筒形件落料拉深冲孔模具课程设计.docx
《筒形件落料拉深冲孔模具课程设计.docx》由会员分享,可在线阅读,更多相关《筒形件落料拉深冲孔模具课程设计.docx(23页珍藏版)》请在冰豆网上搜索。
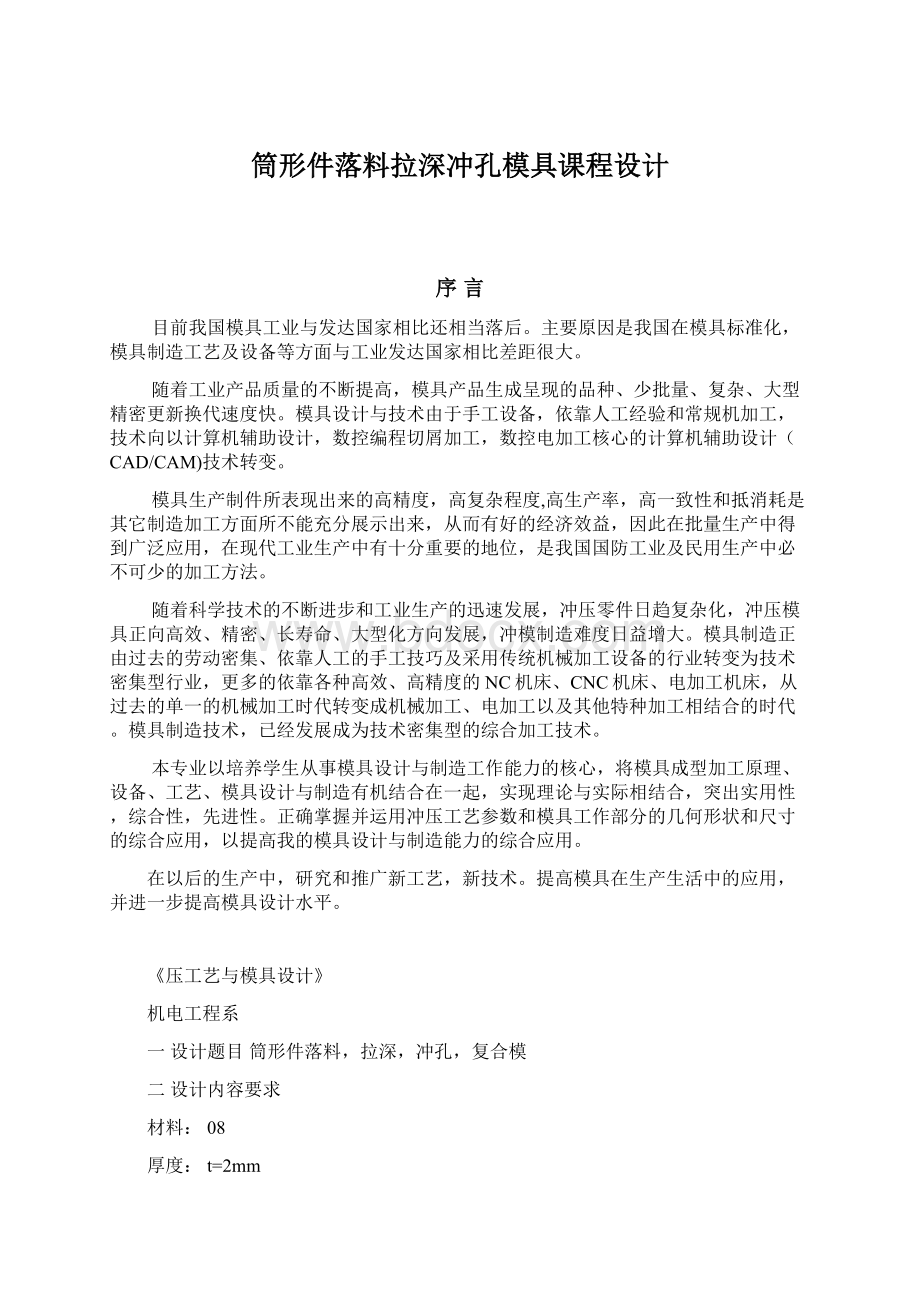
筒形件落料拉深冲孔模具课程设计
序言
目前我国模具工业与发达国家相比还相当落后。
主要原因是我国在模具标准化,模具制造工艺及设备等方面与工业发达国家相比差距很大。
随着工业产品质量的不断提高,模具产品生成呈现的品种、少批量、复杂、大型精密更新换代速度快。
模具设计与技术由于手工设备,依靠人工经验和常规机加工,技术向以计算机辅助设计,数控编程切屑加工,数控电加工核心的计算机辅助设计(CAD/CAM)技术转变。
模具生产制件所表现出来的高精度,高复杂程度,高生产率,高一致性和抵消耗是其它制造加工方面所不能充分展示出来,从而有好的经济效益,因此在批量生产中得到广泛应用,在现代工业生产中有十分重要的地位,是我国国防工业及民用生产中必不可少的加工方法。
随着科学技术的不断进步和工业生产的迅速发展,冲压零件日趋复杂化,冲压模具正向高效、精密、长寿命、大型化方向发展,冲模制造难度日益增大。
模具制造正由过去的劳动密集、依靠人工的手工技巧及采用传统机械加工设备的行业转变为技术密集型行业,更多的依靠各种高效、高精度的NC机床、CNC机床、电加工机床,从过去的单一的机械加工时代转变成机械加工、电加工以及其他特种加工相结合的时代。
模具制造技术,已经发展成为技术密集型的综合加工技术。
本专业以培养学生从事模具设计与制造工作能力的核心,将模具成型加工原理、设备、工艺、模具设计与制造有机结合在一起,实现理论与实际相结合,突出实用性,综合性,先进性。
正确掌握并运用冲压工艺参数和模具工作部分的几何形状和尺寸的综合应用,以提高我的模具设计与制造能力的综合应用。
在以后的生产中,研究和推广新工艺,新技术。
提高模具在生产生活中的应用,并进一步提高模具设计水平。
《压工艺与模具设计》
机电工程系
一设计题目筒形件落料,拉深,冲孔,复合模
二设计内容要求
材料:
08
厚度:
t=2mm
硬度:
60—64HRC
实体图
第一部分冲压成形工艺设计
Ⅰ明确设计任务,收集相关资料
冲压工艺设计应在收集﹑调查﹑研究并掌握有关设计设计的原始资料的基础上的基础上进行,做到有的放矢,避免盲目性。
工艺设计的原始资料主要包括如下内容:
⑴冲压件的产品图及技术要求
零件图如设计任务书中所示的零件图。
技术条件应明确合理。
由此可对拉深件的结构,尺寸大小,精度要求以及装配关系,实用性能等有全面了解,以便制定工艺方案,选择模具类型和确定模具精度。
⑵生产类型
生产类型是企业生产产业程度的分类,一般分为大量生产、成批生产、、小批量生产。
根据生产纲领和产品零件的特征或工作的每月担负的工序数查文献表1-3生产类型和生产纲领的关系,确定该零件的生产类型为大批量生产。
⑶生产组织形式
生产类型不相同,零件和产品的组织形式,采用的技术措施和达到的技术经济效果会不同。
因为该零件是大批量生产,所以其生产类型查文献【1】表1-5的各种生产类型的工艺性,特征其生产组织形式为零件的互换性,有修配法、钳工修配、缺乏互换性、毛坯的制造方法和加工余量、手工造型或自由锻造毛坯精度低,加工余量大。
⑷工艺装备
大批量的的采用专用夹具,标准附件,标准刀具和万能量具,靠划线和试切法达到精度要求。
Ⅱ冲压工艺性分析
1材料08钢是优质碳素结构刚,易于拉伸成形,具有良好的冲压性能
2工件结构该工件为圆形带孔拉深件,拉伸高度不大,孔在底部并且不在拉深变形区
3尺寸精度零件图上工件高度8孔Φ30+0.210。
工件外轮廓Φ39,一般冲压均能满足精度要求。
Ⅲ制定冲压工艺方案
1工序性质和数量
(1)工序性质的确定
在冲压加工中,工序性质是指冲压件所需的工序种类,剪裁,落料,冲孔,切边等使材料产生分离的工序。
弯曲拉深局部成形等使材料产生变形的工序。
冲压工序性质的确定主要取决于冲压件的形状尺寸和精度要求。
同时还应考虑冲压变形规律及某些具体条件的限制。
通常在确定工序性质时应当考虑以下几方面:
1)从零件图上直观的确定工序性质,平板件冲压加工时常采用剪裁,落料,冲孔等冲裁工序。
当平面度要求较高时采用较平的工序进行精压,当零件的断面质量尺寸精度要求较高时,需增加修整工序或采用精密冲裁工艺进行加工。
2)对零件图进行计算分析,比较后确定工序性质。
3)为改善冲压变形条件,方便工序定位,增加附加工序。
预冲工序工艺切口达到改善冲压变形条件,提高成型质量母的。
根据零件图分析冲压加工时须用落料,冲孔,拉深,翻边等工序。
(2)工序数量的确定
确定工序数量的基本原则是:
在保证工件质量,生产率和经济性要求的前提下,工序数量应尽可能地减少。
该零件精度要求较高,故采用复合模。
2工序顺序和组合
(1)工序顺序
各工序的安排主要取决于冲压变形规律和零件质量要求。
工序顺序的安排一般应注意以下几方面:
1)所有的孔只要其形状和尺寸不受后续工续的影响,都应在平板坯料上冲出。
2)所在位置会受到以后某工序变形的影响的孔,一般都应在有关的成型工序完成后再冲孔。
3)孔靠近或孔边缘较小时,如果模具强度够高,最好同时冲出。
否则应先冲出大孔和一般精度孔,后冲出小孔和高精度孔或者先落料再冲孔,力求把可能产生的畸变限制在最小范围内。
4)如果在同一个零件的不同位置冲压时,变形区域互相不发生作用,根据模具结构定位和操作的过程难易程度来确定。
5)多角弯曲件主要从材料变形核材料的运动两方面安排弯曲的顺序。
一般是先弯外部角后弯内部角,弯角根据零件图先冲裁后落料,由固定挡料销定位。
(2)工序组合方式选择
冲压工序的组合是指将两个或两个以上的工序分析合并在一道工序内完成。
减少工序及占用的模具设备和数量,提高效率和冲压件的精度,在确定工序组合时,首先应考虑组合的必要性和可行性,然后再决定是否组合。
1)工序组合的必要性主要取决于冲压件的生产批量。
2)工序的组合的可行性受到多种因素的限制,应保证能冲压出形状、尺寸和精度均符合要求的图样,实现其所需动作保证有足够的强度与现有的冲压设备条件相适应。
根据零件图的要求及批量采用落料,拉深,冲孔,切边复合模。
3冲压工艺方案
(1)工艺方案
该工件包括落料,拉深,冲孔,切边四个基本工序,可以有以下三种工艺方案。
方案一:
先落料,再拉深,然后冲孔,最后切边。
采用单工序模生产。
方案二:
落料-拉深-冲孔-切边复合冲压。
采用复合模生产。
方案三:
落料-拉深-冲孔-切边连续冲压。
采用连续模生产。
(2)工艺方案分析
方案一模具结构简单,但需四道工序,即需要落料模,拉深模,冲孔模,切边模四副模具,生产效率低,难以满足该零件的年产量要求。
方安二只需一副模具,冲压件的形位精度和尺寸精度易保证,且生产效率也高。
尽管模具结构较方案一复杂,但由于零件的几何形状简单对称,模具制造并不困难。
方案三也只需一副模具,生产效率也很高,但零件的冲压精度稍差。
欲保证冲压件的形位精度,需在模具上设置导正销导正,故其模具制造,安装较复合模复杂。
通过对上述三种方案的分析比较,该件的冲压生产采用方案二为佳。
Ⅳ确定毛坯形状,尺寸和主要参数计算
1毛坯尺寸计算
该工件位无凸缘圆筒形件,根据等面积原则采用解析法求毛坯直径。
如图1所示,将工件分为三个简单的几何体。
图1
1毛坯尺寸
1确定是否加修边余量
由于坯料的各向异性和模具间隙不均等因素的影响,拉深后工件的边缘不整齐,甚至出现突耳,需在拉深后进行修边,所有在计算坯料直径时,要确定是否需要增加修边余量。
零件的相对高度h/d=(8+1)/(39-2)=0.243,而高度h﹤10mm,根据文献[1]查表4-3可知,修边余量δ=1㎜
1)计算毛坯直径
D=
d1=39-(1.5+2)×2=32㎜,
d2=39-2=37㎜,δ=1㎜,
h=10-1.5-2=6.5㎜,rg=1.5+1=2.5㎜
D=51.83mm
取D=55㎜
2)确定是否需要压边圈
根据坯料相对厚度:
t/d×100=2/55×100=3.64>2
式中t——坯料厚度,㎜
D——毛坯直径,㎜
查文献【1】P185表5-1可知
不用压边圈,若怕该冲件在拉深过程中会发生起皱,保险起见,采用带弹性压边装置的模具也可。
这里的压边圈实际上是作为定位与顶件之用。
2确定拉深次数
由于拉深件的高度与其直径的比值不同,有的拉深件科研用一次拉深制成,而有的高度大的拉深件,则需要多次拉深才能制成。
所有根据工件的相对高度(h/d)和坯料的相对厚度(t/D×100)的大小确定拉深次数。
查表可知,由于工件相对高度0.35远远小于一次拉深时的相对高度0.70~0.57,则可一次拉深成形。
也可根据相对厚度查表确定出筒形件(带压边圈)极限拉深系数m=0.53~0.55,而工件的拉深系数为h/d=9/37=0.243>m则可一次拉成。
3排样及材料利用率
(1)排样方法
冲裁件在板料,带料或条料上的布置方法称为排样。
合理的排样是将低成本和保证冲件质量及模具寿命的有效措施。
应考虑以下原则:
1〉提高材料得利用率(不影响冲件的使用性能的前提下可适当改变冲件形状)。
2〉合理排样可使操作方便,劳动强度低。
3〉模具结构简单寿命长。
4〉保证冲件质量和冲件对板料纤维方向的要求。
A:
根据零件图可选用少废料的利用率情况,排样有三种:
a有废料排样b少废料排样c无废料排样
根据零件图可选用少废料排样。
沿冲件部分外形切断或冲裁。
只有在冲件与冲件之间或冲件与条料侧边之间留有搭边。
这种排样利用率高,用于某些精度要求不是很高的冲裁件排样。
B:
排样的形式分为直排式,斜排式,直对排,斜对排,混合排等。
根据零件的形状和排样方法确定为直排排样。
如图2所示
图2
(2)搭边与料宽
1〉搭边
排样中相邻两个零件之间的余量或零件与条料边缘件的余量称为搭边。
其作用时补偿定位误差,保持条料有一定的刚度,以保证零件质量和送料方便。
由排样图知搭边值a=a1=1.5
式中a——侧面搭边值
a1——冲件之间的搭边值
搭边值的大小与下列因素有关:
a材料的力学性能b材料的厚度c零件的外形和尺寸d排样方法e送料及挡料方式
2〉送料步距和条料宽度的确定
a.送料步距
条料在模具上每次送进的距离称为送料步距(简称步距或进距)其大小应为条料上两个对应冲裁件的对应点之间的距离。
b.条料宽度
条料宽度的确定原则:
最小条料宽度要保证冲裁件零件周边有足够的搭边值。
最大条料宽度要能在冲裁时顺利在导料板之间送行并与导料板之间有一定的间隙。
根据零件图要求,导料板之间无测压装置。
送料进距:
s=D+a1=55+1.5mm=56.5mm
条料宽度:
b=D+2a=55+2×1.5mm=58mm
式中D——平行于送料方向冲裁件的宽度
3〉裁板方法
板料规格选用2mm×1000mm×3000mm
每张钢板裁板条数n1:
为了操作方便,采用横裁,即
n1=3000/58=51条余42mm
每条裁板上的工件数n2
n2=(B-a1)/s=(1000-1.5)/56.5=17个
式中B——钢板宽度(每条裁板的长度)1000mm
每张钢板上的工件总数:
n总=n1×n2=51×17=867个
(3)材料的利用率
衡量材料的经济利用率的指标是材料的利用率
=(n总×πD2)/(4L×B)x100%=(867×3.14×552)/(4×3000×1000)×100%
=74.3%
第二部分冲压模具设计
Ⅰ确定冲模类型机结构形式
在冲压工艺性分析后拟定冲压工艺方案时选择复合模,又因零件的几何形状简单对称,工件间无搭边