化工原理谭天恩简答重点资料.docx
《化工原理谭天恩简答重点资料.docx》由会员分享,可在线阅读,更多相关《化工原理谭天恩简答重点资料.docx(24页珍藏版)》请在冰豆网上搜索。
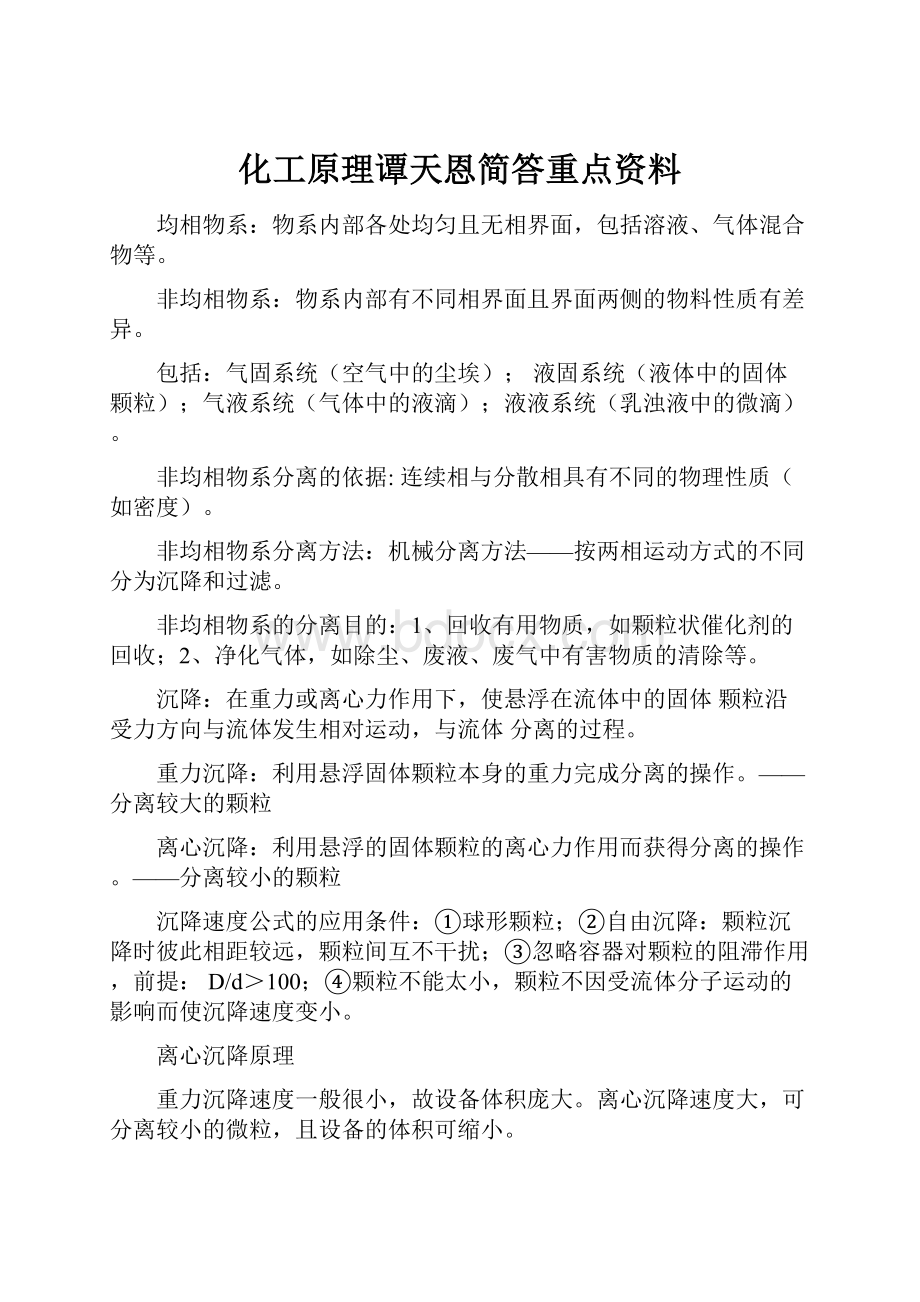
化工原理谭天恩简答重点资料
均相物系:
物系内部各处均匀且无相界面,包括溶液、气体混合物等。
非均相物系:
物系内部有不同相界面且界面两侧的物料性质有差异。
包括:
气固系统(空气中的尘埃);液固系统(液体中的固体颗粒);气液系统(气体中的液滴);液液系统(乳浊液中的微滴)。
非均相物系分离的依据:
连续相与分散相具有不同的物理性质(如密度)。
非均相物系分离方法:
机械分离方法——按两相运动方式的不同分为沉降和过滤。
非均相物系的分离目的:
1、回收有用物质,如颗粒状催化剂的回收;2、净化气体,如除尘、废液、废气中有害物质的清除等。
沉降:
在重力或离心力作用下,使悬浮在流体中的固体颗粒沿受力方向与流体发生相对运动,与流体分离的过程。
重力沉降:
利用悬浮固体颗粒本身的重力完成分离的操作。
——分离较大的颗粒
离心沉降:
利用悬浮的固体颗粒的离心力作用而获得分离的操作。
——分离较小的颗粒
沉降速度公式的应用条件:
①球形颗粒;②自由沉降:
颗粒沉降时彼此相距较远,颗粒间互不干扰;③忽略容器对颗粒的阻滞作用,前提:
D/d>100;④颗粒不能太小,颗粒不因受流体分子运动的影响而使沉降速度变小。
离心沉降原理
重力沉降速度一般很小,故设备体积庞大。
离心沉降速度大,可分离较小的微粒,且设备的体积可缩小。
离心沉降分离设备:
旋流(旋风或旋液)分离器和沉降离心机。
前者的特征:
设备静止、流体旋转;后者:
机器带动流体一起旋转。
旋风分离器结构和工作原理:
含尘气体高速切向进入分离器,在外筒与排气管间呈螺旋形旋转向下,到锥底后以相同的旋向折转向上至上部排气管流出。
夹带的颗粒在螺旋流中均受离心力作用向器壁方向抛出,在重力作用下沿壁面下落到排灰口。
评价旋风分离器性能的主要指标:
分离性能和气体的压力降
旋风分离器的特点:
流量大、压头低。
(1)气体的膨胀或压缩引起的不可逆机械能损失;
(2)气流旋转引起的动能损失;(3)摩擦阻力损失以及各个部位的局部阻力损失等。
阻力系数主要由旋风分离器的结构决定。
选择旋风分离器的型式的主要依据:
生产能力、允许的压降、粉尘
性质、要求的分离效率。
选型时,应在高效率与低压降之间作权衡:
不同型号的旋风分离器压降还与其形状有关:
短粗形的旋风分离器压降较小,处理量大,但分离效率低;长径比大且出入口截面小的细长形设备压降大,处理量小,但分离效率高。
过滤:
在重力或压力作用下,利用多孔过滤介质,使液体通过而将固体颗粒截留,实现悬浮液的固-液分离。
原悬浮液——滤浆,通过过滤介质的液体——滤液,截留在过滤介质上的固体颗粒堆积层——滤渣或滤饼.:
.过滤介质
作用:
滤液通过、截留颗粒,支撑滤饼。
特性:
多孔、理化性质稳定、机械强度高、可反复使用。
可压缩滤饼:
由非刚性颗粒形成的滤饼,在压力差作用下会变形,过滤压力提高时使过滤阻力明显增大。
不可压缩滤饼:
由刚性颗粒形成的滤饼,在过滤过程中颗粒形状和颗粒间的空隙率保持不变。
过滤的操作方式
过滤操作中的主要阶段,在过程中滤饼不断增厚、阻力不断上升,流体的通过能力则不断减小;洗涤:
无论是以滤饼还是滤液为产品,都有必要在卸料之前用清液置换滤饼中存留的滤液并且洗涤滤饼;脱湿:
以滤饼为产品时洗涤后还可用压缩空气进行脱湿;卸料:
将滤饼从过滤介质上移去;清洗过滤介质:
使被堵塞的网孔“再生”,以便重复使用。
过滤操作分为:
间歇式:
对以上各步骤分阶段操作;连续式:
连续操作完成全部或其中部分阶段。
板框压滤机:
通过直接给悬浮液加压,迫使其穿过过滤介质来实现过滤。
结构:
由交替排列的滤板、滤框与板框间的滤布叠合组装压紧而成。
板框数由工艺要求在机座长度范围内灵活调节。
组装后,板框的四角位置形成连通的通道,由阀门控制悬浮液、滤液及洗液的进出。
过滤:
悬浮液从通道进入滤框,滤液在压力下穿过滤框两边的滤布、沿滤布与滤板凹凸表面之间形成的沟道流下,既可单独由每块滤板上设置的出液旋塞排出,称为明流式;也可汇总后排出,称为暗流式。
洗涤:
洗涤液由洗涤板上的通道进入其两侧与滤布形成的凹凸空间,穿过滤布、滤饼和滤框另一侧的滤布后排出。
洗涤液的行程(包括滤饼和滤布)约为过滤终了时滤液行程的2倍,而流通面积却为其1/2,故洗涤速率约为过滤终了速率的1/4。
每个操作循环由组装、过滤、洗涤、卸料、重整五个阶段。
优点:
结构简单紧凑,过滤面积大,可承受的压力高。
缺点:
间歇式操作,所费的装、折、清洗时间较长,劳动强度大,生产效率较低。
转筒真空过滤机
结构与原理:
转筒表面开孔,外面覆盖滤布,内部分隔成互不相通的若干扇形区,各区都有管道通至轴心,轴心处装分配头,分配头由转动盘与固定盘构成,转动盘小孔与转筒表面的一段相通,固定盘上开三个凹槽,分别与真空抽滤系统、洗水抽吸回收系统和压缩空气反吹系统相通。
转动过程借助分配头作用使各区与各系统连接和断开,每转一周,过滤表面任一部分都顺序完成过滤、洗涤、吸干、吹松、刮渣等阶段的连续操作。
过滤操作:
转筒旋转一周,每一个扇形区依次完成真空过滤、洗涤、吸干滤饼和压缩空气吹松、刮刀卸料等全部操作。
转筒转速多在0.1~3r/min,浸入悬浮液中的吸滤面积约占总表面的30~40%。
滤饼厚度范围大约3~40mm。
优点:
连续进料,操作自动化,便于在转鼓表面预涂助滤剂后用于黏、细物料的过滤。
缺点:
过滤推动力有限,滤饼含液量较大,常达30%。
传热的三种基本方式
一、热传导:
依靠物体中微观粒子的热运动,热量从物体内部高温部分传递到低温部分或者相互接触的物体之间由高温物体传递到低温物体的过程,如固体中的传热;
特点:
单纯的热传导过程中,物体各部分之间不发生相对位移,即没有物质的宏观位移。
从微观角度来看,气体、液体、导电固体和非导电固体的导热机理各不相同:
气体:
气体分子做不规则热运动时相互碰撞的结果
导电固体:
自由电子在晶格间的运动;良好的导电体中有相当多的自由电子在晶格之间运动,正如这些自由电子能传导电能一样,它们也能将热能从高温处传到低温处。
非导电固体:
非导电体导热是通过晶格结构的振动来实现的
液体:
存在两种不同的观点,类似于气体和非导电固体。
二、对流:
流体各部分质点发生相对位移而引起的热量传递过程,对流只能发生在流体中。
通常把传热固体表面与接触流体的传热也称为对流给热,简称给热。
自然对流:
静止流体内部由于温度不同、密度不同,造成流体内部发生对流而传热。
强制对流:
流体在外力的强制作用下运动而发生的对流。
三、辐射传热:
以电磁波传递能量的现象。
物体会因各种原因发射出辐射能
热辐射:
物体因热的原因发出辐射能的过程,高温物体把热能转变成辐射能,以电磁波的形式进行传热现象。
任何物体能以电磁波的形式把热能辐射出来,也能把其他物体辐射的电磁波吸收并转变成热能。
特点:
热辐射既是能量的转移,又伴有能量形式的转化。
此
外,辐射能可以在真空中传播,不需要任何物质作媒介。
高温下,辐射传热是主要传热方式。
热传导
一、温度场和等温面
温度场:
某一时刻,物体(或空间)各点的温度分布
不稳定温度场:
各点的温度随时间而改变的温度场。
稳定温度场:
任一点的温度均不随时间而改变的温度场
等温面:
在同一时刻,温度场中所有温度相同的点组成的面。
不同温度的等温面不相交。
温度梯度:
两等温面的温度差t与其间的垂直距离n之比,在n趋于零时的极限(表示温度场内某一点沿等温面法线方向上的温度变化率)
温度梯度是向量,其方向垂直于等温面,温度增加方向为正
傅立叶定律
热传导速率(单位时间内传导的热量)与温度梯度及垂直于法向的导热面积成正比。
物理意义:
温度梯度为1时,单位时间内通过单位传热面积的热通量;数值上等于单位温度梯度下的热通量,
,导热性能越好。
两流体通过间壁的传热
直接混合式传热:
冷热两种流体直接接触,在混合过程中进行热交换,如凉水塔。
间壁式换热:
参与传热的两种流体在固体间壁的两侧,冷热流体在不直接接触的条件下通过固体间壁进行热量交换
换热器换热过程:
固体间壁的导热;流体与壁面间的传热——对流给热。
流体在间壁两侧作湍流流动,近壁处分为:
层流底层、过渡层、湍流主体。
过渡区域:
温度分布不像湍流主体那么均匀,也不像层流底层变化明显,传热以热传导和对流两种方式共同进行。
实质上对流传热是流体的对流与热传导共同作用的结果。
逆流和并流传热的平均温差的特点
当传热量一定时,逆流操作所需的传热面积小于并流操作
当加热任务一定时,采用逆流传热可最大限度地利用热能,加热剂的用量少
并流的优点:
当工艺要求被加热流体不得高于某一温度,或被冷却的流体不得低于某一温度,采用并流较易控制。
错流和折流
错流:
两种流体的流向垂直交叉。
折流:
一流体只沿一个方向流动,另一流体作双程流动流动;或者两流体都反复折回。
复杂流:
几种流动型式的组合。
大容积自然对流:
传热面放置在大空间内,四周没有阻碍自然对流的物体存在,如换热设备或管道的热表面向周围大气的散热、无搅拌时釜内液体的加热。
大容积自然对流的给热系数仅与Gr数和Pr数有关
提高对流传热系数的途径
增加湍动程度,提高传热系数
1、提高壳程
2、加强壳程的湍动程度,如加折流挡板或添加物
有相变的传热过程
蒸汽冷凝传热:
膜状冷凝,滴状冷凝
膜状冷凝:
冷凝液体能润湿壁面,在壁面上形成一层完整的液膜。
特点:
液膜成为壁面与蒸汽间传热的主要热阻。
冷凝液受重力沿壁流下,液膜越往下越厚,给热系数越小,如果壁面足够高,下部液膜中冷凝液会出现湍流流动,又使给热系数增加
滴状冷凝:
冷凝液不能完全润湿壁面,在壁面上形成小液滴,沿壁面落下时,使壁面重新暴露在蒸汽中。
特点:
滴状冷凝时没有完整液膜,热阻很小,给热系数约为膜状冷凝的5~10倍甚至更高
液体沸腾传热
大容积沸腾:
加热面浸在有自由表面的液体中所发生的沸腾,液体运动由自然对流和汽泡扰动引起。
管内沸腾:
液体在管内流动过程中受热沸腾。
产生的汽泡不能自由上浮,而是被迫与液体一起流动,形成汽-液两相流动,沿途吸热,直至全部汽化
大容积沸腾传热过程的机理
沸腾机理:
汽泡生成、长大、脱离并上升至液体表面。
汽泡生成的条件:
液体过热;加热壁面上存在汽化核心。
汽化核心:
加热面上若干粗糙不平处,由于表面张力较小或微量气体或蒸汽附着等原因,使新相容易生成,为气泡形成提供条件
沸腾曲线:
过热度t=tw-ts增加,出现沸腾传热给热系数α与t的变化关系
辐射传热
热辐射:
物体因热的原因发出辐射能的过程称为热辐射
辐射传热:
辐射传热是不同物体间相互辐射和吸收的综合结果
热射线:
可见光线和红外光线统称为热射线
黑体(绝对黑体):
能全部吸收辐射能的物体,即A=1。
例如没有光泽的黑墨表面,吸收率A=0.96~0.98。
镜体(绝对白体):
能全部反射辐射能的物体,即R=1。
例如表面抛光的铜,反射率R=0.97。
透热体:
能全部透过辐射能的物体,即D=1。
例如单原子和对称双原子气体O2、N2、H2等。
灰体:
能够以相等的吸收率吸收所有波长辐射能的物体。
特点:
吸收率A与波长无关;为不透热体(A+R=1)
物体发射能力物体在一定的温度下,单位表面积、单位时间内所发射的全部波长的总能量。
用E表示,单位:
W/m2。
单色发射能力物体在一定的温度下,单位表面积、单位时间内的发射某一特定波长的能力
气体热辐射的特点:
不同气体发射能力不同:
对称双原子——透热体;
不对称双原子和多原子气体——有大的发射能力和吸收率
气体辐射对波长具有选择性:
固体能发射和吸收全部波长范围的辐射能,气体只在某波段具有吸收和发射能力;
气体发射和吸收辐射能是在整个气体体积内进行的:
灰体的辐射和吸收发生在物体表面。
蒸发:
将稀溶液在沸腾状态下进行浓缩的单元操作。
蒸发的目的:
溶液中溶剂的汽化,获得溶剂产品或不挥发溶质产品。
蒸发的必要条件:
不断供给热能,不断排除蒸汽,溶剂易挥发。
真空蒸发:
减压(真空)下蒸发。
目的:
降低溶液沸点。
优点:
真空下溶液的沸点低,加热蒸汽与沸腾液体间温差大,减小蒸发器的传热面积;利用低压蒸汽或废气作热源;适于热敏性物料;沸点低,蒸发器热损失小。
缺点:
耗能大;低压沸点低,粘度大,给热系数减小。
单效蒸发:
二次蒸汽不再利用,1kg水/1kg多加热蒸汽
多效蒸发:
加热蒸汽通入蒸发器,液体受热沸腾产生的二次蒸汽加以利用引入到下一级蒸发器,多个蒸发器依次连接形成多效蒸发。
蒸发意义:
提高蒸汽的利用率(或经济程度)。
蒸发过程的特点:
(1)沸点升高:
(2)能耗大:
(3)溶液的特性决定蒸发器的结构特性。
温度差损失的原因1)溶液中含有溶质导致沸点升高引起的温度差损失;
(2)加热管内不同高度静压力不同,使溶液沸点升高,(3)管内流体阻力损失使沸点升高,存在温度差损失
杜林规则:
说明溶液的沸点和相同压强下标准溶液沸点之间呈线性关系
传质过程导论
单元操作动量传递流体输送、机械分离、沉降、流态化等热量传递加热、冷却、蒸发等质量传递吸收、蒸馏、萃取、吸附、干燥、膜分离等
扩散原理
分子扩散在静止或层流流体内部,若某一组分存在浓度差,则因分子无规则的热运动使该组分由浓度较高处传递至浓度较低处这种现象称为分子扩散。
Fick定律扩散通量:
单位时间内通过垂直于扩散方向的单位截面积扩散的物质量,J表示,kmol/(m2·s)。
Fick定律:
对双组分体系,在稳态下组分A在扩散方向上任一点处的扩散通量与该处A的浓度梯度成正比。
几点说明:
A、与导热不同,分子扩散的特点是:
当一个分子沿扩散方向移去后,留下的空位由其他分子填空。
B、对JA的定义是通过“分子对称”的截面:
既有一个净A分子通过这截面,也有相等的净B分子反方向通过同一截面,填补A的净空位。
C、分子对称面在空间上既可以是固定,也可以是移动的。
漂流因子(DriftFactor):
其大小反映了总体流动对传质速率的影响程度,其值>1,为总体流动使传质速率较分子扩散增大的倍数。
分压PA高(PB低)时,漂流因数大,总体流动的影响大。
分压PA低(PB高)时,漂流因数近似等于1,总体流动的影响小。
单向扩散与等摩尔相互扩散相差无几。
扩散系数:
单位浓度梯度下的扩散通量,反映某组分在一定介质中的扩散能力,是物质的一种传递属性,特性常数之一;D,m2/s。
D的影响因素:
A、B、T、P、浓度。
湍流扩散特点:
1)存在着杂乱的质点涡流运动:
既有主体方向上的整体流动也有其他方向上的脉动运动。
2)质点脉动引起的物质扩散要比分子扩散大得多3)涡流或脉动的复杂性,尚不能从理论上进行分析计算。
双膜理论:
1)相互接触的两流体间存在着稳定的相界面,界面两侧各存在着一个很薄的流体膜层。
溶质以分子扩散方式通过此两膜层。
(2)相界面没有传质阻力,即溶质在相界面处的浓度处于相平衡状态3)在膜层以外的两相主流区由于流体湍动剧烈,传质速率高,传质阻力可以忽略不计,相际的传质阻力集中在两个膜层内。
吸收分离操作:
利用混合气体中各组分(component)在液体中溶解度(solubility)差异,使某些易溶组分进入液相形成溶液(solution),不溶或难溶组分仍留在气相(gasphase),从而实现混合气体的分离
气体吸收是混合气体中某些组分在气液相界面上溶解、在气相和液相内由浓度差推动的传质过程
物理吸收:
吸收过程溶质与溶剂不发生显著的化学反应,可视为单纯的气体溶解于液相的过程。
如用水吸收二氧化碳、用水吸收乙醇或丙醇蒸汽、用洗油吸收芳烃等
化学吸收:
溶质与溶剂有显著的化学反应发生。
如用氢氧化钠或碳酸钠溶液吸收二氧化碳、用稀硫酸吸收氨等过程。
化学反应能大大提高单位体积液体所能吸收的气体量并加快吸收速率。
但溶液解吸再生较难。
单组分吸收:
混合气体中只有单一组分被液相吸收,其余组分因溶解度甚小其吸收量可忽略不计。
多组分吸收:
有两个或两个以上组分被吸收
非等温吸收:
体系温度发生明显变化的吸收过程
等温吸收:
体系温度变化不显著的吸收过程。
吸收操作的用途:
(1)制取产品用吸收剂吸收气体中某些组分而获得产品。
如硫酸吸收SO3制浓硫酸,水吸收甲醛制福尔马林液,碳化氨水吸收CO2制碳酸氢氨等。
(2)分离混合气体吸收剂选择性地吸收气体中某些组分以达到分离目的。
如从焦炉气或城市煤气中分离苯,从乙醇催化裂解气中分离丁二烯等。
(3)气体净化一类是原料气的净化,即除去混合气体中的杂质,如合成氨原料气脱H2S、脱CO2等;另一类是尾气处理和废气净化以保护环境,如燃煤锅炉烟气,冶炼废气等脱除SO2,硝酸尾气脱除NO2等。
吸收剂的选择
(1)对溶质有较大的溶解度。
溶解度上升,溶剂用量下降,溶剂再生费用下降;溶解度上升,对一定的液气比,吸收推动力上升,吸收传质速率上升,完成一定的传质任务所需设备尺寸下降;
(2)良好的选择性,即对待吸收组分的溶解度大,其余组分溶解度度小;
(3)稳定不易挥发,以减少溶剂损失;(4)粘度低,有利于气液接触与分散,提高吸收速率;
(5)无毒、腐蚀性小、不易燃、价廉等。
吸收过程的气液相平衡关系
平衡问题:
物质传递的方向和限度;
传质速率问题:
传质推动力和阻力。
过程快慢的问题。
相平衡:
相间传质已达到动态平衡,从宏观上观察传质已不再进行。
平衡状态下溶质在气相中的分压称为平衡分压或饱和分压,与之对应的液相浓度称为平衡浓度或气体在液体中的溶解度。
溶解度曲线:
在一定温度、压力下,平衡时溶质在气相和液相中的浓度的关系曲线
亨利定律当总压不太高时,一定温度下的稀溶液的溶解度曲线近似为直线,即溶质在液相中的溶解度与其在气相中的分压成正比。
传质过程的方向
若系统气、液相浓度(y,x)在平衡线上方,则体系将发生从气相到液相的传质,即吸收过程。
若系统气、液相浓度(y,x)在平衡线下方,则体系将发生从液相到气相的传质,即解吸过程
若系统气、液相浓度(y,x)处于平衡线上,则体系从宏观上讲将不会发生相际间的传质,即系统处于平衡状态。
吸收过程是溶质由气相向液相转移的相际传质过程,可分为三个步骤:
(1)溶质由气相主体扩散至两相界面气相侧(气相内传质);
(2)溶质在界面上溶解(通过界面的传质);
(3)溶质由相界面液相侧扩散至液相主体(液相内传质)。
双膜理论的基本论点是
(1)相互接触的两流体间存在着稳定的相界面,界面两侧各存在着一个很薄(等效厚度分别为1和2)的流体膜层。
溶质以分子扩散方式通过此两膜层。
(2)相界面没有传质阻力,即溶质在相界面处的浓度处于相平衡状态
3)在膜层以外的两相主流区由于流体湍动剧烈,传质速率高,传质阻力可以忽略不计,相际的传质阻力集中在两个膜层内
吸收塔的计算
设计型计算:
按给定的生产任务和工艺条件来设计满足任务要求的单元设备。
操作型计算:
根据已知的设备参数和工艺条件来求算所能完成的任务。
设计计算的主要内容与步骤
计算依据:
物系的相平衡关系和传质速率
(1)吸收剂的选择及用量的计算;
(2)设备类型的选择;(3)塔径计算;4)填料层高度或塔板数的计算;(5)确定塔的高度;(6)塔的流体力学计算及校核;7)塔的附件设计
传质系数包含了传质过程速率计算中一切复杂的、不易确定的影响因素,其数值的大小主要取决于物系的性质、操作条件及设备的性能(填料特性)三个方面
传质系数的获取途径:
(1)实验测定;
(2)针对特定体系的经验公式;(3)适用范围更广的准数关联式。
蒸馏分离操作:
利用液体混合物中各组分(component)挥发性(volatility)的差异,以热能为媒介使其部分汽化,从而在汽相富集轻组分,液相富集重组分,使液体混合物得以分离的方法。
蒸馏操作的用途:
许多生产工艺常常涉及到互溶液体混合物的分离问题,如石油炼制品的切割,有机合成产品的提纯,溶剂回收和废液排放前的达标处理等等。
分离的方法有多种,工业上最常用的是蒸馏或精馏。
简单蒸馏或平衡蒸馏使用条件:
一般用在混合物各组分挥发性相差大,对组分分离程度要求又不高的情况下。
精馏:
在混合物组分分离纯度要求很高时采用。
特殊精馏:
混合物中各组分挥发性相差很小,或形成恒沸液,难以或不能用普通精馏加以分离时,借助某些特殊手段进行的精馏。
间歇精馏:
多用于小批量生产或某些有特殊要求的场合。
连续精馏:
多用于大批量工业生产中。
常压蒸馏:
蒸馏在常压下进行。
减压蒸馏:
用于常压下物系沸点较高,使用高温加热介质不经济或热敏性物质不能承受的情况。
减压可降低操作温度。
加压蒸馏:
对常压沸点很低的物系,蒸汽相的冷凝不能采用常温水和空气等廉价冷却剂,或对常温常压下为气体的物系(如空气)进行精馏分离,可采用加压以提高混合物的沸点。
多组分精馏:
例如原油的分离。
双组分精馏:
例如乙纯-水体系的分离。
连续接触(微分接触):
气、液两相的浓度呈连续变化。
如填料塔
级式接触:
气、液两相逐级接触传质,两相的组成呈阶跃变化。
如板式塔。
蒸馏分离的物系由加热至沸腾的液相和产生的蒸汽相构成。
相平衡关系既是组分在两相中分配的依据,也为确定传质推动力所必需,是蒸馏过程分析和设计计算的重要基础。
汽、液两相物系分为理想物系与非理想物系两大类。
理想物系:
液相为理想溶液、汽相为理想气体的物系。
理想溶液服从拉乌尔定律,理想气体服从理想气体定律或道尔顿分压定律。
理想溶液的汽液平衡——拉乌尔定律
相平衡图或简称相图,对于双组分汽、液两相,当固定一个独立变量时,可用二维坐标中的曲线图来表示两相的平衡关系。
理想溶液:
组分分压和系统总压与液相组成的关系符合拉乌尔定律。
非理想溶液:
正偏差溶液:
组分在汽相中的分压比拉乌尔定律预计值大。
例如乙醇-水体系
负偏差溶液:
组分在汽相中的分压比拉乌尔定律预计值小。
例如硝酸-水体系。
挥发度:
其定义为组分在汽相中的平衡蒸汽压与在液相中的摩尔分数的比值。
简单蒸馏也称微分蒸馏,为间歇非稳态操作,特点:
釜内任一时刻的汽、液两相组成互成平衡。
蒸馏过程中系统的温度和汽、液相组成均随时间改变。
简单蒸馏的过程特征:
任一瞬时釜内的汽、液相互成平衡。
以物料衡算式、热量衡算式以及相平衡关系作为计算的基本依据。
平衡蒸馏是液体的一次部分汽化或蒸汽的一次部分冷凝的蒸馏操作
闪蒸操作流程:
一定组成的液体物料被加热后经节流阀减压进入闪蒸室。
液体因沸点下降变为过热而骤然汽化,汽化耗热使得液体温度下降,汽、液两相温度趋于一致,两相组成趋于平衡。
由闪蒸室塔顶和塔底引出的汽、液两相即为闪蒸产品。
精馏原理:
平衡蒸馏以及简单蒸馏只能使混合液得到部分分离。
简单蒸馏操作是对液体的连续部分汽化,釜液组成沿t-x(y)相图的泡点线变化,其结果可得难挥发组分(重组分)含量很高而易挥发组分(轻组分)摩尔分数x很低的釜液。
在一定压力下,将混合蒸汽进行连续部分冷凝,蒸汽相的组成沿t-x(y)相图的露点线变化,结果可得到难挥发组分(重组分)含量很低而易挥发组分(轻组分)摩尔分数y很高的蒸汽。
精馏是多次部分汽化与多次部分冷凝的联合操作.
塔板的作用:
塔板提供了汽液分离的场所。
每一块塔板是一个混合分离器,足够多的板数可使各组分较完全分离
精馏与简单蒸馏的区别:
汽相和液相的部分回流。
也是精馏操作的基本条件。
精馏塔内的汽、液相摩尔流率不仅取决于塔顶的回流比和塔底再沸器的汽化量,而且与加料的热状态(即入塔原料的热状态)直接相关。
进料浓度的影响:
当xF降至x’F,若R和D/F不变,精操线斜率不变。
但xF下降使塔板上y,x均减小,xD和xW也随之下降,精馏段操作线将