CAE在精密铸造中的应用.docx
《CAE在精密铸造中的应用.docx》由会员分享,可在线阅读,更多相关《CAE在精密铸造中的应用.docx(22页珍藏版)》请在冰豆网上搜索。
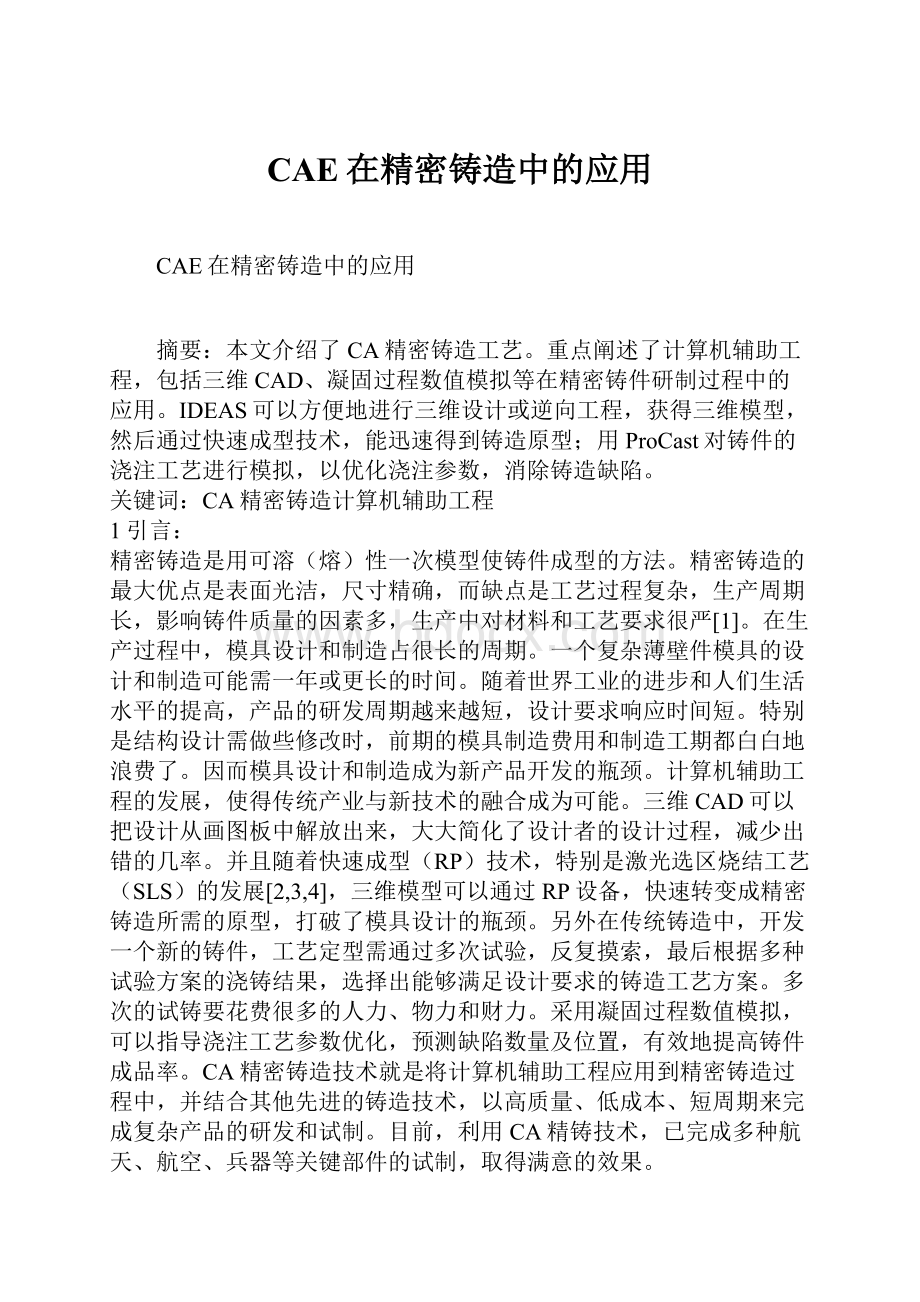
CAE在精密铸造中的应用
CAE在精密铸造中的应用
摘要:
本文介绍了CA精密铸造工艺。
重点阐述了计算机辅助工程,包括三维CAD、凝固过程数值模拟等在精密铸件研制过程中的应用。
IDEAS可以方便地进行三维设计或逆向工程,获得三维模型,然后通过快速成型技术,能迅速得到铸造原型;用ProCast对铸件的浇注工艺进行模拟,以优化浇注参数,消除铸造缺陷。
关键词:
CA精密铸造计算机辅助工程
1引言:
精密铸造是用可溶(熔)性一次模型使铸件成型的方法。
精密铸造的最大优点是表面光洁,尺寸精确,而缺点是工艺过程复杂,生产周期长,影响铸件质量的因素多,生产中对材料和工艺要求很严[1]。
在生产过程中,模具设计和制造占很长的周期。
一个复杂薄壁件模具的设计和制造可能需一年或更长的时间。
随着世界工业的进步和人们生活水平的提高,产品的研发周期越来越短,设计要求响应时间短。
特别是结构设计需做些修改时,前期的模具制造费用和制造工期都白白地浪费了。
因而模具设计和制造成为新产品开发的瓶颈。
计算机辅助工程的发展,使得传统产业与新技术的融合成为可能。
三维CAD可以把设计从画图板中解放出来,大大简化了设计者的设计过程,减少出错的几率。
并且随着快速成型(RP)技术,特别是激光选区烧结工艺(SLS)的发展[2,3,4],三维模型可以通过RP设备,快速转变成精密铸造所需的原型,打破了模具设计的瓶颈。
另外在传统铸造中,开发一个新的铸件,工艺定型需通过多次试验,反复摸索,最后根据多种试验方案的浇铸结果,选择出能够满足设计要求的铸造工艺方案。
多次的试铸要花费很多的人力、物力和财力。
采用凝固过程数值模拟,可以指导浇注工艺参数优化,预测缺陷数量及位置,有效地提高铸件成品率。
CA精密铸造技术就是将计算机辅助工程应用到精密铸造过程中,并结合其他先进的铸造技术,以高质量、低成本、短周期来完成复杂产品的研发和试制。
目前,利用CA精铸技术,已完成多种航天、航空、兵器等关键部件的试制,取得满意的效果。
2材料与实验方法
CA精铸可应用于不锈钢、耐热钢、高温合金、铝合金等多种合金。
三维模型可采用IDEAS、UGII、PROE等三维设计软件进行设计,工艺结构和模型转换采用MagicRp进行处理和修复,在AFSMZ320自动成型系统上进行原型制作,采用熔体浸润进行原型表面处理,凝固过程数值模拟采用PROCAST和有限差分软件进行计算。
3CA精密铸造工艺的关键问题及相关技术讨论
近年来,与CA精铸技术相关的三维CAD设计、反求工程、快速成型、浇注系统CAD、铸造过程数值模拟(CPS)以及特种铸造等单体技术取得了长足的进步,这些成就的取得为集成化的CA精铸技术的形成奠定了基础,促进了CA精铸技术的迅猛发展和应用。
为了使各单体技术成功地用于CA精铸,必须消除彼此之间的界面,将这些技术有机地结合起来。
从而在产品开发中做到真正意义上的先进设计+先进材料+先进制造。
3.1三维模型的生成与电子文档交换
如何得到部件精确的电子数据模型,是CA精铸至关重要的第一步。
随着三维CAD软件、逆向工程等技术的发展,这项工作变得简单而且迅捷。
在此主要介绍利用IDEAS进行实体建模和数据转换的过程。
IDEAS9集成了三维建模与逆向工程建模模块。
通过MasterModeler模块可以得到复杂模型,既可以进行全几何约束的参数化设计,又可进行任意几何与工程约束的自由创新设计;曲面设计提供了包括变量扫掠、边界曲面等多种自由曲面的造型功能。
逆向工程Freeform可将数字化仪采集的点云信息进行处理,创建出曲线和曲面,进行设计,曲面生成后可直接生成RPM用文件,也可传回主建模模块进行处理。
实体文件生成后需转变成STL文件以作为RP设备的输入。
转换过程应注意选择成型设备名称,通常选用SLA500,三角片输出精度在0.005~0.01之间。
采用MagicRp处理时应注意乘上25.4,得到实际设计尺寸。
3.2凝固过程的数值模拟
3.2.1凝固过程的数值模拟原理
铸造是一个液态金属充填型腔、并在其中凝固和冷却的过程,其中包含了许多对铸件质量产生影响的复杂现象。
实际生产中往往靠经验评价一个工艺是否可行。
对一个铸件而言,工艺定型需通过多次试验,反复摸索,最后根据多种试验方案的浇铸结果,选择出能够满足设计要求的铸造工艺方案。
多次的试铸要花费很多的人力、物力和财力。
铸造过程虽然很复杂,偶然因素很多,但仍遵循基本科学理论,如流体力学、传热学、金属凝固、固体力学等。
这样,铸造过程可以抽象成求解液态金属流动、凝固及温度变化的问题,就是要在给定的初始条件和边界条件下,求解付立叶热传导方程、弹塑性方程。
计算机技术的发展,使得求解物理过程的数值解成为可能。
应用计算机数值模拟,可对极其复杂的铸造过程进行定量的描述。
通过数学物理方法抽象,铸造过程可表征成几类方程的耦合:
1热能守恒方程:
2连续性方程:
3动量方程:
常用的数值模拟方法主要是有限差分法、有限元法。
有限元差分法数学模型简单,推导简单易于理解,占用内存较少。
但计算精度一般,当铸件具有复杂边界形状时,误差较大,应力分析时需将差分网格转换成有限元网格进行计算。
有限元法技术根据变分原理对单元进行计算,然后进行单元总体合成,模拟精度高,可解决形状复杂的铸件问题。
无论采用什么数值方法,铸造过程的数值模拟软件应包括三个部分:
前处理、中间计算和后处理。
前处理主要为中间计算提供铸件、型壳的几何信息;铸件和型壳的各种物理参数和铸造工艺信息。
中间计算主要根据铸造过程设计的物理场,为数值计算提供计算模型,并根据铸件质量或缺陷与物理场的关系预测铸件质量。
后处理是指把计算所得结果直观地以图形方式表达出来。
铸造过程流场、温度场计算的主要目的时就是对铸件中可能产生的缩孔缩松进行预测,优化工艺设计,控制铸件内部质量。
通过在计算机上进行铸造过程的模拟,可以得到各个阶段铸件温度场、流场、应力场的分布,预测缺陷的产生和位置。
对多种工艺方案实施对比,选择最优工艺,能大幅提高产品质量,提高产品成品率。
3.2.2铸造过程数值模拟软件[5]
经过多年的研究和开发,世界上已有一大批商品化的铸造过程数值模拟软件,表明这项技术已经趋于成熟。
这些软件大都可以对砂型铸造、金属型铸造、精密铸造和压力铸造等工艺进行温度场、应力场和流场的数值模拟,可预测铸件的缩孔、疏松、裂纹、变形等缺陷和铸件各部位的纤维组织、并且与CAD实体模型有数据转换接口,可将实体文件用于有限元分析。
ProCAST是目前应用比较成功的铸造过程模拟软件。
在研制和生产复杂、薄壁铸件和近净型铸件中尤能发挥其作用。
是目前唯一能对铸造过程进行传热-流动-应力耦合分析的系统。
该软件主要由八大模块组成:
有限元网格剖分,传热分析及前后处理,流动分析,应力分析,热辐射分析,显微组织分析,电磁感应分析,反向求解等。
它能够模拟铸造过程中绝大多数问题和物理现象。
在对技术充型过程的分析方面,能提供考虑气体、过滤、高压、旋转等对铸件充型的影响,能构模拟出消失模铸造、低压铸造、离心铸造等几乎所有铸造工艺的充型过程,并对注塑、压蜡模和压制粉末材料等的充型过程进行模拟。
ProCAST能对热传导、对流和热辐射三类传热问题进行求解,尤其通过“灰体净辐射法”模型,使得它更擅长解决精铸尤其是单晶铸造问题。
应力方面采用弹塑性和粘塑性模型,使其具有分析铸件应力、变形的能力。
对铸件进行分析时,简单的模型网格可以直接在ProCAST生成。
复杂模型可以由IDEAS等软件生成,划分网格后输出*.unv通用交换文件,该文件应带有节点和单元信息。
Meshcast模块读入网格文件后输出四面体单元用于前处理。
PreCast对模型进行材料、界面传热、边界条件、浇注速度等参量进行定义,最后由ProCAST模块完成计算。
应用IDEAS与ProCAST,我们对某发动机部件进行了凝固过程模拟。
该部件由于有一个方向尺寸较薄,浇注过程中极易发生裂纹与变形,通过模拟,对浇注系统结构进行了优化,减少应力集中,防止变形和开裂,取得明显的效果。
专用机床是一种专门适用于特定零件和特定工序加工的机床,而且往往是组成自动生产线式生产制造系统中,不可缺的机床品种。
组合机床是专用机床的一种,它以标准化部件为基础,配以少量的专用部件组成。
而目前一些机床厂对其生产的通用机床若作改动时,也习惯用专用机床来取代。
比如数控车床由于盘改为专用设计的,这台数控车床则不用原机床型号,而采取编专用机床号的办法。
由于专用机床是一种《量体裁衣》产品,具有高效自动化的优点,是大批量生产企业的理想装备。
随着制造技术的进步,数控技术的普及,专用机床的数控化发展也很快,专用机床在生产实践中占有一定的比重。
据有关资料介绍,日本2001年专用机床产值占机床产值的比达到8.8%;我国台湾省这一数字达到6.9%;而我国仅为0.67%。
所以,在当前产品结构调整中,发展专用机床是行业发展中的一个值得注意的问题。
专用机床及其自动化生产线的制造,与大量生产汽车等性质不一样,也与普通机床的制造性质不一样,它具有两个极其鲜明的特征:
一是集成性。
用户订购专用机床都是要求交钥匙工程,它集加工工艺(含工艺方法及工艺参数),机床、夹具、工具(包含辅助)的开发设计与选择,检验测量(包括进入机床前的毛坯检验、加工中及成品的检验测量)物流的输送,切屑和冷却液的防护与处理等于一体。
它不仅仅解决其中的某一问题,而是要解决好涉及较宽的技术领域可能遇到的每一个问题。
二是单一性。
专用机床几乎都是单台性生产,要根据用户提出的要求,进行一次性开发,一次性制造,而且还要保证一次性成功。
根据长期从事专用机床及其自动生产线开发制造的体会,我将专用机床制造业的工作归纳为以下八个特点:
一是技术难度大。
由于它是集加工工艺、机床、夹具、辅具、刀具、检验测量、物流等于一体,实现交钥匙工程,从而涉及技术领域宽且复杂,又是一次性制造,要保证一次成功,所以技术难度大。
二是经营风险率高。
专用机床(或自动线)根据用户订单“量体裁衣”制造的,不可能有试制探索过程,要确保一次成功,有相当大的技术风险。
由于技术方案不当,造成局部或整体报废的情况屡见不鲜;由于一次性制造,在制造调试过程中难保不出现问题,解决这些总是需要时间,从而按期交货也有一定的风险;由于装备是专门为某一用户订做的,当该用户因种种原因不能如期付款、甚至无力付款时,势必造成制造企业的损失;在现行的金融制造还无法约束对方,产品无法转让他人的情况下,经营显而易见。
三是协作困难大。
由于是一次性制造,它不像汽车零部件那样大量生产,也不像通用设备那样批量生产,找协作厂家很困难。
条件一般的企业,很难保证一次性制造出合格的产品;条件好的企业,又不愿当配角,对这种委托协作看不上。
四是技术依赖性强。
专用机床及其自动线从设计、工艺编制、生产制造到装配调试的全过程,都需要一批有经验的技术人员、管理人员和技术工人。
五是利润空间小。
在国外不同的生产模式的企业(指大量生产、批量生产或单件小批生产),其生产产品的效益相差不会太大,但国内这几种生产模式的企业效益却相差悬殊。
如果做一比较,就很能说明问题,假如国外的某种产品价格为1,相对国内轿车价格则为1.15-1.25,对通用机床国内的价格为0.7左右,而国内专用机床的价格仅为0.3-0.4。
由于国情或用户对专用机床制造业不够理解等原因,专用机床的销售价格总体偏低。
近几年,国内市场专用机床的单台平均售价呈下降趋势,以组合机床为例,其单台平均售价从1996年的31万多元下降到2000年的23万多元,降幅达25%。
在国外购买一台标准的加工中心的费用和为其配全成加工某种零件所需的夹具、刀具及相关辅具的费用之比,一般是100:
60左右,之所以后者占有如此高的比例,是因为除了考虑硬件的消耗外,更多是考虑技术的投入和由此而带来的风险。
而国内这一比值一般用户仅能接受100:
25左右。
如果在考虑5%的质量保证金要在一年后才能拿到,这种种原因把产品的利润压缩到极小的空间。
六是技术成长期长。
专用机床的设计制造涉及专业面广,要具备较丰富的工艺知识,要比较熟悉用户的制造工艺,要保证一次成功,培养一名熟练的主管设计师,要花几年时间,才能做出好的产品设计、好的制造工艺,生产出好的产品,技术成长期要长。
七是人员流动困难。
由于订单不均衡,会引起生产的不均衡,国外除了零部件外协条件优越外,还有成熟的技术劳动力市场,企业可以根据订单情况输出或吸收有关劳动力,使这与企业生产相适应。
国内则无法做到这一点,有时可以招些临时工,但多数只能承担一些辅助性工作,熟练技工则难以寻求。
八是技术引进困难,与国外合作难。
由于专用机床是一次性设计制造,引进技术若仅供一次使用,则成本太高,很难实现。
到目前为止,我国专用机床制造业没有一家谈成合资,虽有接触,但都仅限于具体项目的合作。
八个特点,八种原因,既相互关联,又各具特性,但确实是影响我国专用机床制造业发展的重要方面。
今天,我们要调整机床工业的产业结构,发展专用机床是一项十分重要的工作。
因此,我们建议:
1、国家要在政策上进一步支持装备工业,特别是基础机械工业的发展。
近几年,我国数控机床虽较快发展,但多是通用机床,而代表国家装备能力和知识水平的集成化、成套装备,尤其是以专用机床(包括各种数控专用机床)及其自动线的生产企业和产品产量却在不断萎缩,这里固然有专用机床市场需求的萎缩,也有用户选择装备上的偏见。
而政策上的引导是必要的。
2、专用机床制造业要进行必要的调整。
制造业的自我调整,一是要解决好主机生产与配套协作的关系;二是要解决好技术引进与自主创新的关系;三是要解决好用先进技术改造提升企业和产品的关系;四是要解决好用高技术提高产品档次,增加产品附加值的关系。
3、虽然专用机床及其自动线的市场在发生变化,但是,企业要根据自己的情况,主动地适应市场,以新技术、新工艺改造传统的专用机床,进一步提高其市场适应能力,进一步提高产品档次和水平,进一步提高产品质量。
高效专用设备有着较大的市场和潜在市场,要瞄准国内大中型企业和相当一部分民营企业的需要,开发制造质量更好、性能更优异的专用机床及其自动线,以其优质完善的服务,满足需求。
同时,我也建议一些从事专机制造的企业,也应选择开发一种或几种通用,作为与专机生产的互补,形成犄角之势,形成企业的特色,在市场中求得发展的空间。
结论:
1.计算机辅助工程与精密铸造结合而成的CA精密铸造技术具有很强的通用性,可以缩短研制周期,节约开发成本;
2.IDEAS与RPOCAST的配合,可以对复杂件进行铸造过程数值模拟;
3.计算机凝固模拟技术可用于复杂件的浇注系统设计和优化,并能较为准确的预测缺陷及其位置、变形开裂倾向,用于指导浇注系统的优化。
电火花加工作为一种特种精密加工技术,近年来得到了迅速的发展。
特别是慢走丝线切割加工,已经成为模具制造和金属加工行业必不可少的加工手段。
线切割技术的发展,离不开电极丝技术的同步发展。
因为线切割机的切割效率和切割质量与电极丝的性能紧密相关,而电极丝技术的突破往往会导致线切割机设计的革新。
从1979年镀锌电极丝的发明到今天,市场上不断出现了各种各样比普通黄铜丝性能更好的电极丝,电极丝的正确选用已经成为使线切割机的性能得到最大限度的发挥并为用户创造更多利润的关键。
现在,在欧美和日本等发达国家,以镀锌电极丝为主的高性能电极丝正在逐渐取代放电性能受到很大局限的黄铜丝。
同时,除了早已将镀锌电极丝作为标准配置的线切割机制造商Agie和Charmilles外,现在Mitsubishi和Sodick公司也在最新的机型上增加了采用镀锌丝的模式和加工参数,使这些设备的切割速度较之采用黄铜丝有30%~50%的显著提升。
但是在国内,前几年由于欧洲进口的镀锌电极丝价格较高,不仅几乎所有的日本、台湾和国产慢走丝机的用户都只用黄铜丝,一些本来使用镀锌电极丝的Agie机和Charmilles机用户,也改用了“便宜”的黄铜丝,造成了相当多的用户以为“电极丝就是黄铜丝”这一行业内的误区。
有不少国内的用户在引进最新的高性能线切割机的同时,忽视了电极丝的重要性,以为它只不过是一种普通的消耗品。
不管什么机型或加工要求,黄铜丝都以其低廉的价格似乎成了唯一的选择。
从2002年起,来自韩国的性价比较好的镀锌电极丝在广东地区为不少用户所采用,取得了明显的效益,至2003年行业内越来越多的用户开始关注镀锌电极丝的应用,“不同的加工,采用不同的电极丝”这一概念开始为精明的线切割用户所接受。
实际上现在的线切割加工有着比过去更多的变化,从加工材料、切割速度、轮廓精度、表面质量到工厂的运行模式等等。
对于这些相互起作用的变数来说,只有选择合适的电极丝才能使工厂对加工效率、加工成本和加工质量整体进行优化。
一、电极丝的性能
高性能的电极丝必须是各种有用特性的有机组合,那么电极丝有哪些有用的特性呢?
1、电气特性
现代线切割电源对电极丝提出了严格的要求。
它要能承受峰值超过700安培或平均值超过45安培的大切割电流,而且能量的传输必须非常有效,才能提供为达到高表面光洁度(0.2Ra以上)所需的高频脉冲电流。
这取决于电极丝的电阻或电导率。
紫铜是电导率最高的材料之一,它被用来作为衡量其他材料的基准。
紫铜的电导率标为100%IACS(国际退火紫铜标准),而黄铜的电导率为20%。
2、机械特性
拉伸强度:
拉伸强度是衡量材料在受到径向负荷时抵抗断裂的能力。
它是用单位截面积所能承受的重量来标度的,如英制的PSI(磅/平方英寸)或公制的N/mm2(牛顿/平方毫米)。
紫铜属于拉伸强度最低的材料(245N/mm2),而钼则最高(1930N/mm2)。
电极丝的拉伸强度取决于材料的选择以及各种热处理和拉伸处理工艺。
电极丝有时被分为"软丝"和"硬丝",对于不同的设备和应用来说,各有其长处。
记忆效应:
这与电极丝的"软"或"硬"直接相关。
软丝抽离线轴时没有恢复成直线的记忆能力,所以无法用于自动穿丝,但这对切割来说并没有影响,因为加工时电极丝上是加了张力的。
软丝适用于上、下导丝咀不能倾斜的设备进行超过7度的大斜度切割。
而硬丝则是自动穿丝机的最佳选择,同时因为拉伸强度高,其抵抗因切割时电流和冲洗力造成丝的抖动的能力较强。
延伸率:
延伸率是切割加工中由于张力和热量引起电极丝长度变化的百分比。
软丝的延伸率可大到20%,而硬丝则小于2%。
软丝在斜度加工时,延伸率高的电极丝能更保证斜面的几何精度,并且较软的电极丝在导丝咀中滑动时产生的震动也较小。
不过电极丝进入切割区后软丝的抖动程度比硬丝大,所以还得折中考虑。
3、几何特性
在线切割技术发展的早期(1969年到七十年代中期),对电极丝几乎没有做任何的研究,用的是现成的电机和电缆上的紫铜丝。
而今天,高效率高精度的线切割机要求电极丝具有误差极小的几何特性。
电极丝制造的最后工序是采用多个宝石拉丝模来得到光滑、圆度极好、丝径公差为+/-0.001mm的成品。
另一方面,还有一些电极丝却特意设计成具有相对粗糙的表面,可以提高切割速度。
4、热物理特性
电极丝的热物理特性是提高切割效率的关键。
这些特性是通过合金成分的配比或基础芯材的选择来确定的。
熔点:
电极丝的熔点是一项重要的指标。
由于电极丝通过导丝咀时的机械运动,以及冲洗力和放电等因素,电极丝在切割时是有抖动的。
这将造成无数次的极小的短路,使切割过程减慢。
电极丝工作时如果在外径上能够损耗一些,这样它在面对切口方向的空隙可以防止或减少短路效应。
同时它在背对切口方向的空隙有助于改善冲洗作用,可以更好的去除加工废屑。
电极丝外径的损耗不会影响加工精度,因为新的电极丝在不断的进给。
这是冶金学家在研究电极丝的冲洗性时要考虑的材料的两个特性之一。
气化压力:
电火花切割时会产生大量的热量,其中的一些热量被电极丝吸收走了,这会降低切割效率。
如果太多的热量损耗在电极丝上,电极丝就会因过热而熔断。
因此需要电极丝表面能够快速气化,在电极丝得到冷却的同时把热能释放到工件上。
材料受热达到熔点后就会气化,产生气化压力。
熔点低的材料更容易气化。
电极丝所应该具有的另一个特性就是低熔点和高气化压力,可以帮助把废渣吹离切缝。
这就是电极丝冲洗性好所应该具备的另一个特性。
当电极丝和工件在切割表面处是气化而不是熔化时,产生的是气体而不是熔化的金属颗粒。
这反过来又改善了冲洗过程,因为要冲走的颗粒少了。
二、电极丝的种类与应用
目前,市场上可选用的电极丝可分为以下几类:
1、黄铜丝
黄铜丝是线切割领域中第一代专业电极丝。
1977年,黄铜丝开始进入市场。
这种电极丝曾带来了切割速度上的突破,当时对于厚度为50mm的工件,切割速度从12mm2/分钟提高到25mm2/分钟。
是什么使速度翻了一倍呢?
黄铜是紫铜与锌的合金,最常见的配比是65%的紫铜和35%的锌。
当时发现黄铜丝中的锌由于熔点较低(420℃,而紫铜为1080℃)能够改善冲洗性。
在切割过程中,锌由于高温而气化使得电极丝的温度降低并把热量传送到工件的加工面上。
理论上讲,锌的比例越高越好,不过在黄铜丝的制造过程中,当锌的比例超过40%后,电极丝的α单相结晶结构变成了α和β双相结晶结构。
这时材料变得太脆而不适合把它拉成直径很小的细丝。
黄铜丝可以有不同的拉伸强度来满足不同的设备和应用场合。
这是通过一系列的拉丝(淬火作用)和热处理(退火)工序来实现的。
普通黄铜丝的拉伸强度在490-900N/mm2之间。
黄铜丝的主要缺点:
(1)加工速度无法提高:
由于黄铜中锌的比例一定,所以放电时的能量转换效率无法进一步提高;以0.25mm黄铜丝切割30-60mm厚的钢材为例,国内很多用户的主切速度都在120mm2/分钟左右。
(2)表面质量不佳:
黄铜丝表面的铜粉和放电时由于电极丝表层气化而带出的铜微粒会积存在工件的加工面上形成表面积铜。
同时由于冲洗性不好而在工件表面产生较厚的变质层,这些都会影响工件的表面硬度和粗糙度;
(3)加工精度不高:
特别是在加工较厚的工件时,由于冲洗性不良,会产生较大的直线度误差(上下端尺寸误差和鼓形差)。
此外,由于价格竞争的原因,目前国内的低价黄铜丝普遍存在着各种质量问题,例如因采用的铜材胚料材质不良以及拉丝设备和工艺上的原因导致黄铜丝表面铜粉较多,截面几何误差太大等等,这些都会导致放电稳定性下降,严重影响加工速度和质量。
同时,还会污染设备部件加大设备的损耗。
黄铜丝的应用场合:
(1)加工量不足,不是24小时开机的用户。
因为加工效率对于这些用户来说不是主要问题;
(2)对加工精度特别是表面质量要求不高的用户;
(3)以加工小尺寸、薄厚度为主的用户。
因为工件装夹调整的时间占总加工时间的比例较高,切割时间较少,对加工效率的影响不明显。
(4)工件的材料硬度不高或厚度不超过80-100mm。
虽然随着各种更好性能的镀层电极丝的出现和普及,黄铜丝的市场份额呈不断下降的趋势,但是,由于它成本低廉,并且能满足普通的加工需求,因此还会继续得到广泛的应用。
同时,市场上还出现了一些在性能上有不同程度改善的且价格低于镀层电极丝的新型黄铜丝:
(1)超净型黄铜丝:
针对普通黄铜丝表面铜份过多这一弊端,通过在后道工序中增加特别的清洗工艺而制成;
(2)超硬型黄铜丝:
通过在黄铜中加入其他微量元素,使黄铜丝的拉伸强度高达1200N/mm2。
这种丝在加工超厚或超硬工件时可以改善加工精度和速度;
(3)高速型黄铜丝:
将黄铜中锌的比例加大到极限的40%,可以改善冲洗性,提高切割速度。
但是,其切割速度还是比镀锌电极丝要慢。
2、镀层电极丝
由于低熔