基于solidworks的ca6140机床后托架加工工艺及镗孔夹具设计.docx
《基于solidworks的ca6140机床后托架加工工艺及镗孔夹具设计.docx》由会员分享,可在线阅读,更多相关《基于solidworks的ca6140机床后托架加工工艺及镗孔夹具设计.docx(21页珍藏版)》请在冰豆网上搜索。
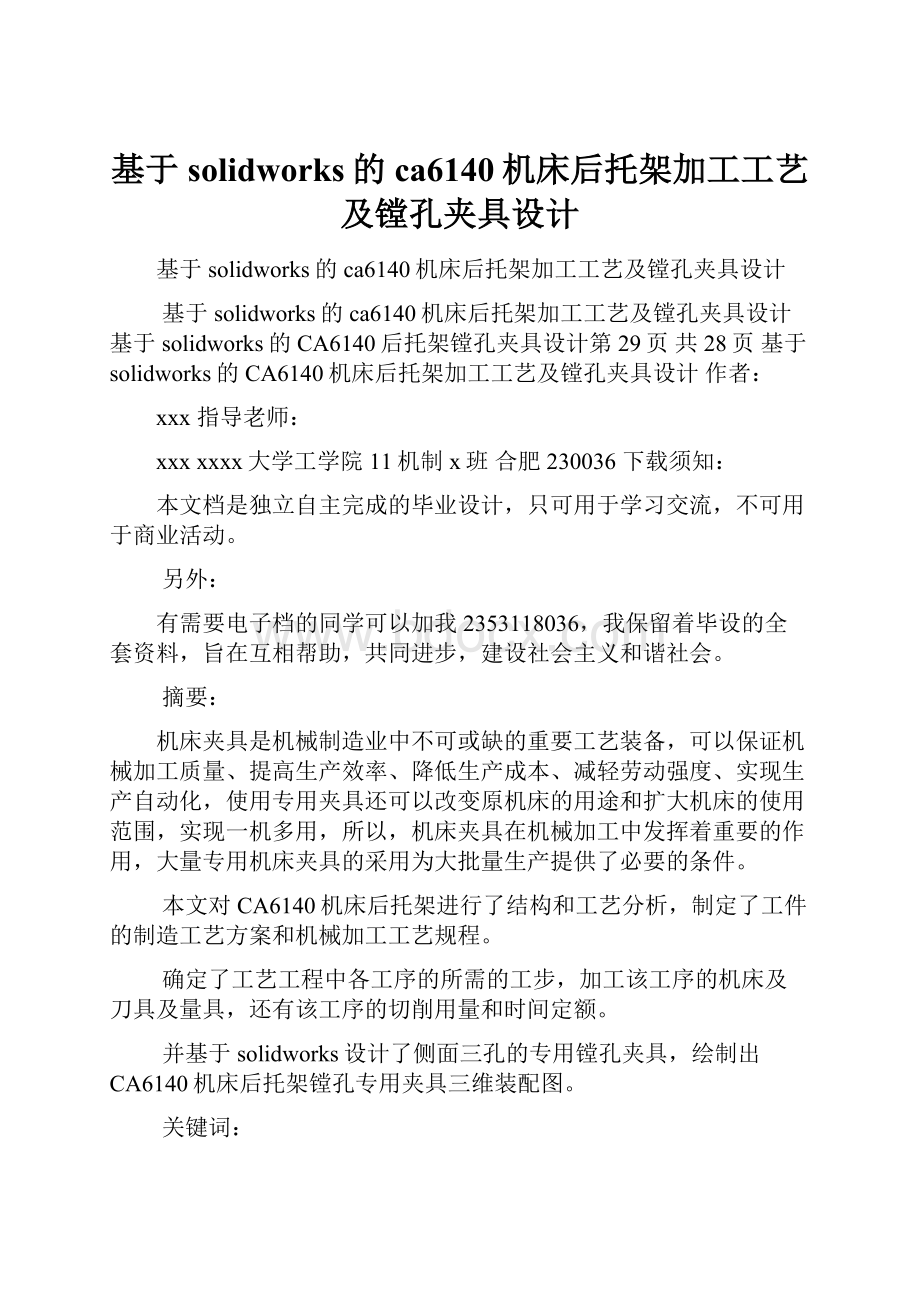
基于solidworks的ca6140机床后托架加工工艺及镗孔夹具设计
基于solidworks的ca6140机床后托架加工工艺及镗孔夹具设计
基于solidworks的ca6140机床后托架加工工艺及镗孔夹具设计基于solidworks的CA6140后托架镗孔夹具设计第29页共28页基于solidworks的CA6140机床后托架加工工艺及镗孔夹具设计作者:
xxx指导老师:
xxxxxxx大学工学院11机制x班合肥230036下载须知:
本文档是独立自主完成的毕业设计,只可用于学习交流,不可用于商业活动。
另外:
有需要电子档的同学可以加我2353118036,我保留着毕设的全套资料,旨在互相帮助,共同进步,建设社会主义和谐社会。
摘要:
机床夹具是机械制造业中不可或缺的重要工艺装备,可以保证机械加工质量、提高生产效率、降低生产成本、减轻劳动强度、实现生产自动化,使用专用夹具还可以改变原机床的用途和扩大机床的使用范围,实现一机多用,所以,机床夹具在机械加工中发挥着重要的作用,大量专用机床夹具的采用为大批量生产提供了必要的条件。
本文对CA6140机床后托架进行了结构和工艺分析,制定了工件的制造工艺方案和机械加工工艺规程。
确定了工艺工程中各工序的所需的工步,加工该工序的机床及刀具及量具,还有该工序的切削用量和时间定额。
并基于solidworks设计了侧面三孔的专用镗孔夹具,绘制出CA6140机床后托架镗孔专用夹具三维装配图。
关键词:
后托架机床夹具加工工艺定位基准solidworks1引言1.1机械加工工艺的现状与发展从国内外机械制造工艺的技术水平来看发展较迅速,出现了很多新型的加工工艺技术。
如制造自动化:
(1)在形式方面,制造自动化有三个方面的含义:
代替人的体力劳动;代替或辅助人的脑力劳动;制造系统中人机及整个系统的协调、管理、控制和优化。
(2)在功能方面,制造自动化代替人的体力劳动或脑力劳动仅仅是制造自动化功能目标体系的一部分。
制造自动化的功能目标是多方面的,已形成一个有机体系。
(3)在范围方面,制造自动化不仅涉及到具体生产制造过程,而是涉及产品生命周期所有过程。
近年来,机械制造工艺有着飞速的发展。
比如,应用人工智能选择零件的工艺规程。
因为特种加工的微观物理过程非常复杂,往往涉及电磁场、热力学、流体力学、电化学等诸多领域,其加工机理的理论研究极其困难,通常很难用简单的解析式来表达。
近年来,虽然各国学者采用各种理论对不同的特种加工技术进行了深入的研究,并取得了卓越的理论成就,但离定量的实际应用尚有一定的距离。
然而釆用每一种特种加工方法所获得的加工精度和表面质量与加工条件参数间都有其规律。
因此,目前常采用研究传统切削加工机理的实验统计方法来了解特种加工的工艺规律,以便实际应用,但还缺乏系统性[1]。
受其限制,目前特种加工的工艺参数只能凭经验选取,还难以实现最优化和自动化,例如:
电火花成形电极的沉入式加工工艺,它在占电火花成形机床总数95%以上的非数控电火花成形加工机床和较大尺寸的模具型腔加工中得到广泛应用。
虽然已有学者对其CAD、CAPP和CAM原理幵展了一些研究,并取得了一些成果,但由于工艺数据的缺乏,仍未有成熟的商品化的CAD/CAM系统问世。
通常只能采用手工的方法或部分借助于CAD造型、部分生成复杂电极的三维型面数据。
随着模糊数学、神经元网络及专家系统等多种人工智能技术的成熟发展,人们开始尝试利用这一技术来建立加工效果和加工条件之间的定量化的精度、效率、经济性等实验模型,并得到了初步的成果。
因此,通过实验建模,将典型加工实例和加工经验作为知识存储起来,建立描述特种加工工艺规律的可扩展性开放系统的条件己经成熟。
并为进一步开展特种加工加工工艺过程的计算机模拟,应用人工智能选择零件的工艺规程和虚拟加工奠定基础[2]。
1.2CA6140机床后托架夹具设计任务分析为了能具体确切的说明过程,使工件能按照零件图的技术要求加工出来,就得制定复杂的机械加工工艺规程来作为生产的指导性技术文件,学习研究制定机械加工工艺规程并基于solidworks设计绘制专用夹具就是本课题研究目的。
(1)我们必须仔细了解后托架零件结构,认真分析其零件图,培养我们独立识图能力,增强我们对零件图的认识和了解,通过对夹具零件的绘制,增强我们的solidworks建模能力和AutoCAD绘图能力。
(2)制订工艺规程、确定加工余量、工艺尺寸计算、工时定额计算、定位误差分析等。
在整个设计中也是非常重要的,通过这些设计,不仅让我们更为全面地了解零件的加工过程、加工尺寸的确定,而且让我们知道工艺路线和加工余量的确定,必须与工厂实际的机床相适应。
这对以前学习过的知识的复习,也是以后工作的一个铺垫。
(3)在这个设计过程中,我们还必须考虑工件的安装和夹紧.安装的正确与否直接影响工件加工精度,安装是否方便和迅速,又会影响辅助时间的长短,从而影响生产率,夹具是加工工件时,为完成某道工序,用来正确迅速安装工件的装置.它对保证加工精度、提高生产率和减轻工韧动量有很大作用。
这是整个设计的重点,也是一个难点。
2CA6140机床后托架加工工艺的制订2.1CA6140机床后托架的工艺分析2.1.1CA6140机床后托架的用途后托架在CA6140车床床身的尾部,三个孔分别装丝杠、光杆、转向开关,作用是加强固定;在∅40mm和∅30mm之间的孔为毛隙孔,其作用为导通油路,旁路的螺纹孔用来连接油盖;正面的四个孔将后托架固定在车床尾部。
2.1.2CA6140机床后托架的技术要求机床后托架零件图由零件图可知,CA6140机床后托架的主要加工要求是加工孔和底平面,其特点和技术要求如下:
①底平面为主要加工表面,底面采用铣削加工,其底面粗糙度要求为Ra1.6,平面度要求是0.03;②侧面三个孔,分别是∅40mm、∅30.2mm、∅25.5mm,内表面粗糙度要求是Ra1.6,加工精等级分别为IT7、IT7以及IT7~IT8,且以底平面为基准,要求平行度为100:
0.07;孔25.5mm一侧面锪平42,表面粗糙度要求是Ra6.3;③顶面的四个孔,分别是2—∅13和2—∅20为一组的阶梯孔这组孔的表面粗糙度要求是Rz50,Ra6.3,以及2—∅10的装配绞孔,其中∅13的孔的表面粗糙度要求是Ra1.6;④其余未注要求表面为不去除材料。
2.1.3CA6140机床后托架的工艺性CA6140机床后托架的是CA6140车床的一个重要零件,因为其零件尺寸较小,结构形状也不是很复杂,但侧面三杠孔和底面的精度要求较高,此外还有顶面的四孔要求加工,但是对精度要求不是很高。
后托架上的底面和侧面三杠孔的粗糙度要求都是Ra1.6,所以都要求精加工。
其三杠孔的中心线和底平面有平面度的公差要求等。
因为其尺寸精度、几何形状精度和相互位置精度,以及各表面的表面质量均影响机器或部件的装配质量,进而影响其性能与工作寿命,因此它的加工是非常关键和重要的。
2.2确定毛坯种类和制造方法2.2.1材料的工艺性能CA6140机床后托架的材料是灰铸铁(HT150),灰铸铁属于脆性材料,抗拉强度和弹性模量均比钢低,塑性和韧性接近零,硬度HB为150~200。
因为灰铸铁的显微组织有金属基体(珠光体)和片状石墨组成,石墨的强度、硬度、塑性极低,对金属基体起着割裂的作用,减少了承载的有效面积,石墨的尖角处还会引起应力集中。
因此,使石墨片得到细化,并改善石墨片的分布,可提高铸铁的性能。
可采用石墨化退火,来消除铸铁表层和壁厚较薄的部位可能出现的白口组织(有大量的渗碳体出现),以便于切削加工。
2.2.2毛坯的结构工艺要求CA6140机床后托架的材料是灰铸铁,生产类型为中批量生产,故采用铸造毛坯。
其结构工艺要求:
①铸件的壁厚应合适、均匀、不得有突然变化;②铸造圆角要适当,不得有尖角;③铸件结构要尽量简化,并要有合理的起模斜度,以减少分型面、芯子便于起模;④加强筋的厚度和分布要合理,以免冷却是铸件变形或产生裂纹。
2.3拟定工艺路线2.3.1定位基准的选择定位基准的选择在最初的工序中是铸造、锻造或轧制等得到的表面,这种未经加工的基准称为粗基准。
用粗基准定位加工出光洁的表面以后,就应该用加工过的表面做以后工序的定位表面。
加工过的基准称为精基准。
为了便于装夹和易于获得所需的加工精度,在工件上特意作出的定位表面称为辅助基准。
粗基准的选择:
(1)保证相互位置要求原则如果必须首先保证工件上加工表面与不加工表面之间的位置要求,应以不加工表面作为粗基准。
如果在工件上有很多不需加工的表面,则应以其中与加工面的位置精度要求较高的表面作为粗基准。
(2)保证加工表面加工余量合理分配的原则如果必须首先保证工件某重要表面的余量均匀,应选择该表面作为粗基准。
(3)便于工件装夹的原则选作粗基准时,必须考虑定位准确,夹紧可靠以及夹具结构简单、操作方便等问题。
为了保证定位准确,夹紧可靠,要求选用粗基准尽可能平整、光洁和有足够大的尺寸,不允许有锻造飞边、铸造浇、冒口或其他缺陷。
(4)基准一般不得重复使用的原则如果能使用精基准定位,则粗基准一般不应被重复使用。
这是因为若毛坯的定位面很粗糙,在两次装夹中使用同一粗基准,就会造成相当大的定位误差。
选择粗基准时,考虑的重点是如何保证各加工表面有足够的余量,使不加工表面与加工表面间的尺寸、位置符合图纸要求。
要从保证孔与孔、孔与平面、平面与平面之间的位置,能保证CA6140机床后托架在整个加工过程中基本上都能用统一的基准定位。
从CA6140机床后托架零件图分析可知,选择侧面三孔作为CA6140机床后托架加工粗基准。
精基准的选择原則
(1)基准重合原则应尽可能选择被加工表面的设计基准为精基准,以免产生基准不重合误差,增大加工难度。
(2)同一基准原则当工件以某一精基准定位,可以较方便地加工大多数其他表面,则应尽早地把这个基准面加工出来,并达到一定精度,以后工序以它为精基准加工其他表面。
采用统一基准原则,可以减少工件搬动和翻转次数,在自动化生产中有广泛的应用。
(3)自为基准原则旨在减小表面粗糙度,减小加工余量和保证加工余量均匀的工序,常以加工面本身为基准进行加工。
(4)互为基准原则某些位置度要求很高的表面,常采用互为基准反复加工的办法来达到位置度要求。
(5)便于装夹原则所选的精度基准,应能保证定位准确、可靠,夹紧机构简单,操作方便。
选择精基准时要考虑的主要问题是如何保证设计技术要求的实现以及装夹准确、可靠、方便。
从CA6140机床后托架零件图分析可知,它的底平面与侧面三孔平行而且占有的面积较大,适于作精基准使用。
但用一个平面定位仅仅能限制工件的三个自由度,如果使用典型的一面两孔定位方法,则可以满足整个加工过程中基本上都采用统一的基准定位的要求。
至于两侧面,因为是非加工表面,所以也可以用与顶平面的四孔的加工基准。
2.3.2表面加工方法的选择工件上的加工表面往往需要通过粗加工、半精加工、精加工等才能够逐步达到质量要求。
加工方法的选择一般应根据每个表面的精度要求,先选择能够保证该加工要求的最终加工方法,然后再选择前面一系列预备工序的加工办法和顺序。
平面的加工由参考文献[3]《机械加工工艺手册》表1-11确定,底面平面的加工方案应选择:
粗铣——精铣,粗糙度为6.3~1.6,一般未淬硬的平面,加工经济精度等级为:
IT7~IT9。
侧面孔的加工由参考文献[3]《机械加工工艺手册》表1-10确定,侧孔的加工方案选择:
粗镗——半精镗——精镗,粗糙度为1.6~0.8,毛坯有铸出孔或锻出孔,加工精度等级为:
IT7~IT9。
顶面的四个孔的加工因为孔的表面粗糙度的要求都不高,是Rz50,所以我们采用一次钻孔的加工方法,2—∅13的孔选择的加工方法是钻,因为2—∅20的孔和2—∅13是一组阶梯孔,所以可以在已经钻了2—∅13的孔基础上再锪孔钻锪到2—∅20,而另一组2—∅10和2—∅13是一组锥孔,其表面粗糙度的要求是Ra1.6,所以加工的方法是钻——扩——铰。
2.3.3加工工艺方案对于大批量生产的零件,一般总是首先加工出统一的基准。
CA6140机床后托架的加工的第一个工序也就是加工统一的基准。
具体安排是先以孔定位粗、精加工顶平面。
后续工序安排应当遵循粗精分开和先面后孔的原则。
在保证零件尺寸公差、形位公差及表面粗糙度等技术条件下,成批量生产可以考虑采用专用机床,以便提高生产率。
但同时考虑到经济效果,降低生产成本,拟订两个加工工艺路线方案。
加工工艺路线方案工序号方案Ι方案Ⅱ工序内容定位基准工序内容定位基准01粗、精铣底平面A侧面和外圆粗、精铣底平面A侧面和外圆02粗镗孔:
∅40、∅30.2、∅25.5底面和侧面钻孔:
2—∅10、2—∅13底面和侧面03半精镗孔:
∅40、∅30.2、∅25.5底面和侧面锪钻孔:
2—∅20底面和侧面04精镗孔:
∅40、∅30.2、∅25.5底面和侧面扩孔:
2—∅10底面和侧面05粗铣油槽底面和侧面精绞锥孔:
∅10底面和侧面06锪平面:
∅42底面和侧面粗镗孔:
∅40、∅30.2、∅25.5底面和侧面07钻孔:
2—∅10、2—∅13底面和侧面半精镗孔:
∅40、∅30.2、∅25.5底面和侧面08锪钻孔:
2—∅20底面和侧面精镗孔:
∅40、∅30.2、∅25.5底面和侧面09扩孔:
2—∅10底面和侧面粗铣油槽底面和侧面10精绞锥孔:
∅10底面和侧面锪平面:
∅42底面和侧面11钻孔:
∅6、M6底面和孔∅25.5钻孔:
∅6、M6底面和孔25.512攻螺纹M6底面和孔∅25.5攻螺纹M6底面和孔25.513倒角、去毛刺倒角、去毛刺14检查入库检查入库2.3.4工艺方案的比较与分析⑴上面两种方案都是以侧面和外圆面为粗基准,先加工底平面A,然后再以加工后的底平面A面为精基准加工孔,这样做满足零件加工先面后孔的加工要求;⑵方案Ⅰ先加工有严格形位要求和配合精度的∅40mm、∅30.2mm、∅25.5mm孔,再加工其他孔;方案Ⅱ先加工繁琐小而杂的孔,最后才加工有严格形位要求和配合精度的∅40mm、∅30.2mm、∅25.5mm孔;两相比较方案二更能够保证孔的位置要求35±0.07mm和63±0.05,以及∅40mm、∅30.2mm、∅25.5mm孔与A面的平行度,更好的减少加工误差,更能保证位置精度和配合精度。
由以上分析:
方案Ⅰ为合理、经济的加工工艺路线方案。
具体工艺过程如下:
CA6140机床后托架加工工序流程零件名称材料CA6140机床后托架HT150工序号工序名称及内容机床名称和型号工装夹具量具01金属型铸造02除去浇冒口,锋边及型砂03退火处理04检查毛坯05粗、精铣底平面A双立轴圆工作台铣床X25K底平面铣夹具(0~200)0.02mm游标卡尺、百分表06粗镗孔:
∅40、∅30.2、∅25.5卧式镗床TX611A侧面孔镗孔夹具(0~200)0.02mm游标卡尺07半精镗孔:
∅40、∅30.2、∅25.5卧式镗床TX611A侧面孔镗孔夹具(0~200)0.02mm游标卡尺、百分表08精镗孔:
∅40、∅30.2、∅25.5卧式镗床TX611A侧面孔镗孔夹具(0~200)0.02mm游标卡尺、百分表09粗铣油槽双立轴圆工作台铣床X25K侧面孔铣夹具10钻孔:
2—∅10、2—∅13立式钻床Z525顶面钻孔夹具(0~200)0.02mm游标卡尺11锪钻孔:
2—∅20立式钻床Z525顶面钻孔夹具(0~200)0.02mm游标卡尺、百分表12扩孔:
2—∅10立式钻床Z525顶面钻孔夹具(0~200)0.02mm游标卡尺13精绞锥孔:
∅10立式钻床Z525顶面钻孔夹具(0~200)0.02mm游标卡尺、百分表14去毛刺台虎钳15钻孔:
∅6、M6立式钻床Z525侧面钻孔夹具(0~200)0.02mm游标卡尺16攻螺纹M6组合攻丝机侧面钻孔夹具17倒角、去毛刺台虎钳18检查入库2.4确定毛坯尺寸、绘制毛坯简图零件为大批量生产,采用精度较高的金属型铸造,查参考文献[4]《机械制造技术基础课程设计指导教程》表2—1知毛坯加工余量等级为E,由表2—3知毛坯尺寸等级为CT8。
2.4.1机械加工余量和工序尺寸的确定⑴底平面A加工余量与工序尺寸计算根据工序设计要求,底平面加工方案为粗铣——精铣。
粗铣加工:
由参考文献[5]《机械加工余量与公差手册》表2—24查得其余量值规定为2.0~2.7,现取2.5;由表2—27知粗铣平面的精度等级为IT12~IT13,厚度偏差为-0.21~-0.33。
精铣加工:
由参考文献[5]《机械加工余量与公差手册》表2—25查得其余量值规定为1.0;由表2—27知精铣平面的精度等级为IT8~IT9。
底平面与侧面孔∅40、∅30.2、∅25.5中心线的的尺寸为35±0.07,粗、精铣底平面各工序基本尺寸为:
精铣:
35±0.07mm粗铣:
36-0.210mm毛坯尺寸:
38.5±0.55mm⑵侧面三孔的加工余量与工序尺寸计算毛坯预先铸造出侧面三个孔,根据工序设计要求,侧面三个孔的加工方案为粗镗——半精镗——精镗。
由参考文献[5]《机械加工余量与公差手册》表2—22查得各工序尺寸为:
孔∅40mm:
粗镗基本尺寸:
d1=38.0mm工序精度等级IT12,尺寸偏差为0.25mm;半精镗基本尺寸:
d2=39.7mm,工序精度等级IT10,尺寸偏差为0.1mm;精镗基本尺寸:
d3=40mm:
,工序精度等级IT7,尺寸偏差为0.025mm;各工序的加工余量分别为:
精镗:
Z精=(40—39.7)mm=0.3mm;半精镗:
Z半精=(39.7—38)mm=1.7mm;粗镗:
Z粗=(4—0.3—1.7)mm=2mm;各工序尺寸为:
精镗:
400+0.025mm半精镗:
39.70+0.01mm粗镗:
380+0.25mm毛坯尺寸:
36±0.45mm孔∅30.2mm:
粗镗基本尺寸:
d1=28.2mm工序精度等级IT12,尺寸偏差为0.21mm;半精镗基本尺寸:
d2=29.8mm,工序精度等级IT10,尺寸偏差为0.084mm;精镗基本尺寸:
d3=30.2mm:
,工序精度等级IT7,尺寸偏差为0.021mm;各工序的加工余量分别为:
精镗:
Z精=(30.2—29.8)mm=0.4mm;半精镗:
Z半精=(29.8—28.2)mm=1.6mm;粗镗:
Z粗=(4—0.4—1.6)mm=2mm;各工序尺寸为:
精镗:
30.20+0.021mm半精镗:
29.80+0.084mm粗镗:
28.20+0.21mm毛坯尺寸:
26.2±0.45mm孔∅25.5mm:
粗镗基本尺寸:
d1=23.5.mm,工序精度等级IT12,尺寸偏差为0.21mm;半精镗基本尺寸:
d2=25.0mm,工序精度等级IT10,尺寸偏差为0.084mm;精镗基本尺寸:
d3=25.5mm,工序精度等级IT7,尺寸偏差为0.021mm;各工序的加工余量分别为:
精镗:
Z精=(25.5—25)mm=0.5mm;半精镗:
Z半精=(25—23.5)mm=1.5mm;粗镗:
Z粗=(4—0.5—1.5)mm=2mm;各工序尺寸为:
精镗:
25.50+0.021mm半精镗:
250+0.084mm粗镗:
23.50+0.21mm毛坯尺寸:
21.5±0.45mm⑶顶面两组2—∅13和2—∅20,以及另外一组2—∅10和2—∅13的锥孔毛坯为实心,不冲孔。
两孔精度要求为,表面粗糙度要求为。
参照参考文献[5]《机械加工余量与公差手册》表2.3-47,表2.3-48。
确定工序尺寸及加工余量为:
第一组:
2—∅13和2—∅20加工该组孔的加工方案是:
钻——锪钻孔:
∅13锪孔:
∅20第二组:
2—∅10和2—∅13的锥孔加工该组孔的工艺是:
钻——扩——铰钻孔:
∅10扩孔:
∅13铰孔:
∅102.4.2毛坯尺寸图CA6140后托架毛坯图2.5切削用量的选择和时间定额的计算2.5.1确定切削用量一、工序1——粗、精底平面A根据参考文献[3]《机械加工工艺手册》表3—31和表4—15查得:
选用机床:
立式铣床X52K主轴转速30~1500r/min铣刀刀具:
嵌齿套式面铣刀材料:
高速钢外径D=80mm齿数Z=101粗铣取背吃刀量=2.5mm;切削宽度=60mm;根据参考文献[3]《机械加工工艺手册》表5—5知,粗铣每齿进给量=0.18mm;根据参考文献[3]《机械加工工艺手册》表5—11知,高速钢面铣刀铣削速度v=71.1m/min;铣刀转速:
取铣刀转速n=290r/min;该工序的实际铣削速度:
;每转进给量:
;进给速度:
;2精铣取背吃刀量=1.0mm;切削宽度=60mm;根据参考文献[3]《机械加工工艺手册》表5—5知,精铣每转进给量=1.2mm;根据参考文献[3]《机械加工工艺手册》表5—11知,高速钢面铣刀铣削速度v=83.7m/min;铣刀转速:
取铣刀转速n=340r/min;该工序的实际铣削速度:
每齿进给量:
;进给速度:
;二、工序2——粗镗、半精镗、精镗侧面三孔根据参考文献[3]《机械加工工艺手册》表3—31和表4—15查得:
选用机床:
卧式镗床TX611A主轴转速:
12~950r/min镗刀刀具:
硬质合金镗刀镗刀材料:
YT5;1粗镗孔∅25.5mm取切削深度=2.0mm,毛坯孔径d0=21.5mm;根据参考文献[3]《机械加工工艺手册》表5—36知,刀杆伸出长度取200mm,切削深度为2mm,因此确定进给量=0.35mm/r;切削速度为v=21m/min。
镗刀杆转速:
取镗刀转速n=300r/min;该工序的实际切削速度:
进给速度:
;2粗镗孔∅30.2mm取切削深度=2.0mm,毛坯孔径d0=26.2mm;根据参考文献[3]《机械加工工艺手册》表5—36知,刀杆伸出长度取200mm,切削深度为2mm,因此确定进给量=0.45mm/r;切削速度为v=21m/min。
镗刀杆转速:
取镗刀转速n=250r/min;该工序的实际切削速度:
进给速度:
;3粗镗孔∅40mm取切削深度=2.0mm,毛坯孔径d0=36mm;根据参考文献[3]《机械加工工艺手册》表5—36知,刀杆伸出长度取200mm,切削深度为2mm,因此确定进给量=0.5mm/r;切削速度为v=24m/