涂层检验与涂层系统修补程序中文版.docx
《涂层检验与涂层系统修补程序中文版.docx》由会员分享,可在线阅读,更多相关《涂层检验与涂层系统修补程序中文版.docx(27页珍藏版)》请在冰豆网上搜索。
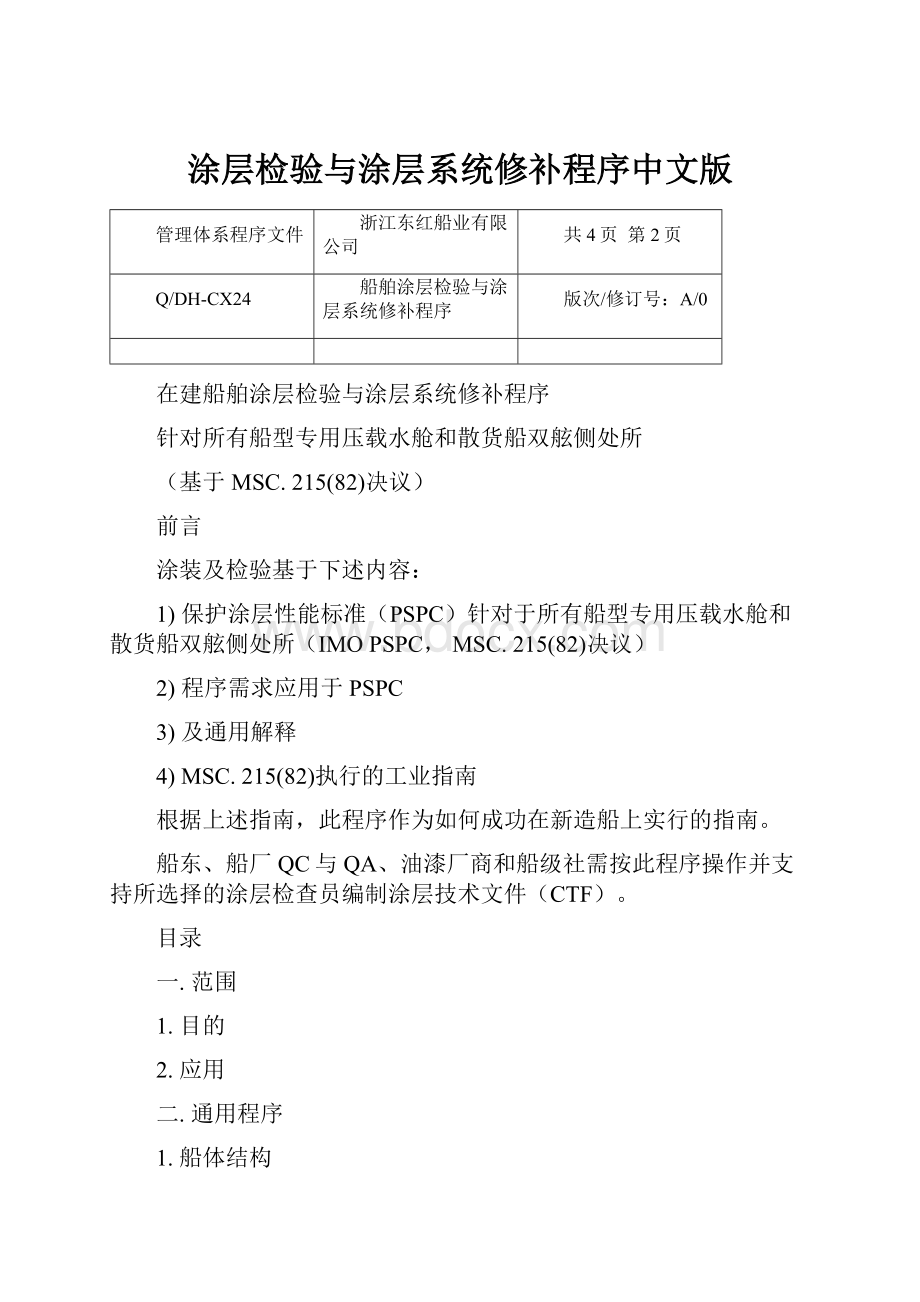
涂层检验与涂层系统修补程序中文版
管理体系程序文件
浙江东红船业有限公司
共4页第2页
Q/DH-CX24
船舶涂层检验与涂层系统修补程序
版次/修订号:
A/0
在建船舶涂层检验与涂层系统修补程序
针对所有船型专用压载水舱和散货船双舷侧处所
(基于MSC.215(82)决议)
前言
涂装及检验基于下述内容:
1)保护涂层性能标准(PSPC)针对于所有船型专用压载水舱和散货船双舷侧处所(IMOPSPC,MSC.215(82)决议)
2)程序需求应用于PSPC
3)及通用解释
4)MSC.215(82)执行的工业指南
根据上述指南,此程序作为如何成功在新造船上实行的指南。
船东、船厂QC与QA、油漆厂商和船级社需按此程序操作并支持所选择的涂层检查员编制涂层技术文件(CTF)。
目录
一.范围
1.目的
2.应用
二.通用程序
1.船体结构
2.独立项目(舾装件)
三.涂装工作质量标准
1.表面处理标准
2.预处理及车间底漆喷涂
3.二次及局部表面处理
4.涂装施工
5.涂装缺陷处理
四.检验
1.检验程序
2.干膜厚检验标准
3.涂层日志
一.范围
1.目的
基于保护涂层性能标准(PSPC)针对于所有船型专用压载水舱和散货船双舷侧处所(IMOPSPC,MSC.215(82)决议),为了确保船舶钢结构涂装质量,钢材及表面处理,涂装和检验作为船厂涂装质量要求而提出。
2.应用
1)此程序覆盖所有船型专用压载水舱和散货船双舷侧处所钢结构保护涂层需求。
舱室内其它独立项目(舾装件)需提供保护涂层以防止腐蚀。
2)所有涂装工作需根据此程序操作。
3)如果此程序发生任何修改或变化,须将修改或变化提交给相关方协商同意。
二.通用程序
1.船体结构
1.1钢板及板材存储
1.2预处理及车间底漆喷涂
1.3钢板切割
1.4小组立
1.5单元组立(分段组立)
1.6预舾装
1.7二次表面处理
1.8分段涂装
1.9预搭载
1.10二次表面处理及涂装(总段接缝与烧损/破坏处表面处理及涂装)
1.11搭载
1.12二次表面处理及涂装(搭载焊缝与烧损/破坏处表面处理及涂装)
2.独立项目(舾装件包括管子)
2.1通用工作过程
1)制作
2)表面处理:
a.外来物质需清除。
b.动力工具使用于指定的舾装件需涂装;
3)检验:
检验需在油漆厂商及船厂检查员指导下由QC完成;
4)涂装:
a.底漆涂装;对于所有的舾装件需施工一度船厂配套环氧底漆,除非指定涂装特定的涂层系统。
b.面漆涂装:
面漆按指定要求施工。
5)检验:
检验需在油漆厂商及船厂检查员监督下由QC完成;
6)安装:
舾装件安装于分段和船体。
7)破损区域修补涂装:
a.在总段阶段及船坞码头阶段,所安装的各类舾装件,由于焊接、烧损等引起的破坏,需在适当的时候用动力工具进行处理。
b.表面处理及涂装条件需在油漆厂商及船厂检查员指导下由QC进行控制。
8)管子及管子支撑典型截面处理:
如下图
2.2已安装的镀锌舾装件的处理方式
1)压载舱内的镀锌管子与扶手需按下述程序进行处理,除非在规格书中有其它指定。
2)工作流程
a.制作与镀锌:
b.安装:
在分段装配和/或预舾装,及分段涂装后,镀锌舾装件安装;
c.清洁:
油、湿气、灰尘及其它外来物质需清理;
d.复涂:
备注:
.如果在镀锌件安装前,进行复涂,则在安装后仅需对破损处进行修补。
.大致地复涂一度底漆面漆,然或按周围船体油漆对可达到的区域进行喷涂一度面漆,为了装饰目的,不用遮盖/蚀刻底漆。
因此,复涂的干膜厚可以不用达到周围船体指定的要求。
.如果指定为无机硅酸锌或其它特殊的类型的底漆,环氧或同等类型的底漆需使用以代替无机硅酸锌或其它特殊的类型的底漆。
三.涂装工作质量标准
1.参考标准
ISO8501-1-2007涂料和相关产品使用前钢衬底的制备.表面清洁度的目测评估.第1部分:
未涂覆钢衬底和彻底清除原有涂层后钢衬底。
ISO8501-3-2006涂装油漆和有关产品前钢材的预处理.表面清洁度的目视评定.第3部分:
焊接、切边及其它表面缺陷区域的处理等级。
ISO8502-3-1992涂装油漆和有关产品前钢材预处理表面清洁度的评定试验第3部分:
油漆前预处理后的钢材表面上的灰尘评定(压敏胶带法)。
ISO8502-6-2006涂覆油漆和相关产品前钢材的预处理表面清洁度的评定试验第6部分:
提取分析用可溶性杂质-Bresle法。
ISO8502-9-1998涂装油漆和有关产品前钢材预处理表面清洁度的评定试验第9部分:
水溶性盐的现场电导测定法。
ISO8503-1-1988涂装油漆和有关产品前钢材预处理喷射清理钢材的表面粗糙度特性第1部分:
磨料喷射清理表面粗糙度的ISO评定。
ISO8503-2-1988涂装油漆和有关产品前钢材预处理喷射清理钢材的表面粗糙度特性第2部分:
磨料喷射清理表面的粗糙度定级方法。
SSPC-PA2使用磁性仪进行干膜厚测量。
2.预处理及车间底漆喷涂
2.1预处理
2.1.1钢材预处理流水线流程:
清洁、预热、抛丸除锈、自动涂装、后加热、钢板运输。
预处理及车间底漆喷涂需自动执行。
2.1.2钢材表面预处理前应除去表面的油污、水分和杂物。
钢材正面有泥土、石子、稻草等垃圾的,用扫把、铲子将表面垃圾清除。
钢板反面存在草包等垃圾的,因先将预处理辊道暂停,再对钢板进行清理。
钢板表面有油污的,需将钢板吊离预处理辊道,并通知后道工序工作人员注意。
先用干抹布清除可初期的油污,再用高效洗涤剂对钢板进行清理,最后用清水清洗干净。
2.1.3轧钢需冲砂至ISOSa2.5,产生30~75微米的粗糙度,用Testex方法进行测量。
对钢板可以采用冲砂达到ISa2.5的标准代替抛丸。
2.1.4舾装件的钢材表面例如直径大于250毫米的管子、管子支架、基座、格栅支架、辅机基座、等等,需冲砂至指定等级。
上述提到的管子尺寸可以根据船厂的判断来改变。
2.1.5新批号磨料到达制造部之后需要按照ISO标准对磨料取样检测,含氯量最大允许值为250µs/cm。
由船厂QA进行检查并记录。
2.1.6当相对湿度大于85%或钢材表面温度低于露点温度3℃,不能进行冲砂。
(相对湿度85%限制参照于冲砂房内的湿度)
2.1.7根据油漆厂商推荐,钢板表面清洁和粗糙度需在表面处理后及车间底漆施工前予以检查。
2.1.8在涂装施工前,氯化钠不能超过50mg/m2。
2.1.9在冲砂后,需立即进行车间底漆喷涂。
2.1.10在阶段性的抽检中(一般,每月一次,选取3张钢板),需满足预处理检查要求且由涂层检查员记录。
2.2车间底漆喷涂
2.2.1当预处理完成后,一般情况下,为了防止钢结构及其构件返锈,一般施工一度20±5μm,无机硅酸锌车间底漆。
2.2.2在钢板切割开始前,油漆商需确认车间底漆与主油漆配套的兼容性。
2.3.钢结构要求
涂装前,自由边处理成至少为2mm的圆角,或经过三次打磨或至少经过等效的处理。
“等效处理”意为处理后产生的边几何形状上的等效,或优于可产生有效涂装性能的三次打磨。
用动力工具打磨时须考虑等同于上面指定的方式。
动力工具打磨见下图:
细节:
一度打磨+去除毛口
细节:
应用结果
※为了使毛口最小,磨具旋转方向面向切割边
※毛口去除:
砂皮纸
※毛口去除后,光顺边口
3.二次表面处理与局部表面处理
3.1要求
1)二次表面处理等级须符合IMOPSPC。
2)焊接和火焰切割的烟雾须适当去除,但是可残留痕迹。
3)推荐压载舱使用锈蚀等级为A或B的钢板,以确保可得到规定的粗糙度30~75微米且可以减少粗糙度仪的使用。
若使用锈蚀等级C的钢板,需提高粗糙度仪的检验范围。
4)当表面处理检查时,焊缝上的焊接缺陷例如局部气孔等需进行补焊或标注出来以后修补。
5)火焰切割的边、焊缝和破损区域需尽可能地根据船厂的需求进行跟踪补漆。
3.2分段阶段表面处理
1)车间底漆破损处和焊缝需冲砂至Sa2.5。
“破损的车间底漆”意为根据涂层检查员或主涂层油漆商意见判断车间底漆的条件,会降低主涂层性能,(例如烧损或腐蚀的区域)。
2)残留车间底漆的锌盐等污染物需根据油漆厂商的推荐用砂盘或扫砂去除。
3)除了清洁污染物,上述区域无需再作进一步处理,例如如果车间底漆(通过PSPC认可)与第一度油漆有良好的兼容性,则好的车间底漆不需要清除或拉毛。
4)当采用整体或局部冲砂时,要求粗糙度达到30-75微米(用Testex方法测试)。
5)当冲砂后有少量遗漏可用St3进行修正。
6)每个分段至少一点的钢板需进行残留氯化钠的含量测试。
7)氯化钠不能超过50mg/m2。
注:
在某种情况下,到达船厂的钢板已在钢厂或涂装分包商处施工了车间底漆。
在此情况下,车间底漆需冲砂至Sa2.5除了二次表面的标准需求,除非预处理完全符合标准需求,包括标准中的检查需求。
在二次表面开始前,涂层检查员需记录所有的检查与测试内容。
3.3预搭载后及在总组/船坞/码头阶段的表面处理
1)基于船厂施工方便,大接头(搭载焊缝)需处理至St3或更好或Sa2.5。
(大接头参照搭载焊缝)
2)小的破坏面积低于压载舱整个面积2%,处理至St3。
连续的破坏面积达25m2或超过压载舱整个面积2%,则处理至Sa2.5。
3)连续的破坏面积达25m2或超过压载舱整个面积2%主要靠目测,船东、油漆商、船厂三方中的任意两方可以判断。
4)破坏意为破损到达钢表面。
如仅表层受损可用适当动力工具修补。
缺陷不包括在2%或25m2估算内。
5)涂层叠加根据油漆厂商推荐进行处理。
认可的主涂层不可避免的接触或复涂另一类型认可的主涂练层,主涂层的兼容性需经油漆厂商认可,例如,涂层破损及靠近接头的局部涂层复涂将根据环境条件变化施工不同季节型的油漆。
6)涂装施工前,搭载焊缝的检查需在涂层检查员的判断下进行可视检查。
7)搭载焊缝宽度仅需满足PSPC最低要求。
4.涂装施工
4.1.涂装清洁标准
1)需去除湿气直到无可见湿气残留。
用适当的方法去除油和油脂,但痕迹允许可见。
清洁油污染物可根据油漆商的推荐用溶剂擦拭等。
2)用抹布、扫帚、刷子、压缩空气或真空吸尘器等清除灰尘和污泥。
然而,如果根据油漆商建议和船厂的施工程序,从喷枪出来的灰尘可接受。
3)表面处理和清洁后,进行钢表面灰尘的可视检查。
4)如果所有检查方中有异议,且任意两方认为是必需的,则可采用胶带测试法。
5)合适的记号笔可用且不用清除,记号笔需经油漆商认可。
4.2.涂装标准
1)统喷
.一般情况下,采用无气喷涂;然而,手工刷或辊涂也可用于当此类方法比无气喷涂适合的区域。
.例如复涂间隔、混合率等要素需根据油漆商的推荐。
.当相对湿度超过85%或表面温度低于露点温度3°C,则不能进行涂装工作。
.少量流挂(覆盖不超过½m2)可保留除非流挂严重且/或覆盖范围广或流到焊缝处或边缘导致干膜厚大于指定的干膜厚的最大值。
.由于不同涂装阶段/时间而产生的色差认为是自然状态,且可保留,除非涂层性能和质量受到影响。
.镀锌表面的破损区域,主要由于焊接,可以修补与周围环境相同或相等的油漆。
.每度涂层的湿膜厚由油漆工进行检查已达到指定干膜厚的目的。
.为了指导后续工作,除最后涂层外,每一度涂层施工后需测量干膜厚,总膜厚在最后一度施工完后须得到确认。
.应用90/10测定名义干膜厚320µm。
.总膜厚的最大值需根据油漆商具体规格书。
同时,需注意避免超范围的测量膜厚。
.稀释剂的使用需根据油漆商的推荐。
.面漆需为浅色以便于保养期内的检验。
浅色意为颜色可在一定范围内反射光线即简易闪光易于快速检查。
通常为浅灰色、浅黄色、游泳池兰/绿等,易于与锈蚀区别。
2)预涂(修补)
.边、焊缝、难以到达的区域等需预涂,以确保关键区域良好的涂层结合力及合适的膜厚。
.预涂需用刷子或同等方式进行。
.除了对焊缝进行第二度预涂,两度预涂在一定范围内可减少,当确保通过涂装施工,名义干膜厚能够满足,以避免不必要的超膜厚。
任何(第二度)的预涂需在CTF中充分描述。
确立(第二度)预涂范围,干膜厚测量靠近焊缝,但离焊缝不小于15mm,是可接受的。
名义干膜厚的确认可类似抽样测量靠近平面区域。
焊缝包括接头与密性焊缝。
.焊缝的第二道预涂减少需由船厂决定并得到涂层检查员的认可。
.如果施工2度预涂,第一度预涂的颜色不同于第一度主要涂层,第二度预涂的颜色需与最后一度主要涂层相同。
.预涂如下:
项目
子项目
处理方式
区域
图号
预涂
Remark
边
火焰割边
打磨
洞边缘
小洞
①
after1stand2ndcoat
大洞
②
after1stand2ndcoat
自由边
围圈板
③
after1stand2ndcoat
加强筋
④
after1stand2ndcoat
轧边
轧机器
T排
⑤
after1stand2ndcoat
轧机器
角纵材,轧平板
⑥
after1stand2ndcoat
自动焊
用焊接机器/设备
纵材板接缝
⑦
after1stor2ndcoat
O
焊缝
手工焊
手工焊接
围圈板的接缝(统喷可得到足够的膜厚的区域)
⑧
after1stor2ndcoat
O
加强筋的接缝(统喷可得到足够的膜厚的区域)
⑨
after1stor2ndcoat
O
备注:
标准"O":
除非名义膜厚未被证实。
须提供两度预涂。
5.涂装缺陷处理方式
油漆缺陷处理如下:
缺陷
处理方式
气泡
1)用砂纸擦掉气泡
2)清洁表面且施工原有涂层
复涂间隔期超期
1)用砂皮纸或砂轮片拉毛表面
2)施工后续配套
变暗
1)小范围或小区域可接受
2)大区域的可见范围需用溶剂擦拭
3)如必要,可重新涂装
开裂
1)砂轮扫过开裂达到的区域
2)按规格书施工配套
脱皮
1)刮擦受到影响的涂层表面
2)动力工具清洁表面且施工原有涂层
流挂,起皱
1)保留原样除非严重及大面积覆盖
2)如必要,修补此区域
褪色
保留原样
备注:
具体的修补按船厂工作流程及油漆商的推荐。
四.检验
1.检查程序
表面处理和涂装程序的检验需经过船东、船厂和油漆公司的认可且提交船级社审阅。
船级社可以,如果是要求的,参加协议过程。
这些检查项目需报告且包含于涂层技术文件(CTF)。
过程的细节和涂层的应用需在预备会议中由各方认可。
涂层检查员须拥有NACE涂层检查员2级或FROSIO检察员3级的认证。
涂层检查员的选择作为检验协议的一部分。
检查协议中的任何一方有权要求替换检查员,当原检查员被认定为不适合或不满足船舶建造的正确流程。
如果协议中的各方认为此需求是正当的,检查员需尽可能地立即替换。
在涂层检查员监督下,涂层检查员需要助手完成一部分的检查工作,这些人成为涂层检查员须满足船厂的协议。
在涂层过程执行中,涂层检查员须检查表面处理和涂层施工,例如最小值,这些测量项目在惯例中定义。
典型的结构部件需进行非破坏性的膜厚测量。
检查员需将检查工作进行记录并将其纳入涂装技术文件(CTF)。
1.1.涂装工作检查
1)检查总则
认可的有资质的涂层检查员需检查表面处理条件和以认可的方式进行的涂层质量施工。
2)检查员出勤
船厂需提供给检查员每日检查项目计划。
检查的结果须记录在施工日志上,包括任何涉及的备注。
3)检查须知
当涂装检查计划已完成,船厂须在同一天早上提供检查须知。
考虑到涂装工作的特定环境性,检查员可以重新安排及通报由于不可预料的船厂现场情况而取消或补充的检验项目计划。
在整个船舶建造过程中,船厂需在正常的工作时间安排涂装检验项目。
然而,如果为了满足船厂建造计划,所安排的检验在一般工作日之外包括周末和/或假期,船厂需提前通知涂层检查员,涂层检查员需配合进行检查。
如果在预期的须知后,涂层检查员缺席,涂层检查员需与船厂、船东检查员及涂料公司合作,在不打扰建造过程的情况下继续检查工作。
所有相关方在协议中需明确定义检查员有权认可指定的工作且根据所给标准编制报告。
4)检查结果判定
如果涂层检查员要求进行额外的测试、测量和检查,他需由明确的理由才能有权要求额外的测量。
合理的检验判定需基于PSPC及常识,且需经过相关检查员的同意。
5)涂层检查员的检查项目
在涂层过程执行中,涂层检查员须检查表面处理和涂层施工。
具体检验项目根据“压载水舱保护涂层质量控制流程”。
2.膜厚测量检验标准
2.1通则
1)干膜厚测量需使用磁性或电子测膜仪。
2)最后涂层施工完后,需进行最终膜厚测量。
除最后一度之外,作为后续工作的指导,每度的典型膜厚需进行测量。
3)结构的边缘及孔的部件等不用测量,一般对其进行预涂和/或测量困难或无法进行,以避免得到错误的信息。
4)对于每个舱室或小于舱室的单元,例如部件的局部/区域,需确认测试的干膜厚须满足PSPC的要求。
至少以下项目须记录:
(1)涂层检查员的数据及签名。
(2)舱室的名称(区域的名称/部件的名称,如果是比舱室小的单元)
(3)涂层规格书(名义干膜厚度,最大和最小膜厚等)
(4)测量的数量,最小值、最大值、平均值。
2.2干膜厚测量要求及认可准则
原则上测量如下:
1)平面上每5m2测量一个数据。
2)在尽可能靠近压载舱的边界,但距边界不小于15mm,每隔2到3米测量一个数据。
舱室边界意为纵向、横向、垂直角焊缝的顶端,测量仪器需尽量接近焊缝,但需离焊缝15mm远。
3)对纵向和横向扶强材
按下图,每间隔2到3米进行一组数据测量,在主要支撑结构之间至少测量2组数据。
备注:
图示箭头方向为关键区域,应理解为指示两侧。
4)对主要支撑件,每一组取3个读数,其他构件每一组取1到2个读数;
5)对于主要支撑件(纵向梁及横向肋板),如图3所示,每隔2到3米测量一组数据,且不少于3组。
双翼结构内的纵向梁及横向肋板作为平面进行测量,例如每5平方米测一点且每一纵向梁或横向肋至少测一点。
6)开口周围,开口每一面测一个数据。
开口意为直径大于等于400mm。
7)在复杂的区域(例如主要支撑件的大肘板),每平方米测量5点,且不少于3个点。
8)涂层检查员出于任何必须的考虑,可进行额外的抽检以检验膜厚。
2.3.认可准则
1)90/10检验规则
2)任何仪器读数可以小于指定膜厚的90%。
3)去除非连续性的不寻常的高或低的读数。
五.涂装日志
格式附表1~5
附表1
涂装日志(预处理)
地点:
日期:
序列号:
船名/编号
文件编号
钢板编号
船厂/钢厂
测试环境(要求:
相对湿度<85%;钢板温度-露点温度>3℃)
施工前
天气突然变化
备注
测量时间
气温(℃)
相对湿度(%)
露点(℃)
表面温度(℃)
预处理(要求:
表面粗糙度:
30-75μm;可溶性盐<50mg/m2NaCi)
盐分
油/油脂
灰尘
表面粗糙度
钢表面清洁度
备注
车间底漆
涂料生产商
施工方法
涂料名称
备注
产品标识/编号
涂料批号
标准干膜厚度
干膜厚度测量值
固化
检查人员
意见
结论
签名
日期/时间
涂层检查员
附表2
涂装日志(二次表面处理)
地点:
测试日期:
序列号:
船名/编号
舱/分段号
施工队
带班人员
内检QC
钢结构条件(要求:
ISO8501-3,P2;边缘处理成至少为2mm半径的圆角,或经三次打磨)
缺陷类型
修补方式
修补确认/日期
测试环境(要求:
相对湿度<85%;钢板温度-露点温度>3℃)
测量时间
气温(℃)
相对湿度(%)
露点(℃)
表面温度(℃)
二次表面处理
盐分
油/油脂
有□
无□
灰尘
表面粗糙度
钢表面清洁度
备注
测量参考:
ISO8502-9;测量参考:
ISO8502-3
检查人员
意见
结论
签名
日期/时间
涂层检查员:
附表3
涂装日志(涂装及干膜厚度检查报告)
地点:
测试日期:
序列号:
船名/编号
舱/分段号
建造阶段
大合拢后
施工劳务队
带班人员
内检QC
涂料生产商
第一道涂层
第二道涂层
涂料名称
产品标识/编号
涂料批号
第一度
第二度
之前
之后
之前
之后
测量时间
钢板温度(℃)
干温(℃)
相对湿度(%)
露点(℃)
油污染
干膜厚度要求
1SiCoat
2ndCoat
位置
最终涂层
测量数量
百分比
测量数量
百分比
最小膜厚
最大膜厚
平均膜厚
<90%
平面
肋位
舾装件
90%
≥NDFT
TOTAL
最后涂层状况确认
缺席类型
修补方式
修补确认/日期
备注:
附测量数据表
检查人员
意见
结论
签名
日期/时间
涂层检查员
附表4
涂装日志(合拢表面处理)
地点:
测试日期:
序列号:
船名/编号
舱/分段号
施工队
带班人员
内检QC
钢结构条件(要求:
ISO8502-3;P2)
缺席类型
修补方式
修补确认/日期
大合拢处理
舱室面积(含附件)
要求
表面清洁度
表面粗糙度
备注
接头
涂装面积见测量报告
其他要求参考二次表面处理
邻近区域的破坏面积小于25m2或破损面积不超过2%
邻近区域的破坏面积大于25m2或破损面积超过2%
油/油脂
灰尘
测量环境(要求:
相对湿度<85%;钢板温度-露点温度>>3℃)
测量时间
钢板温度(℃)
气温(℃)
相对湿度(%)
露点(℃)
表面温度(℃)
备注:
检查人员
意见