落料拉深冲孔翻边复合模设计.docx
《落料拉深冲孔翻边复合模设计.docx》由会员分享,可在线阅读,更多相关《落料拉深冲孔翻边复合模设计.docx(54页珍藏版)》请在冰豆网上搜索。
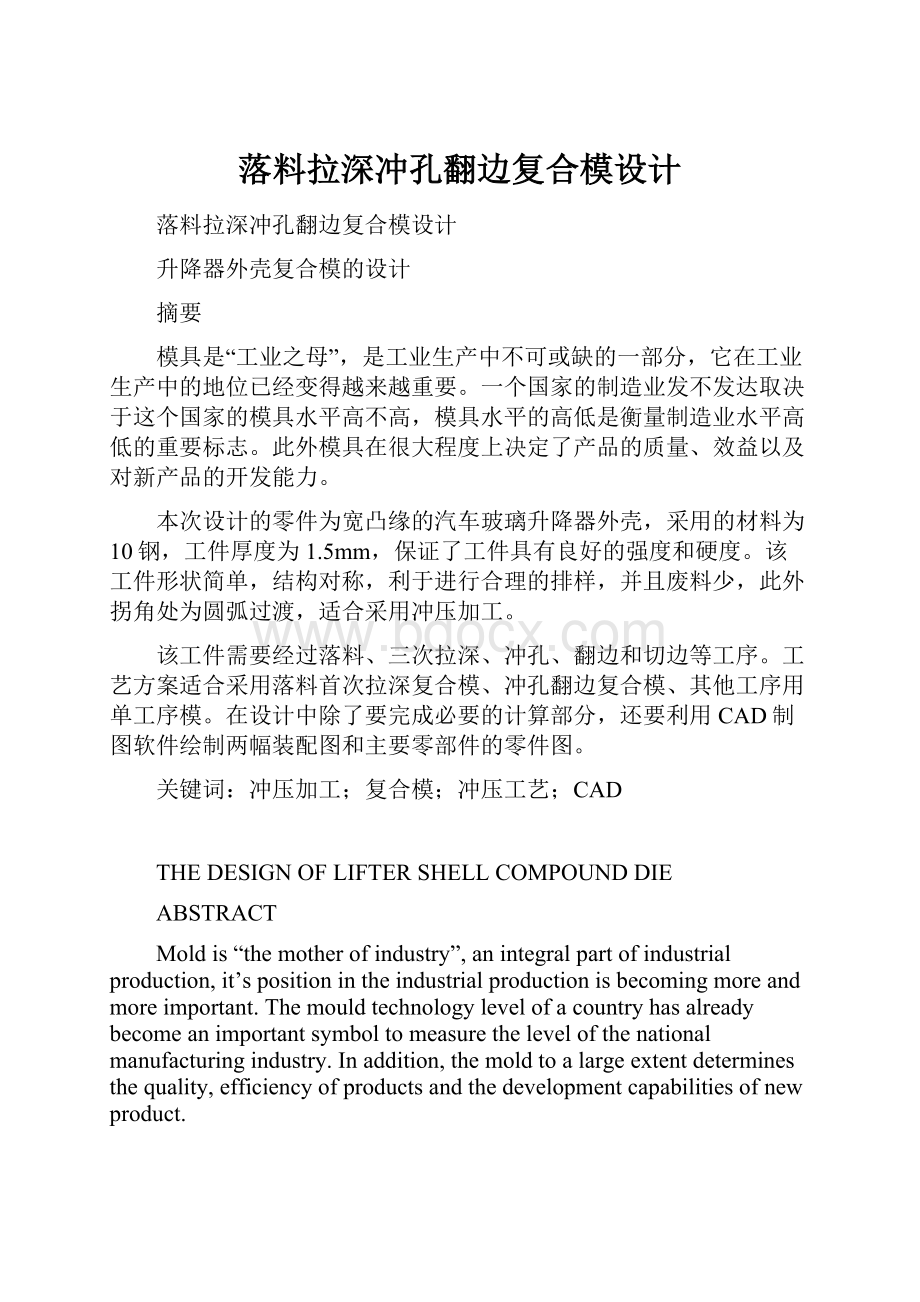
落料拉深冲孔翻边复合模设计
落料拉深冲孔翻边复合模设计
升降器外壳复合模的设计
摘要
模具是“工业之母”,是工业生产中不可或缺的一部分,它在工业生产中的地位已经变得越来越重要。
一个国家的制造业发不发达取决于这个国家的模具水平高不高,模具水平的高低是衡量制造业水平高低的重要标志。
此外模具在很大程度上决定了产品的质量、效益以及对新产品的开发能力。
本次设计的零件为宽凸缘的汽车玻璃升降器外壳,采用的材料为10钢,工件厚度为1.5mm,保证了工件具有良好的强度和硬度。
该工件形状简单,结构对称,利于进行合理的排样,并且废料少,此外拐角处为圆弧过渡,适合采用冲压加工。
该工件需要经过落料、三次拉深、冲孔、翻边和切边等工序。
工艺方案适合采用落料首次拉深复合模、冲孔翻边复合模、其他工序用单工序模。
在设计中除了要完成必要的计算部分,还要利用CAD制图软件绘制两幅装配图和主要零部件的零件图。
关键词:
冲压加工;复合模;冲压工艺;CAD
THEDESIGNOFLIFTERSHELLCOMPOUNDDIE
ABSTRACT
Moldis“themotherofindustry”,anintegralpartofindustrialproduction,it’spositionintheindustrialproductionisbecomingmoreandmoreimportant.Themouldtechnologylevelofacountryhasalreadybecomeanimportantsymboltomeasurethelevelofthenationalmanufacturingindustry.Inaddition,themoldtoalargeextentdeterminesthequality,efficiencyofproductsandthedevelopmentcapabilitiesofnewproduct.
Thedesignofthepartisawideflangeautomobileglassliftershell,thematerialis10steel,thethicknessoftheworkpieceis1.5mm,it’sguaranteetheworkpiecehasgoodstrengthandhardness.Theworkpiecehasasimpleshapeandsymmetricalstructure,isadvantageoustolayoutreasonable,andhaslesswaste,inaddition,thecorneristhearctransition,it’ssuitableforstampingprocess.
Theworkpieceneedstothroughblanking,drawingthreetimes,punching,flangingandcuttingprocesses.Theprocessschemeissuitableforblankingandthefirsttimedrawingcompounddie,punchingandflangingcompounddie,otherprocessesusingsingleprocessmode.Duringthedesign,it’snotonlyneedtocompletethenecessarycalculationpart,butalsoneedtousetheCADdrawingsoftwaredrawtwopiecesoftheassemblydrawingandthemainpartsdrawing.
Keywords:
punching;compounddie;stampingprocess;CAD
1绪论
1.1课题研究背景及目的
进入21世纪以来,我国的经济发展的非常之快,我国的制造业在经济快速发展的带动下也有了很大程度的发展。
而模具是作为衡量一个国家制造业水平高低的一个标志,同时又是工业发展不可或缺的部分,因此我国的模具行业也随之得到了很好的发展和进步。
而作为模具当中很常见的一种:
复合模,它不仅工作效率高、精度高而且使用寿命长,因为复合模的这么多优点使得它在工业生产中被广泛的应用。
此外,复合模还涉及到模具当中的很多关键技术,如:
冲压的基本理论、冲压工艺性分析及工艺方案确定、模具的设计原则以及如何选用模具材料。
本设计中需要涉及到落料、拉深、冲孔和翻边四道非常常见的冲压工序,结合工件的形状尺寸去推导模具的结构。
这将要用到我们之前所学的相关模具理论知识,并结合在实习当中取得的收获,才能合理地解决复合模设计中可能出现的各种问题。
当然除此之外还必须要查找与本复合模设计相关的文献和图册,从中进一步地熟悉和了解模具的结构,做到科学合理地熟练应用。
本次的设计是我在大学里最后的一门课,也是走向工作岗位前的一次热身。
通过对本复合模的结构设计,让我对冲压工艺性分析、冲压工艺方案确定、冲模结构设计有了更深刻的认识,也提高了我冲压工艺计算、绘制模具装配图、编写说明书及工艺卡和查阅文献资料的能力。
1.2国内外研究现状与发展趋势
1.2.1国内外模具行业的发展现状
一个制造企业最重要的部分就是模具,可以说模具就是制造业的心脏。
全球绝大部分的产品和零件都必须依靠模具才能生产出来,由此可见模具的重要性及应用范围的广泛程度。
一个国家模具工业的发达程度决定了他们的电子、电器、塑料、汽车、仪表、航空、轻工、日常用品等制造部门所生产出来的产品的质量,可以说模具的质量决定了产品的质量。
模具在工业上占据着及其重要的地位,比如在工业发达的国家,他们把模具作为机械制造方面的高科技产品来对待。
他们认为:
“模具可以带动社会的发展,促进社会更快的走向富裕”。
因此,了解和熟悉模具的发展的重要性是不言而喻的。
我国的模具产业在改革开放之后得到了很大的发展,尤其是在上个世纪90年代后进步幅度非常大,并且呈现出一些特点:
我国的模具发展方向将逐渐转向大型化、精密化和复杂化;模具的生产也开始出现区域集中化,在长三角和珠三角地带出现一大批优秀的模具企业;模具的生产效率显著提高,并且专业化程度有了很大提升,模具的制造水平较以往也有了很大提高[1]。
在经过最近这几十年的发展之后,我国的模具工业有了显著的进步,无论是在质量、数量还是在技术方面。
随着国外的CAD/CAE/CAM技术变得越来越成熟,我国也正广泛的将这些计算机辅助技术应用到模具设计制造中来,这也有效的提高了我国模具制造的效率和精度。
虽然我国的模具行业直观上看起来发展的速度很快,但是实质上模具的水平与世界先进水平相比还是相差甚远,尤为显著的是那些大型、复杂、精密、高寿命的高档模具。
举个例子来说:
我国的汽车模具行业,到目前为止已经经过了多年的发展,也取得了很大的进步和成效,在全国范围内已经有几十家车身模具企业具有了一定的规模,但是在那些高档的模具上,还是缺少创造性,每年还是需要从德国、日本等发达国家大量进口,这就是因为我国的模具还不能达到世界一流水平,与别的国家还有很大差距。
除了这个外,我国的模具行业在发展过程中还存在很多其他的问题,如:
模具制造的综合技术不高,模具设计能力不强,并且缺乏创新性;模具企业的规模较小;模具工业产品结构不合理,我国生产的模具中主要以简单模和单工序模为主,大型、精密、复杂、长寿命类型的模具还在研发阶段,主要依靠进口等。
相比之下,国外的模具工业就要比我国发达很多。
尤其像欧美,日本这些工业发达国家,他们的模具行业起步得比我国早,拥有着良好的创新能力和先进的技术。
他们在模具设计制造中应用了很多的先进技术,例如:
他们制造的模具精度很高,这就是因为他们很好的推广了CAD/CAM/CAE信息技术的使用;高速切削技术使得他们的生产效率大大提高[2],在行业中更具竞争力;有着先进的工艺管理,模具的标准化程度高[3]。
比如他们国家的汽车模具生产就已经进入了专业化、标准化、现代化的阶段。
1.2.2汽车覆盖件冲压工艺现状
我国以往的工艺性分析主要是靠个人的经验,通过粗略分析零件的几何形状和特点、材料特性等,从而做出定性分析结论,这样必然会产生很大的误差。
但是随着计算机技术的发展,慢慢出现了新的方法,如:
几何模拟法、力学模拟法、专家系统法等。
在计算机的帮助下,利用这些方法可以在一定程度、一定范围内做出一些定量的分析结论[4],但是对于汽车覆盖件冲压工艺性分析中的一些根本性问题还是无法解决。
随着零件模型的发展,出现了一种新的方法,叫可成形性分析方法[5]。
但是这种方法具有很大的局限性,它只能解决各特征的局部可成形性分析,不能对覆盖件各特征的协调工艺性和整体工艺性进行分析。
近年来,随着人工智能技术的发展,出现了基于知识工程的覆盖件产品可成形性分析法[6-8]。
这是建立在零件知识模型基础上的工艺性推理过程。
工艺方案设计往往要涉及到很多的内容,而且要考虑很多的因素,最主要的是很多工作难以用一个工艺决策来表达,不能进行定量的计算,因此目前汽车覆盖件冲压工艺方案的确定仍以经验设计为主。
但是随着计算机技术、人工智能技术和逐步发展和应用,人们开展了一些借助计算机技术来确定工艺方案设计的研究。
目前计算机辅助覆盖件工艺方案设计是以交互式为主流,以智能化为研究热点。
采用混合决策方式和基于知识的设计方法将是当前研究的趋势[9]。
1.2.3我国模具行业的发展趋势
虽然目前我国在模具的水平上还达不到世界一流水平,与日本、欧美等工业发达国家相比还远远落后,但这同时也表明了我国模具工业将有很大的发展空间。
我们将汲取外国的丰富经验,借鉴他们的方法来促进我国模具行业的发展。
我国的模具企业经过调整后,模具在规模上将会向着大型化,在效率上将向着快速化,在结构上将向着标准化,精密化等方向发展,至此我国的模具制造水平也将有更大程度的提高,与工业发达国家的模具制造水平之间的差距将逐渐缩小[10,11]。
在今后,我国的模具行业的发展趋势将体现在:
(1)将会有更多的模具企业兴起,不仅模具企业的数量将越来越多,其规模也会越来越大;
(2)减少进口模的数量,致力于自主研发制造大型、复杂、精密、长寿命模具,用来满足国内市场的需要;
(3)考虑到生产效率问题,因此快速成型技术将得到大力开发,高速、高精度加工技术将得到广泛应用;
(4)计算机技术将会得到广泛的应用,智能化、信息化、数字化技术会有更好的
发展和推广,除了CAD/CAM/CAE外,电子商务、WEB、ERP、CAPP、PDM、PLM等技术也将大力推广,以提高模具制造过程的自动化程度;
(5)模具的制造精度将越来越高,标准化程度也会有很大程度的提高,这将很好的提高模具质量,缩短模具制造周期;
(6)将会出现更多的模具新工艺和新技术,这将集中体现在模具制造的节能、节
材技术,模具热处理、表面处理和表面光整加工新技术等方面[12]。
1.2.4汽车覆盖件冲压工艺的发展趋势
华中科技大学模具技术国家重点实验室的四位专家郑金桥、黄勇、王义林和李志刚对汽车覆盖件工艺设计过程中关键技术的现状进行了分析讨论之后,全面的分析了该项设计今后的发展趋势。
随着计算机技术和人工智能技术的飞速发展,汽车覆盖件冲压工艺技术也要与这些先进技术紧密结合在一起,由此可以预见该项设计在今后的发展将主要体现在以下方面。
首先,综合多种方法的混合智能科技是今后处理问题的主要发展方向,该项科技会是今后非常主流的发展方法。
其次,对冲压工艺设计的关键部分如:
拉延冲压方向、工艺补充面、压料面、拉延筋的设计进行各个突破和集成设计。
再次,工艺设计与工艺管理的一体化设计。
最后就是基于CAE的覆盖件工艺自适应设计[13,14]。
总的来说,冲压工艺设计是一项覆盖范围非常广,涉及内容相当多的繁琐事项。
通过分析当前的生产活动的具体规定,将虚拟单位和网络化等当成是前提,使用多项智能科技,搭配管控科技等,对该项冲压内容进行深入的论述,建立智能型的优化CAPP系统及与CAD/CAE/CAM的集成化将是汽车车身制造信息化的重要内容和发展方向。
1.3课题研究方法
(1)了解工件的形状和结构,熟悉冲裁该工件所需的工序;
(2)熟悉冲压成型的理论,冲裁模的工艺性、结构以及设计原则,确定工艺方案;
(3)整理工件的外形尺寸,计算各工序的冲裁力,采用合理的排样方法,计算材料利用率,确定各工序中凸模、凹模以及凸凹模的刃口尺寸及工作部分的尺寸,完成所有的计算部分,选择好模架及压力机;
(4)认真学习CAD三维制图软件,提高在制图中的效率及准确性;
(5)结合冲裁模设计相关的手册及图册,确定最终的工艺方案,并完成装配图和零件图的绘制。
1.4论文的构成
本课题主要是对升降器外壳进行模具设计,由计算分析可知,需要经过落料、三次拉深、冲孔、翻边和切边工序。
而根据本次设计采取的工艺方案可知,主要是设计一套落料首次拉深复合模和一套冲孔翻边复合模。
论文中将包含有工件工艺性分析,毛坯尺寸计算,拉深次数计算,材料利用率及排样设计,冲压力计算,压力机选择,模具刃口尺寸及工作尺寸的计算,模架、模柄、螺钉和销钉的选用、弹性元件的选用。
除此之外还包括一张冲压工艺卡、两个主要零件的机加工工艺卡。
最后对全文做一个总结,附上参考文献、致谢词和附录。
2工艺性分析
2.1工件的工艺分析
(1)材料。
该工件为汽车玻璃升降器外壳,所用材料为10钢,厚度为1.5mm。
10钢是一种碳素结构钢,表2-1中列出了其各参数,由表中的参数可知,10钢具有良好的强度和硬度,适合采用冲压加工[15]。
表2-110钢的力学性能
材料名称
牌号
抗剪强度
b/MPa
抗拉强度
b/MPa
伸长率
(%)
屈服点
s/MPa
弹性模量
E/MPa
碳素结构钢
10
260~340
300~440
29
210
198000
(2)精度。
该工件的主要配合尺寸是Ф22.3和Ф16.5以及拉深高度16。
加工过程中得确保这两个直径尺寸的同轴度,并且对这两个尺寸的精度要求也较高,此外口部圆角半径较小,因此可能需要整形工序。
但是通过制造精度高、间隙小的模具是可以实现的,因此,从精度方面来说,该工件也适合冲压加工。
(3)结构。
该工件是带凸缘的筒形轴对称零件,形状比较简单,有利于进行合理排样,材料利用率也高。
连接处为圆弧过渡,不至于对模具造成大的损坏。
并且尺寸设计的也比较合理,冲压加工经济性良好。
从结构上来看,大致可以通过落料、拉深、冲孔、翻边工序来实现。
综上所述,该工件适合采用冲压加工来实现。
图2.1工件图
2.2修边余量的计算
dF1/d=50/23.8=2.1
式中:
dF1为工件的凸缘直径,mm;
d为筒形件拉深直径,mm。
表2-2凸缘筒形件的修边余量(mm)
凸缘直径dF
凸缘相对直径dF/d
﹤1.5
1.5~2
2~2.5
2.5~3
≤25
﹥25~50
﹥50~100
﹥100~150
﹥150~200
﹥200~250
﹥250
1.6
2.5
3.5
4.3
5.0
5.5
6.0
1.4
2.0
3.0
3.6
4.2
4.6
5.0
1.2
1.8
2.5
3.0
3.5
3.8
4.0
1.0
1.6
2.2
2.5
2.7
2.8
3.0
查表2-2,得ΔR=1.8mm≈2.0mm,
故翻边之前工件的直径dF=50+2+2=54mm。
由dF/d=54/23.8=2.27﹥1.4,可知该工件属于宽凸缘筒形件。
2.3毛坯尺寸的计算
D0=
(2-1)
式中:
D0为毛坯直径,mm;
h为拉深件高度,mm;
r为圆角半径,mm。
代入数值有:
D0=
=65mm
2.4确定是否采用压边圈
t/D0*100=1.5/65*100=2.3
其中t为材料厚度,mm。
查表2-3可知,t/D0*100=2.3﹥2.0,故不用压边圈[16]。
表2-3采用压边圈的条件
拉深方式
第一次拉深
(t/D)*100
m1
用压边圈
不用压边圈
可用可不用压边圈
﹤1.5
﹥2.0
1.5~2.0
﹤0.6
﹥0.6
0.6
注:
t为材料厚度;D为毛坯直径。
2.5拉深次数的确定
dF/d=54/23.8=2.27,
t/D0*100%=1.5/65*100%=2.3%
凸缘筒形件首次拉深极限相对高度h1/d1=0.28~0.35,而实际h/d=16/23.8=0.67﹥0.35。
故不能一次拉深。
表2-4推荐采用的筒形件不用压边圈时的拉深系数
毛坯相对厚度
(t/D)*100
各次拉深系数
m1
m2
m3
m4
m5
m6
1.5
2.0
2.5
3.0
3以上
0.65
0.60
0.55
0.53
0.50
0.80
0.75
0.75
0.75
0.70
0.84
0.80
0.80
0.80
0.75
0.87
0.84
0.84
0.84
0.78
0.90
0.87
0.87
0.87
0.82
—
0.90
0.90
0.90
0.85
注:
此表适用于08、10及15Mn等材料。
根据表2-4选取各次拉深系数如下:
m1=0.56,d1=m1D0=0.56*65=36.5mm﹥23.8mm
m2=0.75,d2=m2d1=0.75*36.5=27.4mm﹥23.8mm
m3=0.80,d3=m3d2=0.80*27.4=21.9mm﹤23.8mm
故需要三次拉深。
经调整后:
m1=0.56,d1=36.5mm
m2=0.81,d2=29.5mm
m3=0.81,d3=23.8mm
计算各次拉深高度:
hn=0.25/dn(D02-DF2)+0.43(rn+Rn)+0.14/dn(rn2-Rn2)(2-2)
式中:
hn为第n个工序后拉深件高度,mm;
dn为第n个工序后拉深件直径,mm;
rn为第n个工序后拉深件底部圆角半径,mm;
Rn为第n个工序后拉深件凸缘处圆角半径,mm。
由于rn=2.25,Rn=2.25,故rn2-Rn2=0,代入数值得:
h1=0.25/36.5*(652-542)+0.43*(2.25+2.25)+0.14/36.5*(2.252-2.252)=11mm;
h2=0.25/29.5*(652-542)+0.43*(2.25+2.25)+0.14/29.5*(2.252-2.252)=13mm;
h3=0.25/23.8*(652-542)+0.43*(2.25+2.25)+0.14/23.8*(2.252-2.252)=16mm。
2.6冲孔和翻边的尺寸计算
翻孔的竖边高度为H,由工件图的尺寸可知,H=21-16=5mm。
由公式:
H=(D-d0)/2+0.43r+0.72t
=D/2(1-K)+0.43r+0.72t(2-3)
其中,D为翻孔后工件直径,mm;
K为翻孔系数。
代入数值则有:
5=18/2(1-K)+0.43*1+0.72*1.5
求得K=0.61
由公式K=d/D,有d0=KD=0.61*18=11mm。
即翻边前所冲裁的孔的直径为11mm。
d0/t=11/1.5=7.3,查[15]表19.5-1可知,其极限翻边系数Kmin=0.5﹤0.61,故可以一次翻出高度为5的竖边。
2.7工艺方案的确定
根据以上的计算可知,该工件需要经过落料、首次拉深、二次拉深、三次拉深、冲孔、翻边和切边工序才能加工完成。
根据这些工序可以拟定以下几种方案:
方案一:
全部采用单工序模;
方案二:
采用一套落料首次拉深复合模,其余采用单工序模;
方案三:
采用一套落料、首次拉深和冲孔复合模,其余采用单工序模;
方案四:
采用一套落料首次拉深复合模,一套冲孔翻边复合模,其余采用单工序模。
对于方案一,单工序模虽然优点很多,比如结构简单,制造费用低,但是最大的缺陷就是生产效率低,不适合大批量生产,因此不满足本设计的要求。
对于方案二,虽然采用了一套复合模,较方案一相比,有效的提高了生产效率,但是单工序模还是很多,制造精度和生产效率还是不太适合大批量生产。
对于方案三,生产效率较前面两种有很大提高,但是在冲完孔之后再进行二次拉深和三次拉深,不能精确的保证孔径的位置和尺寸,要是孔径一旦发生变化的话,将会对翻边的高度尺寸和翻边口部的质量产生严重影响,有可能加工出来的工件完全不符合要求,因此这种工序安排不太合理。
对于方案四,无论是从生产效率还是制造精度方面较前面三种相比都更合理。
综上,采用第四种方案最合适。
即先落料首次拉深复合、然后再二次拉深、三次拉深、冲孔翻边复合、最后再切边修整。
2.8排样设计
该工件的落料件为圆形,形状简单,故可以采用直排的方式,考虑到产品精度和模具寿命的因素,可以采用搭边排样。
表2-5最少搭边值
材料厚度/mm
圆形
非圆形
a
a1
a
a1
≤1
1~2
2~3
3~4
4~5
5~6
6~8
1.5
2
2.5
3
4
5
6
1.5
1.5
2
2.5
3
4
5
2
2.5
3
3.5
5
6
7
1.5
2
2.5
3
4
5
6
注:
a为工件到条料边缘的距离,a1为连个工件之间的距离。
查表2-5可知,a1=1.5mm,a=2mm。
排样图如下:
图2.2排样图
板材可以选1800mm*900mm*1.5mm的标准钢板。
分别比较纵裁和横裁两种排样,看哪一种材料利用率高,从中选择材料利用率较高的那一种[17]。
(1)纵裁:
每块板料可以裁成的条料数为n1,
n1=900/69=13;
每块条料可裁制件数为n2,
n2=1800/66.5=27;
每块条料可裁制件数为n,
n=n1*n2=13*27=351。
材料利用率为η,
η=
*100%=72%
(2)横裁:
每块板料可以裁成的条料数为n1’,
n1’=1800/69=26;
每块条料可裁制件数为n2’,
n2’=900/66.5=13;
每块条料可裁制件数为n,
n=n1’*n2’=26*13=338。
材料利用率为η’,
η’=
*100%=69%
通过上述比较可知,纵裁的材料利用率为72%,而横裁的材料利用率为69%,故采用纵裁的排样方式较好。
2.9模具工艺性分析
2.9.1各工序冲压力的计算
2.9.1.1落料
(1)落料力的计算
F落料=KLt
0(2-4)
式中:
F落料为落料力,N;
K为安全系数,K=1.3;
t为材料厚度,mm;
0为材料的抗剪强度,Mpa。
代入数值有:
F落料=1.3*3.14*65*1.5*300=119.42KN。