呼机上盖的塑件注射模设计.docx
《呼机上盖的塑件注射模设计.docx》由会员分享,可在线阅读,更多相关《呼机上盖的塑件注射模设计.docx(25页珍藏版)》请在冰豆网上搜索。
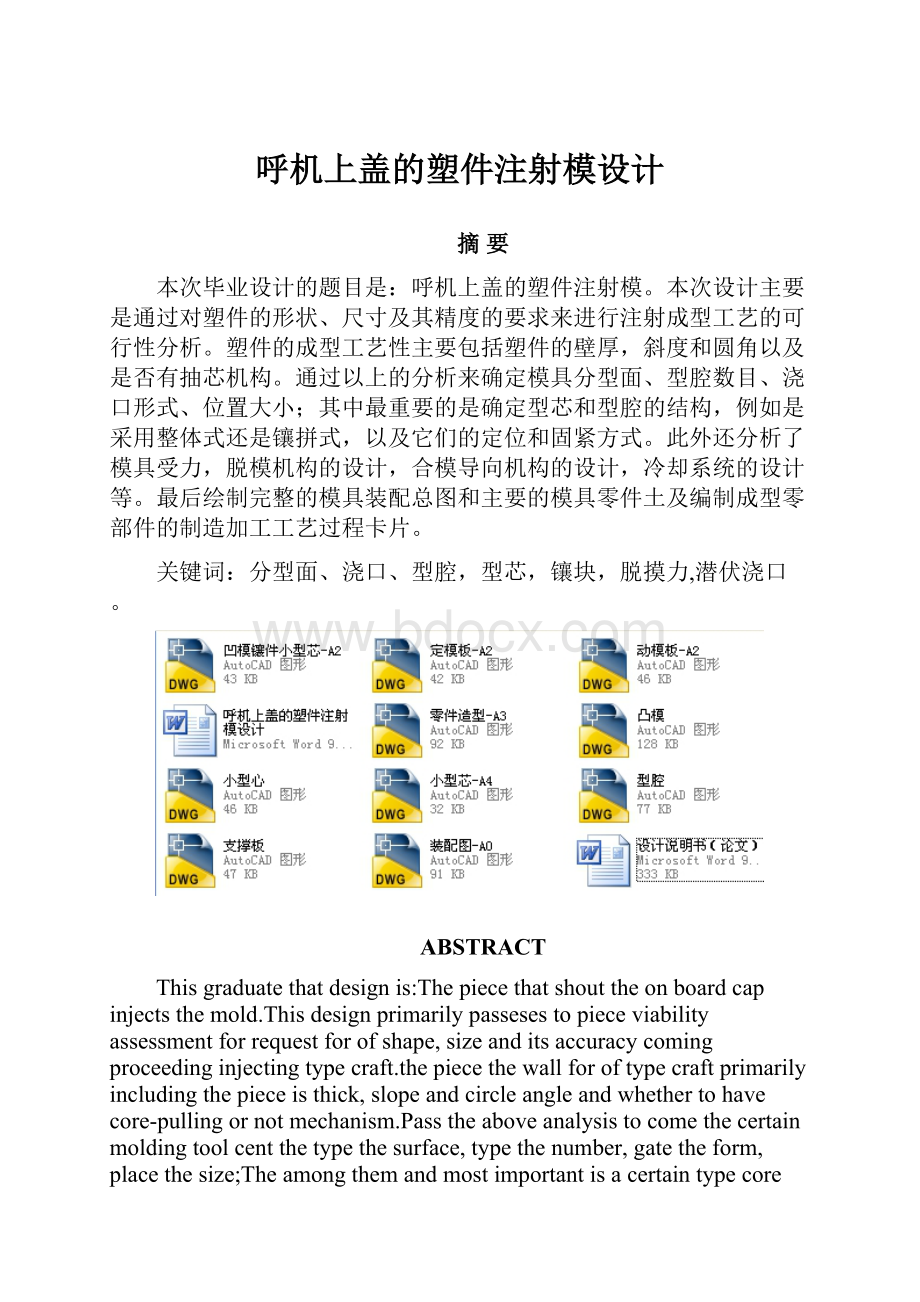
呼机上盖的塑件注射模设计
摘要
本次毕业设计的题目是:
呼机上盖的塑件注射模。
本次设计主要是通过对塑件的形状、尺寸及其精度的要求来进行注射成型工艺的可行性分析。
塑件的成型工艺性主要包括塑件的壁厚,斜度和圆角以及是否有抽芯机构。
通过以上的分析来确定模具分型面、型腔数目、浇口形式、位置大小;其中最重要的是确定型芯和型腔的结构,例如是采用整体式还是镶拼式,以及它们的定位和固紧方式。
此外还分析了模具受力,脱模机构的设计,合模导向机构的设计,冷却系统的设计等。
最后绘制完整的模具装配总图和主要的模具零件土及编制成型零部件的制造加工工艺过程卡片。
关键词:
分型面、浇口、型腔,型芯,镶块,脱摸力,潜伏浇口。
ABSTRACT
Thisgraduatethatdesignis:
Thepiecethatshouttheonboardcapinjectsthemold.Thisdesignprimarilypassesestopieceviabilityassessmentforrequestforofshape,sizeanditsaccuracycomingproceedinginjectingtypecraft.thepiecethewallforoftypecraftprimarilyincludingthepieceisthick,slopeandcircleangleandwhethertohavecore-pullingornotmechanism.Passtheaboveanalysistocomethecertainmoldingtoolcentthetypethesurface,typethenumber,gatetheform,placethesize;Theamongthemandmostimportantisacertaintypecoreandtheconstructionofthetype,forexampleadoptthewholethetypeoftypestill,andtheirfixedpositionandtightwayof.Inadditionandstillanalyzedthemoldingtooltosufferforce,moldthatdesignthatthedesignofthepatterndrawmechanism,matchthedesignetc.toleadtothemechanism,coolingsystem.Finallydrawtheproductionthatcompletemoldingtoolassemblethegeneraldrawingsumthesoilandestablishmentofprinipalmoldingtoolpartstypezerothepartsprocessthecraftprocessthecard.
Keywords:
partingline,thegate,cavity,core,moldinsert,
ejectionforce,submarinegate.
目录
摘要1
ABSTRACT2
目录3
前言5
概论6
第一章塑件分析6
第二章塑件材料的成型特性与工艺参数7
第一节塑件材料的特性7
第二节成型特性7
第三节工艺参数8
第四节塑料制件的结构工艺性8
第五节塑件在模具中的位置9
第三章设备的选择10
第一节最大注射量10
第二节注射量校核10
第三节塑件在分型面上的投影面积与锁模力的校核11
第四节注射压力的校核11
第五节开模行程的校核11
第六节注射机的技术规格11
第四章浇注系统的设计12
第一节浇注系统的功能阐述12
第二节主流道的设计12
第三节分流道的设计13
第四节浇口形式的选择13
第五节冷料穴的设计14
第六节排溢系统的设计14
第七节模架组合的选择15
第五章成型零件工作部分尺寸的计算15
第一节成型零件的结构设计15
第二节成型工作零件的工作尺寸15
第三节模具型腔侧壁和底板的厚度的计算19
第六章推出机构与复位机构20
第一节推出机构的组成20
第二节推出机构的设计原则20
第三节简单推出机构21
第七章合模导向机构的设计23
第八章冷却系统的设计24
总结25
致谢26
参考文献26
前言
一、本次设计的任务
本次的设计是毕业生的最后一次课程设计,是我们对以前所学的理论知识和技能的一次综合性训练。
模具设计是一项很复杂的工作,它要求我们在掌握理论知识的基础上要有更好的实践经验。
设计一付好的模具,其中牵涉到许多的内容,一套模具有好多种方案,在进行的比较中需要考虑的内容包括对塑件成型工艺的分析,如何确定分型面、型腔数目以及选择注射机型号。
确定模具的总体结构、型腔型芯的结构,同时还考虑了模具制造工艺的可行性以及模具制造的经济性;浇注系统的设计,确定浇口形式及位置大小;确定主流道,分流道和冷料穴的形式及尺寸;脱模机构的设计,脱模力的计算;侧向分型及抽芯机构的设计,导向机构的设计,冷却系统的设计。
二、设计要求
1、在设计过程中要理论联系实际,扎实的掌握理论基础知识,以便灵活应用解决实际问题。
2、在设计过程中要不断地修改,拟定几种方案以便进行比较,在保证塑件使用要求和外观精度的基础上尽量采用简单的模具结构。
3、在设计过程中要不断地查取有关的设计资料,在努力采用以前的模具结构的基础上要进行大胆的修改,以便设计出有新颖的模具。
、
4、设计中遇到的问题要多与指导老师交流,要合理、认真、独立地完成。
5、设计中应尽量采用标准件,这样就可以减少模具的制造难度。
.
概论
模具是工业生产中的重要工艺装备模具工业是国民经各部门发展的重要基础之一。
塑料模具是指用于成型塑料制件的模具,它是型腔模的一种类型。
模具设计水平的高低、加工设备的好坏、制造力量的强弱模具质量的优劣,直接影响着许多新产品的开发和老产品的更新换代,影响着产品质量和经济效益的提高。
在现代塑料制件的生产中,采用合理的加工工艺,高效设备,先进的模具。
塑料成型技术的发展趋势是:
一、模具的标准化
1.为了适应大规模成批生产塑料成型模具和缩短模具制造周期的需要,模具的标准化工作十分重要。
二、模具加工技术的革新。
1.为了提高加工精度,缩短模具制造周期,塑料模成型零件加工广泛应用仿行加工,电加工,数控加工及微机控制加工等先进技术,并使用坐标镗,坐标磨和三坐标测量仪等精密加工与测量设备。
三、各种新材料的研制和应用。
1.模具材料影响模具加工成本使用寿命和塑件成型质量等。
四、CAD/CAM/CAE技术的应用。
第一章塑件分析
参看产品零件图如(图1)
图1呼机上盖
从零件图来看,塑件的外表面精度要求较高,而内表面的精度要求一般,由于是采用上下盖配合而成,从而避免了侧向凹凸,简化了模具结构。
塑件的四个角和各侧面采用了圆角过渡,这样使塑件的外观变得更加圆滑,而且可避免在尖角处产生应力集中或在脱摸过程中由于成型内应力而开裂。
综合以上各点分析,采用一模两件,以提高生产率和降低制造成本。
第二章塑件材料的成型特性与工艺参数
本章着重介绍塑料成型的工艺特点以及塑件的工艺要求,塑件结构设计方面的知识。
为后面几章的模具设计奠定了基础。
对零件的分析得塑件材料取ABS(丙烯腈-丁二-苯乙烯共聚物)。
第一节塑件材料的特性
ABS是由丙烯腈、丁二烯、苯乙烯共聚而成的。
这三种组分的各自特性使ABS具有良好的性能。
ABS无毒、无味,呈微黄色,成型的塑件有较好的光泽。
密度为1.02—1.05g/cm.ABS有极好的抗冲击强度,且再低温下也不迅速下降。
有良好的机械强度和一定的耐磨性、耐寒性、耐油性、耐水性、化学稳定性和电器性能。
ABS在机械工业上用来制造齿轮、泵叶轮、轴承、把手、管道、电机外壳、仪表壳、仪器盘、水箱外壳等。
ABS还用来制作水表壳、纺织器材、电器零件、文教用品、玩具、电子琴及收录机壳体、食品包装容器、农药喷雾器及家具等。
第二节成型特性
ABS在升温是粘度增高,所以成型压力较高,塑料上的脱模斜度宜稍大;ABS易吸水,成型加工前应进行干燥处理;易产生熔接痕,模具设计是应注意尽量减小浇注系统对料流的阻力;在正常的成型条件下,壁厚、熔料温度及收缩率影响极小。
要求塑件精度高时,模具温度可控制在50~60℃,要求塑件光泽和耐热时,应控制在60~80℃。
第三节工艺参数
塑料性能
ABS(苯乙烯共聚)
塑料性能
ABS(苯乙烯共聚)
屈服强度/Mpa
50
玻璃化温度/℃
拉伸强度/Mpa
38
熔点(粘流温度)/℃
130~160
断裂伸长率/%
35
热变形温度/℃
45N/cm
108N/cm
90~108
拉伸弹性模量/Gpa
1.8
83~103
弯曲强度/Mpa
80
线膨胀系数/(10¯5/℃)
7.0
弯曲弹性模量/Gpa
1.4
比热容 /[J/(kg·K)]
1470
简支架冲击强度/(kJ/m²)
无缺口
缺口
261
热导率 /[W/(m·K)]
0.263
11
燃烧性 /(cm/min)
慢
氏硬度 HBS
9.7R121
体积电阻/Ω·cm
6.9×10
密度 /(g/cm³)
1.02~1.16
击穿电压/(Kv/mm)
比体积 /(cm²/g)
1.02~1.16
成型收缩率/%
0.4~0.7
吸水性/%(24h)
长时间
0.2~0.4
拉伸模量E/×10³
1.91~1.98
泊松比 µ
0.38
透明度或透光率
不透明
与钢的摩擦因子f
0.20~0.25
第四节塑料制件的结构工艺性
要想获得合格的塑料制件,除选择合理的塑件材料外,还必须考虑塑件的结构工艺性。
塑件的结构工艺性与模具设计有直接关系,只有塑件设计满足成型工艺要求,才能设计出合理的模具结构。
一、尺寸及精度
塑件尺寸的大小取决于塑料的流动性。
在注射成型华中,薄壁塑件的尺寸不能设计的过大。
塑件的尺寸精度是指所获得的塑件尺寸与产品图中尺寸的符合程度,及所获得塑件尺寸的准确度。
根据本次设计的要求,结合表3-9(参一)初步选定该零件的三个表面的精度分别为4、5、6级。
二、表面粗糙度
塑件的外观要求越高,表面粗糙度应越低。
一般模具表面粗糙度,要比塑件的要求低1-2级。
塑件的表面粗糙度一般为Ra0.8-0.2um。
三、形状
塑件的内外表面形状应尽可能保证有利于成型。
四、斜度
为了便于从塑件中抽出型心或从型腔中脱出塑件,防止脱模时拉伤塑件,在设计时必须使塑件内外表面沿脱模方向留有足够的斜度,由于本次设计所选材料为ABS,内外表面均取拔模斜度为1度。
五、壁厚
塑件的壁厚对塑件的质量有很大的影响,塑件壁厚尽可能均匀。
本次设计的壁厚非均匀,尽量保证两侧均匀,且满足塑件的最小壁厚。
六、圆角
塑件除了使用上要求采用尖角外,其余所有转角处均应尽可能采用圆角过渡,本设计未注圆角处均为R3。
第五节塑件在模具中的位置
一、型腔数量及排列方式
塑件的设计已完成,根据塑件品种,形状及尺寸分析,塑件的材料、形状尺寸于浇口的位置和形状有关,同时也对分型面和脱模位置有影响,此外质量控制要求,塑件的成本,注射机技术规范对型腔均有影响。
本次设计初步选定型腔数目为2个,采用平衡式布局,可直接达到各个型腔均衡进料的目的。
二、分型面的设计
1、分型面设在零件开口最大轮廓处
2、分型面设在零件开口处以使塑件开模以后留在动模。
便于顺利脱模
3、在分型面上设有1度的拔模斜度,可以保证塑件外观质量和塑件精度要求
第三章设备的选择
第一节最大注射量
一次设计先确定型腔数目,然后根据生产条件,如注射机的有关技术规范进行校核。
据4-2(参1)
n<=Km
K—注射机最大注射量的利用系数,一般K=0.8
M—注射机额定塑化量(g/h)
M2—浇注系统所需塑料的质量或体积(g)
Mn—注射机允许的最大注射量
本次设计采用UG进行三维造型,利用实体测得M1=10g
所以2≤(0.8Mn-2)/10
Mn≥27.5g
初步选定注射机为XS—Z—60(见表4-1)
第二节注射量校核
nm1+m2≤0.8m(参1,4-4)
m≤27.5
m—注射机的最大注射量(g或cm3
第三节塑件在分型面上的投影面积与锁模力的校核
(n*A1+A2)A2——浇注系统在分型面上的投影面积
A1——单个塑件在模具分型面上的投影面积
F——注射机额定锁模力
P——塑料熔体对型腔成型压力,其大小一般为注射压力的80%
经校核,注射机额定锁模力已足够,不会发生涨模溢料的现象。
第四节注射压力的校核
塑件材料为ABS,注射压力一般为70—90,取80KN,而注射机额定压力为122,注射机最大注射压力能满足塑件成型的要求。
第五节开模行程的校核
S≥H1+H2+(5~10)
H1——推出距离(mm)
H2——包括浇注系统凝料在内的塑件高度(mm)
S≥15+50+10=75(mm)
而XZ—S—60的最大开模距离为180mm
故开模距离满足要求
第六节注射机的技术规格
注射机技术规格为:
额定注射量cm³:
60
螺杆直径mm:
38
注射压力MPa:
122
注射行程mm:
170
合模力KN:
500
最大成型面积cm²:
130
最大开模行程mm:
160
模具最大厚度mm:
200
模具最小厚度mm:
70
动模固定板尺寸mm:
330×440
第四章浇注系统的设计
第一节浇注系统的功能阐述
浇注系统是熔体从注射机喷嘴射出后到达型腔之前在模具中流经的通道,浇注系统的设计是注射模具设计的一个重要环节,它对获得优良性能和理想外观的塑料制件以及最佳的成型效率有直接的影响,是模具设计者十分重视的技术问题。
浇注系统分为普通流道的浇注系统和热流道的浇注系统,前者较为常用,一般由主流道、分流道、浇口和冷料穴等四部分组成。
它的主要作用为将来自注射机喷嘴的塑料熔体均匀而平稳地输送到型腔,同时使型腔内的气体能及时顺利地排出。
在塑件熔体填充及凝固的过程中,将注射压力有效地传递到型腔的各个部位,以获得形状完整,内外在质量优良的塑料制件。
第二节主流道的设计
主流道是浇注系统中从注射机喷嘴与模具相接触的部位开始到分流道为止的塑料熔体的流动通道。
在卧式注射机上使用的模具中,主流道垂直于分型面,为使凝料能从其中顺利拔出,需设计成圆锥形,锥角为2°—6°,表面粗糙度为Ra<0.8um
主流道的尺寸为:
d=注射机喷嘴直径+1=5mm
SR=喷嘴球面直径+1=15mm
h=3—5
a=2°
L=60mm
D=10mm
如图:
主流道衬套与定位圈设计成整体式。
第三节分流道的设计
由于所设置的模具为一模四件,属于多型腔模具,应设置分流道,分流道是指主流道末断与浇口之间这一段塑料熔体的流动通道,所选分流道为半圆形分流道,直径为6。
第四节浇口形式的选择
浇口是连接分流道与型腔的一段细短通道,它是浇注系统的关键部分,浇口形状、数量、尺寸和位置对塑件的质量影响很大。
浇口主要有两个作用:
一是塑料熔体流径的通道;二是浇口的适时凝固可控制保压时间。
由于塑件的外观质量要求较高,所以浇口本身设在模具内的隐蔽处,塑料熔体通过型腔侧面斜向注入型腔,因而塑件外表不受损伤,不致因浇口痕迹而影响塑件的表面质量及美观效果
第五节冷料穴的设计
冷料穴一般位于主流道对面的动模板上,或处于分流道的末端。
其作用是存放料流前端的“冷料”,防止冷料进入型腔而形成冷接缝。
开模时又能将主流道中的凝料拉出。
并采用与推杆匹配的冷料穴。
这里采用Z字的冷料穴。
这样在开摸时推杆将浇注系统凝料推出模外。
推料杆和冷料穴的具体形式如图所示:
第六节排溢系统的设计
当塑料熔体填充型腔时,如果型腔内的气体因各种原因不被排除干净的话,一方面将会在塑件上形成气泡、接缝、表面轮廓不清等成型缺陷,另一方面气体受压,体积缩小而产生高温会导致塑件局部表面炭化,同时积存的气体还会产生反向压力而降低充模速度,因此设计型腔时必须考虑排气问题。
此塑件可以利用拉料杆,推件杆等利用间隙排气。
第七节模架组合的选择
根据注射机固定模板尺寸和各项工艺参数,以及塑件尺寸形状凸凹模尺寸的计算,注射模架选取基本型A2(见参2表2-95),定模和动模均由两快模板组成,推杆推出塑件。
注射模中小型模架组合选为250×250
第五章成型零件工作部分尺寸的计算
第一节成型零件的结构设计
凹模是成型塑件外表面的主要零件,本次设计采用组合式型腔,并采用整体嵌入式凹模。
小型塑件用多型腔模具成型时,各单个凹模采用机械加工、冷挤压3、电加工等方法加工制成,然后压入模板中,这种结构加工效率高,装拆方便,可以保证各个型腔形状、尺寸一致。
凸模和型心均是成型塑件内表面的零件,凸模又称主型芯。
在一般模具中采用将型芯单独加工,在镶入模板中,为了便于加工,形状复杂的型芯往往采用镶拼式结构。
小型芯成型塑件上的小孔或槽,小型芯单独制造,在嵌入模板中。
第二节成型工作零件的工作尺寸
成型零件工作尺寸是指成型零件上直接用来构成塑件的尺寸,主要有型腔和型芯的径向尺寸,型腔的深度尺寸和型芯的高度尺寸,型芯和型腔的位置尺寸等。
一、型腔和型芯的径向尺寸
(1)型腔径向尺寸
利用平均收缩率法
LM+δz=[(1+Scp)LS-3/4Δ]+δz
LM凹模径向尺寸(mm)
LS————塑件径向公称尺寸(mm)
Scp————塑料的平均收缩率(%)
Δ—————塑件公差值(mm)
Δz
————凹模制造公差(mm)
查表得:
ABS的收缩率为0.4~0.7%
则塑料的平均收缩率Scp=0.55%
型腔的径向尺寸:
实践证明:
成型零件的制造公差约占
塑件总公差的1/3~1/4,因此在确定成型
零件工作尺寸公差值时可取塑件公差的1/3~1/4。
为了保持较高精度选1/4。
由于外表面精度较高,Δ1=0.32mmΔ2=0.28mmΔ3=0.18mm
δz1=0.25×0.32=0.08mmδz2=0.25×0.28=0.07mm
δz3=0.25×0.18=0.045mm
则:
LM1+δz=[(1+Scp)L1-3/4Δ]+δz
=[(1+0.55%)×64.3-3/4×0.32]+0.08
=64.4+0.08mm
LM12+δz=[(1+Scp)LS-3/4Δ]+δz
=[(1+0.55%)×43.5-3/4×0.28]+0.07
=43.53+0.07mm
LM13+δz=[(1+Scp)LS-3/4Δ]+δz
=[(1+0.55%)×12-3/4×0.18]+0.045
=53.2+0.045mm
二、型芯的径向尺寸
同样运用平均收缩率法:
LM–δz=[(1+Scp)LS+3/4Δ]–δz
LM————型芯径向尺寸(mm)
Δz————型芯径向制造公差(mm)
其余符号同上
取IT6精度时Δ1=0.64mmΔ2=0.56mm
Δ3=0.36mm
由δz=1/4Δ得:
δz1=0.16mmδz1=0.14mmδz1=0.09mm
则:
LM4–δz=[(1+Scp)LS+1/2Δ]–δz
=[(1+0.55%)×60.3+1/2×0.64]–0.16
=60.95–0.16mm
LM4–δz=[(1+Scp)LS+1/2Δ]–δz
=[(1+0.55%)×39.5+1/2×0.56]–0.14
=39.90–0.0.14mm
LM4–δz=[(1+Scp)LS+1/2Δ]–δz
=[(1+0.55%)×10+1/2×0.36]–0.09
=10.23–0.09mm
L=36Δ=0.52LM4–δz=[(1+Scp)LS+1/2Δ]–δz
=36.46–0.13mm
L=11Δ=0.36LM4–δz=[(1+Scp)LS+1/2Δ]–δz
=11.24–0.09mm
L=40Δ=0.56LM4–δz=[(1+Scp)LS+1/2Δ]–δz
=40.5–0.16mm
L=15Δ=0.40LM4–δz=[(1+Scp)LS+1/2Δ]–δz
=15.28–0.1mm
三、中心距尺寸:
塑件上凸台之间,凹槽之间或凸台到凹槽的中心线之间的距离称为中心距,该类尺寸属于定位尺寸。
由于模具上中心距尺寸和塑件中心距公差都是双向等植公差,同时磨损的结果不会使中心距尺寸发生变化,在计算中心距尺寸时不必考虑磨损量。
Cm=(1+s)Cs
标注上制造公差后得:
(Cm)±δz=(1+s)Cs±δz
¢10(Cm)±δz=(1+s)Cs±δz
=1.0055×10±1/2×1/4×0.32
=10.0055±0.04
¢6(Cm)±δz=(1+s)Cs±δz
=1.0055×6±1/2×1/4×0.28
=6.03±0.035
¢7.1(Cm)±δz=(1+s)Cs±δz
=1.0055×7.1±1/2×1/4×0.32
=7.13±0.04
¢8.2(Cm)±δz=(1+s)Cs±δz
=1.0055×8.2±1/2×1/4×0.28
=8.25±0.035
¢10(Cm)±δz=(1+s)Cs±δz
=1.0055×10±1/2×1/4×0.32
=10.055±0.04
¢24(Cm)±δz=(1+s)Cs±δz
=1.0055×24±1/2×1/4×0.44
=24.13±0.055
¢22(Cm)±δz=(1+s)Cs±δz
=1.0055×22±1/2×1/4×0.44
=22.12±0.055
四、型芯高度尺寸
同样运用平均收缩率法:
HM+δz=[(1+Scp)LS+3/4Δ]–δz
HM————型芯高度尺寸(mm)
Δz————型芯高度制造公差(mm)
其余符号同上
由:
H=2mm如(图13)
取IT3精度时Δ=0.06mm
由δz=1/4Δ得:
δz=0.015mm
则:
HM–δz=[(1+Scp)hs+3/4Δ]–δz
=[(1+0.55%)×2+3/4×0.06]–0.015
=2.056–0.015mm
第三节模具型腔侧壁和底板的厚度的计算
塑料模具型腔在成型过程中受到熔体的高压作用,应具有足够的强度和刚度,如果型腔侧壁和底版厚度过小,可能因强度不足而产生塑料变性甚至破坏,也可能因为刚度