湿硫化氢环境腐蚀与防护.docx
《湿硫化氢环境腐蚀与防护.docx》由会员分享,可在线阅读,更多相关《湿硫化氢环境腐蚀与防护.docx(14页珍藏版)》请在冰豆网上搜索。
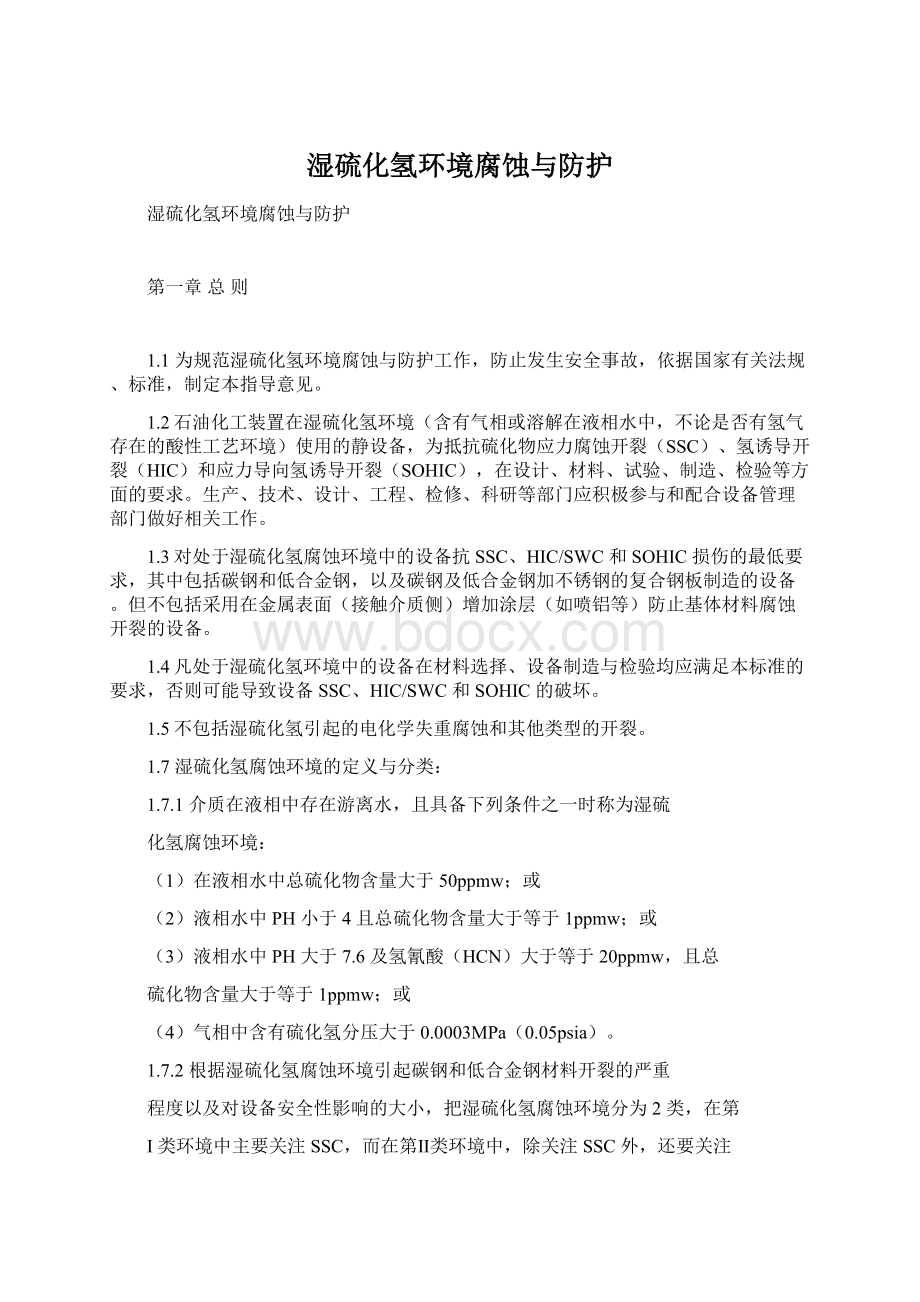
湿硫化氢环境腐蚀与防护
湿硫化氢环境腐蚀与防护
第一章总则
1.1为规范湿硫化氢环境腐蚀与防护工作,防止发生安全事故,依据国家有关法规、标准,制定本指导意见。
1.2石油化工装置在湿硫化氢环境(含有气相或溶解在液相水中,不论是否有氢气存在的酸性工艺环境)使用的静设备,为抵抗硫化物应力腐蚀开裂(SSC)、氢诱导开裂(HIC)和应力导向氢诱导开裂(SOHIC),在设计、材料、试验、制造、检验等方面的要求。
生产、技术、设计、工程、检修、科研等部门应积极参与和配合设备管理部门做好相关工作。
1.3对处于湿硫化氢腐蚀环境中的设备抗SSC、HIC/SWC和SOHIC损伤的最低要求,其中包括碳钢和低合金钢,以及碳钢及低合金钢加不锈钢的复合钢板制造的设备。
但不包括采用在金属表面(接触介质侧)增加涂层(如喷铝等)防止基体材料腐蚀开裂的设备。
1.4凡处于湿硫化氢环境中的设备在材料选择、设备制造与检验均应满足本标准的要求,否则可能导致设备SSC、HIC/SWC和SOHIC的破坏。
1.5不包括湿硫化氢引起的电化学失重腐蚀和其他类型的开裂。
1.7湿硫化氢腐蚀环境的定义与分类:
1.7.1介质在液相中存在游离水,且具备下列条件之一时称为湿硫
化氢腐蚀环境:
(1)在液相水中总硫化物含量大于50ppmw;或
(2)液相水中PH小于4且总硫化物含量大于等于1ppmw;或
(3)液相水中PH大于7.6及氢氰酸(HCN)大于等于20ppmw,且总
硫化物含量大于等于1ppmw;或
(4)气相中含有硫化氢分压大于0.0003MPa(0.05psia)。
1.7.2根据湿硫化氢腐蚀环境引起碳钢和低合金钢材料开裂的严重
程度以及对设备安全性影响的大小,把湿硫化氢腐蚀环境分为2类,在第
I类环境中主要关注SSC,而在第Ⅱ类环境中,除关注SSC外,还要关注
HIC和SOHIC等损伤。
具体划分类别如下:
第I类环境
(1)操作介质温度≤120℃;
(2)游离水中硫化氢含量大于50ppmw;或
(3)游离水的PH<4,且含有少量的硫化氢;或
(4)气相中硫化氢分压大于0.0003MPa(绝压);或
(5)游离水中含有少量硫化氢,溶解的HCN小于20ppmw,且PH>7.6。
第Ⅱ类环境
(1)操作介质温度≤120℃;
(2)水溶液中硫化氢含量大于50ppmw,且PH<4;或
(3)气相中硫化氢分压大于0.0003MPa(绝压),且水中总硫化物含
量大于2000ppmw,PH<4;或
(4)水溶液中总硫化物[注]含量大于2000ppmw,HCN含量大于
20ppmw,且PH>7.6;或
(5)水溶液中含有硫氢化胺(NH4HS)浓度大于2%(wt%)。
1.8湿硫化氢环境下的腐蚀与损伤主要包括:
酸性水腐蚀、湿H2S
损伤(HB/HIC/SOHIC/SSC)、胺腐蚀、碱式酸性水腐蚀(硫氢化氨腐蚀)
等几类。
1.9湿硫化氢环境下装置设计选材与制造应严格执行国家、行业及
中国石油相应标准规范,同时应参照以下标准规范:
(1)GB/T4340.1金属维氏硬度试验第一部分:
试验方法法
(2)GB/T6394金属平均晶粒度测定方法
(3)GB/T10561钢中非金属夹杂物含量的测定/标准评级图显微检
验法
(4)GB150固定式压力容器
(5)TSGR0004固定式压力容器安全技术监察规程
(6)SH/T3074石油化工钢制压力容器
(7)GB151管壳式换热器
(8)SH/T3075石油化工钢制压力容器材料选用规范
(9)GB/T8165不锈钢复合钢板和钢带
(10)GB/T699优质碳素结构钢
(11)GB713锅炉和压力容器用钢板
(12)NB/T47002压力容器用爆炸焊接复合板
(13)NB/T47008承压设备用碳素钢和合金钢锻件
(14)GB24511承压设备用不锈钢钢板和钢带
(15)JB4708钢制压力容器焊接工艺评定
(16)JB/T4711压力容器涂敷与运输包装
(17)其它适应于湿硫化氢环境设计选材与制造相关标准规范。
(18)GB/T4157金属在硫化氢环境中抗特殊形式环境开裂实验室实验
(19)GB/T8650管线钢和压力容器钢抗氢致开裂评定方法
(20)NACEMR0103MaterialsResistanttosulfideStressCrackinginCorrosivePetroleumRefiningEnvironments
(21)NACESP0472MethodsandControlstoPreventIn-ServiceEnvironmentalofCarbonSteelWeldmentsinCorrosivePetroleumRefiningEnvironments
(22)NACETM0177LaboratoryTestingofmetalsforResistancetoSulfideStressCrackingandStressCorrosiveCrackingInH2SEnvironments
(23)NACETM0284EvaluationofpipelineandPressureVesselSteelsforResistancetoHydrogen-InducedCracking
(24)NACERP0296GuidelinesforDetection,Repair,andMitigationofCrackingofExistingPetroleumRefineryPressureVesselsinWetHydrogenSulfideEnvironments
(25)API945(RP)AvoidingEnvironmentalCrackinginAmineUnits
(26)API-571DamageMechanismsAffectingFixedEquipmentintheRefiningIndustry(中文版)
(27)NACERP0103炼厂腐蚀性原油环境中抗硫化物应力开裂材料;
1.10发生部位:
(1)在炼油厂有湿H2S环境存在的部位都能发生HB、HIC、SOHIC、SSC损伤。
(2)在加氢装置中,NH4HS浓度增大到超过2%会增加发生鼓泡、HIC和SOHIC的可能性。
(3)氰化物会明显增加HB、HIC、SOHIC损伤的可能性和严重程度。
对于流体催化裂化和延迟焦化装置的汽相回收单元尤为明显。
典型的部位包括分馏塔塔顶罐,分离塔,吸收塔和汽提塔,压缩机级间分离器和缓冲罐,各种换热器、冷却器和空冷器。
酸性水汽提塔和胺再生塔顶系统尤其容易发生湿H2S损伤,因为此处存在氰化物,NH4HS浓度也很高。
(4)SSC最有可能在硬焊缝和热影响区及高强度部件中发现。
高强度部件包括螺栓,安全阀弹簧,400系列不锈钢阀芯,压缩机轴、套管和弹簧。
1.11各炼化企业在遵循本指导意见的基础上,应加强湿硫化氢环境腐蚀防护新技术的引进与推广,如各种涂层、镀层技术等。
第二章湿硫化氢环境设备的材料选择
2.1处于湿硫化氢腐蚀环境下的设备承压件应选用表2.1中的材料:
表2.1湿硫化氢腐蚀环境下的设备承压件推荐材料
2.2材料选择原则
2.2.1在第I类环境下操作的设备承压件应选用表2.1中的普通碳
钢和低合金钢。
2.2.2在第Ⅱ类环境下操作的设备承压件应选用表2.1中的抗HIC
碳钢和低合金钢,以及表2.1中的复合材料。
2.3材料附加要求
2.3.1碳钢和低合金钢
2.3.1.1在湿硫氢腐蚀环境下操作的设备用碳钢和低合金钢除符合
相应的材料标准及相关规范和规程的规定外还应符合下列附加要求:
a)化学成分(熔炼分析):
硫(S)含量≤0.08%,磷(P)≤0.12%
成品分析偏差应符合GB/T222的规定。
b)碳当量CE:
对普通碳素钢CE≤0.40,对低合金钢CE≤0.45。
元素以重量百分比代入(Wt%)
c)力学性能(试样须经模拟焊后热处理)
材料标准规定的屈服强度下限ReL≤355MPa
材料最高抗拉强度Rm≤600MPa
-20℃冲击功合格指标为:
三个试样平均值KV2≥34J,允许其中一
个KV2≥25J;
d)使用状态:
正火或正火+回火
e)无损检测:
钢板厚度超过12mm时,按JB/T4730.3进行100%超声
检测,气质量等级按下列要求:
钢板厚度12~60mm质量等级不低于Ⅱ级为合格
钢板厚度大于60mm质量等级低于I级为合格
2.3.1.2钢板和锻件应逐张(件)进行布氏硬度试验,硬度值应小于等于200HBW。
2.3.1.3处于湿硫化氢环境的锻焊设备壳体、接管、法兰及接管法兰的锻件级别按设计文件的要求。
2.3.2抗HIC碳钢和低合金钢
2.3.2.1钢板除符合GB/T713、SA516-65/70和NB/T47008的规定外,还应满足2.3.1.2条及以下要求:
a)冶炼方法:
应采用电炉+炉外精炼方法(或其他高质量的冶炼方法),应为本质细晶粒钢
b)化学成分(熔炼分析wt%):
P≤0.010;S≤0.003;Ti≤0.01;B≤0.0005;Nb+V≤0.05。
成品分析偏差应符合GB/T222的规定。
C)碳当量CE:
钢材厚度≤50mm时;CE≤0.43;
钢材厚度>50mm时;CE≤0.45。
d)无损检测(同5.3.1.1e);
e)使用状态:
正火或正火+回火;
2.3.2.2钢板和锻件的晶粒度应符合GB/T6394的要求,晶粒度不粗
于5级。
2.3.2.3锻件和厚度大于20mm的钢板应按照GB10561规定的B法进行非金属夹杂物评定,硫化物类(A类)、氧化铝类(B类)、硅酸盐类(C类)及球状氧化物类(D类)、单颗粒球状类(DS类)均不得大于1.5级,且应满足A+C≤2.0,B+D≤2.0,A+B+C+D+DS≤4.5级。
2.3.2.4钢板和锻件应在正火状态交货,经模拟热处理后的力学性能除应符合GB713、NB47008的规定外,还应满足以下要求,推荐模拟热处理为610℃±10℃,保温时间不小于2.5min/每1mm厚度×预期热处理次数,且最小为2h,或者供需双方协商。
a)厚度大于20mm的钢板应进行厚度方向的性能试验,其Ψz三个试样平均值大于等于35%,单个试样最低值大于等于25%。
b)抗HIC钢板和锻件冲击功三个试样平均值KV2≥34J,允许其中一个试样KV2≥25J。
Q245R(HIC)的试验温度为-20℃;Q345R(HIC)和SA516-65/70(HIC)的试验温度为-30℃。
2.3.2.5抗HIC钢板应按GB/T4157或NACETM0177的规定进行抗SSC试验,其门槛值)应大于等于0.8ReL。
2.3.2.6抗HIC钢板应按GB/T8650或NACETM0284的试验方法进行抗HIC腐蚀试验,其试验溶液和试验要求按如下规定:
2.3.2.6.1采用GB/T8650或NACETM0284的A溶液,
2.3.2.6.2HIC试验合格指标如下:
CLR<5%CTR<1.5%CSR<0.5%。
注:
CLR为裂纹长度率(%);CTR为裂纹厚度率(%);CSR为裂纹敏感率(%)。
2.3.2.7如果用户规定更苛刻的使用环境,HIC试验可采用现场使用环境一样的条件进行评定,其合格指标可由双方商定。
2.3.3复合材料
2.3.3.1复合材料的基材〔Q235R、Q245R、20锻件、16Mn锻件、10钢管、20钢管〕应满足GB713、NB47008的规定,使用状态为正火、正火。
2.3.3.2复合材料的复层(S11306,S30403,S31603,S32168)钢板应符合GB24511的规定,使用状态S11306为退火,奥氏体不锈钢为固溶处理。
2.3.3.3复合材料应满足NB47002或GB8165的规定,其制造方法可采用爆炸复合、轧制复合或爆炸+轧制复合。
2.3.3.4基材为5.1所述材质时,复合钢板爆炸后应进行消除应力
热处理。
2.4螺栓材料
2.4.1处于湿硫化氢环境的螺栓材料应选用强度级别较低的碳素钢、铁素体钢或奥氏体不锈钢。
碳素钢使用状态为正火或退火,铁素体钢使用状态为退火,奥氏体不锈钢使用状态为固溶处理。
2.4.2碳素钢螺栓材料的力学性能除应满足GB/T699的规定外,还应符合下述要求:
2.4.4.1螺栓应进行-20℃冲击试验,冲击功三个试样KV2平均值大于等于34J,单个试样最低值大于等于25J。
2.4.4.2断后伸长率A≥25%。
2.4.4.3螺栓硬度应小于等于22HRC。
2.4.5铁素体和奥氏体钢螺栓硬度应小于等于22HRC。
2.5处于湿硫化氢腐蚀环境的碳钢换热管应满足下述要求:
a)材料标准规定屈服强度Rel≤355MPa;
b)材料标准规定的抗拉强度Rm≤480MPa;
c)材料的使用状态为正火或退火;
d)换热管应采用冷轧(拔)制造方法。
第三章湿硫化氢环境设备的设计
3.1一般规定
3.1.1湿硫化氢腐蚀环境下设备的材料选择应以碳钢、抗HIC钢为
主,腐蚀严重时可选用奥氏体复合材料。
压力容器的设计应符合GB150和
TSGR0004的规定。
3.1.2湿硫化氢腐蚀环境下设备的设计寿命应符合国家现行标准和SH/T3074的规定。
3.1.3湿硫化氢腐蚀环境下碳钢和低合金钢制设备的腐蚀裕量一般取小于等于5mm。
复合材料制设备的复合层一般只作为腐蚀裕量,而不计入强度。
3.2材料匹配
3.2.1选择设备主材材料为普通碳钢和低合金钢时,其接管、接管法兰应选用强度级别较低的碳钢,处于接触介质侧螺栓、螺母宜选用奥氏体(或铁素体)不锈钢。
3.2.2选择设备主体材料为抗HIC碳钢和低合金钢时,其接管、接管法兰应选用同种类的抗HIC钢,处于接触介质侧螺栓、螺母宜选用奥氏体(或铁素体)不锈钢。
3.2.3选择设备主体材料为奥氏体(铁素体)复合材料时时,其接管、接管法兰应采用复合或堆焊奥氏体不锈钢,处于接触介质侧螺栓、螺母应选用奥氏体(或铁素体)不锈钢。
3.3其它
3.3.1材料如果经历Ac3以上温度的热成型后,应按设计文件要求的最终使用状态重新进行热处理。
3.3.2处于湿硫化氢腐蚀环境的碳钢低合金钢换热管宜采用Ф25×3mm或Ф19×3mm的规格,且尺寸偏差采用较高级。
3.3.3换热管U型弯管及300mm直管范围煨弯后应进行消除应力热处理或退火处理,热处理后其硬度应HBW≤200(或HV10≤210)。
第四章湿硫化氢环境设备的制造
4.1一般规定
4.1.1处于湿硫化氢环境的压力容器的制造除应满足本标准的要求外,还应遵守国家颁布的有关法令、法规,并符合GB150、GB151等标准的规定和要求。
4.2焊接工艺评定
4.2.1采用碳钢、抗HIC钢制造的设备其焊接工艺评定应按照JB/T4708有关规定,同时应满足下述要求。
4.2.1.1焊接工艺评定的硬度试验方法应按GB/T4304.1规定的维氏HV10进行,其验收指标为HV10≤235;
4.2.1.2焊接工艺评定的焊接接头(母材、热影响区、焊缝)应按图1、图2规定位置进行硬度检测。
4.2.1.3焊接工艺评定应包括返修工艺。
4.3冷成形
4.3.1碳钢、抗HIC钢制设备壳体、弯管等经任何冷变形后,导致材料表面纤维永久变形量大于5%时,不论硬度多少均应作消除应力热处理。
热处理温度不应低于595℃。
热处理后的硬度应HBW≤200。
.
4.4焊接
4.4.1碳钢、抗HIC钢材料制设备的焊接规程应符合现行国家标准的有关规定外,还应符合下列规定
4.4.1.1当设备主体材料的CE大于0.4,或者Nb+V大于0.01Wt%时,
焊接时应对母材进行预热,预热温度不低于100℃,且层间温度不应低于预热温度,直至焊接工作完成。
4.4.1.2处于湿硫化氢腐蚀环境的设备其焊接方法应采用手工电弧焊(SMAW)、埋弧自动焊(SAW)、气体保护焊(GMAW)、药芯焊丝电弧焊(FCAW)、气体保护钨极电弧焊(GTAW)进行焊接,手工电弧焊应采用低氢型焊条。
4.4.1.3焊接材料(焊条、焊剂、焊丝)中锰、硅含量应尽可能低。
手工电弧焊(SMAW)和埋弧自动焊(SAW)使用的焊接材料中锰含量应小于等于0.10%(wt),硅含量应小于等于0.50%(wt).
4.4.1.4不应采用可能使熔敷金属中镍含量大于1%的焊接工艺和焊材。
4.4.1.5焊接过程中应控制焊缝从800℃到500℃范围内的冷却时间(t8/5),应使此区域焊缝的冷却时间尽可能短。
t8/5时间计算方法见附录B。
4.4.1.6处于湿硫化氢腐蚀环境的设备对接焊缝和角焊缝焊接宜采用回火焊道的焊接技术,回火焊道的焊接宜采用手工GTAW,以保证焊道与焊道之间产生回火作用。
回火焊道焊接结构示意图见图3和图4。
4.4.1.7当采用回火焊道技术进行焊缝表面缺陷返修时,焊接前缺陷的清除范围应不小于4倍的缺陷直径,补焊金属不少于两层,最后的盖面层不应接触基体材料表面,焊缝的焊趾与基体材料的距离应按图4的要求。
4.4.1.8所有与承压部件相连的临时性或永久性附件的焊接应对母材进行预热,预热方法应从附件施焊面的另一侧进行,使得附件焊接区域能够均匀受热。
4.4.1.9所有与承压部件相连的永久性附件的焊接接头应采用全焊
透结构。
4.4.2焊接接头的力学性能不应低于母材标准规定的最低值。
焊接接头的硫化物应力腐蚀试验和HIC试样应符合2.3.2.6条的要求。
图1硬度检测位置
A距表面1.5±0.5mm(0.06±0.02in)
(a)对接焊缝-图1(b)任何给定位置
9
(b)角焊缝
(c)堆焊或修补焊缝-如果堆焊位于工艺介质侧
A距表面1.5±0.5mm(0.06±0.02in)
B距熔合线≤0.5mm(0.02in)
L:
两压痕间距1mm(0.04in)
注:
在临近焊帽和焊缝根部表面进行测量
10
图2硬度测试详图
1
4.5焊后热处理
4.5.1碳钢、抗HIC钢制设备全部焊接工作完成后应进行焊后热处理,热处理温度不应低于620℃,保温时间按壳体厚度每25mm不少于1h,且不应少于2h。
不允许采用降低热处理温度,延长保温时间的方法消除设备的残余应力。
4.5.2热处理后所有焊缝的硬度值HBW应小于等于200。
硬度检测应尽可能在接触介质侧进行。
对接焊缝至少每3m范围内要进行一点硬度检测,每条角接焊缝至少要有三点硬度检测。
4.6无损检测
4.6.1碳钢、抗HIC制设备焊接接头的无损检测要求应符合有关标准、设计文件的规定。
4.6.2磁粉检测推荐采用湿式荧光磁粉法(WFMT).
4.6.3碳钢、抗HIC钢制设备焊接接头的无损检测应在焊接完成后至少48h后进行,且至少有一种无损检测方法应在焊后热处理之后进行。
4.7水压试验
4.7.1湿硫化氢腐蚀环境的设备水压试验应按GB150、GB151、JB/T4732和设计文件的规定要求。
4.8运输包装
湿硫化氢腐蚀环境的设备的运输包装应按JB4711和设计文件的规定执行。
第五章腐蚀监(检)测与检查
5.1工艺条件应当由工艺工程师和腐蚀/材料专家进行评估,以确定管线和设备那些部位的条件最容易促进湿H2S损伤。
应当定期或根据需要采集现场自由水相的样品以监测条件或条件的变化,特别是在水冲洗或注多硫化物时候使用。
5.2湿H2S损伤的检查一般集中在焊缝和管口上。
由于后果严重,炼油厂一般都采取步骤来优先安排和执行这类损伤的检查。
下面总结了湿H2S损伤检查一般要注意的事项。
但对于更详细的检查计划的开发包括方法、范围和表面处理,可以直接参考NACERP0296中检查和维修要点。
5.3虽然裂纹可能通过肉眼看到,但裂纹检查最好采用WFMT、EC、RT或ACFM技术。
通过喷丸、高压水射流或其它方法的表面处理通常需要采用WFMT而不用ACFM。
PT不能发现微裂纹,不能依靠它来检查。
5.4可以使用包括外部SWUT的UT技术。
SWUT对于体积检查和裂纹尺寸特别有用。
电阻仪器对于测量裂纹深度没有作用。
5.5磨削裂纹或采用热弧凿清除是一种确定裂纹深度的可行方法。
5.6AET可以用于监测裂纹生长。
5.7由酸性的酸性水引起的腐蚀通常为均匀减薄。
但可能发生局部腐蚀或局部垢下侵蚀,尤其是有氧存在时。
在含CO2环境中的腐蚀可能还伴随着碳酸盐应力腐蚀开裂。
5.8局部减薄部位的迹象可以通过扫描超声波测厚的方法或轮廓射线透照术来发现。
5.9对于碳钢,损伤通常为均匀减薄,但在高流速或湍流的特定区域可能是高度局部,通常在有水相凝结的部位。
5.10为了尽量减少酸性的酸性水腐蚀的影响,工艺和腐蚀监测是一个健全方案的重要方面。
5.11顶部缓冲罐的排水应当定期进行pH监测。