注射模课程设计说明书.docx
《注射模课程设计说明书.docx》由会员分享,可在线阅读,更多相关《注射模课程设计说明书.docx(27页珍藏版)》请在冰豆网上搜索。
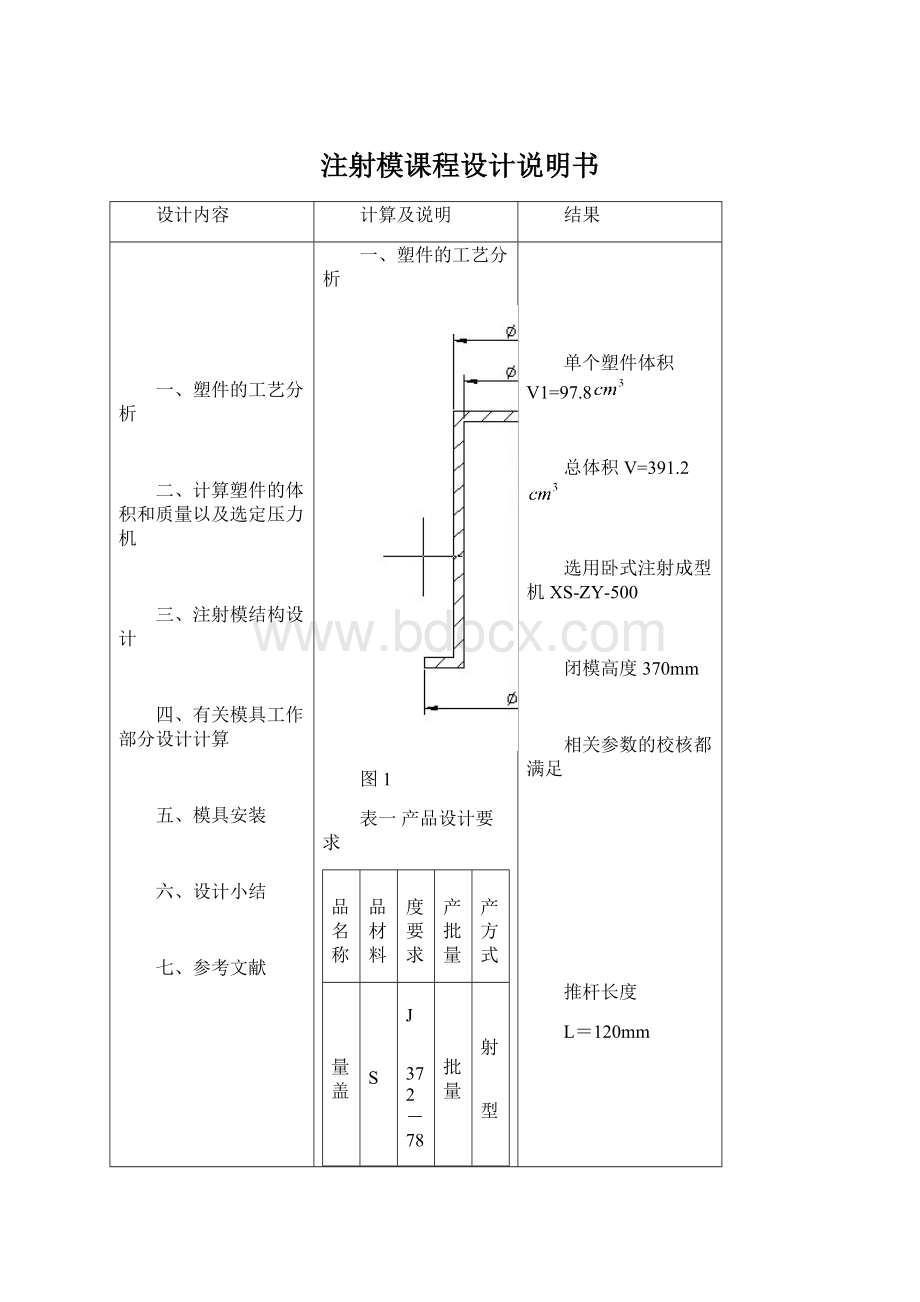
注射模课程设计说明书
设计内容
计算及说明
结果
一、塑件的工艺分析
二、计算塑件的体积和质量以及选定压力机
三、注射模结构设计
四、有关模具工作部分设计计算
五、模具安装
六、设计小结
七、参考文献
一、塑件的工艺分析
图1
表一产品设计要求
产品名称
产品材料
精度要求
生产批量
生产方式
容量盖
PS
SJ
1372-78
6级
大批量
注射
成型
1.材料性能
PS为聚苯乙烯,属于热塑性塑料。
密度1.04~1.06g/cm
收缩率0.5%~0.6%
吸水率0.03~0.05
熔点131℃~165℃
抗拉强度35~63MPa
特点:
普通聚苯乙烯树脂为无毒.无臭.无色的透明颗粒,似玻璃状脆性材料.其制品具有极高的透明度,透光率可达90%以上,电绝缘性能好,易着色.加工流动性好,刚性好及耐化学腐蚀性好等。
普通聚苯乙烯的不足之处在于性脆,冲击强度低,易出现应力开裂,耐热性差及不耐沸水等。
该塑件尺寸较小且要求塑件表面精度等级较低,表面不允许有明显的熔接痕,收缩痕。
采用点浇口的双分型面型腔注射模可以满足其表面要求。
此塑件是采用PS(聚笨乙烯)注塑成的。
查相关手册可知:
聚苯乙烯聚苯乙烯是指有苯乙烯单体经自由基缩聚反应合成的聚合物,英文名称为Polystyrene,日文名称为ポリスチロール,简称PS。
玻璃化温度80~90℃,非晶态密度1.04~1.06克/厘米3,晶体密度1.11~1.12克/厘米3,熔融温度240℃,电阻率为1020~1022欧·厘米。
导热系数30℃时0.116瓦/(米·开)。
通常的聚苯乙烯为非晶态无规聚合物,具有优良的绝热、绝缘和透明性,长期使用温度0~70℃,但脆,低温易开裂。
此外还有全同和间同立构聚苯乙烯。
全同聚合物有高度结晶性。
普通聚苯乙烯树脂属无定形高分子聚合物,聚苯乙烯大分子链的侧基为苯环,大体积侧基为苯环的无规排列决定了聚苯乙烯的物理化学性质,如透明度高.刚度大.玻璃化温度高.性脆等。
可发性聚苯乙烯为在普通聚苯乙烯中浸渍低沸点的物理发泡剂制成,加工过程中受热发泡,专用于制作泡沫塑料产品。
高抗冲聚苯乙工程力学、机械原理及设计、电子与电子技术、微机原理与应用、模具CAD/CAM、检测技术、
控制工程、模具设计与制造、表面工程新技术、材料成型与设备管理学、防伪技术、市场营销、企业管理
工程力学、机械原理及设计、电子与电子技术、微机原理与应用、模具CAD/CAM、检测技术、
控制工程、模具设计与制造、表面工程新技术、材料成型与设备管理学、防伪技术、市场营销、企业管理
工程力学、机械原理及设计、电子与电子技术、微机原理与应用、模具CAD/CAM、检测技术、
控制工程、模具设计与制造、表面工程新技术、材料成型与设备管理学、防伪技术、市场营销、企业管理
工程力学、机械原理及设计、电子与电子技术、微机原理与应用、模具CAD/CAM、检测技术、
控制工程、模具设计与制造、表面工程新技术、材料成型与设备管理学、防伪技术、市场营销、企业管理
工程力学、机械原理及设计、电子与电子技术、微机原理与应用、模具CAD/CAM、检测技术、
控制工程、模具设计与制造、表面工程新技术、材料成型与设备管理学、防伪技术、市场营销、企业管理
工程力学、机械原理及设计、电子与电子技术、微机原理与应用、模具CAD/CAM、检测技术、
控制工程、模具设计与制造、表面工程新技术、材料成型与设备管理学、防伪技术、市场营销、企业管理
工程力学、机械原理及设计、电子与电子技术、微机原理与应用、模具CAD/CAM、检测技术、
控制工程、模具设计与制造、表面工程新技术、材料成型与设备管理学、防伪技术、市场营销、企业管理
工程力学、机械原理及设计、电子与电子技术、微机原理与应用、模具CAD/CAM、检测技术、
控制工程、模具设计与制造、表面工程新技术、材料成型与设备管理学、防伪技术、市场营销、企业管理
工程力学、机械原理及设计、电子与电子技术、微机原理与应用、模具CAD/CAM、检测技术、
控制工程、模具设计与制造、表面工程新技术、材料成型与设备管理学、防伪技术、市场营销、企业管理
工程力学、机械原理及设计、电子与电子技术、微机原理与应用、模具CAD/CAM、检测技术、
控制工程、模具设计与制造、表面工程新技术、材料成型与设备管理学、防伪技术、市场营销、企业管理
工程力学、机械原理及设计、电子与电子技术、微机原理与应用、模具CAD/CAM、检测技术、
控制工程、模具设计与制造、表面工程新技术、材料成型与设备管理学、防伪技术、市场营销、企业管理
烯为苯乙烯和丁二烯的共聚物,丁二烯为分散相,提高了材料的冲击强度,但产品不透明。
间规聚苯乙烯为间同结构,采用茂金属催化剂生产,是近年来发展的聚苯乙烯新品种,性能好,属于工程塑料。
聚苯乙烯(PS)包括普通聚苯乙烯(GPPS).聚苯乙烯.可发性聚苯乙烯(EPS).高抗冲聚苯乙烯(HIPS)及间规聚苯乙烯(SPS)。
聚苯乙烯(Polystyrene,简称PS)是一种无色透明的热塑性塑料。
通式是[(CH2CHC6H5)n]。
具有高于100摄氏度的玻璃转化温度,因此经常被用来制作各种需要承受开水的温度的一次性容器,以及一次性泡沫饭盒等。
普通聚苯乙烯(GPPS)普通聚苯乙烯树脂为无毒.无臭.无色的透明颗粒,似玻璃状脆性材料.其制品具有极高的透明度,透光率可达90%以上,电绝缘性能好,易着色.加工流动性好,刚性好及耐化学腐蚀性好等。
普通聚苯乙烯的不足之处在于性脆,冲击强度低,易出现应力开裂,耐热性差及不耐沸水等。
2.成型特性及条件
(1)无定形料,吸湿小,流动性差.不易分解,但热膨胀系数大,易产生内应力,流动性较好,可用螺杆或柱塞式注射机成形,喷嘴用直通式或自锁式,但应防止飞边。
(2)宜用高料温,高模温、低注射压力、延长注射时间有利于降低内应力,防止缩孔、变形。
(3)可用各种形式浇口,浇口与塑件圆弧连接,以免取出浇口时损坏塑件,脱模斜度大,顶出均匀。
塑件壁厚均匀,最好不带嵌件,如有嵌件应预热,各面应圆弧连接,不许有缺口、尖角。
3.结构工艺分析
零件壁厚基本均匀,所有壁厚均大于塑件的最小壁厚1mm,注射成型时不会发生填充不足的现象。
4.塑件的尺寸精度分析:
该制件的尺寸均未标注公差,等级精度为6级。
5.塑件的表面质量分析
制品要求外观表面光泽、无杂色,无收缩痕迹,生产批量大,比较容易实现。
二、计算塑件的体积和质量以及选定压力机
1.零件体积及质量估算
单个塑件体积
质量M1=1.05*97.8=102.69g
根据塑件的要求和尺寸初步定为一模六腔,并考虑冷凝料。
总体积V=97.8x4=391.2
总质量M=391.2*1.05=410.76g
2.初选压力机
从实际注射量应在额定注射量的20%~80%之间考虑,初选额定注射量在
以上的卧式注射成型机XS-ZY-125。
XS-ZY-500注射机参数:
一次注射量:
500cm3
柱塞直径:
65mm
最大注射面积:
1000
公称注射压力:
104Mpa
定位圈尺寸:
150mm
喷嘴球半径:
R18mm
喷嘴孔直径:
7.5mm
合模力:
3500kN
模板行程:
700mm
模具厚度:
300~450mm
模板最大开距:
600mm
根据塑件材料为PS查《塑料模具设计资料》表2-36,可得:
材料在70~80℃预干燥3h左右;
温度:
料筒前段 140~160℃
料筒后段 170~190℃
喷 嘴 160~170℃
模 具32~65℃
压力:
注塑压力 60~110Mpa
时间:
高压时间 0~3s
保压时间 15~45s
冷却时间 15~60s
成型时间 40~120s
三、注射模结构设计
1.浇口形式的确定:
可能的浇口形式有:
重叠式浇口、侧浇口、扇形浇口、点浇口和潜伏式浇口等。
其中潜伏式浇口去除浇口留下的痕迹在制品内侧,对制品外观影响不大;点浇口的制造较为复杂,点浇口必须采用结构复杂的三板模;重叠式浇口制造简单,对制品外观影响也不大。
但是该制品为密封原件,需要表面的平整,所以为满足使用要求,确定用点浇口形式。
2.模具型腔排列方式的确定
根据材料的尺寸及成型性能要求,本模具采用一模四腔,以达到大批量生产的要求。
图3型芯排布图
3.模具分型面的选择
由以上分型面位置的确定可知,为了便于脱模,分型面的位置应设在塑件断面尺寸最大的地方,还要不影响制品的外观,根据塑件的结构特征,选定水平分型面。
同时,由于浇口形式为点浇口,需要设计成三板模。
可达到降低模具的复杂程度,减少模具加工难度,又便于成型后脱模的效果。
4、注射模浇注系统设计
浇注系统一般由主所示流道、分流道、浇口、冷料穴四部分组成。
(1)主流道的设计
XS-ZY-125型注射机喷嘴的有关尺寸为:
喷嘴前端孔径d1=
7.5mm
喷嘴后端球面半径R1=18mm
根据模具主流道球面半径R=R1+(1~2)mm及小端直径d=d1+(0.5~1)mm,故取主流道球面半径R=
20mm,
小端面直径d=
8.5mm。
为了便于将凝料从主流道中拔出,将主流道设计成圆锥形,其斜度为:
3°,取大端直径D=
12mm。
(2)分流道的设计
为了便于制造,本模具分流道为半圆形,只设在定模板一侧。
分流道宽度同主流道直径一样,既B=10mm,高度h=8mm,长度由排样确定,取l=34mm。
(3)浇口设计
根据塑件的成型要求及型腔的排列方式,选用点浇口较为理想。
点浇口直径的估算:
d=0.206nt^(1/2)×A^(1/4)=1.32≈1.4mm
式中,n为材料系数,t为塑件壁厚,A为塑件表面积。
(4)冷料穴的设计
冷料穴设置在主流道的末端,,其他相关尺寸由《塑料模具设计资料》表2-119所得。
5.推出机构的选择
顶出机构的基本要求是:
使塑件在顶出过程中不会损坏变形;保证塑件在开模的过程中留在设置有顶出机构的动模内。
其中一次顶出机构是最常用的顶出机构,此机构只需一次动作就能使塑件脱模。
本模具选用推杆一次顶出机构。
(1)推杆数量及结构形式
根据推杆布置的许可空间,每个制品设1根推杆,供6根;推杆头部直径为
5mm,为增加其刚度,采用阶梯推杆,尾部直径为
10mm。
(2)复位装置设计
常用复位机构有弹簧复位机构和复位杆复位机构。
因弹簧不可靠,所以此处选用复位杆复位。
(3)拉料杆
如前浇注系统所示,采用N型拉料杆,公称直径
6mm
(4)顶出距离
为确保顶出时塑件能完全脱离动模,顶出距离不小于15mm。
6.合模导向机构的确定
(1)导柱结构形式
为便于加工导柱导套安装孔,获得较好的技术经济效益,使用带头导柱。
(2)导柱的布置
为确保动模和定模只能按一个方向合模,采用等直径导柱的不对称布置。
为保护型芯不受损坏,导柱设在动模一侧,即正装。
7.排气机构
因为该零件为小型零件,一模六腔,所以利用模具分型面及推杆之间的间隙排气即可,不必单独考虑排气方式。
8.温控系统的计算
该塑件在注射成型时,需要设置要温控系统,模具温度应在30~40℃之间,因而主要是塑件的冷却。
塑件表面积较大,重点是冷却型腔,具体措施是布置冷却水管。
(1)冷却水管直径
8mm。
(2)冷却回路的形式型腔和型芯一样均采用直通的形式。
9.标准模架的选择
(1)初选标准模架
根据凹模镶快的外形尺寸、型腔的排列方式,各成型板的厚度要求,并考虑斜导柱的安装空间和滑块的导滑长度和注射机的最大装模厚度,初选模架为:
2025-DAI-A板80-B板25-180-I
模架规格设计选定如下:
1塑件的高度为52mm,型腔设计在定模板A上,于是A值由此确定取为120mm,动模板厚度取30mm,动模支承板厚度为30mm;
②由之前确定,用推杆推出制件;
③推杆固定板厚20mm,支架改为高90mm。
(2)确定闭模高度
由以上的设计各模板厚度的选定,模具厚度M=25+35+120+30+30+90+40mm=370mm。
10.注射机有关参数的校核和最终选择
(1)注射量的校核
由冷料穴以及浇流道的大概体积为98cm3,则可大致确定一个成型周期内塑料的总体积为392cm3左右。
而注射量应满足:
V=nVz+
≤0.8
由此可得,V=392
<0.8*
=400
,满足要求。
(2)锁模力的校核
型腔内熔体压力P=kPa=0.4×40Mpa=16Mpa
塑件在分型面的投影面积
=1/4×π×21^2=0.35
浇注系统在分型面的投影面积
≈0.4
锁模力应满足:
F≥
=P(n
+
)=16×(6×0.35+0.4)
=4KN
所以F=900KN>45KN满足要求。
(3)模具闭合高度的校核
安装模具的厚度应满足:
Hmin+10mm<H<Hmax-5mm
设计模具厚度H总=370mm
XS-ZY-500型,最大装模高度Hmax=460mm,最小装模高度Hmin=295mm
H总=370mm,满足模具厚度安装要求。
(4)模具开模行程校核
模具开模行程应满足:
Sm其中:
Sz为最大开模行程,查注射机XS-ZY-500型Sz=700mm,
Sm为模具的开模行程;
以为模具的开模行程
Sm=Hm+H1+H2+a+(5~10)mm=80+20+20+20+10.5+10≈161mm
所以Sm(5)模具安装部分的校核
该模具的外形尺寸为200mm×250mm,XS-Z-125型注射机模板最大安装尺寸为200mm×300mm,故能满足模具安装要求。
(6)注射机压力的校核
注射机压力应满足:
P机≥P塑
P机——注射机的最大注射压力,Mpa或N/cm3
P塑——成型塑件所需的注射压力,Mpa或N/cm3
该注射产品属于中型塑件,取80Mpa,XS-ZY-500注射机的最大注射压力P机=104Mpa,可见XS-ZY-500注射机满足PP注射压力的要求。
综合验证,XS-ZY-500型注射机完全能满足此模具的注射要求。
四、有关模具工作部分设计计算
为简便计算,凡与脱模方向垂直的面不考虑磨损量,与脱模方向平行的面才考虑磨损。
考虑磨损主要从模具的使用寿命来选定,磨损值随产量的增加而增大;此外,还应考虑塑料对钢材的磨损情况;同时还应考虑模具材料的耐模性及热处理情况,型腔表面是否镀铬、氮化等。
有资料介绍,中小型模具的最大磨损量可取塑件总误差的1/6(常取0.02~0.05mm),而对于大的模具则应取1/6以下。
但实际上对于聚烯烃(如像PP)、尼龙等塑料来说对模具的磨损是很小的,对小型塑件来说,成型零件磨损量对塑件的总误差有一定的影响,而对于大的塑件来说影响很小。
在以上理论基础上,下面按平均收缩率来计算成型尺寸:
1.型腔与型芯的设计:
该制件采用一模六腔的结构形式,考虑加工的难易程度、材料的价值和利用率等因素,凹模拟采镶嵌式结构,根据分流道与浇口的设计要求,分流道和浇口均设在凹模上。
凸模主要是与凹模结合构成的型腔座,采用整体式的结构形式。
2.成型零部件的尺寸计算:
成型零件的强度、刚度分析:
注射模在其工作过程中需要承受多种外力,如注射压力、保压力、合模力和脱模力等。
如果外力过大,注射模及其成型零部件将会产生塑性变形或断裂破坏,或产生较大的弹性弯曲形变,引起成型零部件在他们的对接面或粘合面处出现较大的间隙,由此而引发溢料及飞边现象,从而导致整个模具失效或无法达到技术质量要求。
因此,在模具设计时,成型零件的强度和刚度计算和校核是必不可少的。
一般来说,凹模型腔的恻壁厚度和底部厚度可以利用强度计算决定,并且凹模和型心通常都是由制品内形成或制品上的孔决定,设计时应该对他们进行强度校核,但是,由于在设计时采用的是凸肩式矩形型腔镶嵌在动模板中,动模板有足够的厚度和强度保护型腔,据经验可知,此模具的型腔在浇注成型时是不可能被破坏的,故无需对型腔进行侧壁和底板厚度的计算与较核。
此型腔侧壁厚取经验值即可
由《塑料模具设计资料》表2-16查得的平均收缩率为S=1.5%~2.5%,故平均收缩率为Scp=0.02。
根据对塑件尺寸公差分析,模具的制造公差取δz=Δ/3。
成型零件尺寸计算如下:
型腔径向尺寸:
型腔成型部分的深度:
型芯的径向尺寸:
型芯成型部分的高度:
3.其他零件的设计计算:
(1)导柱长度计算
导柱导向机构是保证动定模或上下模合模时,正确定位和导向的零件。
导柱导向机构的作用:
定位件用:
模具闭合后,保证动定模或上下模位置正确,保证型腔的形状和尺寸精确,在模具的装配过程中也起定位作用,便于装配和调整。
导向作用:
合模时,首先是导向零件接触,引导动定模或上下模准确闭合,避免型芯先进入型腔造成成型零件损坏。
承受一定的侧向压力。
导柱导套的选择。
D=20mm,L=100mm。
导柱和导套与固定板采取H7/m6过渡配合,导柱导向段与导向孔采取H7/f7间隙配合。
(2)推杆长度的计算
推杆长度L=120mm。
五、模具安装
(1)清理模板平面定位孔及模具安装表面上的污物、毛刺;
(2)因模具的外形尺寸不大,故采用整体安装法。
先在机器下面的两根导轨上垫好板,模具从侧面进入机架间,定模入定位孔,并放正,慢速闭合模板,压紧模具,然后用压板或螺钉压紧定模,并初步固定动模,然后慢速开闭模具,找正动模,应保证开闭模具时平稳,灵活,无卡住现象,然后固定动模;
(3)调节锁模机构,保证有足够开模距及锁模力,使模具闭合适当;
(4)慢速开启模板直至模板停止后退为止,调节顶出装置,保证顶出距离。
开闭模具观察顶出机构的运动情况,动作是否平衡、灵活、协调。
(5)模具装好后,待料筒及喷嘴温度上升到距离预定温度约20℃。
六、设计小结
通过长时间的努力,课程设计终于可算是划上一个句号了。
本次设计是一个全面性的设计,是对塑料模课程的一个总结一次回顾。
本次毕业设计翻阅了大量的参考书,使我对《塑料成型工艺与模具设计》及相关知识又进行一次从新的整理、理论联系实际,为我以后搞模具做了一个很好的准备。
更重要的是,通过本次设计对我所掌握的塑料模模具知识实际应用能力起到了检验的作用,通过系统设计,知道自己的不足和缺陷。
通过这课程设计,可以让我们从中获得平时未掌握的知识,或重新温新一下所学的知识。
进一步地了解,进一步地改善。
可以借此机会锻炼自己独立思考能力、动手能力和其它一些综合能力。
同时,还可以为今后的工作奠定一个良好的基础。
在设计过程中我们始终结合计算机进行设计,提高了我们对UG,AutoCAD等软件的应用能力。
同时,还更懂得如何查阅资料、手册等一系列工具书。
通过了本次设计我们已初步掌握了工程技术人员的设计思想,掌握了模具的相关知识,以基本能独立完成一套塑料模模具设计与制造。
在设计中,通过查阅资料,向同学和老师请教,进一步地了解注塑模具的实际设计和制造情况。
在设计中广泛采用标准件。
设计参数的选择不仅来自课本和资料,还根据实际情况来选择和使用。
在设计中得到最大的收获是:
1.提高查阅参考资料的能力。
能在不同的参数推荐值中选择适合本设计的最佳方法。
2.继续巩固各种基础知识。
锻炼自己的动手能力、独立思考问题、解决问题的能力。
3.为将来的工作奠定了一个良好的、稳定的基础。
通过设计,也发现自己的很多不足和有待提高的知识,主要有:
1.各门基础课知识掌握的不够扎实,运用起来不够熟练。
2.实际工作能力还有待提高,设计与社会上的实际生产还有很大差距。
3.专业软件的使用能力(包括熟练度和使用的广度)还需要再提高一个层次。
通过运用CAD/CAM软件来更好的完成和优化设计。
通过这样,来进一步地充实自我、增强自我能力、提高自我水平。
总而言之,我认为,这次毕业设计虽然还存在这样那样的错误和缺陷,但通过这次设计我又学到了很多的知识,把自己的工作能力提高到一个更高的层次。
设计中存在的问题请老师批评指正。
同时感谢课程设计中老师的指导和帮助!
七、参考文献
1、塑料模具设计资料(校内使用)自编;
2、塑料成型工艺与模具设计,齐晓杰主编,机械工业出版社;
3、画法几何与机械制图,冯开平左宗义主编,华南理工大学出版社;
4、塑料注射成型模具设计,陈世煌陈可娟主编,国防工业出版社;
单个塑件体积V1=97.8
总体积V=391.2
选用卧式注射成型机XS-ZY-500
闭模高度370mm
相关参数的校核都满足
推杆长度
L=120mm