提升液压系统设计方案.docx
《提升液压系统设计方案.docx》由会员分享,可在线阅读,更多相关《提升液压系统设计方案.docx(25页珍藏版)》请在冰豆网上搜索。
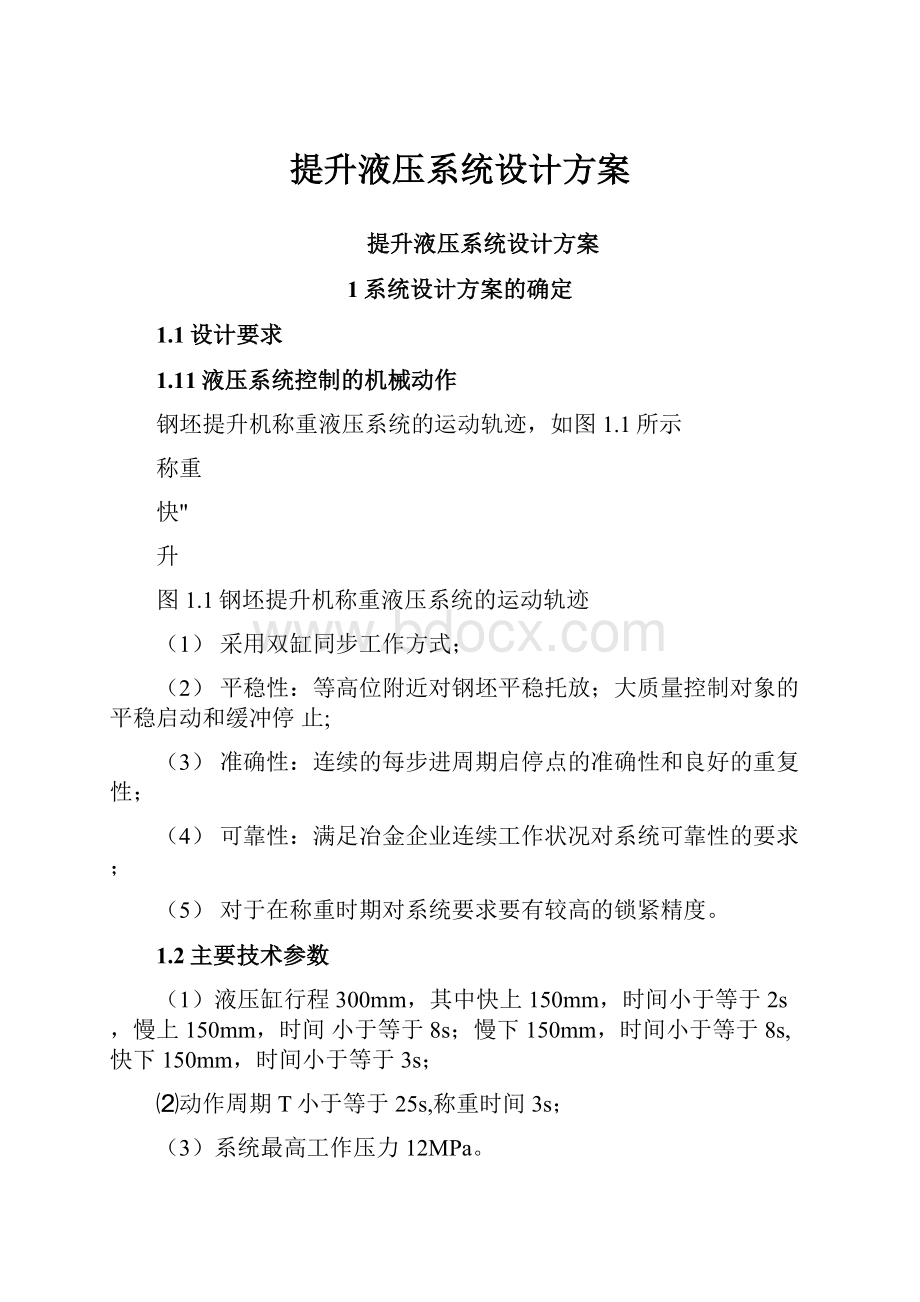
提升液压系统设计方案
提升液压系统设计方案
1系统设计方案的确定
1.1设计要求
1.11液压系统控制的机械动作
钢坯提升机称重液压系统的运动轨迹,如图1.1所示
称重
快"
升
图1.1钢坯提升机称重液压系统的运动轨迹
(1)采用双缸同步工作方式;
(2)平稳性:
等高位附近对钢坯平稳托放;大质量控制对象的平稳启动和缓冲停止;
(3)准确性:
连续的每步进周期启停点的准确性和良好的重复性;
(4)可靠性:
满足冶金企业连续工作状况对系统可靠性的要求;
(5)对于在称重时期对系统要求要有较高的锁紧精度。
1.2主要技术参数
(1)液压缸行程300mm,其中快上150mm,时间小于等于2s,慢上150mm,时间小于等于8s;慢下150mm,时间小于等于8s,快下150mm,时间小于等于3s;
⑵动作周期T小于等于25s,称重时间3s;
(3)系统最高工作压力12MPa。
1.3系统驱动方案的选择
通常传动机构有机械传动和液压传动两种。
钢坯提升机称重液压系统的传动机构选用液压传动。
与机械传动相比,液压传动具有功率一质量比大、便于无极调速和过载保护、布局灵活方便等多种技术优势;同时,在现代工业生产中,自动化程度越来越高,而液压系统也因为其易于实现自动化,工作平稳等优点而被广泛应用。
随着技术的发展,采用液压传动是可靠、合理的,用电磁阀来控制液压执行元件同步和无级调速,可以更好的满足工艺,实现其高产、优质、低消耗的要求。
钢坯提
升机称重液压系统需要比较大的驱动功率,驱动装置一般选用液压缸和液压马,
这是因为液压元件工作可靠、费用较低。
此外,利用液压系统的储能作用,还可以使工作台的能耗较低。
1.4控制方式
根据钢坯提升机称重液压系统的工艺要求,在生产过程中液压系统要完成以下动作,液压缸快升、慢上、停留、慢下,速降,其中停留动作要求锁紧精度要高。
在举升液压缸的控制回路中,采用液控单向阀锁定回路和进油口节流调速回路。
液控单向阀回路容易控制并且锁紧时间较长,利于保障设备安全;同时,根据工况分
析,液压缸在运行过程中负载的变化不大,可以采用进油口调速回路控制液压缸的运动速度。
供油回路采用液压泵直接提供动力的结构,在吸油管道中采用截止阀和减震喉管串联,用于减震。
为了实现系统的自动化,执行元件之间的协调可以通过PLC来完
成,也可以通过继电器来实现。
1.5草拟液压系统原理图
在对钢坯称重的流程进行认真分析,草拟了钢坯提升机称重液压系统原理图,钢坯提升机称重液压系统如1.2所示:
图1.2钢坯提升机称重液压系统
其工作流程如下:
在系统工作时,首先,三位四通换向阀1YA通电,油液经过平
衡阀、调速阀、分流集流阀、液控单向阀,最后进入液压缸下端无杆腔,使两个缸的活塞杆同时上升,完成移动横梁的快速上升动作。
当吊钩达到钢坯下方时光电信号开关1SQ控制1YA、3YA通电,即完成减速缓慢上升工况,当钢坯达到轨道上方100mm时,具有延时功能的光电转换开关2SQ控制5YA通电,延时期内只有二位二通电磁阀5YA通电,其余所有电磁阀均不通电,液控单向阀关闭,活塞杆也停止下降,钢坯处于停止状态,称重设备在2SQ延时期间完成称重、取值任务。
延时结束后2YA、4YA同时通电,完成慢下动作。
当钢坯达到轨道后,1SQ发信号,2YA通电,活塞
杆快速下降,到达底端后3SQ发信号各阀处于断电状态,活塞杆停止下降,一次称重结束。
2执行元件主要参数的计算与选型
2.1液压缸计算与选型
2.1.1液压缸主要参数计算与选型
液压缸活塞面积计算公式为:
FH2
A二一D2(2-1)
P4
式中:
F--液压缸载荷(N);
P--液压缸工作压力(Pa);
D--液压缸内径(m)。
系统压力初定为P=14MPa。
缸的作用力F=20KN,全行程距离s=150mm,作用时间
11=3s。
根据公式(2-1)计算活塞面积A:
二44mm
根据行程速比系数d=0.7・D,计算活塞杆的直径d:
d=0.7•D二0.744二30.08mm
查文献[1],表17-6-2
圆整液压缸的内径D=50mm,圆整液压缸的活塞杆直径d=36mm。
查文献[1],表17-6-3油缸的流量公式
n23n23
Q=AVD2V1030.0524.5103=9.3L/min
4n4汉0.95
式中:
n--油缸的容积效率取0.95
D--单位为m
V--单位为m/min
选择武汉油缸厂液压缸UYTF1050X36X300X267/21
WF—端部法兰式,10--活塞杆为外螺纹连接方式,21--压力级别21MPa
2.1.2液压缸校核
液压缸实际工作所需的压力
式中:
Pb--回油背压,取0.5MPa;
A,--无杆腔面积;
A2--无杆腔面积。
计算得:
PgvP,即系统提供压力要不小于10.5MP&
3泵与电机
3.1泵的计算
泵的选型主要根据系统的工况来选择液压泵,泵的主要参数有压力、流量、转速、效率。
为了保证系统正常运转和泵的使用寿命,一般在固定设备系统中,正常工作压力为泵的额定工作压力的80%左右;要求工作可靠性较高的系统或运动的设备,系统工作压力为泵的额定工作压力的60%左右。
泵的流量要大于系统的最大工作流量。
为了延长泵的使用寿命,泵的最高压力与最高转速不宜同时使用。
3.1.1确定泵的工作压力
因正常工作中进油管路有压力损失,所以系统工作压力为
Ps-PmaxPx=10.50.6=11.MPa(3-1)
式中:
Ps--系统工作压力(MPa);
Pma--执行元件最大工作压力(MPa);
Px--系统压力损失(MPa)。
系统工作压力定为11.1MPa。
故泵的工作压力
Pn-1.3X11.1=14.5MPa
3.1.2确定泵的流量
泵的最大流量计算公式:
qp=Kl(2q)max(3-2)
式中:
qp--液压泵的最大流量;
(R)ma--同时动作的各执行元件所需流量之和的最大值;
Kl--系统泄漏系数,一般取1.1〜1.3。
由于本系统采用双缸同步工作方式,故(2q)max取主弯曲油的流量20L/min。
根
据公式(3-2),得:
qp二KL'qmax=1.220L/min=24L/min
采用斜轴式柱塞泵,采用该泵型号为25MCY-1B,此泵的基本参数为:
排量为
25ml/r,额定压力为MPa,最高转速为1500r/min,最大流量为37.5L/min,效率为92%,功率为24.6。
本系统采用两台泵一工一备,在此选用一样的。
3.1.3泵的安装
液压泵装置安装要求如下:
(1)液压泵与原动机之间的联轴器的型式及安装要求必须符合制造厂的规定。
(2)外露的旋转轴、联轴器必须加装防护罩。
(3)液压泵与电动机的安装底座必须有足够的刚性,以保证运转始终同轴。
(4)液压泵的进油管路应短而直,避免拐弯增多,断面突变。
在规定的油液度范围内,必须使泵的进油压力和其他条件符合泵制造厂家的规定。
(5)液压泵的进油管路密封必须可靠,不得吸入空气。
(6)高压、大流量的液压泵装置推荐采用:
泵进油口设置橡胶弹性补偿接管、
泵出油口连接高压软管、泵装置底座设置弹性减震垫。
3.2电机的选择
电动机有交流电动机和直流电动机之分,一般工厂都采三相交流电动机,而且多
采用丫系列三相异步电动机。
其结构简单,起动性能好,工作可靠,价格低廉,维护方便。
由于液压泵通常在空载下启动,故对电动机的启动转矩没有过高要求,负荷
变化比较平稳,起动次数不多,因此可以采用系列笼型异步电动机。
电动机与液压泵之间通常采用联轴器连接,电动机的转速应在液压泵的最佳转速范围内。
选择2750rmin/工况下选择的,故可选择与其相近的电机转速,则液压泵的流量仍可满足系统2800rmin/的要求。
系统的总电动机的功率选择直接影响到电动机工作性能和经济性能的好坏。
如果
所选电机的功率小于工作要求,则不能保证系统正常工作,使电机经常过载而提早损坏;如果所选电机的功率过大,则电动机经常不能满载运行,功率因数和效率较低,从而增加电能损耗,造成浪费。
因此在设计中一定要选择合适的电动机功率。
根据泵
的功率要求选择重庆电机有限公司生产的丫2系列三相异步电动机,
所需的两台电机选一样。
有参数选定电机型号丫200L-4,功率为30KW,转速为1470r/min,效率为95%
4液压元件的选择
为了方便各液压阀的选择,将总系统拆分为两个个分系统i、u,分别对应举升液压缸缸系统和油源系统,各系统管路流量圆整后,如下表:
表4-1各分回路管路流量表
系统
工作时压力MPa
最大流量L/min
I
12
20
n
压油路
14.5
37.5
回油路
<5
37.5
4.1泵入口液压阀的选择
4.1.1溢流阀的选择
作为泵的的出口的安全用阀,根据泵的的流量37.5L/min,工作压力为32Mpa,
调定压力15MPa,先导式溢流阀选用
DBW10A1-5X/1700-G24N9K4
通径10mm,底板安装,5X安装连接尺寸不变,压力等级150bar。
4.1.2截止阀及减震喉管的选择
泵入口处的低压球式截止阀,查文献[1]表17-7-253选用型号
YJZQ-H15M
通径10mm,管式连接,最大流量37.5L/min,生产商:
威海广元液压联合公司。
泵入口处的减震管,根据上海液压件总厂,选用型号HXK
(1)-65,通径10mm。
图4.2高压球式截止阀
4.1.3
单向阀的选择
泵出口处的单向阀,根据北京华德产品资料,选用型号S20P5-0.0B,通径20mm
4.2执行元件控制阀的选择
4.2.1提升液压缸回路阀的选择
根据I分系统的流量为20L/min,工作压力为12MPa,并根据液压站控制阀台的设计实际选用叠加阀,各阀型号:
液控单向阀:
Z2S1640
分流集流阀:
FJL-B10-H
二位二通电磁阀:
GAB410-4-8ZG1/2
直控单项顺序阀:
XD2F-B10HH17-431
三位四通电磁阀:
34DY-H10B-T-Z
单向调速阀:
AQF3-E10B
5辅助元件的选择计算
5.1油箱的设计
考虑到要保证系统工作时油箱能够保持一定的液位高度,油箱必须有足够大的容量,而不能仅仅是够用即可,一般以装三分之二的油为好。
油箱的排油口与回油口之间的距离应尽可能远些,管口都应插入最低液面之下,以免发生吸空和回油冲溅产生气泡。
管口制成45°的斜角,以增大吸油及出油的截面,本系统中的回油管和泄油管均须设置斜角。
为了使油液流动时速度变化不致过大,管口应面向箱壁。
油箱设计时应考虑如下几点:
油箱必须有足够大的容积,一方面尽可能的满足散热要求,另一方面在液压系统停止时油箱应能容纳系统中的所有工作介质,而工作时
又能保持适当的液位
吸回油管应插入最低液面之下,以防止吸空和回油飞溅产生气泡,管口与箱底、箱壁的距离一般不小于管径的3倍,吸油管口可安装100m左右的网式或线隙式过滤器,安装位置要便于装卸和清洗过滤器。
回油管口斜切成45并面向管壁,以防止
回油冲击油箱底部的沉积物,同时也便于散热。
吸油管和回油管之间的距离应尽量远,之间应设置隔板,以加大液流循环,这样能提高散热、分离空气及沉淀杂质的效果。
隔板高度为液面的2/3〜3/4。
为了保证油液清洁,油箱应有周边密封的盖板,盖板上装有空气过滤器,注油和通气一般都由一个空气过滤器来完成。
为便于放油和清理,箱底应有一定的斜度,并在最低处设置放油。
,对于不易开盖的油箱,应设置清洗孔,以便油箱内部的清理。
箱底应距地面150mm以上,便于搬运、放油和散热,在油箱的适当位置要设置吊耳,以便于吊运,同时还应设置液位计以监视液位。
对油箱内表面的处理要给予充分的注意。
常用的方法有:
(1)酸洗后磷化。
适用于所有介质,但受酸洗磷化槽的限制,油箱不能太大。
(2)喷丸后直接涂防锈油。
适用于一般矿物油和合成液压油,不适合水液压液。
因不受处理条件限制,大型油箱见多采用此法。
(3)喷砂后热喷涂氧化铝。
适用于除水-乙二醇外的所有介质。
(4)喷砂后进行喷塑。
适用于所有介质。
但受烘干设备限制,油箱不能过大。
考虑油箱内表面的防腐处理,不但要顾及与介质的相容性,还要考虑处理后的可加工性、制造到投入使用之间的时间间隔及经济性,条件允许时采用不锈钢制油箱无疑是最理想的选择。
本设计中采用开式矩形油箱,材料不锈钢,详见油箱焊接图(WUSTHC2012-04)。
5.1.1油箱尺寸的确定
该系统那个有两台工作泵,每台流量为37.5L/min,由于泵是一工一备,总流量也为24L/min,查文献1,第17篇第5.2节液压油箱有效容积
V=(3~7)qn=(3~7)X37.5=112.5~262.5(5-1)
油箱的外型尺寸比(长:
宽:
高)一般为1:
1:
1~1:
2:
3。
同时考虑泵站的安装方便及合理,设计油箱的尺寸为
1000X500X1000=500L(容积为500L)
油箱出油口距离油箱底部200mm,液面最低面应高于出油口液面200mm,贝U该邮箱的有效容积
V有效-10005006000.8=240L
考虑到泵在最大流量下工作的时间不是很长,油箱有效容积240L是合适的。
5.1.2油箱安装
(1)油箱应仔细清洗,用压缩空气干燥后,再用煤油检查焊缝质量。
(2)必须有足够的支持面积,以便在装备和安装是用垫片等进行调整。
油箱应设置隔板将吸、回油管隔开,使液流循环,油液中的气泡与杂质分离和沉淀。
隔板结构有很多,另外还可根据需要在隔板上安置过滤网。
油箱可分为开式油箱和闭式油箱两种。
开式油箱,箱中液面与大气相通,在油箱盖上装有空气过滤器。
开式油箱结构简单,安装维护方便,液压系统普遍采用这种形式;闭式油箱一般用于压力油箱,内充一定压力的惰性气体,充气压力可达0.05MPa。
按油箱形状分可分为矩形油箱和圆灌形油箱。
矩形油箱制造容易,箱上易于安放液压器件,所以被广泛采用;圆灌形油箱强度高,重量轻,易于清扫,但制造较难,占用空间较大,在大型冶金设备中经常采用。
本设计中采用开式矩形油箱,材料不锈钢,详见油箱焊接图(WUSTHC2012-04)
5.2工作介质的选择
液压工作介质的要求
(1)粘度合适,随温度的变化小,润滑性良好,抗氧化性能,剪切安定性良好,防锈和不腐蚀金属,同密封材料相容,消泡和抗泡沫性,抗乳化性性,洁净度以及良好的化学稳定性等。
(2)润滑性良好。
工作介质对液压系统中的各运动部件起润滑作用,保证系统能够长时间正常工作。
(3)抗氧化。
工作介质与空气接触会产生氧化变质,而且氧化生成的粘稠物会堵塞元件的孔隙,影响系统正常工作。
(4)防锈和不腐蚀金属。
(5)同密圭寸材料相容。
(6)消泡和抗泡沫性。
(7)清洁度。
根据液压设计手册选取液压工作介质型号为:
L-HM32液压油的工作介质,运
动粘度等级为:
32mm2s^。
5.3冷却器的选择与计算
冷却器除通过管道散热面积直接吸收油液中的热量以外,还使油液流动出现紊流,通过破坏边界层来增加油液的传热系数。
冷却器的基本要求有:
(1)有足够的散热面积。
(2)散热效率高。
(3)油液通过时压力损失小。
(4)
(5-2)
结构力求紧凑、坚固、体积小、重量轻。
系统发热功率计算公式为
H=Pp(1pcm)
式中:
c迪
—Ppqp
H--系统发热功率,W
Pp--油泵的中输入功率,W
P--油泵的效率,油泵的容积效率为85%,机械效率为95%m--液压执行元件的效率,对液压缸一般按95%计算C--液压回油效率
pq--各液压执行元件工作压力和输入流量乘积总和vppqp--各油泵供油压力和输入流量乘积总和由于各执行元件是顺序工作,分段求出各段的发热功率由于电机一直处于工作状态,故
'pPqp-14.615=219MpaLmin」保持不变。
液压缸快速上升和快速下降各用时0~3s
_1
7p1q1=14.68=116.8MpaLmin
c二1168100%=53.34%
219
发热功率:
已=1010392%1-92.15%53.34%95%=4.9Kw
该段持续时间:
匕=3s
液压缸慢升和慢降各同时0~8s
二p2q2=14.62.4=35.04MpaLmin,
35坐100%=16%
219
发热功率:
已=1010392%1-92.15%16%95%i=7.9Kw
该段持续时间:
t^3s
总的发热功率
__沢2+H2t2汇24.9汉3汇2+7.9汇8汇2少
22
H7Kw
式中t--总时间(s)
冷却器的算热面积
式中:
宁-呼,b液压油进口温度(K),匕液压油出口温度(K),
ti、冷却水进口温度(K),t2、冷却水出口温度(K)冷却器的传热系数,初步计算多管式水冷k=116W/(m2K)将数据带入公式得
(5-5)
式中C--油的比热j/(kgK)
--油的密度,kg/m3
V--油箱容积,m3
•--油加热后温升,K
T--加热时间,s
初算
得:
C=1700J/(kgK)
3
r二900kg/m
2
V=1.125m
:
=10K
T二3600s
冷却器选择型号2LQFL—A1.0F为生厂商:
营口液压机械厂
5.4加热器
加热器的加热功率:
装上套管
加热器的使用安装要求:
加热管部分应全部浸入液压油中,不允许因液面降低而
使加热管部分外露;为保证电加热器加热管部分全部浸入液压油中,应使之水平安装;使用电加热器的时候,应同时加一个热电偶,当液压油温度升高至预定值时,加热器自行断电。
在低温环境工作,为保证合适的油温,油箱须进行加热。
可用蒸汽加热或电加热。
SRY4型适合在循环系统内加热油类用,其最高工作温度为300C。
故选择SRY型油用管状电加热
型号:
SRY4-220/1,功率1kw,选用三个。
浸入中250mm,生产商:
上海电热电气厂。
5.5管路选择
管道的作用是保证油路的连通,并便于拆卸、安装;根据工作压力、安装位置确定管件的连接结构;与泵、阀等连接的管件应由其接口尺寸决定管径。
在液压传动中,常用的管子有钢管、铜管、胶管、尼龙管和塑料管等。
钢管能承受较高的压力,价廉;但弯制比较困难,弯曲半径不能太小,多用在压
力较高、装置位置比较方便的地方。
一般采用无缝钢管,当工作压力小于1.6MPa时,也可用焊接钢管。
紫铜管能承受的压力较低(p兰3.6~10MPa),经过加热冷却处理后,紫铜管软化,装配时可按需要进行弯曲;但价贵且抗振能力较弱。
尼龙管用在低压系统;塑料管一般只作回油管用。
胶管作联接两个相对运动部件之间的管道。
胶管分高、低压两种。
高雅胶管是钢丝编织体为骨架或钢丝缠绕体为骨架的胶管,可用于压力较高的油路中。
低压胶管是麻绳或棉线编织体为骨架的胶管,多用于压力较低的油路中。
由于胶管制造比较困难,成本高,因此非必要时不用。
导管内径尺寸应与要求的通流能力相适应,壁厚应满足工作压力和管材的强度要求。
内径和壁厚是选择液压导管的重要参数。
液压系统各个部分的油液流速v都有相应的规定。
对于金属管内油液的流速一般的推荐值为:
吸油管路取v乞0.5~2m/s;压油管路取v乞2.5~6m/s;短管道及局部收缩处取v=5~10m/s;回油管路取v「.5~3m/s;泄油管路取v「m/s
根据公式
(5-6)
计算主要油道的直径,主吸油管路得:
4q437.510^
0.028m=28mm
*二i二160
查文献[1],第17篇表17-8-2,圆整为32mm,低压,壁厚取3mm。
压油管路得:
'4q[4x20x10
d0.010m=10mm
4.560
查文献[1],第17篇表17-8-2,圆整为15mm,高压,壁厚取2mm回油管路得:
=0.019m=19mm
d_阿_4x37.5x10’
'二.二260
查文献[1],第17篇表17-8-2,圆整为25mm,低压,壁厚取2mm
泄漏油管路得:
查文献[1],第17篇表17-8-2,圆整为15mm,低压,壁厚取1.6mm。
结合实际情况,各管路选择如下表2:
表5-1管路选择表
管路名称
最大流量
公称通径
外径
管接头连接螺纹
壁厚
主吸油管道
37.5
32
34
M33X2
3
压油管道
20
15
22
M22<1.5
2
泄漏油管道
5
15
22
M22<1.5
1.6
回油管道
37.5
25
28
M27<1.5
1.6
管路的安装一般在所连接的设备和元件安装完毕后再进行。
钢管路酸洗应在管路配置完毕,且已具备冲洗条件后进行。
管路酸洗复位后,应尽快进行循环冲洗,以保证清洁与防锈。
5.6吸油过滤器的选择
过滤器在液压系统中,滤除外部混入或者系统运转中内部产生的液压油中的固体杂质,使油液保持清洁,延长液压元件使用寿命,保证系统工作的稳定性。
液压系统75%左右的故障是由介质的污染造成的,所以应在系统中设置滤油器。
根据滤油器在液压系统中所处的位置不同,滤油器的种类也多种多样。
线隙式滤油器,一般用于中、低压系统。
这种滤油器阻力小、通流能力大,但不易清洗。
网式滤油器,装在液压泵吸油管路上,用以保护液压泵。
它具有结构简单、通油能力大、阻力小、易清洗等特点。
纸质滤油器,比一般其它类型滤油器过滤精度高,可滤除油液中的微细杂质上的两种。
这种滤油器有高压管路的和低压管路,可安装压差发讯装置,可用于要求过滤
质量高的液压系统中
过滤器选择有两点最基本的要求:
1.过滤精度满足要求。
2.具有足够大的过滤能力,压力损失小。
系统工况:
压力叮OMPa,过滤精度乞2&山,系统最大流量37.5L/min。
高压管式纸质过滤器YCX-25X20LC生厂商:
黎明液压机电厂;
额定压力:
32MPa;额定流量:
37.5L/min;过滤精度:
80'm;压力损失:
0.2MPa。
5.7回油过滤器的选择
油箱的回油口一般都设置系统所要求的过滤精度的回油滤油管,以保证返回油箱
的油液具有允许的污染等级。
由于此系统选用的双筒回油过滤器直接安装在油箱上,故在油箱上方回油管一侧设置两个连接法兰,以安装双筒回油过滤器。
一般来说,是过滤器的过滤精度越高,滤芯堵塞越快,过滤清洗或更换周期就越短,成本所以,在选择过滤器时应根据具体情况合理的选择过滤精度,以达到所需要
的油液清洁度。
另外,应考虑过滤器允许的最高工作压力和在一定压差下允许通过的最大流量。
为了保持滤芯不破坏或系统的压力损失不至过大,要限制过滤器最大允许
压力降。
过滤器的最大允许压力降取决于滤芯的强度。
考虑到生产的因素,在生产过程中不能让液压系统因为回油滤芯堵塞而停止工作。
因此选用STF型双筒自封