轴的设计与校核.docx
《轴的设计与校核.docx》由会员分享,可在线阅读,更多相关《轴的设计与校核.docx(13页珍藏版)》请在冰豆网上搜索。
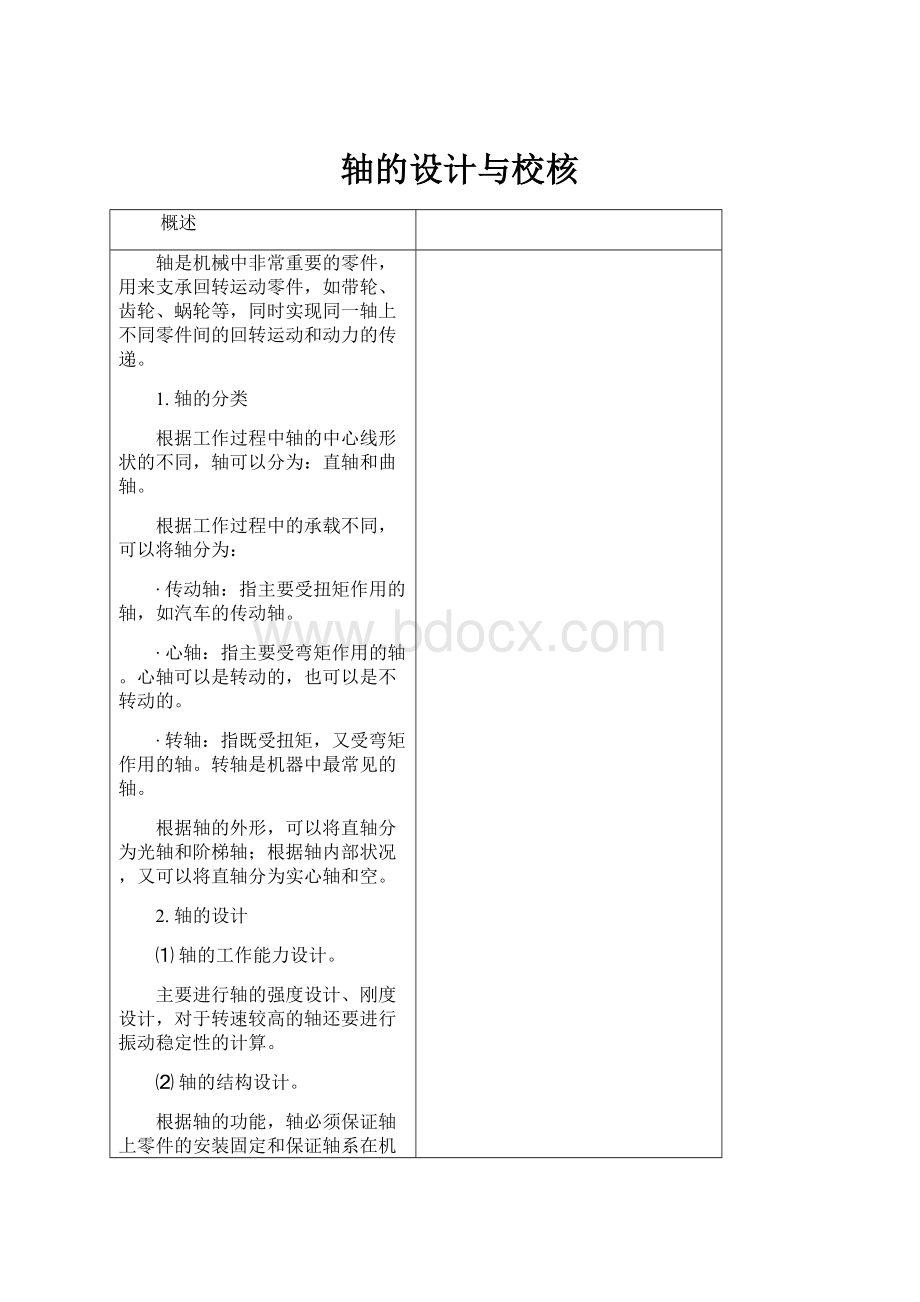
轴的设计与校核
概述
轴是机械中非常重要的零件,用来支承回转运动零件,如带轮、齿轮、蜗轮等,同时实现同一轴上不同零件间的回转运动和动力的传递。
1.轴的分类
根据工作过程中轴的中心线形状的不同,轴可以分为:
直轴和曲轴。
根据工作过程中的承载不同,可以将轴分为:
∙传动轴:
指主要受扭矩作用的轴,如汽车的传动轴。
∙心轴:
指主要受弯矩作用的轴。
心轴可以是转动的,也可以是不转动的。
∙转轴:
指既受扭矩,又受弯矩作用的轴。
转轴是机器中最常见的轴。
根据轴的外形,可以将直轴分为光轴和阶梯轴;根据轴内部状况,又可以将直轴分为实心轴和空。
2.轴的设计
⑴轴的工作能力设计。
主要进行轴的强度设计、刚度设计,对于转速较高的轴还要进行振动稳定性的计算。
⑵轴的结构设计。
根据轴的功能,轴必须保证轴上零件的安装固定和保证轴系在机器中的支撑要求,同时应具有良好的工艺性。
一般的设计步骤为:
选择材料,初估轴径,结构设计,强度校核,必要时要进行刚度校核和稳定性计算。
校核结果如不满足承载要求时,则必须修改原结构设计结果,再重新校核。
3.轴的材料
轴是主要的支承件,常采用机械性能较好的材料。
常用材料包括:
∙碳素钢:
该类材料对应力集中的敏感性较小,价格较低,是轴类零件最常用的材料。
常用牌号有:
30、35、40、45、50。
采用优质碳钢时,一般应进行热处理以改善其性能。
受力较小或不重要的轴,也可以选用Q235、Q255等普通碳钢。
∙合金钢:
对于要求重载、高温、结构尺寸小、重量轻等使用场合的轴,可以选用合金纲。
合金钢具有更好的机械性能和热处理性能,但对应力集中较敏感,价格也较高。
设计中尤其要注意从结构上减小应力集中,并提高其表面质量。
∙铸铁:
对于形状比较复杂的轴,可以选用球墨铸铁和高强度的铸铁。
它们具有较好的加工性和吸振性,经济性好且对应力集中不敏感,但铸造质量不易保证。
轴的结构设计
根据轴在工作中的作用,轴的结构取决于:
轴在机器中的安装位置和形式,轴上零件的类型和尺寸,载荷的性质、大小、方向和分布状况,轴的加工工艺等多个因素。
合理的结构设计应满足:
轴上零件布置合理,从而轴受力合理有利于提高强度和刚度;轴和轴上零件必须有准确的工作位置;轴上零件装拆调整方便;轴具有良好的加工工艺性;节省材料等。
1.轴的组成
轴的毛坯一般采用圆钢、锻造或焊接获得,由于铸造品质不易保证,较少选用铸造毛坯。
轴主要由三部分组成。
轴上被支承,安装轴承的部分称为轴颈;支承轴上零件,安装轮毂的部分称为轴头;联结轴头和轴颈的部分称为轴身。
轴颈上安装滚动轴承时,直径尺寸必须按滚动轴承的国标尺寸选择,尺寸公差和表面粗糙度须按规定选择;轴头的尺寸要参考轮毂的尺寸进行选择,轴身尺寸确定时应尽量使轴颈与轴头的过渡合理,避免截面尺寸变化过大,同时具有较好的工艺性。
2.结构设计步骤
设计中常采用以下的设计步骤:
1分析所设计轴的工作状况,拟定轴上零件的装配方案和轴在机器中的安装情况。
2根据已知的轴上近似载荷,初估轴的直径或根据经验确定轴的某径向尺寸。
3根据轴上零件受力情况、安装、固定及装配时对轴的表面要求等确定轴的径向(直径)尺寸。
4根据轴上零件的位置、配合长度、支承结构和形式确定轴的轴向尺寸。
考虑加工和装配的工艺性,使轴的结构更合理。
3.零件在轴上的安装
保证轴上零件可靠工作,需要零件在工作过程中有准确的位置,即零件在轴上必须有准确的定位和固定。
零件在轴上的准确位置包括轴向和周向两个方面。
⑴零件在轴上的轴向定位和固定
常见的轴向定位和固定的方法采用轴肩、各种挡圈、套筒、圆螺母、锥端轴头等的多种组合结构。
∙轴肩分为定位轴肩和非定位轴肩两种。
利用轴肩定位结构简单、可靠,但轴的直径加大,轴肩处出现应力集中;轴肩过多也不利于加工。
因此,定位轴肩多在不致过多地增加轴的阶梯数和轴向力较大的情况下使用,定位轴肩的高度一般取3~6mm,滚动轴承定位轴肩的高度需按照滚动轴承的安装尺寸确定。
非定位轴肩多是为了装配合理方便和径向尺寸过度时采用,轴肩高度无严格限制,一般取为1~2mm。
∙套筒定位可以避免轴肩定位引起的轴径增大和应力集中,但受到套筒长度和与轴的配合因素的影响,不宜用在使套筒过长和高速旋转的场合。
∙挡圈的种类较多,且多为标准件,设计中需按照各种挡圈的用途和国标来选用。
⑵零件在轴上的周向定位和固定
常见的周向定位和固定的方法采用键、花键、过盈配合、成形联结、销等多种结构。
键是采用最多的方法。
同一轴上的键槽设计中应布置在一条直线上,如轴径尺寸相差不过大时,同一轴上的键最好选用相同的键宽。
4.轴的结构工艺性
⑴从装配来考虑:
应合理的设计非定位轴肩,使轴上不同零件在安装过程中尽量减少不必要的配合面;为了装配方便,轴端应设计45°的倒角;在装键的轴段,应使键槽靠近轴与轮毂先接触的直径变化处,便于在安装时零件上的键槽与轴上的键容易对准;采用过盈配合时,为了便于装配,直径变化可用锥面过渡等。
⑵从加工来考虑:
当轴的某段须磨削加工或有螺纹时,须设计砂轮越程槽或退刀槽;根据表面安装零件的配合需要,合理确定表面粗糙度和加工方法;为改善轴的抗疲劳强度,减小轴径变化处的应力集中,应适当增大其过渡圆角半径,但同时要保证零件的可靠定位,过渡圆角半径又必须小于与之相配的零件的圆角半径或倒角尺寸。
.
轴的强度计算
进行轴的强度校核计算时,应根据轴的具体受载及应力情况,采取相应的计算方法。
∙对于只传递扭矩的轴(传动轴),按扭转强度条件计算;
∙对于只承受转矩的轴(心轴),按弯曲强度条件计算;对于既受到转矩的作用,又受到弯矩作用的轴(转轴),应按弯扭合成强度条件计算;
∙重要的轴还需按疲劳强度条件进行精确校核。
对于瞬时过载很大或应力循环不对称性较为严重的轴,还应校核静强度。
1.扭转强度计算
根据轴的转矩的大小,通过计算切应力来建立轴的强度条件。
这种方法计算简便,但计算精度较低,主要用于初步估算轴径以便进行结构设计和以传递转矩为主的传动轴。
强度条件为:
∙T——轴所传递的扭矩,
∙Wr——轴抗扭截面模量,对实心轴
轴的直径:
mm
∙P——轴所传递的功率(kw)
∙n——轴的转速(r/min);
∙[τ]——许用扭转切应力(Mpa)。
∙C——与材料有关的系数。
当轴所受弯矩较大时,C值宜取较大值,反之相反。
最小直径处有键槽时,单键轴径需增加3%,双键轴径需增加7%。
2.弯扭合成强度计算
根据轴在工作中的受力状况,常见的轴既要受到扭矩的作用又要受到弯矩的作用。
根据强度理论,对轴所受到的弯矩和扭矩进行合成,用合成后的当量弯矩产生的应力作为轴所受到的应力,对影响轴疲劳强度的其它因素,采用降低需用应力的方法来考虑,建立轴的强度分析条件,即为按弯扭合成计算轴的强度。
具体计算步骤为:
1根据结构设计结果,确定外载荷作用点、大小、方向和支点位置,绘制轴的受力计算简图;
2确定坐标系,将外载荷分解为水平面和垂直面内分力,求出水平、垂直两平面支反力;
3绘制水平面、垂直平面的弯矩MX、MY图;
4计算合成弯矩,绘制合成弯矩图
;
5绘制转矩图;
6按照强度理论
求出当量弯矩Me,绘制当量弯矩图;式中α是根据转矩性质而定的应力校正系数。
对于不变的转矩,取
;对于脉动的转矩,取
;对于对称循环的转矩,取α=1。
[σ+1b]、[σ0b]、[σ-1b]分别为材料在静应力、脉动应力和对称循环应力状态下的许用弯曲应力。
实际设计中,常按脉动转矩计算。
7确定危险截面,校核危险截面轴径。
或
∙W——轴的抗弯截面模量;
∙[σ-1b]——许用弯曲应力
3.疲劳强度精确(安全系数强度)校核计算
对于使用场合重要,要求计算精度较高的重要轴,按弯扭合成强度计算时,未考虑轴的细部结构,需进行更准确的计算,通常采用安全系数法。
具体计算步骤为:
8同弯扭合成步骤1;
9绘制弯矩图和扭矩图;
10确定危险截面,求出截面上的弯曲应力σ和切应力τ及应力变化情况;
11计算疲劳强度的安全系数S:
弯矩作用下的安全系数为Sσ:
转矩作用下的安全系数为Sτ:
∙kN——寿命系数;
∙σ-1、τ-1——对称循环应力时材料的弯曲疲劳限和扭转疲劳限;
∙kσ、kτ——弯曲和扭转式的应力集中系数;
∙β——为表面质量系数;
∙εσ、ετ——尺寸系数;
∙σm、τm——平均应力;Ψσ、Ψτ——平均应力折合为应力幅的等效系数,
、
∙σ0、τ0——脉动循环应力时材料的弯曲疲劳极限和扭转疲劳极限。
5.校核疲劳强度:
S≥[S],[S]——许用安全系数。
4.静强度计算
对于工作过程中瞬时过载很大或应力循环不对称性较为严重的轴,轴上的尖峰载荷及时作用实践很短和出现次数很少,不足以引起疲劳破坏,但却能使轴产生塑性变形。
设计时应校核静强度。
(1)按弯扭合成校核:
强度条件为:
式中:
σ0=M/W,τ0=T/Wt;对于实心圆轴,σ0=10M/d3,τ0=5T/d3,代入上式可得
或
式中:
Me0——静强度当量弯矩;[σ0]——静强度许用应力
计算时M和T应取最大载荷的数值。
许用应力取[σ]=σs/S。
σs为材料的屈服极限,S为安全系数,其值根据实践经验确定。
当载荷或应力不能精确计算,材料性能无把握时,上述S值应增大20%~50%。
轴的刚度计算
轴属于细长杆件类零件,对于重要的或有刚度要求的轴,要进行刚度计算。
轴的刚度有弯曲刚度和扭转刚度两种。
弯曲刚度用轴的挠度y或偏转角θ来表征,扭转刚度用轴的扭转角φ来表征。
轴的刚度计算,就是计算轴在工作载荷下的变形量,并要求其在允许的范围内,即:
y<[y],θ<[θ];φ<[φ]。
1.弯曲刚度计算
进行轴的弯曲刚度计算时,通常按材料力学的方法计算挠度和偏转角,常用的有当量轴径法和能量法。
(1)当量轴径法
适用于轴的各段直径相差较小且只需作近似计算的场合。
它是通过将阶梯轴转化为等效光轴后求等效轴的弯曲变形。
等效光轴的直径为:
式中:
di——阶梯轴的第i段直径(i=1~n,n为段数);li为阶梯轴的第I段长度。
若作用于光轴的载荷F位于支承跨矩L的中间位置时,则轴在该处的挠度y和支承处的偏转角θ分别为:
,
式中:
E——材料的弹性模量(N/mm2);I——光轴剖面的惯性矩,
(mm4)
(2)能量法
适用于阶梯轴的弯曲刚度的较精确计算。
它是通过对轴受外力作用后所引起的变形能的分析,应用材料力学的方法分析轴的变形。
2.扭转刚度计算
轴受转矩作用时,对于钢制实心阶梯轴,其扭转角的计算式为:
(rad)
式中:
G——材料的剪切弹性模量,钢的G=81000N/mm;Ti、li、di分别为第i段轴所受的转矩()、长度(mm)和直径(mm)。
3.提高轴的疲劳强度和刚度的措施
设计过程中,除合理选材外还可从结构安排和工艺等方面采取措施来提高轴的承载能力。
(1)分析轴上零件特点,减小轴受载荷
根据轴上安装的传动零件的状况,合理布置和合理设计可以减小轴的受载。
对于受弯矩和转矩联合作用的转轴,可以改进轴和轴上零件结构,使轴的承载减少。
(2)改进轴的结构,减少应力集中
避免轴的剖面尺寸发生较大的变化,采用较大的过渡圆角半径,当装配零件的倒角很小时,可以采用内凹圆角或加装隔离环;尽可能不在轴的受载区段切制螺纹;可能时适当放松零件与轴的配合,在轮毂上或与轮毂配合区段两端的轴上加开卸载槽,以降低过盈配合处的应力集中等。
(3)改进轴的表面质量,提高轴的疲劳强度
减小表面及圆角处的表面粗糙度;对零件进行表面淬火、渗氮、渗碳、碳氮共渗等处理;对零件表面进行碾压加工或喷丸硬化处理等可以显着提高轴的承载能力。
(4)采用空心轴,减轻质量,提高强度和刚度
(内径d0/外径d)为的空心轴与直径为d的实心轴相比,空心轴的剖面模量减少13%,质量减少36%;d0/d仍为的空心轴与同质量的实心轴相比,剖面模量可增加倍。
轴的振动计算
受变载荷作用的轴,如果载荷的变化频率与轴的自振频率相同或接近时,轴会发生共振。
共振使轴的运动状态发生很大变化,严重时会使轴或轴上零件甚至整个机器遭受破坏,发生共振现象时的转速,称为轴的临界转速。
轴的回转频率与轴的自振频率相同或接近时,轴也会发生共振。
对于高转速的轴和受周期性外载荷的轴,必须进行振动计算。
轴的振动计算,主要是计算其临界转速,以采取必要的措施,使轴的自振频率与周期载荷的作用频率不同,以免发生共振现象。
轴的振动有横向振动(弯曲振动)、纵向振动和扭转振动等。
纵向振动的自振频率很高,超出一般轴的工作转速范围,分析时可不予考虑。
横向振动的临界转速可以有多个,最低的一个称为第一阶临界转速,其余为二阶、三阶……。
在一阶临界转速下,振动激烈,最为危险,所以通常主要计算一阶临界转速。
在某些特殊情况下还需计算高阶临界转速。
分析一根装有单圆盘的双铰支轴如图。
设圆盘的质量m很大,相对而言,轴的质量可以忽略不计,并假定圆盘材料不均匀或制造有误差,其重心与轴线间的偏心矩为e。
当轴以角速度ω转动时,由于离心力而产生挠度y。
单圆盘的双铰支轴
旋转时的离心力为:
弯曲变形后的弹性反力为:
k为轴的弯曲刚度
根据平衡条件:
可以求得轴的挠度为:
当轴的角速度ω由零逐渐增大时,y值随角速度ω的增大而增大。
在没有阻尼的情况下,当趋近于1时,挠度y趋近于无穷大,意味着轴会产生极大的变形而导致破坏。
此时所对应的角速度ω称为临界角速度,用ωc表示:
上式右边恰为轴的自振角频率,即轴的临界角速度等于其自振角频率。
由上式可见,临界角速度ωc只与轴的刚度k和圆盘的质量m有关,而与偏心矩e无关。
由于轴的刚度
,式中g为重力加速度,y0为轴圆盘处的静挠度,所以临界角速度ωc可写成:
取g=9810mm/s2,y0的单位为mm,由上式可求得装有单圆盘的双铰支轴在不计自重时的一阶临界转速nc1为:
rpm
由于轴的临界转速nc1与
成反比,故对工作转速较低的轴,可减小其y0,采用直径大而跨矩短的轴,使轴的临界转速高于工作转速(此类轴称为刚性轴);对工作转速很高的轴,可增加其y0,采用直径相对小而跨矩长的轴,使轴的临界转速低于工作转速(此类轴称为柔性轴)。
一般情况下,对于刚性轴,应使工作转速n<;对于柔性轴,应使工作转速振动计算如不符合要求,则需要改进设计。
可以采用改变工作转速,改变轴径尺寸,改变支承跨矩,改变轴上零件的质量和增设减震装置等措施。