,阴极浸没于电解液的深度为0.87米,则每片阴极的有效面积(按两面计)为:
f阴=0.87×(0.666-0.007×2)×2=1.13米2
故共需阴极片数n=
=
片
设一个电解槽装阴极片32块,则共需电解槽数为:
个
每个电解槽的阴极总面积为:
1.13×32=36.16米2
取备用电解槽24个,则一共有电解槽560个。
这就可把电解槽分为两个系列。
每个系列有280个电解槽,在每个系列中可按35个电解槽组成一组,共八组为一系列。
3.4.3电解槽内部尺寸大小的计算
电解槽内部宽度的计算。
设阴极边缘到槽壁距离为95毫米,则电解槽内宽为:
B=666+2×95=856≈860毫米
电解槽内部长度计算。
设每片阴极厚度为5毫米,每片阳极厚度为10毫米,阴阳极间距离为34毫米,电极到两端壁距离为125毫米,每个电解槽有阴极片32片,阳极片33片。
则电解槽内部长度为:
L=32×5+33×10+32×2×34+125×2=2916毫米
电解槽内部高度的计算。
设槽内液面至槽面的距离为100毫米;槽内阴极浸入电解液的深度为880毫米;阴极下部端缘距槽低500毫米。
则电解槽的内高位:
H=100+880+500=1480毫米
故电解槽的内部尺寸为:
长×宽×高=2916×860×1480(毫米)
电解槽容积(不设槽内冷却器)为:
V槽=L×B×H=2.916×0.86×1.48=3.711米2
电解槽体的材料有木质