除锈防腐绝热施工方案.docx
《除锈防腐绝热施工方案.docx》由会员分享,可在线阅读,更多相关《除锈防腐绝热施工方案.docx(14页珍藏版)》请在冰豆网上搜索。
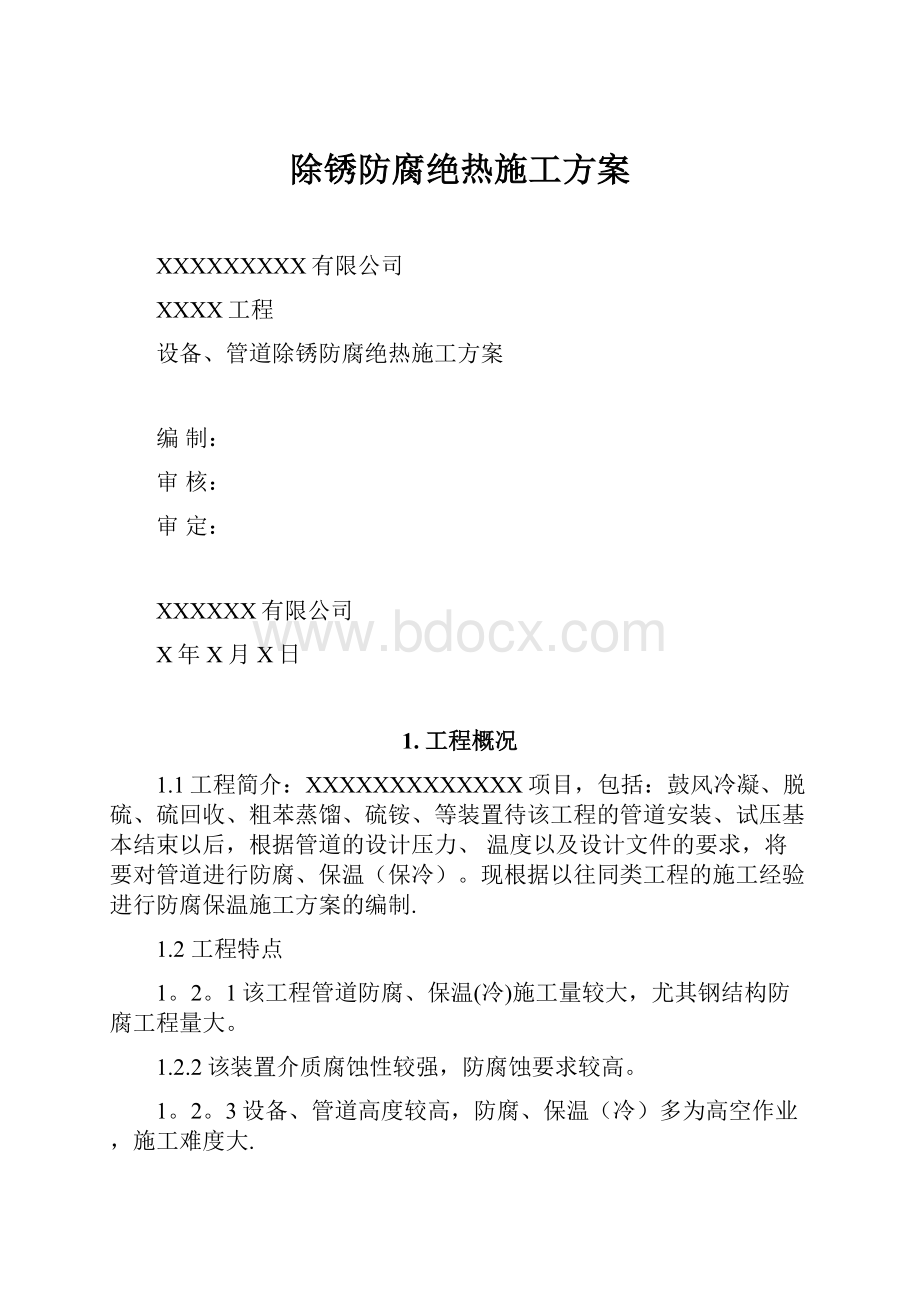
除锈防腐绝热施工方案
XXXXXXXXX有限公司
XXXX工程
设备、管道除锈防腐绝热施工方案
编制:
审核:
审定:
XXXXXX有限公司
X年X月X日
1.工程概况
1.1工程简介:
XXXXXXXXXXXXX项目,包括:
鼓风冷凝、脱硫、硫回收、粗苯蒸馏、硫铵、等装置待该工程的管道安装、试压基本结束以后,根据管道的设计压力、温度以及设计文件的要求,将要对管道进行防腐、保温(保冷)。
现根据以往同类工程的施工经验进行防腐保温施工方案的编制.
1.2工程特点
1。
2。
1该工程管道防腐、保温(冷)施工量较大,尤其钢结构防腐工程量大。
1.2.2该装置介质腐蚀性较强,防腐蚀要求较高。
1。
2。
3设备、管道高度较高,防腐、保温(冷)多为高空作业,施工难度大.
1.2.4交叉作业时间长,相对工期安排较为紧凑,需合理统筹安排方能确保工期和质量。
1.3技术要求
1。
3。
1绝热材料:
泡沫玻璃(-196~—60OC)、发泡聚氨脂(—80~0OC)、岩棉(0~350OC)、硅酸铝(350~800OC);
1。
3.2外保护层采用铝皮:
设备用0。
8~1。
0mm,管道用0。
5mm;
1.3.3所有需保温、保冷及需人身防护的碳钢设备管道表面均需喷砂机除锈达Sa2.5级,再涂防腐底漆一遍,对于非保温的管道设备,均需喷砂机除锈达Sa2.5级,应涂底漆两遍,面漆两遍;不锈钢的管道、设备及镀锌管原则上不涂漆,地下管外表面喷砂机除锈达Sa2。
5级,涂环氧沥青漆防腐,等级:
特加强级。
2。
编制依据
2。
1《石油化工设备和管道涂料防腐蚀技术规范》SH/T3022-2011
2.2《建筑防腐蚀工程质量验收规范》GB50224-2010
2.3《钢制储罐外防腐层技术标准》SY/T0320—2010
2。
4《钢制管道液体环氧涂料内防腐层技术标准》SY/T0457—2010
2。
5《石油建设工程质量检验评定标准防腐保温钢管制作》SY/T0468-2000
2.6《工业设备及管道绝热工程施工规范》GB50126—2008
2。
7《工业设备及管道绝热工程施工质量验收规范》GB50185—2010
3。
材料验收及施工准备
3.1防腐蚀施工所用材料必须符合国家行业标准,并具有出厂合格证和验收资料,必要时对原材料应进行抽查复检.
3.2绝热材料的品种、密度及规格等应符合设计文件要求。
3。
3绝热材料的性能指标应符合国家或行业标准国家或行业标准。
3.4材料堆放、保管应按品种、材质、规格、密度等划分区域、分类存放,并应作好防潮措施。
3。
5防腐绝热施工前,应充分熟悉技术文件,技术标准及验收规范,完成施工方案和技术交底,并进行安全技术教育.
3。
6设备、管子、管件应施工检验完毕并具有工序交接证书.
3。
7材料、机具检测仪器,施工设施及场地已齐备,
3.8防护设施安全可靠、施工用水、电、气等能满足连续施工的需要。
3.9绝热施工前,设备或管道的支吊架、支撑件、固定件及仪表接管等已安装完毕,强度试验、严密性试验、管道吹扫及表面防腐等工作应全部合格.
3.10设备及管道表面的油漆、尘土等杂物应清除干净。
4.施工工艺程序
4。
1支架防腐施工程序
4。
2地上管道防腐施工程序
4.3埋地管道防腐施工程序
4.4钢结构防腐
4。
5设备、管道保温施工程序
4.6操作方法
4.6。
1喷砂除锈操作方法选择
除锈操作方法选择
优点
缺点
备注
石英砂
除锈后钢材表面粗糙度均匀,生产效率高
施工过程中产生粉尘
工厂化预制厂中使用工业吸尘器除尘
钢砂
除锈质量好,无粉尘、改善了劳动条件
使用成本高
磨料可重复使用
结论
本工程选用以钢砂作磨料的干法喷砂对管道外壁及钢材进行工厂化喷砂除锈工作
、4.6.2涂料施工操作方法的选择
喷涂操作
方法选择
优点
缺点
备注
高压无气
喷涂
1)喷涂效率高
2)对涂料(粘度)适应性强
3)涂层厚
4)稀释剂用量少,减少对环境污染
5)涂料利用率高
6)一般拐角及间隙处都可喷涂
1)调节喷雾幅度和喷出量时需更换喷嘴
2)不宜喷涂面积较小的工件
贮罐、设备
钢结构:
≥58m2/t
管材:
管径≥273mm
空气
喷涂
1)操作稳定
2)更换涂料方便
3)漆膜光滑均匀
1)涂料罐小使用时要卸下加料
2)漆膜较薄涂料损失大环境污染大
3)只适合用于油漆粘度在50s以内
对于钢结构:
<58m2/t
管道:
管径<273mm
5。
施工技术要点
5.1防腐蚀施工
5。
1。
1设备管子、管件等金属表面处理采用机械砂轮除绣,除绣质量等级应符合设计要求。
5。
1。
2设备管子、管件等钢材表面,不得有伤痕、气孔、夹渣、重叠皮、严重腐蚀斑点,加工表面必须平整,表面局部凹凸不得超过2mm。
5。
1。
3防腐蚀施工,按常规:
不保温管道及设备,刷底漆两道,面漆两道,保温设备及管道刷底漆两道,如与设计要求不符,应按设计要求施工.
5。
1。
4涂漆环境要求:
5。
1。
4.1施工环境湿度易为15-30°C,相对湿度<85%,被涂物表面湿度应高于露点3°C以上。
5。
1.4。
2不能在风沙、雨天、雪天施工.
5。
1.5涂料的配制与施工
5.1.5.1所有涂料必须有出厂合格证、使用说明书,并要选用同一厂家的底、中、面漆,稀释剂配套使用。
5.1。
5。
2大面积施工前应进行试涂。
5.1.5.3涂料配置与施工所用工具,应保持清洁,不得混用。
5.1.5.4被涂物应垫起离开地面.
5.1.5。
5刷涂时,层间应纵横交错,每层都应涂刷均匀,无漏涂。
5。
1。
5。
6所用涂料的种类、名称、配比、层数均要符合设计要求。
5.1.5。
7底漆干固后,再进行各层的涂覆,每层漆的涂刷必须持前一层漆干固后进行。
5.1.6质量检查
5.1.6。
1每道涂层均应进行检查,涂层应光滑平整、颜色一致,无气泡、剥落、漏刷、反锈、透底和起皱等缺陷,用5-10倍的放大镜检查,无微孔者合格。
5.1.6。
2用磁性测厚仪测定漆膜厚度,其厚度偏差不得小于设计规定厚度的5%为合格.
5.2绝热层施工
5。
2。
1需保温设备、管道及其附件应全面检查,确认合格,并办理工序交接手续后,方可进行施工。
5.2.2保温层的厚度大于等于100mm时,应分层施工,分层厚度宜接近,同层错位,上、下层压缝,各层应均匀连续,层间不得有缺肉现象。
角封必须是盖式搭接,各层表面应找平,拼缝应规则整齐。
6。
2.3保温层缝隙应做严缝处理,其缝隙不应大于5mm.
5.2。
3保温层缝隙应作严缝处理,其缝隙不应大于5mm。
5。
2。
4保温层接缝施工
5.2。
4。
1软质材料绝热层接缝须紧密无缝,水平位置接缝须放在管道的侧面。
5.2。
4.2硬质材料绝热层应留伸缩缝。
5.2。
4。
3两个固定管架间水平管道绝热层的伸缩缝至少要留设一道。
5。
2。
4。
4立式设备及垂直管道,应在支撑环下留设伸缩缝.
5.2。
4.5弯头两端的管段上,可各留一道伸缩缝,当两弯头之间的间距很少时,可根据介质温度确定仅留一道或不留设.公称直径大于300mm的高温管道,必须在弯头中部增设一道伸缩缝。
5。
2.4.6应在卧式设备的筒体上距封头连接处100—150mm均设一道伸缩缝。
5.2.4.7伸缩缝留设的宽度:
设备为:
25mm,管道为:
25mm。
5。
2.4。
8伸缩缝内须清除杂物后,用矿物棉毡条或软质泡沫填严密,捆扎固定。
5.2.5绝热层的捆扎采用镀锌铁丝,DN≥100mm的管道采用18#镀锌铁丝捆扎.DN<100mm的管道采用20#镀锌铁丝,其捆扎间距岩棉管壳不应大与300mm,硅酸盐复合板不应大于200mm。
5.2。
6管道端部或有盲板的部位,应敷设绝热层,并应密封,法兰应在连接螺栓经热紧固后,进行绝热层施工,并应在法兰的一侧留出螺栓长度加25mm的空隙。
5。
2。
7设备绝热层施工其铭牌和标记不得覆盖,有座架时铭牌周围要割成喇叭型开口,开口处应密封规整,无座架时,铭牌应移至保护层外表面。
5.3保护层施工
5。
3。
1绝热层施工完毕,检查合格后应及时进行保护层的施工.
5。
3。
2正确下料,合理排版,精心加工预制。
5。
3。
2.1现场实测是以管道或设备绝热层的外表尺寸,确定保护层的下料规格。
5.3.2.2根据实测和计算进行放样,经检查合格后,方可下料,下料时应留出必要的要口量和搭接量。
5.3。
2。
3根据成型要求,分别进行压线、卷折方、压搭、咬口、冲孔等.
5。
3。
3管道金属保护层预制应按下列规定施工.
5.3。
3。
1直管圆筒式金属保护层,其下料尺寸,长度宜为1000mm,宽度应为绝热层外径周长加30—50mm。
并应在保护层的环向、纵向搭接缝一端压出凸筋线。
5.3。
3。
2弯头处的保护层,可选用虾米腰搭接式,虾米腰采用咬口式或冲压成型式结构.其下料尺寸根据接缝形式计算确定,搭接缝一端应压出凸筋线。
5。
3。
3.3弯管与直管段金属保护层搭接量应符合下列规定:
(1)高温管道:
75—150mm
(2)中低温管道:
60-70mm
(3)保冷管道:
30-50mm
5.3。
4设备保护层预制,应按下列规定施工:
5.3.4.1设备保护层下料尺寸,长度宜为1-2m,宽度宜为0。
5—1m。
根据搭接缝形式和膨胀收缩量,应留出20-50mm余量。
5.3.4.2设备封头保护层,应按封头绝热层表面尺寸分瓣下料.可采用咬口、插接或搭接等形式,根据接缝形式应分别留30-50mm余量,当采用搭接形式时,应在一端压出凸筋线,另一边为直边搭接,
5。
3.4.3阀门、法兰、人孔等处的保护层根据物件的外型尺寸,作成可拆卸式结构。
5.3。
5管道保护层安装,应符合下列规定:
5.3。
5。
1金属板应紧贴绝热层。
垂直管道应从支承板起由下向上敷设,搭缝应上口搭下口。
水平管道应从低处向高处敷设,纵向接缝位置布置在水平中心线下方15°—45°处缝口朝下.搭接量:
纵向搭接缝应在30—50mm,环向搭接缝应为50mm。
5。
3。
5。
2垂直管道或大于45°斜立管道上,应将金属板保护层分段固定在支承件上。
5。
3。
6设备保护层安装,应符合下列规定:
5.3。
6。
1金属板应紧贴绝热层.立式设备应由下向上敷设,环向接缝应采用搭接式或插接式,纵向接缝应采用咬口或插接式,纵向接缝应上下错缝。
卧式设备应由底部向上附设,纵向搭接缝应上口搭下口,其位置应留设在水平中心线上、下45°位置。
5.3.7已安装的金属保护层,严禁踩踏,有些部位不可避免时,应采取防护措施.
6.质量保证体系及保证措施
6.1质量保证措施
质量目标:
优良率80%以上,加强管理,奖优罚劣,提高职工质量意识,确保防腐、绝热质量。
6.2资料管理
施工技术员及时做好施工原始技术资料及其整理工作并协助班组填写各种施工记录。
6。
3材料管理
材料的合格证、材质证明、说明书、领料单等由材料员管理,坚决制止不合格品进入施工现场。
6.4施工过程管理
专职质检员巡回检查,每进行喷砂处理检验合格打上标识后方可允许进行防腐工作,发现不合格立即重新喷砂直至合格为止,并做好施工记录.
6.5检验管理
建立自检、互检和专职检查相结合的检验体系,不合格的产品坚决不允许进行下道工序。
7.安全文明施工及保证措施
7.1严格按照我公司ISO9001标准质量体系运行。
7.2认真熟悉设计文件、施工图纸及国家标准和施工规范,并结合产品使用说明书,做好施工方案和技术交底。
7.3执行质量层层负责制,每一环节都能设置专人把好质量关,除绣、防腐、绝热、防潮、保护层每道工序施工完毕后均须及时报检,上一道工序不合格,严禁进行下一道工序的施工。
7。
4防腐、绝热工程的操作人员应佩戴工作服、工作鞋、手套、口罩、毛巾等常用防护用品。
对接触有毒及腐蚀性材料的操作人员,必须佩戴防护工作服、防护(防毒)面具、防护鞋、防护手套等,并应备有防护药物和用具。
7。
5施工完毕或告一段落时,应将工机具及施工场地清理干净。
易燃、有毒物品应移至规定场所。
7。
6应在固定构件安装牢固后方可拆除临时支撑。
7.7拧紧绑扎铁丝时不得用力过猛,并应将铁丝头嵌人绝热层内。
7。
8作业现场应改善作业环境或采取严密保护措施,粉尘和有害气体的最高容许浓度应符合现行国家《工业企业设计卫生标准》的规定。
7.9施工现场应设有消防器材。
雨天禁止高空作业。
7.10脚手架应搭设牢固,跳板两头应与架管固定,不得悬空。
高空作业人员需佩带安全带,穿防滑鞋,不得高空抛掷传递物品。
7.11作业人员工作时间严禁饮酒。
防护用品不全或操作人员生病、服用有镇静作用药物的禁止高空作业。
8.环境保护措施
8。
1严格执行公司ISO18000环境管理模式,使各项环境保护措施得以贯彻落实。
8。
2各种边角料、成品、半成品分类堆放整齐,标识一目了然。
8.3各种机械应定期进行维修保养,确保机械正常运转减少噪声污染。
8。
4施工中焊条头要回收到指定地点保管,不得随意乱扔。
8.5废塑料袋、废纸箱、废砂轮片等应及时回收统一处理。
8.6喷沙时应设围棚,防止粉尘污染大气.
8.7防腐施工中的废油漆桶要及时回收,统一保管,并作好回收记录。
废毛刷等需及时回收统一处理。
8.8机械废油应分类存放,准备二次利用或统一回收处理。
9。
主要施工机具
机械或
设备名称
数量
额定功率(KW)
用于施工部位
备注
咬口机
2
2
绝热
卷管机
2
1。
5
绝热
压边机
2
2
绝热
喷枪
3
1
防腐
剪板机
1
2
绝热
电钻
20
1
绝热
喷砂机
3
防腐
拉铆枪
40
1
绝热