多孔陶瓷的制备技术.docx
《多孔陶瓷的制备技术.docx》由会员分享,可在线阅读,更多相关《多孔陶瓷的制备技术.docx(11页珍藏版)》请在冰豆网上搜索。
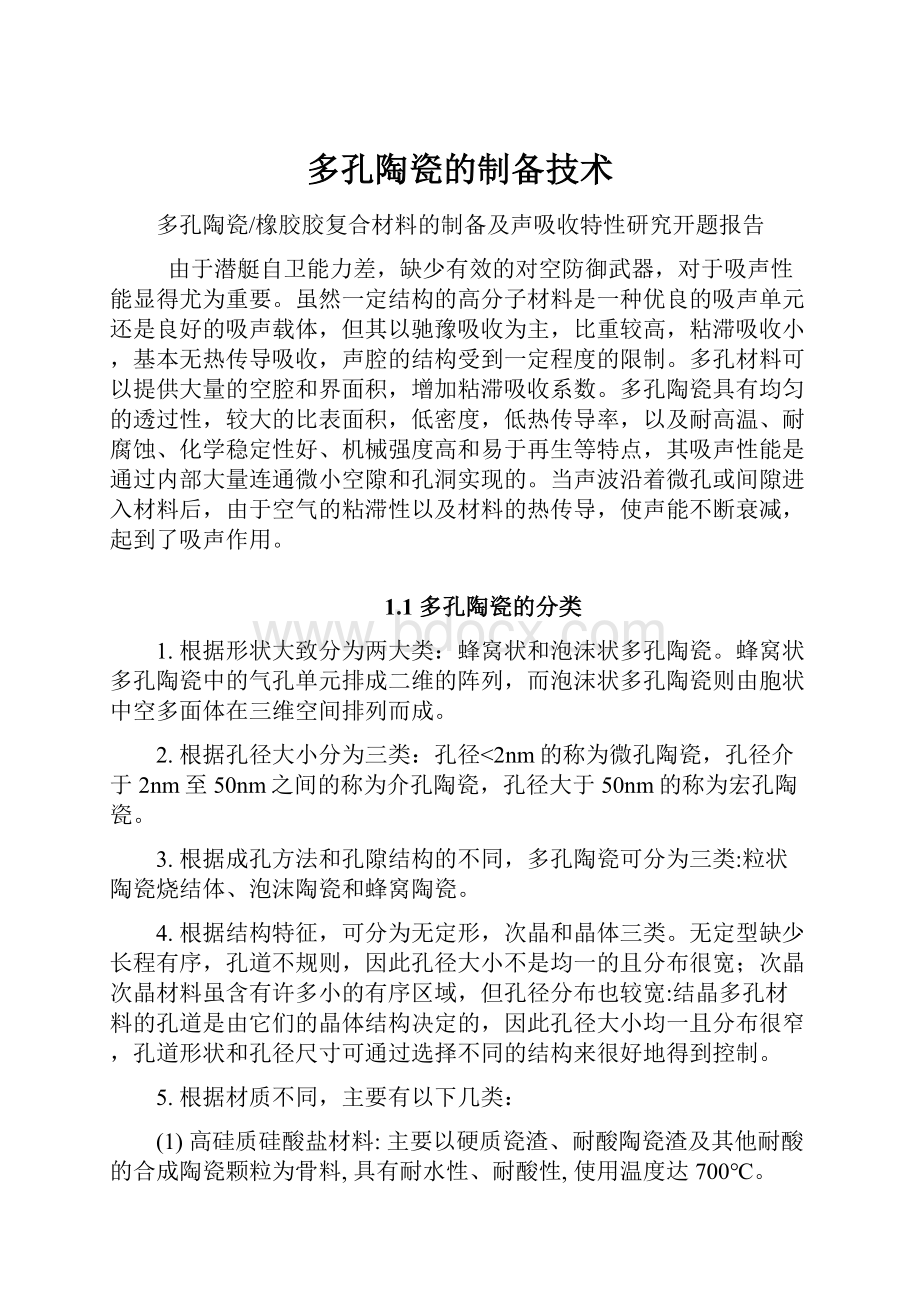
多孔陶瓷的制备技术
多孔陶瓷/橡胶胶复合材料的制备及声吸收特性研究开题报告
由于潜艇自卫能力差,缺少有效的对空防御武器,对于吸声性能显得尤为重要。
虽然一定结构的高分子材料是一种优良的吸声单元还是良好的吸声载体,但其以驰豫吸收为主,比重较高,粘滞吸收小,基本无热传导吸收,声腔的结构受到一定程度的限制。
多孔材料可以提供大量的空腔和界面积,增加粘滞吸收系数。
多孔陶瓷具有均匀的透过性,较大的比表面积,低密度,低热传导率,以及耐高温、耐腐蚀、化学稳定性好、机械强度高和易于再生等特点,其吸声性能是通过内部大量连通微小空隙和孔洞实现的。
当声波沿着微孔或间隙进入材料后,由于空气的粘滞性以及材料的热传导,使声能不断衰减,起到了吸声作用。
1.1多孔陶瓷的分类
1.根据形状大致分为两大类:
蜂窝状和泡沫状多孔陶瓷。
蜂窝状多孔陶瓷中的气孔单元排成二维的阵列,而泡沫状多孔陶瓷则由胞状中空多面体在三维空间排列而成。
2.根据孔径大小分为三类:
孔径<2nm的称为微孔陶瓷,孔径介于2nm至50nm之间的称为介孔陶瓷,孔径大于50nm的称为宏孔陶瓷。
3.根据成孔方法和孔隙结构的不同,多孔陶瓷可分为三类:
粒状陶瓷烧结体、泡沫陶瓷和蜂窝陶瓷。
4.根据结构特征,可分为无定形,次晶和晶体三类。
无定型缺少长程有序,孔道不规则,因此孔径大小不是均一的且分布很宽;次晶次晶材料虽含有许多小的有序区域,但孔径分布也较宽:
结晶多孔材料的孔道是由它们的晶体结构决定的,因此孔径大小均一且分布很窄,孔道形状和孔径尺寸可通过选择不同的结构来很好地得到控制。
5.根据材质不同,主要有以下几类:
(1)高硅质硅酸盐材料:
主要以硬质瓷渣、耐酸陶瓷渣及其他耐酸的合成陶瓷颗粒为骨料,具有耐水性、耐酸性,使用温度达700℃。
(2)铝硅酸盐材料:
以耐火粘土熟料、烧矾土、硅线石和合成莫来石质颗粒为骨料,具有耐酸性和耐弱酸性使用温度达1000℃。
(3)精陶质材料:
组成接近第一种材料,以多种粘土熟料颗粒与粘土等混合,得到微孔陶瓷料。
(4)硅藻土质材料:
主要以精选硅藻土为原料,加粘土烧结而成,用于精滤水和酸性介质。
(5)纯碳质材料:
以低灰分煤或石油沥青焦颗粒,或者加入部分石墨,用稀焦油粘结烧制而成,用于耐水、冷热强酸、冷热强碱介质以及空气消毒、过滤等。
(6)刚玉和金刚砂材料:
以不同型号的电熔刚玉和碳化硅颗粒为骨料,具有耐强酸、耐高温特性,耐温可达1600℃。
(7)堇青石、钛酸铝材料:
因其热膨胀系数小,广泛用于热冲击的环境。
(8)以其他工业废料,尾矿以及石英玻璃或者普通玻璃构成的材料,视原料组成的不同具有不同的应用。
1.2多孔陶瓷的发展历史及研究状况
1.2.1国外主要研究状况
国外对多孔陶瓷的研究较早,1935年,Ewell等(13]人最早提出溶胶一凝胶法,但真正在陶瓷制备中使用这种方法是在1952年左右。
当时,Roy利用这种方法制备了多种陶瓷材料,并把这种方法定名为“Sol-gel"。
1956年,Uh11I等人采用阳极氧化方法首次制得了多孔硅。
1963年,Schwartzwalde等人最早提出了用泡沫塑料浸演法制备多孔材料,过去该材料主要用作过滤器。
1973年,Sunderman等[(;〕人用氧化钙、氢氧化钙、硫酸铝和双氧水作发泡剂,率先发明了发泡工艺,该法首先将经过预处理的球形粘土颗粒放在模子中,于900^'1000℃的氧化气氛下加热,在压力作用下使粘土颗粒相互粘结,当足够的热传到粘土颗粒内部时,材料发泡充满整个模子,冷却后获得多孔陶瓷材料。
1978年美国人F.R.Mollard和N.Davidson等人首先利用氧化铝、高岭土等陶瓷原料制成多孔陶瓷用于铝合金铸造过滤,可以显著提高铸件质量,降低废品率。
1988年O.Lyckfeldt等人则用淀粉同时作为粘结剂和造孔剂,制备出气孔率在23%-70%、孔径在1微米-80微米的多孔氧化铝,发明了一种简单而又经济的工艺方法。
1992年,Dauscher等人以Ti[OCHCCH3)2]4和CeCl3.7H20为原料,用溶胶一凝胶法制备了Ti02-Ce02复合材料多孔陶瓷,标志着溶胶一凝胶的应用已不仅局限在制备单质多孔材料。
Kresge等人首次在Nature上报道了一类以硅铝酸盐为基的新颖得介孔氧化硅材料M41S,其中以命名为MCM41的材料最引人注目,从而将分子筛的规则孔径从微孔范围拓展到介孔领域。
1.2.2国内研究状况
我国于80年代初期开始研制多孔陶瓷,1988年,孙鸿涛等人采用外加石墨为造孔剂制备了多孔钻铁氧陶瓷,具有稳定的力学性能、物化性能和电气性能。
1993年,吴皆正等人用十二烷基磺酸钠和碳酸钙为发泡剂,以石英为原料,制备出了显气孔率在3555%,平均孔径8-60微米,具有狭窄的孔径分布(PSD)和一定强度的可控微米级多孔陶瓷。
1994年,彭长琪等人以天然石英为骨料,选择合适的助剂和烧成制度制备了气孔率为35%-45%,孔径为5-30微米,适用于过滤液体、气体、蒸气的石英质多孔陶瓷。
1995年,吴国安采用溶胶一凝胶法制备了孔径约为3Onm,孔径分布窄,孔隙率30%左右的TiO2多孔陶瓷膜。
多孔陶瓷的制备技术。
1996年,曾庭英等人制取了多种纳米级微孔玻璃球;他们还采用不同的条件用溶胶-凝胶法住的了孔径分布范围在1-20纳米之间的微孔玻璃粉,可用作纳米级微孔基质载体。
1997年,奚红霞等人以异丙醇铝为原料,用溶胶一凝胶技术在多孔陶瓷管上制备了中孔膜稳定性好、孔径分布均匀的v-Ab03膜。
1998年,龚森蔚等[[46]人采用聚甲基丙烯甲酷作为造孔剂制备了孔径可控的经基磷灰石复相陶瓷。
薛明俊等人用溶胶一
凝胶工艺制备了氧化铝多孔陶瓷。
方国家等人以TEOS和无水乙醇为主要原料,制备了纳米微孔Si02薄膜,研究了合成工艺条件及浓H2SOa表面修饰对Si02多孔膜气孔率和稳定性的影响。
1999年,姚秀敏等人以碳粉为造孔剂,研究了多孔羟基磷灰石陶瓷的制备方法及性能。
2000年,唐竹兴等人采用90年代初发明的注凝成型技术制备微孔梯度陶瓷材料,通过研究实现了孔梯度陶瓷材料一次烧成,制备了结合强度高、粒度及孔径在横向方向呈均勾分布,在纵向方向呈梯度分布的孔梯度陶瓷材料。
2001年,赵俊亮等人以羟基磷灰石粉、生物玻璃粉为浆料,以硅溶胶作溶剂和粘结剂,以羟甲基纤维素作流变剂,采用有机
泡沫浸演法制备了孔径为450-500微米,孔径均匀、孔隙连通的多孔羟基磷灰石生物活性复相陶瓷。
1.3多孔陶瓷制备方法
多孔陶瓷的制备方法很多,从性质上来说,则分为物理方法和化学方法,下面从这两个角度来说明其制备工艺。
1.3.1物理方法
1.3.1.1有机泡沫浸渍(Polymericsponge)工艺
有机泡沫体浸渍工艺是Schwartzwalder在1963年发明的,它是凭借有机泡沫体所具有的开孔三维网状骨架的特殊结构,将制备好的料浆均匀地涂覆在有机泡沫网状基体上,干燥后烧掉有机泡沫体而获得一种网眼多孔陶瓷。
该法适于制备高气孔率,开气孔的多孔陶瓷。
其具体工艺流程如图1。
图1 有机泡沫体浸渍工艺流程图
有机泡沫的选择,陶瓷浆料的制备以及多余浆料的移去是此法的关键步骤。
(1)有机泡沫的选择
多孔体的尺寸主要取决于有机泡沫体的尺寸,与浆料在有机泡沫体上的涂覆厚度也有一定的关系。
用作模板的有机泡沫材料一般是经过特定发泡工艺制作的聚合海绵,材质常为聚氨基甲酸已酸(聚氨酯)、聚氯乙烯、聚苯乙烯、胶乳、纤维素等。
由于开孔有机泡沫塑料的孔尺寸决定了多孔陶瓷的孔尺寸(通常为2~25pores/cm长),所以应根据制品对气孔大小、气孔率高低来选择合适的有机泡沫塑料。
(2)陶瓷浆料的制备
浆料的基本组成是陶瓷颗粒、水和添加剂。
陶瓷颗粒的成分选择取决于多孔陶瓷制品的具体用途。
颗粒的大小一般应小于100Lm,最好是小于45Lm,水的用量为10240%。
添加剂主要有粘结剂、流变化剂、反泡沫剂、絮凝剂。
粘结剂主要用来提高干坯的强度,防止在有机泡沫气化过程中倒塌。
最常用的有硅酸盐、磷酸盐、硼酸盐等及胶化的Al(OH)3和SiO2胶体。
此外,还可以使用有机粘结剂。
流变化剂则用来提高浆料的触变性,以便浸渍时使浆料在进入泡沫,并均匀地涂在泡沫网上后有足够的粘度保持在泡沫中。
流变化剂主要是一些天然的粘土,用量一般为01121.5%。
反泡沫剂的加入是为了防止浆料起泡,多用低分子量的醇或树脂等。
絮凝剂则用于改善浆料与有机泡沫之间的粘结性,主要有聚乙二胺等。
(3)浸渍及多余浆料的移去
有机泡沫浸渍浆料的目的是挤压泡沫使泡沫中的空气排出,把泡沫浸入桨料中,多次重复该过程,直至最终达到所要求的比重。
泡沫渍上浆料后,下一步是去掉多余的浆料,最简单的方法是用两块木板挤压浸渍了浆料的泡沫,但大批量生产则可用离心机或滚轧机等设备来完成。
辊压法除浆示意图如图5所示。
这种特殊结构使其作为过滤材料具有以下优点:
①通过流体时,压力损失小;②表面积大和流体接触效率高;③重量轻。
该类多孔陶瓷被用于流体过滤尤其是熔融金属过滤时,与传统的使用陶瓷颗粒烧结体、玻璃纤维布相比,不但操作简单、节省能源、成本降低,而且过滤效率较高。
除了用于熔融金属等流体过滤外,它还可用作高温烟气的处理、催化剂载体、固体热交换器和电极材料等。
该工艺特别适合制备孔径为100μm~5mm的高气孔率网眼陶瓷,而且工艺简单,从而成为一种非常重要的制备工艺。
朱新文等人先选用软质聚氨酯海绵制备出一种具有高气孔率且几乎没有堵孔的网眼预制体,然后通过对预制体的涂覆处理可得到结构非常均匀的网眼陶瓷。
实验表明,通过控制涂覆次数可实现对其孔径大小、相对密度的调节,为网眼陶瓷孔结构的精确设计提供了一种新工艺。
而赵俊亮等人以羟基磷灰石粉、生物玻璃粉为浆料,以硅胶作溶剂和粘结剂,以羧甲基纤维素作流变剂,聚氨酯海绵作为载体制备了孔径约450-500微米、孔径均匀、孔隙连通的多孔羟基磷灰石生物活性复相陶瓷。
1.3.1.2添加造孔剂工艺
添加造孔剂工艺是通过在陶瓷配料中添加造孔剂,利用造孔剂在坯体中占用一定的空间,然后经烧结除去造孔剂从而生成气孔来制备多孔陶瓷。
其工艺流程如图6所示。
图6添加造孔剂工艺流程图
造孔剂加入的目的在于促使气孔率增加,必须满足下列要求:
在加热过程中易于除去;排除后在基体中无有害残留物;不与基体反应。
其优点在于通过优化造孔剂的形状、粒径和制备工艺条件能精确地设计气孔的形状、尺寸和气孔率,但其缺点是难以获得高气孔率制品(一般不超过50%),而且气孔分布的均匀性也较差。
(1)造孔剂种类和用量的选择
造孔剂的种类有无机和有机二类。
无机造孔剂有碳酸铵、碳酸氢铵、氯化铵等高温可分解盐类,以及其它可分解化合物如Si3N4或无机碳如煤粉、碳粉等。
有机造孔剂主要是一些天然纤维、高分子聚合物和有机酸等,如锯末、萘、淀粉、及聚乙烯醇、尿素、甲基丙烯酸甲脂、聚氯乙烯、聚苯乙烯等。
造孔剂颗粒的大小和形状决定了多孔陶瓷材料气孔的大小和形状。
造孔剂添加量不同,不仅直接影响最终多孔陶瓷的气孔率,而且随造孔剂添加量增加,多孔Al2O3的平均孔径和最大孔径都将增大,因此也提高了其透气系数,但对其烧结活化能并无影响。
(2)混料
混料的均匀性对多孔陶瓷制品的气孔分布均匀有重要影响。
一般造孔剂的比重小于陶瓷原料的比重,另外它们的粒度大小往往不同,因此,难以使其很均匀混合。
Sonuparlak等采用二种不同的混料方法解决了上述问题。
如果陶瓷粉末很细,而造孔剂颗粒较粗或造孔剂溶于粘结剂中,可以将陶瓷粉末与粘结剂混合造粒后,再与造孔剂混合。
另一方法是将造孔剂和陶瓷粉末分别制成悬浊液,再将二种料浆按一定比例喷雾干燥混合。
而日本专利则采用将造孔剂微粒与ZrCl4和稳定剂YCl3水溶液充分混合,加氨水共沉淀,得到一种胶状物质,从而使造孔剂分布均匀。
(3)成型
多孔陶瓷的成型方法主要有模压、挤压、等静压、轧制、注射和粉浆浇注等。
挤压成型用途比较广泛,特别是用于工业废气和汽车尾气净化的蜂窝状陶瓷的成型。
注浆工艺制得的多孔陶瓷气孔分布均匀,且设备简单,也是制备多孔陶瓷的常用方法。
其关键是料浆的制备。
(4)烧结
多孔陶瓷的烧结制度主要取决于原料,添加剂及最后制品所需的性能。
提高烧结温度,延长烧结时间,有利于提高烧结体的强度,但会降低制品的气孔率,这是目前需要解决的问题之一。
近期,J.H.She和T.Ohji.在Al2O3,SiC粉混合物中引入造孔剂石墨,制备出具有低的热膨胀系数,良好得热震性能得多孔莫来石质陶瓷。
研究发现烧结温度对多孔陶瓷的孔径大小、分布和抗压强度有较大影响。
在气孔率为32.4%时样品的平均抗压强度可达到106MPa,另一方面气孔率为61%时样品有较大的比表面积12.4m2/g.
1.3.1.3挤压成型工艺
挤压成型是制备多孔蜂窝陶瓷最普遍采用的方法。
它的工艺流程为:
粉体原料+水+有机添加剂→研磨→陈腐→挤压成型→干燥→烧结。
该类工艺的优点在于可以根据需要对孔形状和孔大小进行精确设计,其缺点是不能成形复杂孔道结构和孔尺寸较小的材料,同时对挤出物料的塑性有较高要求。
其工艺流程图如图7所示。
图7挤出成型工艺流程图
目前,我国已研制出并生产使用的蜂窝陶瓷挤出成型模具达到了每平方英寸40孔的格。
美国与日本已开发研制出了每平方英寸600孔、每平方英寸900孔孔密度、超薄壁型蜂窝陶瓷。
我国也已经开始了每平方英寸600孔挤出成型模具的研究.并取得了初步成功。
1.3.1.4冷冻干燥法形成气孔
冷冻—干燥法全名为真空冷冻干燥,该技术由英国人Wollaston于1813年发明。
冷冻干燥的原理是将需干燥的物料在低温下先行冻结至其共晶点以下,使物料中的水分变成固态的冰,然后在适当的真空环境下,通过加热使冰直接升华为水蒸汽而除去,从而获得干燥的制品。
该工艺的特点是坯体烧成收缩小、烧成控制简单、孔结构可设计性强、制品机械强度相对较好,制备过程中对环境无污染。
目前,人们已经应用冷冻原理来制备多孔陶瓷。
例如,Bethtold和Mahler报道的一种用于陶瓷纤维的冷冻成形工艺,该工艺对胶状水合物(如硅酸)使用了相分离技术。
在该工艺中,让冰将柱状的凝胶包围和隔离着,并且控制溶液中冰的生长方向为单向生长,冰溶化后纤维就形成了。
在另外一种制备多孔陶瓷的冻干工艺中,溶剂是直接由固态升华到气态而排除的,通过控制金属盐溶液的冷冻方向获得了方向性好、气孔率很高(>90%)的多孔陶瓷。
1.3.1.5 颗粒堆积成孔(固态烧结工艺)
依靠粗颗粒堆积,颗粒结合部形成多孔结构。
其原理是利用微细颗粒易于烧结的特点,在高温状况下产生液相,使陶瓷粉粒相互连接在一起形成多孔陶瓷。
粗的颗粒靠细粒熔化粘合,也可以加入易熔的粘结剂结合。
。
制备过程中.粉体颗粒的形状、粒径、粒径分布、各种添加剂的含量和种类及烧成温度对微孔体的孔径分布和孔径大小有直接的影响。
这种工艺可通过调整颗粒级配对孔结构进行控制,制品的空隙率一般为20%~30%左右,在原料中加入碳粉、木屑、淀粉、塑料等成孔剂,高温下使其挥发可将整体孔隙率提高至75%左右。
1.3.2化学方法
1.3.2.1 溶胶-凝胶工艺
溶胶一凝胶法(Sol-Gel法,简称S-G法)主要用来制备微孔陶瓷材料,特别是微孔陶瓷薄膜。
它采用无机盐或金属有机化合物,如醇盐(即金属烷氧基化合物)为前驱物。
首先将前驱物溶于溶剂(水或有机液体)中。
通过在溶剂内发生水解或醇解作用,反应生成缩合聚集物形成溶胶,然后经蒸发干燥从溶胶转变为凝胶。
其在材料制备中的应用图及其基本工艺过程分别见图3、图4。
图3 溶胶-凝胶法在材料制备中的应用图
图4 溶胶-凝胶基本工艺过程
溶胶-凝胶法与其它化学合成法相比具有独特的优点:
操作过程简单,环境好;制品纯度高;材料组分均匀性好;制备的材料易实现分子或纳米层次的亚结构;界面具有良好的相容性;烧成温度低等。
但其也有待解决的问题:
原料成本高,有些对健康有害;处理时间长,不利于规模生产;制品易开裂等。
最近,Ichinose等提出了一种“假凝胶”的方法制备多孔陶瓷。
所谓“假凝胶”实际上是由陶瓷颗粒和有机凝胶组成的。
他们把Al2O3与藻朊酸氨溶液和聚羧酸氨(分散剂)均匀混合后,注入到Al2(SO4)3溶液中,成为凝胶物质,陶瓷颗粒均匀地分散其中,清洗干燥后,加热除去藻朊酸氨,烧结成多孔陶瓷。
该工艺中,凝胶通过藻朊酸盐与多价金属离子或H+进行离子交换而产生。
Katskki及合作者用盐酸与藻朊酸盐进行离子交换也制成了多孔陶瓷,并认为控制酸的浓度和藻朊酸氨的浓度是关键。
1.3.2.2 发泡工艺
发泡工艺与泡沫浸渍工艺相比,更容易控制制品的形状、成分和密度,并且可制备各种孔径大小和形状的多孔陶瓷,特别适于生产闭气孔的陶瓷制品。
它在陶瓷组分中添加有机或无机化学物质,通过化学反应等产生挥发气体,经干燥和烧结制成多孔陶瓷。
用做发泡剂的化学物质有很多种类,例如,用碳化钙、氢氧化钙、硫酸铝或双氧水等作发泡剂;由亲水性聚氨醋塑料和陶瓷泥浆同时发泡制备多孔陶瓷;用硫化物和硫酸盐混合作发泡剂。
近几年,由于多孔陶瓷的应用逐渐扩展到生物化学领域,要求孔径分布范围狭窄,使可控多孔陶瓷的研究得到进一步的重视。
吴皆正等采用碳酸钙和十二烷基苯磺酸钠作发泡剂,以廉价硅砂为原料,研究了原料粒度、烧成条件、发泡剂等因素对孔结构的影响,发现多孔陶瓷的平均气孔孔径与平均骨料粒径成正比,且随保温时间的延长,气孔孔径趋向均一,另外,增加粘结剂用量也有利于促进平均气孔孔径的集中趋势。
对于多孔陶瓷的制备,除了从成型角度加以研究之外,采用新的烧结工艺,如自蔓延高温合成(SHS)工艺、脉冲电流烧结工艺(PECS)、水热-热静压工艺、热等静压、压力脉冲化学气相渗透(PCVI)等,都可以制备具有一定孔结构的陶瓷烧结体。
本实验所需的多孔陶瓷在深水下需要一定的强度,而开孔多孔陶瓷很容易由于水的浸入而重量变化超标。
发泡工艺适用于生产闭气孔,且气孔率高,孔可以得到控制,试样强度高,符合本实验试样的要求,因此可以用发泡法制备。