带钢冷轧机组的工作辊换辊操作doc.docx
《带钢冷轧机组的工作辊换辊操作doc.docx》由会员分享,可在线阅读,更多相关《带钢冷轧机组的工作辊换辊操作doc.docx(15页珍藏版)》请在冰豆网上搜索。
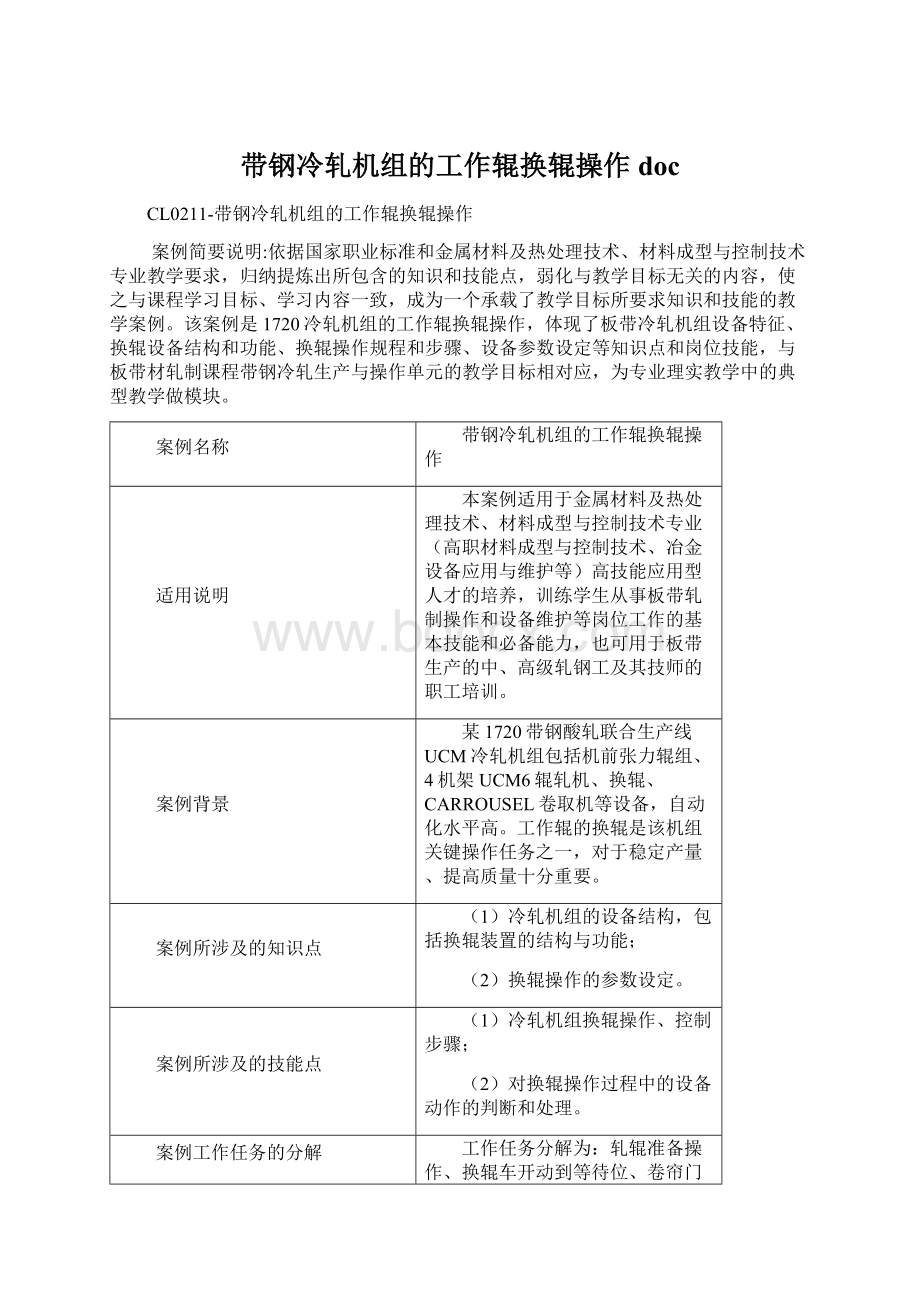
带钢冷轧机组的工作辊换辊操作doc
CL0211-带钢冷轧机组的工作辊换辊操作
案例简要说明:
依据国家职业标准和金属材料及热处理技术、材料成型与控制技术专业教学要求,归纳提炼出所包含的知识和技能点,弱化与教学目标无关的内容,使之与课程学习目标、学习内容一致,成为一个承载了教学目标所要求知识和技能的教学案例。
该案例是1720冷轧机组的工作辊换辊操作,体现了板带冷轧机组设备特征、换辊设备结构和功能、换辊操作规程和步骤、设备参数设定等知识点和岗位技能,与板带材轧制课程带钢冷轧生产与操作单元的教学目标相对应,为专业理实教学中的典型教学做模块。
案例名称
带钢冷轧机组的工作辊换辊操作
适用说明
本案例适用于金属材料及热处理技术、材料成型与控制技术专业(高职材料成型与控制技术、冶金设备应用与维护等)高技能应用型人才的培养,训练学生从事板带轧制操作和设备维护等岗位工作的基本技能和必备能力,也可用于板带生产的中、高级轧钢工及其技师的职工培训。
案例背景
某1720带钢酸轧联合生产线UCM冷轧机组包括机前张力辊组、4机架UCM6辊轧机、换辊、CARROUSEL卷取机等设备,自动化水平高。
工作辊的换辊是该机组关键操作任务之一,对于稳定产量、提高质量十分重要。
案例所涉及的知识点
(1)冷轧机组的设备结构,包括换辊装置的结构与功能;
(2)换辊操作的参数设定。
案例所涉及的技能点
(1)冷轧机组换辊操作、控制步骤;
(2)对换辊操作过程中的设备动作的判断和处理。
案例工作任务的分解
工作任务分解为:
轧辊准备操作、换辊车开动到等待位、卷帘门操作、换辊车准备操作、轧辊抽出、轧辊侧移换位、轧辊插入固定、启动轧机操作等操作项目。
教学目标
(1)了解带钢UCM冷轧机的基本结构与各部件的功能;
(2)掌握设备参数设定的依据与计算;
(3)掌握带钢冷轧机换辊操作的基本步骤及其作用;
(4)全面复习所学知识,并将理论知识转化为操作能力。
案例建议的教学时间
8~10学时
案例的操作演示
现场调研、操作规程学习、仿真训练、分组讨论、总结点评。
案例点评
本案例通过现场教学、理论学习和仿真训练,引导学生准确完成冷轧机组换辊的各项工作,训练其严格按规程操作的职业素质,独立分析和解决生产操作问题的能力。
同时,培养学生观察总结、沟通交流的能力,团结协作的团队精神和严谨务实的工作作风。
带钢冷轧机组的工作辊换辊操作
1背景介绍
某带钢酸洗-冷轧厂采用1720酸轧联合机组,轧机型式为四机架UCM,具备中间辊的轴向窜动,工作辊和中间辊的弯辊功能,轧机出口配以多段冷却,为控制平直度和板型提供硬件条件。
该带钢冷轧机组的操作控制系统分为3级,其中,1级和2级可以实现生产准备、穿带操作、轧制准备、轧制生产和生产监控、换辊操作和数据传递等模拟操作环节。
2主要内容
2.1冷轧机组设备基本情况
冷轧带钢轧制段车间分为四个部分,分别是带钢进轧机入口前段、轧机段、出口卷曲段、打捆喷号段。
(1)轧机入口前段
图1冷轧机组入口前段设备
(2)轧机段
图2冷轧机组轧机段布置
(3)出口卷取段
图3冷轧机组出口CARROUSEL卷取机
(4)打捆喷号段
图4机组出口打捆喷号设备
2.2冷轧机组工作辊换辊操作步骤
(1)换辊准备的操作
1)换辊请求
图5换辊操作轧辊数据界面
进入操作控制二级界面(轧机数据建立操作界面)中输入换辊请求。
单击“轧辊更换”后,确定换辊原因(到吨位、划伤、检修、变规格、断带、爆辊和辊印等)。
假定换辊原因为“变规格”,进行后续操作。
2)轧制力恒定操作
执行“恒定轧制力”。
3)辊缝打开
执行“打开辊缝”。
进入“换辊操作界面”,依此执行“换辊大车等待”、“卷帘门打开”、“换辊准备”、“轧辊抽出”、“轧辊侧移”、“轧辊插入”、“轧制准备”等步骤。
(2)换辊车向前到等待位置
包括换辊大车和推拉车两个子操作步骤。
1)换辊大车操作步骤
执行“换辊大车前进至等待位”,根据现场检测信号反馈判断其是否已到位,再予后续操作。
2)推拉车操作步骤
按动按钮,执行“推拉车至等待位”将推拉车前进至等待位置。
(3)卷帘门打开
打开轧机卷帘门,点击执行“卷帘门打开”,确定其位置后,再予执行后续操作。
(4)换辊车准备
执行“换辊车准备”后,依此执行以下子步骤:
1)防缠板挡块抽出
执行“防缠板挡块抽出”,并确认其位置。
2)工作辊到平衡位置
执行“工作辊弯辊”设置至“平衡”位置(包括“关闭”、“平衡”和“打开”3个位置)。
3)中间辊到平衡位置
执行“中间辊弯辊”设置至“平衡”位置(包括“关闭”、“平衡”和“打开”3个位置)。
4)液压主令关闭
执行“液压主令关闭”,并确认主令缸关闭。
5)辊缝快速打开到位
按下操作台上的按钮,打开“旁通液压缸”,观察液压缸的传动侧位置和工作侧位置数值的变化,当数值变为0后,表示辊缝打开液压缸下降到位,然后松开按钮。
6)支撑辊平衡下降
执行“支承辊平衡”的“下降”操作(包括“下降”、“保持”、“关闭”、“上升”)。
7)斜楔和阶梯块抽出
输入轧机斜楔和阶梯块的位置参数为“0”,表示斜楔和阶梯块退出轧制线。
以1号轧机为例,进行斜楔的操作:
输入1号轧机斜楔位置参数为“0”,并执行。
阶梯块的操作:
输入1号轧机阶梯块位置参数为“0”,并执行。
8)支撑辊平衡到上部位置
执行“支承辊平衡”至“上部”位置(包括“下降”、“保持”、“关闭”、“上升”),并确认。
9)接轴定位
执行“接轴定位”,并确认对应的状态信息。
10)接轴托架升起
执行“接轴托架”“上升”操作(包括“上升”和“下降”2个操作),并确认对应的状态信息。
11)上、下中间辊窜移
上中间辊窜移操作步骤,输入“上中间辊窜移值”到“500”,“下中间辊窜移值”到“0”,并执行,确认对应的状态信息。
12)换辊车前进到位
按动操作台“换辊车”“前进”按钮,到位后,现场反馈换辊车位置信号。
13)换辊车挡块到设定位置
设置“换辊车挡块”到“设定”,并执行,确认对应的状态信息。
14)推拉车向前到位
按动操作台的按钮“推拉车”“前进”(包括“前进”、“返回”2种操作),推拉车向前到位,并确认其状态信息。
(5)轧辊抽出
执行“轧辊抽出”操作,然后执行子步骤:
1)工作辊锁紧打开
执行“工作辊锁紧”“锁紧打开”,并确认对应的状态信息变化。
2)中间辊锁紧打开
执行“中间辊锁紧”“锁紧打开”,并确认对应的状态信息变化。
3)工作辊抓钩抓紧
执行“工作辊抓钩”“抓紧”(包括“抓紧”和“松开”2个动作),并确认对应的状态信息。
4)中间辊抓钩抓紧
执行“中间辊抓钩”“抓紧”(包括“抓紧”和“松开”2个动作),并确认对应的状态信息。
5)推拉车后移
按下操作台按钮“推拉车”“后退”(包括“前进”、“后退”2个动作),并确认对应状态信息的变化。
6)工作辊抓钩松开
执行“工作辊抓钩”“松开”(包括“抓紧”和“松开”2个操作),并确认对应状态信息的变化。
7)中间辊抓钩松开
执行“中间辊抓钩”“松开”(包括“抓紧”和“松开”2个操作),并确认对应状态信息的变化。
(6)轧辊侧移
执行“轧辊侧移”操作。
(7)轧辊插入
执行“轧辊更换”操作,确认并输入换辊数据和原因,换辊原因包括:
“到吨位”、“划伤”、“检修”、“变规格”、“断带”、“爆辊”和“辊印”。
确认换辊原因为“变规格”,确认后并匹配,新辊数据覆盖旧辊数据,然后执行里面的子步骤:
1)防缠板挡块的数据设定
防缠板挡块根据辊径变化需要进行设定值,输入数据,并执行“防缠板挡块”和“位置参数”操作。
依据公式为:
防缠导板挡块位置=1/2*(425-ØWR)
2)工作辊和中间辊抓钩抓紧
同前述操作步骤。
3)推拉车向前到位
按动操作台的按钮“推拉车”“前进”操作,确认对应信息的变化。
4)工作辊和中间辊锁紧
执行“工作辊锁紧”和“中间辊锁紧”的“锁紧”操作,确认对应信息的变化。
5)工作辊和中间辊的抓钩打开
工作辊抓钩松开:
执行“工作辊抓钩”“松开”(包括“抓紧”和“松开”2个操作),并确认对应状态信息的变化。
中间辊抓钩松开:
执行“中间辊抓钩”“松开”(包括“抓紧”和“松开”2个操作),并确认对应状态信息的变化。
6)大车定位挡块到松开位置
执行“大车定位挡块”至“释放”位置,并确认对应的状态信息。
7)换辊大车和推拉车后退操作
同时按下操作台的“换辊大车”“后退”按钮和“推拉车”“后退”按钮,然后“换辊大车”和“推拉车”同时“后移”到位,并确认对应的状态信息。
8)轧制准备
执行“轧制准备”操作。
9)调整上中间辊和下中间辊的窜移量
进行上中间辊窜移操作步骤,执行“上中间辊窜移”和“下中间辊窜移”操作。
中间辊窜移值计算:
中间辊窜移值=837.5-1/2*B-50B为成品宽度。
注意:
工作辊中间辊在bal位置,支撑辊在up位置。
10)接轴托架降下
执行“接轴托架”“下降”操作(包括“上升”和“下降”2个操作),并确认对应的状态信息变化。
11)弯辊和平衡操作
执行“工作辊弯辊”“关闭”操作(包括“关闭”、“平衡”和“打开”3种操作),并确认对应的状态信息变化。
12)轧制线定位
根据换辊的辊径变化进行轧制线定位,输入阶梯块和斜楔数值,见下表。
阶梯块定位
阶梯块高度(TR)
9
90
轧辊直径(Dw+Di+1/2Db)
1=85
1565≥Dw+Di+1/2Db>1540
MAX=490+425+0.5×1300=1565mm
2=125
1540≥Dw+Di+1/2Db>1500
3=165
1500≥Dw+Di+1/2Db>1480
4=205
1480≥Dw+Di+1/2Db>1420
5=245
1420≥Dw+Di+1/2Db>1400
MIN=440+385+0.5×1150=1400mm
说明:
(1)1-5表示阶梯档位,TR表示阶梯块高度;
(2)Dw:
工作辊直径,Di:
中间辊直径,Db:
支承辊直径;
(3)阶梯块定位根据轧辊直径变化选择定位挡块,轧辊直径由二级系统换辊数据传输。
斜楔APC定位值:
APC=斜楔伸出高度×斜楔斜率=[1667.5-(Dw+Di+1/2Db)-TR]×20
斜楔伸出长度实际上结余阶梯挡块之间的补偿量。
13)辊缝上升进行调零
执行轧机“调零模式”的“开始”操作(包括“自动”、“人工”、“跟随”、“停止”、“开始”和“脱离”等6种操作),并对应的状态信息变化。
调零数据计算公式见下表。
F1
F2
F3
F4
MAN.ZERO
H1=(1650-(ФWR+
ФIMR+0.5ФBUR))×K
H2=(1650-(ФWR+
ФIMR+0.5ФBUR))×K
H3=(1650-(ФWR+
ФIMR+0.5ФBUR))×K
H4=(1650-(ФWR+
ФIMR+0.5ФBUR))×K
ACT.GAP
H-h1
h2-h1
h2-h3
h3-h4
ACT.CYL
MAN.ZERO-ACT.GAP
MAN.ZERO-ACT.GAP
MAN.ZERO-ACT.GAP
MAN.ZERO-ACT.GAP
说明:
(1)WR、IMR、BUR直径由二级系统换辊数据传输;
(2)H、h1、h2、h3、h4是各机架带钢厚度,通过二级系统设定相对压下率计算得出;
(3)K表示轧辊弹性模量影响因素,取值K=1.02.
表中,H为原料厚度,可从所下生产计划中获得。
(8)启动轧机操作
执行“轧机启动”操作,开启轧机。
3分析路径
该案例是1720冷轧机组的工作辊换辊操作,体现了板带冷轧机组设备特征、换辊设备结构和功能、换辊操作规程和步骤、设备参数设定等知识点和岗位技能,与材料成型与控制技术专业《板带材轧制》课程“带钢冷轧生产与操作”单元的教学目标相对应,为专业理实教学中的典型教学做模块。
根据国家职业标准关于轧钢工的要求,对应教学目标,从此生产案例归纳提炼出所包含的知识和技能点,弱化与教学目标无关的内容,使之与课程学习目标、学习内容一致,成为一个承载了教学目标所要求知识和技能的教学案例。
采用现场调研、理论学习和仿真操作等手段,引导学生通过讲授、操作、讨论、总结等方式学习冷轧机组的设备知识(包括冷轧基本工艺),掌握换辊操作和控制技能,达到教学目标要求。
分析路径如下:
(1)通过现场调研,使学生了解带钢冷轧的工艺流程、设备状况等,构建案例教学的情境;
(2)分析冷轧机组的基本结构和特征,特别是轧辊组件在机架中安装状况、换辊装置的结构和作用,为换辊操作的案例教学进行理论铺垫;
(3)课堂讲授冷轧机组换辊的操作步骤,并分析其设备动作和作用,其中,包括设定参数的确定,为实施教中学、教中做,切实提升学生岗位技能作出详细、具体的指导;
(4)通过学生进行冷轧机组的换辊操作,总结和掌握操作要领,对技能培训效果进行反馈;
(5)通过课中和课后作业,巩固冷轧机组换辊操作技能和设备结构知识。
4教学目标
(1)了解带钢UCM冷轧机的基本结构与各部件的功能;
(2)掌握设备参数设定的依据与计算;
(3)掌握带钢冷轧机换辊操作的基本步骤及其作用;
(4)全面复习所学知识,并将理论知识转化为操作能力。
5教学方式方法
现场调研、问题讨论、点评、讲授、仿真操作练习、作业。
具体教学过程设计如下:
5.1课前计划
(1)学生掌握知识:
带钢冷轧的基本工艺、冷轧机组和卷取机的基本结构、板形控制原理、冷轧带钢计划安排;
(2)将班级学生分成若干组,指定组长,每组最佳6-8人;
(3)与现场联系,进行现场教学准备,包括安全教育、劳保用品、行走路线,现场兼职教师与现场教学场所等;
(4)安全教育,教师(包括兼职教师)带领学生下厂调研,记录冷轧机组换辊操作中设备的基本动作,并收集相关信息和资料;
(5)学生根据所学知识和实习、调研中获得的资料,总结换辊操作要点;
(6)学习冷轧机组换辊操作规程和注意事项;
(7)由兼职教师(现场技术人员)交流,请技术人员准备讲授换辊操作中容易出现的问题。
5.2课中计划
(1)学生按小组就座带钢冷轧仿真操作台,确定记录人、发言人和各组员的操作顺序。
(2)各组员分别在教师的指导下操作带钢冷轧仿真生产系统,换辊时间约5-8分钟,其余人员记录其操作流程。
(3)小组成员全部完成换辊操作后,讨论换辊步骤并阐述其作用,对换辊失败的组员的操作进行分析和总结。
(4)小组发言人在讨论、分析和总结的基础上,向全体师生汇报轧机换辊操作要领,其他同学可以补充,时间约6分钟。
(5)各小组汇报完成后,本组自评,其它组进行点评打分,教师或现场技术人员参与对学生汇报的操作要点评价,指出优点和不足,每组时间2-3分钟。
各小组评分汇总后,排出次序。
(6)教师讲授换辊操作实际实际中的易发生故障,时间约15分钟。
5.3课后计划
布置作业,见6.3。
6思考题及考评
6.1课前思考题
布置课前思考题,引导学生在生产现场了解冷轧的原料、工艺参数和流程、设备的基本参数、换辊操作及其过程中设备的动作。
(1)冷轧原料成分和卷号是什么?
常见原料缺陷有哪些?
(2)冷轧过程的流程和压下规程是什么?
(3)冷轧机组的设备型式,板形控制手段有哪些?
(4)换辊过程中主要设备的工作?
(5)换辊操作的时间统计?
(6)换辊时间间隔(轧制里程)?
(7)监控系统中换辊操作的基本步骤有哪些?
6.2课堂练习
课堂提问或者集体回答,目的:
及时复习、巩固知识,检查教学效果。
练习题
1、下列照片中为冷轧原料的缺陷,容易导致。
(A)
A夹渣、孔洞B折叠、断带
C孔洞、影响外观D压氧、冲压开裂
2、冷轧的工艺特点是(ABC)。
A加工温度低,在轧制中产生不同程度的加工硬化。
B冷轧机中要采用工艺润滑和冷却。
C冷轧中要采用大张力轧制。
3、UCM轧机的板形控制手段有(ABC)。
A中间辊的轴向窜动
B工作辊弯辊
C中间辊弯辊
4、对换辊大车与推拉车描述正确的是(ABC)。
A换辊大车承载着推拉车
B推拉车承载轧辊组件
C两者在换辊过程中都需位置检测和反馈
D两者的动作无先后次序
5、冷轧机组的监控系统中,对“执行”与“设定”描述正确的是(A)。
A先设定后执行
B先执行后设定
C两者可同时操作
D没有限定
6、抽出辊时,换辊车准备,对轧辊的平衡要求是(ABC)。
A工作辊到平衡位置
B中间辊到平衡位置
C支承辊不需要动作
D支承辊先先下降后上升
7、换辊原因有(ABD)。
A到吨位B变规格C辊缝D划伤
8、选中下图中的“ON”并点击
,表示(C)。
A工作辊弯辊B工作辊平衡C中间辊弯辊D支承辊平衡
9、轧辊抽出环节的操作流程是:
工作辊锁紧打开—中间辊锁紧打开—工作辊抓钩抓紧—中间辊抓钩抓紧—推拉车后移—工作辊抓钩松开—中间辊抓钩松开。
(√)
10、换辊后的轧制线定位只要输入阶梯块的数值就能够实现。
(×)
6.3课后作业
课后作业,复习巩固知识、提升能力。
(1)每人均独立对冷轧机组进行换辊操作一次。
(2)每人结合自己操作过程,总结换辊的操作要点。
6.4评价
学生考核评价实施表如下。
评价方式
评价内容
评价结果
得分
过程性评价
(100%)
学生出勤(10%)
迟到、缺勤等。
2~10
现场调研(20%)
工艺状况、操作步骤和设备动作记录详细。
5~20
课堂参与
(60%)
仿真操作评价
(30%)
符合换辊操作标准,系统给分。
0~30
小组协作评价
(10%)
小组合作融洽,讨论能达到预定的目标。
2~10
展示评价
(10%)
展示内容全面,条理清楚、语言流畅。
2~10
小组成员互评
(10%)
学习状况相互评价。
2~10
完成作业(10%)
作业完成情况。
4~10
总分