烟气脱硫技术方案实例.docx
《烟气脱硫技术方案实例.docx》由会员分享,可在线阅读,更多相关《烟气脱硫技术方案实例.docx(32页珍藏版)》请在冰豆网上搜索。
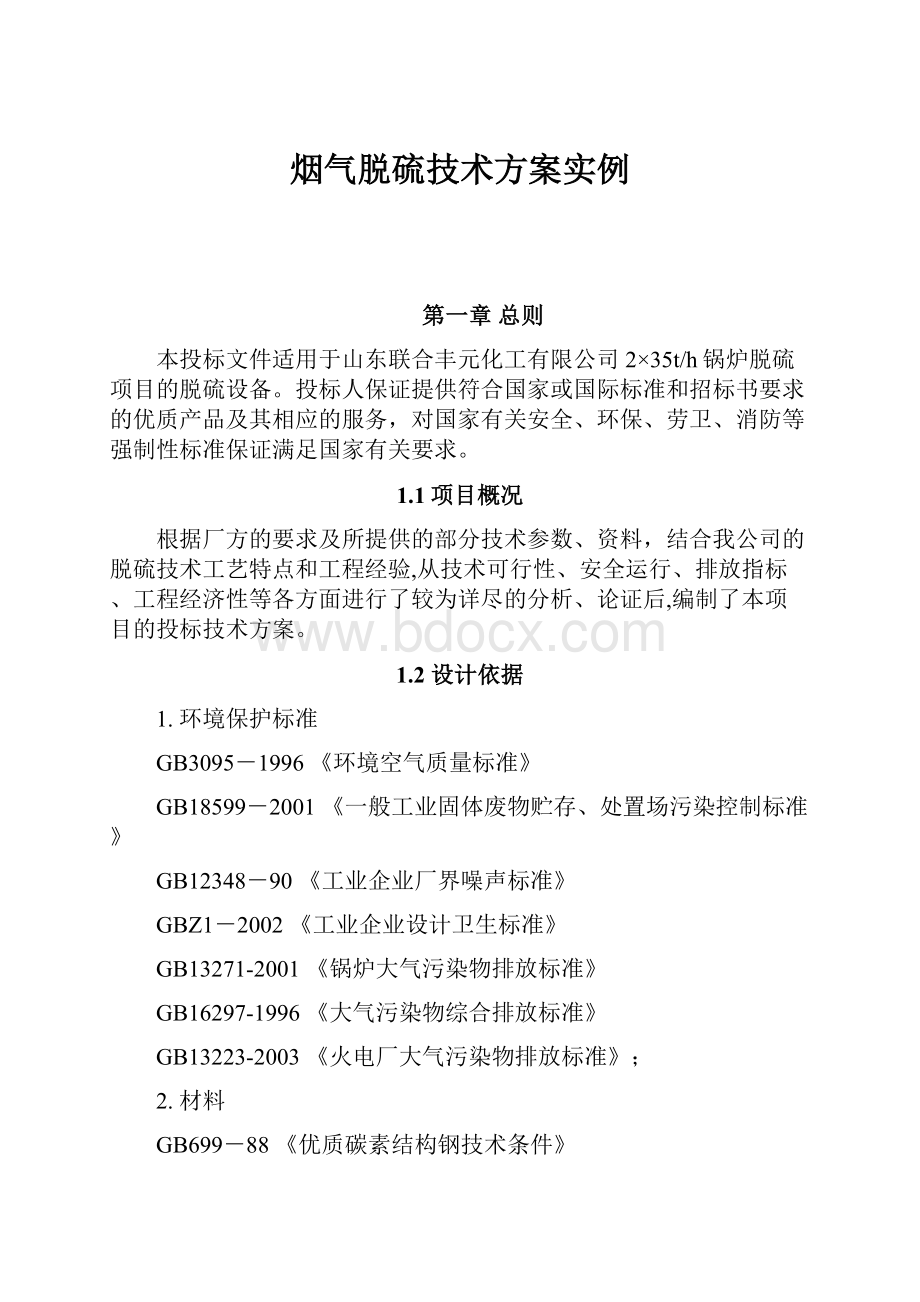
烟气脱硫技术方案实例
第一章总则
本投标文件适用于山东联合丰元化工有限公司2×35t/h锅炉脱硫项目的脱硫设备。
投标人保证提供符合国家或国际标准和招标书要求的优质产品及其相应的服务,对国家有关安全、环保、劳卫、消防等强制性标准保证满足国家有关要求。
1.1项目概况
根据厂方的要求及所提供的部分技术参数、资料,结合我公司的脱硫技术工艺特点和工程经验,从技术可行性、安全运行、排放指标、工程经济性等各方面进行了较为详尽的分析、论证后,编制了本项目的投标技术方案。
1.2设计依据
1.环境保护标准
GB3095-1996《环境空气质量标准》
GB18599-2001《一般工业固体废物贮存、处置场污染控制标准》
GB12348-90《工业企业厂界噪声标准》
GBZ1-2002《工业企业设计卫生标准》
GB13271-2001《锅炉大气污染物排放标准》
GB16297-1996《大气污染物综合排放标准》
GB13223-2003《火电厂大气污染物排放标准》;
2.材料
GB699-88《优质碳素结构钢技术条件》
GB711-85《优质碳素结构钢热轧厚钢板技术条件》
GB710-88《优质碳素结构钢薄钢板和钢带技术条件》
GB3087-82《碳钢焊条技术条件》
3.设备标准
JB1620-83《锅炉钢结构制造技术条件》
JB1615-83《锅炉油漆和包装技术条件》
GBJ17-91《钢结构设计规范》
GBJ10-89《混凝土结构设计规范》和1993年局部修订
GBJ7-89《建筑地基基础设计规范》
HCRJ040-1999《花岗石类湿式烟气脱硫除尘装置》
GB/T19229-2003《燃煤烟气脱硫设备》
GB50212-2002《建筑防腐蚀工程施工及验收规范》
4.设计、安装、调试
DL/T-5196-2004《火力发电厂烟气脱硫设计技术规程》;
DL/T5121-2000《火力发电厂烟风煤粉管道设计技术规程》
GB50054-95《低压配电设计规范》
GB50055-93《通用用电设备配电设计规范》
GB50254-96《电气装置安装工程低压电气施工和验收规范》
GB50217-94《电力工程电缆设计规范》
GB50205-95《钢结构施工及验收技术规范》
1.3设计原则
(1)确保烟气(烟尘、二氧化硫)达标排放并达到总量控制要求;
(2)确保烟气治理系统的安全、稳定运行;
(3)因地制宜,优化组合,制定具有针对性的技术实施方案;
(4)可利用废碱(液)脱硫,实现以废治废;
(5)采用先进、成熟的脱硫工艺技术和设备,在确保达到设计指标的前提下,结合厂方的实际情况,尽可能降低工程投资和运行费用。
1.4设计参数
本方案所依据的主要设计参数,来源于山东联合丰元化工有限公司提供技术要求,其中厂方未提供的部分数据,暂取经验值,主要原始设计参数见下表。
表1.1设计参数
项目
参数
锅炉额定蒸发量
35t/h
锅炉数量
2台
烟气量
90000m3/h
锅炉出口烟气温度
150℃
锅炉耗煤量
5.5t/h
燃煤含硫量
1.0%
年运行时间
8000h
1.5设计指标
设计指标根据相应的环保标准和招标书的要求执行。
具体的设计技术指标见表1.2。
表1.2设计技术指标
项目
技术指标(设计保证值)
林格曼黑度
≤1级
脱硫效率
≥90%
净烟气二氧化硫浓度
≤400mg/m3
脱硫装置压降
≤800Pa
净烟气含湿率
≤8%
净烟气温度
55~65℃
脱硫装置可用率
>99%
钙硫比
1.05
1.6设计范围
本方案设计范围包括:
风机出口至吸收塔出口之间的脱硫设备及相应的配套系统。
具体包括:
(1)烟气系统
(2)SO2吸收系统;
(3)吸收剂制备及供给系统;
(4)石膏脱水系统;
(5)工艺水系统;
(6)电气、自控系统;
(7)其它辅助设施及土建设施。
1.7技术方案总体说明
我方保证所提供的脱硫设备达到技术先进,所有设备的制造和设计符合安全可靠、连续有效运行的要求。
●脱硫工艺采用钠-钙双碱法。
●脱硫装置采用二炉一塔,脱硫装置的烟气处理能力为每台锅炉BMCR工况时30%~110%的烟气量,设计保证值为吸收塔出口二氧化硫浓度<400mg/m3。
●采用直接从厂外采购供应吸收剂的方案,不考虑在脱硫岛内设干磨或湿磨系统。
●避免在脱硫过程中带来新的环境污染。
废水用管道直接送到公司污水处理厂前池,由污水处理厂处理后排放。
●脱硫渣脱水后含水量≤10%,可安全、卫生外运。
●脱硫设备年平均运行时间按8000小时年考虑。
●FGD系统可用率≥99%。
●FGD装置设计寿命为30年。
根据招标方提出的实际参数,本脱硫装置的设计采用二炉一塔烟气系统,并满足锅炉负荷和运行方式时有良好的适应特性。
FGD装置将满足如下运行特性:
●全套烟气脱硫装置包括辅助设施能适应锅炉在2×35t/h时运行。
FGD装置在没有大量的和非常规的操作或准备的情况下,能顺利投入运行;特别是在锅炉不同模式运行工况下,FGD装置对锅炉运行方式能相适应。
而且FGD装置能够在烟气污染物浓度在一定范围内变化时也能正常运行,达到排放设计要求。
●FGD装置故障及退出运行时不影响发电机组的正常运行。
●本系统对整个装置的运行是重要和必需的设备设置备用。
●在装置停运期间,各个需要冲洗和排水的设备和系统(如:
浆液系统的泵、管道、箱罐等)在不需要过多的或非常规的准备和操作的情况下就能实现冲洗和排水。
●设计选用的材料能适应实际运行条件,包括考虑适当的腐蚀余量。
●在设备的冲洗和清扫过程中产生的废水收集在FGD系统的循环池内,然后送至吸收塔系统中重复利用。
第二章脱硫工艺
2.1双碱法脱硫工艺介绍
2.1.1烟气脱硫原理
湿式石灰/石灰石法技术工艺成熟,脱硫率高,但其主要缺点之一是容易结垢造成吸收系统的堵塞,而双碱法则是先用可溶性的碱性清液作为吸收剂吸收SO2,然后再用电石渣或石灰浆液对吸收液进行再生,由于在吸收和吸收液处理中,使用了两种不同类型的碱,故称为双碱法。
双碱法的明显优点是,由于采用液相吸收,从而不存在结垢和浆料堵塞等问题。
针对公司的实际情况,因此本方案拟选用钠-钙双碱法工艺。
钠-钙双碱法是以Na2CO3或NaOH溶液为第一碱吸收烟气SO2,然后再用石灰作为第二碱,对吸收液进行再生。
再生后的吸收液可循环使用。
其反应原理是:
(1)吸收反应
2NaOH+SO2——Na2SO3+H2O
Na2CO3+SO2——Na2SO3+CO2
Na2SO3+SO2+H2O——2NaHSO3
该过程中由于使用钠碱作为吸收液,因此吸收系统中不会生成沉淀物。
此过程的主要副反应为氧化反应,生成Na2SO4:
2Na2SO3+O2——2Na2SO4
(2)再生过程(用石灰浆液)
CaO+H2O——Ca(OH)2
2NaHSO3+Ca(OH)2——Na2SO3+CaSO3﹒1/2H2O
Na2SO3+Ca(OH)2——2NaOH+CaSO3﹒1/2H2O
再生后所得的NaOH液送回吸收系统使用。
所得半水亚硫酸钙可经氧化生成石膏(CaSO4﹒2H2O)。
此外,在运行过程中,由于烟气中还有部分的氧气,所以还有副反应-氧化反应发生:
2CaSO3﹒1/2H2O+O2+3H2O——2CaSO4﹒2H2O
2.1.2空塔喷淋脱硫工艺
烟气通过电除尘器后进入吸收塔,在吸收塔内烟气向上运动且被吸收液滴以逆流方式所洗涤。
喷嘴为无堵塞螺旋喷嘴,吸收液通过喷喷雾液滴800~1200μm,可使气体和液体得以充分接触,脱硫后的净烟气进入折流式除雾器,去除烟气中通过喷淋层夹带的水分。
双碱法喷淋空塔具有以下优点:
(1)系统简便,投资省;
(2)脱硫效率高;
(3)不易结垢;
(4)液气比低,电耗省,运行成本低;
(5)吸收塔采用喷淋空塔,阻力小,运行可靠。
(6)克服了旋流板塔易结垢、阻力大的缺点。
(7)以钠碱液为塔内主脱硫剂,以石灰或电石渣为脱硫液塔外再生剂,可以达到设备和管道不结垢。
(8)本脱硫装置同时也是二级除尘设备。
2.1.3脱硫设备说明
脱硫设备的工艺流程图和平面布置图见附图1和附图2。
整套设备由六大部分组成:
(1)烟气系统;
(2)SO2吸收系统;(3)吸收剂制备及供给系统;(4)石膏脱水系统;(5)工艺水系统;(6)电气、自控系统。
(1)烟气系统
本工程的FGD不设GGH,烟气从锅炉引风机后的烟道上引出,进入吸收塔。
在吸收塔内脱硫净化,经除雾器除去水雾,送入锅炉引风机后的总烟道,经然后烟囱排入大气。
在烟道上设一段旁路烟道,并设置旁路挡板门,当锅炉启动、进入FGD的烟气超温和FGD装置故障停运时,烟气由旁路挡板经烟囱排放。
烟气系统主要包括FGD进出口烟道,进出口挡板门,旁路挡板门以及与挡板门配套的电动执行机构。
(2)SO2吸收系统
锅炉烟气通过静电除尘器,除去99.5%左右的烟尘,然后进入引风机,在引风机出口进入FGD吸收塔,烟气从底部进入喷雾吸收塔,与喷淋液逆流接触。
烟气中的SO2经过FGD吸收塔的吸收,其出口烟气二氧化硫脱除率在90%以上。
净烟气在塔体上段通过高效组合式除雾装置(有二级除雾设施,机械去除雾滴效率在99.8%以上)除去烟气中的雾滴,净化后的烟气经塔后烟道进入烟囱排放。
吸收塔采用耐高温玻璃钢制作。
脱硫液在吸收塔内与烟气充分接触、反应后,经塔体底部排灰水沟回流入混合池,流入混合池的脱硫液与石灰(或电石渣)浆液进行再生反应。
循环混合池分为四个部分:
再生区,沉淀区,清水区和氧化区。
回流液首先进入再生池,与石灰浆液发生置换反应;接着进入沉淀区沉淀,上清液进入清水池后经循环水泵返回吸收塔。
沉淀则由泥浆泵打入氧化池,通入氧化空气进行氧化。
在本脱硫设备中,吸收塔为逆流式喷淋空塔,喷淋层为四层布置,在满足吸收SO2所需的比表面积的同时,同时满足不同锅炉负荷和含硫量的要求。
同时把喷淋造成的压力损失减少到最小。
每个喷淋层都装有多个雾化喷嘴,交叉布置,覆盖率可达200%-300%。
喷嘴采用螺旋喷嘴,材质为防腐耐磨的特种不锈钢喷嘴。
设计进水压力0.3Mpa。
吸收塔内的除雾装置由带加强的阻燃聚丙烯制作,主要由除雾板、反清洗装置组成,经除雾器后的烟气含水量在75mg/m3以下。
(3)吸收剂制备及供给系统
本工程脱硫吸收剂采用外购石灰粉(250目,90%过筛率),用气力输送系统将石灰粉送至制浆区的石灰粉仓储存。
储存于石灰粉仓中的石灰粉在流化风的流化下,通过旋转给料阀进入石灰浆液池,由搅拌机将粉与工艺水搅拌充分混合,制成浓度约15%~30%的石灰浆液,石灰浆液用浆液泵送至再生池进行置换反应。
(4)石膏脱水系统
氧化池的石膏浆液通过石膏排出泵送入石膏水力旋流站浓缩,浓缩后的石膏浆液进入真空皮带脱水机。
进入真空皮带脱水机的石膏浆液经脱水处理后表面含水率小于10%,由皮带输送机送入石膏储存间存放待运。
石膏旋流站的溢流浆液进入滤液池,以备吸收塔及石灰石制浆系统的循环使用。
石膏旋流站浓缩后的石膏浆液全部送到真空皮带机进行脱水运行。
为控制脱硫石膏中Cl-等成份的含量,确保石膏品质,在石膏脱水过程中用工业水对滤布进行冲洗,石膏过滤水大部分收集在滤液箱中,另一部分作为石膏冲洗水的补充。
(5)工艺水系统
工艺水系统负责提供FGD足够的水量,补充系统运行期间水的散失,以保证FGD系统的正常功能。
工艺水通常采用循环水排水作为水源,一般设置两台工艺水泵(一用一备),一个工艺水箱。
工艺水的主要用水如下:
系统的补充水,主要有:
除雾器冲洗水、石灰浆液补充水等。
不定期对系统的一些管路进行冲洗,水量不定。
主要有:
石灰浆液管路冲洗水,石膏排放管路冲洗水、污泥管路冲洗水等。
(6)电气、自控系统
为了保证系统脱硫效率稳定,本脱硫设备控制采用PLC+上位机,上位机画面上可在同时监视和控制脱硫设施内设备的运行。
2.2物料衡算
2.2.1二氧化硫产生量
两台锅炉的耗煤量为11t/h,燃煤含硫量为1.0%,则2台锅炉每小时产生的二氧化硫的质量为2×11000×1.0%×85%=187kg/h,按年8000工作小时计,二氧化硫的年产生量为1496吨。
2.2.2脱硫量
按平均脱硫效率90%计,则湿法脱硫年脱除量为1346.4吨。
2.2.3吸收塔的硫平衡
吸收塔的硫平衡见表2.1。
表2.1吸收塔的硫平衡
进
出
1#炉烟气带入的SO2
93.5kg/h
净烟气带出的SO2
18.7kg/h
2#炉烟气带入的SO2
93.5kg/h
钠碱液吸收的SO2
168.3kg/h
进脱硫塔总的SO2
187kg/h
出脱硫塔的Na2SO3
331.3kg/h
2.2.4系统总钠平衡
由于钠是在脱硫液塔外循环系统中循环使用,钠只是在循环过程中由排水及脱硫渣带走的一些损耗。
根据经验数据,纯Na(OH)耗量为10.5kg/h,钠碱溶液浓度按30%计,所需的该钠碱溶液为35kg/h。
2.2.5副产物和脱硫渣量产生量
脱硫的产物主是石膏(CaSO4﹒2H2O),灰水中除了烟气中吸收下来的尘以外,主要是亚硫酸钙(CaSO3﹒1/2H2O)及少量未反应的脱硫剂。
石膏(干基)的每小时产生量为0.5t/h。
2.2.6反应池钠、钙、硫平衡
反应池钠、钙、硫平衡见表2.2。
表2.2反应池钠、钙、硫平衡
进
出
进反应池的Na2SO3
331.3kg/h
出反应池的CaSO3
315.5kg/h
进反应池的Ca(OH)2
194.6kg/h
出反应池的Na(OH)
210.4kg/h
2.2.7系统的水平衡
脱硫循环用水为闭路循环,在整个系统中的补充水有除雾器冲洗水、各个泵的循环水、管路冲洗水和补充钠碱中含水等,整个系统的出水有蒸发水、脱硫渣带出的水和石膏结晶水等。
除雾器冲洗水、补充钠碱水及各个泵的循环水等补充水量为3.4t/h,
烟气蒸发的水量为3.25t/h,随脱硫渣带走的水分及石膏结晶水为0.15t/h,整个系统的水可以保持平衡。
第三章工程内容
3.1主要内容
3.1.1烟气系统
●吸收塔进口烟道、烟道挡板门及执行机构、净烟气烟道、烟道挡板门及执行机构、旁路烟道、烟道挡板门及执行机构。
从锅炉空气预热器来的烟气经静电除尘后由原引风机导入脱硫吸收塔。
为了防止因系统设备故障影响锅炉运行情况的发生,在脱硫主体设备旁设有100%容量旁路烟道,烟道进口设置入口挡板。
挡板为百叶窗形式,挡板及烟气管道全部采用钢制结构,外设加强筋板。
并对管道全部进行保温处理,保温层厚度50mm,外表面油漆饰面。
进出口烟道长度待初设时根据具体情况确定。
3.1.2SO2吸收系统
3.1.2.1FGD吸收塔
本脱硫系统采用两炉一塔形式,塔体材质为玻璃钢。
吸收塔采用4层喷淋+组合式除雾脱硫装置,空塔喷淋结构,脱硫效率≥90%。
●吸收塔包括吸收塔壳体、喷淋系统、组合式除雾器、预埋件及外部钢结构等。
●吸收塔采用耐腐耐磨花岗岩进行制作,能承受烟气飞灰和脱硫工艺固体悬浮物的磨损,并满足严格的防腐要求。
●吸收塔设计能防止液体泄漏。
塔体上的人孔、通道、连接管道等在壳体穿孔的地方进行密封,防止泄漏。
●吸收塔壳体设计能承受各种荷载,包括吸收塔及作用在吸收塔上的设备和管道的自重、介质重、保温重,以及风载、雪载、地震荷载等。
●吸收塔底面能完全排空浆液。
●塔的整体设计方便塔内部件的检修和维护,吸收塔内部的喷淋系统和支撑等不会堆积污物和结垢。
●吸收塔烟道入口段的设计考虑防止烟气倒流和固体物堆积。
●吸收塔配备足够数量和大小合适的人孔门,在附近设置走道和平台。
●吸收塔系统包括设置所有必需温度、压力等测点。
●喷淋系统的设计将合理分布要求的喷淋量,使烟气流向均匀,并确保吸收浆液与烟气充分接触和反应。
●喷头的选型将避免快速磨损、结垢和堵塞。
●喷嘴与管道的设计将便于检修,冲洗和更换。
●吸收塔顶部设置组合式除雾装置:
为了达到最佳脱水效果并有效防止除雾板的腐蚀,本次设计中除雾板的采用聚丙烯制作,除雾板在脱硫和脱水的同时也可以有效解决腐蚀与磨损问题。
除雾器的设计保证其具有较高的可利用性和良好的去除液滴效果。
除雾器冲洗用水为FGD工艺水,由单独设置的除雾器冲洗水泵提供。
3.1.2.2除雾器
除雾器是FGD系统中的关键设备,其性能直接影响到湿法FGD系统能否连续可靠运行。
除雾器系统由除雾器本体及冲洗系统组成。
烟气通过除雾器的弯曲通道,在惯性力及重力的作用下将气流中夹带的液滴分离出来:
脱硫后的烟气以一定的速度流经除雾器,烟气被快速、连续改变运动方向,因离心力和惯性的作用,烟气内的雾滴撞击到除雾器叶片上被捕集下来,雾滴汇集形成水流,因重力的作用,下落至浆液池内,实现了气液分离,使得流经除雾器的烟气达到除雾要求后排出。
除雾器的除雾效率随气流速度的增加而增加,这是由于流速高,作用于雾滴上的惯性力大,有利于气液的分离。
但是,流速的增加将造成系统阻力增加,也使能耗增加。
而且流速的增加有一定的限度,流速过高会造成二次带水,从而降低除雾效率。
通常将通过除雾器断面的最高且又不致二次带水时的烟气流速定义为临界流速,该速度与除雾器结构、系统带水负荷、气流方向、除雾器布置方式等因素有关。
具体为二级除雾器本体、冲洗水管道、喷嘴、支撑架、支撑梁及相关连接、固定、密封件等组成。
除雾器性能保证
(1)除雾效率:
在正常运行工况下,除雾器出口烟气中的雾滴浓度低于75mg/Nm3;
(2)压降:
不考虑除雾器前后的干扰,保证在100%烟气负荷下,整个除雾器系统的压降低于120Pa。
(3)耐高温:
80--95℃。
(4)耐压:
保证承受冲洗水压为0.3MPa时,叶片能正常工作。
(5)冲洗喷嘴:
为全锥形喷嘴,冲洗水喷射角度为90—120度,喷射实心圆锥,能够保证叶片全部被覆盖。
(我们设计的均为最大气体负荷时的水耗量,考虑到系统水平衡的要求,如果气体负荷降低,可通过增加冲洗间隔时间将水耗量降低一半)。
3.1.2.3脱硫液循环系统
本系统循环浆液管道的设计将满足系统循环水量要求、浆液管线布置无死区存在,以避免管道沉积和堵塞;吸收剂给料量根据吸收塔回流浆液PH值进行控制;有关阀门的选型能满足控制要求。
●吸收塔浆液循环泵
吸收塔循环泵选用防腐耐磨性能优良的高分子衬塑泵,共三台,两用一备。
循环泵为离心泵,叶轮由防腐耐磨材料制成。
泵吸入口配有滤网,以防止泵及系统的堵塞。
循环泵及驱动电机能适应户外露天布置的要求。
循环泵型号为150UHB-ZK-150-40,Q=150m3、H=40m、N=45KW。
●循环水池
包括混合池、沉淀池、清水池、氧化池。
循环混合池用钢筋混凝土砌筑,为地下池。
●污泥泵
设置二台污泥泵,一用一备。
将选用高分子防腐耐磨泵,另外包括电机、联轴器、泵和电机的底座、法兰、配件、紧固件等。
污泥泵型号为65UHB-ZK-10-12.5,Q=10m3、H=12.5m、N=2.2KW。
3.1.3吸收剂制备及供给系统
●石灰粉仓
本工程共设1个石灰粉贮仓,石灰粉贮仓的容量按不小于台锅炉在燃用设计煤种BMCR工况下7天的吸收剂总耗量设计。
石灰粉卸料及输送装置装置为带称重的螺旋定量给料机,满足随锅炉负荷的变化调整给料量,达到节省脱硫剂的目的。
石灰粉仓采用钢制结构,容积为30m3,设高低料位、仓顶装有布袋除尘器,锥斗段仓壁装有振打装置,避免石灰下料不畅。
●石灰粉制浆池
其有效容不小于二台锅炉BMCR工况的3小时左右的石灰浆液量,按10m3设计(2.0×2.0×2.5m),为了保持浆液的均匀性,石灰浆池装有搅拌器。
石灰粉制浆池为混凝土结构,包括搅拌机和对于搅拌机、溢流和排水需要的连接管道。
●石灰浆液泵
石灰浆液泵包括:
石灰浆液泵,设置2台,一用一备,将选用高分子防腐耐磨泵,另外包括电机、联轴器、泵和电机的底座、法兰、配件、紧固件等。
石灰浆液泵型号为65UHB-ZK-5-11,Q=5m3、H=11m、N=2.2KW。
3.1.4石膏脱水系统
●氧化风机:
氧化风机及驱动电机适应户外露天布置的要求。
氧化风机设置2台,一用一备,氧化风机采用空冷,氧化空气无油,氧化风机设置隔音罩。
氧化风机型号为RSR-80,Q=196m3/h、P=49KPa、N=5.5KW。
●石膏排出泵
设置二台脱硫石膏排出泵,一用一备。
将选用高分子防腐耐磨泵,另外包括电机、联轴器、泵和电机的底座、法兰、配件、紧固件等。
石灰浆液泵型号为65UHB-ZK-10-45,Q=10m3、H=45m、N=7.5KW。
●石膏旋流器
水力旋流器的入口浆液浓度为10%-15%,底流浓度为45%-55%(与石膏粒径分布有关),固相主要为粗大的石膏结晶,底流直接进入真空皮带脱水机进行过滤。
而溢流则进入废水池。
水力旋流器溢流含固量为1%-3%左右,固相颗粒细小,主要为为反应的吸收剂、细小的石膏结晶等。
石膏旋流器为自带支撑结构,所有支撑结构件采用碳钢构件。
石膏旋流器型号为FXDS100-GK-Ⅱ×2。
溢流液打入工艺楼地坑,底流液进入真空皮带脱水机进液箱。
●真空皮带脱水机
真空皮带脱水机与石膏旋流器位于工艺楼的不同层面,经其脱水后的石膏(含水率≤10%)进入石膏库储存。
真空皮带脱水机的作用原理为:
通过真空泵抽真空的作用,在滤饼上下表面形成压力差,并以此来挤出水分,达到脱水的目的。
在通常情况下,对石膏滤饼的Cl-含量有一定的要求,所以在脱水的同时使用滤饼冲洗水对滤饼进行冲洗,以达到冲洗Cl-的效果。
在二级脱水运行过程中,会遇到以下一些问题。
真空皮带脱水机型号为PBF2.4m2-400。
此设备与石膏排出泵同步运行,需要冲洗水量约为3~4m3/h。
3.1.5工艺水系统
工艺水系统包括工艺水泵及工艺水箱。
●工艺水泵
工艺水系统负责提供FGD足够的水量,补充系统运行期间水的散失,以保证FGD系统的正常功能。
工艺水通常采用循环水排水作为水源,设置两台工艺水泵(一用一备)。
水泵与整个脱硫系统同步运行,采用回流管路,采用带泄压阀或安全阀的回路。
工艺水泵型号为IS80-50-200,Q=50m3、H=50m,15KW。
●工艺水箱
工艺水箱采用碳钢进行制作,工艺水箱大小为10m3。
工艺水箱进水采用厂区的工业水,要求每小时的供水量不小于50m3。
3.1.6电气系统
本部分为脱硫岛电气系统的设计技术规范。
系统分为烟气吸收系统、脱硫剂制备及输送系统、脱水系统的电气系统。
电气系统包括:
配电系统、电气控制与保护、防雷接地系统、电缆和电缆构筑物、电气设备布置。
脱硫岛电气系统构建原则:
(1)电源:
低压用电系统:
采用动力、检修及照明共用的供电方式,中性点直接接地系统。
低压用电系统采用单母线接线方式。
(2)电缆敷设设施:
电缆敷设设施如桥架、电缆沟和金属管件
(3)接地:
脱硫岛接地网与厂区接地网将设置不少于两处连接,以两点连接至厂区接地网。
设计遵循IEC、GB、DL的标准。
设计应遵循下列标准,但不限于此:
《火力发电厂设计技术规程》DL5000-2000
《电力工程制图标准》DL5028-93
《继电保护和安全自动装置技术规程》DL400-91
《火力发电厂厂用电设计技术规定》DL/T5153-2002