机电一体化专业论文.docx
《机电一体化专业论文.docx》由会员分享,可在线阅读,更多相关《机电一体化专业论文.docx(38页珍藏版)》请在冰豆网上搜索。
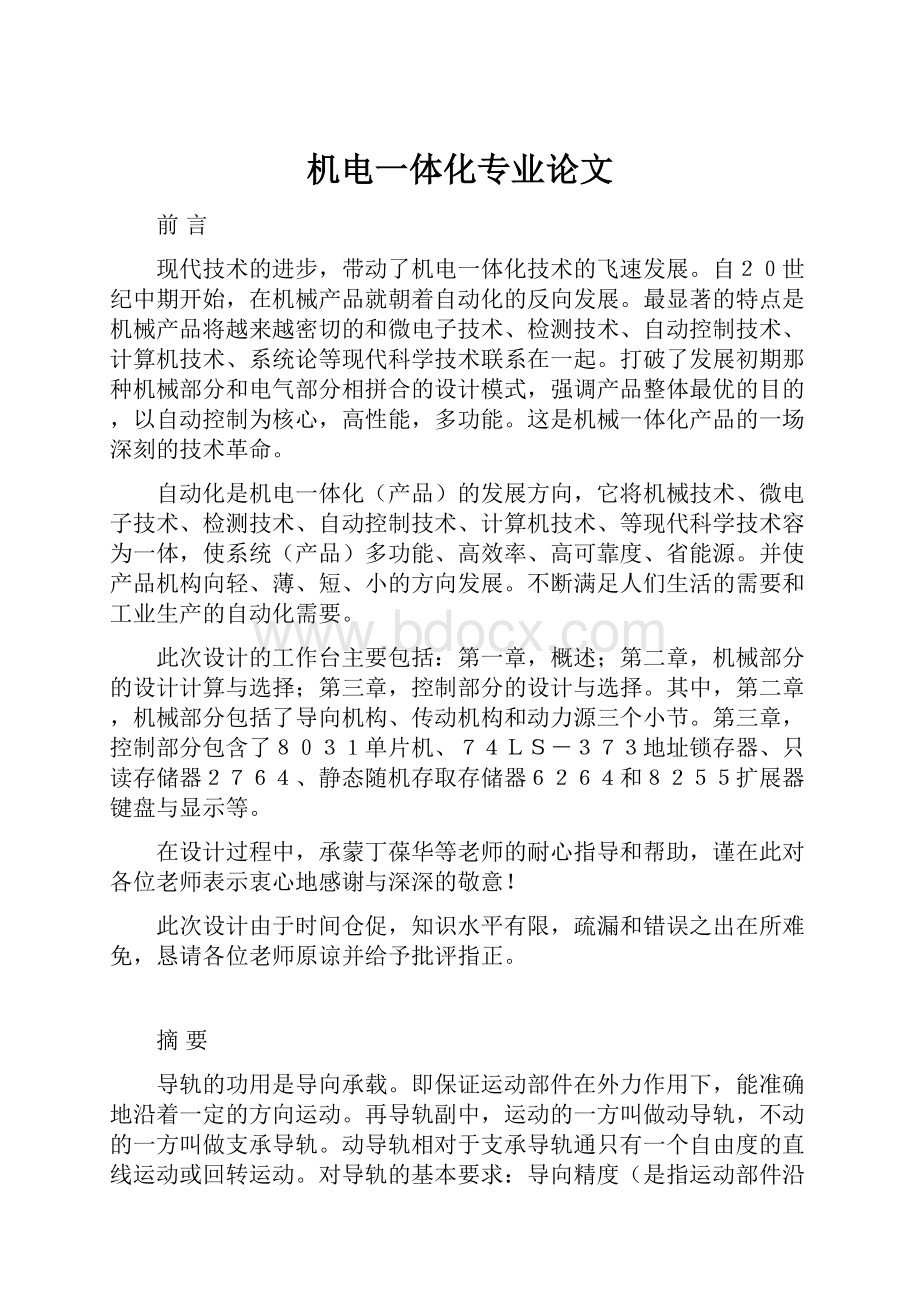
机电一体化专业论文
前言
现代技术的进步,带动了机电一体化技术的飞速发展。
自20世纪中期开始,在机械产品就朝着自动化的反向发展。
最显著的特点是机械产品将越来越密切的和微电子技术、检测技术、自动控制技术、计算机技术、系统论等现代科学技术联系在一起。
打破了发展初期那种机械部分和电气部分相拼合的设计模式,强调产品整体最优的目的,以自动控制为核心,高性能,多功能。
这是机械一体化产品的一场深刻的技术革命。
自动化是机电一体化(产品)的发展方向,它将机械技术、微电子技术、检测技术、自动控制技术、计算机技术、等现代科学技术容为一体,使系统(产品)多功能、高效率、高可靠度、省能源。
并使产品机构向轻、薄、短、小的方向发展。
不断满足人们生活的需要和工业生产的自动化需要。
此次设计的工作台主要包括:
第一章,概述;第二章,机械部分的设计计算与选择;第三章,控制部分的设计与选择。
其中,第二章,机械部分包括了导向机构、传动机构和动力源三个小节。
第三章,控制部分包含了8031单片机、74LS-373地址锁存器、只读存储器2764、静态随机存取存储器6264和8255扩展器键盘与显示等。
在设计过程中,承蒙丁葆华等老师的耐心指导和帮助,谨在此对各位老师表示衷心地感谢与深深的敬意!
此次设计由于时间仓促,知识水平有限,疏漏和错误之出在所难免,恳请各位老师原谅并给予批评指正。
摘要
导轨的功用是导向承载。
即保证运动部件在外力作用下,能准确地沿着一定的方向运动。
再导轨副中,运动的一方叫做动导轨,不动的一方叫做支承导轨。
动导轨相对于支承导轨通只有一个自由度的直线运动或回转运动。
对导轨的基本要求:
导向精度(是指运动部件沿着导轨运动的轨迹准确性)、精度保持性(为了能长期保持导向精度,对导轨提出了刚度和耐磨性的要求、低速运动平稳性(就是要保证在做低速运动或微量位移时不出现不平稳现象)。
结构工艺性(在可能的情况下,应尽量是导轨结构简单,便于制造和维护)。
此次设计采用的导轨为闭式双矩形导轨,行程为100mm,负载为300N,动导轨长度L=120mm。
静导轨长度为L=263mm与机架做为一体。
润滑油选用N46机械油,在油中加入能形成吸附膜的添加剂。
间隙的调整用压板调整间隙,有平镶条调整侧向间隙。
防护:
用刮板式,选用毛毡。
传动机构:
使用滚珠丝杠螺母副主要将旋转运动转换为工作台的直线运动。
滚珠丝杠螺母机构虽然结构复杂、制造成本高,但其最大优点是摩擦阻力矩小、传动效率高(92%~98%)定位精度高,精密保持性好。
该工作台采用外循环双圆弧滚珠丝杠螺母副,预紧方式为双螺母罗纹预紧,支承方式为双推-简支式无冲击平稳运转精度为E级,传动精度为σ=
动力源采用反应式步进电动机,该类电动机由定子绕组产生的反应电磁力吸引用软磁钢制成的齿形转子作步进驱动,故又称作反应式步进电动机。
其特点:
无激磁时没有保持力,将气隙做得极小。
制造材料费用低、结构简单、步距角小等优点。
此次采用的步进电动机为此系列的五相单十拍,步距角α=0.36。
脉冲当量δρ=0.005mm的步进电动机。
最大进给速度vmax0.4m/min,定位精度σ=±0.001mm。
控制部分。
在控制电路中采用MCS-31单片机、74LS-373地址锁存器、只读存储器2764、静态随机存取存储器6264和8255扩展器。
为了减少硬件开锁,提高系统可靠性和降低成本,使用了动态扫描显示。
为简化电路还使用了非编码键盘。
目录
摘要…………………………………………………………………1
前言…………………………………………………………………2
第一章概述………………………………………………………..1
第二章机械部分…………………………………………………..2
第一节导轨………………………………………………………………2
第二节滚珠丝杠副………………………………………………………8
第三节步进电动机……………………………………………………...16
第四节滚动轴承及联轴器选用………………………………………...21
第三章控制电路部分的选择与设计…………………………….22
第一节MCS-51单片机结构和工作方式………………………….22
第二节8031对片外存储器的连接………………………………….25
第三节MCS-51系列单片机工作方式…………………………...26
第四节存储器2764与6264………………………………….29
第五节8255扩展芯片及键盘/显示系统……………………….31
参考文献………………………………………………….33
结束语…………………………………………………….34
第一章概述
“机电一体化”是微电子技术与机械工业融合过程中形成的一个新概念,是各相关技术有机结合的一种新形领域。
机电一体化的目的是使系统(产品)高附加值化。
机电一体化系统(产品)由机械系统、控制系统、动力系统、传感检测系统、执行元件等五个子系统组成。
机电一体化系统设计的考虑方法通常有:
机电互补法、融合法和组成法。
其目的是综合运用机械系统技术和微电子技术的特长,设计最佳的机电一体化系统。
机电一体化系统的机械系统与一般的机械系统相比,除要求具有较高的定位精度之外,还应有良好的动态响应特性,无间隙、低摩擦、低惯量、高刚度、高谐振频率、适当的阻尼比等要求。
达到上述要求所采取的措施:
⑴采用低摩擦的传动件和导向支承部件。
如采用滚动丝杠副、滚动导向支承(如滚动导轨)。
⑵缩短传动链,提高传动与支承刚度,如用加预紧了的方法提高丝杠副和导轨副的传动与支承刚度。
⑶选用最佳传动比,以达到提高系统转动惯量,尽可能的提高加速能力⑷缩小反向死区误差,如采取消除传动间隙减少支承变形的措施。
⑸改进支承及机架的结构设计以提高刚性、减少振动、降低噪声。
如选复合材料来提高刚度和强度、减轻重量、缩小体积使结构紧密,以确保系统的小型化、轻量化、高速化和高可靠性。
对于传动机构有以下三个方面的要求⑴精密化。
虽然不是越精密越好,但一定要适应产品的定位精度的性能要求,由于产品性能的需要,对机械传动机构的精密度要求也越来越高。
⑵高速化。
产品工作效率的高低,直接与机械传动部件的运动速度有关。
⑶小型化、轻量化。
随着机电一体化系统(或产品的)精密化、高速化的发展,必然要求其传动机构的小型化、轻量化,以提高运动灵敏度,减少冲击,降低能耗。
第二章机械部分
第一节导轨
一.导轨的功用、分类和基本要求
㈠导轨的功用
导轨的功用是导向承载。
即保证运动部件在外力作用下,能准确地沿着一定的方向运动。
再导轨副中,运动的一方叫做动导轨,不动的一方叫做支承导轨。
动导轨相对于支承导轨通只有一个自由度的直线运动或回转运动。
㈡导轨的分类
导轨可按下列性质分类
①按工作性质可分为主运动导轨、进给运动导轨和调位导轨。
调位导轨只用于调整部件之间的相对位置,在加工时没有相对运动。
例如
车床尾架用的导轨。
②按摩擦性质可分为滑动导轨和滚动导轨。
滑动导轨按两导轨面间的摩擦状态又可分为混合摩擦的导轨、边界摩擦导轨、液体动压导轨和液体静压导轨。
滚动导轨按其滚动体不同又可分为滚珠导轨、滚柱导轨和滚针导轨。
③按受力情况可分为开式导轨和闭式导轨。
所谓开式导轨,是指靠外载荷和部件自重,使两导轨面在全长上保持贴合的导轨。
所谓闭式导轨,是指必须用压板作为辅助导轨面才能保证主导轨面贴合的导轨。
㈢导轨应满足的基本要求
机床导轨的质量在一定程度上决定了机床的加工精度、工作能力和使用寿命。
因此,导轨必须满足下列基本要求。
①导向精度是指运动部件沿导轨运动轨迹的直线度(对直线运动导轨)或圆度(对圆周运动的导轨)。
影响导向精度的主要因素有导轨
的几何精度、导轨的结构形式、导轨及其支承件的自身刚度和油膜刚度以及热变形等。
②精度保持性为了能长期保持导向精度,对导轨提出了刚度和耐磨性的要求。
若刚度不足,则直接影响部件之间的相对精度和导轨的导向精度,是导轨面上的比压分布不均,加剧导轨的磨损,所以刚度是导轨工作质量的一个重要指标。
导轨的耐磨性是决定导向精度能否长期保持的关键,是衡量机床质量的重要指标。
导轨耐磨性与导轨材料、导轨面的摩擦性质、导轨受力情况及两导轨相当运动速度等有关。
③低速运动平稳性就是要保证在做低速运动或微量位移时不出现不平稳现象。
进给运动的不平稳使加工表面粗糙读增大;定位运动的不平稳,将降低定位精度。
低速运动平稳性与导轨的结构和润滑,动、静摩擦系数的差值,以及传递导轨运动的传递系统的刚度等有关。
④结构工艺性在可能的情况下,应尽量是导轨结构简单,便于制造和维护。
对于刮研导轨,应尽量减少刮研量;对于镶装导轨,应做到更换容易。
㈣导轨的设计内容
1根据工作条件选择合适的导轨类型。
2根据导向精度要求和制造工艺性,选择导轨的截面形状。
3确定导轨的结构尺寸,保证导轨有足够的刚度,并使单位面积下压力小于许用值,以免导轨磨损过快。
4设计导轨磨损后的补偿调整装置,使导轨保持合理的间隙。
5选择合适的导轨材料、热处理方法、精加工方法等,保证导轨有足够的使用寿命。
6设计润滑系统,使导轨在良好的润滑条件下工作,减少摩擦及磨损。
7设计良好的防护装置,以防止切削脏物等进入导轨内。
8拟定导轨制造的技术要求。
㈤导轨的材料
导轨的材料有铸铁、钢、有色金属和塑料等。
对导轨材料的主要要求是:
耐磨性高、工艺性好和成本低等。
㈥导轨副材料的选用
在导轨副中,为了提高耐磨性和防止咬焊,动导轨和支承导轨应分别采用不同的材料。
如果采用相同的材料,也应采用不同的热处理使双方具有不同的硬度。
目前在滑动导轨副中,应用较多的是动导轨采用镶装氟塑料导轨软带,支承导轨采用淬火刚或淬火铸铁;其次是动导轨的精加工,可采用不淬火的耐磨铸铁导轨副。
只有移置导轨或不重要的导轨,才采用不淬火的普通灰铸铁导轨副。
在直线运动导轨中,长导轨用较耐磨的和硬度较高的材料制造。
这是因为:
1长导轨各处使用机会难以均等,磨损往往不均匀。
不均匀磨损对加工精度的影响较大。
因此,长导轨的耐磨性应该高一些。
短导轨磨损比较均匀,即使磨损大一些,对加工精度的影响也不太大。
2减少修理的劳动量。
短而软的导轨面容易刮研。
3不能完全防护的导轨都是长导轨,他露在外面,容易被刮伤。
㈦滑动导轨结构简介
⑴导轨的截面形状与组合
直线运动滑动导轨截面形状主要有三角形、矩形、燕尾形和圆形,并可互相组合,一对导轨副一凸一凹。
支承导轨为凸形,不易积存较大的切屑,但也不易存留润滑油,除用于进给导轨外,还可用于主运动导轨,但必须很好的防护,以免落入切屑和灰尘。
⑵导轨间隙的调整
导轨接合面间隙过小,不但增加运动阻力,而且会加速导轨磨损;若间隙过大,又会使导向精度降低,还容易产生振动。
因此,除装配过程中应仔细调整导轨的间隙外,再使用一段时间后,因磨损还需重调。
常用镶条和压板来调整导轨的间隙。
1压板压板用于调整间隙和承受颠覆力矩。
2镶条用来调整矩形和燕尾形导轨的侧面间隙,以保证导轨面的正常接触。
㈧滑动导轨的验算
⑴验算步骤
导轨的变形主要是接触变形,有时也应考虑导轨部分局部变形的影响。
导轨的设计,首先初步确定导轨的型式和尺寸,然后进行验算。
对于滑动导轨,应验算导轨的压强和压强的分布。
压强的大小直接影响导轨表面的耐磨性,压强的分布影响磨损的均匀性。
通过压强的分布还可以判断是否应采用压板,即决定导轨应采用闭式还是开式结构。
验算滑动导轨的步骤如下。
1受力分析导轨上所受的外力一般包括切削了、工件和夹具的重量、动导轨所在部件的重力和牵引了。
这些外力使各导轨面产生支反力和支反力矩。
牵引力、支反力、支反力矩都是未知力,一般可用静力平衡方程式求出。
当出现超静定时,可根据接触变形的条件建立附加方程式求各力。
首先建立外力矩方程式,然后依次求牵引力、支反力、和支反力矩。
2计算导轨的压强导轨的宽度远小于其长度。
因此在宽度方向,可以认为压强分布是均匀的。
这个假设使得导轨面的压强计算可以按一维问题处理。
每条导轨所受的载荷,都可以归接为一个支反力和一个支反力矩。
根据支反力可求出导轨的平均压强。
加入支反力矩的影响,就可以求出导轨的最大压强。
⑵导轨压强的分布
当导轨的自身刚度大于接触刚度时,可忽略导轨自身变形的影响,而只考虑接触变形的影响。
这时,沿导轨长度方向的接触变形和压强可视为线性分布,沿宽度方向可视为均匀分布。
当导轨的自身刚度较低时,既要考虑导轨表面接触变形,又要考虑导轨自身变形,这时压强为非线性分布。
下面只讨论线性分布的导轨压强的分析计算。
每条导轨面所受的载荷,都可最终归纳为一个其作用点距导轨中心距离为x的力F的作用。
这个力又等价于一个作用于导轨中心的力F和一个颠覆力矩M的作用。
在力F作用下,导轨面的压强
(单位为MPa):
=
在力F作用下,导轨面产生的压强(单位为MPa)
由于M=
aL
L=
a
因此
=
式中F-导轨承受的集中力,N;
M-导轨承受的颠覆力矩,N
mm
a-导轨的宽度,mm;
L-动导轨的长度,mm;
-集中力F引起的压强,MPa;
-颠覆力矩M引起的压强,MPa。
由于力F与力矩M同时作用,因此导轨所承受的最大、最小、平均压强分别为
4-1
4-2
4-3
从4-3式可见,平均压强
只与力F的大小和导轨几何尺寸有关,而与里的作用点无关。
从式(4-1),(4-2)可知:
1x=0,即力F作用于导轨中点,M=Fx=0时,
=
=
,压强呈矩形分布,导轨受力均匀,单实际上很难实现这种情况。
2x<L/6,即M=Fx<FL/6时,6M/FL<1,
=>,
<2
,压强呈梯形分布。
设计时,应尽可能保证导轨在这种受力状态下工作。
3x=L/6,即M=Fx=FL/6时,6M/FL=1,
=0,
=2
,压强呈三角形分布。
导轨两端压强分布相差较大,但仍保持了导轨面全长接触。
设计时可采用。
4x>L/6,即M=Fx>FL/6时,6M/FL>1,
<0。
这时,导轨一端将出现间隙。
为此,需要在导轨下面安装压板,形成辅助导轨面。
设计时应避免出现这种情况。
⑶导轨的许用压强
导轨的压强是影响导轨耐磨性的一个主要因素。
导轨的支承面积应与导轨所承受的载荷相适应。
如果导轨面的压强很大,导轨表面将因油膜压破而加剧磨损。
为此,应保证导轨面上的平均压强不超过许用值。
由于导轨面上的压强分布不可能完全均匀,所以还必须保证最大压强不超过许用值。
㈨导轨选用与计算
选用闭式双矩形导轨窄式凸式导轨,行程100mm,负载30kg工作台自重2kg。
动导轨选用灰铸铁HT200,长度L=120mm。
支承导轨选用45号中碳钢,整体淬火,HRC>48,属镶钢支承导轨,长度L=263mm宽度B=20mm.属低速进给运动导轨。
、
均小于许用压强(P)=1.2MPa
属低速进给运动导轨
⑷铸铁-钢的有润滑剂时的动摩擦系数u=0.05-0.15
铸铁-钢的静,动摩擦系数差为0.05
铸铁-钢的静摩擦系数u=0.1-0.2
静摩擦里F=32N-64N,取50
润滑油选用N46机械油,在油中加入能形成吸附膜的添加剂。
如在加如0.5%的油酸或0.3%的硬脂酸及1%的硬脂酸铝后,可使静、动摩擦系数茶将为接近于零
间隙的调整
用压板调整间隙,有平镶条调整侧向间隙。
防护:
用刮板式,选用毛毡。
技术要求
表面粗糙度支承导轨Ra=0.8
动导轨 Ra=1.6
第二节滚珠丝杠副的工作原理及特点
一.丝杠螺母机构的简介
丝杠螺母机构有称螺旋传动机构。
它主要用来将旋转运动变换为直线运动或将直线运动变换为旋转运动。
有以传递能量为主的(如螺旋压力机、千斤顶),也有以传递运动为主的(如工作台的进给丝杠),还有调整零件之间相当位置的螺旋传动机构等。
丝杠螺母机构有滑动摩擦机构和滚动摩擦机构之分。
滑动丝杠螺母机构结构简单、加工方便、制造成本低、具有自锁功能,但其摩擦阻力矩大、传动效率低(30%~40%)。
滚珠丝杠螺母机构虽然结构复杂、制造成本高,但其最大优点是摩擦阻力矩小、传动效率高(92%~98%),因此在机电一体化系统中得到广泛应用。
二.丝杠和螺母基本传动形式
⑴螺母固定、丝杠转动并移动,该传动形式因螺母本身起着支承作用,消除了丝杆轴承可能产生的附加轴向窜动,结构较简单,可获得较高的传动精度。
但其轴向尺寸不易太长,刚性较差。
因此只适用于行程较小的场合。
⑵丝杆传动、螺母移动,该传动形式需要限制螺母的传动,故需导向装置。
其特点是结构紧凑、丝杆刚性较好。
适用于工作行程较大的场合。
⑶螺母转动、丝杆移动,该传动形式需要限制螺母移动和丝杆的转动,由于结构复杂且占用轴向空间较大,故应用较少。
⑷丝杆固定、螺母转动并移动,该传动方式结构简单、紧凑,但在多数情况下,使用极不方便,故很少应用。
此外,还有差动传动方式,该方式的丝杆上有基本导程(或螺距)不同的两段螺纹,其旋向相同。
当丝杆转动时,可动螺母的移动距离为S=n×(l01-l02),如果两基本导程的大小相差较小,则可获得较小的位移S.因此,这种传动方式多用于各种微动机构中。
三.滚珠丝杠传动部件
⒈滚珠丝杠副的组成及特点
滚珠丝杠副是一种新型螺旋传动机构,其具有螺旋槽的丝杆与螺母之间装有中间传动元件-滚珠。
滚珠丝杠螺母机构由丝杆、螺母、滚珠和反向器等四部分组成。
当丝杆转动时,带动滚珠沿螺纹滚道滚动,为防止滚珠从滚道端面掉出,在螺母的螺旋槽两端设有滚珠回程引导装置构成滚珠的循环返回通道,从而形成滚珠流动的闭和通路。
滚珠丝杠副与滑动丝杠副相比,除上述优点外,还具有轴向刚度高(既通过适当遇紧可消除丝杠与螺母之间的轴向间隙)、运动平稳、传动精度高、不易磨损、使用寿命长等优点。
但由于不能自锁,具有传动的可逆性,在用作升降传动机构时,需要采取制动措施。
⒉滚珠丝杠副的典型结构类型
滚珠丝杠副的结构类型可以从螺纹滚道的截面形状、滚珠的循环方式和消除轴向间隙的调整方法进行区别。
⑴螺纹滚道型面(法向)的形状及主要尺寸
我国生产的滚珠丝杠副的螺纹滚道有单圆弧型和双圆弧型,滚道型面与滚珠接触点之法线与丝杠轴向之垂线间的夹角β称为接触角,一般为45。
。
单圆弧型的螺纹滚道的接触角随轴向载荷大小的变化而变化,主要由轴向载荷所引起的接触变形的大小而定。
β大时,传动效率、轴向刚度以及承载能力也随之增大。
由于单圆弧滚道加工用砂轮成型较简单,故容易得到较高的加工精度。
单圆弧型面的滚道圆弧半径R稍大于滚珠半径rb。
双圆弧型的螺纹滚道的接触角β在工作过程中基本保持不变。
两圆弧相交处有一个空隙,可使滚道底部与滚珠不接触,并能存储一定的润滑油以减少摩擦磨损。
由于对加工其型面的砂轮进行修整和加工、检验均较困难,故加工成本较高。
⑵滚珠的循环方式
滚珠丝杠副中滚珠的循环方式有内循环和外循环两种。
内循环方式的滚珠在循环过程中始终与丝杆表面接触。
在螺母的侧面孔内装有接通相邻滚道的反向器,利用反向器引导滚珠越过丝杆的螺纹顶部进入相邻滚道,形成一个循环回炉。
一般在同一螺母上装有2-4个滚珠用反向器,并沿螺母圆周均匀分布。
内循环方式的优点是滚珠循环的回路短、流畅性好、效率高、螺母的径向尺寸也较小。
其不足是反向器加工困难、装配调整也不方便。
浮动式反向器的内循环滚珠丝杠副。
其结构特点是反向器上的安装孔有0.01mm—0.015mm的配合间隙,反向器弧面上加工有圆弧槽,槽内安装拱形片簧,外有弹簧套,藉助拱形片簧的弹力,始终给反向器一个径向推力,使位于回珠圆弧槽内的滚珠与丝杆表面保持一定的压力,从而是槽内滚珠代替了定位键而对反向器起到自定位作用。
这种反向器的优点是在高频浮动中达到回珠圆弧槽进出口的自动对接,通道流畅、摩擦特性较好,更适用于高速、高灵敏度、高刚性的精密进给系统。
外循环方式中的滚珠在循环返向时,离开丝杆螺纹滚道,在螺母体内或体外作循环运动。
从结构上看,外循环有一下三种形式:
①螺旋槽式在螺母的外圆表面上铣出螺纹凹槽,槽的两端钻出两个与螺纹滚道相切的通孔,螺纹滚道内装入两个挡珠器引导滚珠通过两个孔,应用套筒盖住凹槽,构成滚珠的循环回路。
这种结构的特点是工艺简单、径向尺寸小、易于制造。
但是挡珠器刚性差、易磨损。
②插管式用一弯管代替螺纹凹槽,弯管的两端插入与螺纹滚道相切的两个内孔,用弯管的端部引导滚珠进入弯管,构成滚珠的循环回路,再用压板和螺钉将弯管固定。
插管式结构简单、容易制造。
但是径向尺寸较大,弯管端部用作挡珠器比较容易磨损。
③端盖式在螺母上钻出纵向孔作为滚子回程滚道,螺母两端装有两块扇形盖板或套筒,滚动的回程道口就在盖板上。
滚道半径为滚珠直径的1.4-1.6倍。
这种方式结构简单、工艺性好,但滚道吻合弯曲处圆角不易准确制作而影响起性能,故应用较少。
常以单螺母形式用作升降传动机构。
四.滚珠丝杠副的主要尺寸参数
滚珠丝杠副的主要尺寸参数有:
公称直径d0:
它指滚珠与螺纹滚道在理论接触角状态时包络滚珠球心的圆柱直径。
它是滚珠丝杠副的特征尺寸
基本导程l0:
它指丝杆相对于螺母旋转2π弧度时,螺母上基准点的轴向位移。
行程l:
它指丝杆相对于螺母旋转任意弧度时,螺母上基准点的轴向位移。
此外还有丝杆螺纹大径d、丝杆螺纹小径d1、滚珠直径db、螺母螺纹大径D、螺母螺纹小径D1、丝杆螺纹全长ls等。
五.滚珠丝杠副轴向间隙的调整与预紧
滚珠丝杠副在负载时,起滚珠与滚道面接触点处将产生弹性变形。
换向时,起轴向间隙会引起空回,这种空回是非连续的,既影响传动精度,又影响系统的稳定性。
单螺母丝杠副的间隙消除相当困难。
实际应用中,常采用以下几种调整预紧方法。
⑴双螺母螺纹预紧调整式
螺母的外端有凸缘,而螺母的外端虽无凸缘,但制有螺纹,并通过两个圆螺母固定。
调整时旋转圆螺母2消除轴向间隙并产生一定的预紧力,然后用锁紧螺母1缩紧。
预紧后两个螺母中的滚珠相向受力,从而消除轴向间隙。
其特点是结构简单、刚性好、预紧可靠,使用中调整方便,但不能精确定量地进行调整。
⑵双螺母齿差预紧调整式
两个螺母的两端分别制有圆柱齿轮,二者齿数相差一个齿,通过二端的两个内齿轮与上述圆柱齿轮相啮合并用螺钉和定位销固定在套筒上。
调整时先取下二端的内齿轮,当二个滚珠螺母相对于套筒同一方向转动同一个齿后固定后,则一个滚珠螺母相对于另一个滚珠螺母产生相对角位移,使而个滚珠螺母产生相当移动,从而消除间隙并产生一定的预紧力。
其特点是可实现定量调整即可进行精密微调,使用中调整较方便。
⑶双螺母垫片调整预紧式
调整垫片的厚度,可使两螺母产生相当位移,以达到消除间隙、产生预紧拉力之目的。
其特点是结构简单刚度高、预紧可靠,但使用中调整不方便。
六.滚珠丝杠副支承方式的选择
实践证明,丝杠的轴承组合及轴承座以及其它零件的连接刚性不足,将严重影响滚珠丝杠副的传动精度和刚度,因为,在设计安装时应认真考虑。
为了提高轴向刚度,常用以止推轴承为主的轴承组合来支承丝杠,当轴向载荷较小时,也可用角接触球轴承来支承丝杠。
常用轴承的组合方式有以下几种。
1单推-单推式止推轴承分别装在滚珠丝杠的两端并施加预紧力。
其特点是轴向刚度较高,预拉伸安装时,预紧力较大,但轴承寿命比双推―双推式低。
2双推-双推式 两端分别安装止推轴承与深够球轴承的组合,并施加预紧力,其轴向刚度较高。
该方式适合于高刚度、高转速、高精密的精密丝杠传动系统。
但随温度的升高会使丝杠的预紧力增大,易造成两端支承的预紧力不对称。
3双推-简支式 一端安装止推轴承与深够球轴承的组合,另一端仅安装深够球轴承,其轴向刚度较低,使用时应注意减少丝杠热变形的影响。
双推端可预拉伸安装,预紧力小,轴承寿命较高,适合于中速、传动精度较高的