铸铁的热处理.docx
《铸铁的热处理.docx》由会员分享,可在线阅读,更多相关《铸铁的热处理.docx(17页珍藏版)》请在冰豆网上搜索。
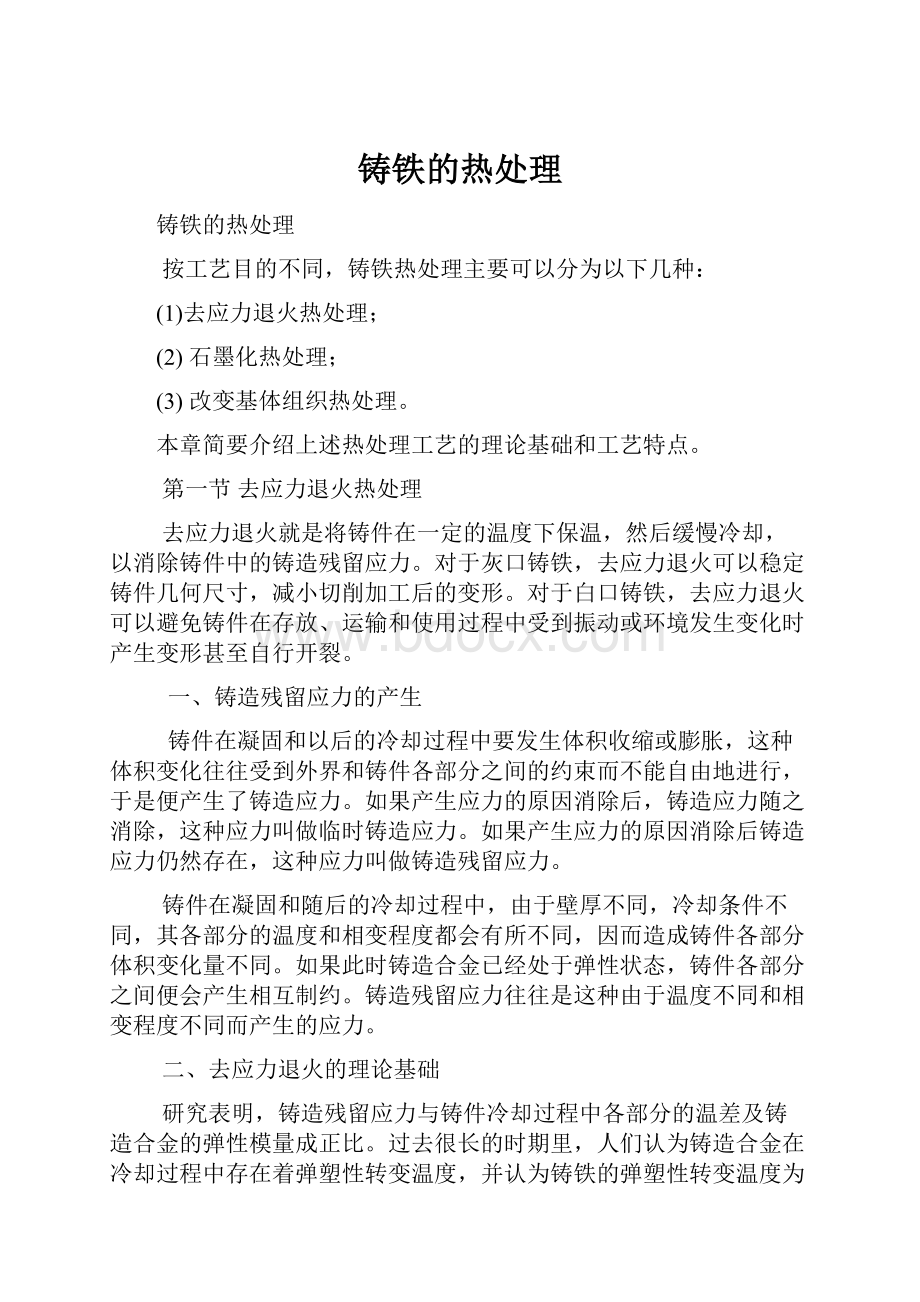
铸铁的热处理
铸铁的热处理
按工艺目的不同,铸铁热处理主要可以分为以下几种:
(1)去应力退火热处理;
(2)石墨化热处理;
(3)改变基体组织热处理。
本章简要介绍上述热处理工艺的理论基础和工艺特点。
第一节去应力退火热处理
去应力退火就是将铸件在一定的温度下保温,然后缓慢冷却,以消除铸件中的铸造残留应力。
对于灰口铸铁,去应力退火可以稳定铸件几何尺寸,减小切削加工后的变形。
对于白口铸铁,去应力退火可以避免铸件在存放、运输和使用过程中受到振动或环境发生变化时产生变形甚至自行开裂。
一、铸造残留应力的产生
铸件在凝固和以后的冷却过程中要发生体积收缩或膨胀,这种体积变化往往受到外界和铸件各部分之间的约束而不能自由地进行,于是便产生了铸造应力。
如果产生应力的原因消除后,铸造应力随之消除,这种应力叫做临时铸造应力。
如果产生应力的原因消除后铸造应力仍然存在,这种应力叫做铸造残留应力。
铸件在凝固和随后的冷却过程中,由于壁厚不同,冷却条件不同,其各部分的温度和相变程度都会有所不同,因而造成铸件各部分体积变化量不同。
如果此时铸造合金已经处于弹性状态,铸件各部分之间便会产生相互制约。
铸造残留应力往往是这种由于温度不同和相变程度不同而产生的应力。
二、去应力退火的理论基础
研究表明,铸造残留应力与铸件冷却过程中各部分的温差及铸造合金的弹性模量成正比。
过去很长的时期里,人们认为铸造合金在冷却过程中存在着弹塑性转变温度,并认为铸铁的弹塑性转变温度为400℃左右。
基于这种认识,去应力退火的加热温度应是400℃。
但是,实践证明这个加热温度并不理想。
近期的研究表明,合金材料不存在弹塑性转变温度,即使处于固液共存状态的合金仍具有弹性。
为了正确选择去应力退火的加热温度,首先让我们看看铸铁在冷却过程中应力的变化情况。
图8─1是用应力框测定的灰铸铁冷却过程中粗杆内应力的变化曲线。
图8─1灰铸铁应力变化曲线
在a点前灰铸铁细杆已凝固完毕,粗杆处于共晶转变期,粗杆石墨化所产生的膨胀受到细杆的阻碍,产生压应力,到达a点时,粗杆的共晶转变结束,应力达到极大值。
从a点开始,粗杆冷却速度超过细杆,二者温差逐渐减小,应力随之减小,到达b点时应力降为零。
此后由于粗杆的线收缩仍然大于细杆,加上细杆进入共析转变后石墨析出引起的膨胀,粗杆中的应力转变为拉应力。
到达c点时粗杆共析转变开始,细杆共析转变结束,两杆温差再次增大,粗杆受到的拉应力减小。
到达d点时,粗杆受到的拉应力降为零,粗杆所受到的应力又开始转变为压应力。
从e点开始,粗杆的冷却速度再次大于细杆,两杆的温差再次减小,粗杆受到的压应力开始减小。
到达f点时,应力再度为零。
此时两杆仍然存在温差,粗杆的收缩速度仍然大于细杆,在随后的冷却过程中,粗杆所受到的拉应力继续增大。
从上述分析可以看出,灰铸铁在冷却过程中有三次完全卸载(即应力等于零)状态。
如果在其最后一次完全卸载(即f点)时,对铸件保温,消除两杆的温差,然后使其缓慢冷却,就会使两杆间的应力降到最小。
对灰铸铁冷却过程中的应力测定表明,灰铸铁最后一次完全卸载温度在550~600℃。
这与实际生产中灰铸铁的退火温度相近。
三、去应力退火工艺
为了提高去应力退火的实际效果,加热温度最好能达到铸件最后一次完全卸载温度。
在低于最后一次完全卸载温度时,加热温度越高,应力消除越充分。
但是,加热温度过高,会引起铸件组织发生变化,从而影响铸件的性能。
对于灰铸铁件,加热温度过高,会使共析渗碳体石墨化,使铸件强度和硬度降低。
对于白口铸铁件,加热温度过高,也会使共析渗碳体分解,使铸件的硬度和耐磨性大幅度降低。
普通灰铸铁去应力退火的加热温度为550℃。
当铸铁中含有稳定基体组织的合金元素时,可适当提高去应力退火温度。
低合金灰口铸铁为600℃,高合金灰口铸铁可提高到650℃。
加热速度一般为60~100℃/h。
保温时间可按以下经验公式计算
H=铸件厚度/25+H'
式中铸件厚度的单位是毫米,保温时间的单位是小时,H'在2~8范围里选择。
形状复杂和要求充分消除应力的铸件应取较大的H'值。
随炉冷却速度应控制在30℃/h以下,一般铸件冷至150~200℃出炉,形状复杂的铸件冷至100℃出炉。
表8─1为一些灰铸铁件的去应力退火规范,供参考。
表8─1一些灰铸铁件去应力退火规范
普通白口铸铁去应力退火的加热温度不应超过500℃,高合金白口铸铁由于其共析渗碳体稳定性好及铸造应力大,其加热温度一般远远高于普通白口铸铁,可达800~900℃。
表8─2给出了两种高合金白口铸铁的去应力退火规范,供参考。
表8─2两种高合金白口铸铁的去应力退火规范
第二节石墨化退火热处理
石墨化退火的目的是使铸铁中渗碳体分解为石墨和铁素体。
这种热处理工艺是可锻铸铁件生产的必要环节。
在灰铸铁生产中,为降低铸件硬度,便于切削加工,有时也采用这种工艺方法。
在球墨铸铁生产中常用这种处理方法获得高韧性铁素体球墨铸铁。
一、石墨化退火的理论基础
根据相稳定的自由能计算,铸铁中渗碳体是介稳定相,石墨是稳定相,渗碳体在低温时的稳定性低于高温。
因此从热力学的角度看,渗碳体在任一温度下都可以分解为石墨和铁碳固溶体,而且在低温下,渗碳体分解更容易。
但是,石墨化过程能否进行,还取决于石墨的形核及碳的扩散能力等动力学因素。
对于固态相变,原子的扩散对相变能否进行起重要作用。
由于温度较高时,原子的扩散比较容易,因此实际上渗碳体在高温时分解比较容易。
尤其是自由渗碳体和共晶渗碳体分解时,由于要求原子做远距离扩散,只有在温度较高时才有可能进行。
1.石墨的形核
对于可锻铸铁,渗碳体的分解首先要求形成石墨核心。
在固相基体中,石墨形核既要克服新相形成所引起的界面能的增加,同时又要克服石墨形核时体积膨胀所受到的外界阻碍,因此其形核比在液态时要困难得多。
由于在渗碳体与其周围固溶体的界面上存在有大量的空位等晶体缺陷,石墨晶核首先在这里形成。
在渗碳体内,尽管也可能存在有晶体缺陷,但是由于石墨形核会引起较大的体积膨胀,而渗碳体硬度高,体积容让性差,必然会对此产生巨大的阻力,从而阻碍石墨核心在其内部形成。
在实际生产中,铸铁内往往存在有各种氧化物、硫化物等夹杂物。
其中一些夹杂物与石墨有良好的晶格对应关系,可以作为石墨形核的基底,减小了由于石墨形核所造成的界面能的增加。
因此在实际条件下,石墨形核要比理想状态容易些。
对于灰铸铁和球墨铸铁,石墨化过程不需要石墨重新形核。
2.高温石墨化过程
高温石墨化的主要目的是使自由渗碳体和共晶渗碳体分解。
如果把含有渗碳体的铸铁加热到奥氏体温度区域,石墨的形核则发生在奥氏体与渗碳体的界面上。
石墨形核后,随着渗碳体的分解,借助于碳原子向石墨核心的扩散不断长大,最终完成石墨化过程。
需要指出的是,对于可锻铸铁而言,其铸态组织是按亚稳定系凝固而成,其中奥氏体相对于稳定系奥氏体呈碳过饱和状态,石墨化后,奥氏体中碳浓度也要发生变化。
石墨化完成后,铸铁的平衡组织为奥氏体加石墨。
如果此时将铸铁缓慢冷却,奥氏体将发生共析转变,其转变产物是铁素体和二次石墨,铸铁的最终平衡组织为铁素体加石墨。
3.低温石墨化过程
低温石墨化是指在A1温度(720~750℃)以下保温的石墨化过程。
可分为两种情况:
一种是铸铁经过高温奥氏体化后再进行低温石墨化处理;
另一种是铸铁不经过高温奥氏体化,而仅加热到A1温度以下进行低温石墨化。
前者的目的是使奥氏体在共析转变时按稳定系转变为铁素体和石墨。
后者不形成奥氏体,共析渗碳体直接分解为铁素体加石墨。
如前所述,从热力学条件看,在低温下石墨化是可能的。
此时关键的问题是碳原子的扩散。
在低温下,碳原子本身的扩散能力很低,加之铁素体溶解碳的能力很小,碳原子的扩散比较困难,主要通过晶粒边界和晶体内部缺陷进行。
因此,要提高低温石墨化的速度,关键是减小碳原子的扩散距离。
细化铸态组织,增加晶界,增加石墨核心是减小碳原子扩散距离的有效措施。
二、石墨化退火工艺
1.铁素体(黑心)可锻铸铁的石墨化退火工艺
图8─2铁素体可锻铸铁退火工艺图
图8─2所示,黑心可锻铸铁的石墨化有五个阶段:
(1)升温;
(2)第一阶段石墨化;
(3)中间阶段冷却;
(4)第二阶段石墨化;
(5)出炉冷却。
表8─3为一些典型可锻铸铁件石墨化退火实例,供参考。
表8─3铁素体可锻铸铁石墨化退火实例
2.珠光体可锻铸铁石墨化退火工艺
珠光体可锻铸铁的石墨化退火与铁素体可锻铸铁的第一阶段石墨化相同,但不进行第二阶段石墨化,或在第一阶段石墨化后淬火并高温回火。
其热处理实例见表8─4。
表8─4珠光体可锻铸铁石墨化退火实例
3.灰口铸铁和球墨铸铁的石墨化退火
灰口铸铁和球墨铸铁的石墨化退火又称为软化退火。
当铸件中共晶渗碳体不多时,石墨化退火的目的是使共析渗碳体分解,此时可选用低温石墨化退火。
当铸件中含有自由渗碳体或共晶渗碳体时石墨化退火的目的是消除自由渗碳体和共晶渗碳体,此时须进行高温石墨化退火。
退火工艺见表8-5。
表8─5灰口铸铁和球墨铸铁石墨化退火工艺
退火类型
铸铁类型
加热温度(℃)
保温时间(h)
出炉温度(℃)
低温
石墨化
灰口铸铁
650~750
1~4
<300
球墨铸铁
720~760
2+铸件厚度/25
<600
高温
石墨化
灰口铸铁
900~950
2+铸件厚度/25
100~300
球墨铸铁
880~980
1+铸件厚度/25
<600
第三节改变基体组织的热处理
一、改变基体组织热处理的理论基础
1.过冷奥氏体的转变及其产物
如果将奥氏体化后的铸铁冷却到A1温度以下(此时的奥氏体称为过冷奥氏体),奥氏体就会发生转变。
其转变可以是珠光体转变、贝氏体转变、或马氏体转变。
究竟发生何种转变一方面取决于各种转变生成相在不同温度下的自由能,另一方面与各种转变所要求的动力学条件有关。
对于铁碳合金,珠光体转变发生在A1以下至550℃左右。
在此温度下,原子可以充分扩散,转变产物为珠光体。
在一般情况下,珠光体内的铁素体和渗碳体呈片状相间分布,其片层厚度与珠光体转变温度有关。
转变温度越低,所形成的珠光体分散度越高,片层间距越小,其力学性能越高。
随着转变温度的降低,其转变产物依次为粗大珠光体或称珠光体,细珠光体或称索氏体,极细珠光体或称屈氏体(托氏体)。
如果奥氏体冷却到大约220~550℃进行转变,由于温度较低,原子的扩散不能充分进行,奥氏体分解为介稳定的过饱和α-Fe与碳化物(或渗碳体)的混合物。
这种转变产物称为贝氏体。
贝氏体分为上贝氏体和下贝氏体。
在接近珠光体转变温度(550℃稍下)所形成的贝氏体称为上贝氏体,由平行的α-Fe相和其间分布的碳化物所组成。
在金相显微镜下,上贝氏体呈羽毛状,因此又叫做羽毛状贝氏体。
在靠近马氏体转变温度(220℃稍上)所形成的贝氏体称为下贝氏体,由针状过饱和α-Fe及其上分散的微细碳化物所组成,又叫做针状贝氏体。
如果奥氏体冷却到更低的温度进行转变,原子的扩散已无法进行,奥氏体只能以非扩散的形式转变为马氏体。
奥氏体只有冷却到某一温度以下才可以发生马氏体转变,这个温度称为马氏体转变开始点,简称马氏体点。
马氏体转变的特点是在转变过程中铁、碳原子都不发生扩散,所生成的马氏体与原来的奥氏体成分相同。
从晶体结构上看,马氏体仍是碳在α-Fe中的过饱和固溶体。
高碳马氏体在金相显微镜下呈针状。
2.过冷奥氏体等温转变动力学曲线(C曲线)
过冷奥氏体等温转变动力学曲线是表示不同温度下过冷奥氏体转变量与转变时间关系的曲线。
由于通常不需要了解某时刻转变量的多少,而比较注重转变的开始和结束时间,因此常常将这种曲线绘制成温度─时间曲线,简称C曲线(如图8─3所示)。
图8─3共析成分奥氏体的C曲线
C曲线的左边一条线表示转变开始时间,称为孕育期。
孕育期的长短取决于过冷奥氏体在该温度下的稳定性,它与该温度下过冷奥氏体与形成新相之间的能量差和碳原子的扩散能力有关。
如图8─4所示,温度越低,过冷度越大,自由能差越大,转变驱动力越大;但同时,温度的降低又使原子的扩散能力降低。
因此过冷奥氏体在某一特定温度下转变的孕育期最短。
温度过高和过低都不利。
图8─4过冷奥氏体的转变与温度的关系
对于铸铁,其奥氏体成分一般是过共析的,其C曲线上多出一条表示先共析渗碳体(或石墨)析出的曲线(如图8─5所示)。
奥氏体的成分偏离共析点越远,这条先共析相析出线距离珠光体转变开始线也越远。
铁成分不同,其过冷奥氏体转变的C曲线不同。
根据不同成分铸铁过冷奥氏体转变的C曲线,可以容易地预测该成分铸铁不同温度下奥氏体等温转变的产物,从而制订合理的等温转变热处理工艺。
图8─5过共析奥氏体等温转变曲线
3.过冷奥氏体的连续冷却转变曲线(CCT曲线)
在实际热处理中,等温热处理工艺比较繁琐,因而较多的是采用连续冷却热处理。
在连续冷却过程中,奥氏体是在不断降温过程中发生转变的。
为简便起见,可以将铸铁的冷却曲线绘制到C曲线上,以定性地分析在连续冷却条件下过冷奥氏体的转变。
如图8─6所示,当冷却速度为V1时,冷却曲线与C曲线有两个交点,a1点表示珠光体转变开始,b1点表示珠光体转变结束。
将冷却速度提高到V2,转变开始时间和结束时间缩短,转变温度降低。
如果将冷却速度提高到临界冷却速度V'c以上(比如V3),则冷却曲线不与转变终了线相交,这表明只有一部分奥氏体转变为珠光体,而其余部分被过冷到Ms点以下转变为马氏体。
在此范围里,冷却速度越大,奥氏体转变为珠光体的量越少,而马氏体量越多。
如果冷却速度大于Vc,则奥氏体全部转变为马氏体。
图8─6应用C曲线分析不同冷却速度下过冷奥氏体转变示意图
虽然应用C曲线可以定性地分析过冷奥氏体连续冷却转变,但是由于连续冷却时奥氏体转变的孕育期与等温转变有所不同,上述分析在数值上存在着一定的偏差。
因此,在分析过冷奥氏体连续冷却时比较多的是采用过冷奥氏体的连续冷却转变曲线(CCT曲线)。
图8─7是共析成分奥氏体连续冷却转变曲线,为便于对比,图中还画出了C曲线。
与其C曲线相比,连续冷却时转变开始时间和开始温度降低。
图8─7共析奥氏体连续冷却转变曲线
连续冷却速度很小时,转变的过冷度很小,转变开始和终了的时间很长。
如果提高冷却速度,则转变温度降低,转变的开始和终了时间缩短,转变所经历的温度区间增大。
图中CC’线为转变中止线,表示冷却曲线与此线相交时转变并未完成,但奥氏体分解停止,剩余部分被冷却到更低的温度下转变为马氏体。
如果冷却速度很大,奥氏体将全部转变为马氏体。
化学成分、加热速度、奥氏体化温度都对奥氏体连续冷却转变曲线有影响。
因此,实际铸铁的连续冷却转变曲线与图8─7有比较大的出入。
图8─8是一种球墨连续冷却转变曲线,供参考,冷却曲线下面的数据为硬度(HV10)。
图8─8一种球墨铸铁的连续冷却转变曲线
C3.59%,Si2.71%,Mn0.29%,Cr0.04%,Ni0.03%,Mo0.022%
4.珠光体、马氏体、贝氏体相变特点
珠光体、马氏体和贝氏体相变机制在有关金属学及钢的热处理教材中都有详细介绍,限于篇幅,这里不再赘述。
表8─6给出了上述三种转变的特点,供参考。
表中所注温度是针对铁碳合金的,对于铸铁,则视硅、锰含量而有所不同。
表8─6珠光体、马氏体、贝氏体相变特点
二、改变基体组织的热处理及其工艺
1.正火
铸铁的正火处理主要用于球墨铸铁、蠕墨铸铁和灰铸铁,其目的是使基体组织中珠光体含量增多,提高铸铁的耐磨性和强度。
对于球墨铸铁而言,根据加热时是否保留部分铁素体,正火可分为完全奥氏体化正火和部分奥氏体化正火。
(1)灰口铸铁的正火工艺
灰口铸铁共晶渗碳体较少时,正火加热温度一般为850~900℃;共晶渗碳体较多时,加热温度一般为900~950℃。
加热温度高,可提高奥氏体的碳含量,使冷却后珠光体量提高。
保温时间为1~3小时。
保温后在空气中冷却,或采用风冷和喷雾冷却,以提高珠光体含量,并使其细化。
(2)球墨铸铁的正火处理
球墨铸铁的热处理主要有高温奥氏体化正火,两阶段正火,部分奥氏体化正火和高温不保温正火。
这些正火工艺的目的、工艺规范、及所得到的基体组织见表8─7。
表8─7球墨铸铁常用正火工艺
2.淬火和回火
淬火的目的是获得普通冷却条件下不能得到的急冷组织,以提高铸件的硬度、耐磨性和综合力学性能。
回火则是淬火处理的一种后处理工序,其目的是减小淬火中产生的应力。
(1)抗磨白口铸铁的淬火及回火工艺
表8─8给出了一些抗磨白口铸铁的热处理规范,供参考。
表8─8一些白口铸铁的热处理参考规范
(2)球墨铸铁的淬火及回火工艺
球墨铸铁的淬火及回火工艺见表8─9。
表8─9球墨铸铁的淬火及回火工艺
3.等温淬火
等温淬火的目的是使材料具有高强度和高硬度的同时具有较高的塑性和韧性,是目前有效发挥材料最大潜力的一种热处理方法。
在白口铸铁生产中,等温淬火可用于犁铧、粉碎机锤头、抛丸机叶片及衬板等铸件的热处理。
其工艺是将白口铸铁在900℃奥氏体化,然后根据不同成分铸铁的过冷奥氏体等温转变曲线确定等温转变温度,在该温度下等温1~1.5小时后空冷。
在球墨铸铁、蠕墨铸铁和灰铸铁生产中,等温淬火工艺主要用来获得贝氏体加残余奥氏体基体组织。
其工艺是将铸铁加热到奥氏体化温度,保温后进行等温淬火。
提高奥氏体化温度,会提高奥氏体含碳量,使形成上贝氏体的下限温度降低,有利于形成上贝氏体组织。
增加奥氏体化保温时间,会提高奥氏体的稳定性,有利于保留一定数量的残留奥氏体,从而改善材料的韧性。
等温淬火温度要根据C曲线确定。
等温淬火时间过长会析出碳化物,降低材料的韧性;过短则贝氏体量不足。
加入一定的合金元素,诸如Mo、Cu、Ni可提高淬透性。
图8─9和图8─10分别是球墨铸铁上贝氏体和下贝氏体等温淬火工艺,供参考。
图8─9球墨铸铁上贝氏体等温淬火工艺
图8─10球墨铸铁下贝氏体等温淬火工艺