世界名企汽车模具制造技术.docx
《世界名企汽车模具制造技术.docx》由会员分享,可在线阅读,更多相关《世界名企汽车模具制造技术.docx(14页珍藏版)》请在冰豆网上搜索。
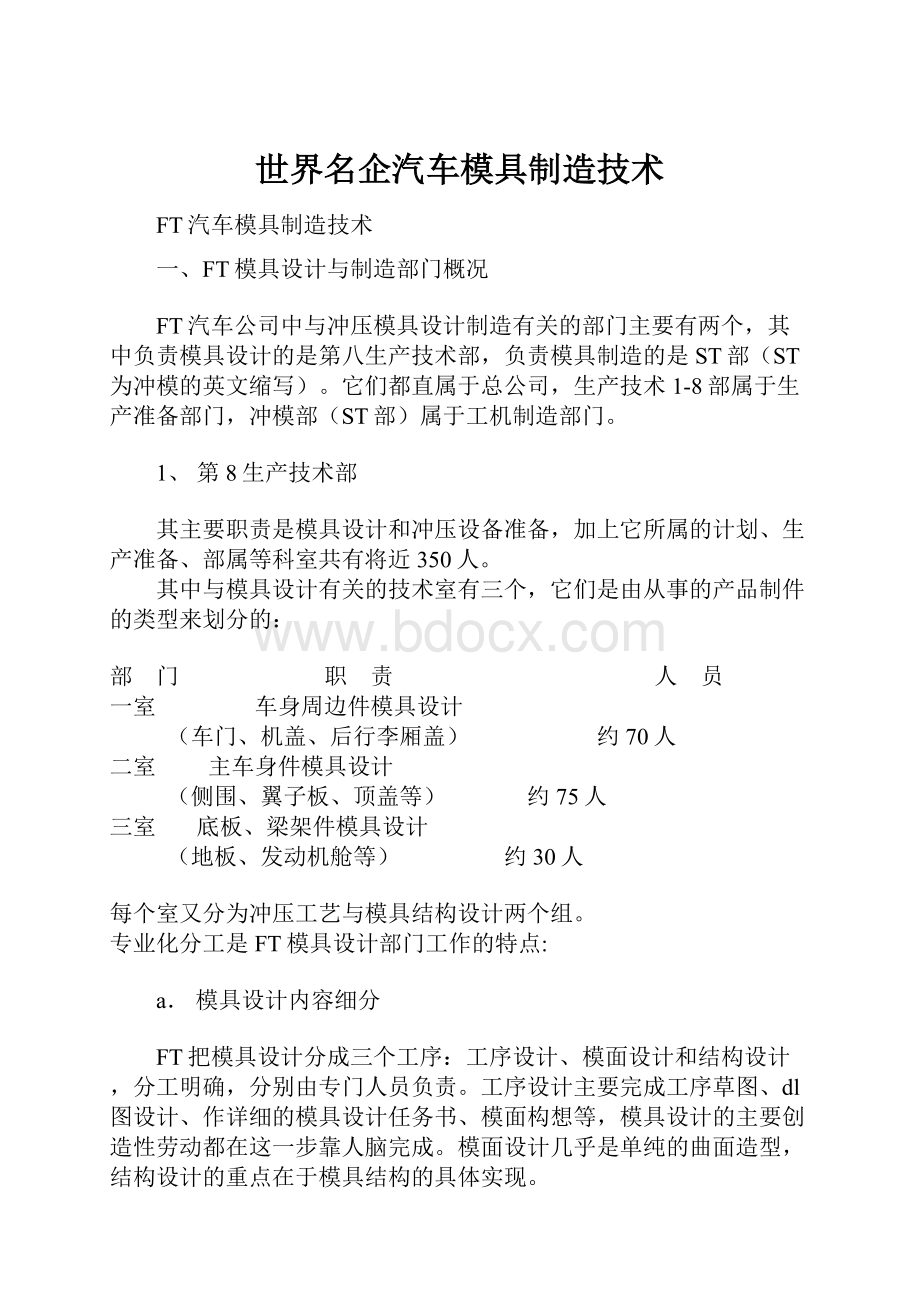
世界名企汽车模具制造技术
FT汽车模具制造技术
一、FT模具设计与制造部门概况
FT汽车公司中与冲压模具设计制造有关的部门主要有两个,其中负责模具设计的是第八生产技术部,负责模具制造的是ST部(ST为冲模的英文缩写)。
它们都直属于总公司,生产技术1-8部属于生产准备部门,冲模部(ST部)属于工机制造部门。
1、 第8生产技术部
其主要职责是模具设计和冲压设备准备,加上它所属的计划、生产准备、部属等科室共有将近350人。
其中与模具设计有关的技术室有三个,它们是由从事的产品制件的类型来划分的:
部 门 职 责 人 员
一室 车身周边件模具设计
(车门、机盖、后行李厢盖) 约70人
二室 主车身件模具设计
(侧围、翼子板、顶盖等) 约75人
三室 底板、梁架件模具设计
(地板、发动机舱等) 约30人
每个室又分为冲压工艺与模具结构设计两个组。
专业化分工是FT模具设计部门工作的特点:
a. 模具设计内容细分
FT把模具设计分成三个工序:
工序设计、模面设计和结构设计,分工明确,分别由专门人员负责。
工序设计主要完成工序草图、dl图设计、作详细的模具设计任务书、模面构想等,模具设计的主要创造性劳动都在这一步靠人脑完成。
模面设计几乎是单纯的曲面造型,结构设计的重点在于模具结构的具体实现。
b. 人员专业化分工细微
各个室只负责一类产品件,每个人在一定时间内负责同一个件,甚至是同一类模具。
由于FT每年开发的新车可达十种,这就是说,可能有的人在一年内画十套非常相似的前车门外板拉延模,其专业化程度可想而知。
c.模具的社会大分工
日本的模具制造专业性分工很强,FT虽然自己的模具制造能力很强,但它并不是什么模具都干。
比如,整车所有件的冲压工艺和模具的整车协调,都由他自己负责,但模具设计和制造他只干车身内外覆盖件,地板和梁架件全部到定点厂家外协。
不但FT如此,国外的大汽车公司所属模具厂无不如此,比如日本大发公司模具厂,甚至只做侧围、翼子板、顶盖等有限的几种外覆盖件。
这可以看作是一种发展趋势,在韩国、台湾甚至是专业模具厂家也是向只做几种件的更专业方向发展。
2、 模具制造部(ST部)
FTST部负责模具制造和新车整车模具的协调,并一直到大批量生产之前的冲压生产准备。
ST部构成:
科 室 责 任 人 员
技术室 生产技术开发、生产计划生产准备、设备计划 89人
NC课 NC编程、检查 175人
实型课 验具、实型制造 142人
机械课 机械加工 173人
钳工课 钳工、装配 237人
调试课 试模、调试 204人
总共:
1020人
主要数控加工设备:
构造面加工数控铣床39台
型面加工高速、五轴五面铣15台
新型一体化加工设备6台
其他小件加工设备31台
3、FT的模具设计和制造能力
模具设计与制造能力:
每年大约可开发10个轿车整车模具;
模具产量(标准套)约2000套/年;
内制率60%(外协40%);
主要产品中:
模具占80%;
验具占7%;
其他占13%;
全年完成模具制造成本预算近200亿日元。
人均模具产量2标准套/人。
年模具制造成本(不含设计)约600万日元/套
工时成本(平均)约1万日元/小时
整车模具设计制造周期12个月(由车身设计完成至新车批量生产)
其中包括整车全部模具设计周期5个月
制造周期5个月
调试周期6个月
由此可见,FT一年的轿车生产能力大约500万辆(日本国内部分约占50%),是中国大陆轿车产量的十倍,而模具设计制造能力也超过我们全国汽车模具生产能力的数倍。
FT的整车模具制造周期,远远短于我们的一般单套模具制造周期,它的标准单套模具制造周期为三至四个月,在我们看来还是一个梦想。
我们的模具质量水平与FT相比相差更远。
3、 FT一般模具制造周期
FT把模具的制造计划形成了标准化,根据模具的复杂程度可分为短周期、标准周期和长周期三种。
现以单套模具的设计制造周期(拉延模,标准周期)为例:
冲压工艺 20天
模具设计 20天
模面设计 8天
NC编程 15天
实型制作 7天
铸造 12天
机加工 9天
钳工装配 7天
单套拉延模总周期62天,其中制造周期52天
以上周期包括模具的设计、制造直至模具初次试模完成为止。
如果再考虑产品件各序模具的总周期,单个制件各序模具的总周期,要在拉延模的基础上再加22天(包括模具调试,但不包括整车调试),总共84天。
以上天数均为工作日(节假日除外),换算为日历日大约为20天等于一个月,也就是单套模具制造周期三至四个月。
FT的模具制造也是按照准时化生产方式进行的,全部倒排计划,计划到每一个工作日,不提前投产,避免增加在产模具。
我们的倒排计划往往是为赶工期,人为的压缩工期。
而FT的倒排计划,是为了在必要的时候生产出必要的产品,避免提前投产造成生产过剩的浪费。
二、FT模具制造技术
近十年来本人曾在日本多家模具制造厂进行过较为深入的学习和考察,先后累计时间达6个多月。
对比以后发现,FT的模具技术在日本的模具厂家中也是十分突出的,无论是能力、效率及技术都不愧为世界一流水平。
通过对FT的了解我们可以看到,世界汽车模具制造技术正在向这些方向发展:
计算机前的操作逐步代替现场操作,以高精度加工代替人的手工劳动,模具的设计、制造高度标准化,单件生产方式向流水线式生产方式发展等等。
结合我们国内的模具制造情况,FT在以下一些地方与我们有很大的不同,值得我们很好的借鉴。
1、冲压工艺设计
a、 精细模面设计
我们常说的模具设计实际上分为三个部分:
冲压工艺设计、模面设计和结构设计。
这三种设计的内容和侧重点是完全不同的,FT的工作流程为先有冲压工艺设计然后指导模面设计和模具结构设计,分别由不同的人来做,专业分工很明确。
传统的冲压工艺设计采用工序图或是DL图,它的模面设计是非常粗略的,以这样的图纸指导下的工艺造型,必须在后序靠人工修整、制造工艺祢补,造成模具制造的人工钳修量很大、周期延长。
FT在设计阶段通过计算机的曲面造型,完成模面的精细设计。
比如:
针对进料量不同设计各种拉延筋,同一套模不同部位的拉延筋截面不同,防回弹、过拉延处理,最小压料面设计,凸凹模不等间隙设计等等。
精细模面设计的结果,可以极大的减少型面加工,减少钳修,减少试模工时,它的作用非同小可。
对比之下,国内的模具设计还停留在结构设计阶段,模面设计没有受到很好的重视,模面实际上是靠后天完成,模具设计的落后造成了制造的落后,也就毫不奇怪了。
b、 板料成型分析技术应用情况
FT公司从5-6年前,开始应用有限元法做计算机模拟板料成型分析,主要应用的解算软件为美国的dyna3d,他们经过了近三年的努力才达到实用水平。
目前,FT建立了一个整车身各种典型件的分析结果库。
对一个新车型的件,如果成型性没有太大的变化,只是参考原工艺不做分析,只有特殊的新造型才做板料成型分析。
FT的新车要做样车,对造型特殊的件除了做板料成型分析外一般还要做简易模进行验证。
因此,FT人认为目前板料成型分析还不是一件必需的、简单的事,无论是周期还是成本都有很大代价。
本人认为,FT的车型开发量很大,车型之间变化不大、类似件很多,又积累了丰富的人的经验,板料成型分析确实用武之地不多,建立一个分析结果库是一个好方法(日本富士模具公司也是这么做的)。
反观国内现状,一方面模具厂专业分工很低,各种件都会遇到,难有现成经验,似乎更需要板料成型技术。
另一方面,技术水平低支持环境差(如:
板料参数、摩擦系数等难掌握),模具厂应用起来,要达到实用(不讲效果、不计代价的研究不算)也是非常困难的。
即使是成立专业分析公司,考虑用户数量、周期、价格等因素,恐怕也难成立。
目前,这项技术在国内的实际应用效果还难有定论。
c、 模面设计经验积累机制
FT的设计部门除手工勾画草图以外,设计已全部计算机化,一般设计人员除一台工作站外还有一台笔记本电脑。
但,真正创造性的设计还是靠人脑,特别是靠人的经验积累。
FT特别强调经验积累机制:
只有集体的经验不能有只属于个人的经验,比如:
资料的统一管理,草图设计的小组讨论,图纸的多部门集体审核,设计标准、规范的经常性增改等等。
经验积累机制是FT能够不断提高模面精细设计的主要手段。
比如:
模具加工完成之后,一般模具型面不用研合,刃口不必对间隙,钳工只负责安装,在初次试模时也不能随便修调模具,调试模具有模面设计人员在场,初次试模缺陷需要记录下来。
最后的休整结果,像拉延筋、拉延圆角变动、对称件的不对称现象等,还要进行现场测量。
这些资料的积累、整理、分析、存档,都是模面设计的经验积累,并随时加入到下一次的设计中去。
FT的模具设计和调试过程,真正做到了是一个闭环制造系统,借助于这种自我完善的经验积累机制,模具的设计越来越精细,越来越准确。
d、间隙图设计
在FT,模面设计实际上是由曲面造型和NC编程两部分共同完成的,为了传达和描述模面设计思想,就产生了除DL图、模具图之外的第三种图---间隙图也叫质量保证图。
间隙图本人在以前还没有见识过,这可能是FT的一种创造。
模具的设计不是单纯为了设计出一种机器,能够完成它一定的动作就完了(这只能叫作结构设计),模具设计的最终目的是为了保证它所压出的产品件是合格的高质量的,间隙图就是这样一种专为保证产品件质量的图。
质量保证图中,主要包括这样几项内容:
模具实际符型面区域、各个符型区域的间隙值、工艺要求的模面变化情况、拉延圆角的变化、各种模面的挖空等等。
凡是无法通过曲面造型实现的模面设计,都通过间隙图的传达,依靠NC编程的设计来实现,在这里NC编程也不再是单纯的实现模具结构的加工,它实际上也参与到模面设计中来了。
因此,间隙图的应用也是精细模面设计的一种必然。
e、大规模生产对模具的影响
FT的生产规模是世界一流的,它在模具设计如何适应大规模生产的要求方面具有丰富的经验。
提高材料利用率:
对于大批量汽车生产来说,提高板料的利用率是模具设计的第一大事。
只要把材料利用率提高几个百分点,模具的成本就可乎略不计了。
如果一套模具40万人民币,只相当于100吨钢板的价格,以寿命50万件计算,平均每件节约0.2Kg钢板,就足可节约出这套模具费用了。
减少冲压工序:
模具设计的趋势是,零件的合并,左右对称件合模,前后顺序件合模等等,原来几个件合成一个件,不同的件合在一套模,模具越来越大,单件工序大大减少,整车模具数量越来越少,这对降低冲压的成本起关键作用。
例如:
FT把整车制件的模具系数,由过去的3点几降到2左右。
冲压自动化:
为适应冲压线完全自动化,模具必须考虑机械手上下料,废料的自动排出,气动、自动和传感装置普遍采用等等。
模具的快速装换:
冲压线的换模时间,也成为一个模具设计必须考虑的问题。
如:
拉延模完全以单动代替双动,模具自动卡紧,换模不换气顶杆等等。
2、 模具结构的设计和加工
设计有两种目的:
一个是面向设计本身,一个是面向制造。
设计者在画图过程中逐步完善自己的设计思路,图画完了,自己也清楚了,因此图纸首先要设计者自己看得方便,并使设计的工作效率高。
另一方面,设计要面向制造,以提高生产效率为最终目的。
我们应当认识到不同的生产工艺流程决定了图纸的表达形式。
传统的模具总装图加零件图的形式,适应的是非框架结构的模具生产。
采用大型数控铣加工以后,模具总成图成为更好的形式。
在全面应用CAD设计之后,如果生产方式没变,那么二维设计和总图设计也不会变,只是把图板换成了屏幕和键盘。
我公司在97年曾一度改二维设计为三维实体设计,然而效果并不好,设计效率降低、生产上也没有得多少实惠。
FT在CAD三维实体设计与制造紧密相配合方面为我们提供了比较成功的经验。
a、实体设计
FT的模具设计已全部采用三维实体设计,应用的软件为enginner。
模面设计与结构设计的分开:
FT把模具结构设计与模面设计完全分开的,前者是实体设计,后者仍然是曲面设计。
在结构设计中模面部分只是示意性的,可用于实型加工,不能用于模具加工。
这种分工大大简化了模具实体设计,这种简化对三维实体设计的成败很重要。
取消二维图纸:
尺寸标注大约占绘图工作量的40%,FT不绘制传统意义上的二维图纸,也就完全省去了这一部分的工作量。
取而代之的是根据各工序需要,给出必须的三维立体简图,和标注必要尺寸的平面简图。
如果从三维设计出发,最终得二维图的结果,那把一个三维实体转变成符合人看图习惯的二维图,将是非常费时、费事的,设计出的实体变得毫无价值,这显然违背了实体设计的初衷,FT的成功之处就是没有这么做。
搭积木和编辑式设计:
三维实体设计采用搭积木式设计,依靠三维标准件和典型结构库,使模具结构极大的标准化,变二维绘图构思为三维立体布置。
同时大量借用已有的相似模具结构,经过简单编辑、修改,完成新模设计。
这对设计者来说,是观念上的一场革命,如果还墨守成规,先画平面图再生成立体型,那三维设计的优势就成了负担,效率太低了。
干涉检查:
在二维设计中,往往设计者并没有真正的建立起三维的模具形象,对复杂的空间问题只能靠断面图,一旦经验不足,考虑不周,空间干涉就再所难免。
三维实体设计最直接的好处,就是非常直观方便的干涉检查,甚至可以作运动干涉分析。
以往二维图设计时的一个老大难问题,在实体设计面前迎刃而解。
实体设计中的删繁就简:
实体设计直接面向制造,它所设计的繁简因加工需要而定,完全不必考虑人的看图习惯。
比如:
铸件的倒角,在加工中凹角靠刀具完成,凸角靠人工修整,所以,设计中就不必做了;又如:
标准件,完全是采购件,在设计中也可以变成示意性的简单几何体等等。
还有许多设计工作,实际上是靠后序的工艺规范完成的,如螺钉孔位置,镶块形状等。
因加工需要而设计是最经济的设计。
半自动设计:
FT在实体设计的基础上,对拉延模等一些结构典型而标准化比较高的模具,已经开发出具有一定功能的辅助程序,做到半自动设计。
比如:
拉延模结构设计一般都交给,新手、女职员来完成,设计一套模全部工作也用不了一周时间。
b、实型数控加工
实体设计的第一个用途,就是铸件泡沫实型完全采用数控加工。
FT的实型模是用一整块矩形泡沫数控加工出来的。
实型的数控化加工生产,就是通过对实体模型的工艺编辑(如:
加工面贴加工余量,模型分层编辑等),再经过数控编程,泡沫毛坯下料,数控加工,人工粘接和修整等几道工序完成的。
在FT,实型的生产员工,已完全从手工制作转变到大量的数控编程上来了,现场的简单人工粘接和修整工作,由临时工所充当。
实型的数控化生产直接得利于实体设计,而又提高了铸件的精度,为后序的精细加工带来极大的优势。
c、构造面数控加工
模具构造面就是模具型面以外的机加工面,如:
导向面、镶块安装面、螺钉孔、其他需加工面等等。
这些在FT也都是靠编程,数控加工出来的。
实体设计为模具的构造面数控编程加工带来了可能。
构造面加工编程化,可以大大提高机加工效率,减少现场的人为操作失误,提高加工的自动化程度。
当然要做到这一点,除实体设计之外,还要作许多工作,如:
自动对刀、刀具管理、加工参数、编程经验等等,这方面我们与FT的差距就更大,没有这些基础,构造面的编程加工是不可能的。
FT通过实体设计真正做到在模具结构上的CAD/CAM一体化,也只有一体化,取消绘制二维图的束缚,实体设计才显示出的它的价值,两者应该同步发展相宜得彰,这就是FT为我们提供的经验。
3、 高精度加工
模面的加工是模具加工的重点,FT在近年来大力发展高精度模面加工技术,取得了让人耳目一新的成果。
a、型面的高精度加工
型面高精度加工主要体现在这样几个方面:
提高模面加工精度、提高加工到位程度、实现模面的精细设计。
高精度加工除机床精度和刀具的管理外,主要是靠编程技术的改进来实现的。
加工方法包括等高线加工、最大长度顺向走刀加工,精加工走刀移行密度达到0.3mm,同时改垂直刀为30度角的高速加工等等方法,以提高加工精度。
同时在凹角清根、凸圆角加工到位、控制模具配合的不等距间隙、最大可能的缩小符型面方面都要加工到位,以实现模面的精细加工。
b、二维刃口的高精度加工
FT的二维刃口镶块加工,采用在专用的镶块加工流水线上,单块加工成活,加工精度可以达到按销定位装配,合模无须对间隙的程度。
当二维刃口整体加工时,也采用在线测量的方法来保证凸凹模的合模间隙,二维刃口的高精度最大的好处是能保证制件的修边毛刺得到很好的控制。
c、高精度加工的效果
FT通过高精度加工,使模具精度达到了模面的少钳工、无钳工化的目标。
FT的标准计划中,由机加工完成之后到第一次试模之间,只有七个钳工工作日,它基本是钳工装配时间,而没有钳工修磨工时。
在FT,模具一经加工完成,基本上不用修圆角、不用开间隙、不用修清根,不对刃口,不研合,甚至拉延模的型面都不用去刀痕、不推磨,唯一的钳修就是用油石推磨拉延凸圆角和压料拉延面。
而且第一次试模,无须修模的试压制件合格率都达到80%以上。
如果不是亲眼所见难以让人置信,这就是精细模面设计和高精度加工的威力。
4、其他技术
a、模具材料
FT的拉延模材料主要采用球墨铸铁而不是目前国内流行的合金铸铁。
球墨铸铁焊接性能、可加工性能好、耐磨性能和表面淬火硬度都比较理想,而成本比合金铸铁要低得多了。
修边刃口材料,选用型材镶块而不是符型的铸钢,主要是因为铸钢成本要高得多。
最值得注意的是,FT现已经大量采用基体与刃口一体化的特殊铸铁材料作修边模,使模具的机加工成本大为降低。
请注意这里的刃口既不堆焊,也不是钢材,铸铁整体刃口只经表面火焰淬火,直接用于几十万次寿命的薄板料修边模。
而且这种铸件的成本还不高。
b、表面处理
FT的拉延模型面的表面处理,要求较高的采用电镀,其它模,翻边、修边刃口镶块基本上采用火焰淬火。
日本目前没有采用离子渗氮技术,据FT人讲,也有试用的考虑。
对厚板料长寿命的刃口材料,FT采用具有自己专利的特殊钢材,也是火焰淬火。
而先加工成型,后整体淬火的方法,由于淬火带来的变形只能靠人工修整,在FT没有见到使用。
c、模具生产中的检验
模具是单件生产,保证质量是一件非常困难的事,国内的模具厂大都配备大量的专职工序质检人员,这严重影响生产效率,但质量把关效果还不佳。
FT是怎么做的呢?
工序检验:
FT人认为产品的质量在源头,设计、工艺、编程、机床、刀具才是质量真正的保证,质量是生产出来的而不是检查出来的,因此,模具各序之间没有专职检验,只有自检和互检,质量的把关靠得是每一个生产者。
型面检测:
模具的型面也基本没有测量检验。
大量的型面检测,如测拉延圆角,拉延筋的修正量,曲面的光顺度等主要是为了模面设计积累经验,而不是为了检验模具质量是否合格。
制件检测:
FT的产品件检查,主要靠三维测量机进行自动数值检测,但他们也做验具,验具只起产品件定位支撑的作用。
因此验具结构简单,没有强制卡紧装置,他们的产品件检测几乎是处于自由状态下的检测,这对产品件的符型性是一个非常严格的要求。
三、技术发展动向
前几年我们看到发达国家的汽车模具行业似乎在萎缩。
因为,当时认为模具生产离不开人的手工劳动,发达国家具有工资成本高、没有人愿意干这一行等因素,模具行业大有向第三世界转移的趋势。
通过FT的发展,我们有了一些新的认识,模具生产越来越依赖高科技,完全可以把人工劳动降到很低,汽车对模具生产的需求最重要的是高质量和短周期,在大规模汽车生产中,模具本身的成本远远不如模具的使用成本更重要。
从这一点上看,目前我们的模具生产不具什么优势,这种工业转移也不会成潮流,这十多年来,我们通过硬件的技术引进得到的技术进步,并没有祢补上因人家更加努力的追求技术进步而带来的新的差距。
换个角度说,如果汽车模具行业真的向第三世界转移的话,那一定是个夕阳产业,目前汽车模具在车身材料没有突破性变化的情况下,还是有一定的发展空间和需求的。
1、 重点发展计算机技术
FT模具制造技术发展的重点,在于突出计算机的应用,越来越多的人从生产现场转移到计算机前。
实体设计加上数控编程,取代了人工实型制作和机床操作。
精细模面设计和精细数控编程大大减少了钳修,高精度加工取消了模具的研合、修配。
现在数控编程人员已超过了现场操作工人,数控编程的工时费用,超过了机床的加工工时费50%,编程的周期超过了机加工周期。
计算机技术应用的发展,目前没有降低模具成本,但模具生产已从依赖人的技巧转向数控化的自动、半自动化生产,这种高精度和无人化加工,使模具和产品件的质量有了极大的提高,生产周期大大缩短,计算机技术使模具制造技术又达到了一个新的高度。
相比较就可以看出,国内目前的计算机应用还比较初级,并不是我们的机床和软件不行,而是在应用的基础技术上有很大的差距,即使是把FT的技术全搬来,真正做到那种效果,也不是一件容易的事。
2、 消灭钳工
原来我们认为,模具这种单件生产、型面复杂的产品,离开手工是不可能的,而FT提出要消灭钳工。
消灭钳工是一种目标,主要是指极大减少或完全避免修磨和调整钳工(装配钳工还是要的)。
正如我们在前面所介绍的,目前FT的这一目标已基本实现,除修磨拉延面和拉延凸圆角外,推磨、修模和调配钳修,已大部分属于异常或祢补设计、制造的缺陷,不再是一件必要的和正常的工作。
我们举个例子,拉延模型面的光洁度历来是我们强调的质量标准,过去为达到这一点主要是靠钳工推磨。
为减少或不推磨,就要减少铣削刀痕余量,有人主张采用垂直型面加工的五轴铣床,也有采用数控型面磨。
这些FT也都采用过,但实践证明,五轴机床成本高、效率低,编程十分困难,效果也十分不理想。
最后,FT采用高速、小移行的三轴铣削加工方式,得到高精度型面,把圆角人工推磨,而其他型面干脆不修磨,模面带刀痕拉延。
结果证明,虽然模面谈不上光洁度(还带刀痕呢),但即使是表面质量要求很高的轿车外板件,除制件内表面有一些拉痕外,对有用的制件外表面没有任何不良影响,就是需要电镀的那些模面,也同样是带刀痕电镀。
据说德国和美国有些汽车模具厂也早已废除了型面推磨。
这对那些追求模具表面光洁度的人来说,真是命运开