孔用弹性挡圈工艺分析及模具设计材料成型及控制工程大学论文.docx
《孔用弹性挡圈工艺分析及模具设计材料成型及控制工程大学论文.docx》由会员分享,可在线阅读,更多相关《孔用弹性挡圈工艺分析及模具设计材料成型及控制工程大学论文.docx(35页珍藏版)》请在冰豆网上搜索。
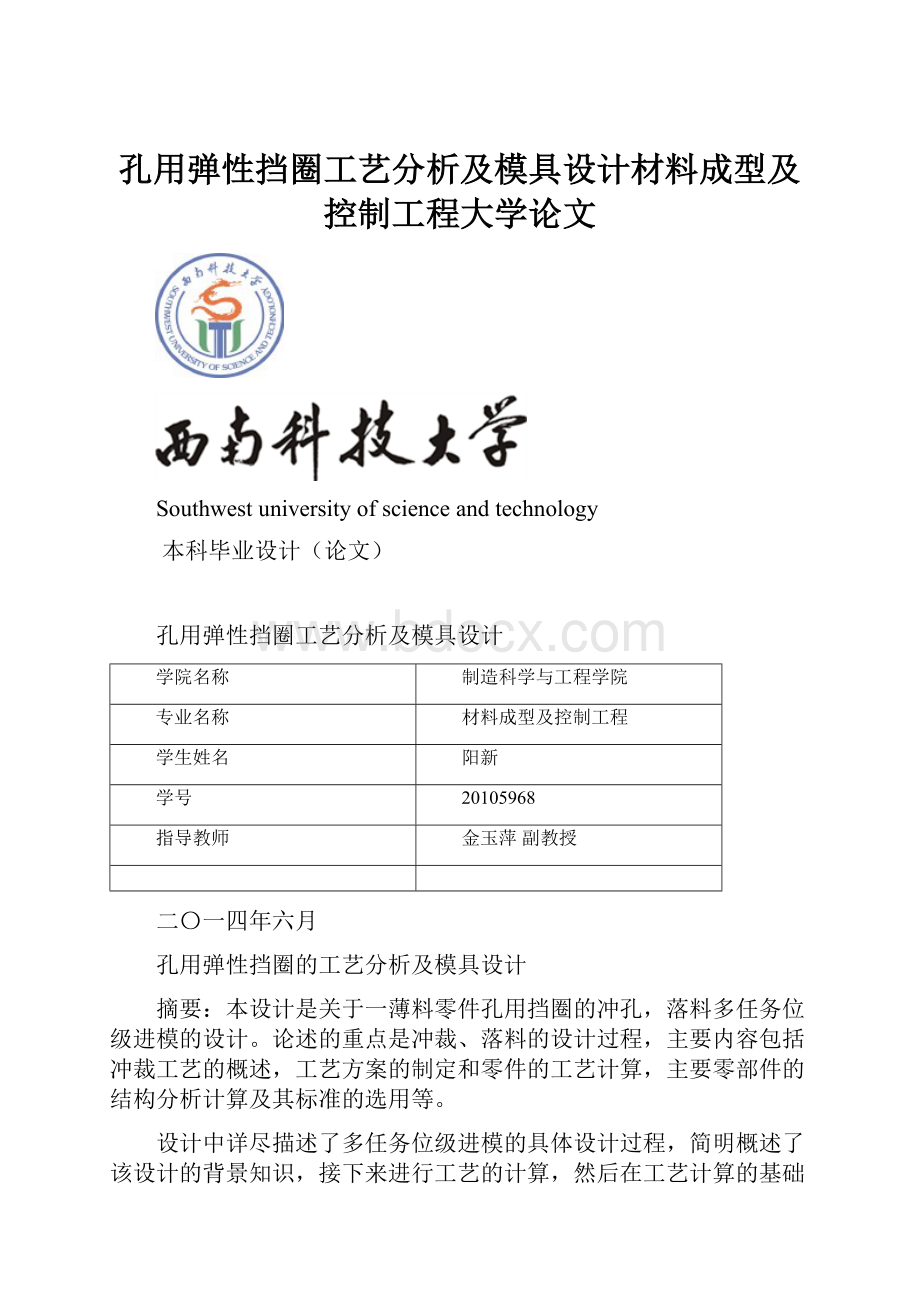
孔用弹性挡圈工艺分析及模具设计材料成型及控制工程大学论文
Southwestuniversityofscienceandtechnology
本科毕业设计(论文)
孔用弹性挡圈工艺分析及模具设计
学院名称
制造科学与工程学院
专业名称
材料成型及控制工程
学生姓名
阳新
学号
20105968
指导教师
金玉萍副教授
二〇一四年六月
孔用弹性挡圈的工艺分析及模具设计
摘要:
本设计是关于一薄料零件孔用挡圈的冲孔,落料多任务位级进模的设计。
论述的重点是冲裁、落料的设计过程,主要内容包括冲裁工艺的概述,工艺方案的制定和零件的工艺计算,主要零部件的结构分析计算及其标准的选用等。
设计中详尽描述了多任务位级进模的具体设计过程,简明概述了该设计的背景知识,接下来进行工艺的计算,然后在工艺计算的基础上对凸、凹工作部分尺寸进行计算,以便选择其它零件,最后使用在现代设计中应用最广的软件CAD对零件装配图和零件图进行了绘制。
关键词:
模具;冲裁;落料;级进模
DieDesignofMiddlePins
Abstract:
Thisdesignisaboutathinpartsandforming,cutting,bendingandblankingprogressivediedesign.Thepaperfocusesoncuttingandrollingforming,bendingandblankingprocessdesign,themaincontentsincludecuttingtechnologyoverviewoftechnologicalscheme,theformulationandprocessofcalculation,themainpartsofthecalculationandanalysisofstructuralcomponentsoftheselectioncriteria.
Thedesigndetailthemulti-positionprogressivespecificdesignprocess,thedesignofconcisesummarybackgroundknowledge,theprocessofcalculation,andthenintheprocessofcalculationbasedonconvex,concavepartsizecalculationwork,inordertochooseotherparts,finallyusedinmoderndesignisthemostwidelyusedfortheassemblypartsandAutoCADsoftwarechartdrawing.
Keywords:
die,punching,blank,ProgressiveDie
第1章绪论
1.1课题背景
1.1.1国内研究现状
模具生产技术水平的高低,已成为衡量一个国家产品制造水平高低的重要标志,因为模具在很大程度上决定着产品的质量、效益和新产品的开发能力。
中国经济的高速发展对模具工业提出了越来越高的要求,也为其发展提供了巨大的动力。
近10年来,中国模具工业一直以每年15%左右的增长速度快速发展。
但与发达国家相比,中国模具工业无论在技术上,还是在管理上,都存在较大差距。
特别在大型、精密、复杂、长寿命模具技术上,差距尤为明显。
中国每年需要大量进口此类模具,在模具产品结构上,中低档模具相对过剩,市场竞争加剧价格偏低,降低了许多模具企业的效益。
而中高档模具能力不足,模具的开发能力较弱,技术人才严重不足,科研开发和技术攻关投入少等一系列问题,严重制约了中国模具行业的发展。
由于近年市场需求的强大拉动,中国模具工业高速发展,市场广阔,产销两旺。
2003年我国模具产值达到450亿元人民币以上,约折合50多亿美元,按模具总量排名,中国紧随日本、美国其后,位居世界第三。
中国模具已涵盖了各种用于金属和非金属成形的特殊装备,被分为10大类、46小类。
1996年至2002年间,中国模具制造业的产值年平均增长14%左右,2003年增长25%左右,广东、江苏、浙江、山东等模具发达地区的增长在25%以上。
近两年,我国的模具技术有了很大的提高,生产的模具有些已接近或达到国际水平。
2003年模具出口3.368亿美元,比上年增长在33.5%,形势喜人。
总的来看,我国技术含量低的模具已供过于求,市场利润空间狭小,而技术含量较高的中、高档模具还远不能适应国民经济发展的需要,精密、复杂的冲压模具和塑料模具、轿车覆盖件模具、电子接插件等电子产品模具等高档模具仍有很大一部分依靠进口。
近五年来,我国平均每年进口模具约11.2亿美元,2003年就进口了近13.7亿美元的模具,这还未包括随设备和生产线作为附件带进来的模具。
中国现有模具企业超过2万家,从业人数50多万人。
中国的模具生产目前主要集中在华南和华东,大约占了全国模具制造业产值和销售额的三分之二,每年平均增长在20%左右。
1.1.2国外研究现状
我国模具生产厂中多数是自产自配的工模具车间(分厂),自产自配比例高达60%左右,而国外模具超过70%属商品模具。
专业模具厂大多是“大而全”、“小而全”的组织形式,而国外大多是“小而专”、“小而精”。
国内大型、精密、复杂、长寿命的模具占总量比例不足30%,而国外在50%以上。
2004年,模具进出口之比为3.7﹕1,进出口相抵后的净进口额达13.2亿美元,为世界模具净进口量最大的国家。
3、未来冲压模具制造技术发展趋势模具技术的发展应该为适应模具产品“交货期短”、“精度高”、“质量好”、“价格低”的要求服务。
达到这一要求急需发展如下几项:
(1)全面推广CAD/CAM/CAE技术
模具CAD/CAM/CAE技术是模具设计制造的发展方向。
随着微机软件的发展和进步,普及CAD/CAM/CAE技术的条件已基本成熟,各企业将加大CAD/CAM技术培训和技术服务的力度;进一步扩大CAE技术的应用范围。
计算机和网络的发展正使CAD/CAM/CAE技术跨地区、跨企业、跨院所地在整个行业中推广成为可能,实现技术资源的重新整合,使虚拟制造成为可能。
(2)高速铣削加工
国外近年来发展的高速铣削加工,大幅度提高了加工效率,并可获得极高的表面光洁度。
另外,还可加工高硬度模块,还具有温升低、热变形小等优点。
高速铣削加工技术的发展,对汽车、家电行业中大型型腔模具制造注入了新的活力。
目前它已向更高的敏捷化、智能化、集成化方向发展。
(3)模具扫描及数字化系统
高速扫描机和模具扫描系统提供了从模型或实物扫描到加工出期望的模型所需的诸多功能,大大缩短了模具的在研制制造周期。
有些快速扫描系统,可快速安装在已有的数控铣床及加工中心上,实现快速数据采集、自动生成各种不同数控系统的加工程序、不同格式的CAD数据,用于模具制造业的“逆向工程”。
模具扫描系统已在汽车、摩托车、家电等行业得到成功应用,相信在“十五”期间将发挥更大的作用。
(4)电火花铣削加工
电火花铣削加工技术也称为电火花创成加工技术,这是一种替代传统的用成型电极加工型腔的新技术,它是有高速旋转的简单的管状电极作三维或二维轮廓加工(像数控铣一样),因此不再需要制造复杂的成型电极,这显然是电火花成形加工领域的重大发展。
国外已有使用这种技术的机床在模具加工中应用。
预计这一技术将得到发展。
(5)提高模具标准化程度
我国模具标准化程度正在不断提高,估计目前我国模具标准件使用覆盖率已达到30%左右。
国外发达国家一般为80%左右。
(6)优质材料及先进表面处理技术
选用优质钢材和应用相应的表面处理技术来提高模具的寿命就显得十分必要。
模具热处理和表面处理是否能充分发挥模具钢材料性能的关键环节。
模具热处理的发展方向是采用真空热处理。
模具表面处理除完善应发展工艺先进的气相沉积(TiN、TiC等)、等离子喷涂等技术。
(7)模具研磨抛光将自动化、智能化
模具表面的质量对模具使用寿命、制件外观质量等方面均有较大的影响,研究自动化、智能化的研磨与抛光方法替代现有手工操作,以提高模具表面质量是重要的发展趋势。
(8)模具自动加工系统的发展
这是我国长远发展的目标。
模具自动加工系统应有多台机床合理组合;配有随行定位夹具或定位盘;有完整的机具、刀具数控库;有完整的数控柔性同步系统;有质量监测控制系统。
1.1.3我国模具业发展趋势
随着电子、信息等高新技术的不断发展,模具技术的发展呈现以下趋势。
(1)模具CAD/CAE/CAM正向集成化、三维化、智能化和网络化方向发展
模具CAD/CAE/CAM技术是模具设计、制造技术的发展方向,模具和工件的检测数字、模具软件功能集成化、模具设计、分析及制造的三维化、模具产业的逆向工程以及模具软件应用的网络化是主趋势。
新一代模具软件以立体的、直观的感觉来设计模具,所采用的三维数字化模型能方便地用于产品结构的分析、模具可制造性评价和数控加工、成形过程模拟(CAE)及信息的管理与共享。
值得强调的是,模具数字化不是孤立的计算机辅助功能或数控技术的集合,其关键是它们与人工智能的有机集成,不仅可以整理知识、保存知识,还可以挖掘知识、繁衍知识。
新一代的模具数字化将是一个集工程师的智能和经验、计算机的硬件和软件、数值模拟和数控技术、工艺及工程管理为一体的模具优化的开发、设计和认证的系统工程。
(2)模具制造向精密、高效、复合和多功能方向发展。
精密数控电火花加工机床(电火花成形机床、快走丝线切割和慢走丝线切割机床)不断在加工效率、精度和复合加工上取得突破,国外已经将电火花铣削用于模具加工。
加工精度误差小于1μm的超精加工技术和集电、化学、超声波、激光等技术综合在一起的复合加工将得到发展。
国外近年来发展的高速铣削技术和机床(HSM)开始在国内应用,将大幅提高加工效率。
模具抛光的自动化、智能化也是发展趋势之一,日本已研制了数控研磨机,可实现三维曲面模具的自动化研磨抛光。
此外,特种研磨方法如挤压研磨、电化学抛光、超声抛光也应是发展趋势。
其他方面,如采用氮气弹簧压边、卸料、快速换模技术、冲压单元组合技术、刃口堆焊技术及实型铸造冲模刃口镶块技术等。
(3)快速经济制模技术得到应用。
快速制模主要从以下四方面加快制模速度:
一是提高加工速度(如高速铣削);二是基于快速原型的快速制模技术;三是选择易切削模具材料(如铝合金)来加快制模速度;四是采用复合加工、多轴加工提高加工效率。
快速原型制造技术(RPM)被公认为是继数控(NC)技术之后的一次技术革命,基于快速原型的快速制模技术是现在和未来的一个热点。
此外表面成形制模技术、浇铸成型制模技术、冷挤压及超塑性成形制模技术、无模多点成形技术和KEVRON钢带冲裁落料制模术也在蓬勃发展。
(4)特种加工技术有了进一步的发展。
电火花加工向着精密化、微细化方向发展。
在简化电极准备、简化编程和操作、提高加工速度以及不断降低设备制造成本上也做了大量研究和实践。
在其他机械特种加工(如磨料流动加工、喷水加工、低应力磨削、超声波加工等)和特种加工(如电子束加工、电火花磨削、激光加工、等离子束加工等)已经进入实用阶段,在各自的特殊加工领域发挥着重要作用。
(5)模具自动加工系统的研制和发展。
随着各种新技术的迅速发展,国外已出现了模具自动加工系统。
这也应是中国的长远发展目标。
模具自动加工系统应有如下特征:
多台机床合理组合;配有随行定位夹具或定位盘;有完整的机具、刀具数控库;有完整的数控系统同步系统;有质量监测控制系统。
(6)模具材料及表面处理技术发展迅速。
在模具材料方面,一大批专用于不同成形工艺的模具材料相继问世并投入使用。
在模具表面处理方面,其主要趋势是:
由渗入单一元素向多元素共渗、复合渗(如TD法)发展;由一般扩散向CVD、PVD、PCVD、离子渗入、离子注入等方向发展;同时热处理手段由大气热处理向真空热处理发展。
另外,目前激光强化、辉光离子氮化技术及电镀(刷镀)防腐强化等技术也日益受到重视。
(7)模具工业新工艺、新理念和新模式逐步得到了认同。
由于车辆和电机等产品向轻量化发展,许多轻型材料和轻型结构用于汽车业,如以铝代钢,非全密度成形,高分子材料、复合材料、工程陶瓷、超硬材料。
新型材料的采用使得生产成形和加工工艺发生了根本变革,相应地出现了液态(半固态)挤压模具及粉末锻模、冲压模具功能复合化、超塑性成形、塑性精密成形技术、塑料模气体辅助注射技术及热流道技术、高压注射成型技术等。
另一方面,随着先进制造技术的不断发展和模具行业整体水平的提高,在模具行业出现了一些新的设计、生产、管理理念与模式。
主要有:
适应模具单件生产特点的柔性制造技术;创造最佳管理和效益的精益生产;提高快速应变能力的并行工程、虚拟制造及全球敏捷制造、网络制造等新的生产模式;模具标准件的日渐广泛应用(模具标准化及模具标准件的应用将极大地影响模具制造周期,且还能提高模具的质量和降低模具制造成本);广泛采用标准件、通用件的分工协作生产模式;适应可持续发展和环保要求的绿色设计与制造等。
1.2课题目的及意义
设计的主要目的是:
现代工业的发展和技术水平的提高,很大程度上取决于模具工业的发展水平。
本次毕业设计的目的是:
模具是用来成型物品的工装夹具,这种夹具由各种零件构成。
要求设计一套合适的模具。
学生通过此次的毕业设计,应在下述各方面得到锻炼:
1)巩固本专业的基础理论,专业知识和实践知识,正确地解决设计中遇到各方面问题,初步形成融技术、经济、环境、市场、管理为一体的大工程意识。
2)提高分析和解决问题的能力,培养和加强同学从事设计工作的工程意识、科学的态度和系统工程意识。
3)学会查阅和收集资料,学会使用手册及图表资料。
设计的主要意义是:
通过此次对“孔用弹性挡圈“的级进模具设计,让我了解设计级进模的一般程序,了解相关的理论知识并加以应用和巩固;熟练的运用有关技术资料,如《实用冲模结构图解与冲压新工艺详图》、《常用数据速查速用手册》及其他有关规范等;初步的掌握设计级进模具的能力,为将来的工作打下初步的基础。
1.3课题设计要求
独立完成模具工艺分析、结构设计及计算,并完成模具总装配图和部分零件图,完成设计计算说明书一份。
毕业设计完成后进行答辩。
第2章零件工艺分析及方案确定
2.1冲裁的工艺性分析
此工件成型所需基本工序为冲孔、落料。
所用材料为65Mn弹簧片,厚度t=1.2mm,65Mn具有良好的冲压性能,适合冲压成型。
工件结构简单,精度要求低于IT11,尺寸精度要求一般,一般冲裁即可满足。
零件图如图2-1所示:
图2-1孔用弹性挡圈零件图
孔用弹性挡圈三维图如图2-2所示:
:
图2-2孔用弹性挡圈三维图
由图2—1可知
(1)冲裁件的最小圆角半径
r=1.5mmt=1.2mm
(2)冲裁件的最小和最大尺寸
Φmin=3mmΦmax=54.2mm
(3)最长和最短距离
Lmin=52.14mmLmax=54.2mm
工件的精度和断面粗糙度:
(1)精度
由图2-1得知
内孔公差为0.25mm
孔中心距公差为±0.12
(2)断面粗糙度
由零件要求得知冲裁件表面粗糙度为
2.2确定冲裁件的工艺方案
(1)单工序模每次只能完成一个工序,要完成此零件的加工,需要两个个工序,即要二套模具。
(2)复合模在压力机一次行程中完成全部工序,冲件材料无需进给移动。
(3)级进模在压力机一次行程中完成多个工序的模具。
根据孔用弹性挡圈的结构特点,以及生产要求大批次,采用多任务位级进模加工,其冲压生产效率高。
2.3模具总体结构形式确定
确定冲压工艺方案后,应通过分析比较,选择合理的模具结构型式,使其尽量满足以下要求:
(1)能冲出符合技术要求的工件
(2)能提高生产率
(3)模具制造和维修方便
(4)模具有足够的寿命
(5)模具易于安装调整,且操作方便、安全
1、定位装置
为了使条料送料时有准确的步距,而且要保证条料左右位置的固定,因此,选用侧刃定距进行初始位置的定位,侧刃初定位,用导正销进行精定位,其导正部分孔的直径定为5mm。
2、冲孔装置
考虑到是级进模,冲圆形孔和落料,在凹模处开孔,使废料往下直接掉走。
3落料装置
直接落料,自然漏料,然后条料后面的新冲裁出的工件一个接一个从凹模推出。
4、卸料装置
卸料装置主要有以下三种:
(1)刚性卸料装置:
常用于较硬、较厚且精度要求不太高的工件冲裁。
结构简单,卸料力大。
鞋料板于涂抹之间的单边间隙取
(2)弹性卸料装置:
一般由卸料板、弹性组件(弹簧或橡皮)和卸料螺钉组成,常用于冲裁厚度小于
的板料,由于有压料作用,冲裁件平整。
广泛用于复合模。
卸料板与凸模之间的单边间隙取
(3)废料切刀卸料:
对于大、中型零件冲裁或成型件切边还常采用废料切刀的形式,将废边切断,达到卸料目的。
这里选用弹性卸料装置,由卸料板、橡胶、卸料螺钉组成。
第3章排样及工艺参数的计算
3.1排样
3.1.1合理排样并绘制排样图
由于零件厚度只有1.2mm,属于薄料冲裁,为简化模具结构,采用导正销定距。
条料的送料采用自动送料,无侧压装置的送料。
零件的排样方案采用直行双排,交叉排样,混合排样三种方案,初定为三种排样方案,如图3-1所示。
直行排样混合排样交叉排样
3-1三种排样图的简图
由材料利用率公式;η=S1/S0×100%=S1/AB分别算出了三种排样图的利用率,分别为:
交叉排样利用率是26.2%,直行排样利用率为15.6%,交叉排样利用率为16.7%。
从材料利用率,成本方面考虑交叉排样最佳选择。
共设五个工位工位一:
双侧刃切边定距,同时冲两个导正孔,工位二:
导正销导正孔后冲八个Φ3的小孔,工位三为第一次落料,工位四:
空步,工位五:
第二次落料。
3.1.2送料步距及条料宽度
(1)送料步距A:
A=D+a
式中D——平行于送料方向的冲裁件宽度。
a——冲裁件之间搭边值。
由《冷冲模具设计》可知a1=1.92mma=2.4mm
所以送料步距A=D+a=56.12mm
(2)条料宽度B:
式中
——冲裁件与条料侧边之间的搭边。
——板料剪裁时的下偏差,
=0.5
所以条料宽度B=132.45mm
零件最终排样图如图3-2所示
图3—2最终排样图3.1.3计算材料利用率
以一个步距内零件的实际面积与所需毛坯面积的百分率表示:
η=S1/S0×100%=S1/AB=26.2%
式中
——一个步距内零件的实际面积
——一个步距内所需毛坯面积
A——送料步距B——条料宽度
图3-2零件排样图
3.2工艺参数的计算
3.2.1冲裁力、卸料力等的计算
落料时冲裁力F1=KLtτb
K为修正系数,K=1.3L=288.89mmt=1.2mmτb=735Mpa
F1=2×1.3×288.89×1.2×735/1000(KN)=66.482(KN)(3-1)
冲孔时冲裁力F2=1.3×8×π×3×1.2×735/1000(KN)=86.451(KN)(3-2)
计算推料力Ft:
Ft=nKtP取n=3,查表Kt=0.055
Ft=3×0.055×(126+34)(3-3)
≈26.5(kN)
计算总冲压力P0:
F0=F1+F2+Ft=178(KN)(3-4)
3.2.2初步选择压力机
压力机的吨位应当大于或等于总的压力。
即:
式中
为所选压力机的吨位,
为总的压力,前面计算得到F总=178(KN)
由《冷冲模设计》可知,选压力机为BSTA系列高速压力机,型号为BSTA-18,其详细参数如表3-1所示:
表3-1BSTA压力机
型号
BSTA-30
标称压力/KN
300
滑块行程/mm
40~16
行程次数/(次/min)
100~600
装模高度/mm
200~300
滑块调节量/mm
40
滑块面积/(mm*mm)
φ250
垫板面积/(mm*mm)
400×250
垫板厚度/mm
30
第4章模具刃口尺寸计算
4.1模具工作部分的尺寸和公差
在前面章节分析加工方案时,已经确定,综合考虑零件加工成本,模具制造成本,零件加工工艺,零件生产效率等因素,本零件采用以级进模是最合适的。
由之前章节对所要加工的零件工艺分析可以看出,此零件主要需要冲裁、落料艺都涉及到工作部分尺寸的计算。
冲裁是利用模具使板料沿着一定的轮廓形状产生分离的一种冲压工序。
它包括落料、冲孔、切断、修边、切舌、剖切等工序,其中落料和冲孔是最常见的二种工序
落料:
若使材料沿封闭曲线相互分离,封闭曲线以内的部分作为冲裁件时,称为落料;
冲孔:
若使材料沿封闭曲线相互分离,封闭曲线以外的部分作为冲裁件时,则称为冲孔。
冲裁凸模和凹模刃口尺寸的确定方法:
凸模和凹模的刃口尺寸和公差,直接影响冲裁件的尺寸精度。
模具的合理间隙值也靠凸、凹模刃口尺寸及其公差来保证。
因此,正确确定凸、凹模刃口尺寸和公差,是冲裁模设计中的一项重要工作。
凹模刃口尺寸的计算原则
由于凸、凹模之间存在着间隙,所以冲裁件断面都带有锥度。
但在冲裁件尺寸的测量和使用中,则是以光亮带的尺寸为基准。
落料件的光亮带处于大端尺寸,其光亮带是因凹模刃口挤切材料产生的,且落料件的大端(光面)尺寸等于凹模尺寸。
冲孔件的光亮带处于小端尺寸,其光亮带是凸模刃口挤切材料产生的,且冲孔件的小端(光面)尺寸等于凸模尺寸。
冲裁过程中,凸、凹模要与冲裁零件或废料发生摩擦,凸模轮廓越磨越小,凹模轮廓越磨越大,结果使间隙越用越大。
因此,确定凸、凹模刃口尺寸应区分落料和冲孔工序,并遵循如下原则:
(1)设计落料模先确定凹模刃口尺寸。
以凹模为基准,间隙取在凸模上,即冲裁间隙通过减小凸模刃口尺寸来取得。
设计冲孔模先确定凸模刃口尺寸。
以凸模为基准,间隙取在凹模上,冲裁间隙通过增大凹模刃口尺寸来取得。
(2)根据冲模在使用过程中的磨损规律,设计落料模时,凹模基本尺寸应取接近或等于工件的最小极限尺寸;设计冲孔模时,凸模基本尺寸则取接近或等于工件孔的最大极限尺寸。
这样,凸、凹在磨损到一定程度时,仍能冲出合格的零件。
模具磨损预留量与工件制造精度有关。
用x、Δ表示,其中Δ为工件的公差值,x为磨损系数,其值在0.5~1之间,根据工件制造精度进行选取:
(3)不管落料还是冲孔,冲裁间隙一般选用最小合理间隙值(Z)。
(4)选择模具刃口制造公差时,要考虑工件精度与模具精度的关系,即要保证工件的精度要求,又要保证有合理的间隙值。
一般冲模精度较工件精度高2~4级。
对于形状简单的圆形、方形刃口,其制造偏差值可按IT6~IT7级来选取;对于形状复杂的刃口制造偏差可按工件相应部位公差值的1/4来选取;对于刃口尺寸磨损后无变化的制造偏差值可取工件相应部位公差值的1/8并冠以(±)
(5)工件尺寸公差与冲模刃口尺寸的制造偏差原则上都应按“入体”原则标注为单向公差,所谓“入体”原则是指标注工件尺寸公差时应向材料实体方向单向标注。
但对于磨损后无变化的尺寸,一般标注双向偏差。
凸凹模刃口尺寸的计算方法:
考虑到这个零件的形状复杂并且是薄件,所