机械制造工艺学实验报告.docx
《机械制造工艺学实验报告.docx》由会员分享,可在线阅读,更多相关《机械制造工艺学实验报告.docx(17页珍藏版)》请在冰豆网上搜索。
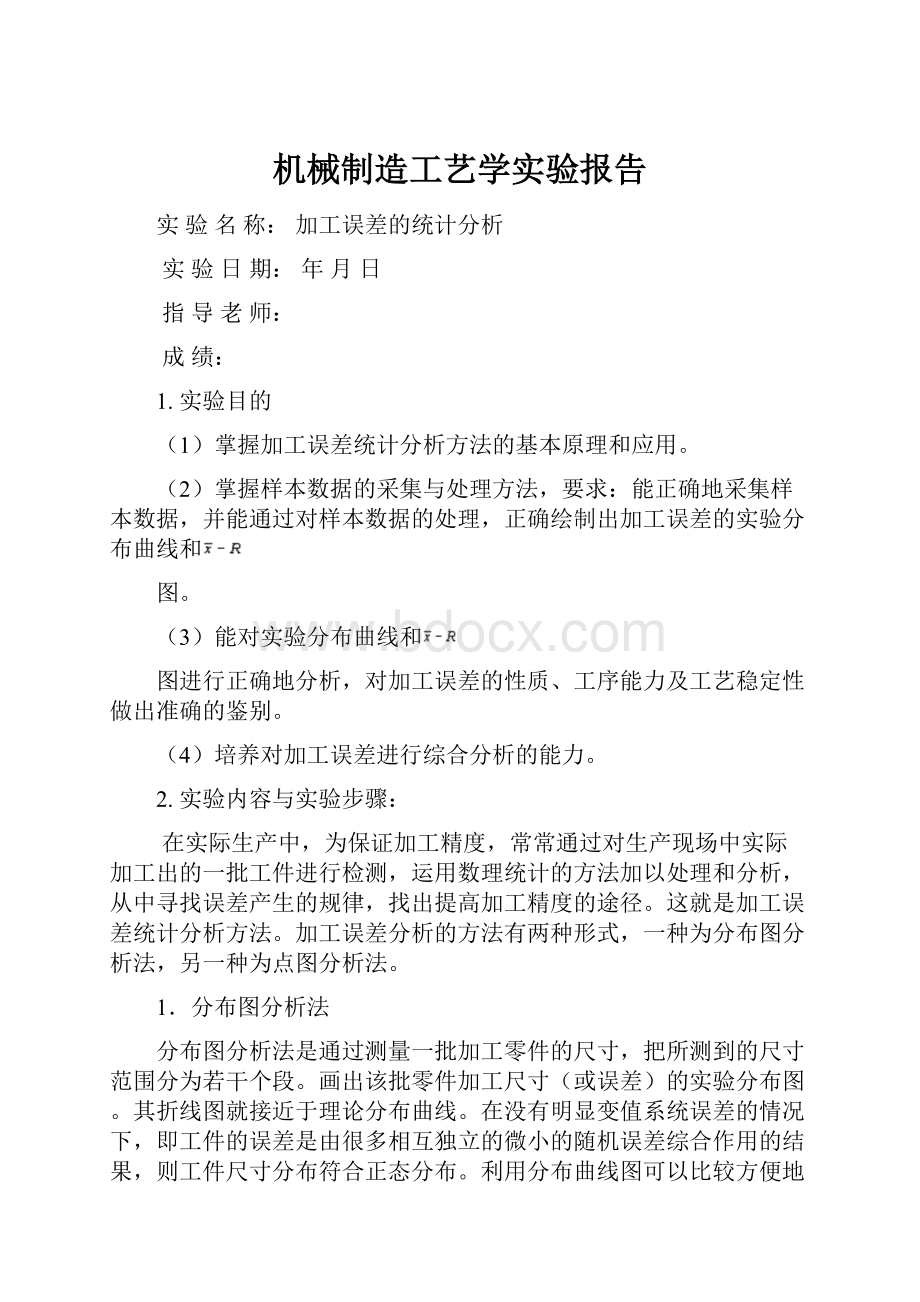
机械制造工艺学实验报告
实验名称:
加工误差的统计分析
实验日期:
年月日
指导老师:
成绩:
1.实验目的
(1)掌握加工误差统计分析方法的基本原理和应用。
(2)掌握样本数据的采集与处理方法,要求:
能正确地采集样本数据,并能通过对样本数据的处理,正确绘制出加工误差的实验分布曲线和
图。
(3)能对实验分布曲线和
图进行正确地分析,对加工误差的性质、工序能力及工艺稳定性做出准确的鉴别。
(4)培养对加工误差进行综合分析的能力。
2.实验内容与实验步骤:
在实际生产中,为保证加工精度,常常通过对生产现场中实际加工出的一批工件进行检测,运用数理统计的方法加以处理和分析,从中寻找误差产生的规律,找出提高加工精度的途径。
这就是加工误差统计分析方法。
加工误差分析的方法有两种形式,一种为分布图分析法,另一种为点图分析法。
1.分布图分析法
分布图分析法是通过测量一批加工零件的尺寸,把所测到的尺寸范围分为若干个段。
画出该批零件加工尺寸(或误差)的实验分布图。
其折线图就接近于理论分布曲线。
在没有明显变值系统误差的情况下,即工件的误差是由很多相互独立的微小的随机误差综合作用的结果,则工件尺寸分布符合正态分布。
利用分布曲线图可以比较方便地判断加工误差性质,确定工序能力,并估算合格品率,但利用分布图分析法控制加工精度,必须待一批工件全部加工完毕,测量了样本零件的尺寸后,才能绘制分布图,因此不能在加工过程中及时提供控制精度的信息,这在生产上将是很不方便的。
2.点图法
在生产中常用的另一种误差分析方法是点图法或
图法。
点图法是以顺序加工的零件序号为横坐标,零件的加工尺寸为纵坐标,把按加工顺序定期测量的工件尺寸画在点图上。
点图可以反映加工尺寸和时间的关系,可以看出尺寸变化的趋势,找出产生误差的原因。
图称为平均尺寸——极差质量控制图。
一般是在生产过程开始前,先加工一批试件(本实验中即用本批加工的零件作为试件),根据加工所得的尺寸,求出平均值
和极差R而绘制成的。
点图:
中线
上控制线
下控制线
R点图:
中线
上控制线Rs=D1
下控制线Rx=D2
是将一批工件依照加工顺序按n个分为一组第i组的平均值,共分成k组;
是第i组的极差;
式中A2、D1、D2的数值根据数理统计原理而定出(见表1)。
表1
每组件数n
A2
D1
D2
4
0.73
2.28
0
5
0.58
2.11
0
将生产中定期抽样的尺寸结果,点在
图上,从点子在图中的位置便可看出
和R的波动,它反映了工件平均值的变化趋势和随机误差的分散程度。
图上的控制界限线,就是用来判断工艺是否稳定的界限。
因此
图是用来判断工艺过程的稳定性的。
实验步骤
1.按无心磨床的操作方法,加工一批零件(本实验为100件)。
加工完的零件,擦洗干净,按加工顺序放置好。
2.按加工顺序测量工件的加工尺寸,记录测量结果。
3.绘制直方图和分布曲线
1)找出这批工件加工尺寸数据的最大值xmax和最小值xmin,按下式计算出极差R。
R=xmax一xmin
2)确定分组数K(K一般根据样本容量来选择,建议可选在8~11之间)。
3)按下式计算组距d。
4)确定组界(测量单位:
微米)。
5)做频数分布表。
6)计算
和
。
7)画直方图
以样本数据值为横坐标,标出各组组界;以各组频率密度为纵坐标,画出直方图。
8)画分布曲线
若工艺过程稳定,则误差分布曲线接近正态分布曲线;若工艺过程不稳定,则应据实际情况确定其分布曲线。
画出分布曲线,注意使分布曲线与直方图协调一致。
9)画公差带
在横轴下方画出公差带,以便与分布曲线相比较。
4.绘制
图
1)确定样组容量,对样本进行分组
样组容量m通常取4或5件。
按样组容量和加工时间顺序,将样本划分成若干个样组。
2)计算各样组的平均值和极差
对于第i个样组,其平均值和极差计算公式为:
式中
——第i个样组的平均值;
——第i个样组的标准差;
——第i个样组第j个零件的测量值;
——第i个样组数据的最大值;
——第i个样组数据的最小值
3)计算
图控制限(计算公式见实验原理)
4)绘制
图
以样组序号为横坐标,分别以各样组的平均值
和极差R为纵坐标,画出
图,并在图上标出中心线和上、下控制限。
5.按下式计算工序能力系数Cp
判别工艺过程稳定性
可按下表所列标准进行判别。
注意,同时满足表中左列3个条件,工艺过程稳定;表中右列条件之一不满足,即表示工艺过程不稳定。
表2
加工误差综合分析
通过对分布图和
图的分析,可以初步判断误差的性质。
进而结合具体加工条件,分析影响加工误差的的各种因素,必要时,可对工艺系统的误差环节进行测量和实验。
3.实验环境
设备:
无心磨床
量仪:
0~25mm数显千分尺一把
试件:
φ24(±0.01)×32的45钢(淬火)100件
4.实验过程与分析
表1-3实验数据
序号
记录数据
序号
记录数据
序号
记录数据
序号
记录数据
1
26
51
76
2
27
52
77
3
28
53
78
4
29
54
79
5
30
55
80
6
31
56
81
7
32
57
82
8
33
58
83
9
34
59
84
10
35
60
85
11
36
61
86
12
37
62
87
13
38
63
88
14
39
64
89
15
40
65
90
16
41
66
91
17
42
67
92
18
43
68
93
19
44
69
94
20
45
70
95
21
46
71
96
22
47
72
97
23
48
73
98
24
49
74
99
25
50
75
100
组
号
组界
中心值
xi
频数
mi
频率
fi
xi-
(xi-
)2
(xi-
)2mi
1
2
3
4
5
6
7
8
9
10
11
12
13
14
15
16
17
18
表1-4实际分布曲线图(直方图)
表1-5
-R控制图数据
样组号
平均值
极差
R
样组号
平均值
极差
R
样组号
平均值
极差
R
1
10
19
2
11
20
3
12
21
4
13
22
5
14
23
6
15
24
7
16
25
8
17
9
18
R
-R控制图
5.实验基本要求
1.明确实验目的、内容、条件及实验步骤,记录好实验原始数据;
2.绘制直方图和分布曲线;绘制
图;
3.计算确定加工方案的工序能力及等级,分析判别加工误差的性质,分析影响加工误差的主要因素,并估算合格品率或者不合格品率。
若有不合格品,判断为可修复还是不可修复,并对加工方案提出改进措施;
4.分析判断工艺过程是否稳定;
5.独立完成实验报告。
6.实验结果总结
1.本工序的实验分布曲线图是否接近正态分布曲线?
为什么?
2.根据工序能力系数Cp,本工序属哪一级?
如果出现了废品,试分析产生废品的原因。
(计算确定加工方案的工序能力及等级,分析判别加工误差的性质,分析影响加工误差的主要因素,并估算合格品率或者不合格品率。
若有不合格品,判断为可修复还是不可修复,并对加工方案提出改进措施)
3.从
图看,本工序的工艺过程稳定吗?
如果不稳定,试分析其原因。
7.心得体会
实验名称:
组合夹具的设计、组装与调整
实验日期:
年月日
指导教师:
成绩:
1、实验目的
(1)掌握组合夹具的特点和设计装配方法,具有按加工要求组装组合夹具并进行检测的能力。
(2)了解组合夹具的元件种类、结构与功用。
(3)掌握六点定位原理及粗、精基准选择原则。
(4)理解夹具各部分连接方法,了解夹具与机床连接及加工前的对刀方法。
(5)掌握定位方法,调整定位尺寸、消除形位误差、夹紧力的分析等。
(6)熟悉铣、钻、镗等机床夹具的特点。
2、实验内容与实验步骤
组合夹具元件及其作用
组合夹具按组装对元件间连接基面的形状不同,可分为槽系和孔系两大系统。
为了适应不同产品加工零件尺寸大小的需要,组合夹具按其尺寸大小又分为大、中、小型三个系列,见下表。
各系列中,其元件用途又可分为八大类。
在每一类元件中又分很多结构类型、品种及规格,以供组装不同夹具时搭配选用。
为了掌握组合夹具的组装技术,必须熟悉各类元件的结构特点、尺寸规格及使用方法,以便灵活运用各类元件,迅速组装出所适用的夹具来。
现以中型系列为例,介绍八大类元件的主要结构形式和基本用途。
1.基础件
它是组合夹具中最大的元件,包括各种规格尺寸的方形、矩形、圆形基础板和基础角铁等。
基础件通常作为组合夹具的基体,通过它将其他各种元件或合件组装成一套完整的夹具,图1为其中的几种结构。
图1基础件图2支承件
2.支承件
支承件是组合夹具的骨架元件。
支承件通常在组合夹具中起承上启下的作用,即把上面的其他元件通过支承件与其下面的基础件连成一体,一般各种夹具结构中都少不了它。
支承件有时可作定位元件使用,当组装小夹具时,也可作为基础件。
图2为其中的几种结构。
3.定位元件
定位件主要用于工件在夹具中的正确定位,也用于保证夹具中各元件的使用精度及其强度和刚度。
图3为其中的几种结构。
图3定位元件
4.导向件
导向件主要用来确定刀具与工件的相对应置,加工时起引导刀具的作用。
有的导向件可作定位用,也可作为组合夹具系统中移动件的导向。
图4为其中的几种结构。
图4导向件图5夹紧件
5.夹紧件
夹紧件主要用来将工件夹紧在夹具上,保证工件定位后的正确位置,也可作垫板和挡块用。
图5为其中的几种结构。
6.紧固件
紧固件主要用来连接组合夹具中各种元件及紧固工件。
由于紧固件在一定程度上影响整个夹具的刚性,因此均采用细牙螺纹,这样可使元件的连接强度好,紧固可靠。
同时所选用材料、精度、表面粗糙度及热处理均高于一般标准紧固件。
图6为其中的几种结构。
图6紧固件
7.其他件
除了上述六类元件以外的各种用途的单一元件称为其他件。
其他件中有的有明显的作用,有的常无固定的用途,但如用得合适,则能在组装中起到极为有利的辅助作用。
图7为其中的几种结构。
图7其他件
图8合件
8.合件
合件是由若干零件装配而成,并在组装过程中不拆散使用的独立部件。
按其用途可分为定位合件、导向合件、分度合件以及必需的专用工具等。
图8为其中的几种结构。
1.设计(2人一组):
(1)根据工件工序要求及结构特点,确定定位方案,画出定位简图;
(2)自行设计夹具组装方案:
构思整个夹具的总体结构,确定夹具中的基础件、支承件、定位元件、夹紧元件、对刀元件及导向元件;(3)确定各元件之间的连接及定位关系。
(4)分析定位误差的构成,计算确定夹具定位元件间允许的位置公差值。
2.试装:
根据夹具总装方案,在夹具标准件库中,找出所需元件,进行试装配,发现问题,及时更正。
3.装配:
利用工具,在指导老师指导下按正确的装配顺序,把各元件装配好,了解装配方法。
4.调整:
调整好各工作表面之间的位置。
5.检测:
按计算出的位置公差值(夹具要求),检测各工作表面之间的位置是否符合要求。
3、实验环境
1.组合夹具元件一套。
2.零件实物一件。
3.活动扳手、铜锤、起子等工具。
4.千分尺、游标卡尺、千分表、磁力表座、块规、心棒等检具。
4、实验基本要求
1.绘出零件定位夹紧简图:
5、实验结果分析与讨论
1.组合夹具与专用夹具有何不同?
2.工件在夹具中定位时,限制了几个自由度?
6.心得体会