煤化工.docx
《煤化工.docx》由会员分享,可在线阅读,更多相关《煤化工.docx(28页珍藏版)》请在冰豆网上搜索。
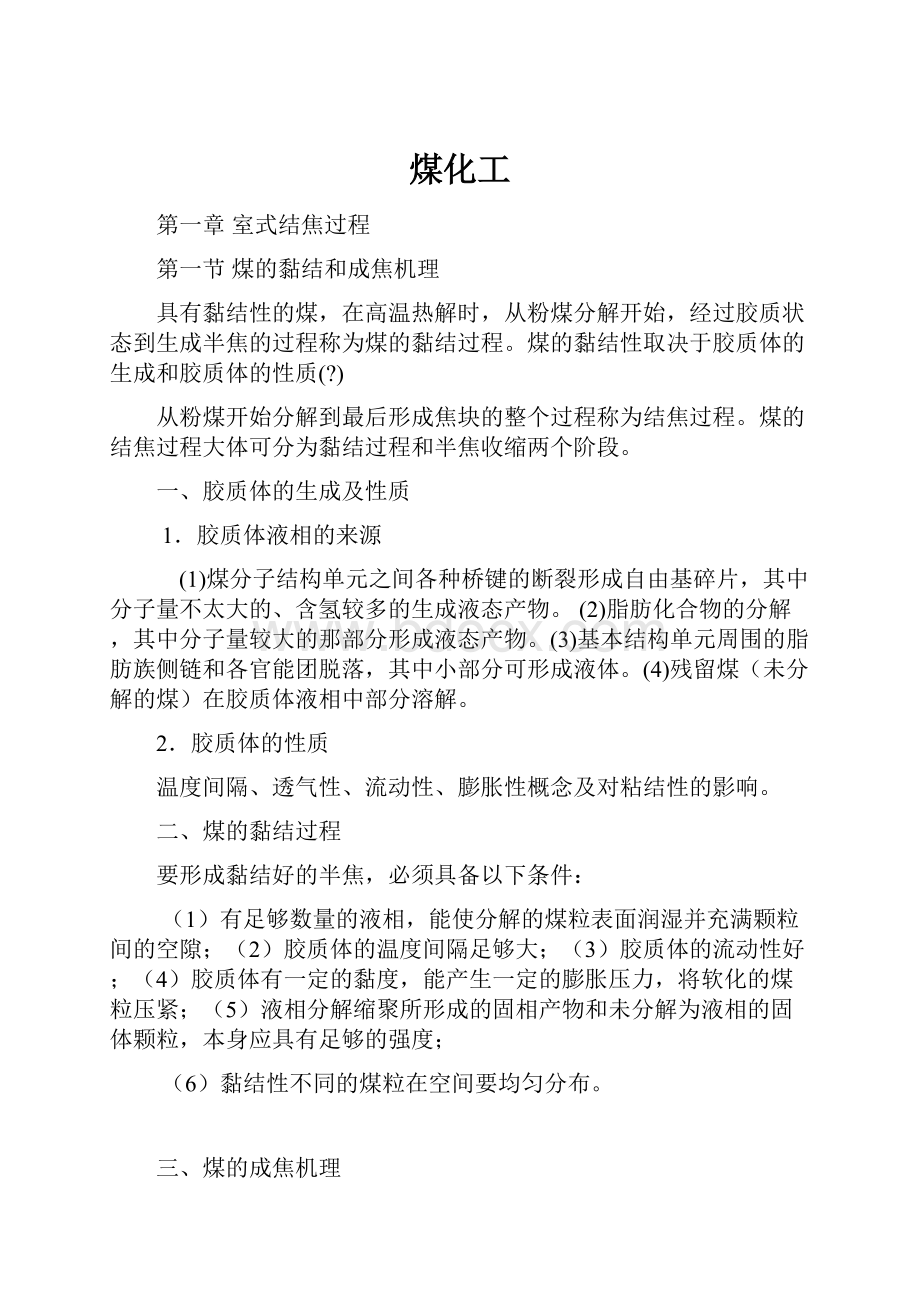
煤化工
第一章室式结焦过程
第一节煤的黏结和成焦机理
具有黏结性的煤,在高温热解时,从粉煤分解开始,经过胶质状态到生成半焦的过程称为煤的黏结过程。
煤的黏结性取决于胶质体的生成和胶质体的性质(?
)
从粉煤开始分解到最后形成焦块的整个过程称为结焦过程。
煤的结焦过程大体可分为黏结过程和半焦收缩两个阶段。
一、胶质体的生成及性质
1.胶质体液相的来源
(1)煤分子结构单元之间各种桥键的断裂形成自由基碎片,其中分子量不太大的、含氢较多的生成液态产物。
(2)脂肪化合物的分解,其中分子量较大的那部分形成液态产物。
(3)基本结构单元周围的脂肪族侧链和各官能团脱落,其中小部分可形成液体。
(4)残留煤(未分解的煤)在胶质体液相中部分溶解。
2.胶质体的性质
温度间隔、透气性、流动性、膨胀性概念及对粘结性的影响。
二、煤的黏结过程
要形成黏结好的半焦,必须具备以下条件:
(1)有足够数量的液相,能使分解的煤粒表面润湿并充满颗粒间的空隙;
(2)胶质体的温度间隔足够大;(3)胶质体的流动性好;(4)胶质体有一定的黏度,能产生一定的膨胀压力,将软化的煤粒压紧;(5)液相分解缩聚所形成的固相产物和未分解为液相的固体颗粒,本身应具有足够的强度;
(6)黏结性不同的煤粒在空间要均匀分布。
三、煤的成焦机理
形成半焦后,温度继续升高,半焦进一步分解:
1、析出分子量最小的气态产物而不生成焦油。
2、产生许多游离基,游离基发生缩聚反应,随着温度的升高,缩聚反应不断加强,使芳香碳网不断增大,碳网间的排列也越来越规则化。
当温度达到1000℃时,形成具有一定机械强度和一定块度的银灰色并具有金属光泽的焦炭。
四.半焦外型的变化产生裂纹?
半焦热缩聚必然引起体积收缩,而焦块的刚性阻止其收缩,半焦内便产生了内应力。
随着温度的升高,其内应力不断增加,当内应力大于半焦本身的强度时,使半焦破裂形成裂纹。
第三节炭化室内的结焦过程
1.炭化室内煤料结焦过程的基本特点有:
单向供热、成层结焦
结焦过程中传热性能随炉料的状态和温度而变化。
煤料水分愈多,结焦时间愈长,炼焦耗热量愈大。
因为:
水的汽化潜热大而煤的导温系数小;
水汽汇集
2.膨胀压力,最大膨胀压力,影响膨胀压力的因素?
煤种、加热速度、堆比重、添加瘦化剂或高挥发性气煤
3.工艺条件对结焦过程的影响?
(1)、加热速度
提高加热速度使煤料的胶质体温度范围加宽,流动性增加,从而改善煤料的黏结性,使焦块致密。
?
利用快速加热,可以提高弱黏结性的气煤、弱黏煤甚至长焰煤的黏结性,这就扩大了炼焦煤源。
但快速加热对半焦收缩是不利的,收缩应力大,产生的裂纹多。
故合理的加热速度应是黏结阶段快,收缩阶段慢。
现代焦炉炭化室内的结焦过程无法调节各阶段的加热,且实际上湿煤、干煤、胶质体由于导热性能差,加热速度慢,半焦和焦炭反而加热快,这是现代炭化室的根本缺点。
(2).煤料细度
煤料粉碎度和焦炭强度呈如下关系:
同一种煤的粉碎度增加,焦炭强度增加,当煤粉碎度达到某极限值后,继续增加时焦炭强度反而降低。
不同的煤种,和其焦炭强度的极大值对应的粉碎度取决于煤的黏结性,黏结性愈好的煤,与其焦炭强度极大值对应的煤粉碎度愈高。
但对配合煤而言一般情况为增加弱黏结煤的用量,则应对强黏结煤粗粉碎以保持其黏结性,弱黏结煤细粉碎以利于分散。
(3)、堆密度
增加装炉煤的堆密度,使煤粒间隙减小,膨胀压力增大,填充间隙所需的液态物质减少,在胶质体数量和性质一定时,可以改善煤的黏结性。
但堆密度的增大,收缩应力的增加,使焦炭的裂纹增加。
因此,只有当黏结性差的气煤配用量较大时,采用增加堆密度的方法来提高焦炭的强度。
(4).填加物
煤料黏结性不好时,可以加入沥青等黏结剂,增加结焦过程中的液相以改善黏结性。
但这种黏结剂应要求在煤料胶质体阶段有较好的热稳定性,故最好采用高沸点沥青。
当煤料收缩性很大时,可在不使煤黏结性降低很多的情况下,加入经细粉碎的无烟煤粉、焦粉等瘦化剂以减少收缩内应力,从而提高焦炭块度。
四、煤料硫分、灰分与焦炭硫分、灰分的关系
1.硫的动态与焦炭硫分
煤中的硫约有60%~70%转入焦炭中。
2.焦炭灰分
煤中灰分全部转入焦炭
第四节炼焦过程的化学产品
一、影响化学产品的因素
1.原料煤的影响
(1)煤化程度
对加热产物及产率的影响表现为:
煤化程度低的煤(如褐煤)热解时,煤气、焦油和热解水产率高,但由于没有黏结性(或很小),不能结成块状焦炭;
中等变质程度的烟煤,热解时煤气、焦油产率高而热解水少,黏结性强,能形成强度高的焦炭;
煤化程度高的煤(贫煤以上),煤气量少,基本没有焦油,由于没有黏结性,故生成大量焦粉。
(2)岩相组成的影响
不同煤岩成分其热解产物及产率不同:
煤气产率:
稳定组为最高,丝质组最低,镜质组居中;
焦油产率:
稳定组为最高,丝质组最低,镜质组焦油产率居中;
焦炭产量:
丝质组最高,镜质组居中,稳定组最低
2.外界条件的影响
(1)热解最终温度的影响
随着热解最终温度的升高,焦油和焦炭的产率下降,煤气产率增加,但煤气中氢含量增加,而烃类减少;焦油中的沥青和芳烃增加,酚类和脂肪烃含量降低。
焦炉的生产实践表明,700~800℃之间最适宜生产贵重的芳烃、苯、甲苯和二甲苯,此时产率最高。
(2)炉顶空间温度和容积的影响
从化学产品的产率和质量来说,炉顶空间温度以750℃左右为宜,但生产上为使焦饼中心温度达到950~1050℃,炉顶空间温度总是大于750℃,只能力求降低,不能完全满足。
炉顶空间温度超过900℃,焦油中含游离碳、萘、蒽、沥青增加,密度增大,含酚减少。
在平煤操作良好,荒煤气导出顺利的条件下,炉顶空间容积应尽可能小,以减少荒煤气在此停留时间,使二次热解适当。
(3)升温速度的影响
随着加热速度的增加,气体开始析出的温度和气体析出最大速度的温度迅速提高。
提高加热速度(缩短结焦时间),使煤气和焦油产率增加,焦炭产率减少,煤气中增加烯烃、苯、乙炔。
如在800℃以上热解,焦油中芳烃增加,萘含量增加,酸性油中苯酚较多,杂酚较少。
热解时的压力增加,可以阻止热解产物挥发和抑制低分子气体的生成,不利于化学产品的回收。
第二章炼焦用煤的预处理技术
第一节炼焦配煤
一、单种煤的结焦特性
二、配煤的意义和原则
配煤炼焦就是将两种或两种以上的单种煤,均匀地按适当的比例配合,使各种煤之间取长补短,生产出优质焦炭,并能合理利用煤炭资源,增加炼焦化学产品。
配煤原则:
(1)保证焦炭质量符合要求;
(2)焦炉生产中,注意不要产生过大的膨胀压力,在结焦末期要有足够的收缩度,避免推焦困难和损坏炉体;
(3)充分利用本地区的煤炭资源,做到运输合理,尽量缩短煤源平均距离,降低生产成本;
(4)在尽可能的情况下,适当多配一些高挥发分的煤,以增加化学产品的产率;
(5)在保证焦炭质量的前提下,多配气煤等弱黏结性煤,尽量少用优质焦煤,努力做到合理利用我国的煤炭资源
此外应考虑焦炉炉体的具体情况,回收车间的生产能力,备煤车间的设备情况等,如炉体损坏严重时,配煤的膨胀压力应小些,回收车间生产能力大时,可多配入高挥发分的煤。
总之,制定配煤比应遵循上述原则,根据配煤理论,拟定初步配煤方案,通过配煤试验,然后进行试生产。
三、配煤理论与焦炭质量预测
传统方法:
挥发分、流动度配煤
先进方法:
煤岩配煤(不考)
用煤化程度指标(挥发分)和黏结性指标(最大流动度)相结合可以反映煤的结焦性,而且这两个指标并非孤立,有着相互关系。
因此不但应该分别考虑各自的适宜值,而且应该考虑两者共同构成的适宜范围。
由此出发,在Vdaf-MF配煤图提出配合煤的适宜范围。
四、配合煤的质量指标及其计算方法
配煤质量指标主要是指配合煤的水分、灰分、挥发分、硫分、胶质层厚度、膨胀压力、黏结性及细度等。
1.水分
配合煤水分一般要求在8%~12%较为合适,并尽量保持稳定。
水分过小:
恶化焦炉装煤操作环境;
水分过大:
延长结焦时间、降低产量、增加耗热。
配煤的水分稳定,有利于焦炉加热制度稳定。
2.灰分
成焦过程中,煤料中的灰分几乎全部转入焦炭中。
灰分是惰性物质,灰分高则黏结性降低。
灰分的颗粒较大,硬度比煤大,它与焦炭物质之间有明显的分界面,而且膨胀系数不同,当半焦收缩时,灰分颗粒成为裂纹中心,灰分颗粒越大则裂纹越宽、越深、越长,所以配合煤的灰分高,则焦炭强度降低。
3.硫分
配合煤硫分可直接测出,也可将各单种煤的硫分按加和性计算。
硫在煤中是一种有害物质,在配煤炼焦中,可通过控制配煤比以调节配合煤的硫分含量,使硫分控制在1.1左右。
降低配合煤硫分的根本途径是降低洗精煤的硫分,或配用低硫洗精煤。
4.配合煤的煤化度指标
常用的煤化度指标有干燥无灰基挥发分Vdaf和镜质组平均最大反射率 。
可进行直接测定,也可按加和性计算,但两者之间有一定的差异。
炼焦时配合煤料适宜的煤化度指标是:
=1.2%~1.3%,相当于Vdaf=26%~28%。
5.配合煤的黏结性指标
根据结焦机理,配合煤中各组分的煤塑性温度区间应彼此衔接和依次重叠。
反映黏结能力大小的指标的适宜范围为:
黏结指数G=58~72,胶质层最大厚度Y=17~22mm,最大流动度MF为70~1000DDPM,奥亚膨胀度指标bt≥50%。
配合煤的黏结性指标一般不能用单种煤的黏结性指标按加和性计算。
6.配合煤的膨胀压力
单种煤的膨胀压力由多种因素决定,煤热解时配合煤中各组分煤之间存在着相互作用,因此其膨胀压力不能用简单的加和性来计算,只能通过实验的方法加以测定。
一般可采用200kg的实验焦炉,将炭化室的一侧炉墙做成可以活动的,通过活动炉墙和框架间的测压装置测定膨胀压力的大小。
在确定配煤方案时有两点内容值得参考:
一是在常规炼焦配煤范围内,煤料的煤化程度加深时,膨胀压力增大;
二是对同一煤料,增大堆密度,膨胀压力增加。
当用增加堆密度的方法来改善焦炭质量时,要注意膨胀压力可能产生的对炉墙的损害。
根据我国的生产经验,膨胀压力的极限值应不大于137~196Pa。
7.煤料细度
煤料必须粉碎才能均匀混合。
煤料细度是指粉碎后配合煤中的小于3mm的煤料量占全部煤料的质量百分率。
常规炼焦煤料细度要求为80%左右,捣鼓炼焦细度一般大于85%。
细度过低,混合不均匀,焦炭内部结构不均一,强度降低。
细度过高:
粉碎机动力消耗增大,设备生产能力降低;粘结性变差(堆密度下降,胶质体流动性差);装炉时的烟尘逸散,造成集气管内焦油渣增加,焦油质量变坏,加速上升管的堵塞。
在具体的配煤操作中,对于弱黏结煤,细度过低所造成的损害是主要的,应细粉碎;而对强黏结煤,细度过高所造成的不利是主要的,应粗粉碎。
五、配煤试验
(1)小焦炉
我国最常用的是200kg试验炉
(2)在炼焦炉中的试验
通过小焦炉试验,选出最佳方案,然后根据此方案,在生产焦炉上选择一孔或数孔焦炉进行工业试验,最终确定配煤方案。
第二节扩大炼焦配煤的途径(了解)
炉外干燥、预热、捣固、配型煤的方法炼焦;
配入添加物炼焦;
炼制缚硫焦
第四节炼焦用煤的粉碎与配合
一、粒度控制
1.各种煤的粉碎性
煤化度:
中等挥发分的强黏结煤,如焦煤和肥煤易被粉碎,弱黏结或不黏结煤,即长焰煤、气煤、瘦煤和无烟煤难粉碎。
煤的岩相组成:
镜煤粒子易碎,暗煤粒子难碎。
2.装炉煤的粒度分布原则
为实现粒度分布最优化以选择适当的粉碎工艺,应遵循以下四个原则:
(1)装炉煤的细粒化和均匀化
装炉煤的大部分粒度应小于3mm
(2)装炉煤的粉碎
黏结性好的煤,应粗粉碎,防止黏结性降低。
黏结性低的煤应细粉碎,以减少裂纹中心。
(3)控制装炉煤粒度的上下限
一般粒度下限均为0.5mm。
粒度上限随堆密度的提高而降低。
在散装煤的堆密度为0.75t/m3时,控制粒度上限为5mm较好,当堆密度为0.9t/m3时,粒度上限为3mm较好。
(4)煤料的堆密度最大原则
装煤炉中各粒级的含量,应保证粗、中、细煤粒间能相互填满空隙,以实现堆密度最大。
二、配煤工艺与设备
1、配煤槽的结构
2.定量给料设备
在配煤槽下部,设有煤料配量的定料给料设备,该设备主要有配煤盘和电磁震动给料机两种型式。
配煤盘的主要特点:
调节简单,运行可靠,维护方便。
但是,设备笨重,耗电量大,传动部件多,刮煤板易挂杂物,影响配煤准确度,需要经常清洗。
电磁振动给料机:
结构简单、维修方便、布置紧凑、投资少、耗电量小、调节方便。
但安装、调整时要求严格,如果调整不好,生产中将产生噪音。
使用情况:
目前电磁给料机多
三、备煤车间的工艺流程
1.先配合后粉碎工艺流程
2.先粉碎后配合工艺流程
3.分组粉碎工艺流程
4.选择粉碎工艺流程
各工艺的特点,适用性
第三章炼焦炉
第一节炉体构造
炼焦炉体由哪几部分构成,各部分的作用?
三室两区
比如:
燃烧室位于炭化室两侧,其中分成许多火道,煤气和空气在其中混合燃烧,产生的热量传给炉墙,间接加热炭化室中煤料,对其进行高温干馏。
再比如:
蓄热室位于炭化室的正下方,其上经斜道同燃烧室相连,其下经废气盘分别同分烟道、贫煤气管道和大气相通。
作用:
蓄积废气(1300℃左右)的热量来预热燃烧所需的空气量和贫煤气量。
第二节焦炉的结构类型
1、火道型式?
2、实现高向加热均匀性的四种方法
3、煤气的入炉方式?
第三节炉型举例
58-Ⅱ型焦炉
结构特点:
双联火道带废气循环,焦炉煤气下喷,两格蓄热室的复热式焦炉。
第四章炼焦炉机械
§5-1 护炉设备
一、护炉设备的作用
•1.焦炉为什么需要护炉铁件?
内因:
升温,炉体膨胀;
外因:
机械力 煤料的膨胀压力
推焦时焦饼的侧挤压
摘、挂炉门时的机械冲撞
二、护炉设备的构成
•构成:
炉柱、拉条、弹簧、保护板和炉门框
•各自的作用:
炉柱:
它通过弹簧把压力传递给炉体,以控制炉体的自由膨胀;同时由于炉门框和保护板均依靠炉柱和弹簧的压力来抵抗例如推焦时的冲击和振动;此外,还支撑集气管装煤车等设备。
拉条:
与炉柱一起组成骨架,固定护炉铁件,防止焦炉倾斜。
纵横拉条
弹簧:
利用弹簧势能,借助保护板、拉条等铁件连续不断地向焦炉施加数量足够、分布合理的保护性压力,使砌体在外力作用下保持完整与严密,并有足够的强度。
二、护炉设备的构成
保护板和炉门框:
保护整个燃烧室砌砖不直接受机械碰撞和冷空气袭击,同时传递炉柱上弹簧的压力,使压力均匀分布在燃烧室炉头砌体上
§5-2 煤气设备
•一、荒煤气导出系统与设备有哪些?
作用?
•二、废气开闭器的类型?
作用?
一、荒煤气导出系统与设备
•作用:
导出、冷却荒煤气;控制炭化室内正压。
•构成:
•上升管;
•桥管;
•集气管;
•П形管;
•氨水喷洒系统;
•吸气主管。
三、废气开闭器
•蓄热室上、下行气流的切换开关,并控制空气、废气的流量。
•提杆式双砣盘型
•杠杆式砣型
5-3焦炉机械
炼焦生产中焦炉机械包括:
顶装焦炉用装煤车、推焦车、拦焦车和熄焦车(焦炉四大车)。
作用?
侧装焦炉用装煤推焦车代替装煤车和推焦车,增加了捣固机和消烟车,用以完成炼焦炉的装煤出焦任务。
第五章
第二节炼焦化学产品的生成与组成和产率
二、影响化学产品产率和组成的因素
炼焦化学产品的产率取决于炼焦配煤的性质和炼焦过程的技术操作条件。
1.配煤性质和组成的影响
焦油、粗苯及煤气产率取决于配煤的挥发分。
煤气中硫化物的产率主要取决于煤中的硫含量。
煤气的成分同干馏煤的变质程度有关。
2.焦炉操作条件的影响
影响因素:
炼焦温度、操作压力、挥发物在炉顶空间停留时间、焦炉内生成的石墨、焦炭或焦炭灰分中某些成分(催化作用)
最主要的影响因素:
炉墙温度(与结焦时间相关)
炭化室顶部空间温度
(1)炉顶部空间温度
炉顶部空间温度不宜超过800℃
温度过高:
由于热解作用,焦油和粗苯的产率均将降低,化合水产率将增加;
氨进行逆反应而部分分解,并在赤热焦炭作用下生成氰化氢,氨的产率降低。
(2)加热温度
高温会使煤气中甲烷及不饱和碳氢化合物含量减少,氢含量增加,因而煤气体积产量增加,热值降低。
(3)炭化室压力
炭化室内压力高时,煤气会漏入燃烧系统而损失;
炭化室内形成负压时,空气被吸入,部分化学产品燃烧,氮和二氧化碳含量增加,煤气热值降低。
化产回收车间功能:
进行冷却、输送,回收焦油、氨、硫、苯族烃等化学产品,同时净化煤气。
两个目的:
为得到有用的化学产品
便于煤气顺利地输送、储存和用户的使用。
煤气中的障害的物质:
含量虽少,却有害
如萘会以固体结晶析出,堵塞设备及煤气管道;
焦油蒸汽存在有害于氨和苯族烃的回收;
氨水溶液会腐蚀设备和管路,等。
对于障害物质,根据煤气的用途不同而有不同程度的清除要求,因而从煤气中回收化学产品及净化方法的流程也有所不同。
对荒煤气一般采用的处理方法:
冷却、冷凝的方法除去煤气中的焦油和水;
用电捕方法除少量的焦油雾;
煤气中其他成分的脱除大多采用吸收法;对于净化程度要求高的场合,可采用吸附法或冷冻法。
一、在正压下操作的焦炉煤气处理系统
了解工艺流程
特点:
正压下操作,煤气体积小,有关设备及煤气管道尺寸相应较小;吸收氨、苯族烃等的吸收推动力较大,有利于提高吸收速率和回收率;安全。
二、在负压下操作的焦炉煤气处理系统
了解工艺流程
优缺点
全负压流程中的设备均处于负压下操作,鼓风机入口压力为-7~-10kpa,机后压力为15~17kPa。
此种系统发展于德、法等国,目前中国也有采用。
全负压处理系统具有如下优点:
(1)不必设置煤气终冷系统和黄血盐系统:
(2)可减少低温水用量,总能耗亦有所降低,
(3)净煤气经鼓风机压缩升温后,成为过热煤气,远距输送时,冷凝液甚少,减轻了管道腐蚀。
缺点:
(1)负压状态下,煤气体积增大,有关设备及煤气管道相应增大。
例如洗苯塔直径约增7%~8%,
(2)负压设备与管道越多,漏入空气的可能性增大,需特别加强密封:
(3)在较大的负压下,煤气中硫化氢、氨和苯族烃的分压也低。
减少了吸收推动力。
据计算,负压操作下苯族烃回收率比正压操作时降低2.4%。
综上所述,全负压回收工艺可供采用水洗氨工艺或弗萨姆法生产无水氨工艺的回收系统选用。
煤气净化车间回收的焦油和粗苯,经过进一步的精制可得到许多产品。
精制车间过去多设于同一焦化厂内,致使生产规模、品种及技术发展均受到限制。
近年来的发展趋势是将焦化厂生产的粗焦油和粗苯集中加工。
第六章煤气的初冷和焦油氨水的分离
一、将出炉煤气在鼓风机前进行初步冷却的原因?
焦炉煤气从炭化室经上升管逸出时的温度为650-750℃,此时煤气中含有焦油气,苯族烃、水汽,氨、硫化氢、氰化氢,萘及其他化合物,为回收和处理这些化合物,首先应将煤气冷却,这是因为:
1.从煤气中回收化学产品和净化煤气时,多采用比较简单易行的冷凝,冷却法和吸收法,在较低的温度下(25~35℃)才能保证较高的回收率;
2.含有大量水汽的高温煤气体积大(例如0℃时lm3干煤气,在80℃经水蒸汽饱和后的体积2.429m3,而在25℃经水汽饱和的体积为1.126m,前者比后者大1.16倍),显然所需输送煤气管道直径、鼓风机的输送能力和功率均增大,这是不经济的;
3.在煤气冷却过程中,不但有水汽冷凝,且大部分焦油和萘也被分离出来,部分硫化物,氰化物等腐蚀性介质溶于冷凝液中,从而可减少回收设备及管道的堵塞和腐蚀。
2.集气管用氨水而不用冷水喷洒,原因?
①因冷水温度低不易蒸发,使煤气冷却效果不好,所带入的矿物杂质会增加沥青的灰分。
②由于水温很低,使集气管底部剧烈冷却、冷凝的焦油黏度增大,易使集气管堵塞。
③氨水又有润滑性,便于焦油流动,可以防止煤气冷却过程中煤粉、焦粒、焦油混合形成的焦油渣因积聚,而堵塞煤气管道。
煤气冷却的流程:
间接冷却
直接冷却
间直混合冷却
三种流程各有的优缺点?
中国目前广泛采用的是横管式冷却器间接初冷工艺。
三、间冷和直冷结合的煤气初冷
煤气的直接初冷法,不仅冷却了煤气,且具有净化煤气效果良好、设备结构简单造价低及煤气阻力小等优点。
间冷直冷结合的煤气初冷工艺即是将二者优点结合的方法,在国内外大型焦化已得到采用。
高温冷却阶段:
间接冷却
低温冷却阶段:
直接冷却
4、间冷和直冷结合的煤气初冷原理
高温冷却阶段50-55℃:
间接冷却 ?
①自集气管来的荒煤气几乎为水蒸汽所饱和,水蒸汽热焓约占煤气总热焓的94%,所以煤气在高温阶段冷却所放出的热量绝大部分为水蒸汽冷凝热,因而传热系数较高;
②在温度较高时(高于52℃),萘不会凝结造成设备堵塞。
低温冷却阶段:
直接冷却?
低温冷却阶段,由于煤气中水汽含量已大为减少,气体对壁面间的对流传热系数低,同时萘的凝结也易于造成堵塞。
所以,此阶段宜采用直接冷却。
循环氨水、剩余氨水?
一、煤气冷却设备
横管式间接冷却器
结构、特点及工作原理
直接式冷却塔
结构、特点及工作原理
第七章煤气的输送和焦油雾的清除
一、煤气输送系统及阻力
吸入方(机前)为负压,压出方(机后)为正压,鼓风机的机后压力与机前压力差为鼓风机的总压头
鼓风机的位置:
(1)一般设置在初冷器后面:
鼓风机吸入的煤气体积小,负压下操作的设备和煤气管道少。
(2)有的焦化厂将油洗萘塔及电捕焦油器设在鼓风机前,进入鼓风机的煤气中焦油、萘含量少,可减轻鼓风机及以后设备堵塞,有利于化学产品回收和煤气净化。
(3)全在负压下回收化学产品的系统,鼓风机设置在洗苯塔后(净化末端)。
二.离心式鼓风机的性能与调节
转速不变时鼓风机的Q—H特性曲线
所以,B点右侧的特性曲线范围是鼓风机的稳定工作区,B点的左侧为鼓风机的不稳定工作区。
低流量时的常用的调节方法有以下几种:
(上述调节方法可联合使用)
(1)改变转速
(2)进口节流。
(3)出口节流。
(4)交通管调节。
一、煤气中焦油雾的形成和清除目的
煤气中焦油雾需较彻底地清除,否则对化产回收操作产生严重影响。
?
危害:
焦油雾在饱和器凝结下来,会使硫铵质量变坏;焦油雾进入洗苯塔内,会使洗油质量变坏,影响粗苯的回收;等等。
从焦油雾滴的大小及所要求的净化程度来看,采用电捕焦油器最为经济可靠。
二、电捕焦油器
1.电捕焦油器的工作原理?
2、绝缘箱在结构采取了哪些特殊的安全措施?
将压力氮气充入,蛇管蒸汽加热器,顶部设排气阀,设有与大气相通的气孔
为了保证电捕焦油器的正常工作,除对设备本身及其操作要求外;主要是:
1要维护好绝缘装置
2控制好绝缘箱温度
3保证氮气的压力及通入量
4定期擦拭清扫绝缘子。
此外,还要经常检查煤气含氧量,目前有些厂增加了煤气含氧量自动检测装置用以控制,并将煤气含氧控制在1.5%以下。
第八章煤气中氨和粗轻吡啶的回收
一、硫铵生产的方法原理
1.硫铵生产的方法
三种方法半直接法、直接法和