毕业设计雨伞手柄塑料模具设计管理资料.docx
《毕业设计雨伞手柄塑料模具设计管理资料.docx》由会员分享,可在线阅读,更多相关《毕业设计雨伞手柄塑料模具设计管理资料.docx(32页珍藏版)》请在冰豆网上搜索。
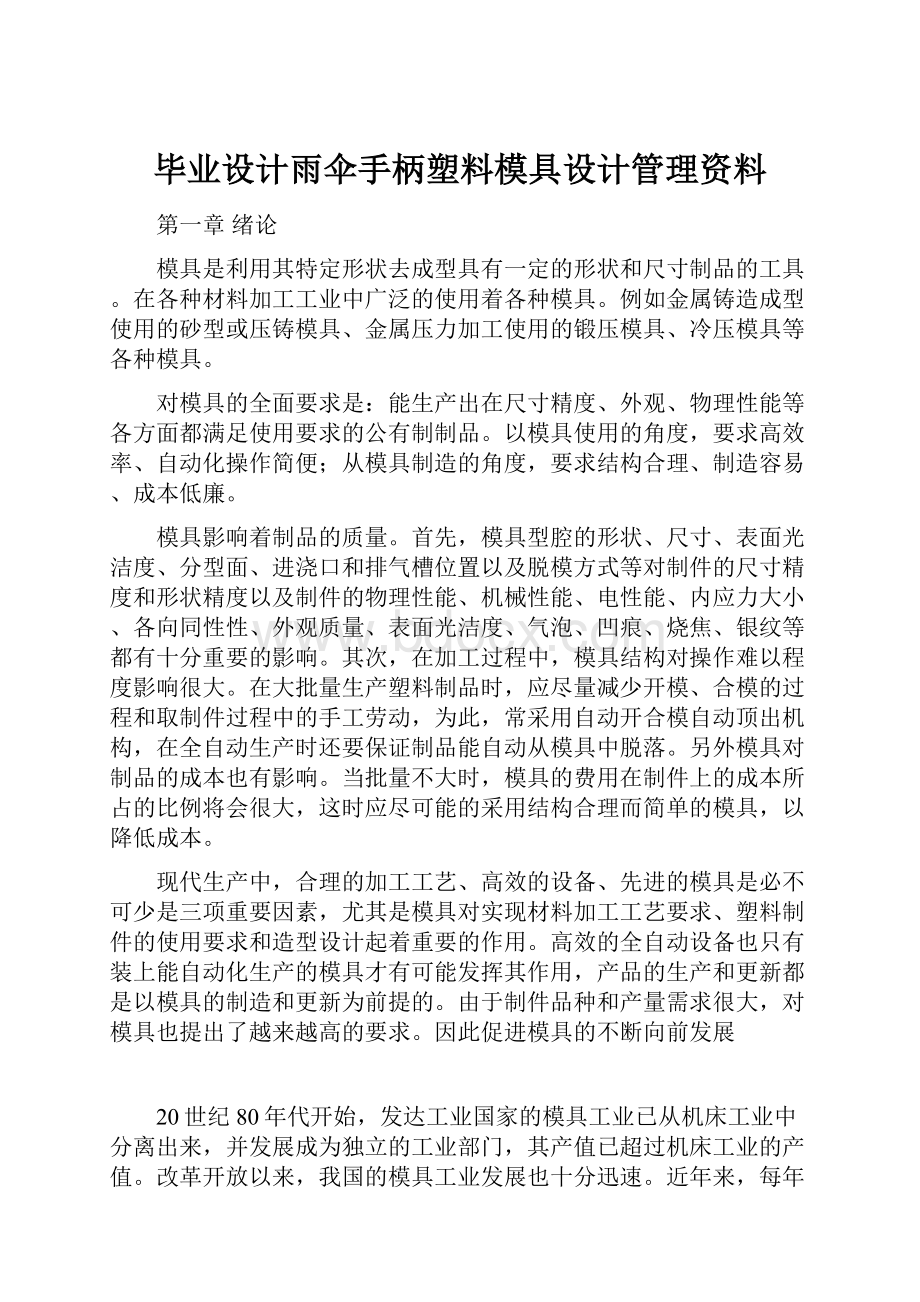
毕业设计雨伞手柄塑料模具设计管理资料
第一章绪论
模具是利用其特定形状去成型具有一定的形状和尺寸制品的工具。
在各种材料加工工业中广泛的使用着各种模具。
例如金属铸造成型使用的砂型或压铸模具、金属压力加工使用的锻压模具、冷压模具等各种模具。
对模具的全面要求是:
能生产出在尺寸精度、外观、物理性能等各方面都满足使用要求的公有制制品。
以模具使用的角度,要求高效率、自动化操作简便;从模具制造的角度,要求结构合理、制造容易、成本低廉。
模具影响着制品的质量。
首先,模具型腔的形状、尺寸、表面光洁度、分型面、进浇口和排气槽位置以及脱模方式等对制件的尺寸精度和形状精度以及制件的物理性能、机械性能、电性能、内应力大小、各向同性性、外观质量、表面光洁度、气泡、凹痕、烧焦、银纹等都有十分重要的影响。
其次,在加工过程中,模具结构对操作难以程度影响很大。
在大批量生产塑料制品时,应尽量减少开模、合模的过程和取制件过程中的手工劳动,为此,常采用自动开合模自动顶出机构,在全自动生产时还要保证制品能自动从模具中脱落。
另外模具对制品的成本也有影响。
当批量不大时,模具的费用在制件上的成本所占的比例将会很大,这时应尽可能的采用结构合理而简单的模具,以降低成本。
现代生产中,合理的加工工艺、高效的设备、先进的模具是必不可少是三项重要因素,尤其是模具对实现材料加工工艺要求、塑料制件的使用要求和造型设计起着重要的作用。
高效的全自动设备也只有装上能自动化生产的模具才有可能发挥其作用,产品的生产和更新都是以模具的制造和更新为前提的。
由于制件品种和产量需求很大,对模具也提出了越来越高的要求。
因此促进模具的不断向前发展
20世纪80年代开始,发达工业国家的模具工业已从机床工业中分离出来,并发展成为独立的工业部门,其产值已超过机床工业的产值。
改革开放以来,我国的模具工业发展也十分迅速。
近年来,每年都以15%的增长速度快速发展。
许多模具企业十分重视技术发展。
加大了用于技术进步的投入力度,将技术进步作为企业发展的重要动力。
此外,许多科研机构和大专院校也开展了模具技术的研究与开发。
模具行业的快速发展是使我国成为世界超级制造大国的重要原因。
今后,我国要发展成为世界制造强国,仍将依赖于模具工业的快速发展,成为模具制造强国。
中国塑料模工业从起步到现在,历经了半个多世纪,有了很大发展,模具水平有了较大提高。
在大型模具方面已能生产48"(约122CM)大屏幕彩电塑壳注射模具,,精密塑料模方面,以能生产照相机塑料件模具,多形腔小模数齿轮模具及塑封模具。
经过多年的努力,在模具CAD/CAE/CAM技术,模具的电加工和数控加工技术,快速成型与快速制模技术,新型模具材料等方面取得了显著进步;在提高模具质量和缩短模具设计制造周期等方面作出了贡献。
尽管我国模具工业有了长足的进步,部分模具已达到国际先进水平,但无论是数量还是质量仍满足不了国内市场的需要,每年仍需进口10多亿美元的各类大型,精密,复杂模具。
与发达国家的模具工业相比,在模具技术上仍有不小的差距。
今后,我国模具行业应在以下几方面进行不断的技术创新,以缩小与国际先进水平的距离。
(1)注重开发大型,精密,复杂模具;随着我国轿车,家电等工业的快速发展,成型零件的大型化和精密化要求越来越高,模具也将日趋大型化和精密化。
(2)加强模具标准件的应用;使用模具标准件不但能缩短模具制造周期,降低模具制造成本而且能提高模具的制造质量。
因此,模具标准件的应用必将日渐广泛。
(3)推广CAD/CAM/CAE技术;模具CAD/CAM/CAE技术是模具技术发展的一个重要里程碑。
实践证明,模具CAD/CAM/CAE技术是模具设计制造的发展方向,可显著地提高模具设计制造水平。
(4)重视快速模具制造技术,缩短模具制造周期;随着先进制造技术的不断出现,模具的制造水平也在不断地提高,基于快速成形的快速制模技术,高速铣削加工技术,以及自动研磨抛光技术将在模具制造中获得更为广泛的应用。
第二章塑件的工艺分析
分析塑件使用材料的种类及工艺特征
该塑件材料选用ABS(丙烯腈—丁二烯—苯乙烯共聚物)。
用途:
汽车配件(仪表板、工具舱门、车轮盖、反光镜盒等),收音机壳,电话手柄、大强度工具(吸尘器,头发烘干机,搅拌器,割草机等),打字机键盘,娱乐用车辆如高尔夫球手推车以及喷气式雪橇车等。
比重:
燃烧鉴别方法:
连续燃烧、蓝底黄火焰、黑烟、浅金盏草味
溶剂实验:
环已酮可软化,芳香溶剂无作用
特点:
1、综合性能较好,冲击强度较高,化学稳定性,电性能良好.
2、与372有机玻璃的熔接性良好,制成双色塑件,且可表面镀铬,喷漆处理.
3、有高抗冲、高耐热、阻燃、增强、透明等级别。
4、流动性比HIPS差一点,比PMMA、PC等好,柔韧性好。
5、用途:
适于制作一般机械零件,减磨耐磨零件,传动零件和电讯零件.
6、同PVC(聚氯乙烯)一样在屈折处会出现白化现象。
成型特性:
,流动性中等,吸湿大,必须充分干燥,表面要求光泽的塑件须长时间预热干燥80-90度,3小时.
,高模温,但料温过高易分解(分解温度为>270度).对精度较高的塑件,模温宜取50-60度,,模温宜取60-80度.
3、如需解决夹水纹,需提高材料的流动性,采取高料温、高模温,或者改变入水位等方法。
4、如成形耐热级或阻燃级材料,生产3-7天后模具表面会残存塑料分解物,导致模具表面发亮,需对模具及时进行清理,同时模具表面需增加排气位置。
ABS树脂是目前产量最大,应用最广泛的聚合物,它将PS,SAN,BS的各种性能有机地统一起来,兼具韧,硬,刚相均衡的优良力学性能。
ABS是丙烯腈、丁二烯和苯乙烯的三元共聚物,A代表丙烯腈,B代表丁二烯,S代表苯乙烯。
ABS工程塑料一般是不透明的,外观呈浅象牙色、无毒、无味,兼有韧、硬、刚的特性,燃烧缓慢,火焰呈黄色,有黑烟,燃烧后塑料软化、烧焦,发出特殊的肉桂气味,但无熔融滴落现象。
ABS工程塑料具有优良的综合性能,有极好的冲击强度、尺寸稳定性好、电性能、耐磨性、抗化学药品性、染色性,散热性(现在ABS工程塑料的工艺已经很成熟了,笔记本电脑只要内部结构设计合理,同样可以有出色的散热效果。
)
成型加工和机械加工较好。
ABS树脂耐水、无机盐、碱和酸类,不溶于大部分醇类和烃类溶剂,而容易溶于醛、酮、酯和某些氯代烃中。
ABS工程塑料的缺点:
热变形温度较低,可燃,耐候性较差。
ABS有良好的耐化学腐蚀及表面硬度,有良好的加工性和染色性能。
ABS无毒、无味、呈微黄色,成型的塑件有较好的光泽。
~³。
ABS有良好的机械强度和一定的耐磨性、耐寒性、耐油性、耐水性、化学稳定性和电气性能。
水、无机盐、碱和酸类对ABS几乎无影响。
ABS不溶于大部分醇类及烃类溶剂,但与烃长期接触会软化溶胀。
ABS有一定的硬度和尺寸稳定性,易与成型加工,经过调色可配成任何颜色。
ABS的缺点是耐热性不高,连续工作温度为70ºC左右,热变形温度为93ºC左右,且耐气候性差,在紫外线作用下易发脆。
ABS在升温时粘度增高,所以成型压力高,故塑件上的脱模斜度宜稍大;ABS易吸水,成型加工前应进行干燥处理;ABS易产生熔接痕,模具设计时应注意尽量少浇注系统对料流的阻力;在正常的成型条件下,壁厚、熔料温度对收缩率影响极小。
ABS主要技术指标:
表1-1热物理性能
密度(g/cm³)
—1.05
比热容(J·kg-1K-1)
1255—1674
导热系数
(W·m-1·K-1×10-2)
—
线膨胀系数
(10-5K-1)
—
滞流温度(°C)
130
表1-2力学性能
屈服强度(MPa)
50
抗拉强度(MPa)
38
断裂伸长率(﹪)
35
拉伸弹性模量(GPa)
抗弯强度(MPa)
80
弯曲弹性模量(GPa)
抗压强度(MPa)
53
抗剪强度(MPa)
24
冲击韧度
(简支梁式)
无缺口
261
布氏硬度
缺口
11
表1-3电气性能
表面电阻率(Ω)
×1013
体积电阻率(Ω·m)
×1014
击穿电压(KV/mm)
\
介电常数(106Hz)
介电损耗角正切(106Hz)
耐电弧性(s)
50—85
雨伞手柄的形状较简单,其内侧有凸凹台及加强肋。
雨伞手柄的注塑材料首先选用ABS,雨伞手柄的中心决定了它的重心位置的所在。
所以我们必须很好的处理它壁厚的均匀,譬如在注塑成型过程中因为壁厚的不均匀造成了收缩率的不一致,这样就只能通过有效的控制模具温度来调节收缩率。
由于雨伞手柄的主体作用是起固定作用,它的内部结构就相应的给注塑带来了一定的难度。
主要是它内侧凸台的壁厚跟加强肋及外侧一样,在注塑的时候,所受到的力相差不大,不大容易造成塑件填充不满的缺陷,可以考虑采用单浇口。
而在外侧有绳索孔,在生产过程中,凸凹模是无法解决这个问题,所以就使用外侧抽芯机构。
该塑件尺寸中等,。
除了配合尺寸要求精度较高外,其他尺寸精度要求相对较低,但表面粗糙度要求较高,再结合其材料性能,故选一般精度等级:
5级。
为了满足制品表面光滑的要求与提高成型效率采用侧浇口。
该浇口的分流道位于模具的分型面处,浇口横向开设在模具的型腔处,从塑料件侧面进料,因而塑件外表面不受损伤,不致因浇口痕迹而影响塑件的表面质量与美观效果。
塑件的工艺参数:
干燥条件:
80-90℃2小时
成型收缩率:
%
模具温度:
25-70℃(模具温度将影响塑件光洁度,温度较低则导致光洁度较低)
融化温度:
210-280℃(建议温度:
245℃)
成型温度:
200-240℃
注射速度:
中高速度
注射压力:
500-1000bar
第三章注射机的选择
塑件体积的计算
塑件:
零件塑件的体积V=
浇注系统的体积:
V2=
塑件与浇注系统的总体积为V=*4+=
:
查手册取密度ρ=
塑件体积:
V=
塑件质量:
根据有关手册查得:
ρ=
所以,塑件的重量为:
M=V×ρ=
×=
根据
(4-1)
得
(4-2)
注射机最大注射量的利用系数,;
注射机最大注射量,cmз或g;
浇注系统凝料量,cmз或g;
单个塑件体积或质量,cmз或g;
根据塑件的结构及尺寸精度要求,该塑件在注射时采用1模2腔
,其初步设定方案如下
浇注系统示意图
根据三维模型,利用三维软件直接可查询到浇注系统的体积V2=
注塑机的主要参数有公称注射量,注射压力,注射速度,塑化能力,锁模力,合模装置的基本尺寸,开合模速度,,制造,购买和使用注塑机的主要依据.
(1)公称注塑量;指在对空注射的情况下,注射螺杆或柱塞做一次最大注射行程时,注射装置所能达到的最大注射量,反映了注塑机的加工能力.
(2)注射压力;为了克服熔料流经喷嘴,浇道和型腔时的流动阻力,螺杆(或柱塞)对熔料必须施加足够的压力,我们将这种压力称为注射压力.
(3)注射速率;为了使熔料及时充满型腔,除了必须有足够的注射压力外,熔料还必须有一定的流动速率,描述这一参数的为注射速率或注射时间或注射速度.
常用的注射速率如表3-4所示。
表3-4注射量与注射时间的关系
注射量/CM
125250500100020004000600010000
注射速率/CM/S125200333570890133016002000
注射时间/S135
(4)塑化能力;,若塑化能力高而机器的空循环时间长,则不能发挥塑化装置的能力,反之则会加长成型周期.
(5)锁模力;注塑机的合模机构对模具所能施加的最大夹紧力,在此力的作用下模具不应被熔融的塑料所顶开.
(6)合模装置的基本尺寸;包括模板尺寸,拉杆空间,模板间最大开距,动模板的行程,.
(7)开合模速度;为使模具闭合时平稳,以及开模,推出制件时不使塑料制件损坏,要求模板在整个行程中的速度要合理,即合模时从快到慢,开模时由慢到快在到停.
(8)空循环时间;在没有塑化,注射保压,冷却,取出制件等动作的情况下,完成一次循环所需的时间.
查国产注射机主要技术参数表取SZ-160/1000,主要技术参数如下。
特性
内容
特性
内容
结构类型
卧
拉杆内间距(mm)
360×260
理论注射容积(cm
)
179
移模行程(mm)
280
螺杆(柱塞)直径(mm)
44
最大模具厚度(mm)
360
注射压(MP
)
132
最小模具厚度(mm)
170
注射速率(g/s)
110
锁模形式(mm)
液压
塑化能力(g/s)
模具定位孔直径(mm)
120
螺杆转速(r/min)
10~150
喷嘴球半径(mm)
10
锁模力(KN)
1000
喷嘴口直径
第四章浇注系统的设计
浇注系统的设计原则:
浇口位置应尽量选择在分型面上,以便于模具加工及使用时浇口的清理;浇口位置距型腔各个部位的距离应尽量一致,并使其流程为最短;浇口的位置应保证塑料流入型腔时,对着型腔中宽敞、壁厚位置,以便于塑料的流入;避免塑料在流入型腔时直冲型腔壁,型芯或嵌件,使塑料能尽快的流入到型腔各部位,并避免型芯或嵌件变形;尽量避免使制件产生熔接痕,或使其熔接痕产生在之间不重要的位置;浇口位置及其塑料流入方向,应使塑料在流入型腔时,能沿着型腔平行方向均匀的流入,并有利于型腔内气体的排出。
设计时必须按如下要求:
(1)型腔布置和浇口开设部位力求对称,防止模具承受偏载而造成溢料现象。
(2)型腔和浇口的排列要尽可能地减少模具外形尺寸。
(3)系统流道应尽可能短,断面尺寸适当(太小则压力及热量损失大,太大则塑料耗费大):
尽量减少弯折,表面粗糙度要低,以使热量及压力损失尽可能小。
(4)对多型腔应尽可能使塑料熔体在同一时间内进入各个型腔的深处及角落,及分流道尽可能平衡布置。
(5)满足型腔充满的前提下,浇注系统容积尽量小,以减少塑料的耗量。
(6)浇口位置要适当,尽量避免冲击嵌件和细小型芯,防止型芯变形浇口的残痕不应影响塑件的外观。
主流道是指浇注系统中从注射机喷嘴与模具处到分流道为止塑料熔体流动通道,是塑料熔体进入模具型腔是最先经过的部位,它将注塑机喷嘴注出的塑料熔体导入分流道或型腔,其形状为长圆锥形,流道宽度随着连接分流道的距离的减小而比增大,便于熔体顺利的向前流动,开模时主流道凝料又能顺利拉出来,主流道的尺寸直接影响到塑料熔体的流动速度和充模时间,由于主流道要与高温塑料和注塑机喷嘴反复接触和碰撞,通常不直接开在定模上,而是将它单独设计成主流道套镶入定模板内。
主流道套通常用高碳工具钢制造并热处理淬硬。
塑件外表面不许有浇口痕,又考虑取料顺利,对塑件与浇注系统联接处能自动减断。
根据选用的型号注射机的相关尺寸得
喷嘴前端孔径:
d0=;
喷嘴前端球面半径:
R0=10mm;
根据模具主流道与喷嘴的关系
取主流道球面半径:
R=11mm;
取主流道小端直径:
d=
为了便于将凝料从主流道中取出,将主流道设计成圆锥形,起斜度为
,此处选用2°,。
主流道示意图
分流道的设计
分流道是主流道与浇口之间的通道,一般开设在分型面上,起分流和转向作用,分流道的长度取决于模具型腔的总体布置和浇口位置,分流道的设计应尽可能短,以减少压力损失,热量损失和流道凝料。
常用分流道断面尺寸推荐如表4-1所示。
表4-1流道断面尺寸推荐值
塑料名称
分流道断面直径mm
塑料名称
分流道断面直径mm
ABS,AS
聚乙烯
尼龙类
聚甲醛
丙烯酸
抗冲击丙烯酸
醋酸纤维素
聚丙烯
异质同晶体
~
~
~
~10
8~10
8~
5~10
5~10
8~10
聚苯乙烯
软聚氯乙烯
硬聚氯乙烯
聚氨酯
热塑性聚酯
聚苯醚
聚砜
离子聚合物
聚苯硫醚
~10
~10
~16
~
~
~10
~10
~10
~13
分流道的断面形状有圆形,矩形,梯形,U形和六角形。
要减少流道内的压力损失,希望流道的截面积大,表面积小,以减小传热损失,因此,可以用流道的截面积与周长的比值来表示流道的效率,其中圆形和正方形的效率最高,但正方形的流道凝料脱模困难,所以一般是制成梯形流道。
在该模具上取圆形断面形状,直径为7mm。
分流道选用圆形截面:
直径D=7mm
流道表面粗糙度
分流道示意图
塑料在模具型腔凝固形成塑件,为了将塑件取出来,必须将模具型腔打开,也就是必须将模具分成两部分,即定模和动模两大部分。
定模和动模相接触的面称分型面。
通常有以下原则:
(1)分型面的选择有利于脱模:
分型面应取在塑件尺寸的最大处。
而且应使塑件流在动模部分,由于推出机构通常设置在动模的一侧,将型芯设置在动模部分,塑件冷却收缩后包紧型芯,使塑件留在动模,这样有利脱模。
如果塑件的壁厚较大,内孔较小或者有嵌件时,为了使塑件留在动模,一般应将凹模也设在动模一侧。
拔模斜度小或塑件较高时,为了便于脱模,可将分型面选在塑件中间的部位,但此塑件外形有分型的痕迹。
(2)分型面的选择应有利于保证塑件的外观质量和精度要求。
(3)分型面的选择应有利于成型零件的加工制造。
(4)分型面应有利于侧向抽芯,但是此模具无须侧向抽芯,此点可以不必考虑
分型面是决定模具结构形式的重要因素,它与模具的整体结构和模具的制造艺有密切关系,并且直接影响着塑料熔体的流动特性及塑料的脱模。
该塑件的模具只有一个分型面,垂直分型。
由于分型面受到塑件在模具中的成型位置、浇注系统的设计、塑件的结构工艺性及精度、形状以及摧出方法、模具的制造、排气、操作工艺等多种因素的影响,因此在选择分型面时应综合分析。
选择分型面时一般应遵循以下几项基本原则:
(1)分型面应选在塑件外形最大轮廓处
(2)确定有利的留模方式,便于塑件顺利脱模
(3)保证塑件的精度
(4)满足塑件的外观质量要求
(5)便于模具制造加工
(6)注意对在型面积的影响
(7)对排气效果
(8)对侧抽芯的影响
在实际设计中,不可能全部满足上述原则,一般应抓住主要矛盾,在此前提下确定合理的分型面。
图5.3.1分型面示意图
浇口又称进料口,是连接分流道与型腔之间的一段细短流道(除直接浇口外),它是浇注系统的关键部分。
其主要作用是:
(1)型腔充满后,熔体在浇口处首先凝结,防止其倒流。
(2)易于在浇口切除浇注系统的凝料。
~,~2mm,浇口具体尺寸一般根据经验确定,取其下限值,然后在试模是逐步纠正。
当塑料熔体通过浇口时,剪切速率增高,同时熔体的内磨檫加剧,使料流的温度升高,粘度降低,提高了流动性能,有利于充型。
但浇口尺寸过小会使压力损失增大,凝料加快,补缩困难,甚至形成喷射现象,影响塑件质量。
浇口位置的选择:
(1)浇口位置应使填充型腔的流程最短。
这样的结构使压力损失最小,易保证料流充满整个型腔,同时流动比的允许值随塑料熔体的性质,温度,注塑压力等的不同而变化,所以我们在考虑塑件的质量都要注意到这些适当值。
(2)浇口设置应有利于排气和补塑。
(3)浇口位置的选择要避免塑件变形。
采侧浇口在进料时顶部形成闭气腔,在塑件顶部常留下明显的熔接痕,而采用点浇口,有利于排气,整件质量较好,但是塑件壁厚相差较大,浇口开在薄壁处不合理;而设在厚壁处,有利于补缩,可避免缩孔、凹痕产生。
(4)浇口位置的设置应减少或避免生成熔接痕。
熔接痕是充型时前端较冷的料流在型腔中的对接部位,它的存在会降低塑件的强度,所以设置浇口时应考虑料流的方向,浇口数量多,产生熔接痕的机会很多。
流程不长时应尽量采用一个浇口,以减少熔接痕的数量。
对于大多数框形塑件,浇口位置使料流的流程过长,熔接处料温过低,熔接痕处强度低,会形成明显的接缝,如果浇口位置使料流的流程短,熔接处强度高。
为了提高熔接痕处强度,可在熔接处增设溢溜槽,是冷料进入溢溜槽。
筒形塑件采用环行浇口无熔接痕,而轮辐式浇口会使熔接痕产生。
(5)浇口位置应避免侧面冲击细长型心或镶件。
因点口在脱开时会伤塑件的内表面在这里是可以的,考虑到点浇口有利浇注系统的废料和塑件的脱离,所以本次设计选取用点绕口。
在利用了Pro/E的塑料顾问对其进行模仿CAE的注塑之后选择了更具优势的浇口。
根据浇口的位置选择要求,尽量缩短流动距离,避免熔体破裂现象引起塑件的缺陷,浇口应开设在塑件壁厚处等要求。
采用扇形浇口可以保持产品外观精度。
本设计采用边缘浇口,边缘浇口(又名为标准浇口、侧浇口)该浇口相对于分流道来说断面尺寸较小,属于小浇口的一种。
边缘浇口一般开在分型面上,具有矩形或近矩形的断面形状,其优点是浇口便于机械加工,易保证加工精度,而且试模时浇口的尺寸容易修整,适用于各种塑料品种,其最大特点是可以分别调整充模时的剪切速率和浇口封闭时间。
该模具采用侧浇口,其有以下特性:
(1)形状简单,去除浇口方便,便于加工,而且尺寸精度容易保证;
(2)试模时如发现不当,容易及时修改;
(3)能相对独立地控制填充速度及封闭时间;
(4)对于壳体形塑件,流动充填效果较佳。
浇口示意图
冷料井位于主流道的正对面的动模板上,其作用是收集熔体前锋的冷料,防止冷料进入模具型腔而影响制品质量。
冷料穴分两种,一种专门用于收集、储存冷料,另一种除储存冷料外还兼有拉出流道凝料作用,此处应用后者。
在分流道的末端,~2倍,相机面壳模具属于中小型模具,,。
在主流道对面采用冷料井底部带推料杆的冷料井,推杆为带Z型头拉料钩,其侧凹可以将主流道凝料钩住,分模时即可将凝料从主流道中拉出。
拉料杆的根部固定在推出板上,在推出制件时,冷料也一同被推出,取产品时向拉料钩的侧向稍许移动,即可脱钩将制件连同浇注系统凝料一道取下。
由文献资料[11],其结构尺寸如下:
Z头高3/4d,其中
d=D+(~1)(3-3)
则d=8+(~1)=8.mm,
Z头底部自分流道距离为5/4d,如下图所示:
冷料穴示意
第五章塑料件的工艺尺寸计算与侧向分型设计
、型芯工作尺寸计算
%%
平均收缩率:
=(%%)/2=%
型腔内径:
=46mm
型腔深度:
=
型芯外径:
=
型芯深度:
=
型腔径向尺寸(mm);
-塑件外形基本尺寸(mm);
-塑件平均收缩率;
-塑件公差
-成形零件制造公差,一般取1/4—1/6
;
-塑件内形基本尺寸(mm);
-型芯径向尺寸(mm);
-型腔深度(mm);
-塑件高度(mm)
-型芯高度(mm);
-塑件孔深基本尺寸(mm);
型腔:
钢材选用P20,使用数控精雕及电火花加工成型
型芯:
钢材选用P20,使用数控精雕及电火花加工成型
注塑模模架国家标准有两个,即GB/T12556——1990《塑料注射模中小型模架及其技术条件》和GB/T12555——1990《塑料注射模大型模架》。
由于塑料模具的蓬勃发展,现在在全国的部分地区形成了自己的标准,该设计采用龙记标准模架,型号为:
AI-1525-A30-B45-C60。
模架模型图
第六章导向机构的设计
导向机构的作用:
1)定位作用;2)导向作用;3)承受一定的侧向压力
导柱导向部分的长度应比凸模端面的高度高出8—12c