LED结温.docx
《LED结温.docx》由会员分享,可在线阅读,更多相关《LED结温.docx(8页珍藏版)》请在冰豆网上搜索。
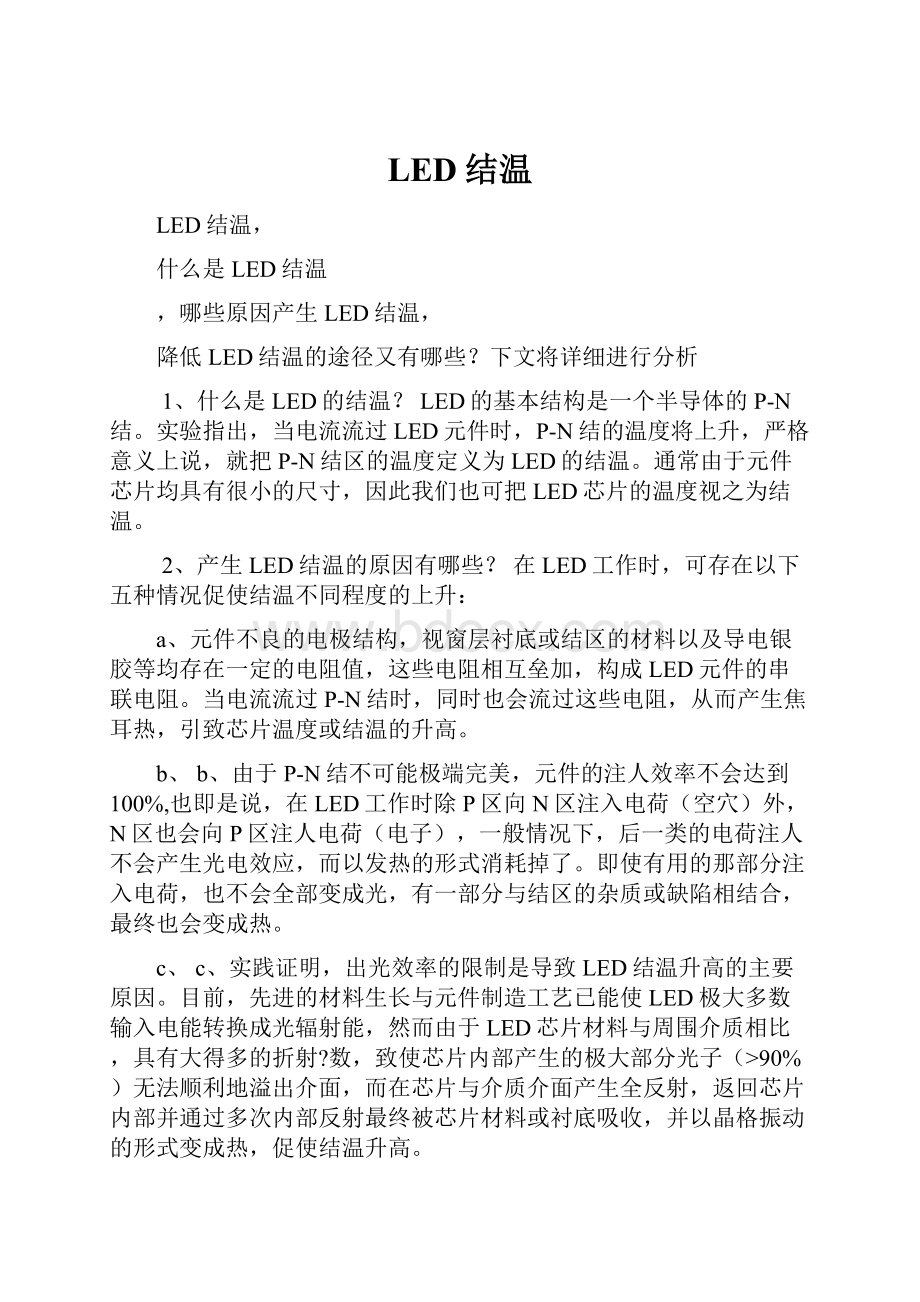
LED结温
LED结温,
什么是LED结温
,哪些原因产生LED结温,
降低LED结温的途径又有哪些?
下文将详细进行分析
1、什么是LED的结温?
LED的基本结构是一个半导体的P-N结。
实验指出,当电流流过LED元件时,P-N结的温度将上升,严格意义上说,就把P-N结区的温度定义为LED的结温。
通常由于元件芯片均具有很小的尺寸,因此我们也可把LED芯片的温度视之为结温。
2、产生LED结温的原因有哪些?
在LED工作时,可存在以下五种情况促使结温不同程度的上升:
a、元件不良的电极结构,视窗层衬底或结区的材料以及导电银胶等均存在一定的电阻值,这些电阻相互垒加,构成LED元件的串联电阻。
当电流流过P-N结时,同时也会流过这些电阻,从而产生焦耳热,引致芯片温度或结温的升高。
b、b、由于P-N结不可能极端完美,元件的注人效率不会达到100%,也即是说,在LED工作时除P区向N区注入电荷(空穴)外,N区也会向P区注人电荷(电子),一般情况下,后一类的电荷注人不会产生光电效应,而以发热的形式消耗掉了。
即使有用的那部分注入电荷,也不会全部变成光,有一部分与结区的杂质或缺陷相结合,最终也会变成热。
c、c、实践证明,出光效率的限制是导致LED结温升高的主要原因。
目前,先进的材料生长与元件制造工艺已能使LED极大多数输入电能转换成光辐射能,然而由于LED芯片材料与周围介质相比,具有大得多的折射?
数,致使芯片内部产生的极大部分光子(>90%)无法顺利地溢出介面,而在芯片与介质介面产生全反射,返回芯片内部并通过多次内部反射最终被芯片材料或衬底吸收,并以晶格振动的形式变成热,促使结温升高。
d、d、显然,LED元件的热散失能力是决定结温高低的又一个关键条件。
散热能力强时,结温下降,反之,散热能力差时结温将上升。
由于环氧胶是低热导材料,因此P-N结处产生的热量很难通过透明环氧向上散发到环境中去,大部分热量通过衬底、银浆、管壳、环氧粘接层,PCB与热沉向下发散。
显然,相关材料的导热能力将直接影响元件的热散失效率。
一个普通型的LED,从P-N结区到环境温度的总热阻在300到600℃/w之间,对于一个具有良好结构的功率型LED元件,其总热阻约为15到30℃/w.巨大的热阻差异表明普通型LED元件只能在很小的输入功率条件下,才能正常地工作,而功率型元件的耗散功率可大到瓦级甚至更高。
3、降低LED结温的途径有哪些?
a、减少LED本身的热阻;
b、良好的二次散热机构;
c、减少LED与二次散热机构安装介面之间的热阻;
d、控制额定输入功率;
e、降低环境温度LED的输入功率是元件热效应的唯一来源,能量的一部分变成了辐射光能,其?
部分最终均变成了热,从而抬升了元件的温度。
显然,减小LED温升效应的主要方法,一是设法提高元件的电光转换效率(又称外量子效率),使尽可能多的输入功率转变成光能,另一个重要的途径是设法提高元件的热散失能力,使结温产生的热,通过各种途径散发到周围环境中去。
led怕高温的,他的结温是125度,led最高承受温度在80来度,整灯外壳温度一般会要求小于65度,呵呵温度越低越好,大功率的温度一般在80度都是很正常的,当工作时散热不理想使结温升高后,电压小幅变大,导致电流变大,甚至烧坏内部金线。
解决办法是LED采用恒流源驱led外形是环氧树脂胶水,空气温度对他造成死灯的情况不长见,但也不要超出200度。
如果是灯不亮可能是静电给里面的发光芯片击穿先造成漏电,然后死灯的。
还有就是作业时的温度要求,LED因为一般要经过焊接使用的,所以焊接位置是LED胶体下面最少3MM烙铁温度最高260度时间最长3S,但这只是正常LED使用时规格书中的要求,有时超出这个要求也不一定会死灯,但在这个要求之内使用LED一定是正常的,只要作业时防静电做到位。
LED是个光电器件,其工作过程中只有15%~25%的电能转换成光能,其余的电能几乎都转换成热能,使LED的温度升高。
在大功率LED中,散热是个大问题。
例如,1个10W白光LED若其光电转换效率为20%,则有8W的电能转换成热能,若不加散热措施,则大功率LED的器芯温度会急速上升,当其结温(TJ)上升超过最大允许温度时(一般是150℃),大功率LED会因过热而损坏。
因此在大功率LED灯具设计中,最主要的设计工作就是散热设计。
另外,一般功率器件(如电源IC)的散热计算中,只要结温小于最大允许结温温度(一般是125℃)就可以了。
但在大功率LED散热设计中,其结温TJ要求比125℃低得多。
其原因是TJ对LED的出光率及寿命有较大影响:
TJ越高会使LED的出光率越低,寿命越短。
K2系列白光LED的结温TJ与相对出光率的关系。
在TJ=25℃时,相对出光率为1;TJ=70℃时相对出光率降为0.9;TJ=115℃时,则降到0.8了。
TJ=50℃时,寿命为90000小时;TJ=80℃时,寿命降到34000小时;TJ=115℃时,其寿命只有13300小时了。
TJ在散热设计中要提出最大允许结温值TJmax,实际的结温值TJ应小于或等于要求的TJmax,即TJ≤TJmax。
大功率LED的散热路径.
大功率LED在结构设计上是十分重视散热的。
图2是Lumiled公司K2系列的内部结构、图3是NICHIA公司NCCW022的内部结构。
从这两图可以看出:
在管芯下面有一个尺寸较大的金属散热垫,它能使管芯的热量通过散热垫传到外面去。
大功率LED是焊在印制板(PCB)上的,如图4所示。
散热垫的底面与PCB的敷铜面焊在一起,以较大的敷铜层作散热面。
为提高散热效率,采用双层敷铜层的PCB,其正反面图形如图5所示。
这是一种最简单的散热结构。
热是从温度高处向温度低处散热。
大功率LED主要的散热路径是:
管芯→散热垫→印制板敷铜层→印制板→环境空气。
若LED的结温为TJ,环境空气的温度为TA,散热垫底部的温度为Tc(TJ>Tc>TA),散热路径如图6所示。
在热的传导过程中,各种材料的导热性能不同,即有不同的热阻。
若管芯传导到散热垫底面的热阻为RJC(LED的热阻)、散热垫传导到PCB面层敷铜层的热阻为RCB、PCB传导到环境空气的热阻为RBA,则从管芯的结温TJ传导到空气TA的总热阻RJA与各热阻关系为:
RJA=RJC+RCB+RBA
各热阻的单位是℃/W。
可以这样理解:
热阻越小,其导热性能越好,即散热性能越好。
如果LED的散热垫与PCB的敷铜层采用回流焊焊在一起,则RCB=0,则上式可写成:
RJA=RJC+RBA
散热的计算公式
若结温为TJ、环境温度为TA、LED的功耗为PD,则RJA与TJ、TA及PD的关系为:
RJA=(TJ-TA)/PD
(1)
式中PD的单位是W。
PD与LED的正向压降VF及LED的正向电流IF的关系为:
PD=VF×IF
(2)
如果已测出LED散热垫的温度TC,则
(1)式可写成:
RJA=(TJ-TC)/PD+(TC-TA)/PD
则RJC=(TJ-TC)/PD(3)
RBA=(TC-TC)/PD(4)
在散热计算中,当选择了大功率LED后,从数据资料中可找到其RJC值;当确定LED的正向电流IF后,根据LED的VF可计算出PD;若已测出TC的温度,则按(3)式可求出TJ来。
在测TC前,先要做一个实验板(选择某种PCB、确定一定的面积)、焊上LED、输入IF电流,等稳定后,用K型热电偶点温度计测LED的散热垫温度TC。
在(4)式中,TC及TA可以测出,PD可以求出,则RBA值可以计算出来。
若计算出TJ来,代入
(1)式可求出RJA。
这种通过试验、计算出TJ方法是基于用某种PCB及一定散热面积。
如果计算出来的TJ小于要求(或等于)TJmax,则可认为选择的PCB及面积合适;若计算来的TJ大于要求的TJmax,则要更换散热性能更好的PCB,或者增加PCB的散热面积。
另外,若选择的LED的RJC值太大,在设计上也可以更换性能上更好并且RJC值更小的大功率LED,使满足计算出来的TJ≤TJmax。
这一点在计算举例中说明。
各种不同的PCB
目前应用与大功率LED作散热的PCB有三种:
普通双面敷铜板(FR4)、铝合金基敷铜板(MCPCB)、柔性薄膜PCB用胶粘在铝合金板上的PCB。
MCPCB的结构如图7所示。
各层的厚度尺寸如表3所示。
其散热效果与铜层及金属层厚如度尺寸及绝缘介质的导热性有关。
一般采用35μm铜层及1.5mm铝合金的MCPCB。
柔*PCB粘在铝合金板上的结构如图8所示。
一般采用的各层厚度尺寸如表4所示。
1~3W星状LED采用此结构。
采用高导热性介质的MCPCB有最好的散热性能,但价格较贵。
计算举例
这里采用了NICHIA公司的测量TC的实例中取部分数据作为计算举例。
已知条件如下:
LED:
3W白光LED、型号MCCW022、RJC=16℃/W。
K型热电偶点温度计测量头焊在散热垫上。
PCB试验板:
双层敷铜板(40×40mm)、t=1.6mm、焊接面铜层面积1180mm2背面铜层面积1600mm2。
LED工作状态:
IF=500mA、VF=3.97V。
用K型热电偶点温度计测TC,TC=71℃。
测试时环境温度TA=25℃.
1.TJ计算
TJ=RJC×PD+TC=RJC(IF×VF)+TC
TJ=16℃/W(500mA×3.97V)
+71℃=103℃
2.RBA计算
RJA=(TC-TA)/PD
=(71℃-25℃)/1.99W
=23.1℃/W
3.RJA计算
RJA=RJC+RBA
=16℃/W+23.1℃/W
=39.1℃/W
如果设计的TJmax=90℃,则按上述条件计算出来的TJ不能满足设计要求,需要改换散热更好的PCB或增大散热面积,并再一次试验及计算,直到满足TJ≤TJmax为止。
另外一种方法是,在采用的LED的RJC值太大时,若更换新型同类产品RJC=9℃/W(IF=500mA时VF=3.65V),其他条件不变,TJ计算为:
TJ=9℃/W(500mA×3.65V)+71℃
=87.4℃
上式计算中71℃有一些误差,应焊上新的9℃/W的LED重新测TC(测出的值比71℃略小)。
这对计算影响不大。
采用了9℃/W的LED后不用改变PCB材质及面积,其TJ符合设计的要求。
PCB背面加散热片
若计算出来的TJ比设计要求的TJmax大得多,而且在结构上又不允许增加面积时,可考虑将PCB背面粘在"∪"形的铝型材上(或铝板冲压件上),或粘在散热片上,如图10所示。
这两种方法是在多个大功率LED的灯具设计中常用的。
例如,上述计算举例中,在计算出TJ=103℃的PCB背后粘贴一个10℃/W的散热片,其TJ降到80℃左右。
这里要说明的是,上述TC是在室温条件下测得的(室温一般15~30℃)。
若LED灯使用的环境温度TA大于室温时,则实际的TJ要比在室温测量后计算的TJ要高,所以在设计时要考虑这个因素。
若测试时在恒温箱中进行,其温度调到使用时最高环境温度,为最佳。
另外,PCB是水平安装还是垂直安装,其散热条件不同,对测TC有一定影响,灯具的外壳材料、尺寸及有无散热孔对散热也有影响。
因此,在设计时要留有余地。
温度越低,LED的寿命约长,在做比较对比试验时,一定要给不同LED装相同的散热型材。
不同厂家生产的晶片主要是工艺的问题吧,一般控制晶片的温度在100度以下比较好,再高的话,LED光衰特别大,但晶片的温度不能测量,一般LED的晶片到铝基板的热阻引起的温度差在20度左右(1W),而铝基板的温度是可以测量的。
我们一般控制LED铝基板的温度在60度以下。
晶片的温度就在80度左右。
LED1W灯珠的寿命如果是在实验室情况下,及常温25摄氏度,做好良好散热的条件下,电流保持在而定的350MA以内,且电源谐波保持在极小的额度内,理论上寿命会在50000到10万小时。
灯珠工作的时候一般要保持散热板的温度不高于60摄氏度,LED的发光波长随温度变化为0.2-0.3nm/℃,光谱宽度随之增加,影响颜色鲜艳度。
另外,当正向电流流经pn结,发热性损耗使结区产生温升,在室温附近,温度每升高1℃,LED的发光强度会相应地减少1%左右,封装散热;时保持色纯度与发光强度非常重要,以往多采用减少其驱动电流的办法,降低结温,多数LED的驱动电流限制在20mA左右。
但是,LED的光输出会随电流的增大而增加,目前,很多功率型LED的驱动电流可以达到70mA、100mA甚至1A级,需要改进封装结构,全新的LED封装设计理念和低热阻封装结构及技术,改善热特性。
例如,采用大面积芯片倒装结构,选用导热性能好的银胶,增大金属支架的表面积,焊料凸点的硅载体直接装在热沉上等方法。
此外,在应用设计中,PCB线路板等的热设计、导热性能也十分重要。
进入21世纪后,LED的高效化、超高亮度化、全色化不断发展创新,红、橙LED光效已达到100Im/W,绿LED为501m/W,单只LED的光通量也达到数十Im。
LED芯片和封装不再沿龚传统的设计理念与制造生产模式,在增加芯片的光输出方面,研发不仅仅限于改变材料内杂质数量,晶格缺陷和位错来提高内部效率,同时,如何改善管芯及封装内部结构,增强LED内部产生光子出射的几率,提高光效,解决散热,取光和热沉优化设计,改进光学性能,加速表面贴装化SMD进程更是产业界研发的主流方向