储罐安装施工方案.docx
《储罐安装施工方案.docx》由会员分享,可在线阅读,更多相关《储罐安装施工方案.docx(29页珍藏版)》请在冰豆网上搜索。
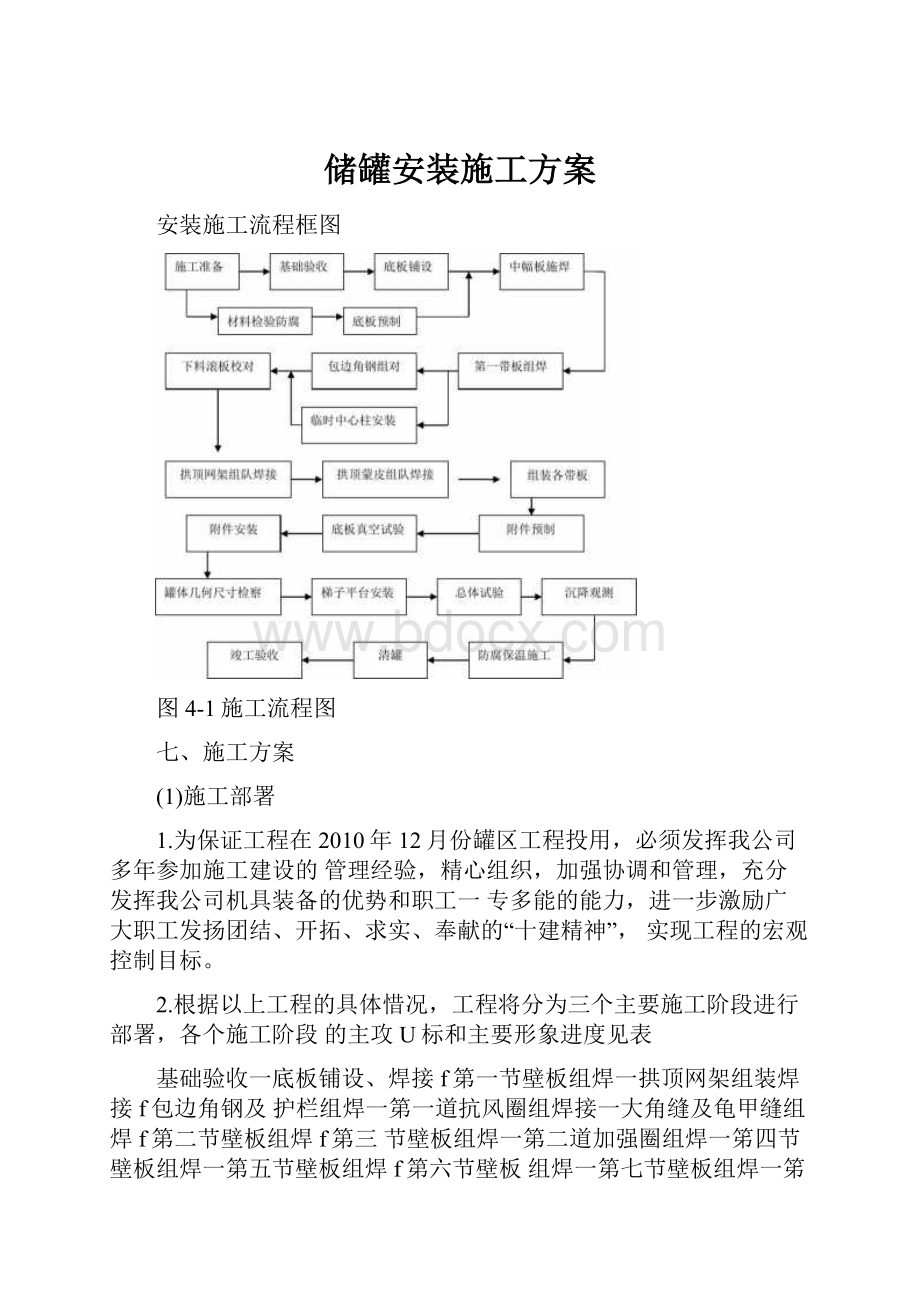
储罐安装施工方案
安装施工流程框图
图4-1施工流程图
七、施工方案
(1)施工部署
1.为保证工程在2010年12月份罐区工程投用,必须发挥我公司多年参加施工建设的管理经验,精心组织,加强协调和管理,充分发挥我公司机具装备的优势和职工一专多能的能力,进一步激励广大职工发扬团结、开拓、求实、奉献的“十建精神”,实现工程的宏观控制目标。
2.根据以上工程的具体惜况,工程将分为三个主要施工阶段进行部署,各个施工阶段的主攻U标和主要形象进度见表
基础验收一底板铺设、焊接f第一节壁板组焊一拱顶网架组装焊接f包边角钢及护栏组焊一第一道抗风圈组焊接一大角缝及龟甲缝组焊f第二节壁板组焊f第三节壁板组焊一第二道加强圈组焊一笫四节壁板组焊一第五节壁板组焊f第六节壁板组焊一第七节壁板组焊一笫八节壁板组焊一第九节壁板组焊一附件安装完毕f其它附件安装f充水试验f清罐f交工验收。
主要形象进度表
工期
第一施工阶段
20天
第二施工阶段
80夭
第三施工阶段
20天
主攻
目标
施工准备机具进现场主抓油罐预制底板焊接完
力保油罐主体安装完
油罐扫尾充水试验、工程竣工
验收
进度
要求
1•熟悉图纸、编制施工组织设计和施工方案
2.罐体材料预制
3.盘梯、瓜皮板预制
1.油罐壁板安装完
2.拱顶焊接完,罐
底气密完
3.油罐附件预制完
1•油罐附件安装
2油罐充水试验
3油罐内清扫封
闭
(2)储罐施工:
1.施工准备;
a.根据设备制作图样,编写详细的施工方案,编制详细的材料、配件预算进行施工材料准备。
b.准备现场临时加工厂:
安装好卷板机、剪板机、电焊机、空压机等机械设备。
c.搭设好预制钢平台,并根据方案要求制作工装、卡具和器具,所用计量器具应全部调校合格并在有效期内。
d.组织施工作业人员认真熟悉施工图样,进行详细的技术交底,了解施工方法、技术要求。
2.材料检验
a现场制作设备用钢板、配件、钢管、紧固件等,应具有质量合格证明书,当无合格证或对合格证有疑问时,应对材料、配件进行复验,合格方可使用。
b焊接材料(焊条、焊丝)应具有质量合格证书。
其合格证检测内容和结果应符合相应国家标准规定,否则应进行复验,合格方可使用。
C材料表面锈蚀、薄量、划痕深度与钢板实际负偏差之和,应符合响应国家标准规定.存放过程中,应防止钢板产生变形,严禁用带棱角的物件下垫。
D设备的小型接管、法兰、人孔、手孔、紧固件等配件,均在专业加工厂加工成品交付现场使用,配件交付时应具有产品质量合格证。
(3)基础验收
底板铺设前,应先会同有关部门对罐基础整体儿何尺寸、表面标高、坡度等进行验收
(1)基础中心标高允许偏差为±20mm
(2)支撑罐臂的基础表面,每3in弧长内任意两点的高差不得大于12mm.
(3)沥青砂层表面应平整密实,无明显的隆起、凹陷及贯穿裂纹。
(4)验收完毕应办理基础中间交接手续。
(4)储罐制作一般要求
(1)放样、下料询应根据设备制作图样进行排版,按排版图进行放样和下料。
(2)材料放样应釆用1:
1实样放样,放样时应根据工艺要求预留焊接缩和加工裕量。
(3)板材下料可采用火焰切割下料,机械剪切下料。
(4)板材边缘加工面应平滑,不得有夹渣、分层、裂纹及熔渣等缺陷.火焰切割坡口产生的表面硬化层应磨除。
(5)罐在预制放样、下料组装及检验过程中所使用的样板应符合下列规定:
—样板采用0.5〜0.7mm的镀锌铁皮制作,样杆釆用1.5〜2mm厚,宽30〜40mm的扁铁制作。
—当构件的曲率半径小于或等于12.5m时,弧形样板的弦长不得小于1.5m。
曲率半径大于12.5m时弧形弦长不得小于2mo
—直线样板的长度不得小于Imo
—测量焊缝角变形的样板,其弦长不得小于lmc
—样板、样杆周边应光滑整齐。
弧形大样板为避免其变形,可作加固处理。
—样板制作完毕后,用铅油在样板上标出正、反面及所代表的的构件名称、部位、规格,并妥善保管。
—号料前,应核对钢板材质、规格,钢板放置要平。
在钢板上定出基准线,然后划出长度、宽度的切割线,经检查后,在切割线上打上样冲眼,并用色笔作出标记,在切割线内侧50mm处划出检查线,同时在钢板上角标明罐号、排版编号、规格与边缘加工等符号。
底圈罐壁与罐底边缘板角焊接缝的坡口型式应严格按照图纸要求进行施工。
(5)罐底板预制
1.底板预制前,应根据图样要求及材料规格绘制排版图,罐底排版形式如下图:
2•罐底的排版直经,按设计•比例绘制。
3•边缘板沿罐底半径方向的最小尺寸不得小于700mm。
4•中幅板宽度不得小于lm,长度不得小于2m。
5.底板任意相邻焊缝之间距离不得小于200nmi。
罐底板结构形式示意图
6.罐底边缘板的对接焊缝全部釆用带垫板的对接接头形式,其下料的单面坡口角度为30°±2.5°,对接接头坡口形式如下图:
7•弓形边缘板的对接接头,宜采用不等间隙,外侧间隙el宜为6〜7111111,内侧间隙e2宜为8〜12mm,弓形边缘板的对接接头间隙形式见下图:
弓形边缘板的对接接头间隐示意圈
8.弓形边缘板直边切割釆用半自动切割机切割,弧形段有手工氧一烘焰切割,其外缘半径按图纸计算半径放大25mm,边缘板间对接焊缝间隙外部较内部小3mm下料,边缘板预制的质量要求如下图示:
C
F
D
罐底板弓形边板测量部位图:
弓形边板尺寸允许偏差(mm)表
测量部位
允许偏差
长度ABCD
±2
宽度AC、BD、EF
±2
对角线之差1AD-BC|
W3
9.罐底板中幅板下料,采用半自动切割机,下料按底板排版图尺寸进行,其预制质量要求见下图。
与边缘板间对接边留存150nmi,等焊接龟屮缝时再精确下料。
中幅板尺寸允许偏差应符合下列表的要求:
弓形边缘板尺寸允许偏差(mm)表5・2
测量部位
允许偏差
长度AB、CD
±2
宽度AC、BD、EF
±2
对角线之差|AD-BC|
W3
C.中幅板尺寸允许偏差应符合表5・3的要求。
中幅板(罐壁板)尺寸允许偏差5m)表5・3
测量部位
环缝对焊(mm)板长AB(CD)W10m
环缝搭接(mm)
宽度AB、BD、EF
±1
±2
长度AB、CD
±1.5
±1.5
对角线之差AD-BC
W2
W3
直线度
AC、BD
AB、CD
<2
W2
中幅板(罐壁板)尺寸测量部位
10.罐底板铺设前,要清除表面的泥土、油污、其下表面涂刷两边沥青防锈漆,四周留出50mm不予涂刷。
口.底板采用对接接头,条形垫板。
12.中幅板焊接时应先焊短焊缝,第一层焊道应采用分段退焊或跳焊法。
(6)罐壁板预制
1.罐壁板预制前应绘制排版图,排版图应符合下列要求:
a各圈壁板的纵缝宜向同一方向逐圈错开,其间距宜为板长的1/3,且不得小于500mm。
b底圈壁板纵向焊缝与罐底边缘板的对接焊缝之间的距离不得小于200mm。
c罐壁开孔接管或开孔接管补强板外缘与罐壁纵向焊缝之间距离不得小于
200mm;与环向焊缝之间的距离不得小于lOOnun。
d包边角钢对接接头与罐壁纵向焊缝之间的距离不得小于200mm。
e壁板宽度不得小于lm,长度不得小于2m。
f壁板宽度变更时,各圈壁板厚度不得小于壁板变化圈上相应高度的尽度。
g坡口型式及尺寸要符合图样的要求:
罐壁板尺寸允许偏差应符合设讣技术文件规定;
h罐壁板采用净料法进行预制,璧板的周长按下式进行汁算:
L=n(Di+S)-nb+na+工A
式中:
L一壁板周长(mm)
Di—油罐内径(mm)
S—油罐壁片(mm)
b—对接接头间隙(mm)
a-每条焊缝收缩量(mm)手工焊取2mm,
△—每块壁板长度偏差值(mm)
n—单圈壁板的数量
2.罐墜板预制用半自动切割机进行放线切割下料,壁板预制不留调整板,一次下净料,预制一圈壁板的累计误差等于零,这样预制,有利于保证罐体整体儿何尺寸,采用这种方法,要求预制精度高。
壁板尺寸允许偏差见表
测量部位
环缝对焊(min)板长AB(CD)W10m
环缝搭接(mm)
宽度AB、BD、EF
±1
±2
长度AB、CD
±1.5
±1.5
对角线之差AD-BC
W2
W3
直线度
AC、BD
W1
W1
AB
W2
W3
壁板尺寸测量部位
3.壁板下料后,根据质量检查表进行检查,并检查其坡口形式符合要求,纵缝对接接头的坡口角度a应为60°±5°,钝边F为1mm,组对间隙G应为3mm,坡口形式见下图:
S>10mm
纵缝对接接头的坡口、环缝对接接头的坡口角度a应为50°±5°,钝边F为1mm,组对间隙G应为3mm,坡口形式见下图
环缝对接接头的接头型式
4.壁板预制合格后,用8吨义车吊运到指定地点存放,存放地点距卷板机较近,存放时要按安装先后,分门别类存放,板边错开150mm。
5.壁板下料后检查合格后,在卷板机上滚弧,滚弧时应用前后拖架,壁板卷制后,应直立放在平台上,水平方向用弧形样板检查,其间隙不大于4mm・垂直方向上用直线样板检查,其间隙不得大于1mmo
6.预制壁板时,用义车配合,防止在卷制过程中使已卷成的圆弧回直或变形,卷制好的壁板用专用胎架运输、存放。
(7)罐顶板预制
1.浮顶板预制时要绘制排版图,且应符合下列要求;
顶板任意相邻焊缝的间距大于200mm
单块顶板本身的拼接,可釆用对接。
2.拱顶的顶板及加强筋,应进行成行加工。
加强筋用弧形样板检查,其间隙不得大于2mm,加强筋与顶板组焊时,应采取防变形措施。
加强筋的拚接釆用对接街头时,应加垫板,且必须完全焊透。
(8)构件预制
1•加强圈、包边角钢等弧形构件加工成型后,用弧形样板检查,其间隙不得大于2mm,放在平台上检查,其翘曲变型不得超过构件长度的0.1%且不大于4価。
2.热炜成型的构件不得有过烧、变质现象,其厚度减簿量不应超过1mm。
3、储罐主体安装工艺措施
(1).罐地板组装
1.罐底板铺设前,要清除表面的泥土、油污、其下表面涂刷两边沥青防锈漆,四周留出50mm不予涂刷。
2.罐底板山中幅板和边缘板组成,罐底板采用对接接头,条形垫板。
基础验收合格证,确定方位画出中心线,得出中点、画出垫板,边缘板安装位置线,其中边缘板安装铺设按设讣直径和基础坡度长度外加收缩余量来确定半径。
边缘板铺设间隙外侧为6mm,内侧为8mm。
3.板铺设时,按照排版图从中心向四周铺设。
边缘板依安装位置线铺设,垫板与相邻两块底板中的一块先点焊,底板与垫板应贴紧,其间隙不大于lmmo
4.中幅板组对时,其间隙控制在4—6mm之间。
地板与垫板之间的点焊应按焊接技术措施规定的次序严格执行。
5.中幅板焊接时,应先焊短焊缝,后焊长焊缝,笫一层焊道应釆用分段退焊或跳焊法。
搭接角焊缝至少焊两遍。
6.底板焊接完后,检查凹凸度,凹凸变形的深度不应大于变形长度的2%,且不应大于50mm,并对所有焊接进行真空试验,试验负压值应符合图纸要求。
(2)・罐壁组装
1.壁板采用正装组装。
随着工程施工进度对基础进行沉降观测,并做好记录。
发现问题及时停止施工,处理好后再继续施工。
首先确定壁板的安装半径,安装半径的讣算公式如下:
Rl=(R+n*a/2*刃)/cosB
式中:
R1一壁板安装内半径(nun):
R—储罐的内半径(mm);
n—壁板立焊缝数;
a—每条立焊缝的收缩量(mm),手工焊取2;
B—基础坡度夹角(°);
2.按照安装圆内半径在罐底划出圆周线及每张壁板的安装位置线,并在安装圆内侧
100mm画出检查圆线,并打样冲眼作出标记;
3.壁板运到施工现场后应逐张检査壁板的预制质量,合格后方可组装,需重新校正时应防止出现锤痕;
4.壁板组装前,应对预制的壁板进行复验,按排版图号对号入座,需要校正时,防止出现锤痕。
5.壁板组装时应保证内表面平齐,错边量应符合表5-4要求。
内表面错边量允许偏差表5-4
项目
板后(mm)
错差量允许偏差(mm)
纵向焊缝
8^10
1.5
纵向焊缝
8<10
1/105且不大于1.5
环向焊缝
8W8
1.5
环向焊缝
8>8
1/56且不大于3
组装焊接后,罐壁的局部凹凸变形要小于3nmi,焊缝的角变形用lin长的弧
形样
板检查要W10mmo
顶圈壁板的组装允许偏差见表5-5所示。
顶圈壁板的组装允许偏差表5-5
项目
允许偏差(mm)
相邻两壁板上口水平度
2
整个圆周上任意两点水平度
6
壁板的铅垂度
3
顶圈壁板lm高处内表面任意点半径
±13
6•罐壁的焊接,应先焊纵焊缝,后焊环焊缝。
当焊完相邻两圈壁板的纵焊缝后再焊其间的环焊缝。
在壁板组立前,在存运胎架上安装好帽,龙门板及蝴蝶板,如右图示。
壁板的吊装用履带吊车进行,并使用吊梁。
第一带壁板组对前,按施工图划线安装组对档板。
履莊、战醴组裝夹具安裳示意爲
7•壁板逐张组对,每张安装2个加减丝以调节壁板垂直度。
安装纵缝组对卡具,及方楔,以将壁板固定。
整圈壁板全部组立后调整壁板立纵组对错
边量,上口水平度及壁板的垂直度符合以要求,并检查lin高处任意半径的偏差不超过±32mm。
二至九带板的组装方法参照第一带壁板的组装。
环缝应安装组对用龙门板、槽钢。
如图。
8.组装第二带板前在第一带板上搭设简易脚手架,以后组对上一带板时在下带板上搭
设同样的脚手架,在罐人孔处搭设斜梯,以供上下脚手架。
在浮顶施丄时将浮顶下面的斜梯拆除,浮顶上面的斜梯逐层搭设,每台罐三层脚手架循环使用。
9.
壁板焊接先焊立缝,再焊环缝,立缝焊接前,先焊上定位龙门板,见左图示,然后拆下立缝组对卡具。
立缝的坡口型式是:
24.5mm及以上厚的壁板立缝为X型坡口,其余V型坡口。
焊接时,先焊外部,后焊内部,立缝下端150nini焊缝采用手工焊,其余为自动焊,立缝焊接上端加熄弧板,见左图示。
大角焊缝焊接前安装防变形卡具如左下图示。
焊缝内外侧手工打底,用角焊自动焊机(LT-7)焊接内外盖面焊缝,同时外部附加钢板,作为焊机运行的轨道。
其焊接顺序为:
内外侧第一道手工打底一一外侧自动焊一一拆内侧固定块及方楔子一一内侧自动焊。
环缝焊接均采用埋弧自动焊方法进行。
15nun以下壁板环缝为单V型坡口,18nun以上为X型坡口,均需要双面焊接,先焊外侧焊缝,外侧焊后,罐内侧卡具拆除,用自动碳弧气刨方法进行清根,然后用砂轮打磨,如果清根深度达到焊缝厚度的2/3,要用手工焊方法进行补焊,清理完后,进行内侧环缝焊接。
10.圈壁板的内半径按下式汁算:
Rb=(Ri+na/2an)cos0
(2)
式
(2)中Rb顶圈壁板安装内半径(min)
Ri——罐内半径
N——顶圈壁板立缝数量
a——每条立缝焊接收缩量(mm)
0——基础坡度夹角。
11•按顶圈壁板安装内半径,在罐底板上划出圆周线及每张壁板上的安装位置线,并在安装圆内侧100mm处划出检查圆线,打上样冲眼,并用口油漆做出标记。
12.圆壁板安装圆周线,每隔在内侧焊上挡板,在安装圈外侧60mm处同样焊上挡板,作为组装卡具用限位。
13•罐壁组焊完毕后其总体儿何尺寸应符合表5-6的要求。
罐体总体儿何尺寸允许偏差(mm)
表5-6
序号
检查项目
允许偏差
1
罐壁高度
0.5%H
2
罐壁垂直度
0.4H且W50mm
3
各圈壁板lm高处内半径
±13
组装顶部第一节壁板前应在安装圆的内侧捍上挡板,挡板与壁板之间加组对垫板(见下图),垫板厚度按下列公式计算:
6=n*a/2刃
式中:
6一垫板厚度(nun);
n—壁板立焊缝数;
a—每条立焊缝的收缩量(mm),手工焊取2;
B—基础坡度夹角(°);
壁板
底圈壁板安装示意图
14.在壁板上应按组装夹具及吊装夹具位置划线,在壁板组立前,在存运胎架上安装好方帽,龙门板及蝴蝶板,壁板的吊装用履带吊车进行,并使用吊梁,如上图示;
15.壁板逐张组对,每张安装三个加减丝以调节壁板垂直度。
安装纵缝组对卡具及方楔子,用以将壁板固定。
整圈壁板全部组立后调整壁板立纵缝组对错边量,上口水平度及壁板的垂直度应符合以下要求,并检查lm高处任意点半径的偏差不得超过土32mm。
16.相邻两壁板上口水平的允许偏差,不应大于2mm,在整个圆周上任意两点水平的允许偏差,不应大于6mm。
17.壁板的垂直允许偏差,不大于3nun。
18.纵向焊缝的错边量,不大于lnmio
19.环向焊缝的错边量(任意点),不大于板厚的2/10,且不大于3nun。
20•顶部第二至底圈壁板的组装方法参照顶部第一节壁板的组装。
环缝应安装组对用龙门板、槽钢。
21.组装顶部第二节壁板前在顶部第一节壁板上搭设简易脚手架,如图示,以后组对上一带板时在下带板上搭设同样的脚手架,在罐人孔处搭设斜梯,以供上下脚手架,每台罐两层脚手架循环使用,如下图示:
22.璧板应按排版图组装,壁板立缝宜用夹具组对,壁板的组对应符合下列规定:
a相邻两壁板上口水平的允许偏差,不应大于2mm,在整个圆周上任意两点水平的允许偏差,不应大于6nini。
b壁板的垂直允许偏差,不大于3nuno
c纵向焊缝的错边量,不大于lnun。
d环向焊缝的错边量(任意点),不大于板厚的2/10,且不大于3nmi。
24•在顶部第一节壁板组装、焊接完毕并经检查符合设计要求后,进行锥板的安装,安装前应先检查预制的锥板的弧度和翘曲度,符合要求后安装锥板,并应符合下列要求:
a锥板与壁板搭接时应先焊锥板的对接缝,再焊锥板与壁板内壁搭接的间断角焊缝,最后焊锥板与壁板外壁搭接的连续角焊缝;
b应保证锥板和罐壁板的安装角度,误差不得大于土5°;
c锥板自身连接必须采用全焊透的对接接头;
(3)・罐顶的组装
(1)浮顶的组装,宜在临时支架上进行。
(2)浮顶板搭接宽度允许偏差为±5nun。
(3)外边缘板的搭接宽度允许偏差为±5in】n。
3.内浮顶组装应按设汁要求执行。
(4)•附件安装;
(1)罐体的开孔接管应符合规范要求;开孔补强板的曲率,应与罐体曲率一致;开孔接法兰的密封面不应有焊瘤和疤痕,法兰的密封面应与接管的轴线垂直,且保证法兰面垂直或水平,法兰的螺栓孔应跨中安装。
(5).焊接施工
(1)凡是定位焊接及工卡具的焊接,山合格焊工担任。
其焊接工艺应与正式焊接相同。
引弧不应在母材或完成的焊道上。
(2)焊接长度不应小于30mm;焊接前应检査组装质量,清除坡口面,充分达到干净干燥无污染物。
(3)板厚大于6mm的搭接角焊缝,应至少焊两遍。
(6)・焊接顺序
(1)罐底的焊接。
应采用收缩变形最小的焊接工艺及焊接顺序,中幅板焊接时。
先焊短焊缝。
后焊长焊缝。
(2)弓形边缘板的对接焊缝采用手工焊。
先焊其外侧300mm焊缝,如右下图:
打底焊后进行渗透检查,以第二层开始每层错开50〜70mm,焊接完成,上部磨平,进
行磁粉和真空试漏检查,边缘板对接焊缝的其余部分在大角焊缝焊完后进行。
为控制焊接引起的角变形和控制外部的成形,须安装防变形龙门板,并在边缘板外部焊缝处焊接引弧块。
中幅板的焊接采用手工焊打底、埋弧自动焊盖面成型。
在焊接长缝时,采用防变形措施。
距边缘板2m范圉内焊缝暂留不焊接,在与边缘板组对后再焊接。
边缘板剩余部分对接焊缝焊接,在焊第二层环缝前将卡具拆下,进行焊接。
焊完后,切割出中幅板周边小板与底板的接缝坡口。
龟甲缝点焊时,用龙门板加背杠防止焊接变形。
龟屮缝打底焊时,分成的均匀8等份,同时焊接。
(3)罐底与罐壁连接的角焊缝,在底圈壁板纵焊缝焊完后施焊,山数对焊工从罐内、外沿同一方向进行分段焊接。
(4)罐壁的焊接,先焊纵向焊缝,后焊环向焊缝,焊工均匀分布,并沿同一方向施焊。
纵焊缝采用气体保护焊时,自下向上焊接。
(5)固定顶顶板的焊接。
先焊内侧焊缝,后焊外侧焊缝,并山中心向外分段退焊。
顶板与包边角钢焊接时,焊工应均匀分布,并沿体同一方向分段退焊。
3•焊接外观质量检查
(1)焊缝外观检查前,将熔渣飞溅清理干净。
焊缝表面及热影响区不的有裂纹、气孔、加渣和弧坑等缺陷。
(2)对接焊缝咬边深度不大于0.5mm,咬边连续长度不大于lOOnmi,每条焊缝两侧咬边的总长度不超过焊缝总长度的10%O
(3)罐壁纵向对接焊缝不得有低于母材表面的凹陷。
(4)罐壁环向对接焊缝和罐底对接焊缝低于母材表面的凹陷深度不大于0.5nun,凹陷的连续长度不超过焊缝总长度的10%O
(5)焊缝宽度为坡口宽度两侧各增加l-2mmo
b.焊缝无损检测
(1)从事焊缝无损检测人员,必须具有有关部门分颁发的与其工作范围相适应的资格证书。
(2)罐底焊缝检验应按标准及规范要求进行,真空负压严密性试验和局部无损检验的范围、比例应符合标准要求。
(3)罐壁焊缝应按焊工进行对接直缝及丁字焊缝的无损检测,检测的标准、数量及方法按相应的规范执行。
(4)罐底板与底圈壁板之间的T型焊缝应进行渗透探伤,并符合要求。
(5)开孔补强的补强板焊缝应进行气体严密性试验,并符合图纸要求。
(7)浮顶附件
顶附件包括船舱人孔、支柱、集水坑、透气阀、量油管口,呼吸阀,浮梯轨道,刮腊现场、密封系统、浮顶人孔及中央排水管等组成,先在罐外进行预制,待浮顶焊完后,先按照图纸标定的位置进行测量、放线、划出各个附件的安装位置线,开船舱人孔,然后到各个区域对照浮顶顶板上划线位置。
准确确定支柱套管,集水坑,浮顶人孔、透气阀、量油管口、呼吸阀、浮顶轨道等的位置,确定后进行上述各项的开孔,安装和焊接。
焊接后按设讣要求进行检查合格,再进行刮腊密封等附件的安装,最后进行板和浮顶挡板的安装和焊接,以及浮顶中央排水管的安装和焊接。
浮顶上面的附件安装焊接完后,再进行浮顶底板面的搭接花焊,支柱套管底面补强板和其他附件底面补强板的焊接,支柱在罐底板的安装和焊接,排水管的安装和焊接,量油管下支撑固定现场的安装和焊接。
浮顶立柱安装时,先调整其高度。
按其设计高度预留出200mm调整量,安装时由多人同时进行,可用临时架台可调整螺母调整,安装支柱,用销子固定在套管上,每根立柱都安装后,即可拆除浮顶架台,并从人孔将其导出,架台拆除后,即可进行浮顶底面各附件的安装和焊接。
浮顶支柱的再调整是在充水试验时,再放水过程中进行。
其调整方法是放水至水位比浮顶最底位置疡出300mm时停止放水,调整各个立柱的实际需要长度,调整公式为L=H-L0-H0式中:
L:
浮顶支柱销孔至柱底端部需要的实际长度(nun)。
H:
罐底至套管端部的长度(mm)
Lo:
套管端部至支柱销孔中心的距离(mm)
Ho:
测量时浮顶比设计高度高出部分(mm)
逐个支柱进行调整,全部调整完以后,再放水使浮顶座落。
浮顶排水管安装前要进行焊后正压试验,并确定预制时在罐外已进行过摸拟试验。
(8)包边角钢、盘