FANUC系统特殊功能指令在数控编程中的应用.docx
《FANUC系统特殊功能指令在数控编程中的应用.docx》由会员分享,可在线阅读,更多相关《FANUC系统特殊功能指令在数控编程中的应用.docx(8页珍藏版)》请在冰豆网上搜索。
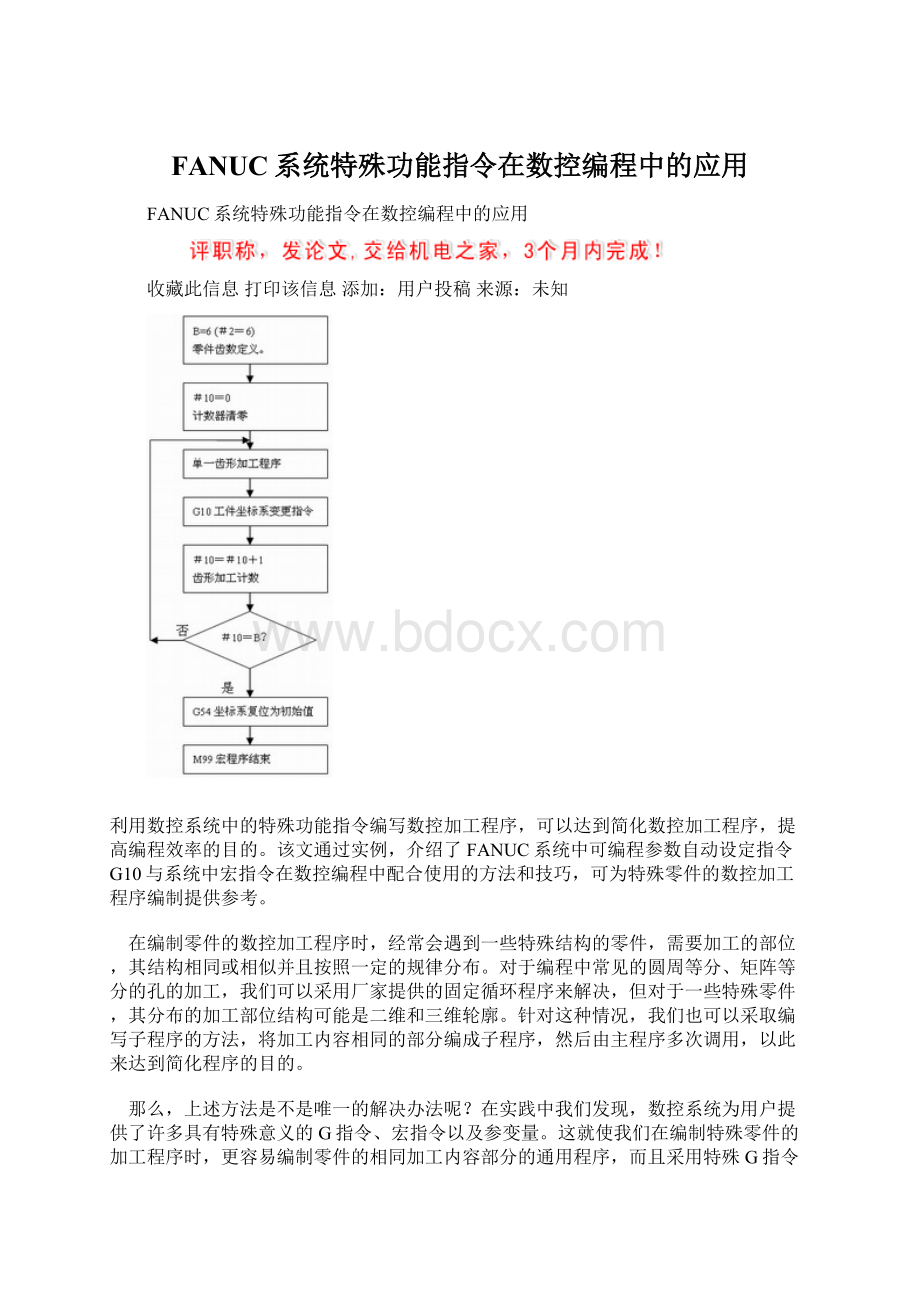
FANUC系统特殊功能指令在数控编程中的应用
FANUC系统特殊功能指令在数控编程中的应用
收藏此信息打印该信息添加:
用户投稿来源:
未知
利用数控系统中的特殊功能指令编写数控加工程序,可以达到简化数控加工程序,提高编程效率的目的。
该文通过实例,介绍了FANUC系统中可编程参数自动设定指令G10与系统中宏指令在数控编程中配合使用的方法和技巧,可为特殊零件的数控加工程序编制提供参考。
在编制零件的数控加工程序时,经常会遇到一些特殊结构的零件,需要加工的部位,其结构相同或相似并且按照一定的规律分布。
对于编程中常见的圆周等分、矩阵等分的孔的加工,我们可以采用厂家提供的固定循环程序来解决,但对于一些特殊零件,其分布的加工部位结构可能是二维和三维轮廓。
针对这种情况,我们也可以采取编写子程序的方法,将加工内容相同的部分编成子程序,然后由主程序多次调用,以此来达到简化程序的目的。
那么,上述方法是不是唯一的解决办法呢?
在实践中我们发现,数控系统为用户提供了许多具有特殊意义的G指令、宏指令以及参变量。
这就使我们在编制特殊零件的加工程序时,更容易编制零件的相同加工内容部分的通用程序,而且采用特殊G指令及宏指令、参变量编程,使数控程序更加简化,更具灵活性,如FANUC 15M系统中的可编程参数设定指令G10以及相关的宏指令等。
一、可编程参数设定指令G10及宏指令
FANUC 15M系统中的G10指令,可实现刀具几何参数的设定与编辑功能,由程序指令变更刀具加工过程中的半径补偿量。
其另一功能是在加工程序中实现工件坐标系的设定与设定值的变更。
1. G10指令变更刀具补偿量
格式:
G90/G91 G10 L 11 P R;
其中,变量 L—赋值为11,表示变更刀具补偿量方式;
P—刀具补偿号;
R—刀具的补偿量;
G90—覆盖原有补偿量;
G91—在原有补偿量的基础上累加。
在程序中通过改变R变量中的刀具半径补偿量,实现零件轮廓粗加工时调整加工余量,使用同一把刀具实现粗、精加工。
2. G10指令实现工件坐标系的设定、变更
格式:
G90/G91 G10 L2 P X Y Z;
其中,变量L—赋值为2表示变更工件坐标系方式;
P—工件坐标系,赋值1~6表示G54~G59;
X、Y、Z—工件坐标系原点坐标值;
G90—覆盖原有补偿量;
G91—在原有补偿量的基础上累加。
利用G10工件坐标系的设定、变更功能,可实现工件坐标系的设定、修改和平移。
3. 用户宏指令
(1)变量的赋值与运算
格式:
#i= #j+#k ;
FANUC系统中以“#”作为变量名,“#”后的数值为变量的下标,用来区分各变量。
“=”表示变量的赋值,“#i”为被赋值的变量,“=”右边可以是实际值或表达式。
表达式中可包含“+”、“-”、“×”、“/”运算符以及三角函数运算。
(2)无条件转移指令 GOTO
格式:
GOTO n ;
n表示转移到目的程序段的行号。
该指令将无条件转移到指定的程序段。
(3)条件转移指令IF
格式:
IF [conditional expression] GOTO n ;
“[ ]”中是一个逻辑运算式,逻辑运算功能指令有:
EQ:
“=”;NE:
“≠”;GT:
“>”;GE:
“≥”;LT:
“<”;LE:
“≤”。
在逻辑运算式中,实际值、变量、表达式均可参与逻辑运算。
n是转移目标程序段的行号。
当“[ ]”中逻辑运算式成立时,程序将转移到n所指定的程序段,否则,继续执行下一程序段。
在数控编程中,我们可以根据零件结构的特点,灵活运用数控系统中的特殊指令。
例如,将G10指令与用户宏指令配合使用,可以使零件的加工程序更加简化,达到事半功倍的效果。
程序可以缩短到原来的1/3,甚至更短。
二、应用实例分析
1. 零件特点
图1是橡胶传送带的成型模板。
齿形为曲线凹槽,横截面为梯形,齿形成直线等距排列。
初始工件坐标系设定为G54原点位置,如图1所示。
2. 程序处理
首先在初始工件坐标系G54下,编写模板零件的第一个齿形加工宏程序O7001。
在零件的加工过程中,由主程序O7000调用O7001宏程序。
第一个齿形加工完成后,利用可编程参数设定指令G10的工件坐标系变更功能,在加工其他齿形时通过变更初始工件坐标系G54的设定值,使工件坐标系按齿形排列间距产生平移,为下一齿形的加工重新自动设定工件坐标系。
程序执行框图如图2所示。
宏程序O7001中利用系统宏指令的参数计算以及判断循环功能,通过多次循环执行,将各齿形依次加工完成。
下面是具体加工程序。
O7000
(T-XING CHUAN SONG DAI)
(KMC-4000SV)
G00 G90 G80 G49 G53 Z0
N10 T25 M06 (ENDMILL D=25MM)
G00 G90 G54 X812.554 Y-330.85 S220 M03
G43 Z20. H25
G65 P7001 B=6
GOO G49 G53 Z0 M05
T0 M06
M30
O7001
(MACRO)
#10=0
N20 G00 G90 G54 X812.554 Y-330.85
Z5.
G01 Z-20.2 F40
X618.961
G02 X600.095 Y-323.983 I0 J29.35
G01 X494.334 Y-235.239
G00 Z75.
X454.5 Y-201.815
Z5.
G01 Z-20.2
X312.265 Y-82.465
G02 X312.265 Y82.465 I69.196 J82.465
G01 X454.5 Y201.815
G00 Z75.
X494.334 Y235.239
Z5.
G01 Z-20.2
X600.095 Y323.983
G02 X618.961 Y330.85 I18.866 J-22.483
G01 X812.554
G00 Z75.
X273.811 Y0
Z5.
G01 Z-20.2
X0
G00 Z75.
X275.449 Y18.713
Z5.
G01 Z-20.2
G02 X253.144 Y0 I-22.305 J3.937
G02 X275.449 Y-18.713 I0 J-22.65
G00 Z100.
G91 G10 L2 P1 X454.5 Y0 Z0
#10=#10+1
IF [#10 EQ #2] GOTO 100
GOTO 20
N100 G90 G10 L2 P1 X-1583.75 Y-560.03 Z-683.7 (初始工件坐标系设定值)
M99
图2 宏程序O7001执行框图
三、结束语
采用可编程的参数设定指令G10,通过编程的方式更改刀具补偿量、根据需要重新设定工件坐标系,使工件坐标系可在任意方向上移动。
将该指令与宏指令配合使用,增强了零件加工程序的逻辑性和灵活性,进一步扩展了数控系统的功能。
零件加工程序大幅度简化,提高了编程效率,降低了编程差错率。
在数控程序中采用特殊功能指令及参变量,为解决一些特殊及复杂零件的加工程序编制问题打开了思路。
高速加工的数控编程问题与技巧探讨
收藏此信息打印该信息添加:
用户投稿来源:
未知
高速加工作为高效率的加工手段之一,在目前的制造业中得到了广泛的应用。
高速加工从上世纪末进入实用化阶段以后,在国内的制造业中立即得到了响应,初始阶段我们的工程技术人员对于此类加工设备和编程手段很陌生,因此在实际应用中遇到了很多问题。
截止目前,此类加工手段还远远没有被广大工程技术人员熟悉和掌握,这一点从目前的媒体和网上论坛中的反映就可以看得出来。
这里就高速加工中的一些问题和技巧进行一些探讨,希望能给大家带来一些启发和帮助。
高速加工包含了两层含义,一是高主轴转数,一般情况下主轴转数至少在12000转/分,目前最高可达60000转/分(Mikron可提供此类设备)。
二是高速进给,进给速度一般在每分几米甚至几十米,由于机床设备、切削刀具的正常工作状态与普通加工有很大的差异,因此在编写数控加工程序和工艺流程的时候就不能再沿用老一套的思路。
在高速加工过程中,由于进给速度很大,机床主轴(或工作台等运动部件)的惯性就成为不能忽略的一个要素,在机床设计和控制系统的选配过程中都要充分的予以考虑。
作为一个面向市场的成功产品,该类设备在设计制造过程中肯定在这方面作了很多的改进。
不过千万不要认为,惯性问题就此彻底解决了。
在使用过程中,使用者时刻都要考虑到这个因素,否则使用不当,不仅会缩短现有的高速加工设备的使用寿命,还会对您生产的产品质量产生影响。
机床的设计和制造过程如何改进的问题我们不在这里探讨,我们这里关注的是使用过程中的注意事项。
为避免高速加工过程中机床惯性的影响,理论上只要我们在切削过程中尽量减少在加工过程中改变进给方向就可以了,但是实际上确实不可能实现的,改变进给方向不可避免的经常使用,这时我们要尽量在空走刀的时候换向,不在刀具处于切削状态的时候改变方向;或则改变进给方向之前降低进给速度;这就给我们编写加工程序提了一个难题,这时可以选用合适的CAM软件来完成编程工作。
例如图2中的例子,我们选择螺旋线的方式进行铣切,其效果要比图1中的传统铣切方式效果要好的多。
尽量选择刀具未处于切削状态的时候改变进给方向。
例如下面两个例子:
图3:
利用圆弧导出(导入)使切削方向改变时刀具处于非切削状态:
图4:
刀具完全导出的时候改变切削方向
在加工型腔等特殊的形状时,由于刀具没有办法导出,在编程时,转角部分尽量采用圆弧过渡,以便使转向变的尽量平稳,如果能够在转角的时候适当的降低进给速度,那么效果会更好。
高速加工中,还要注意切削深度的控制,这里有两个层面需要注意,一个是刀具的轴向切削深度,一个是刀具径向的切削深度。
切削深度的控制对于能否加工出一个漂亮的零件以及延长刀具的使用寿命起到了非常关键的作用。
目前大多数使用者习惯于在精加工的时候使用高速加工,其实粗加工的时候使用高速切削可以更快的剔除加工余量,也应该推广使用;一般情况下,在粗加工过程中,使用轴向小切深,多次分层切削剔出加工余量是最常用的加工办法;在精加工过程中,小余量高速切削可以得到很好的表面加工质量,这主要是针于模具制造过程中的精加工而言,不能绝对的照搬,例如在精加工长缘条的时候,我们要考虑到加工变形的影响,如果此时选择小余量的精加工办法,就会加大缘条变形的影响。
此时我们一般采用大余量分层切削的方法来减小缘条中间变形的影响。
也就是说粗加工时多保留一些余量,而不是习惯上的保留较少余量进行精加工;(常规上加工此类细长缘条时,一般情况下宽度与深度比达到1:
5时,加工到缘条中间部分缘条不变形已经很不容易了,如果采用高速加工,达到1:
10却很轻松)如下图:
图5高速加工中大余量分层切削精加工缘条示例
高速加工中刀具的选择是非常重要的,目前的刀具供应商几乎都可以提供适合高速加工的刀具,选择刀具主要有以下两个方面考虑,一个是高速旋转下刀具的动平衡状态,另一个就是刀具的有效切削时间(即刀具寿命)。
为保证高速旋转状态下的刀具能够绕轴线稳定旋转,目前采用两种办法,一是采用带有动平衡装置的刀具,刀套里面安装了机械划块或采用流体动平衡设计;另外一种就是采用整体刀具,刀套与刀体合为一体,其实目的就是保证刀体与刀套安装过程中减小安装间隙,整体刀具这方面是最理想的,但是由于刀具的刀套和刀体是一体的,一旦刀体报废,刀套也就一起报废了,因此费用较高。
采用热胀冷缩的办法装夹刀具,也可以得到很好的效果,即将刀套通过加热装置加热后,再装入刀体的方法,待冷却后即可加紧刀具。
高速加工过程中,刀具的磨损要比低速状态大很多,因此刀具的寿命也是影响高速加工广泛应用的一个原因,使用高速加工的时候,应该根据工厂自身的实际情况找到一个降低成本与提高效率的平衡点才能真正的体现出高速加工的价值。
是否选用高速加工,不能盲目的跟风,其实并不见得所有的行业都适合采用这种加工手段,高速加工固然可以提高加工效率,但是由于设备、刀具的成本也相应的提高,因此找到一个提高效率和降低成本的平衡点尤其重要。
高速加工不仅可以提高加工效率,还可以克服低速加工中遇到的一些工艺难题。
例如,零件在加工过程中存在变形,在工程应用中是一个很令人头痛的问题,利用普通的加工方法,往往不能得到理想的结果,此时可以考虑采用高速加工的办法来解决。
首先,在高速切削过程中产生的切削热有90%被切屑带走,而不是传导到工件中,这样可以大大的减小由于切削热传入工件,使工件产生热变形。
其次,在上面的例子中可以看到,在加工长缘条过程中,如果采用小切深分层加工的办法,可以减小径向切削力对工件的影响,从而减小工件变形。
另外,高速加工还有一个公认的好处,就是加工后的表面质量很好。
如果为达到某些工艺要求而采用高速加工的时候,成本因素就显得不那么重要了。
总之,是否采用高速加工,采用高速加工的比例要根据工厂的自身情况来决定。
高效率的加工手段目前除了高速加工之外,大切深的强力切削其实也是一种有效的手段。
在高速加工没有实用化之前,人们在这方面已经作了很多的研究和探讨,目前高速小切深加工比较流行,但是大切深强力切削也没有被遗忘。
也许有一天还会重新被人们关注,原因就是不同的行业特点和加工内容有着不同的追求目标。