谐波减速器零件机械加工工艺规程及夹具设计.docx
《谐波减速器零件机械加工工艺规程及夹具设计.docx》由会员分享,可在线阅读,更多相关《谐波减速器零件机械加工工艺规程及夹具设计.docx(33页珍藏版)》请在冰豆网上搜索。
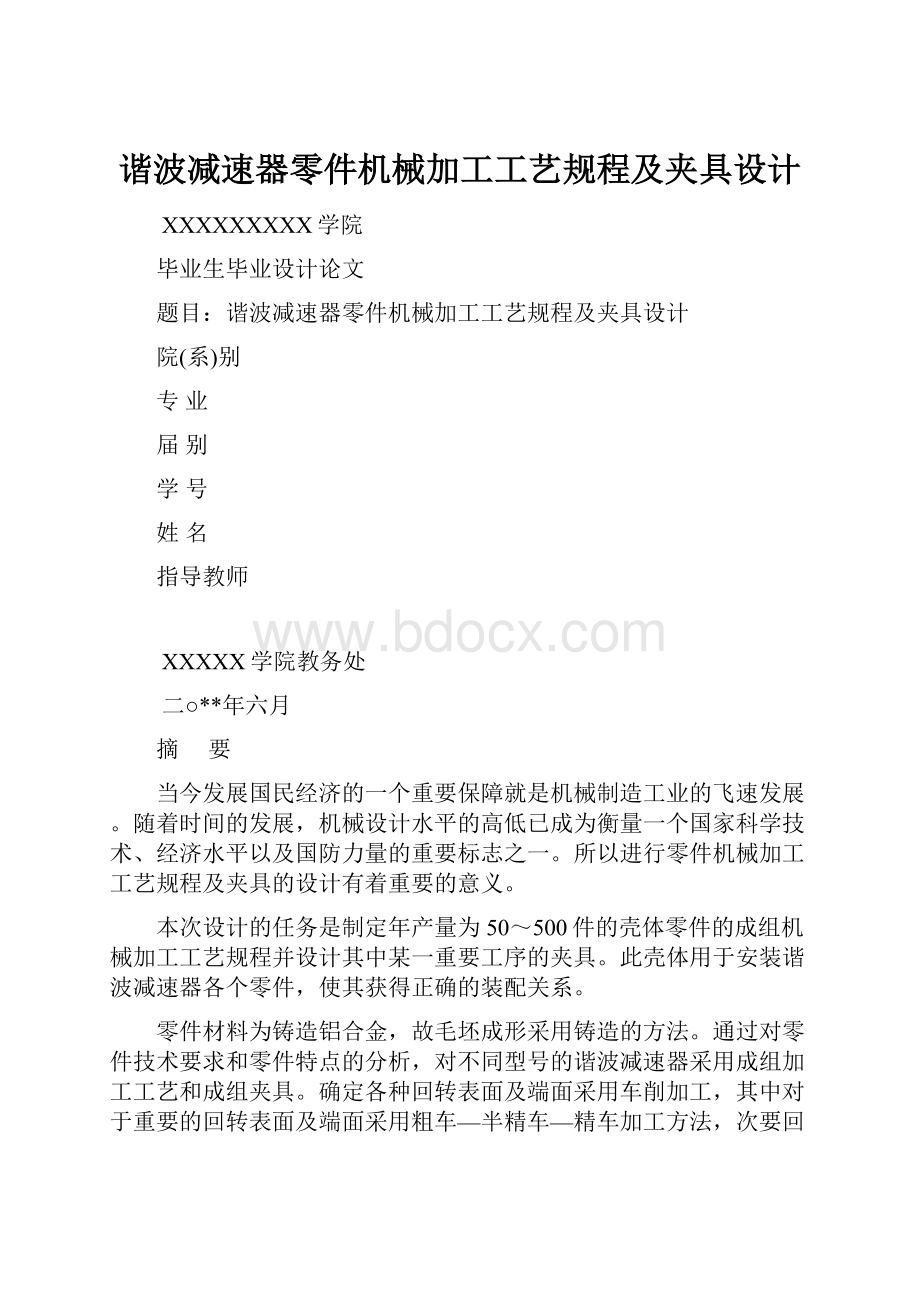
谐波减速器零件机械加工工艺规程及夹具设计
XXXXXXXXX学院
毕业生毕业设计论文
题目:
谐波减速器零件机械加工工艺规程及夹具设计
院(系)别
专业
届别
学号
姓名
指导教师
XXXXX学院教务处
二○**年六月
摘 要
当今发展国民经济的一个重要保障就是机械制造工业的飞速发展。
随着时间的发展,机械设计水平的高低已成为衡量一个国家科学技术、经济水平以及国防力量的重要标志之一。
所以进行零件机械加工工艺规程及夹具的设计有着重要的意义。
本次设计的任务是制定年产量为50~500件的壳体零件的成组机械加工工艺规程并设计其中某一重要工序的夹具。
此壳体用于安装谐波减速器各个零件,使其获得正确的装配关系。
零件材料为铸造铝合金,故毛坯成形采用铸造的方法。
通过对零件技术要求和零件特点的分析,对不同型号的谐波减速器采用成组加工工艺和成组夹具。
确定各种回转表面及端面采用车削加工,其中对于重要的回转表面及端面采用粗车—半精车—精车加工方法,次要回转表面及端面采用粗车—半精车加工方法;螺孔采用钻孔-攻丝加工方法。
对10工序的夹具进行了设计,为保证螺孔的位置精度,选用钻夹具。
关键词:
谐波减速器壳体,机械加工工艺规程,夹具,车削
Abstract
Nowtherapiddevelopmentofmachiningmanufactureisanimportantsafeguardofthenationaleconomyindustry.Withthetimepassingby,themachiningdesignlevelhasbecomeavitalsymbolwhichstandsforthelevelofscienceandtechnology,economy,aswellasthenationaldefensecapability.Thereforethecomponentsmachine-finishingtechnologicalprocessandthejigdesignwillplayagreatrole.
Themissionofthisprojectistoestablishthemachiningprocessregulationsofasetofshellswitha50~500yearlyoutput.Theclampofacertainprocedureisalsodesigned.Theshellsaremainlyusedtoinstallcomponentsoftheharmonicspeedchangersothattherightassemblyconnectioncanbegained.
Thematerialoftheshellsarecastaluminiumalloy,soweusefoundingasthewaytogetroughcast.Throughtheanalysisoftechnicalrequestandcharacteristicsoftheshells,groupmachiningmethodandmodularjigareusedtoproducetheshellsofharmonicspeedchangers.Alltherotativesurfacesandendsurfacesareproducedbyturningprocessing.Amongthosethemostimportantsurfacesareprocessedbyroughturning-semifinishing-finishturningandothersurfacesbyroughturning-semifinishing.Forscrews,weusetheprocessofdrilling-threading.
Theclampofprocedure10isdesignedduringwhichthedrillingjigsareusedtoassurethepositionalaccuracyofthescrews.
Keywords:
Harmonicspeedchanger,Technologicregulationsofmachiningprocess,Jig,Turning
2.1确定毛坯制造方法
2.2确定总余量
2.3绘制毛坯图
3制定零件工艺规程
3.1选择表面加工方法
3.2选择定位基准………………………………………………………………………….
3.2.1精基准的选择…..………………………………………………………………
3.2.2粗基准的选择…….……………………………………………………………
3.3拟定零件加工工艺路线
3.4选择各工序所用机床、夹具、刀具、量具和辅具
3.5填写工艺过程卡片
3.6.1
4.3夹具制造与操作说明
5结论
附录
前 言
机械制造工业是国民经济的装备部,在国民经济中具有十分重要的的地位。
机械制造工业提供的装备水平对国民经济各部门的技术进步有很大的影响。
而机械制造技术基础设计是综合运用“机械制造技术基础”及有关课程内容,分析和解决实际工程问题的一个重要教学环节。
现代机械制造技术的特点可用先进性、实用性和前沿性来概括。
(1) 先进性
现代机械制造技术的先进性主要表现在优质、高效、低耗、洁净、灵活(柔性)五个方面。
优质:
利用现代制造技术,使加工制造出的零部件或整机质量高,性能好;零部件尺寸精确,表面光洁,内部组织致密,无缺陷及杂质,使用性能好;整机的结构合理、色彩美观宜人,可靠性高。
高效:
使用现代制造技术,不仅表现在生产过程中,生产效率得到了很大的提高,大大降低了操作者的劳动强度。
而且还表现在产品的开发过程中,提高了产品的开发效率和质量,缩短了生产准备时间。
低耗:
采用现代制造技术,可以降低整个生产过程中的原材料及能源消耗。
洁净:
生产过程不污染环境,使有害废弃物零排放或少排放。
灵活:
能快速对市场变化及产品设计的更改作出反应,适应多品种柔性生产。
(2)实用性
现代制造技术是面向工业生产的实用技术,它具有量大面广和讲究实效的特点。
因为现代制造技术内涵极其丰富,同时又是动态发展的,它具有多种不同的模式和层次,可以应用于各种类型的机械工厂。
(3)前沿性
先进制造技术的前沿性主要表现在:
先进制造技术是信息技术和其它高新技术与传统制造技术相结合的产物,是制造技术研究最为活跃的前沿领域。
某些先进制造工艺和装备可能目前应用还不广泛,但是它们代表着一定的发展方向,可望得到越来越广泛的应用。
通过毕业设计培养了我制定零件机械加工工艺规程和分析工艺问题的能力,以及设计机床夹具的能力。
通过本次设计,我可以对所学专业课程进行一次系统的回顾,熟悉有关标准和设计资料,学会使用有关手册和数据库,也是对所学内容的一次综合检验,对我即将走向工作岗位之前的系统培训和作为未来从事机械制造技术工作的一次基本训练。
本次设计的任务是制定年产量为500件的谐波减速器壳体的机械加工工艺规程,编制机械加工工艺卡片,选择所用机床、夹具、刀具等;对所制定的工艺进行必要的分析论证和计算;确定毛坯制造方法及主要表面的总余量;确定主要工序的工序尺寸、公差和技术要求;对主要工序进行工序设计,编制机械加工工序卡片,画出工序简图;设计某一工序的夹具,绘制夹具装配图;编写设计说明书。
本次设计的零件它是依靠柔性零件产生弹性机械波来传递动力和运动,其承载能力高,传动比大,体积小中重量轻,传动效率高寿命长,传动平稳。
在设计毛坯成形时应特别注意这些方面,同时在进行工艺设计时本人对零件的设计要求和技术条件进行了深刻的研究分析。
严格按照设计人员的意图进行工艺编程,发现问题时及时和设计人员进行沟通以达到最佳的设计状态。
在对夹具进行设计时,查阅了大量车床夹具手册。
本次设计采用了车间工艺技术员必不可少的理论和技术,使其更具体、更贴近生产实际,论文具有一定的应用价值。
在设计过程中查阅了大量资料和文献,涉及到加工、装配、绘图、极限与配合、工程材料等多个方面。
在设计过程中,本人立足于理论联系实际,研究了谐波减速器壳体零件的机械加工工艺过程与原理,以及各工艺环节之间相互联系,并通过大量齐全的数据、准确的图表、框图等,对加工工艺进行系统性、原理性地纵向和横向综合分析比较。
通过本次设计可以达到以下目的:
(1)使设计者具有编制中等复杂程度零件的常规工艺规程的初步能力;
(2)具有对已编好的机械加工工艺规程在生产现场进行实施和服务的初步能力;
(3)具有对新工艺、新技术了解和推广应用的能力。
所设计的工艺重点突出,某些不重要的环节进行了省略,有不明之处,请参阅相关书籍和资料。
1零件图分析
图1.1谐波减速器壳体
图1.1为谐波减速器壳体零件图,各种壳体年产50-500件不等,按订单生产,属小批量生产。
1.1零件的功用
本零件为谐波减速器壳体,用于安装谐波减速器各零件,使其获得正确的装配关系。
其中内孔D1用于安装刚轮,内孔D6用于安装支承低速轴(输出轴)的轴承。
同时壳体外圆表面D7也是谐波减速器的安装基准面。
1.2零件工艺分析
本零件主体形状为回转体零件,其最主要加工面是内孔D1、D6,外圆D7,以及与内孔D1、D6垂直度要求较高的几个端面,如何保证这些表面本身的加工精度和相互位置精度是加工工艺需要重点考虑的问题。
本零件的另一特点是螺孔较多,其中螺孔S1位置度要求较高,螺孔S3、S4、和S5也有一定的位置度要求,在工艺上应给予保证。
本零件结构对于4种不同型号的谐波减速器完全一样,仅尺寸有所区别,但也在一定的尺寸范围内。
故可以采用成组工艺和成组夹具。
2确定毛坯制造方法
本零件的材料是简单硅铝明ZALSi12(ZL102),此铝硅系列铸造铝合金的铸造性和力学性能配合最佳。
有相当好的抗蚀性和耐热性,该合金适用于制作形状复杂但强度要求不是很高的铸造零件或者薄壁零件,例如仪表,水泵的壳体以及一些承受低载荷的零件。
而且本设计中谐波减速器壳体年产量为50-500件,属于小批量生产,考虑到经济因素,毛坯采用砂型铸造的成形方法。
2.1选定铸件分型面
铸型分型面指铸型组元间的结合面。
铸件的分型面确定之后,铸件在砂箱中的位置被确定,分型面的位置是否合理,关系到模样的结构,型芯的数量,制造工艺等。
因而,选择合理的分型面对铸件的质量和生产成本有重要的影响。
分型面的选择要遵循以下原则:
(1)尽量减少分型面
(2)尽量减少型芯
(3)分型面尽量为平面
(4)分型面尽量位于下型
本铸件的分型面位置见毛坯图。
2.2确定机械加工余量和最小铸孔
机械加工余量是指在切削加工时需要从铸件上切削掉的材料的厚度。
造型时必须考虑铸件所需要的机械加工面的加工余量。
加工余量的大小与铸件的批量、合金的种类、铸件的尺寸和浇注位置有关。
大批量生产时采用机器造型的方法,铸件的精度高,加工余量可以小一些。
单件或者小批量时一般是手工造型,铸件的精度低,应该选择比较大的加工余量。
铸件越大,铸造的误差越大加工余量应该越大。
浇注时位于铸件顶面部位的质量较差,加工余量比较大。
由表2.1确定外圆、内孔直径上总余量为5mm,端面总余量为2.5mm。
铸件的孔、槽是否铸出,不仅取决于工艺上的可能性,还必须考虑其必要性。
一般来说,较大的孔、槽应当铸出,以减少切削加工工时、节省金属材料,同时也可减小铸件上的热节。
但较小的孔、槽则不必铸出,留待加工反而更经济。
本设计中,壳体零件图中D4、D5、D13孔径都较小,因此不予铸出。
表2.1铸件的机械加工余量(mm)
2.3选定起模斜度
为了便于造型时的起模,将模样垂直于分型面的表面设计成一定斜度的表面,该斜度称为起模斜度。
起模斜度的大小与模样的种类,垂直壁的高度,造型的材料的特点和造型的方法有关。
起模斜度一般是0.5~3。
立壁越高,斜度越小,内壁的斜度应该大于外壁的斜度。
金属模样与型砂的摩擦力比较小,起模斜度小于木模样。
2.4铸造收缩率
由于合金的线收缩,铸件冷却的尺寸将比型腔尺寸略为缩小,为保证铸件应有的尺寸,模样尺寸必须比铸件放大一个该合金的收缩量。
在铸件冷却过程中其线收缩率不仅受到铸型和型芯的机械阻碍,同时还受到铸件各部分的相互制约。
因此,铸件的实际线收缩率除随合金的种类而异外,还与铸件的形状、尺寸有关。
通常,铝硅合金的收缩率为0.8%~1.2%。
在毛坯制造时应考虑到这一点。
2.5型芯头与型芯座
在铸型中,型芯头对型芯起着定位和排气作用。
型芯头的形状尺寸将影响型芯的安装稳定性。
按照固定的方法不同,型芯头可以分为垂直型芯头和水平型芯头两种,垂直型芯头一般设有上,下型芯头。
为了便于型芯防止和固定,下型芯头高读比上型芯头大,斜度要小于上型芯头,型芯头和型芯座之间要留有空隙,以便于铸型的装配。
对于段而且粗的垂直,也可以不设计上型芯头。
水平型芯的两端一般都有型芯头。
通过件图结构,由于零件是带有空腔的,所以选择空腔部分设计使用型芯。
2.6绘制毛坯图
绘制的毛坯图见图2.1。
图2.1谐波减速器壳体铸造毛坯图
3.制定零件工艺规程
3.1选择表面加工方法
1)由于工件材料为ZL102铸铝合金,故各回转表面及端面均采用车削方法加工:
对于重要回转表面及端面,为保证其尺寸精度和位置精度,采用粗车-半精车-精车加工方法,对于次要回转表面及端面则采用粗车或粗车-半精车的加工方法。
2)螺孔采用钻孔-攻丝加工方法。
为保证螺孔的位置精度,均使用钻夹具进行加工。
3.2选择定位基准
定位基准有粗基准和精基准之分。
工件加工的第一道工序中,只能用毛坯上未经加工的表面作为定位基准,这种定位基准称为粗基准。
在以后的工序中则使用经过加工的表面作为定位基准,这种定位基准称为精基准。
合理选择定位基准,对保证加工精度、安排加工顺序和提高加工生产率有着重要的影响。
从定位的作用来看,它主要是为了保证加工表面的位置精度。
因此定位基准的总原则,应该是从优位置精度要求的表面中进行选择。
3.2.1精基准的选择
精基准又称光基准,其选择原则如下:
(1)“基准重合”原则
就是尽量选用设计基准和工序基准作为定位基准,以避免定位基准与设计基准不重合而引起的定位误差。
(2)“基准统一”原则
位置精度要求较高的某些表面加工时,尽可能选择同一定位基准,这样有利于保证各加工表面的位置精度。
(3)“互为基准”原则
当两个表面相互位置精度以及他们自身的尺寸与形状精度都要求很高时,可以采取互为经基准得原则,反复多次进行精加工。
(4)“自为基准”原则
有些精加工或光整加工工序余量小而均匀,在加工时就应尽量选择加工表面本身作为精基准,即遵循自为基准的原则。
本零件的设计基准是D6孔和大端面C,根据基准重合原则,并同时考虑统一精基准原则,选D6孔和大端面C作为主要定位精基准。
在钻螺纹底孔的工序中,考虑工件定位和装夹的方便,选大端面C和D1孔作为定位精基准。
为保证D7外圆和D6孔的同轴度,加工D6孔时采用D7外圆表面作为定位基准;而在精加工D7外圆表面时,采用D6孔作为定位基准。
这体现了互为基准的原则。
3.2.2粗基准的选择
主要不影响不加工表面和加工表面间的相互位置精度,以及影响加工表面的余量分配。
因此,选择粗基准的基本原则是:
(1)若工件必须保证某重要表面的加工余量均匀,则应选择该表面为粗基准。
(2)在没有要求保证重要表面加工余量均匀的情况下,若零件的每个表面都要加工,则应该以加工余量最小的表面作为粗基准。
(3)在与上项相同的前提条件下,若零件上有的表面不需加工,则应以不加工表面和加工表面终于加工表面的位置精度要求较高的表面作为粗基准,以达到壁厚均匀,外形对称等要求。
(4)选用粗基准的表面应尽量平整光洁,保证零件夹紧可靠。
(5)粗基准一般只使用一次,因此,一般只在第一道工序中使用,以后不应重复使用。
为保证加工面与不加工面的位置关系,选不加工的四方面作为定位粗基准。
3.3时效处理
铸造和机械加工都会留下残余内应力,故应采用时效处理予以消除。
对于铸件,特别是形状复杂的大型铸件,应在粗加工前后各安排一次时效处理。
对于精度要求高的工件,一般在粗加工和半径加工后各安排一次时效处理。
3.4拟定零件加工工艺路线
生产车间有普通车床和数控车床可供选择。
考虑到该零件孔的加工难度较大,为了稳定地保证加工精度,也为了提高加工效率,精加工采用数控车床。
主要加工工序确定如下:
1)半精车小端面、D7外圆、台阶面及D4孔(普通车床,四爪卡盘);
2)半精车内空刀槽D3×(L2-L3)(普通车床,三爪卡盘);
3)时效处理;
4)精车大端面,精车D1孔,半精车D2孔,精车D6孔,倒角0.5×45°(数控车床,三爪卡盘);
5)精车D7外圆,精车台阶面,倒角1×45°,精车D4孔,精车L9槽(直径D5)(数控车床,可胀心轴);
6)中间检验:
精车各部尺寸;
7)钻4-S3螺纹底孔(台式钻床,钻夹具);
8)钻6-S4螺纹底孔(台式钻床,钻夹具);
9)钻4-S5螺纹底孔(台式钻床,钻夹具);
10)钻S1和S2螺纹底孔,锪沉头孔(台式钻床,钻夹具);
11)中间检验:
螺纹底孔尺寸及位置;
12)攻丝:
4-S3(台式钻床,钻夹具);
13)攻丝:
6-S4(台式钻床,钻夹具);
14)攻丝:
4-S5(台式钻床,钻夹具);
15)攻丝:
S1和S2(台式钻床,钻夹具);
16)最终检验。
3.4选择各工序所用机床、夹具、刀具、量具和辅具
3.4.1机床
机床是机械制造业的基本加工装备,它的品种、性能、质量和技术水平直接影响着其他机电产品的性能、质量、生产技术和企业的经济效益。
机床可分为传统机床和数控机床两大类,按机床的加工方式、加工对象或主要用途,我国将机床分成为12大类,它们是:
车床、钻床、镗床、磨床、齿轮加工机床、螺纹加工机床、铣床、刨插床、拉床、特种加工机床、锯床和其它机床。
每一类机床,又可按其结构、性能和工艺特点的不同细分为若干组,如车床类就有:
普通车床、立式车床、六角车床、多刀半自动车床、单轴自动车床和多轴自动车床等等。
机床的主要组成部分有主传动部件、进给传动部件、工件安装装置、刀具安装装置、支承件和动力源。
3.4.2夹具
夹具是加工工件时,为完成某道工序,用来正确迅速安装工件的装置。
它对保证加工精度、提高生产效率和减轻工人劳动量有很大作用。
机床夹具一般按用途分类,通常分为两大类:
通用夹具和专用夹具。
通用夹具指加工两种或两种以上工件的同一夹具,一般已经标准化,不需特殊调整就可以用于加工不同的工件。
他们的适应性较强,对于充分发挥机床的技术性能、扩大机床的使用范围起着重要作用。
专用夹具是指为某一零件的加工而专门设计和制造的夹具,没有通用性。
利用专用夹具加工工件,即可保证加工精度,又可提高生产效率。
此外,还可按夹紧力源不同,将夹具分为手动夹具、气动夹具、电动夹具和液压夹具等。
单件小批生产中重要使用手动夹具。
夹具主要由定位元件、夹紧机构、导向元件、夹具体及其他部分组成。
工件的加工精度在很大程度上决定于夹具的精度和结构,因此整个夹具及其零件都要具有足够的精度和刚度,并且结构要紧凑、形状要简单,装卸工件和清除切屑要方便等。
3.4.3刀具和量具
切削过程中刀具用来直接完成切削工作。
无论哪种刀具,一般都有切削部分和夹持部分组成。
夹持部分用来将刀具夹持在机床上的部分,要求它能保证刀具正确的工作位置,传递所需要的运动和动力,并且夹固可靠,装卸方便。
切削部分是刀具上直接参与切削工作的部分,刀具切削性能的优劣,取决于切削部分得材料、角度和结构。
量具的选择取决于生产类型和加工精度。
单件小批生产尽量采用通用量具,大量生产且精度要求较高时,应采用各种量规和高效检验设备。
表3.1常用加工设备技术参数
机床
最大加工直径×加工长度
主轴转速(转/分)
加工质量
主电机功率KW
不圆柱度
锥度
不平度
粗糙度
普通车床
C6132
320×800
40~1200
0.01
0.01
0.015/180
4
CA6140
400×650
10~1800
0.01
0.01/100
0.015/200
7.5
CM6140
400×900
10~1400
0.005
0.01/150
0.01/200
7.5
机床
最大钻孔直径
主轴行程
主轴转速级数
主轴转速
(转/分)
主轴功率
立式钻床Z518
18
150
6
310~2975
1
Z525
25
175
9
97~1360
28
摇臂钻床Z35
50
350
18
34~1700
5.5
Z37
75
450
22
11.2~1400
7.5
机床
最大刨削长度
工作台工作
面积
每分钟滑枕
往复次数
每往复工作台进给量
主电机功率
牛头刨B650
500
顶面:
450*405
侧面435*355
8级
11~120
6级
0.35~2.13
4
B665
650
侧面:
650*450
6级
12.5~72.7
10级
0.33~3.33
3
机床
最大镗孔直径
主轴转速
(转/分)
加工质量
不圆柱度
端面不平度
粗糙度
卧式T617
240
13~1160
0.02
0.02
T68
240
20~1000
0.02/300
0.02/300
精密窝镗铣T646
240
8~1036
0.01
0.01
立式金刚镗T716
165
19~600
0.01
0.01
外圆磨床M2120
磨削直径
8~315
磨削长度1000
0.003
0.006
内圆磨床M2120
磨孔直径
500~200
磨孔深度
120~160
0.006
0.005/200
平面磨床M1040
磨削面积长*宽1000*300
不平度0.015/1000
无心磨床M1040
磨削直径2~40
磨削宽度140
椭圆度0.002
不圆柱度0.004
机床
工作台工作
面积长*宽
工作台
最大行程
主轴转速
(转/分)
主电机功率KW
卧式铣床X60
800*200
500*160*300
50~2240
3
卧式铣床X62
1250*320
700*255*360
30~1500
7.5
立式铣床X52K
1250*320
700*255*370
30~1500
7.5
万能铣床X62W
1250*320
700*255*370
30~1500
7.5
机床
额定拉力(吨)